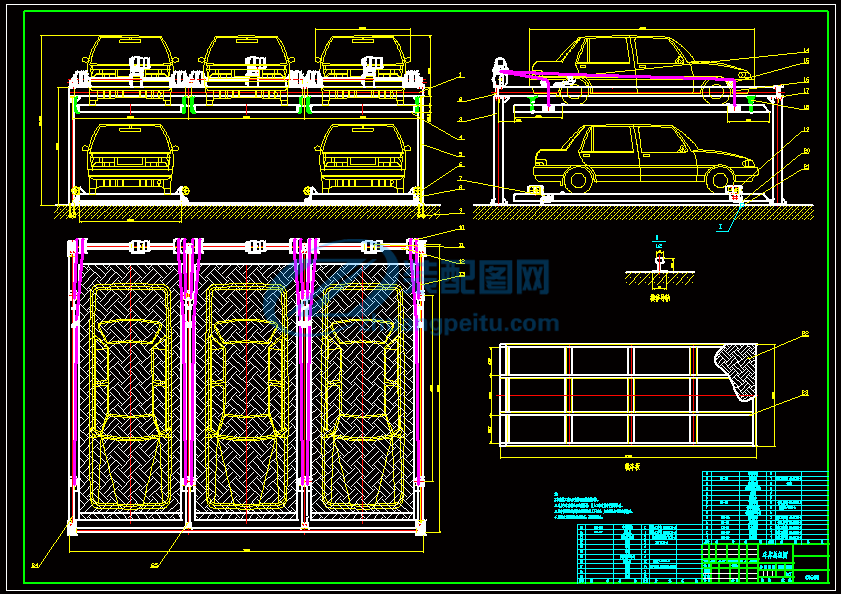
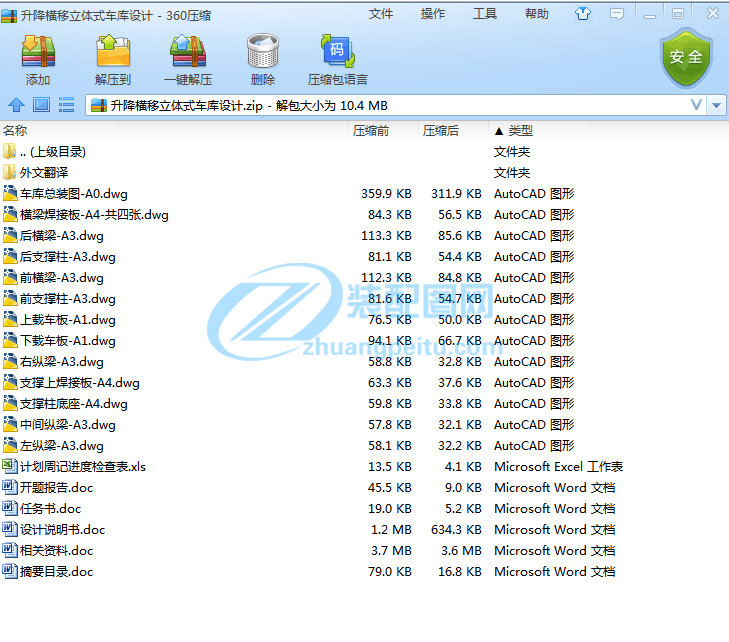
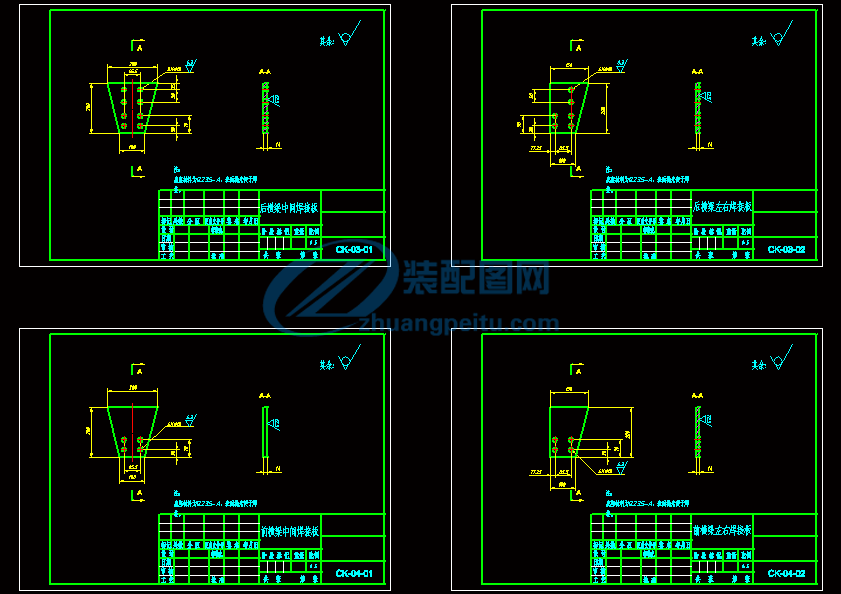
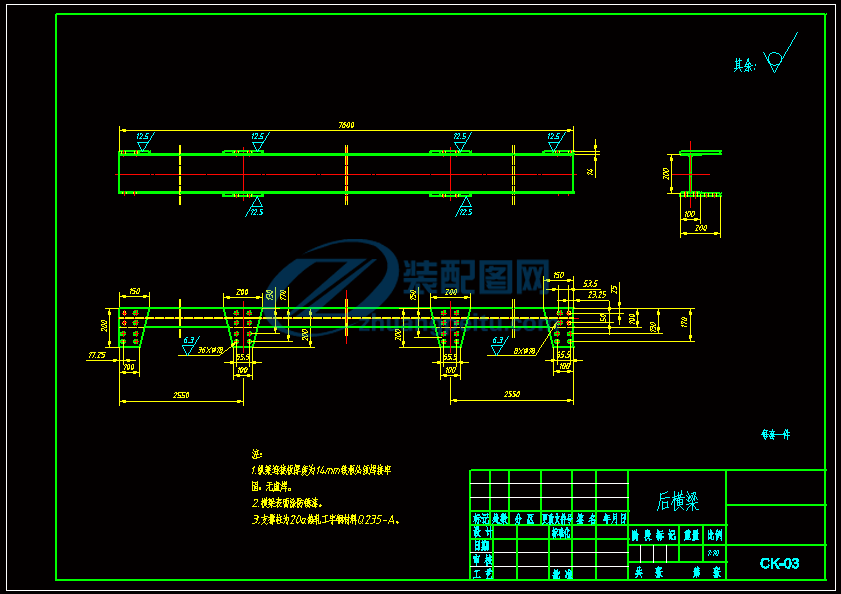
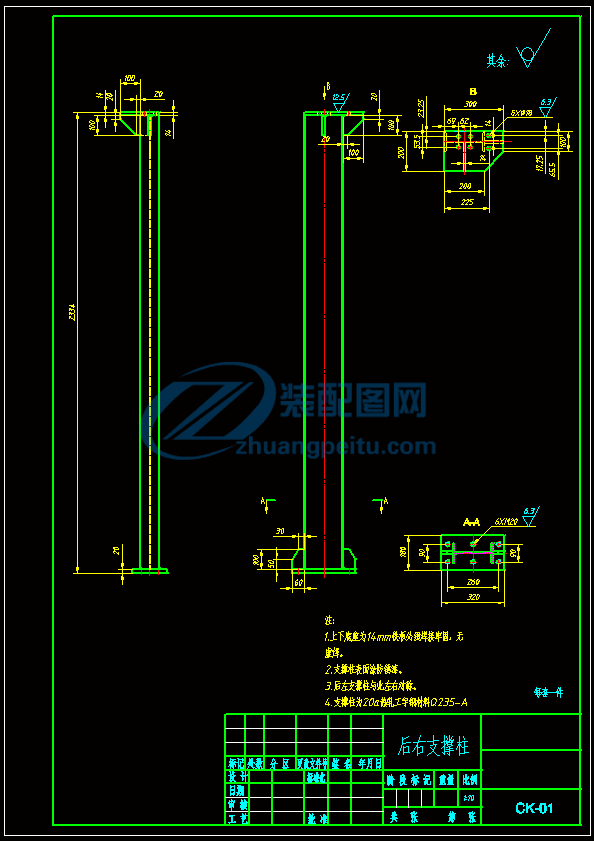
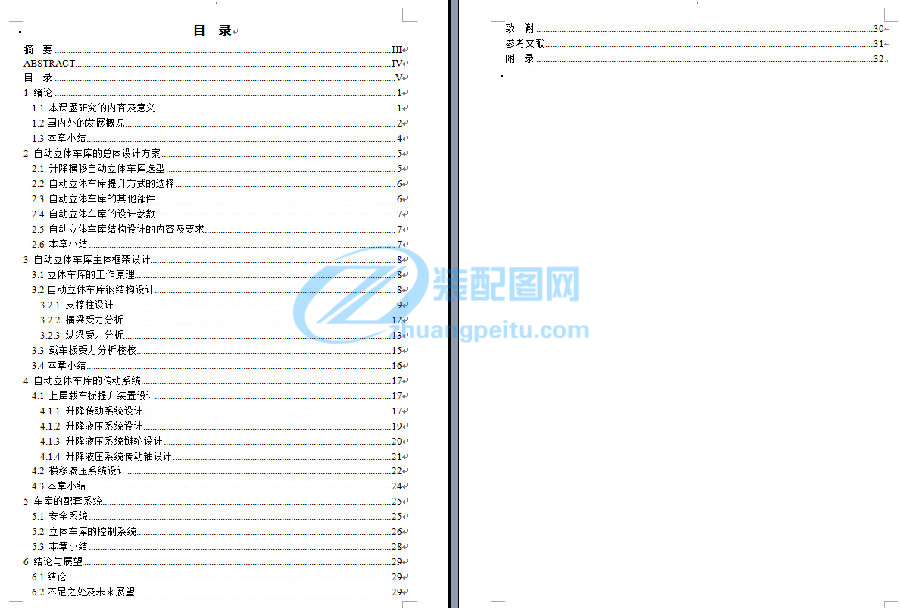
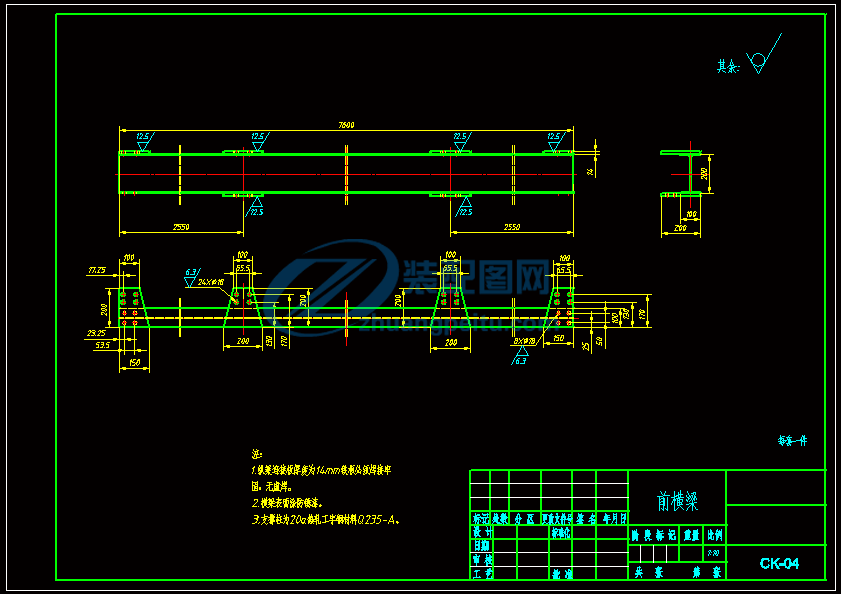
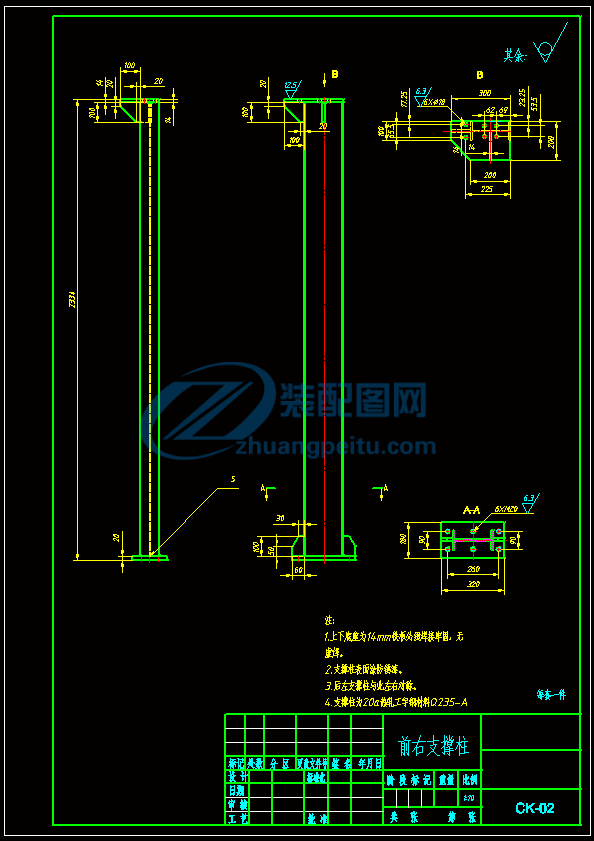
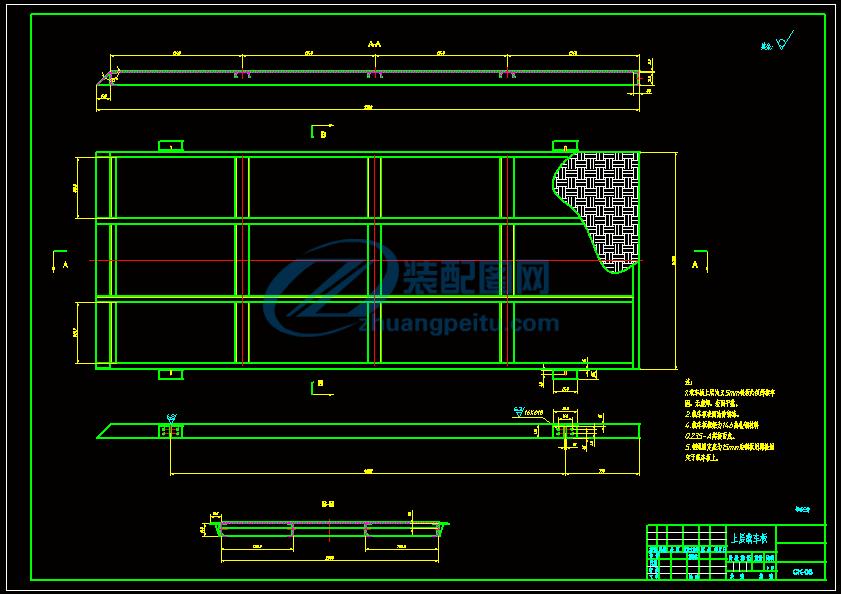
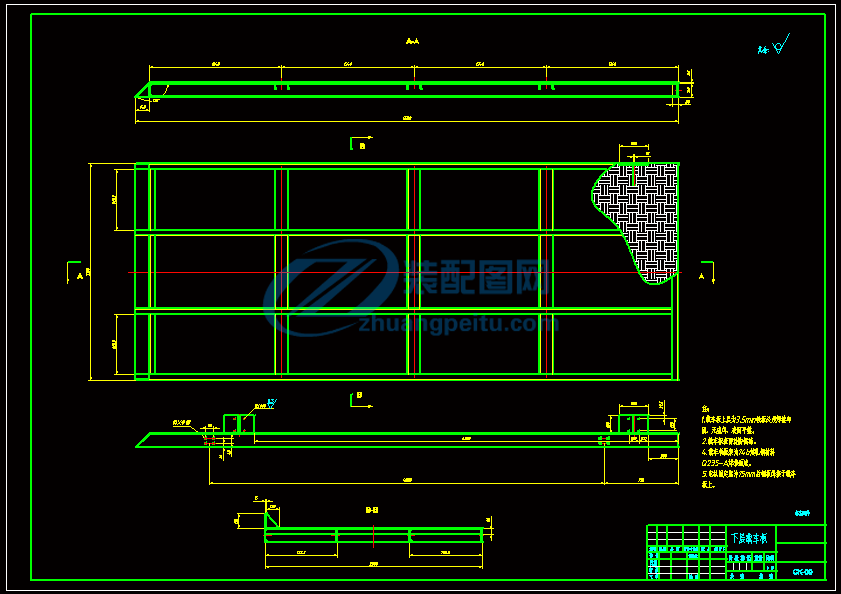
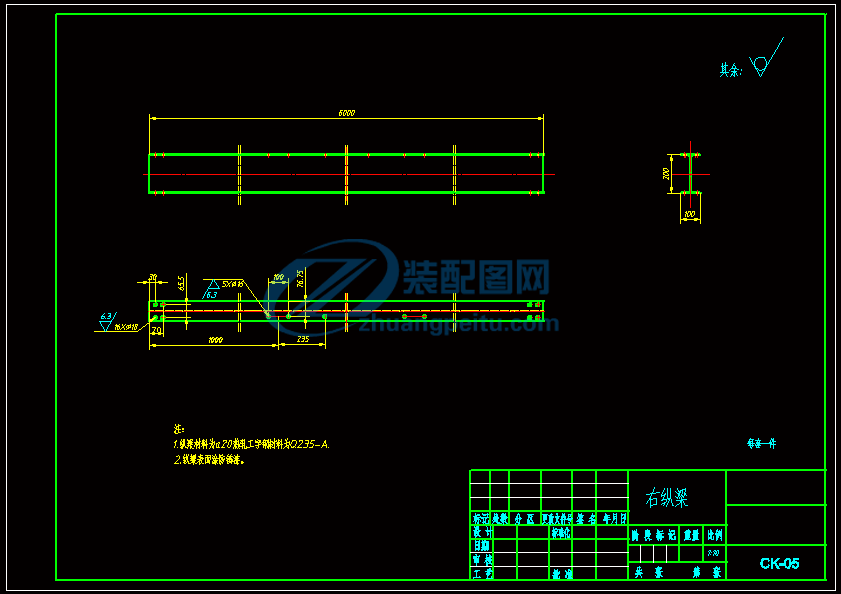
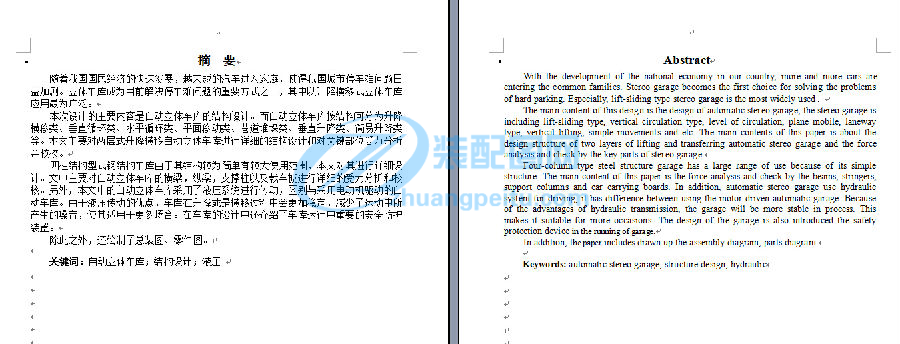
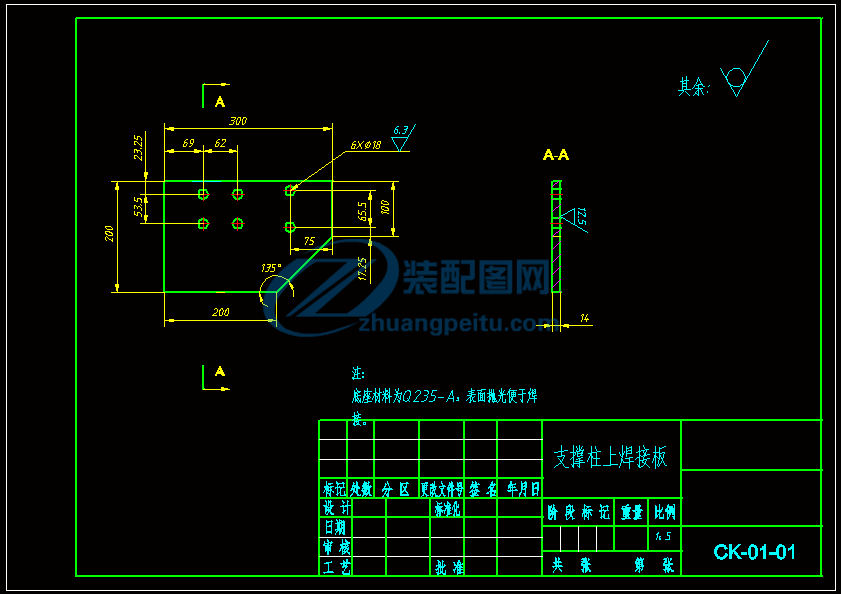
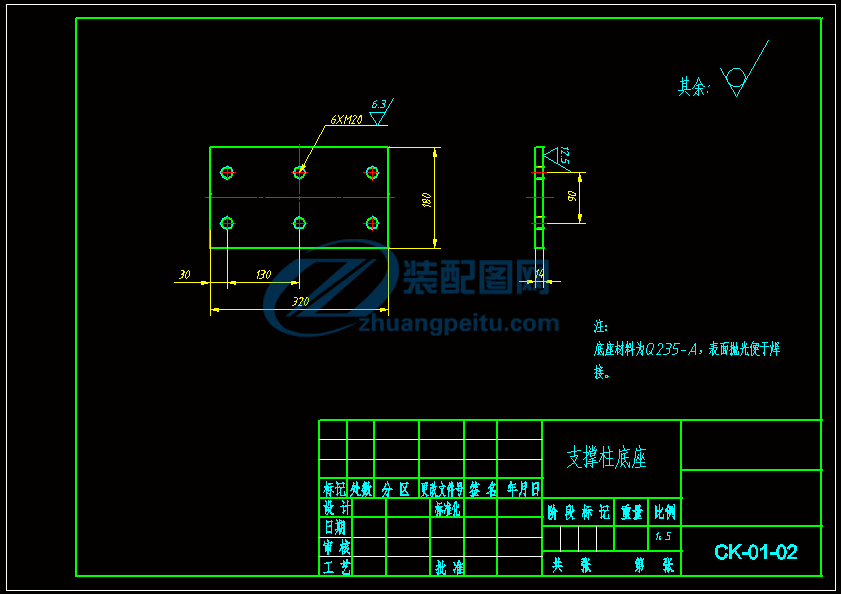
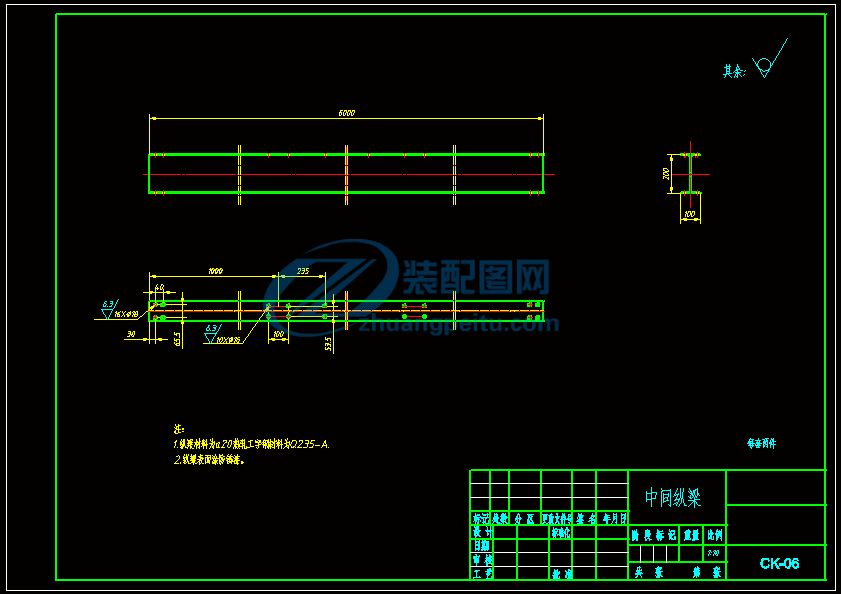
英文原文THE 6 LAYERS STEREO GARAGE DESIGN BASED ON OMRON PLCZhuoran Zhang Department of Electrical especially the private cars, putting a great pressure on urban transportation and parking slot. This article is mainly concerned about the entire structure, running procedure and electrical system design including hardware and program design ideas for lifting-traversing stereo garage, which will not only shorten the developing period but also orient parking to centralization and automation direction; Owning some reference value.Keywords- Stereo Garage, Omron PLC, DesignInsufficient parking slots is resulted from the development of the cities, economy and transportation of the cities, the traditional garages are always making the use of the nature vacancy, in a community, the ratio between parking slots and residents is approximately 1:1, one parking slot for a family at least, in order to solve the contradiction that the parking slots using precious commercial land, the stereo mechanical garages with the advantage of the average parking slot takes of less area have been gradually in front of us. Compared with the traditional underground parking garage, the stereo garages have more advantages. First of all, the stereo garages can save more area. The traditional ways must be amassed driving path for vehicles, averagely, a car will take up 40m2 If we take multi-layers garage (6 layers) in to consideration, it is possible for 13 cars to park in the area of 50m2, which will save lots of land resources and land construction expenditure. Meanwhile, the stereo garage could guarantee the safety of the people and their cars. If there is anybody in the garage or the cars are not fully stopped, the system controlled by electrical equipment will not run either. It means that, in the scale of the management, the mechanical garage could separate the people and vehicles, which makes it more systematically. Especially for underground garages, install this kind of garage will save a large area of illumination system, so it is also emerge conservation and environment protection.