畢業(yè)設計CA6140數(shù)控車床進給伺服系統(tǒng)機械部分的設計
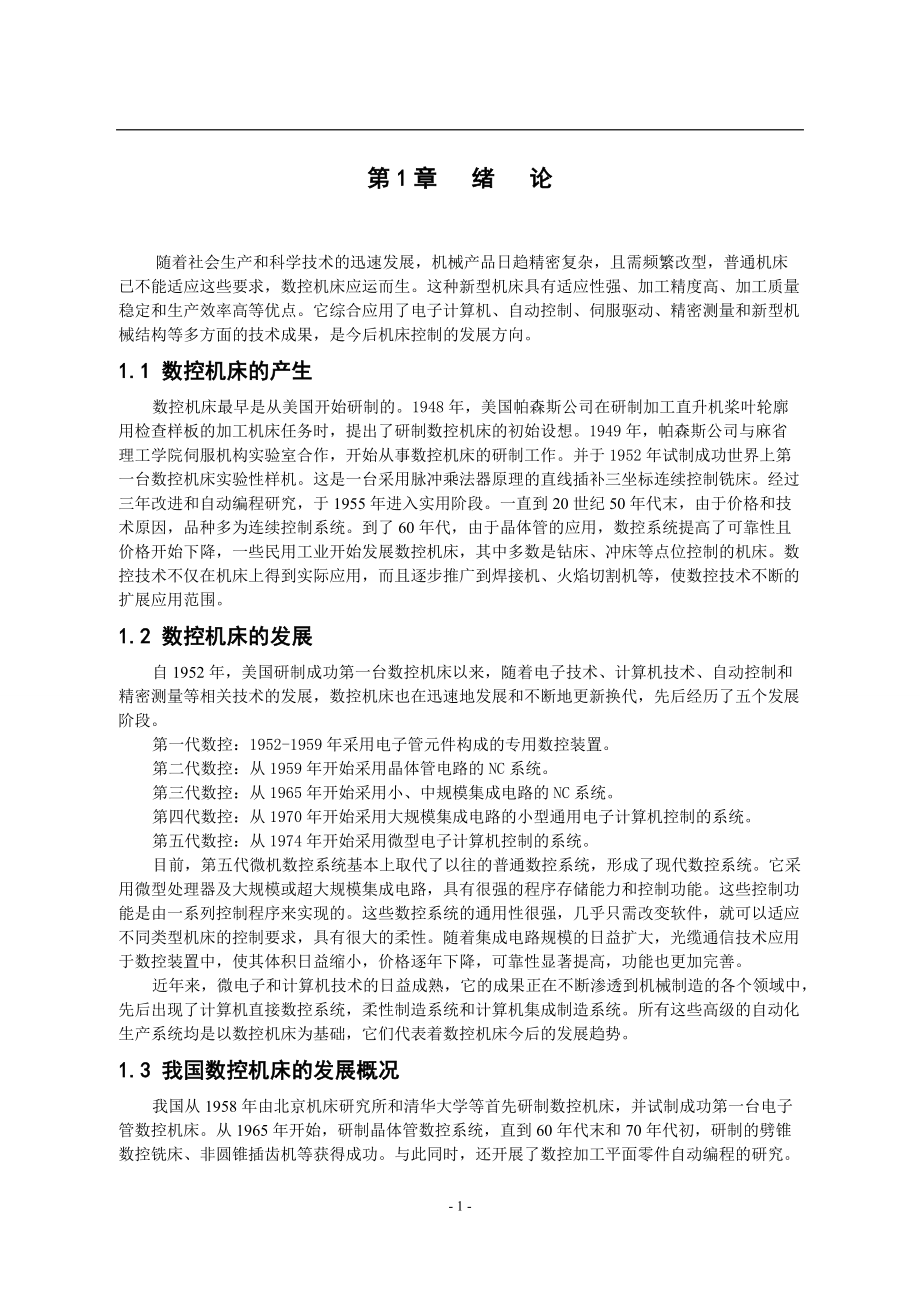


《畢業(yè)設計CA6140數(shù)控車床進給伺服系統(tǒng)機械部分的設計》由會員分享,可在線閱讀,更多相關《畢業(yè)設計CA6140數(shù)控車床進給伺服系統(tǒng)機械部分的設計(30頁珍藏版)》請在裝配圖網(wǎng)上搜索。
1、 第1章 緒 論 隨著社會生產(chǎn)和科學技術的迅速發(fā)展,機械產(chǎn)品日趨精密復雜,且需頻繁改型,普通機床已不能適應這些要求,數(shù)控機床應運而生。這種新型機床具有適應性強、加工精度高、加工質(zhì)量穩(wěn)定和生產(chǎn)效率高等優(yōu)點。它綜合應用了電子計算機、自動控制、伺服驅(qū)動、精密測量和新型機械結(jié)構等多方面的技術成果,是今后機床控制的發(fā)展方向。 1.1 數(shù)控機床的產(chǎn)生 數(shù)控機床最早是從美國開始研制的。1948年,美國帕森斯公司在研制加工直升機槳葉輪廓用檢查樣板的加工機床任務時,提出了研制數(shù)控機床的初始設想。1949年,帕森斯公司與麻省理工學院伺服機構實驗室合作,開始從事數(shù)控機床的研制工作。并于1
2、952年試制成功世界上第一臺數(shù)控機床實驗性樣機。這是一臺采用脈沖乘法器原理的直線插補三坐標連續(xù)控制銑床。經(jīng)過三年改進和自動編程研究,于1955年進入實用階段。一直到20世紀50年代末,由于價格和技術原因,品種多為連續(xù)控制系統(tǒng)。到了60年代,由于晶體管的應用,數(shù)控系統(tǒng)提高了可靠性且價格開始下降,一些民用工業(yè)開始發(fā)展數(shù)控機床,其中多數(shù)是鉆床、沖床等點位控制的機床。數(shù)控技術不僅在機床上得到實際應用,而且逐步推廣到焊接機、火焰切割機等,使數(shù)控技術不斷的擴展應用范圍。 1.2 數(shù)控機床的發(fā)展 自1952年,美國研制成功第一臺數(shù)控機床以來,隨著電子技術、計算機技術、自動控制和精密測量等相關技術的發(fā)展,
3、數(shù)控機床也在迅速地發(fā)展和不斷地更新?lián)Q代,先后經(jīng)歷了五個發(fā)展階段。 第一代數(shù)控:1952-1959年采用電子管元件構成的專用數(shù)控裝置。 第二代數(shù)控:從1959年開始采用晶體管電路的NC系統(tǒng)。 第三代數(shù)控:從1965年開始采用小、中規(guī)模集成電路的NC系統(tǒng)。 第四代數(shù)控:從1970年開始采用大規(guī)模集成電路的小型通用電子計算機控制的系統(tǒng)。 第五代數(shù)控:從1974年開始采用微型電子計算機控制的系統(tǒng)。 目前,第五代微機數(shù)控系統(tǒng)基本上取代了以往的普通數(shù)控系統(tǒng),形成了現(xiàn)代數(shù)控系統(tǒng)。它采用微型處理器及大規(guī)?;虺笠?guī)模集成電路,具有很強的程序存儲能力和控制功能。這些控制功能是由一系列控制程序來實現(xiàn)的。
4、這些數(shù)控系統(tǒng)的通用性很強,幾乎只需改變軟件,就可以適應不同類型機床的控制要求,具有很大的柔性。隨著集成電路規(guī)模的日益擴大,光纜通信技術應用于數(shù)控裝置中,使其體積日益縮小,價格逐年下降,可靠性顯著提高,功能也更加完善。 近年來,微電子和計算機技術的日益成熟,它的成果正在不斷滲透到機械制造的各個領域中,先后出現(xiàn)了計算機直接數(shù)控系統(tǒng),柔性制造系統(tǒng)和計算機集成制造系統(tǒng)。所有這些高級的自動化生產(chǎn)系統(tǒng)均是以數(shù)控機床為基礎,它們代表著數(shù)控機床今后的發(fā)展趨勢。 1.3 我國數(shù)控機床的發(fā)展概況 我國從1958年由北京機床研究所和清華大學等首先研制數(shù)控機床,并試制成功第一臺電子管數(shù)控機床。從1965年開始,
5、研制晶體管數(shù)控系統(tǒng),直到60年代末和70年代初,研制的劈錐數(shù)控銑床、非圓錐插齒機等獲得成功。與此同時,還開展了數(shù)控加工平面零件自動編程的研究。1972-1979年是數(shù)控機床的生產(chǎn)和使用階段。例如:清華大學研制成功集成電路數(shù)控系統(tǒng);數(shù)控技術在車、銑、鏜、磨、齒輪加工、電加工等領域開始研究與應用;數(shù)控加工中心機床研制成功;數(shù)控升降臺銑床和數(shù)控齒輪加工機床開始小批生產(chǎn)供應市場。從80年代初開始,隨著我國開放政策的實施,先后從日本、美國、德國等國家引進先進的數(shù)控技術。上海機床研究所引進美國GE公司的MTC-1數(shù)控系統(tǒng)等。在引進、消化、吸收國外先進技術基礎上,北京機床研究所又開發(fā)出BSO3經(jīng)濟型數(shù)控系統(tǒng)
6、和BSO4全功能數(shù)控系統(tǒng),航空航天部706所研制出MNC864數(shù)控系統(tǒng)等。進而推動了我國數(shù)控技術的發(fā)展,使我國數(shù)控機床在品種上、性能上以及水平上均有了新的飛躍。我國的數(shù)控機床已跨入一個新的發(fā)展階段。 1.4 數(shù)控機床的發(fā)展趨勢 從數(shù)控機床技術水平看,高精度、高速度、高柔性、多功能和高自動化是數(shù)控機床的重要發(fā)展趨勢。對單臺主機不僅要求提高其柔性和自動化程度,還要求具有進入更高層次的柔性制造系統(tǒng)和計算機集成制造系統(tǒng)的適應能力。 在數(shù)控系統(tǒng)方面,目前世界上幾個著名的數(shù)控裝置生產(chǎn)廠家,諸如日本的FANCU,德國的SIEMENS和美國的A-B公司,產(chǎn)品都向系列化、模塊化、高性能和成套性方向發(fā)展。它
