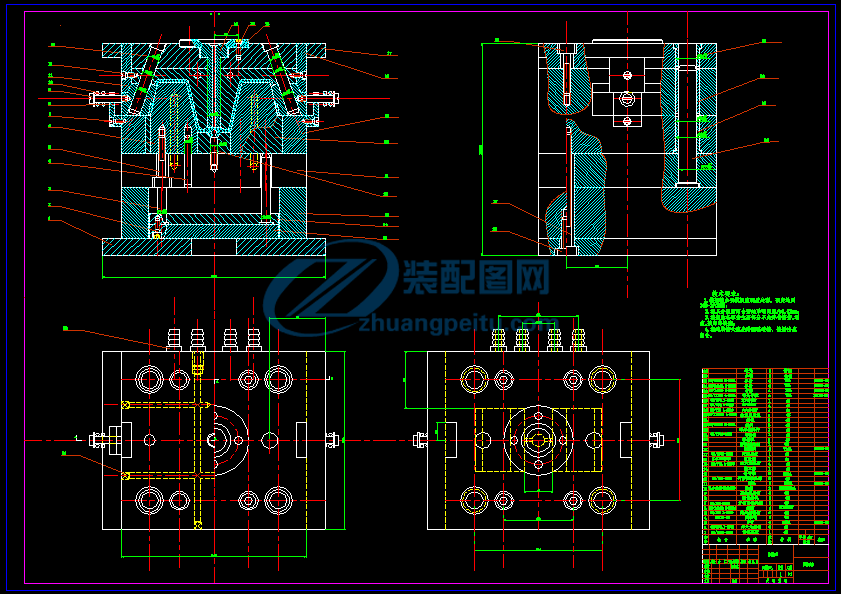
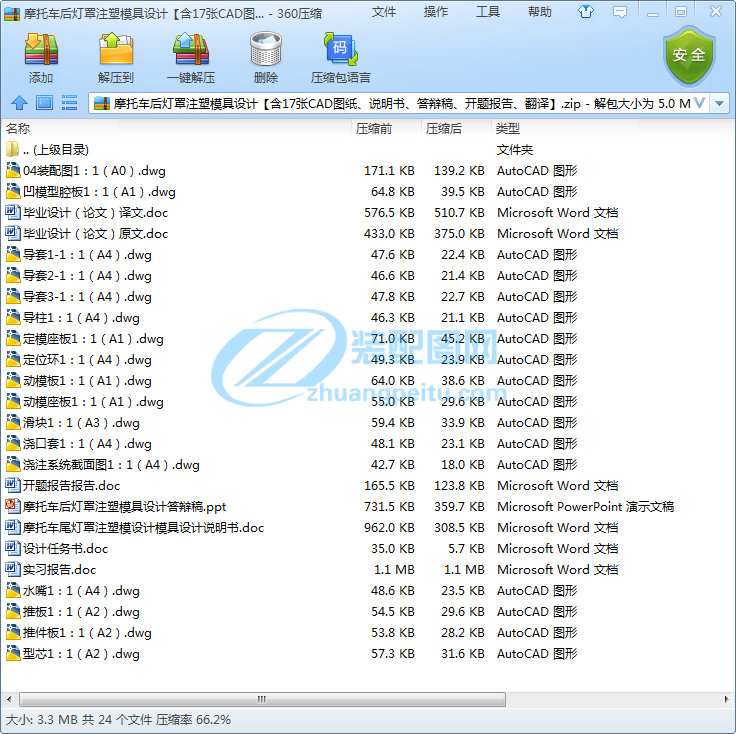