Ⅰ.THE CLASSIFICATION AND IMPLEMENT BACKDROP OF THE STEREO GARAGEA.THE CLASSIFICATION OF THE STEREO GARAGEAccording to the present development of the stereo garage, the stereo garage is including lifting-traversing, roadway stacking, vertical lifting, vertical circulating, circle level circulation; The concept of the stereo garage is all from automatic logistic material transmitting system. [3]The purpose of the stereo garage is to solve the parking problem in developed cities, that is make use of limited area to park more vehicles so as to save land resources of the cities and manage the static transportation of the urban. This article gives out a way to design lifting-traversing stereo garage based on Omron PLC CP1H, which could extend to solve relevant projects.B. A BRIEF INTRODUCTION TO LIFTING-TRAVERSING STEREO GARAGE.The modularization concept is imported in lifting-traversing stereo garage. It can be designed into two to five layers or half underground type, the number of the slot is from tens to hundreds. This kind of garage is suitable for both above ground and underground, the characteristics could be generalized as less occupation of land, simple structure, flexible configuration, lower cost in construction, decoration and fire protection and short period of construction; Safe and convenient for saving and taking cars; Smoothly operation, lower noise during running. [4] It is also appropriate for commercial, bureau and residential use. The safety equipment mainly is photoelectrical sensors, limiting displacement protector and emergency switch.C. THE ENTIRE FRAME OF THE SYSTEMAs the fig. l representing, besides the central controller PLC, the stereo garage system could be divided into three sections: I. Mechanical System; It includes column, beam, carrying board, vehicle frame, hooks and etc. II. Electrical System; this section is the core of this article, which controls the whole system to operate. III. Touching Panel; it is the port from which operators and the system exchanging messages, operators could not only operate the system, but also in the situation of the malfunction, it could let operator enter the manual or debugging mode.Figure 1. The structure of the system Figure 2. Touch Screen (Auto running and Manual)? THE MAIN HARDWARE OF THE SYSTEMWe mainly use the Omron PLC CPH1, on considering the control requirement and the cost, we adopting CP1HX40DR-A PLC, the programming ways are ladder diagram or ST instruction list. The instruction length is 1 to 7 steps per instruction, each I/O relays has 1600 ports, USB 1.1 for communication.The display part, we import screen of WEINVIEW MT6056i series, the screen material is TFT, 5.6 inches, and the resolution is 320x234, with USB2.0 port supporting downloading. The frequency of the CPU is 400 MHz, 128RAM.D.THE SYSTEM STR UCTURE AND FUNCTIONSThe mechanical parts cooperating with electrical system are carrying board, hooks and chains. There are 6 slots on each layer besides 7 slots on the top layer, totally 37 slots, the purpose for one slot empty on each layer is that making