7、們的數(shù)控系統(tǒng)都采用了16位和32位微機處理機、標準總線及軟件模塊和硬件模塊結(jié)構,內(nèi)存容量擴大到1MB以上,機床分辨率可達0.1微米,高速進給可達100m/min,控制軸數(shù)可達16個,并采用先進的電裝工藝。 在驅(qū)動系統(tǒng)方面,交流驅(qū)動系統(tǒng)發(fā)展迅速。交流傳動已由模擬式向數(shù)字式方向發(fā)展,以運算放大器等模擬器件為主的控制器正在被以微處理器為主的數(shù)字集成元件所取代,從而克服了零點漂移、溫度漂移等弱點。 1.5 數(shù)控機床進給系統(tǒng)改造的意義 進給運動是數(shù)字控制的直接對象,被加工工件的最終位置精度和輪廓精度都與進給運動的傳動精度、靈敏度和穩(wěn)定性有關。因此,在設計傳動結(jié)構,選用傳動零件時應充分注意減小摩
8、擦阻力,提高傳動精度和剛度,消除傳動間隙和減小運動慣量。 數(shù)控機床的進給運動采用無級調(diào)速的伺服驅(qū)動方式,伺服電機的動力和運動只需經(jīng)過由最多一兩級齒輪或帶輪傳動副和滾珠絲杠螺母副或齒輪齒條副或蝸桿蝸條副組成的傳動系統(tǒng)傳動給工作臺等運動執(zhí)行部件。傳動系統(tǒng)的齒輪副或帶輪副的作用主要是通過降速來匹配進給系統(tǒng)的慣量和獲得要求的輸出機械特性,對開環(huán)系統(tǒng),還起匹配所需的脈沖當量的作用。近年來,由于伺服電機及其控制單元性能的提高,許多數(shù)控機床的進給傳動系統(tǒng)去掉了降速齒輪副,直接將伺服電機與滾珠絲杠連接。滾珠絲杠螺母副或齒輪齒條副或蝸桿蝸條副的作用是實現(xiàn)旋轉(zhuǎn)到直線的運動形式的轉(zhuǎn)換。 一般的生
9、產(chǎn)企業(yè)或者工科類職業(yè)學校,一般都不乏普通機床,而這些普通機床,已經(jīng)滿足不了產(chǎn)品不斷改型或人才培養(yǎng)的需要,因此,對數(shù)控設備的需求就凸顯出來了,為了減小投資,充分利用現(xiàn)有的機床設備,可對普通機床進行改造,以下將針對CA6140車床的進給系統(tǒng),闡述將其改造成性能更好的數(shù)控車床。 第2章 CA6140車床進給伺服系統(tǒng)改造方案的擬訂 2.1總體方案確定 圖2-1 CA6140普通車床數(shù)控化改造示意圖 CA6140車床數(shù)控改造方案本文改造后的結(jié)構是一種非常典型臥式車床的數(shù)控改造結(jié)構,改造時拆除原機床的縱向和橫向絲杠光杠、溜板箱、掛輪箱的掛輪、原手動刀架及手柄等部件,用滾珠
10、絲杠替換原有普通絲杠、用電動刀架替換原有的普通刀架??v向和橫向進給采用步進電動機及減速器驅(qū)動,橫向步進電動機及減速器裝置安裝在機床床鞍的后部,縱向的步進電動機減速器裝置安裝在機床的右端。 由于被改裝的機床本身的機械結(jié)構不是按數(shù)控機床的要求設計的,其精度和剛度等性能指標往往不能滿足數(shù)控機床的要求,因此將普通機床改造為全功能的數(shù)控機床,一味追求先進指標則會得不償失,所以確定總體方案的原則應當是在滿足生產(chǎn)需要的前提下,對原機床盡可能減少機械部分的改動量,選擇簡單易用的數(shù)控系統(tǒng),達到合理的性價比。本次改造設計要求就是根據(jù)這一原則提出的。根據(jù)設計要求、依據(jù)設計參數(shù)及機床數(shù)控改造的理解,進給系統(tǒng)
11、總體方案確定如下: 利用微機對縱、橫向進給系統(tǒng)進行開環(huán)控制,驅(qū)動原件采用直流步進電機,傳動系統(tǒng)采用滾珠絲桿;步進電機一級齒輪減速后,帶動滾珠絲桿轉(zhuǎn)動,從而實現(xiàn)進給運動。示意圖如圖2-2所示: 圖2-2 進給系統(tǒng)設計總方案圖 2.2 CA6140車床的設計參數(shù) 根據(jù)型普通原始數(shù)據(jù)及數(shù)控改造設計要求,確定主要如表2-1所示: 表2-1 最大加工直徑 車床身上: 400mm 車床鞍上: 210mm 最大加工長度: 1000mm 快進速度 縱向 2.4m/min 橫向 1.2m/min 最大切削進給速度 縱向 0.6m/min 橫向 0.3m/mi
12、n 脈沖當量 縱向 0.01mm/step 橫向 0.005mm/step 脈沖分配方式 逐點比較法 控制坐標數(shù) 2 機床定位精度 0.015 溜板及刀架重力 縱向: 800N 橫向: 600N 自動生降速性能: 有 起動加速時間: 30ms 主電機功率: 7.5Kw 第3章 數(shù)控系統(tǒng)的選擇 3.1數(shù)控系統(tǒng)的選擇 3.1.1數(shù)控系統(tǒng)的選擇 數(shù)控機床的價格主要由數(shù)控系統(tǒng)來決定,數(shù)控系統(tǒng)從功能上可分為低中高三檔,中高檔系統(tǒng)(如Fanuc、LBNC—2T
13、型、FAGOR、SIEMENS、華中HNC—2T/2M等)功能齊全,性能優(yōu)良,但價格偏高。結(jié)合實際,從實用角度出發(fā),我選擇了華中HNC—21T型數(shù)控車床系統(tǒng),該系統(tǒng)采用先進的開放式體系結(jié)構,內(nèi)置嵌入式工業(yè)PC,配置7.5彩色液晶顯示屏和通用工程面板,集成進給軸接口、主軸接口、手持單元接口、內(nèi)嵌式PLC接口于一體,支持硬盤、電子盤等程序存儲方式及軟驅(qū)、DNC、以太網(wǎng)等程序交換功能,具有低價格、高性能、配置靈活、結(jié)構緊湊、易于使用可靠性高的特點,編程格式符合ISO國際代碼標準,兩軸動態(tài)坐標,具有自動加工、自動換刀、車螺紋和MDI等功能,是教學、生產(chǎn)兩用型的數(shù)控系統(tǒng)。 3.1.2改造部分 對臥式