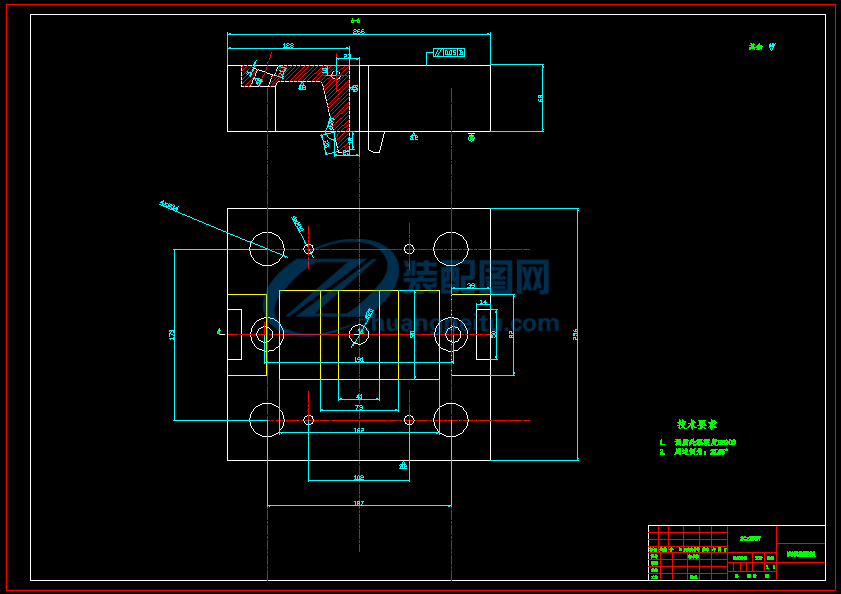
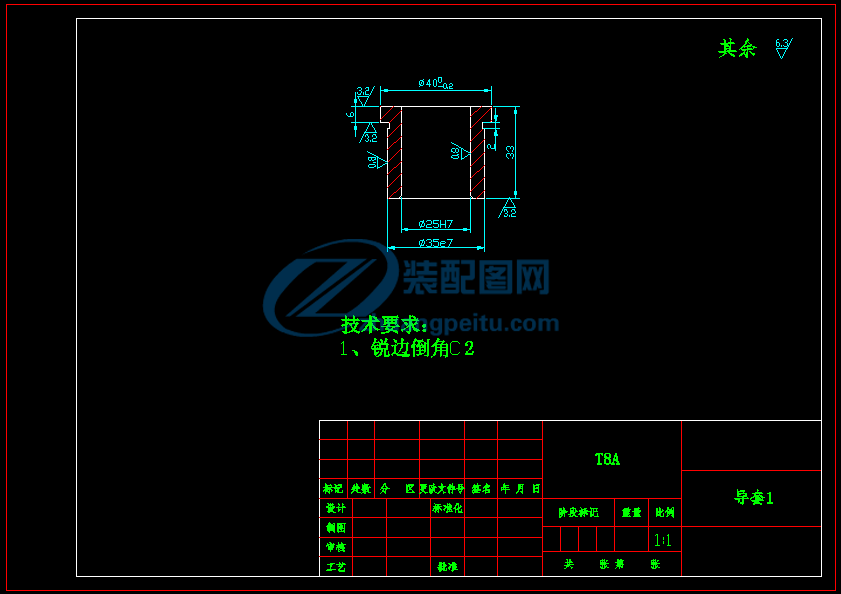

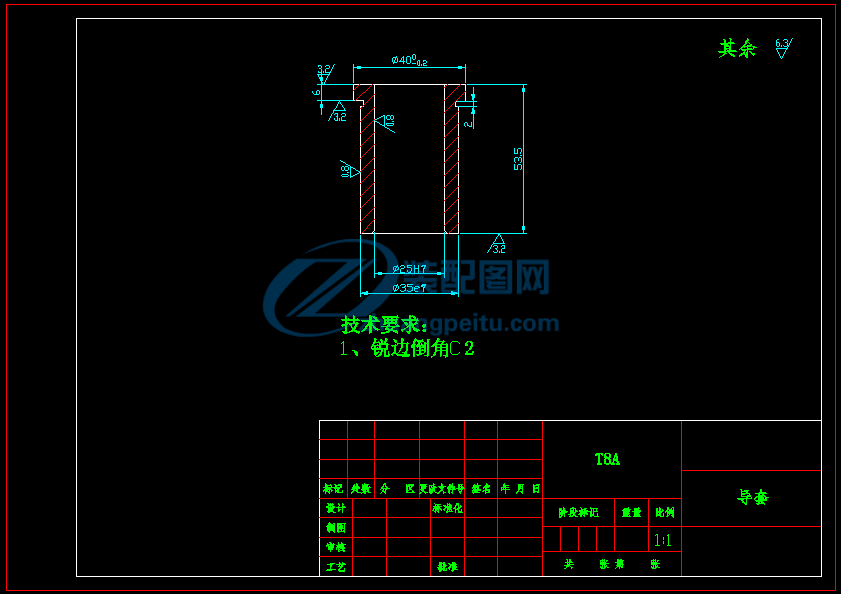