enough space for carrying board to move. The carrying boards of the first floor only design to traverse, also the top floor carrying boards are only supposed to lift. The other carrying boards among these floors are designed to life and traverse. In this way, this system could achieve the saving and taking from any slots among these 6 layers.In addition, this system has a touch screen system, which switches between auto run and manual debugging mode. Under the auto run mode, it could select a certain slot to accomplish saving and taking behavior, at the same time, monitoring the operation of the system. (Green words “System Running“ in auto mode without malfunction). When failure occurs, the system seized and on screen flashing yellow failure code with red backdrop, with the help of the failure code, the professional operator could recognize and eliminate the failures promptly and accurately. On considering more authorities are given in manual debugging mode, to preclude unprofessional persons enter the mode by chance, before enter the mode, there is a cipher verification, in which the sequence could be set by ourselves. This would protect the system from potential dangers.Figure 2 is the graph of system auto running, manual and debugging. Ⅱ. THE COMPOSURE OF THE ELECTRICAL SYSTEMA. STRONG ELECTRICITY SYSTEMThe strong power system includes power supply, protection and driving mechanism, here is electronic motors. Installing XJ3-D on the forepart of the power supply wire, which is used to protect phase sequence of the three-phase voltage, so that guarantee the right rotation of the motors. Moreover, the motors on some layers use the same three-phase voltage.B.THE SET OF THE MOTORSThere are 6 traversing motors on the first layer, 6 traversing motors for 2 to 5 layers each, and so it is with lifting motors for 2 to 5 layers. The top layers have only 7 lifting motors. After setting the motors, mark every motor. For example, the motor driving the third slot of the second layer, we mark it with “23“, the relay before the motor are named KM23. Here series connect all the motors' thermal protection, any motor's problem will stop the system. In this way, it has no influence on the stability of the system, but lowers the cost. At the same time, make it easier to find the problems. (What we need to do is press the thermal protection switch one by one).C .WEAK POWER SYSTEMThe weak power system is also the control system, which are mainly the PLC mode and its 5 extended modules, also the sensors. As the figure below, on the right is the input part, DC 24V, on the left, is the output section, AC 220V, to connect with contactors and drive them. These device's functions have close relationships with the entire system's control requirements. On the above of the graph, the protection equipment are emergency switch, installed beside the touching panel, emergency