立軸傳動風(fēng)力發(fā)電機總體設(shè)計畢業(yè)設(shè)計說明書
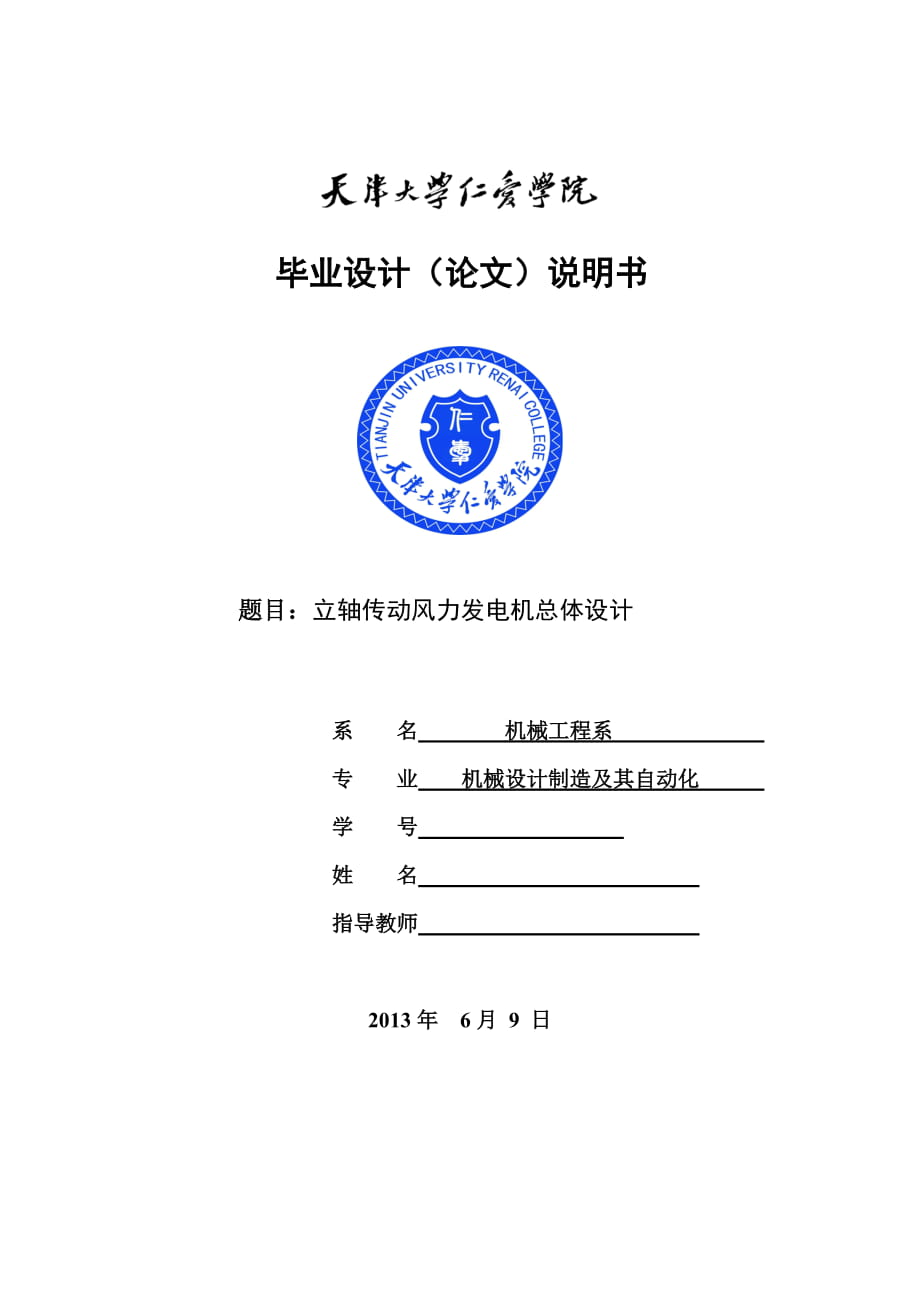


《立軸傳動風(fēng)力發(fā)電機總體設(shè)計畢業(yè)設(shè)計說明書》由會員分享,可在線閱讀,更多相關(guān)《立軸傳動風(fēng)力發(fā)電機總體設(shè)計畢業(yè)設(shè)計說明書(54頁珍藏版)》請在裝配圖網(wǎng)上搜索。
1、 畢業(yè)設(shè)計(論文)說明書 題目:立軸傳動風(fēng)力發(fā)電機總體設(shè)計 系 名 機械工程系 專 業(yè) 機械設(shè)計制造及其自動化 學(xué) 號 姓 名 指導(dǎo)教師 2013年 6月 9 日摘 要風(fēng)力發(fā)電是應(yīng)用前景十分廣闊的一種潔凈可再生能源,而目前大型風(fēng)力發(fā)電機的關(guān)鍵部件都放置于機艙內(nèi)。目前風(fēng)力發(fā)電機都需要定期進行維護,而大型風(fēng)力發(fā)電機高度都達到30米以上,所以在定期維護是就需要耗費大量的人力和財力。本人運用所學(xué)的基礎(chǔ)知識和專業(yè)知識,從設(shè)備可靠性、強度出發(fā)進行了設(shè)備的機構(gòu)和結(jié)構(gòu)的全新設(shè)計,為了提高風(fēng)力發(fā)電機的經(jīng)濟性,根據(jù)課題組提供的參數(shù),采用CAD優(yōu)化設(shè)計,排定最佳傳動方案,選擇穩(wěn)定可靠的構(gòu)件和具有良好力學(xué)特性以及在環(huán)
2、境極端溫差下仍然保持穩(wěn)定的結(jié)構(gòu)。根據(jù)原始數(shù)據(jù):傳動軸輸出端的額定轉(zhuǎn)速為100r/min左右,額定承載功率為600kW,切入風(fēng)速為5級清風(fēng),風(fēng)速為10m/s,原始輸入端轉(zhuǎn)速為50r/min,風(fēng)輪葉片數(shù)為3,葉片直徑為50m,輪轂高度為30m。為了使維護成本降低將主要傳動設(shè)備轉(zhuǎn)移至地面,通過立軸傳動將動能從風(fēng)機輸入轉(zhuǎn)移至地面設(shè)備輸入端,從而完成設(shè)計目的,并完成相關(guān)動力學(xué)和運動學(xué)計算。關(guān)鍵字:風(fēng)力發(fā)電機;齒輪傳動;立軸傳動ABSTRACT Wind power is a very broad application prospects of a clean renewable energy, and
3、 the key components of large wind turbines are placed in the cabin. Wind turbine require regular maintenance, large wind turbines have reached more than 30 meters height, so regular maintenance requires a lot of human and financial resources. I apply the basic knowledge and expertise, starting from
4、equipment reliability, strength of the institutions and structures of the new design, in order to improve the economics of wind turbines, based on the parameters provided by the Task Force, the optimal design using CAD, scheduled the optimum transmission program, choose a stable and reliable compone
5、nts and has good mechanical properties and ambient extreme temperature remains stable structure.Based on the original data: the rated speed of the drive shaft output of about 100r/min rated load power of 600kW,Cut-in speed of 5 breeze, wind speed of 10m / s, speed 50r/min primary inputs,Wind turbine