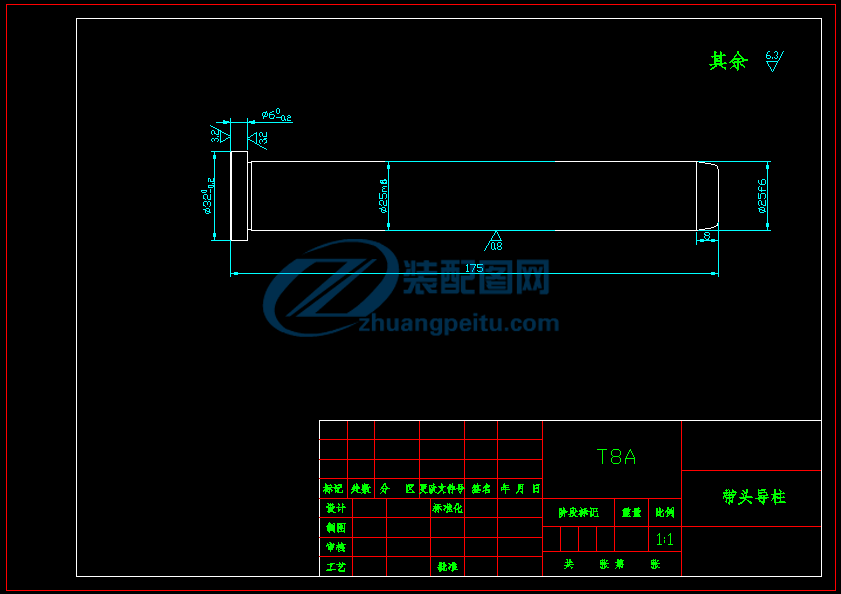
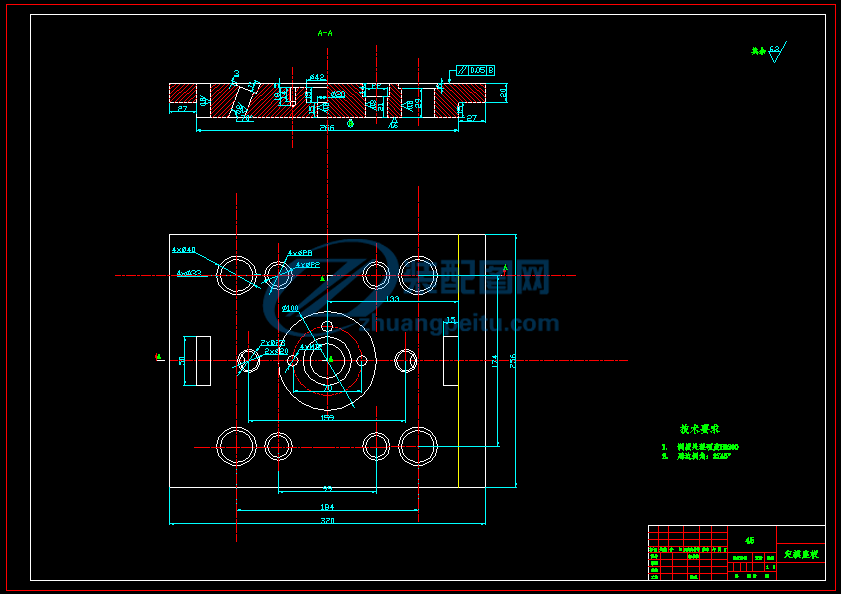