only, trigger it, the system stops; Front and back photoelectrical sensors, which are used to detect people or unidentified objects breaking into the system, if this happens, the system would stop then response with photoelectrical failure, the goal is to protect the people and the vehicles. The phase sequence protection has been illustrated before; Over current protection normally activated under the motor stuck; All the margin switches series connected, cult the main power when any carrying board exceed the limiting position.Limit switches including up ones and down ones or left and right limit switches. In order to achieve the controlling requirements, the level limit switches are installed on the both side of the each slot frame, while the vertical limit switches are installed on the chain which attached to the motor. It is necessary to point out that the first layer only installed down and left right limit switches, the top layer only installed up switches these switches could sense the position of the carrying boards, helping to finish the lifting and traversing control; Hook position sensors is to fix the vehicles and sense the slot empty or not.The output points“00 04 05 06 07“ are to select different phase for each layer, so control the motors' rotation ways.Figure 3. PLC Modules (Segment)There are other 4 extended modules, which only give more I/O ports to the system, similar to this main part. Ⅲ. OPERATION PROCEDUREA. TAKING PROCEDUREAs far as the first layer concerned, it is only designed to traverse, so as to make space to upper layer's carrying boards to move downward. So do the other layers, which are designed to traverse. When traversing meet the requirements, lifting mechanism will run to put the carrying board down, finishing the saving and taking procedure. During the procedure the photoelectrical sensors are open and will behave as fore part has explained. In figure 2A, is the taking condition, at this time “Loading“ will flash until the taking procedure finishes.When we enter “51“, the system will distinguish whether the operation is a taking or a saving according to the hook of the 51 slot. Then prints the message responded to the state of the hook on the screen, the operator could confirm the operation or cancel it. On confirming, the 51 carrying board will wait for its downward boards to finish the traversing move then moving down. In addition, a timer is added to this control module in order to preclude level limit switches malfunction, resulting into the traversing move time up. If the time for traversing move exceeds the set time, the system will warn the operator “traversing move time up“ which displays on the screen, the operator could check out the failure. The up limit switches are used to sense whether the carrying boards are stopped at their routine slots, which the level switches can't finish. Maybe one carrying board