14、車床進行數(shù)控化改造,主要是將縱向和橫向進給系統(tǒng)改造為用數(shù)控裝置控制的、能獨立運動的進給伺服系統(tǒng);刀架改造成為能自動換刀的回轉(zhuǎn)刀架。由于加工過程中的切削參數(shù)、切削次序和刀具都會按程序自動進行調(diào)節(jié)和更換,再加上縱向和橫向進給聯(lián)動的功能,數(shù)控改裝后的車床就可以加工出各種形狀復雜的回轉(zhuǎn)零件,并能實現(xiàn)多工序自動車削。 3.1.3設計要求 總體方案設計應考慮數(shù)控系統(tǒng)的運動方式、伺服系統(tǒng)的類型、數(shù)控系統(tǒng)的選擇,以及傳動方式和執(zhí)行機構的選擇等。在制定總體方案時,要滿足下列要求: 1)臥式車床數(shù)控化改造后應具有定位、縱向和橫向的直線插補、圓弧插補功能,還要求能暫停,進行循環(huán)加工和螺紋加工等,因此,數(shù)控系
15、統(tǒng)選擇連續(xù)控制系統(tǒng)。 2)車床數(shù)控化改裝后屬于經(jīng)濟型數(shù)控機床,在保證一定加工精度的前提下,應簡化結(jié)構,降低成本。因此,進給系統(tǒng)采用步進電動機開環(huán)控制系統(tǒng)。 3)在臥室車床最大加工尺寸、加工精度、控制速度,以及經(jīng)濟性等條件下,經(jīng)濟型數(shù)控車床一般采用經(jīng)濟型數(shù)控系統(tǒng)。 4)重新設計自動回轉(zhuǎn)刀架及其控制電路。 5)縱向和橫向幾給是兩套獨立的傳動鏈,它們由步進電動機、齒輪副、絲杠螺母副組成,其傳動比應滿足機床所要求的分辨率。 6)為了保證進給伺服系統(tǒng)的傳動精度和平穩(wěn)性要求,選用摩擦小、傳動效率高的滾珠絲杠螺母副,并應有預緊機構,以提高傳動剛度,消除間隙。齒輪副也應有消除齒
16、側(cè)間隙的機構。 3.2 數(shù)控系統(tǒng)介紹 3.2.1操作臺介紹 華中“世紀星”HNC-21T是一基于嵌入式工業(yè)PC的開放式數(shù)控系統(tǒng),配備高性能32位微處理器、內(nèi)裝式PLC及彩色LCD顯示器。采用國際標準G代碼編程,與各種流行的CAD/CAM自動編程系統(tǒng)兼容。 1)、操作臺結(jié)構 HNC-21T車床數(shù)控裝置操作臺為標準固定結(jié)構,外形尺寸為420310110毫米 (WHD),如圖3-1所示。 圖3-1 NC-21T車床數(shù)控裝置操作臺 2)、 顯示器 操作臺的左上部為7.5彩色液晶顯示器,分辨率為640480。 3)、 NC鍵盤
17、 NC鍵盤包括精簡型MDI鍵盤和F1~F10十個功能鍵。 標準化的字母數(shù)字式鍵盤的大部分鍵具有上檔鍵功能,當“UPPER”鍵有效時,指示燈亮,輸入的是上檔鍵。 NC鍵盤用于零件程序的編制、參數(shù)輸入、MDI及系統(tǒng)管理操作等。 4)、 機床控制面板 標準機床控制面板的大部分按鍵(除“急?!卑粹o外)位于操作臺的下部。 機床控制面板用于直接控制機床的動作或加工過程。 3.2.2軟件操作界面 HNC-21T的軟件操作界面如圖3-2所示。其界面由如下幾個部分組成: 圖3-2 NC-21T的軟件操作界面 1、 圖形顯示窗口
18、 2、 菜單命令條 3、 運行程序索引 4、 選定坐標系下的坐標值,坐標系可在機床坐標系/工件坐標系/相對坐標系之間切換;顯示值可在指令位置/實際位置/剩余進給/跟蹤誤差/負載電流/補償值之間切換。 5、 工件坐標零點在機床坐標系下的坐標 6、 輔助功能M、S、T;當前刀位CT、選擇刀位ST 7、 當前加工程序行 8、 當前加工方式、系統(tǒng)運行狀態(tài)及當前時間 9、 當前坐標、剩余進給 10、直徑/半徑編程、公制/英制編程、每分鐘進給/每轉(zhuǎn)進給、快速修調(diào)、進給修調(diào)、主軸修調(diào)倍率 第4章 機床進給伺服系統(tǒng)機械部分的設計和計算 4.1進給伺服
19、系統(tǒng)機械部分的結(jié)構改造設計方案 4.1.1縱向進給機械結(jié)構改造方案 拆除原機床的進給箱、溜板箱、滑動絲杠、光杠等,裝上步進電機、齒輪減速箱和滾珠絲杠螺母副。為了提高支承剛度,采用向心推力球軸承對加止推軸承支承方式。齒輪間隙采用雙薄片調(diào)隙方式。 利用原機床進給箱的安裝孔和銷釘孔安裝齒輪箱體。滾珠絲桿仍安置在原來的位置,兩端仍采用原固定方式。這樣可減少改裝工作量,并由于滾珠絲杠的摩擦系數(shù)小于原絲杠,且外徑比原先的大,從而使縱向進給整體剛度只可能增大。 縱向進給機構都采用了一級齒輪減速。雙片齒輪間沒有加彈簧自動消除間隙。因為彈簧的彈力很難適應負載的變化情況。當負載大時,彈簧彈力顯小,起不到消
20、除間隙之目的;當負載小時,彈簧彈力又顯大,則加速齒輪的磨損。因此,采用定期人工調(diào)整、螺釘緊固的辦法消除間隙。 4.1.2橫向進給機械結(jié)構改造方案 拆除原中拖板絲桿,安裝滾珠絲桿副,為提高橫向進給系統(tǒng)剛度,支承方式采用兩端裝止推軸承。步進電機、齒輪箱安裝于機床后側(cè),為了使減速機構不影響走刀,同時消除傳動過程的沖擊,減速機構采用二級傳動,從動輪采用雙薄片錯位消除間隙。 4.2進給伺服機構機械部分的設計計算 4.2.1進擇脈沖當量 根據(jù)機床精度要求確定脈沖當量,縱向:0.01mm/步,橫向:0.005mm/步(半徑)。 4.2.2計算切削力 (1)縱車外圓 主切削力Fz(N)按經(jīng)驗公
21、式估算: Fz=0.67Dmax1.5 (4-1) =0.67 x 4001.5 =5360 按切削力各分力比例: Fz:Fx:Fy=l:0.25:0.4
22、 Fx = 5360 x 0.25 = 1340 Fy = 5360 x 0.4 = 2144 (2)橫切端面 主切削力F’z(N)可取縱切的1/2: 此時走刀抗力為F’y(N),吃刀抗力為F’x(N)。仍按上述比例粗略計算: F’z:F’y:F’x=1:0.25:0.4 F’y=2680 x 0.25 = 670 F’x=2680 x 0.4 = 1072 4.3滾珠絲杠螺母
