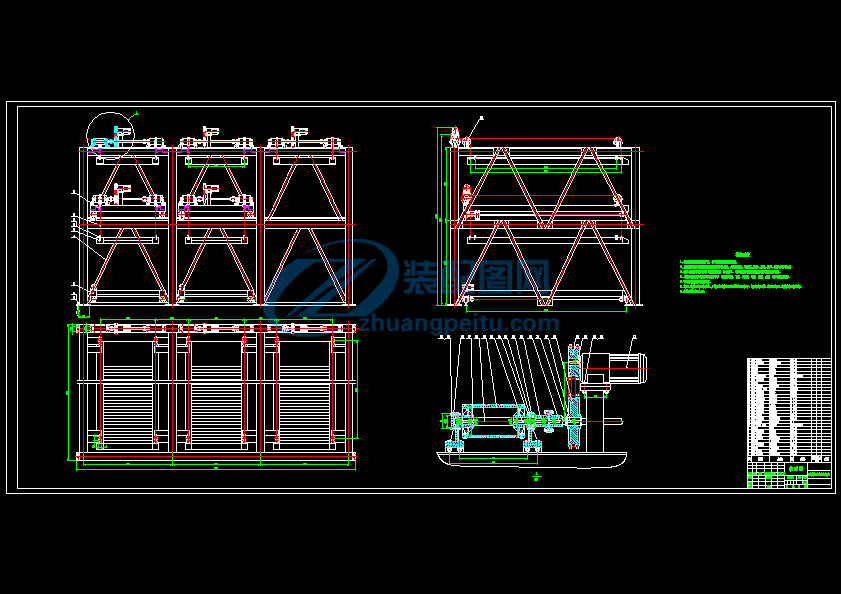
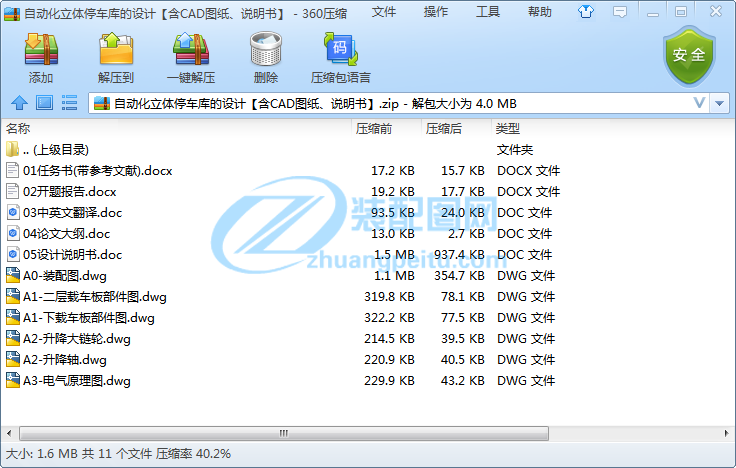
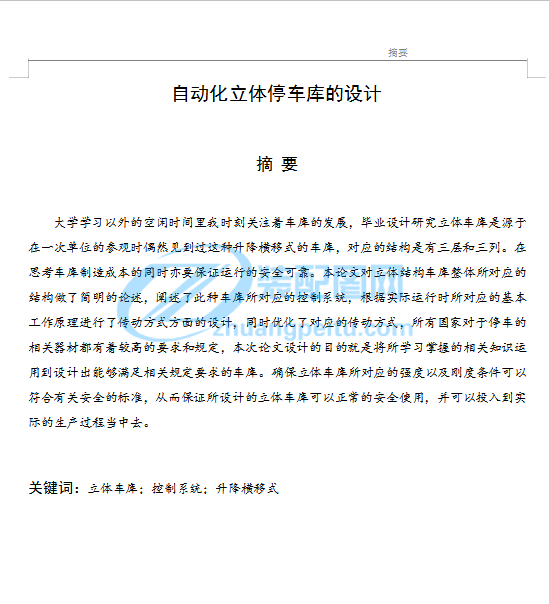
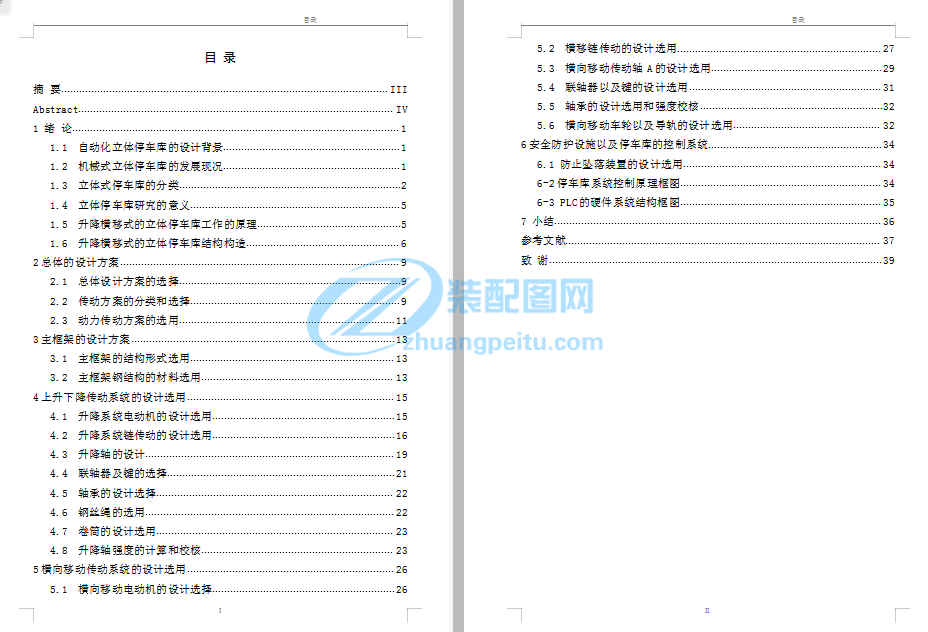
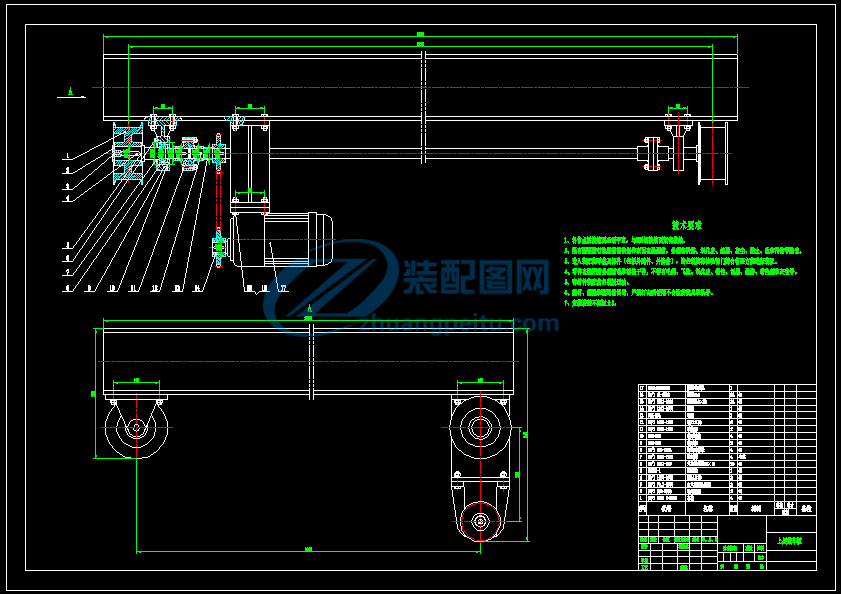
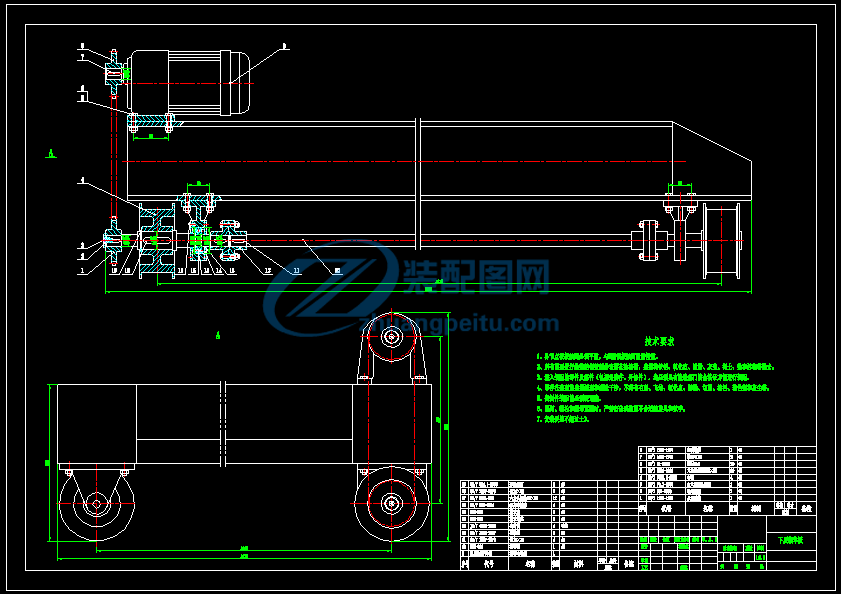
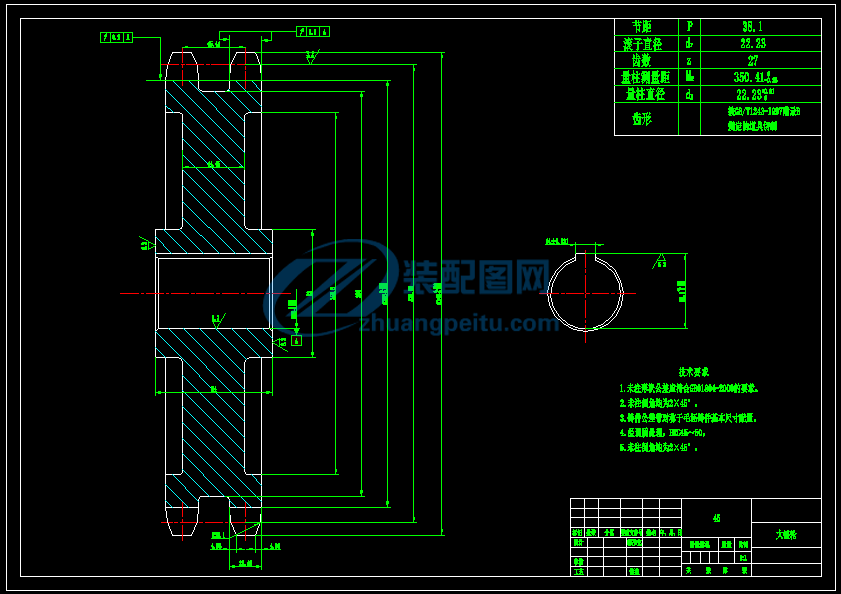
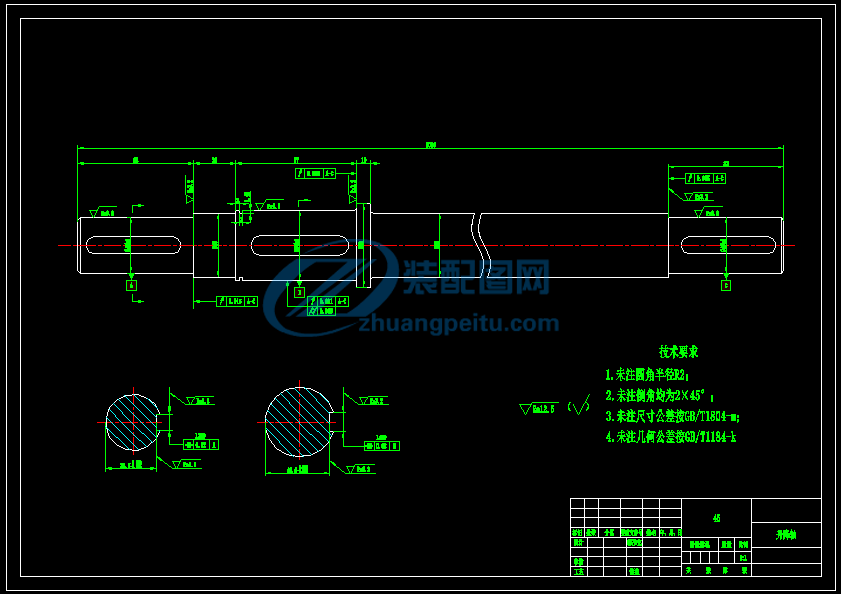

AUTOMATED PARKING: STATUS IN THE UNITED STATESADVANTAGES AND CRITERIARICHARD S. BEEBE, DIRECTOR PARKING AND TRANSPORTATION PLANNING CONSULTING ENGINEERS GROUP, INC. 55 E. EUCLID AVE., MT. PROSPECT, IL 60056 USA PRESENTED AT WORLD PARKING SYMPOSIUM III ST. ANDREWS, SCOTLAND: JUNE 25, 2001AUTOMATED PARKING – THE ENVIRONMENTAL SOLUTION TO THE URBAN PARKING SHORTAGE ADVANTAGES AND CRITERIA GUIDELINES TO AUTOMATED GARAGE DEVELOPMENT??The current state-of-the-art automated parking systems ? Types ? Capacities ? Operating Systems ? Site Area Criteria ? Financial/Operating Advantages ? Land Area and Savings ? Operation’s Savings ? Cost Features of Vehicle/Patron Security ? Time and Motion ? Environmental Advantages ? Reduced Miles of Interior Travel ? Reduced Emissions Production ? Reduced Noise Generation ? Reduced Construction Products and Impacts of Construction Activity ? System Applications ? Location – Freestanding or Inside Buildings ? Capacity and Structure Design ? User Populations and Specific Needs ? Traffic and Exterior Conditions ? Typical Installations ? Above Ground ? Below Ground ? Site and Operating Statistics ? Movement Toward System Recognition/Criteria for Development ? Parking Interests ? Potential User Interests ? International Media Attention ? Product PromotionHISTORY OF MECHANICAL PARKING IN THE U.S. AND ITS STATUS IN 2001 INTRODUCTION Mechanical parking systems were first introduced in the U.S. using freight elevators about the time of World War I. During the 1920’s and 1930’s a series of other patents were granted but it was not until the late 1940’s that the Bowser, Pigeon Hole and Roto Park systems became operational and installed in numerous locations. Some of these early systems were vertical elevator lift modules that placed cars on upper levels of a structure to be moved by attendant and others mechanical devices that could move vehicles into “slots” in a framework built around a central corridor. Capacities ranged typically from less than 100 spaces to more than 600. All of these “early days” systems shared common characteristic—the use of a site area much smaller than the area needed for a conventional garage. During the next twenty-five years many of these systems operated for up to twenty years or so—a few remain in operation today. Problems related to the timely delivery of patron vehicles due largely to inoperative elevator and mechanical systems caused many units to be dismantled. For the next twenty-years there was some discussion of “advanced” mechanical garage systems appearing in Europe and