stuck between two layers. Only do all the upper layers' carrying boards stop at their routine slots, the selected carrying board's lifting move is activated. A timer is also set into the lifting control, with the same function as traversing timer. The elevator carries the vehicle down to the ground, release the hook, now the photoelectrical signal shut down, and waiting for the owners to take their vehicle. On driving away the vehicle and operator's confirming the photoelectrical signal resumes, the carrying board back to its slot from the down way.Figure 4. The flowchart of the taking and saving procedureB. SAVING PROCEDUREThe saving process is based on taking procedure, so they are familiar; the only difference is the hook move. Ⅳ. SOFTWARE PROGRAMMING AND PROGRAMMING ENVIRONMENTA.SOFTWARE PROGRAMMING ENVIRONMENT AND ITS LANGUAGEIn this system, we choose Omron CX-ONE 3.0 to program the PLC. The language for programming is classic ladder diagram. On considering the stereo garages are installed in different condition and requirement of different users, the scale of the stereo garages should be flexible, for example different layers or slots. In order to meet the different scales requirements, the program is modularized, only need to change the I/O ports, the logical relations in the ladder diagram are fixed. In this way, it is not only with highly compatibility but also shortens the period to develop relevant designs and make it easier to debugging and repair.B.MODULARIZED PROGRAMConditional jumps are widely used in the programming; the entire program consists of different modules, on certain conditions, the program jumps.As illustrated before, there are only two movements for a carrying board, lifting or traversing, beside the boards of first and top layers. The condition for the fifth could traverse is all the upper layers slots' up limiting switches closed. Then “Traverse OK“ is activated, and then the program will make analysis of the operation until meet set conditions, the program jumps. For the lifting movements are always with the downward movements, so program the downward standards, the system will run. The entire program is programmed with this method, above the passage, is only a traversing OK and vertical move OK module. Similarly, modules of a fixed slot, for example slot “21“. “21 Traversing Move“, “21 Vertical Move“; for whole system, “Emergency Stop and Protection“, “Button Select“, “System Monitor“ and “Debugging“ modules, which cooperate with each other to accomplish the control and monitor.Figure 5. Monitoring and Display module (Segment)Fig. 5 is the segment program of the monitoring module, all the motors' protection series connected, so are the phase sequence protection and margin switches. Any of them change; PLC will transfer messages to the screen, which displays. Meanwhile, cults off the main KM, the system stops. Ⅵ.A