23、副的計算和選型 滾珠絲杠螺母副的設計首先要選擇結(jié)構類型:確定滾珠循環(huán)方式,滾珠絲杠副的預緊方式。結(jié)構類型確定之后,再計算和確定其他技術參數(shù),包括:公稱直徑d0(絲杠外徑d)、導程L0、滾珠的工作圈數(shù)j、列數(shù)K、精度等級等。 滾珠循環(huán)方式可分為外循環(huán)和內(nèi)循環(huán)兩大類,外循環(huán)又分為螺旋槽式和插管式。我們在此選用螺旋槽式外循環(huán):在螺母外圓上銑出螺旋槽,槽的兩端鉆出通孔,同螺母的螺紋滾道相切,形成滾珠返回通道。為防止?jié)L珠脫落,螺旋槽用鋼套蓋住。在通孔口設有擋珠器,引導滾珠進入通孔。擋珠器用圓鋼彎成弧形桿,并焊上螺栓,用螺帽固定在螺母上。它的優(yōu)點是:工藝簡單,螺母外徑尺寸較小。缺點是:螺旋槽同通孔不易
24、連接準確,擋珠器鋼性差、耐磨性差。 滾珠絲杠副的預緊方法有:雙螺母墊片式預緊、雙螺母螺紋式預緊、雙螺母齒差式預緊、單螺母變導程預緊以及過盈滾珠預緊等。 4.3.1縱向進給絲杠 (1)計算進給率引力Fm(N) 縱向進給為綜合型導軌: 式中: K--考慮顛復力矩影響的實驗系數(shù),綜合導軌取K=1.15; --滑動導軌摩擦系數(shù):0.15--0.18; G ----溜板及刀架重力: G = 800N。 (2) 計算最大動負載c:
25、 (4-2) 式中:L0 ——滾珠絲杠導程,初選L0=6mm; vs——最大切削力下的進給速度,可取最高進給速度的(1/2~1/3),此處vs=0.6m/min; fw——運轉(zhuǎn)系數(shù),按一般運轉(zhuǎn)取fw=1.2~1.5; L——壽命、以106轉(zhuǎn)為1單位。 (3)滾珠絲杠螺母副的選型和校核 可采用外循環(huán)螺紋調(diào)整預緊的雙螺母滾珠絲杠副,1列2.5圈,其額定動負載為16400N,精度等級選3級。 傳動效率計算
26、 (4-3) 式中:γ——螺旋升角,W1L4O0bγ=2044 φ——摩擦角取10滾動摩擦系數(shù)0.003~0.004 (4)剛度驗算 一般滾珠絲杠比較細長,它的剛度應該給與充分重視。 先畫出此縱向進給滾珠絲杠支承方式草圖。最大牽引力為2530N。支承間距L=15OOmm絲杠螺母及軸承均進行預緊,預緊力為最大軸向負荷的1/3。 圖4-1 縱向進給系統(tǒng)計算簡圖 (4.1)絲杠的拉伸或壓縮變形量δ1 根據(jù)Pm=2530N,Do=40mm, 查資料可查出δL/L=l.2﹡lO-5,可算出: δ1=δL/L1500=
27、1.210-51500=1.810-2(mm) 由于兩端均采用向心推力球軸承,且絲杠又進行了預拉伸,故其拉壓剛度可以提高4倍。其實際變形量δ‘1 (mm)為: (4.2)滾珠與螺紋滾道間接觸變形δ2 查資料W系列1列2.5圈滾珠和螺紋滾道接觸變形量δQ 因進行了預緊, (4.3)、支承滾珠絲杠軸承的軸向接觸變形δ3 采用8107型推力球軸承,d1=35mm,滾動體直徑dQ=6.35mm,滾動體數(shù)量z=18, 注意,此公式中Fm單位應為kgf 因施加預緊力,故 根據(jù)以上計算: 定位精度 (5)穩(wěn)定性校核 滾珠絲杠兩端推力軸承
28、,不會產(chǎn)生失穩(wěn)現(xiàn)象不需作穩(wěn)定性校核。 4.3.2橫向進給絲杠 (1)計算進給牽引力F‘m: 橫向?qū)к墳檠辔残危嬎闳缦? (2)計算最大動負載c (3)選擇滾珠絲杠螺母副 查資料,W1L20051列2.5圈外循環(huán)螺紋預緊滾珠絲杠副,額定動載荷為8800N,可滿足要求,選定精度為3級。 (4)傳動效率計算 (5)剛度驗算 橫向進給絲杠支承方式如圖4-2所示,最大牽引力為2425N,支承間距L=450mm,因絲杠長度較短,不需預緊,螺母及軸承預緊。 圖4-2 計算如下: (
29、5.1)、絲杠的拉伸或壓縮變形量δ1 (mm) 查圖4-3,根據(jù)Fm=2023N,D。=2Omm,查出δL /L=5lO-5,可算出 圖4-3 橫向進給系統(tǒng)計算簡圖 (5.2)、滾珠與螺紋滾道間接觸變形δ2 查資料: 因進行了預緊δ2=1/2δQ=0.5*8.5=4.25m (5.3)、支承滾珠絲杠的軸承的軸向接觸變形δ3 采用8102推力球軸承,dQ=4.763,z=12,d=l5mm 考慮到進行了預緊,故 綜合以上幾項變形量之和: 顯然此變形量已大于定位精度的要求,應該采取相應的措施修改設計,因橫向溜板空間限制,不宜再加大滾珠絲杠直徑,故采用
30、貼塑導軌減小摩擦力,從而減小最大牽引力。重新計算如下: 從資料查出,當Fm’=1155N時,δL/L=2.4lO-5 δ2和δ3不變,則δ=δ1+δ2+δ3=0.0108+0.0043+0.0047=0.0198mm定位精度為0.lmm,故此變形量仍不能滿足,如果將滾珠絲杠再經(jīng)過預拉伸,剛度還可提高四倍,則變形量可控制在要求的范圍之內(nèi)。 從上面計算過程可以看出,設計的過程要經(jīng)過反復修改參數(shù),反復計算才能達到滿意的結(jié)果。 (6)穩(wěn)定性校核 計算臨界負載其FK(N) 式中: E——材料彈性模量,鋼:E=20.61O6N/cm2 I——截面慣性矩(cm4)絲杠:,di
31、為絲杠內(nèi)徑; (4-4) L——絲杠兩支承端距離 (cm); fZ-一絲杠支承方式系數(shù),從表4-13中查出,一端固定,一端簡支fZ =2.00 (一般[nk]=2.5~4) 此滾珠絲杠不會產(chǎn)生失穩(wěn)。 4.4縱向及橫向滾珠絲杠副幾何參數(shù) 其幾何參數(shù)如表4-1所示: 表4-1 名稱 符號 公式 公稱直徑 35 20 導程 6 5 接觸角 37’ 433’ 鋼球直徑(㎜) 3.969 3.175 滾道法面半徑 2.064 1.651 偏心距 0.056
32、 0.045 螺紋升角 37’ 433’ 螺桿外徑 34 19.4 螺桿內(nèi)徑 30.984 16.78 螺桿紋接觸直徑 31.258 16.835 螺母螺紋直徑 39.365 23.212 4.5齒輪傳動比計算 4.5.1縱向進給齒輪箱傳動比計算 已確定縱向進給脈沖當量δp=0.01滾珠絲杠導程L0=6mm,初選步進電機步距角0.750??捎嬎愠鰝鲃颖萯 可選定齒輪齒數(shù)為, 或 4.5.2橫向進給齒輪箱傳動比計算 已確定橫向進給脈沖當量δp=O.005,滾珠絲杠導程L0=5mm,初選步進電機步距角0.