Asia, but no major projects which were planned on were constructed in the U.S. During the past decade the constant demand for parking, especially in large urban centers, created a new U.S. interest in these high technology foreign systems—automated, computer-based systems that added speed, reliability and safety to the basic garage types invented fifty years earlier. European and Asian manufacturers have begun to market their systems and establish offices in the U.S. Several U.S. firms also have entered the marketplace and created greater local interest in Automated Parking. System manufacturers or marketers now include such names as TREVI, Klaus, KRUPS, WOHR, Robotic, APS, HK Systems, Stokes, Auto Space, Sky Parking America and others. Some 100 of these projects are now in the planning stage. SYSTEM ADVANTAGES There are obvious advantages for automated parking facilities in almost any urban location. Significant reduction in land area requirements means conservation of land resources and smaller building bulk cubes and costs. Automated garage operation results in far lower vehicle miles of travel, emission volumes and utility services. Reduced personnel and maintenance costs help to offset any higher per-space cost of automated systems. These advantages have created a large scale market potential in the U.S. which needs to be satisfied as quickly as possible. The following basic elements of automated structure construction point out some of these advantages: A. Developmental 1) An important consideration of automated/mechanical parking has always been project cost. For comparison purposes costs must reflect total cost, including land. The higher cost of construction of an automated system can usually be offset by the value of the smaller land area required for automated construction. For example, a site area roughly 100 feet x 120 feet (12,000 square feet) could support a 400 space automated garage. A conventional ramp garage would require a site area at least 120′ x 280′ (or 33,600 square feet). The cost of land, at $100 per square foot, would equal $1,200,000 for the automated site versus $3,600,000 for the conventional garage. This differential translates into a per space allowance of $5,500 for the automated facility. This is usually the primary factor in establishing the need for, and interest in, an automated garage. In densely developed urban areas the availability of large sites for garage construction has become the number one problem. 2) In addition to the land area/cost factor there are other important reasons to consider an automated structure. These include the provision of unusual levels of patron and vehicle security: (This item is particularly appealing to owners of expensive vehicles wishing to protect their investment). Depending upon location, security issues where patrons do not move inside a garage can be a very important consideration to both owners and users. Negative noise and visual impacts of conventional garages are also eliminated. 