6、 blades is 3, a rotor diameter of 50m, 30m hub height. The main transmission equipment to the ground, through the vertical shaft drive fan input kinetic energy transferred to ground equipment input terminal so as to complete the design purposes and to complete the relevant dynamics and kinematics ca
7、lculation in order to reduce maintenance costs.Keywords Wind turbines ;Vertical shaft drive目 錄 第一章 軸(一)的強度校核1 1.1 初步估算軸徑1 1.2 軸上受力分析1 1.3 求支反力1 1.4 作彎矩和轉(zhuǎn)矩圖2 1.5 軸的強度校核3 第二章 花鍵的校核4 2.1 初始數(shù)據(jù)4 2.2 接觸應(yīng)力計算4 2.3 齒根抗彎強度計算4 2.4 齒根抗剪強度計算4 2.5 齒面耐磨損能力計算5 第三章 斜齒圓柱齒輪設(shè)計計算6 3.1 選材料確定試驗齒輪的疲勞極限應(yīng)力6 3.2 按接觸強度初步確定中心距并
8、初選主要參數(shù)6 3.3 校核齒面接觸疲勞強度6 3.4 校核齒根彎曲疲勞強度8 3.5 主要幾何參數(shù)9 第四章 直齒錐齒輪設(shè)計計算10 4.1 初步設(shè)計10 4.2 幾何計算10 4.3 齒面接觸疲勞強度校核11 4.4 齒根抗彎疲勞強度校核12 第五章 軸(二)的強度校核14 5.1 初步估算軸徑14 5.2 軸上受力分析14 5.3 求支反力14 5.4 作彎矩和轉(zhuǎn)矩圖15 5.5 最大合成彎矩15 5.6 作轉(zhuǎn)矩圖15 5.7 軸的強度校核16 第六章 軸(三)的強度校核18 6.1 初步估算軸徑18 6.2 軸上受力分析18 6.3 求支反力18 6.4 作彎矩和轉(zhuǎn)矩圖19 6.5 最
9、大合成彎矩19 6.6 作轉(zhuǎn)矩圖19 6.7 軸的強度校核19 參考文獻21 外文翻譯22 中文譯文34 致謝436第一章 軸(一)的強度校核1.1 初步估算軸徑 選擇軸的材料為40Cr。調(diào)質(zhì)處理,由表19.1.1查得材料力學(xué)性能數(shù)據(jù)位: 根據(jù)表19.3-1公式初步計算軸徑,由于材料為40Cr 1.2 軸上受力分析1.2.1 齒輪的圓周力 1.3 求支反力1.3.1 在水平面內(nèi)的支反力1.3.2 在垂直面內(nèi)的支反力 1.4 作彎矩和轉(zhuǎn)矩圖1.4.1 齒輪作用在水平平面的彎矩圖 1.4.2 齒輪作用在垂直平面的彎矩圖 1.4.3 作轉(zhuǎn)矩圖 T=57294N.m 圖1-11.5 軸的強度校核1.5
10、.1 確定危險截面 根據(jù)圖1.1由于C處合成彎矩最大 所以選擇C面為危險截面。1.5.2 安全系數(shù)校核計算 式中W為抗彎斷面系數(shù),由表19.3-1查得 根據(jù)式(19.3-2) 切應(yīng)力幅為 根據(jù)式(19.3-3) 第2章 花鍵的校核2.1 初始數(shù)據(jù) 花鍵規(guī)格14x176f7x200a11x25d10 P=600KW n=100r/min 表面硬度5864HRC 2.2 接觸應(yīng)力計算 2.3 齒根抗彎強度計算 2.3.1 齒根彎曲應(yīng)力 2.3.2 齒根許用彎曲應(yīng)力 2.4 齒根抗剪強度計算2.4.1 齒根最大剪切應(yīng)力 2.4.2 許用切應(yīng)力 2.5 齒面耐磨損能力計算2.5.1 花鍵副在循環(huán)數(shù)下工
11、作時耐磨損能力計算 2.5.2 花鍵副在長期工作無磨損是耐磨損能力計算 2.5.3 外花鍵的抗扭與抗彎強度計算 第3章 斜齒圓柱齒輪設(shè)計計算3.1 選材料 確定試驗齒輪的疲勞極限應(yīng)力 40Cr 調(diào)質(zhì)處理 硬度217255HBS 由表16.2-59,60,65查得 3.2 按接觸強度初步確定中心距并初選主要參數(shù) 3.3 校核齒面接觸疲勞強度 根據(jù)齒輪的圓周速度參考表16.2-73選擇齒輪的精度等級為8級精度 首先計算當(dāng)量齒數(shù)3.4 校核齒根彎曲疲勞強度 3.5 主要幾何參數(shù) 第4章 直齒錐齒輪設(shè)計計算4.1 初步設(shè)計 4.2 幾何計算 4.3 齒面接觸疲勞強度校核 4.4 齒根抗彎疲勞強度校核