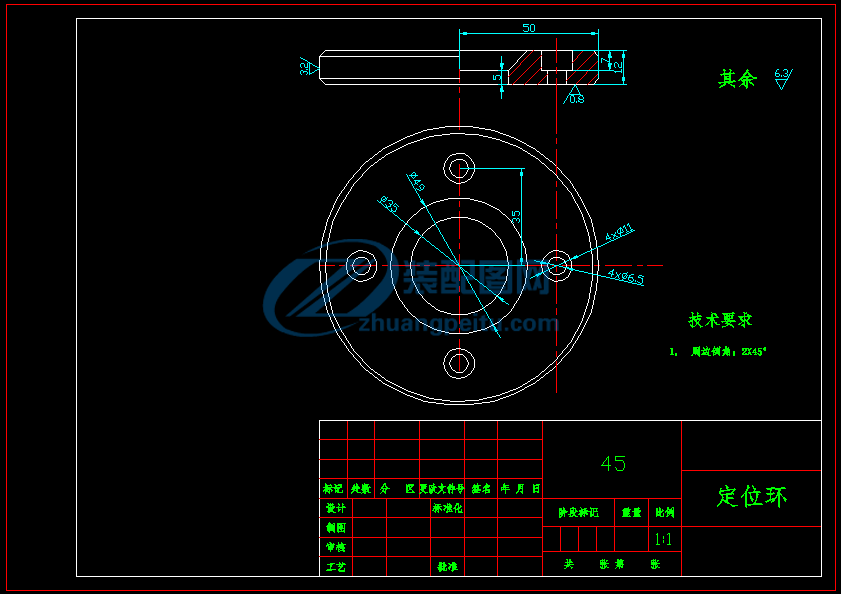
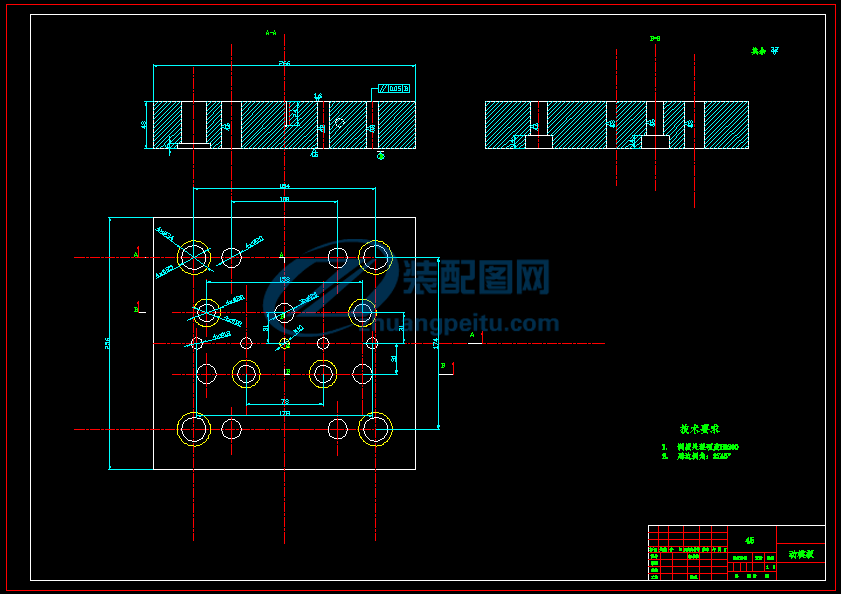