3) Automated structures can be built into larger buildings, either above ground or below ground, in significantly less floor area and within a structural framework compatible with that of the primary use. Since there is no need for open areas along perimeter walls to achieve ventilation requirements the parking facility can be enclosed by an architectural fa?ade on those exposures visible to the public, eliminating the negative visual characteristics of a standard garage building. 4) These new systems offer another great benefit to owners and operators. Because of computerized control and report elements complete garage diagnostic review and warning is always on-line. Any potential problem is reported at once to a central control station where attention can be directed at once to the problem. B. Financial 1) The primary financial benefit of automated parking is usually the reduction in land cost. On the theory that an automated structure uses about one-half the land area, the cost savings in land can range from 100 percent to 400 or 500 percent depending upon the value of adjacent property. 2) Owner or operator savings may well be significant since many of these facilities can operate without any staff or with a single attendant. 3) Security aspects of the facility tend to lower insurance costs and maintenance, except for the automated system components, is also reduced. 4) In some locations there may be an added financial incentive. This is the classification of the automated system as machinery and not as structure which can materially reduce property tax burdens. C. Environmental 1) There is a keen awareness developing in the U.S. of environmental hazard created by vehicle operation in congested areas. Vehicle-generated solution can be significantly reduced by reducing miles of travel in the garage. In a typical 600 space conventional garage with twice daily turnover up to 300 miles to travel are eliminated every day. 2) Reduction in miles of travel equals reduction in emissions such as carbon monoxide and nitrates and oxides of nitrogen which are considered major problems in most urban places. 3) Less disruptive but equally important environmental issues, especially in any densely developed area, include light and noise created by vehicles moving into, through and out of a conventional garage. These elements are almost totally removed by use of an automated structure. 