12、第5章 軸(二)的強度校核5.1 初步估算軸徑選擇軸的材料為45號鋼調(diào)制處理,由表19.1.1查得材料力學(xué)性能數(shù)據(jù)為 根據(jù)表19.3-1公式初步估算軸徑,由于材料為45號鋼由表19.3-2選取=405.2 軸上受力分析(如圖5-1) 5.3 求支反力5.3.1 在水平面內(nèi)的支反力 5.3.2 在垂直平面內(nèi)的支反力 5.4 作彎矩圖和轉(zhuǎn)矩圖5.4.1 水平面彎矩 5.4.2 垂直平面彎矩 5. 5 最大合成彎矩5.5.1 A處最大合成彎矩5.5.2 B處最大合成彎矩 5.6 作扭矩圖 T=57294N/m圖5-15.7 軸的強度校核5.7.1 確定危險截面 根據(jù)圖5-1得A處受彎矩最大,并且軸徑
13、最小,所以選擇截面A處為危險截面。5.7.2 安全系數(shù)校核計算 式中W為抗彎斷面系數(shù),由表19.3-15查得 由于是對稱循環(huán)應(yīng)力,故平均應(yīng)力=0 根據(jù)式(19.3-2) 根據(jù)式(19.3-3)得 第6章 軸(三)的強度校核6.1 初步估算軸徑 選擇軸的材料為40Cr。調(diào)質(zhì)處理,由表19.1.1查得材料力學(xué)性能數(shù)據(jù)位: 根據(jù)表19.3-1公式初步計算軸徑,由于材料為40Cr 6.2 軸上受力分析(如圖6-1)6.2.1 齒輪的圓周力 6.3 求支反力6.3.1 在水平面內(nèi)的支反力 6.3.2 在垂直面內(nèi)的支反力 6.4 作彎矩和轉(zhuǎn)矩圖6.4.1 齒輪作用在水平面的彎矩圖 6.4.2 齒輪作用在垂
14、直平面的彎矩圖 6.5 作最大合成彎矩圖 6.6 作轉(zhuǎn)矩圖T=57294N/m圖6-16.7 軸的強度校核6.7.1 確定危險截面由于C截面處合成彎矩最大,所以選擇截面C處為危險截面。6.7.2 安全系數(shù)校核計算 由于是對稱循環(huán)彎曲應(yīng)力,故平均應(yīng)力根據(jù)式(19.3-2) 根據(jù)式(19.3-3) 參考文獻1 包耳.風(fēng)力發(fā)電技術(shù)發(fā)展現(xiàn)狀J.可再生能源雜志,2004,(2):1215.2 GWEC.Global wind 2005 report,2006.3 Sawin,Janet,Langhlin.Wind power in the United StatesD. Doctors thesis,
15、The Fletcher School of Law and Diplomacy.2001:500513.4 Kramer,Marcel.Long-term costs of electricity generation in GermanyM.Wind Engineering, Multi-Science Publishing Co. Ltd, 2004, 4(28): 465478.5 劉忠明,王長路,段守敏.風(fēng)力發(fā)電齒輪箱設(shè)計制造技術(shù)的發(fā)展和展望J. 機械傳動.2006,6(30): 16.6 濮良貴,紀名剛機械設(shè)計第版北京:高等教育出版社,20057 ANSI/AGMA 6006-A0
16、3. AGMA. 2003.8 ISO 81400-4:2005. Wind Turbines - Part 4:Design and Specification of Gearbox. 2004.9 龔淮義,羅圣國,李平林,張立乃,黃少顏.機械設(shè)計課程設(shè)計指導(dǎo)書(第二 版).北京:高等教育出版社,1990.4(2006重?。?0 湯克平.風(fēng)電增速箱結(jié)構(gòu)設(shè)計敘談J.機械傳動,2004, 28(5):1-3.11 機械設(shè)計手冊(新編軟件版)2008.化學(xué)工業(yè)出版社12 劉鴻文主編.材料力學(xué)(I、II).北京:高等教育出版社,2004.113 何貢互換性與測量技術(shù)中國計量出版社,200014 高金