33、750可計算傳動比i: 考慮到結(jié)構上的原因,不使大齒輪直徑太大,以免影響到橫向溜板的有效行程,故此處可采用兩級齒輪降速: 因進給運動齒輪受力不大,模數(shù)m取2。相關參數(shù)如表4-2所示: 表4-2 齒數(shù) 32 40 24 40 20 25 分度圓 64 80 48 80 40 50 齒頂圓 68 84 52 84 44 54 齒根圓 59 75 43 75 35 45 齒寬 (6~10)m 20 20 20 20 20 20 中心距 72 64 45 第五章
34、 CA6140車床進給部分電機的選擇 5.1縱向進給步進電機計算 5.1.1等效傳動慣量計算 方法計算如下表示。傳動系統(tǒng)折算到電機軸上的總傳動慣量JΣ(kg?cm2)可有下式計算: JΣ=Jm+J1+(Z1Z2)2〔(J2+Js)+Gg(L02π)2〕 (5-1) 式中:Jm—步進電機轉(zhuǎn)子轉(zhuǎn)動慣量(kg?cm2) J1,J2—齒輪Z1、Z2的轉(zhuǎn)動慣量(kg?cm2) Js—滾珠絲杠傳動慣量(kg?cm2) 參考同類型機床,初選反應式步進電機150BF,其轉(zhuǎn)子轉(zhuǎn)動慣量Jm=10(kg?cm2) J1=0.7810-3d14L1=0.7810
35、-36.422=2.6 kg?cm2 J2=0.7810-3d24L2=0.7810-3822=6.39 kg?cm2 Js=0.7810-344150=29.952 kg?cm2 G=800N 代入上式: JΣ=Jm+J1+(Z1Z2)2〔(J2+Js)+Gg(L02π)2〕 =10+2.62+(3240)2〔(6.39+29.592)+8009.8(0.62π)2〕 =36.355 kg?cm2 考慮步進電機與傳動系統(tǒng)慣量匹配問題。 JmJΣ=1036.355=0.275 基本滿足慣量匹配的要求。 5.1.2電機力矩計算 機床在不同的工況下,其所需轉(zhuǎn)距不同,
36、下面分別按各階段計算: A.快速空載啟動力矩M起 在快速空載起動階段,加速力矩占的比例較大,具體計算公式如下: M起=Mamax+Mf+Ma Mamax=JΣε= JΣnnax10-2/(60ta/2π) = JΣ2πnmax10-2/(60ta) nmax=νmaxθbδp360 將前面數(shù)據(jù)代入,式中各符號意義同前。 nmax=νmaxθbδp360=24000.75(0.01360)=500r/min 啟動加速時間ta=30ms Mamax=JΣ2πnmax10-2/(60
37、ta) =36.3552π500102/(600.03) =634.5Ncm 折算到電機軸上的摩擦力距Mf: Mf=FOL02πηi=f(Pz+G)L0(2πηZ2Z1) =0.16(5360+800)0.6(2π0.81.25)=94 Ncm 附加摩擦力距M0 MO=FPOL0(1-η02)/2πηi=13FtL0(1-η02)(2πηZ2Z1) =1325300.6(1-0.92)( 2π0.81.25) =805.30.19=15.3Ncm 上述三項合計: M起=Mamax+Mf+Ma=634.5+
38、94+15.3=743.8Ncm B.快速移動時所需力矩M快。 M快=Mf+M0=94+15.3=109.3Ncm C.快速切削負載時所需力矩 M切 M切=Mf+M0+Mt=Mf+M0+ FOL02πηi =94+15.3+13400.6(2π0.81.25) =94+15.3+127.96 =237.26Ncm 從上面計算可以看出,M起、M快和M切三種工況下,以快速空載起動所需力矩最大,以此項作為初選步進電機的依據(jù)。 從下表查出,當步進電機為三相六拍時 λ=MqMjmax=0.951 最大靜力矩Mjmax=743.80.951=782Ncm 按此最大靜力矩從下表查
39、出,150BF002型最大靜轉(zhuǎn)矩為13.72Nm。大于所需最大靜轉(zhuǎn)矩,可作為初選型號,但還需進一步考核步進電機起動矩頻特性和運行矩頻特性。 5.1.3計算步進電機空載起動頻率和切削時的工作頻率 ===4000 HZ ===1000 HZ 從表中查出150BF002型步進電機允許的最高空載起動頻率為2800Hz運行頻率為8000Hz,再從下表中查出130BF001型步進電機起動矩頻特性和運行矩頻特性曲線如圖2-3,2-4所示。當步進電機起動時,f起=2500時,M=100Ncm,遠遠不能滿足此機床所要求的空載起動力矩(782Ncm)直接使用則會產(chǎn)生失步現(xiàn)象,所以必須采用升降速控制(用
40、軟件實現(xiàn)),將起動頻率降到1000Hz時,起動力矩可增加到588.4Ncm,然后在電路上再采用高低壓驅(qū)動電路,還可將步進電機輸出力矩擴大一倍左右。 圖5-1 130BF001 型運行距頻特性 圖5-2 130BF001 啟動型距頻特性 當快速運動和切削進給時,130BF001型步進電機運行矩頻特性完全可以滿足要求。 5.2橫向進給步進電機計算 5.2.1等效傳動慣量計算 橫向傳動系統(tǒng)折算到電機軸上的總的轉(zhuǎn)動慣量J可由下式計算 JΣ=Jm+J1+(Z1Z2)2{(J2+J3)+Z3Zф〔(Jφ+J
41、ξ)+Gg(L02π)2} (5-2) 式中各符號意義同前,其中 J1=0.7810-3d14L1=0.7810-34.822=0.83kg?cm2 J2=0.7810-3d24L2=0.7810-3842=6.4 kg?cm2 J3=0.7810-3d24L3=0.7810-3442=0.4 kg?cm2 J4=0.7810-3d24L4=0.7810-3542=0.98 kg?cm2 Js=0.7810-32445=0.56kg?cm2 G=600n Jm=4.7 (初選反應式步進電機為110BF) 代入上式為: JΣ=Jm+J1+(Z1Z2)2{(J2+J3)+
42、Z3Zф〔(Jφ+Jξ)+Gg(L02π)2〕} =4.7+0.83+(2410)2{(6.4+0.4)+(2025)2[(0.98+0.56)+60010(0.52π)2]} =8.42kgcm2 考慮到步進電機與傳動系統(tǒng)慣量的匹配問題 JmJΣ=4.78.42=0. 558 基本滿足慣量匹配要求 5.2.2電機力矩計算 A.快速空載起動力矩M M起=Mamax+Mf+Ma (5-3) Mamax=JΣε= JΣnnax10-2(60ta2π) = J