4) Another element here is the reduction in the amount of construction activity and disruption due to the reduction in site area and construction volume. CURRENT CONDITIONS IN THE U.S. An Automated Parking Garage was started in the City of Hoboken, New Jersey in January of 1999. This 320 space project was regarded as the first in a long series of new automated garages to be built across the country. At least 40 to 50 garages were “on the list” for construction and Hoboken was considered the beginning of a new era in parking—catching up to the technology in use in Europe and Asia. More than a dozen U.S. and foreign manufacturers have been ready to sell their products and construct facilities. A series of delays and project completion problems have stopped work on the Hoboken garage for the past year. At this time it appears that this garage will not be completed until spring of 2002. The complex series of delays and problems has generated considerable adverse publicity and apprehension on the part of many possible clients. Nevertheless, there is still great interest in these automated garages throughout the U.S. The advantages of automated parking will overcome the problems now occurring in the Hoboken garage.The experience gained in Europe and Asia by major system manufacturers will be the important factor in starting new projects in the U.S. this year and next. We welcome the entrance to our mark of the European and Asian manufacturers. The international automated parking industry, although small in number and without demonstrable U.S. projects, needs to overcome the current conditions and forge a new understanding of the advantages of automated systems and the broad advantages and practicalities of their use. The objective today is to outline application options and to establish basic project criteria by which clients and manufacturers can assure the adequacy and functionality of the parking system when installed. Understanding of these new systems from several viewpoints is the essential key to expanding acceptance and installation. Public and private agencies need to become aware of performance, reliability, operation and maintenance cost considerations and patron acceptance. The automated parking industry has formed a trade group known as the Automated/Mechanical Parking Association to promote the benefits of these new systems. The subject of automated parking has not been widely recognized in this country for many years, even within parking and development industries. But the new systems are technologically and operationally far superior to the units built in previous decades. Owners, builders, agencies and patrons can be assured of cost-effective, reliable, safe and efficient services at competitive rates. A significant response to the benefits of these new systems is already forming, and use will accelerate rapidly as national awareness of the compelling reasons for the use of automated/mechanical parking systems gains momentum. We need to explore and expand the increased construction of automated parking facilities in the U.S. The advantages of this technology are just too significant to permit further delay in their development and construction. However, a number of important lessons have been learned that need to