17、蓮工程圖學(xué)第版北京:機械工業(yè)出版社,200515 王先逵機械加工工藝手冊第版北京:機械工業(yè)出版社,200716 湯克平.風(fēng)電增速箱結(jié)構(gòu)設(shè)計敘談. 機械傳動,2004,28(5):333417 武楊名.風(fēng)力發(fā)電齒輪箱國產(chǎn)化的材料、工藝和結(jié)構(gòu)研究:學(xué)位論文,杭 州:浙江大學(xué),200118 朱才朝,黃琪,唐倩.風(fēng)力發(fā)電升速齒輪箱傳動系統(tǒng)接觸齒數(shù)及載荷分配. 農(nóng)業(yè)機械學(xué)報,2006(7):878919 佘勃強.風(fēng)力發(fā)電增速裝置的研究:學(xué)位論文,西安:西安理工大學(xué),200820 張展.風(fēng)力發(fā)電傳動裝置的設(shè)計與制造.通用機械,2007(4):313421 饒振剛.行星齒輪傳動設(shè)計M.北京:化學(xué)工業(yè)出版社,
18、2003.22 張展.風(fēng)力發(fā)電機組的傳動裝置J.傳動技術(shù).2003, 6: 35-36.23 會田俊夫主編,張展譯.齒輪的精度與性能M.北京:中國農(nóng)業(yè)機械出版社, 1985.外文資料DESIGN AND DEVELOPMENT OF A 1/3 SCALE VERTICALAXIS WIND TURBINE FOR ELECTRICAL POWERGAbstract: This research describes the electrical power generation in Malaysia by the measurement of wind velocity acting on
19、the wind turbine technology. The primary purpose of the measurement over the 1/3 scaled prototype vertical axis wind turbine for the wind velocity is to predict the performance of full scaled H-type vertical axis wind turbine. The electrical power produced by the wind turbine is influenced by its tw
20、o major part, wind power and belt power transmission system. The blade and the drag area system are used to determine the powers of the wind that can be converted into electric power as well as the belt power transmission system. In this study both wind power and belt power transmission system has b
21、een considered. A set of blade and drag devices have been designed for the 1/3 scaled wind turbine at the Thermal Laboratory of Faculty of Engineering, Universiti Industri Selangor (UNISEL). Test has been carried out on the wind turbine with the different wind velocities of 5.89 m/s, 6.08 m/s and 7.
22、02 m/s. From the experiment, the wind power has been calculated as 132.19 W, 145.40 W and 223.80W.The maximum wind power is considered in the present study.Keywords: Belt power transmission system; Reynolds number; wind power; wind turbine INTRODUCTION Wind energy is the kinetic energy associated wi