BRIEF SUMMARYThis paper introduces lift shifting type six floors of three-dimensional garage design method based on Omron CP1HX40DR-A controller, completing the requirements of three-dimensional garage for city vehicle management toward the direction of automation and centralization. This design can be used to restore occupied pavement, reduce preempting, and ensure safety, in addition that it could reduce traffic congestion time, reducing the injury. On this basis, the problem has been thoroughly eliminated, including various vehicles disorderly stopping and parting in disorder, and the appearance of parking places with dirty, disorderly and poor, thus protecting vehicles away from lost, being damaged and stolen. Finally, the road is giving back to the vehicles and pedestrians, the lawn to the green space, the environment of the neat civilization life to the modern metropolis.The development cycle has been greatly shortened, based on the design about three-dimensional garage design of PLC controller. This is also a kind of inevitable of the electrification, digital and automation advancement. The thoughts and methods of this design can be applied to other scale garage and relevant problems of design.REFERENCES[1] [1] Huo Gang. Application and programmer of the CP1HPLC. China Machine Press [M], 2009.1[2] [2] Omron Power program. Omron Corporation (China), 2008[3] [3] BoSen Ren.General situation of Chinese mechanical parking equipment. Celebrated manufacturers of parking equipment and peripherals directory [J] :PP5-7[4] [4] Lekang Yu Dongxiao Zuo.The development of mechanical parking. [J] Technology and management of construction machinery. 1999 1:PP 30-32[5] [5] Fuen Zhang ? Younai Wu.Principle ? design ? set up and maintenance of AC variable speed elevator. [M] China Machine Press 1999中文譯文基于歐姆龍可編程序控制器的 6層立體車庫(kù)設(shè)計(jì)Zhuoran Zhang 電氣工程 武漢理工大學(xué) 武漢,中國(guó)電子郵件:Harry zzr@126.comZhe Mao, Hailing Wan 電氣工程 武漢理工大學(xué) 武漢,中國(guó)電子郵件:maozhe998@sina.com摘要:隨著現(xiàn)代社會(huì)的快速發(fā)展,許多城市的車輛數(shù)量正在一直以指數(shù)的速度快速增加,特別是私家車。這些情況對(duì)這些城市交通和停車造成了巨大的壓力。這篇文章主要內(nèi)容是關(guān)注立體車庫(kù)的整個(gè)結(jié)構(gòu),運(yùn)行程序和電氣系統(tǒng)的設(shè)計(jì)等方面,其中包括硬件方案的設(shè)計(jì)思路,以及提升立體車庫(kù)整體性能。這不僅將能縮短立體車庫(kù)的開發(fā)周期,也促進(jìn)停車場(chǎng)向集中化和自動(dòng)化方向發(fā)展,對(duì)立體車庫(kù)設(shè)計(jì)有一定的參考價(jià)值。關(guān)鍵詞:立體車庫(kù),歐姆龍 PLC,設(shè)計(jì)停車位不足是導(dǎo)致城市經(jīng)濟(jì)和交通的發(fā)展放緩的主要原因之一,而傳統(tǒng)車庫(kù)的一直使用是導(dǎo)致停車位不足的重要因素。在一個(gè)社區(qū)中停車位和居民家庭比例約為 1:1,也就是一個(gè)家庭中至少有一個(gè)停車位,而為了解決這一矛盾而使用寶貴的商業(yè)用地是不可取的。在停車場(chǎng)中立體機(jī)械車庫(kù)的主要優(yōu)勢(shì)就是相同車位的停車場(chǎng)需要的占地面積較少,這一優(yōu)勢(shì)已經(jīng)逐步在我們面前展現(xiàn)出來。相比與傳統(tǒng)的地下停車場(chǎng)車庫(kù),立體車庫(kù)有更多的優(yōu)勢(shì)。首先,立體車庫(kù)可以節(jié)省更多的占地面積。以傳統(tǒng)的方法停車的停車場(chǎng)必須考慮車輛的行駛軌跡問題,而平均一輛車需要至少 40平方米進(jìn)行停車操作。如果我們考慮使用地是多層的立體車庫(kù)(6 層) ,有可能停放在該區(qū)域的車輛可達(dá) 13輛,而占地面積僅為 50平方米,這將節(jié)省大量寶貴的土地資源和土地建設(shè)成本。