be addressed by any automated system manufacturer.APPLICATIONS In order to properly plan, design, construct, manage and operate an automated facility in the U.S. a number of vital issues must be considered. There follows a summary of these particular items: 1. Theoretically, automated parking requires about one-half the land area of a conventional garage to serve the same number of vehicles. However, this theory has several variables such as: ?? The required capacity of the garage ?? Availability of additional land for conventional garage construction ?? Cost of additional land to facilitate conventional garage construction ?? Garage user populations, turnover, rates, access patterns ?? Parking rates and anticipated revenue compared to costs of garage construction and operation. ?? Project costs of the automated facility versus the conventional facility, given the total cost comparison package. The simple fact that adequate land area is not available to construct a conventional garage does not, in any way, mean an automated facility will prove economically feasible in a particular location. 2. Details of the potential site can be very critical. For an automated facility good street access is essential and, in some cases, multiple frontages can be the difference between feasibility and failure. If primary ingress is from a major street, garage vehicle acceptance rates can be very important. Long queue lines awaiting entry affect the acceptance and use of the facility—more importantly, local police may prohibit vehicles standing in the street to gain access. There are standard ratios of entry/exit portals to garage capacity with a sub-set of determinants based on street traffic patterns and interior garage space layouts and vehicle acceptance/delivery times. Project feasibility can be affected by street traffic operations and other external factors adjacent to the garage site. It is, therefore, essential to fully understand the impacts of these conditions on the design of the facility. 3. The true and total cost of the parking facility—both the automated system and any shell enclosure building—must be properly defined. This leads to a number of questions concerning the project, the project team and the project proposal. For example: ?? Is the automated system manufacturer the contractor or a sub-contractor. ?? If the system manufacturer is the contractor (bidder) he/she must submit all required data and bid realistic costs to include the total price of bid package requirements. ?? If the manufacturer is a sub-contractor will he/she provide project cost data to more than one prime contractor. ?? In most instances the cost of the system and the cost of the shell building should be separated with individual unit costs and payment schedules. ?? Details of the owner’s project bid announcement should describe all project components and cost issues, as well as