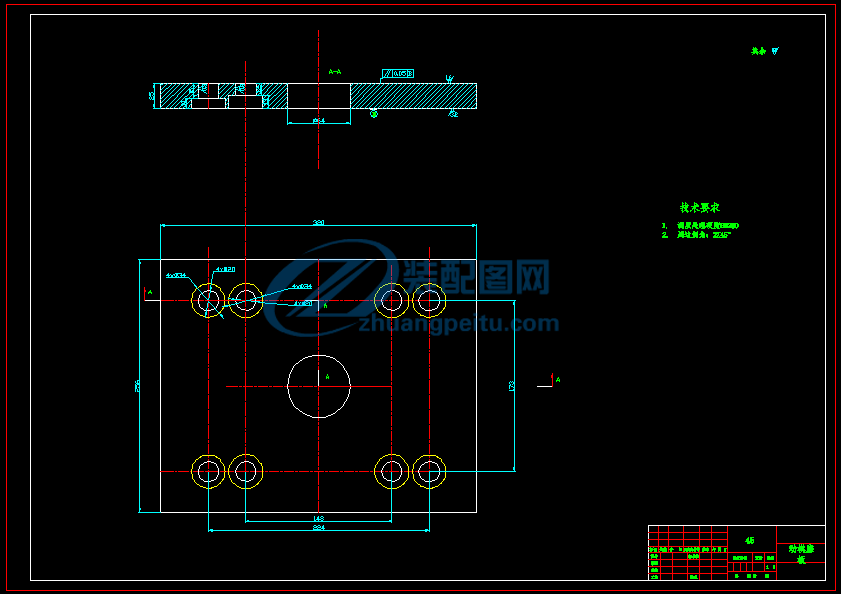
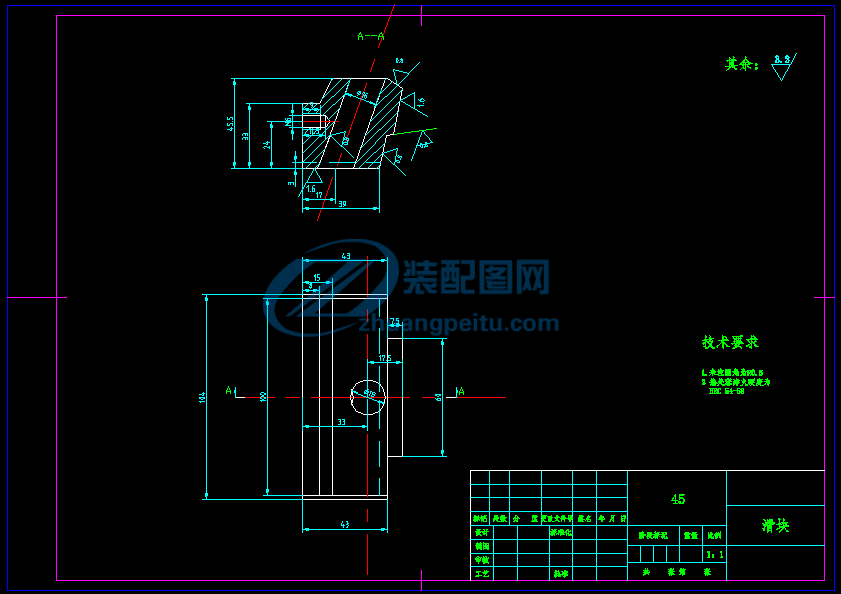