23、th the movement of atmospheric air. It has been used for hundreds of years for sailing, grinding grain, and for irrigation. Wind energy systems convert this kinetic energy to more useful forms of power. Wind energy systems for irrigation and milling have been in use since ancient times and since the
24、 beginning of the 20th century, it is being used to generate electric power. Windmills for water pumping have been installed in many countries particularly in the rural areas.Wind turbine is a machine that converts the winds kinetic energy into rotary mechanical energy, which is then used to do work
25、. In more advanced models, the rotational energy is converted into electricity, the most versatile form of energy, by using a generator (Fitzwater et al., 1996). For thousands of years people have used windmills to pump water or grind grain. Even into the twentieth century tall, slender, multi-vaned
26、 wind turbines made entirely of metal were used in American homes and ranches to pump water into the houses plumbing system or into the cattles watering trough. After World War I, work was begun to develop wind turbines that could produce electricity. Marcellus Jacobs invented a prototype in 1927 th
27、at could provide power for a radio and a few lamps but little else. When demand for electricity increased later, Jacobss small inadequate wind turbines fell out of use. The first large-scale wind turbine built in the United States was conceived by Palmer Cosslett Putnam in 1934; he completed it in 1
28、941. The machine was huge. The tower was 36.6 yards (33.5 meters) high, and its two stainless steel blades had diameters of 58 yards (53 meters). Putnams wind turbine could produce 1,250 kilowatts of electricity, or enough to meet the needs of a small town (Monett et al., 1994). It was, however, aba
29、ndoned in 1945 because of mechanical failure. With the 1970s oil embargo, the United States began once more to consider the feasibility of producing cheap electricity from wind turbines. In 1975 the prototype Mod-O was in operation. This was a 100 kilowatt turbine with two 21-yard (19-meter) blades.