the total package of compliance items necessary for project acceptance. Bidders should review all background information and particularly the project planning or feasibility studies, to understand the required revenue stream necessary to fund the project and cover potential costs, and then to submit realistic bid data that can ensure feasibility of the completed garage. TYPICAL INSTALLATIONS Within the U.S. there are a wide variety of locations and parking facility needs that will attract the installation of automated parking structures. This variety of project types is one of the principal reasons why the market is strong for a number of different system manufactures. Some of the projects now being studied for automated parking facilities provide an interesting directory of potential developments: ? A 400 space garage on an L-shaped site. The garage will support a ten story residential building (120 units) above. ? A 164 space garage to be built underground as part of the foundation for a twelve story residence towers. ? An 800 space garage on the main shopping street in a large city—half of the spaces are to be for short-term parking. ? Two 75 space garages to be constructed in a five building apartment complex to reduce the amount of parking inside residence building. ? A 3,000 space garage as part of a large, mixed-use development with long-term and short-term parking requirements. ? A 56 space garage to serve a small resort hotel. ? A 4,000 space garage to provide on-site storage for rental car facility at a large airport. ? A 130 space garage to store new vehicle in a vehicle sales agency. SYSTEM CRITERIA There are two distinct sets of project criteria to be considered in the process of constructing an automated parking facility. The first Criteria Package is directed to ensuring that Manufacturers address all critical compliance issues and define system characteristics as required by the project plans and specifications. The second Criteria Package is directed to potential Owners as a means of ensuring that contractor bid submissions comply fully with project requirements. These criteria are very important in establishing the detail of the project; how it will be designed and constructed; how much it will cost; how it will be operated and if it will produce revenue to retire its debt.MANUFACTURER CRITERIA PACKAGE A. System Definition and Operating Characteristics ? Type of system – pallet, comb, plate or other. ? Type of frame/slot arrangement and frame connection to building shell details ? Basic operating features of the system – technology description ? Basic operating speeds for vehicle intake and delivery; elapsed time in seconds ? System use of turntable or vehicle thru in/out movement patterns ? Entry/exit bay details – Singing, signals, vehicle/pedestrian controls and alarms – Capacity – Design formats – Pallet, plate or comb movement