同時(shí),立體車庫(kù)能保證他人和汽車的安全。如果在車庫(kù)有任何人活動(dòng)或汽車沒有完全停止,電氣設(shè)備的控制系統(tǒng)將無法正常運(yùn)行。這意味著,在規(guī)模的機(jī)械車庫(kù)管理時(shí)可實(shí)現(xiàn)人車分離,這使得立體車庫(kù)更自動(dòng)化,特別是對(duì)于地下車庫(kù)。安裝這種車庫(kù)的地下停車場(chǎng)將省去大面積的照明系統(tǒng),因此它的出現(xiàn)可以節(jié)約大量的能源并可以保護(hù)周邊的環(huán)境免遭破壞。Ⅰ.立體車庫(kù)的背景分類與實(shí)現(xiàn)A.立體車庫(kù)的分類根據(jù)現(xiàn)在立體車庫(kù)的發(fā)展,可將它分為巷道堆垛式立體車庫(kù),垂直升降式立體車庫(kù),垂直循環(huán)式式立體車庫(kù),圓形水平循環(huán)式立體車庫(kù)等。立體車庫(kù)的概念是從自動(dòng)化的物料傳送系統(tǒng)演變而來。 [3]立體車庫(kù)的使用目的是為了解決停車難的問題,尤其在發(fā)達(dá)的城市中,這是為了使有限的區(qū)域內(nèi)停放更多的車輛,以節(jié)省發(fā)達(dá)城市的土地資源的靜態(tài)交通管理系統(tǒng)。本文提出了一個(gè)簡(jiǎn)單的方式來設(shè)計(jì)基于歐姆龍可編程序控制器 CP1H的立體升降車庫(kù),這可以擴(kuò)展到解決相關(guān)項(xiàng)目的立體車庫(kù)設(shè)計(jì)難題。B.簡(jiǎn)要介紹了升降橫移立體車庫(kù)模塊化設(shè)計(jì)在進(jìn)口的升降橫動(dòng)立體車庫(kù)設(shè)計(jì)中是很重要的。它可以設(shè)計(jì)為兩到五層或半地下型車庫(kù),車位的數(shù)目可以從幾十到幾百個(gè)。這種車庫(kù)合適于地上和地下建造車庫(kù)的特點(diǎn),它的優(yōu)點(diǎn)可概括為占用土地少,操作簡(jiǎn)單,結(jié)構(gòu)配置靈活,建設(shè)成本更低,裝飾防火和建設(shè)周期短,安全方便存儲(chǔ)汽車;使操作更為順暢,降低運(yùn)行時(shí)的噪音。 [4]這也是適用于商業(yè),辦公室和住宅的使用。立體車庫(kù)的安全設(shè)備主要是光電傳感器,限制位移保護(hù)和緊急開關(guān)等。C.整個(gè)系統(tǒng)的框架由圖 l表示,除了中央控制器 PLC,立體車庫(kù)系統(tǒng)還可以被分為三個(gè)部分:一,機(jī)械系統(tǒng),它包括柱,梁,承載板,車架,吊鉤等。二,電動(dòng)系統(tǒng),這部分是本文的核心,它控制整個(gè)系統(tǒng)的正常運(yùn)作。三, 觸摸面板,它是用戶和系統(tǒng)交換消息的設(shè)備,用戶不僅操作該系統(tǒng),還可以在故障的情況下讓操作員輸入命令或進(jìn)入調(diào)試模式。圖 1。系統(tǒng)的結(jié)構(gòu) 圖 2。 觸摸屏(自動(dòng)運(yùn)行和手動(dòng))?該系統(tǒng)的主要硬件我們主要使用歐姆龍可編程序控制器 CPH1,在考慮控制要求和硬件成本的問題上,我們采用 CP1H-X40DR-A PLC的編程方法可使用梯形圖或 ST指令列表。指令的長(zhǎng)度是 1到 7的步驟指令,每個(gè) I/O繼電器有 1600個(gè)端口,使用 USB 1.1接口進(jìn)行通信。顯示部分,我們使用屏幕型號(hào)是 WEINVIEWMT6056i系列型號(hào),屏幕材質(zhì)為 TFT,尺寸大小為 5.6英寸,使用 USB2.0端口,屏幕支持的分辨率為 320X234,下載程序的 CPU的頻率是 400 MHz,運(yùn)行內(nèi)存為 128RAM。D.該系統(tǒng)的結(jié)構(gòu)和功能機(jī)械零件中與電氣系統(tǒng)合作的是承載板、掛鉤和鏈條。各層上除了 7層以外有六個(gè)插槽,一共有 37個(gè)插槽、在每一個(gè)階層上都有一個(gè)空的位置的目的是擁有足夠的空間來使裝載板移動(dòng)。承載板的一層設(shè)計(jì)用來來回移動(dòng),同樣頂樓承載板也應(yīng)該僅用來提升。另一個(gè)承載板在這些樓層中是為了提升和橫移。通過這種方式,該系統(tǒng)可以實(shí)現(xiàn)節(jié)約和降低其中 6層中的任何空位。此外,該系統(tǒng)還具有的觸摸屏系統(tǒng),其中系統(tǒng)還可以在自動(dòng)運(yùn)行和手動(dòng)調(diào)試模式之間切換。在自動(dòng)運(yùn)行模式下,它可以讓用戶選擇某個(gè)位置的停車位完成保存的行為,同時(shí)還可以監(jiān)測(cè)系統(tǒng)的運(yùn)行。 (系統(tǒng)顯示綠字“系統(tǒng)運(yùn)行” ,表示系統(tǒng)在自動(dòng)模式下無故障,可正常運(yùn)行) 。當(dāng)系統(tǒng)發(fā)生故障時(shí),系統(tǒng)檢測(cè)后并在屏幕上顯示為閃爍的黃色和故障代碼,用紅色背景,借助故障代碼,專業(yè)的操作員可以識(shí)別故障代碼并及時(shí)準(zhǔn)確地消除故障。上述考慮情況現(xiàn)在越來越多的部門在手動(dòng)調(diào)試的模式進(jìn)行停車,以排除非專業(yè)人士進(jìn)入該模式的機(jī)會(huì),所以在此之前,輸入模式并有一個(gè)密碼驗(yàn)證,該序密碼可以由自己設(shè)定。這將保護(hù)系統(tǒng)免受潛在的危險(xiǎn),方便維修人員維修。圖 2是曲線圖,系統(tǒng)自動(dòng)運(yùn)行和手動(dòng)調(diào)試。II.對(duì)電氣系統(tǒng)的分類強(qiáng)電系統(tǒng)高效的動(dòng)力系統(tǒng)包括電源系統(tǒng),保護(hù)系統(tǒng)和驅(qū)動(dòng)機(jī)制,這就是電機(jī)。安裝 XJ3-D對(duì)早期的電源配線,可以用來保護(hù)的三相的相序電壓,使保證電機(jī)的右旋轉(zhuǎn)。此外,這也使每些層上使用的電動(dòng)機(jī)擁有相同的三相電壓。電機(jī)的布置在第一層上有 6個(gè)橫動(dòng)電機(jī),在 2到 5層有 6個(gè)橫動(dòng)電機(jī),因此在 2到 5層有起重電機(jī),頂層部分只有 7臺(tái)起重電機(jī)。布置完成后,對(duì)每個(gè)電機(jī)進(jìn)行標(biāo)記。