43、Σ2πnmax102(60ta) 式中: nmax=νmaxθbδp360 =12000.75(0.005360)=500r/min ta=30ms Mamax=JΣ2πnmax102(60ta) =8.422π500102(600.03) =147Ncm 折算到電機軸上的摩擦力矩Mf Mf=FOL02πηi=f(Pz+G)L0(2πηZ2Z1) =0.2(2680+600)0.50.48(2π0.8) =31.3Ncm 附加摩擦力矩M0 MO=FPOL0(1-η02)2πηi=13FˊtL0(1-η02)(2πηZ2Z1)
44、 =1320230.50.48(1-0.92)( 2π0.8) =6.1Ncm 上述三項合計: M起=Mamax+Mf+Ma=147+31.3+6.1=184.4Ncm B.快速移動時所需力矩M快。 M快=Mf+M0=31.3+6.1=37.4Ncm C.最大切削福載時所需力矩M切 M切=Mf+M0+Mt=Mf+M0+ FOL02πηi =37.4+10720.50.48(2π0.8) =88.6Ncm 由上面計算可以看出, M起、M快和M切三種工況下,以快速空載起動所需力矩最大,故以此項作為選擇步進電機的依據(jù)。根據(jù)步進電機轉(zhuǎn)矩Mq與最大靜轉(zhuǎn)矩Mjmax的關系
45、可知,當步進電機為三相六拍時:λ=MqMjmax=0.866 最大靜力矩Mjmax=184.40.866=213Ncm 查BF反應式步進電機技術參數(shù)得,110BF003型步進電機最大靜轉(zhuǎn)矩為7.84Nm。大于所需最大靜轉(zhuǎn)矩,可作為初選型號,但必須進一步考核步進電機起動矩頻特性和運行矩頻特性。 5.2.3計算步進電機空載起動頻率和切削時的工作頻率 Fk=1000Vmax60δp =10002.4600.01=4000Hz Fe=1000Vs60δp =10000.6600.01=1000Hz 由110BF003型步進電機的技術參數(shù)可知其最高空載起動頻率為1500Hz,運行頻率為
46、7000Hz。根據(jù)110BF003型電機的起動距頻特性和運行矩頻特性曲線可以看出,當步進電機起動時F=1500Hz,M=98Ncm,小于機床所需的起動力矩(184.4Ncm),直接使用會產(chǎn)生失步現(xiàn)象,所以必須采用升降速控制(用軟件實現(xiàn))。將起動頻率降為1000Hz時,既可滿足要求。當機床快速起動和切削進給時,則完全滿足運行矩頻要求。 第6章 CA6140車床刀架部分的改造 6.1刀架的選用 電動刀架可分為四或六工位(即刀架上可裝四或六把刀具),機床數(shù)據(jù)MD14510[20]所設定的數(shù)據(jù)應與刀架工位相吻合。每
47、把刀具都有一固定刀號,通過霍爾開關進行到位檢測。到位信號經(jīng)故障設置引至I/O演示板下方的接插件上。根據(jù)實際需求我們選用四工位刀架。 6.2電動刀架工作原理 系統(tǒng)發(fā)出換刀信號,刀架電機正轉(zhuǎn)繼電器動作,電機正轉(zhuǎn),通過減速機構和升降機構將上刀體上升至一定位置,離合盤起作用,帶動上刀體旋轉(zhuǎn)到所選擇刀位,發(fā)訊盤發(fā)出刀位信號,刀架電機反轉(zhuǎn)繼電器動作,電機反轉(zhuǎn),完成初定位后上刀體下降,齒牙盤嚙合,完成精確定位,并通過升降機構鎖緊刀架。 6.3 改造后的刀架 改造后的刀架如圖6-1所示,刀架尺寸如表6-1所示。 圖6-1 改造后的刀架 表6-1刀架
48、尺寸 H1 236mm H3 80mm H2 40mm H4 20mm B 230mm B1 115mm A 90mm L1 379mm 6.4刀架的電氣控制 刀架電氣控制原理如圖6-2、6-3所示 圖6-2刀架電氣控制原理圖 圖6-3刀架電氣控制原理圖 6.5刀架的安裝 刀架安裝時拆除原手動刀架和小拖板,安裝由微機控制的四工位電動刀架。根據(jù)車床的型號及主軸中心高度,選用LD4-I型四工位電動刀架。安裝時,去掉車床小拖板,置刀架于中拖板上,卸掉
49、電機風罩,逆時針方向轉(zhuǎn)動電機,或轉(zhuǎn)動軸承蓋處之內(nèi)六角螺孔,使刀架轉(zhuǎn)動到45左右時,裝上螺釘,然后固定刀架即可。電動刀架的安裝較為方便,安裝時須注意以下兩點: (1)電動刀架的兩側(cè)面與原車床縱、橫向的進給方向平行。 (2)電動刀架與系統(tǒng)的連線在安裝時應合理,以免加工時切屑、冷卻液及其它雜物磕碰電動刀架連線。 第7章 機床的安裝調(diào)試與驗收 7.1 數(shù)控系統(tǒng)調(diào)試 7.1.1 華中數(shù)控系統(tǒng)與車床間I/O信號的處理 車床至數(shù)控系統(tǒng)的輸入信號。 輸入信號包括各種位置、速度及操作信號。主要有:①主軸編碼器向數(shù)控系統(tǒng)發(fā)出的PAS、PAS*、PBS、PBS*、PCS、PCS*信號,用
50、于位置和速度及判向。②X、Z軸參考點開關SQ2、SQ3及行程限位開關SQ4—SQ7分別用做減速回零和超程保護。③限位暫時解除開光,當X、Z軸產(chǎn)生超程保護后。按下此開關暫時解除超程信號,然后反向運行到正常行程范圍內(nèi)。④X、Z軸步進驅(qū)動器報警信號,當驅(qū)動器故障時,向數(shù)控系統(tǒng)發(fā)出信號進行功能保護。⑤刀架信號板,由霍爾元件及磁柱組成,在換刀時檢測到信號T01—T04。⑥急停開關,用于在緊急情況下停止機床的所有輸出。 數(shù)控系統(tǒng)至機床的輸出信號。 ①對主軸的控制信號,數(shù)控系統(tǒng)向變頻器發(fā)出0—10VDC的模塊電壓控制變頻器的輸出頻率,從而實現(xiàn)自動無級調(diào)速。②主軸控制信號(M03—M05 功能及制動信號)
51、。③自動潤滑信號。潤滑信號M32可定時控制潤滑系統(tǒng)泵的接通,對導軌、刀架等運動機構及時補充潤滑油。④冷卻液信號。利用冷卻信號M08控制冷卻泵工作,讓冷卻液帶走車削時產(chǎn)生的熱量以保護刀具和工件。⑤X、Z軸運動信號。數(shù)控系統(tǒng)給驅(qū)動器送出信號有步進脈沖信號(CP+、CP-)方向信號(DIR+、DIR-):驅(qū)動使能信號EN1。⑥換刀信號??墒沟都苷齻鱐L+及刀架反轉(zhuǎn)TL-,也可在程序中編入刀具號。 7.1.2數(shù)控車床的幾種過程原理分析及相應參數(shù)的設置 1、主軸停止 在程序中執(zhí)行M05指令或手動停止主軸時,系統(tǒng)斷開主軸電機的電源。然后經(jīng)適當延時后發(fā)出制動信號并保持一定時間,使主軸停止。其中主軸斷電