30、 More prototypes followed (Mod-OA, Mod-1, Mod-2, etc.), each larger and more powerful than the one before.Currently, the United States Department of Energy is aiming to go beyond 3,200 kilowatts per machine. Many different models of wind turbines exist, the most striking being the vertical-axis Darr
31、ieus, which is shaped like an egg beater (Fitzwater et al., 1996). The model most supported by commercial manufacturers, however, is a horizontal-axis turbine, with a capacity of around 100 kilowatts and three blades not more than 33 yards (30 meters) in length. Wind turbines with three blades spin
32、more smoothly and are easier to balance than those with two blades. Also,while larger wind turbines produce more energy, the smaller models are less likely to undergo major mechanical failure, and thus are more economical to maintain. Wind farms have sprung up all over the United States, most notabl
33、y in California. Wind farms are huge arrays of wind turbines set in areas of favorable wind production. A great number of interconnected wind turbines are necessary in order to produce enough electricity to meet the needs of a sizable population. Currently, 17,000 wind turbines on wind farms owned b
34、y several wind energy companies produce 3.7 billion kilowatt-hours of electricity annually, enough to meet the energy needs of 500,000 homes. A wind turbine consists of three basic parts: the tower, the nacelle, and the rotor blades. The tower is either a steel lattice tower similar to electrical to
35、wers or a steel tubular tower with an inside ladder to the nacelle. The first step in constructing a wind turbine is erecting the tower. Although the towers steel parts are manufactured off site in a factory, they are usually assembled on site. The parts are bolted together before erection, and the
36、tower is kept horizontal until placement. A crane lifts the tower into position, all bolts are tightened, and stability is tested upon completion. Next, the fiberglass nacelle is installed. Its inner workings main drive shaft, gearbox, and blade pitch and yaw controls are assembled mounted onto a ba
37、se frame at a factory (Hammons, 2004). The nacelle is then bolted around the equipment. At the site, the nacelle is lifted onto the completed tower and bolted into place. In addition, the aerodynamics of a wind turbine at the rotor surface is very much important in aerodynamic fields. The rotor axis
38、 is brought to a vertical orientation with a wind vane mounted on a control shaft to orientate the blades with changing wind direction. Using pitch regulation the rotor blades turn around their axis so that the aerodynamic characteristics of the blade and rotor are controlled. The rotor is yaw out o
39、f the wind which turns the rotor plane to follow the changing wind direction. The hub is connected to the rotor with rigid bolt connection and the rotational speed of the rotor is fixed relative to the frequency of the grid. The future can only get better for wind turbines. The potential for wind en
40、ergy is largely untapped. The total amount of electricity that could potentially be generated from wind in the United States has been estimated at 10,777 billion kWh annually (Keith, 2005). These new wind farms demonstrate how wind energy can help to meet the nations growing need for affordable, rel
41、iable power. With continued government encouragement to accelerate its development, this increasingly competitive source of renewable energy will provide at least six percent of the nations electricity by 2020. Research is now being done to increase the knowledge of wind resources. This involves the
42、 testing of more and more areas for the possibility of placing wind farms where the wind is available and strong. Plans are in effect to increase the life span of the machine from five years to 20 to 30 years, improve the efficiency of the blades, provide better controls, develop drive trains that l
43、ast longer, and allow for better surge protection and grounding. The United States Department of Energy has recently set up a schedule to implement the latest research in order to build wind turbines with a higher efficiency rating than is now possible (the efficiency of an ideal wind turbine is 59.