throughout the garage – Elapsed time of vehicle intake movement from bay to carrier to slot/from slot to carrier to bay for retrieval ? Average cycle time in/out per vehicle ? Control system functions via sensors, cameras or other devices and oversight of actual internal parking maneuvers ? Testing schedules and maintenance/warranty assumptions. B. System Design Features ? Redundancies ? Security systems ? Stand-by power ? Sensors-motion detection ? Weather conditioning ? Component cleaning – methods and frequency ? Diagnostics and form of response to service/repair orders and alarms ? Spare parts inventory, location, re-order details ? Maintenance inspection program-schedules, procedures, reports ? Major component replacement program ? Life-cycle data and costs C. System Performance Standards ? Define system development, prior testing, patients, etc. and current status ? Describe completed system installations with detail of type, size, exact location, operating features and owner/operator references ? Describe the system warranty to be provided with purchase ? Describe subsequent system maintenance agreements and terms (one-year to multi-year) ? Describe typical operating and maintenance costs for system and for per-space cost comparison analysis ? Describe system-wide performance testing and acceptance at completion ? Describe system training program and training manuals ? Describe system operations manuals and patron use instruction materials ? Describe patron access control systems and total system (patron use) report formats and detail or report transfer to owner ? Describe administration, marketing and activity/revenue/customer use assistance; reporting—formats, responsibilities, techniques, final forms. OWNERS CRITERIA PACKAGE A. Contractural Items ? Check plans against all applicable codes and utility services requirements. ? Check plans for shell building and erection details, system and sub-system interface, functional operation of the total system as a unified facility. ? Check overall schedule, task completion dates and sign-off requirements. ? Check all contractor references, sub-contractor references, equipment suppliers and major parts descriptions and availability. ? Check bonds, insurance coverages, contract language amendments or exceptions re: claims, performance standards, auditing, payouts, etc. ? Check provision for full-scale warranty, maintenance, training services for minimum multi-year period. ? Check provision for periodic owner inspections and subsequent pay request authorizations based on certified percentage of completion by outside experts. ? Require computer software escrow. ? Check provision for all system operation, maintenance, performance, training and other manuals and practices. ? Check system activity records production, operational audits, management coordination with manufacturer. B. Systems Operations ? Check uti