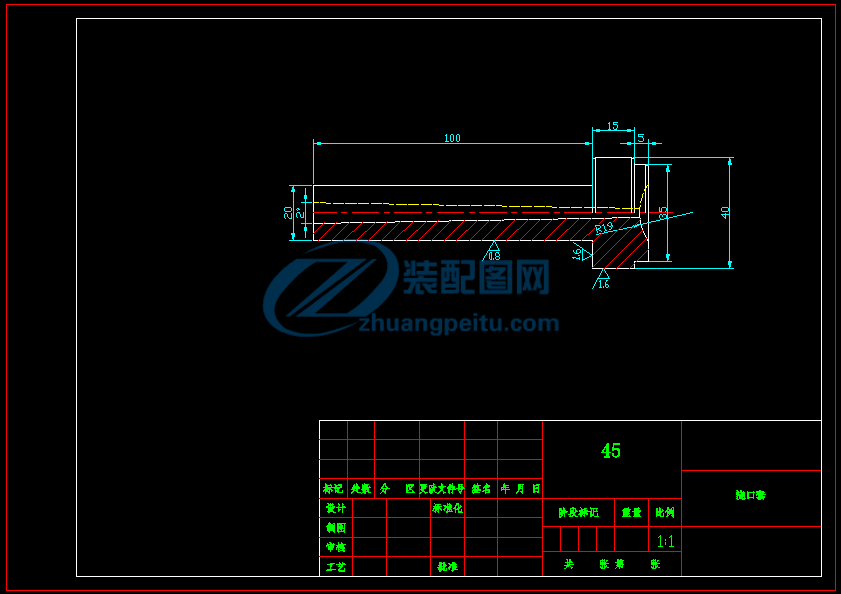
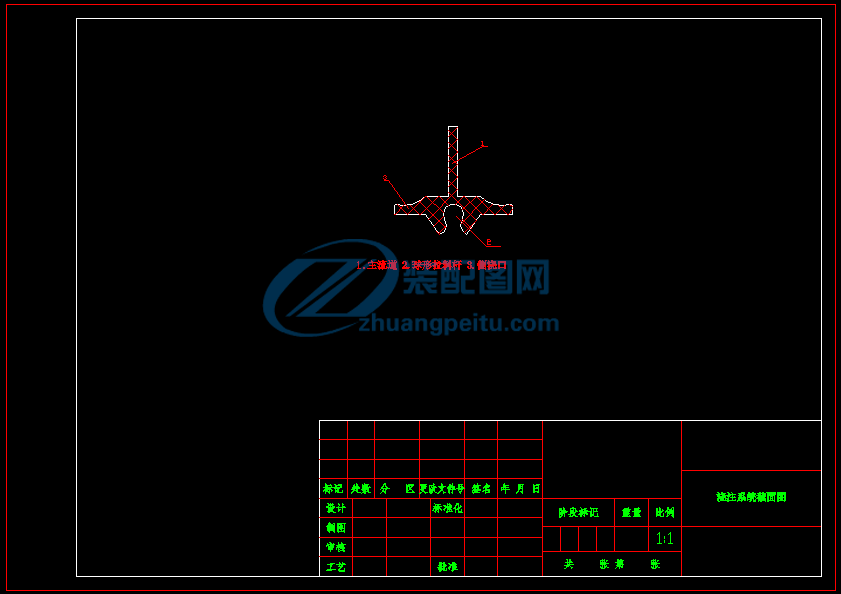
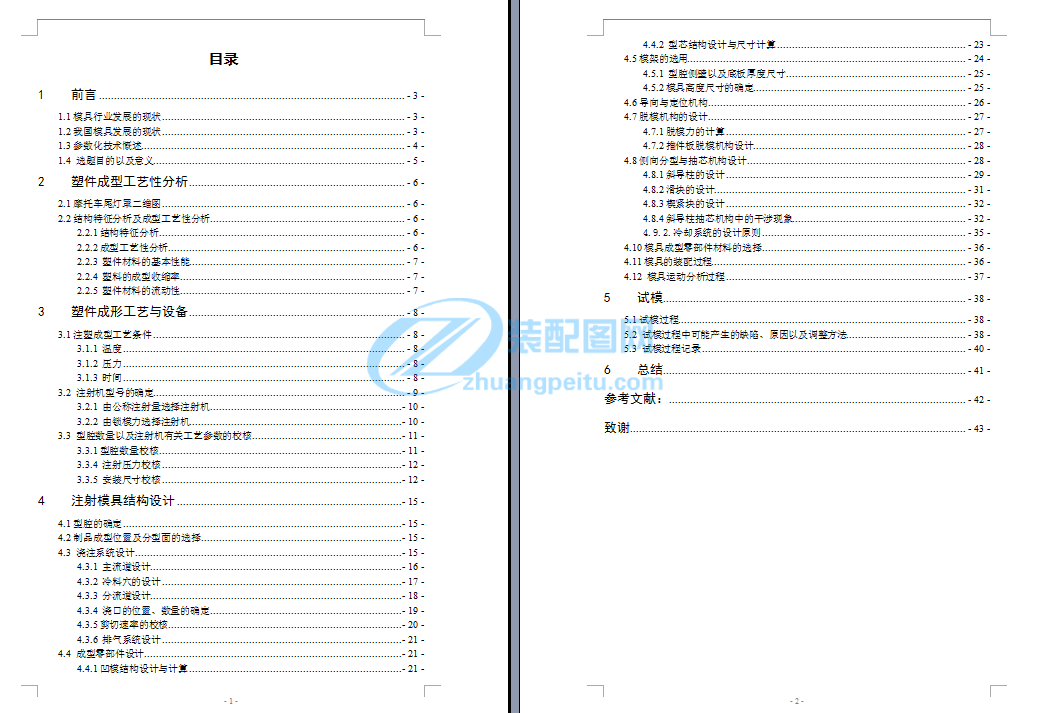