52、后延時由參數(shù)D087、D088設定,制動信號保持時間由參數(shù)D089、D090設定。因主軸變?yōu)樽冾l驅(qū)動,則設定P001.5=1,初始運行時,綜合調(diào)整P021(主軸模擬調(diào)整數(shù)據(jù))、P036(主軸速度偏置補償)、P037—P040(模擬給定10V時對應齒輪1—4擋的轉(zhuǎn)速,最終使指令轉(zhuǎn)速與實際轉(zhuǎn)速一致。有關參數(shù)設定為:①主軸斷電至開始制動時間T1,D087=01001001(低位字節(jié));D088=00000000(高位字節(jié)),則T1=16(256D088+D087)=1168ms。②主軸抱閘時間T2,D089=01111101(底位字節(jié)),D090=00000000,則T2=16(256D090+D0
53、89)=2000ms。③主軸編碼器的齒輪倍率參數(shù)P006.6=0,P006.7=0。 2、回零點。 零點是機床的編程坐標基準點,是機床正常、精確工作的基礎。系統(tǒng)每次上電后都應多兩軸回零。每軸用一個感應開關SQ2(X軸)、SQ3(Z軸)作為減速信號和零位信號?;亓悴僮鲿r,兩軸先以P022、P023設定的快速負向運動,得到減速信號后,開始逐漸減速到零。然后以P033設定的回零速度反向運動,再次收到SQ2、SQ3信號時停止運動,此時的位置就是坐標零點。其中需要設定的參數(shù)為:用感應開關P007.1(X軸)=1,P007.0(Z軸)=1;選擇負方向回零P006.1(X軸)=1,P006.0=(Z軸)
54、=1;有機械回零點P014.1(X軸)=1,P014.0(X軸)=1,P014.0(Z軸)=1;低速回零點速度P033=200mm/min。 3、電動刀架換刀動作及相關參數(shù)設置。 當程序自動或手動換刀時,數(shù)控系統(tǒng)發(fā)出刀架正轉(zhuǎn)信號TL﹢,然后等待相應的刀具到位信號(T01~T04),收到到位信號后停止正轉(zhuǎn),經(jīng)過D082設定的延時后,給出反轉(zhuǎn)信號信號TL-鎖緊與否靠反轉(zhuǎn)時間D085設定,有關參數(shù)為: 1) 刀具到位信號低電平有效時P001.1=1; 2) 無刀具到位信號P041.0=0; 3) 移動一個刀位所需時間上限T3.D076,=11000111(低位字節(jié)),D077=000000
55、00(高位字節(jié)),則T3=16(256D077+D076)=3184ms; 4) 從第一把刀到最后一把刀所需時間上限T3,D078=10001110(低位字節(jié)),D079=00000000(高位字節(jié)),則T4=16(256D079+D078)=6368ms; 5) 刀架正轉(zhuǎn)停止到反轉(zhuǎn)的時間T5,D082=00000111(單字節(jié)),則T5=16D082=1008ms; 6) 刀架反轉(zhuǎn)鎖緊電間T6,D085=00111111(單字節(jié)),則T6=16D085=1008ms。 7) 總刀位數(shù)T*,D084=00000100(單字節(jié)),T*=4。 4、進給軸調(diào)及相關參數(shù)高置。 1)軸運動方
56、向調(diào)整,更改P008.1(X軸)和P008.0(Z軸)可使用進給運動方向改變; 2)數(shù)控系統(tǒng)中設有X、Z軸驅(qū)動器報警電平參數(shù),應將其與驅(qū)動器實際報警電平設為一致。如P009.1(X軸)=1,P009.0(Z軸)=1g表驅(qū)動報警信號為低電平有效。 3)應正確設置電子齒輪比參數(shù),使進給軸的實際行程一致。其與驅(qū)動器細分檔、絲杠螺距、步距角、電動軸的減速比有關。我們設計中驅(qū)動器的細分檔為10、電機的步距角為0.75,X、Z均為1:1的齒輪傳動,絲杠螺距為4mm.5mm,因X軸為直徑編程,所以電機一轉(zhuǎn)對應的移動量為8mm,Z軸電機一轉(zhuǎn)對應的的移動量為5mm。則:CMR/CMD=360/(1000aL
57、,其中CMR為指令倍乘系數(shù),CMD為指令分頻系數(shù):a為步距角,L為電機一轉(zhuǎn)的對應的機床移動量,則X軸;CMR/CMD=3/5:Z軸:CMR/CMD=24/25。參數(shù)設置為:PO15(X軸)=3,PO16(Z軸)=24,PO17(X軸)=5,PO18(Z軸)=25 4)快移動速度和加減速時間常數(shù)設置。PO22(X軸)=800mm/min,PO23(Z軸)=1000mm/min;PO24(X軸)=450ms,PO25(Z軸)=450ms。 5)軟限位參數(shù)。軟限位參數(shù)應設置在硬限位正常的行程方位內(nèi),其作用為避免因行程限位而中斷加工。起單位為um,分正、負兩個方向。可根據(jù)硬限位行程和加工方位自行設
58、定。 6)絲杠反向間隙的補償。進給軸由于裝配、磨損等原應,均存在一定的反向間隙,為提高機床的加工精度,經(jīng)測量必須設定X、Z軸的間隙補償值,單位為um。 5、其他有關參數(shù)的設置及傳動鏈注意事項 華中數(shù)控系統(tǒng)的參數(shù)分系統(tǒng)參數(shù)P、診斷參數(shù)為D、設置參數(shù)S三種。與加工程序編輯有關的參數(shù)應根據(jù)操作員的需要來設置和修改,如公、英制編程選擇等。另外,由于驅(qū)動系統(tǒng)為步進電機開環(huán)系統(tǒng),運行中應避開起低頻震蕩區(qū),最高移動速度也不能太高,以防失步:中間傳動鏈應進行適當?shù)挠杈o,以消除間隙,提高傳動剛度,消除反向空行程死區(qū),最終提高加工精度。 只要對數(shù)控設備認真研究摸索,逐漸積累經(jīng)驗,然后從世界應用出發(fā)選用成。
59、 7.2 電氣系統(tǒng)的調(diào)試 調(diào)試分為兩大步:數(shù)控系統(tǒng)外圍的調(diào)試;數(shù)控系統(tǒng)為適應具體數(shù)控機床需要而調(diào)整機床參數(shù),調(diào)試用戶程序,稱為弱電調(diào)試。 在整機通電前,斷開至CNC單元、伺服單元的電源插頭。這是一項安全措施,以防止不正確的電源進入改造數(shù)控系統(tǒng)的損壞。 1)電源電壓調(diào)試。: 為保證人身和設備安全,必須首先確定各種電源電壓是否正常,如進線電源、DC24V、伺服變壓器副邊電壓等。 2)各控制回路的調(diào)試。 a) 用電器的工作:分別使各用電器正常工作,如照明回路。 b) CNC的啟動停止:以上各種電源電壓正確之后,可以CNC。啟動停止電路。CNC啟動后,LED出現(xiàn)顯示。 c) 急?;芈?/p>