44、3 percent (Milligan & Artig, 1999). That is, 59.3 percent of the winds energy can be captured. Turbines in actual use are about 30 percent efficient). The United States Department of Energy has also contracted three corporations to investigate ways to reduce mechanical failure. This project began in
45、 the spring of 1992 and will extend to the end of the century. Wind turbines will become more prevalent in upcoming years. The turn of the century should see wind turbines that are properly placed, efficient, durable, and numerous. From the investigation of this wind turbine background, an H-type, v
46、ertical axis wind turbine has been designed and built in thermal Laboratory Universiti Industri Selangor that has the capability to self-start. In addition, this turbine has been designed to allow a variety of modifications such as blade profile and pitching to be tested. The first part of the desig
47、n process, which included research, brainstorming, engineering analysis, turbine design selection, and prototype testing have been incorporated. Using data obtained through proper investigation results, the final full-scale turbine has been designed and built. Wind turbines can be separated into two
48、 types based by the axis in which the turbine rotates namely horizontal axis wind turbine (HAWT) and the vertical axis wind turbine (VAWT). HAWT has difficulty operating in near ground, turbulent winds because their yaw and blade bearing need smoother, more laminar wind flows, difficult to install n
49、eeding very tall and expensive cranes and skilled operators, downwind variants suffer from fatigue and structural failure caused by the turbulence and height can be a safety hazard for low-altitude aircraft. Other than that, the aerodynamics of a horizontal-axis wind turbine is complex. The air flow
50、 at the blades is not the same as the airflow far away from the turbine. The very nature of the way in which energy is extracted from the air also causes air to be deflected by the turbine. In addition, the aerodynamics of a wind turbine at the rotor surface includes effects that are rarely seen in
51、other aerodynamic fields. A wide variety of VAWT configurations have been proposed. The Darrieus vertical type wind turbine is the most common and us used extensively for power generation. However, the Darrieus turbine suffered from structural problems as well as a poor energy market. To improve the
52、 performance of a wind turbine, this study has been concentrated on design and built an 1/3 scale H-type, vertical axis wind turbine that has the capability to self-start due to the wind flow and efficient performance of the VAWT that could lead to a change in the standard thinking of how wind energ
53、y is harnessed, and may spur future VAWT design and research. The study on the enhanced performance of the wind turbine is also given by incorporating drag devices. WIND TURBINE DESIGN Theoretical analysis The belt drive system consists of several parts of the belt drive calculation and the VType be
54、lt is considered in this study. Thus the main calculation that has been done at this system are angle of wrap for small and large pulley, belt length, pulley speed, the tension ratio and the power transmitted by the belt. The structure of the V-belt is shown in Fig. 1, which illustrates the main parts in V-belt such as the large pulley diameter indicated by the number 3 and the small pulley by the number 2 and the angle of wrap of large pulley indicated by 3 and small pulley by 2. C indicates the centered radius between large and small pulleys. Angle of wrap for
- 溫馨提示:
1: 本站所有資源如無特殊說明,都需要本地電腦安裝OFFICE2007和PDF閱讀器。圖紙軟件為CAD,CAXA,PROE,UG,SolidWorks等.壓縮文件請下載最新的WinRAR軟件解壓。
2: 本站的文檔不包含任何第三方提供的附件圖紙等,如果需要附件,請聯(lián)系上傳者。文件的所有權(quán)益歸上傳用戶所有。
3.本站RAR壓縮包中若帶圖紙,網(wǎng)頁內(nèi)容里面會有圖紙預(yù)覽,若沒有圖紙預(yù)覽就沒有圖紙。
4. 未經(jīng)權(quán)益所有人同意不得將文件中的內(nèi)容挪作商業(yè)或盈利用途。
5. 裝配圖網(wǎng)僅提供信息存儲空間,僅對用戶上傳內(nèi)容的表現(xiàn)方式做保護處理,對用戶上傳分享的文檔內(nèi)容本身不做任何修改或編輯,并不能對任何下載內(nèi)容負責(zé)。
6. 下載文件中如有侵權(quán)或不適當(dāng)內(nèi)容,請與我們聯(lián)系,我們立即糾正。
7. 本站不保證下載資源的準確性、安全性和完整性, 同時也不承擔(dān)用戶因使用這些下載資源對自己和他人造成任何形式的傷害或損失。
最新文檔
- 四年級上冊火燒云_PPT
- 冀教版小學(xué)科學(xué)六年級上冊《鳥類動物的特征》課件
- 八年級生物上第三章-動物在生物圈中的作用
- 九年級科學(xué)物質(zhì)分類和利用
- 工時定額管理的現(xiàn)狀及問題解決方案
- 結(jié)直腸癌診治進展課件
- 《再塑生命的人》PPT課件
- 聚異戊二烯橡膠課件
- 橋梁結(jié)構(gòu)構(gòu)造圖剖析課件
- PCR的發(fā)明_原理及應(yīng)用1(精品)
- 八年級語文五柳先生傳1
- 方便面行業(yè)分析(1)
- 人教版五年級數(shù)學(xué)上冊練習(xí)二十一詳細答案課件(同名32)
- 車輛動力學(xué)模型課件
- 油井流入動態(tài)(IPR曲線)剖析課件