例如,電動(dòng)機(jī)在第二層的第三個(gè)時(shí)隙時(shí),我們把它標(biāo)記為“23” ,電機(jī)前的繼電器命名 KM23。在此系列連接所有的電動(dòng)機(jī)都進(jìn)行熱保護(hù),任何電機(jī)的問題都會(huì)導(dǎo)致系統(tǒng)出現(xiàn)問題。在這運(yùn)行方式下,它具有的系統(tǒng)穩(wěn)定性并沒有受影響,但這也可以使整個(gè)系統(tǒng)的建造成本大大降低了。同時(shí),維修人員可以更容易地找到問題。 (我們需要做的是將每個(gè)熱保護(hù)開關(guān)一個(gè)一個(gè)地連接) 。弱電系統(tǒng)弱電系統(tǒng)也就是控制系統(tǒng),主要包括 PLC模塊和 5個(gè)擴(kuò)展模塊和傳感器模塊。如下圖所示,右邊是輸入部分,電壓為直流 24V,在左側(cè)為輸出部分,電壓為交流 220V,并把他們連接起來。 這些設(shè)備的控制要求與整個(gè)系統(tǒng)的功能有密切的關(guān)系。在上述的曲線圖中,上述的保護(hù)設(shè)備安裝緊急開關(guān),旁邊觸摸面板安裝有緊急觸發(fā)裝置,按下后系統(tǒng)將迅速停止。正面和背面安裝有光電傳感器,這是用于檢測(cè)人或不明物體闖入自動(dòng)車庫(kù)系統(tǒng),如果發(fā)生這種情況時(shí),系統(tǒng)將會(huì)停止然后響應(yīng)光電響應(yīng)失敗,我們的目標(biāo)是保護(hù)人和車輛的安全。相序保護(hù)器的作用是在電機(jī)卡死或正常啟動(dòng)之前過電流保護(hù),它并于邊緣交換機(jī)系列連接,主電源短路時(shí)承載板超過極限位置時(shí),系統(tǒng)將切斷主要電源。限位開關(guān),包括向上的限位開關(guān)和向下的限位開關(guān)或左右限位開關(guān)。為了更好的實(shí)現(xiàn)控制要求,水平限位開關(guān)都安裝在每個(gè)車位時(shí)隙的兩側(cè),而垂直極限開關(guān)安裝在附加的電機(jī)鏈上。有必要指出的是,第一層只安裝下和左右的限位開關(guān),頂端層只安裝開關(guān),這些開關(guān)能感覺到的車位板的位置,幫助完成解除車的位置控制。鉤位置傳感器是確定車輛和插槽是否有無空間的裝置。輸出點(diǎn)“00 04 05 06 07”的選擇的不同,對(duì)應(yīng)每個(gè)層的不同的相位,所以它也控制的電動(dòng)機(jī)的旋轉(zhuǎn)方向的操作或取消。圖 3。 PLC 模塊(分部)還有其他的 4個(gè)擴(kuò)展模塊,可使系統(tǒng)擁有更多的 I / O端口,圖為 PLC主要部分。III. 操作步驟A.程序的運(yùn)行根據(jù)第一層特點(diǎn),它被設(shè)計(jì)為只做橫向移動(dòng)動(dòng)作,從而使空間上層的面板有空間向下方移動(dòng)。所以,其它層也是如此,這就是模塊化設(shè)計(jì)。當(dāng)詳細(xì)研究符合要求,升降機(jī)構(gòu)的運(yùn)行,將承載板運(yùn)行,完成保存和程序。在過程中,光電傳感器將是打開的,這情況在前文解釋。在圖 2A中,采取此條件,在這個(gè)時(shí)候“加載”燈將閃爍,直到采取過程結(jié)束為止。當(dāng)我們輸入“51”這個(gè)數(shù)值后,該系統(tǒng)將區(qū)分操作是否是通過 51插槽的掛鉤保留和捕獲程序。然后將該消息的狀態(tài)顯示在屏幕上,操作者可以通過屏幕信息確認(rèn)操作或取消操作。在確認(rèn)后,51 個(gè)承載板將等待下層承載板橫向運(yùn)行完成后再向下完成穿越移動(dòng)。此外,一個(gè)定時(shí)器被添加到本控制模塊,以排除水平限位開關(guān)的故障,導(dǎo)致穿越的移動(dòng)時(shí)間過長(zhǎng)的錯(cuò)誤。如果移動(dòng)的時(shí)間超過設(shè)定的時(shí)間后,系統(tǒng)將向操作員發(fā)出警告,并在屏幕上顯示“穿越移動(dòng)時(shí)間過長(zhǎng)” ,操作者可以通過屏幕檢查出失敗的原因,并可很快 修復(fù)。向上的限位開關(guān)是否被用來感測(cè)承載板是否停在他們的應(yīng)有的位子上。若液位開關(guān)無法完成正常檢測(cè),也許是一個(gè)承載板卡在兩層之間。只有做到上面所訴的內(nèi)容后才停止在正確的插槽,程序才會(huì)被被激活。一個(gè)定時(shí)器設(shè)置到起重控制裝置,具有相同的功能,作為定時(shí)器。電梯將該車輛運(yùn)送地,釋放鉤子,現(xiàn)在的光電信號(hào)關(guān)閉,并等待為業(yè)主車輛進(jìn)入。在車輛進(jìn)入車庫(kù)后和操作者的確認(rèn),等待該光電信號(hào)恢復(fù)后,回到其插槽的承載板向下的方式。圖 4。 拍攝和保存過程的流程圖B. 補(bǔ)償程序補(bǔ)償過程的基礎(chǔ)是采樣程序,所以他們是熟悉的,唯一的區(qū)別是掛鉤的應(yīng)用。IV.軟件編程和編程環(huán)境A.軟件編程環(huán)境以及編程語(yǔ)言在這個(gè)系統(tǒng)中,我們選擇了歐姆龍 CX-ONE 3.0編程軟件和 PLC 的硬件,使用的編程的語(yǔ)言是經(jīng)典梯形圖。 在考慮立體車庫(kù)跟具不同的用戶安裝在不同的條件和要求下進(jìn)行設(shè)計(jì),立體車庫(kù)的規(guī)模應(yīng)該是可以靈活進(jìn)行變化,例如不同的層或插槽。為了滿足用戶對(duì)不同尺度車庫(kù)的要求,該程序是模塊化的,只需要更改的 I / O端口的數(shù)目,在邏輯關(guān)系的梯形圖是固定。在這種設(shè)計(jì)方式中,它不僅與系統(tǒng)有高度相容性,也縮短相關(guān)設(shè)計(jì)的周期,使其變得更易于調(diào)試和維修。B.模塊化程序有條件轉(zhuǎn)移被廣泛用于在編程中;整個(gè)程序由不同的模塊組成的,在某些條件,程序跳轉(zhuǎn)到其它程序中。如前文所述,有一個(gè)載板做升降運(yùn)動(dòng)或或進(jìn)行穿越,在板的第一和最上面的一層。 這第五個(gè)條件可以控制所有上層槽的限位開關(guān)并將其關(guān)閉。 “穿越”被激活,然后程序?qū)?huì)進(jìn)行分析并操作,直到達(dá)到設(shè)定的條件,程序的跳躍。為解除一直與向下的運(yùn)動(dòng),所以程序有