60、:按下機床操作面板上的急停按鈕,檢查機床是否臥刻停止運動,保證機床的安全。一般情況下,超程檢測由CNC通過參數(shù)處理(稱為軟件限位),外部的限位開關是不必要的。然而,為了避免由于伺服反饋系統(tǒng)發(fā)生故障而使機床移動超出軟件限位值,必須安裝行程限位開關(稱為硬件限位)。當開關被擋鐵壓上后,CNC復位并進行緊?;芈贰R苿訖C床拖板檢查硬件限位是否能工作。 3) 限位開關超程檢測。 數(shù)控系統(tǒng)進行超程檢測,是CNC的基本功能,稱為軟件限位。硬件限位是指通過行程開關限位。在機床回參考點的動作中,經(jīng)常需要軟件限位和硬件限位結(jié)合使用。若機床帶有刀庫,當?shù)稁煸谇拔粫r,Z軸不能在參考點下移動,因此Z軸需要設置第二軟
61、件限位保護。 4) 軸行程的設置。 主軸控制單元(或稱主軸放大器)接收來自CNC的譯碼指令,同時接收速度反饋實施閉環(huán)控制。還通過PLC將主軸的各種實際工作狀態(tài)報告CNC,用以完成對主軸的各項功能控制。主軸電動機控制接口為主軸串行輸出(與模擬輸出相對,串行輸出中輸出到主軸的命令值數(shù)字數(shù)據(jù))。同時使用外接位置編碼器與CNC相連,用于檢測主軸的位置。 a) 使主軸能以指定的轉(zhuǎn)速旋轉(zhuǎn),如S500 M03。本機床由CNC控制主軸電機的速度和極性。主軸采用高低兩檔齒輪變速,高速檔主軸與主軸電動機之間齒輪傳動比為1:1;低速檔主軸與主軸電動機之間齒輪傳動比1:4.95。需處理CNC側(cè)對主軸速度的控制的
62、接口信號及主軸控制單元側(cè)的接口信號,并設置最高速度、換檔速度等參數(shù)。 b) 使主軸能停留在某個固定位置(主軸準停),如M190。為了保護刀具能準確地在主軸和刀庫之間交換,必須使用主軸準停功能。主軸完成信號檢測水平;P4077:準停偏移量(如果定向停止位置不準,將會損壞換刀裝置,可通過該參數(shù)對主軸定向位置進行精調(diào))。 7.3傳動絲杠的安裝與調(diào)試 1) 利用螺母的間隙調(diào)整裝置調(diào)整絲桿副間隙時,應使調(diào)整后產(chǎn)生的預緊力以絲桿副最大負載的1/3為宜。在實際調(diào)整中,可以把車床處于最大工作負載,使絲桿內(nèi)部仍不產(chǎn)生間隙,或者間隙量小于0.01mm,而且運轉(zhuǎn)靈活,并以次作為螺母間隙調(diào)整裝置預緊量的判斷標準
63、。 2) 傳動絲桿軸線上各聯(lián)軸套上的錐銷孔按十字分布方式進行配作。這是因為同一聯(lián)軸套上分布的錐銷孔都按同一方向加工時,往往會引起軸心線的直線誤差增大,從而使安裝在傳動絲杠上個零件間的同軸度誤差增大,產(chǎn)生傳動附加載荷,影響絲杠副的傳動性能。 消除齒輪間隙的方法很多,用調(diào)整中心距的方法是最簡單的一種。安裝時將大齒輪所在支承架傳動中心與絲桿對中,首先固定,然后把電動機小齒輪按無間隙嚙合,調(diào)整好中心距,再固定。 3) 滾珠絲桿副的制造精度要求高,加工工藝比較復雜,都是由專業(yè)工廠按系列化進行生產(chǎn)。因此,在進行設備改造時,要按廠家生產(chǎn)標準進行選擇。選擇合適以后,再決定被改造設備的其他相關部分的結(jié)構和
64、尺寸。 主軸脈沖發(fā)生器的引出軸與車床主軸按1:1無間隙柔性連接傳動,連接后應該保證兩者有很好的同步性。安裝中要注意主軸脈沖發(fā)生器是玻璃件,不能隨意敲打碰撞。使用中,車床主軸轉(zhuǎn)速不能超過主軸脈沖發(fā)生器的最高許用轉(zhuǎn)速。 4)改造后的機床專用性強,沒有多余的功能;結(jié)構簡單、易于維修、改造周期短、且提高可機床的性價比;可以滿足生產(chǎn)及教學的要求。 總 結(jié) 論文介紹了數(shù)控車床改造的內(nèi)容,在此過程中我不僅運用了以前所學的各個學科方面的知識,而且學到了課本以外的知識。在
65、此次設計過程中遇到了不少問題,也走了不少彎路,通過此次設計實踐讓我學會虛心求教,細心體察,大膽實踐。任何能力都是在實踐中積累起來的,都會有一個從不會到會,從不熟練到熟練的過程,人常說“生活是最好的老師”就是說只有在生活實踐中不斷磨練,才能提高獨立思考和解決問題的能力;同時也培養(yǎng)了自己優(yōu)良的學風、高尚的人生、團結(jié)和合作的精神;學會了勤奮、求實的學習態(tài)度。 勤奮就是要發(fā)奮努力、不畏艱難。唐代思想家韓愈有句名言:業(yè)精于勤,荒于嬉;行成于思,毀于隨。優(yōu)良的學業(yè)是辛勤汗水的結(jié)晶,成就只有通過刻苦的學習和拼搏才能獲得。馬克思說過:“在科學上沒有平坦的大道,只有不畏勞苦沿著陡峭山路攀登的人,才有希望達到光輝的頂點?!鼻髮嵕褪悄_踏實地,求真務實,謙虛謹慎、介驕介躁、對知識的掌握要弄通弄懂,對技術的掌握要嚴守規(guī)范、嚴謹細致、精益求精。一個人的力量是有限的,團結(jié)合作的力量是無窮的,通過對各個設計環(huán)節(jié)的確定讓我明白:一粒沙雖小,但無數(shù)粒卻能匯成無限的沙漠;水滴雖小,卻你匯成遼闊的海洋;你的一個思想、一個方法,他的一個思想和方法,相互交流互換就有了兩個思想和方法,當今社會競爭日益激烈,而我們現(xiàn)在就應該學會與他人合作。 當然,在設計實踐過程中,我們也收獲了快樂、與同學的快樂、與老師的快樂。因
- 溫馨提示:
1: 本站所有資源如無特殊說明,都需要本地電腦安裝OFFICE2007和PDF閱讀器。圖紙軟件為CAD,CAXA,PROE,UG,SolidWorks等.壓縮文件請下載最新的WinRAR軟件解壓。
2: 本站的文檔不包含任何第三方提供的附件圖紙等,如果需要附件,請聯(lián)系上傳者。文件的所有權益歸上傳用戶所有。
3.本站RAR壓縮包中若帶圖紙,網(wǎng)頁內(nèi)容里面會有圖紙預覽,若沒有圖紙預覽就沒有圖紙。
4. 未經(jīng)權益所有人同意不得將文件中的內(nèi)容挪作商業(yè)或盈利用途。
5. 裝配圖網(wǎng)僅提供信息存儲空間,僅對用戶上傳內(nèi)容的表現(xiàn)方式做保護處理,對用戶上傳分享的文檔內(nèi)容本身不做任何修改或編輯,并不能對任何下載內(nèi)容負責。
6. 下載文件中如有侵權或不適當內(nèi)容,請與我們聯(lián)系,我們立即糾正。
7. 本站不保證下載資源的準確性、安全性和完整性, 同時也不承擔用戶因使用這些下載資源對自己和他人造成任何形式的傷害或損失。