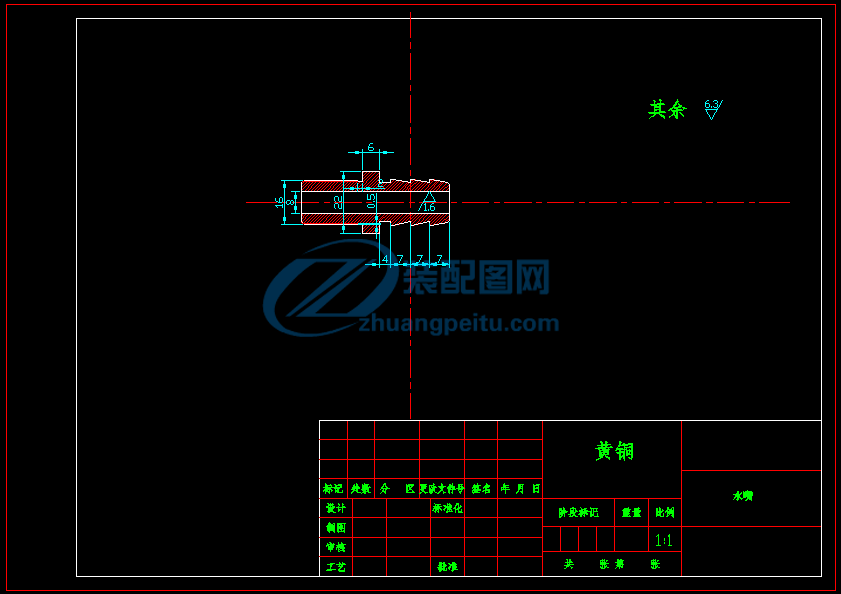
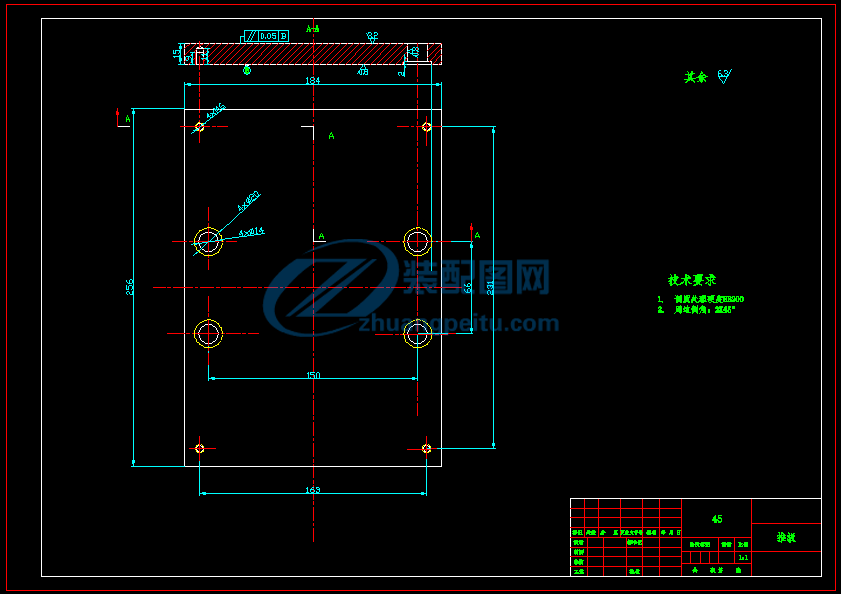
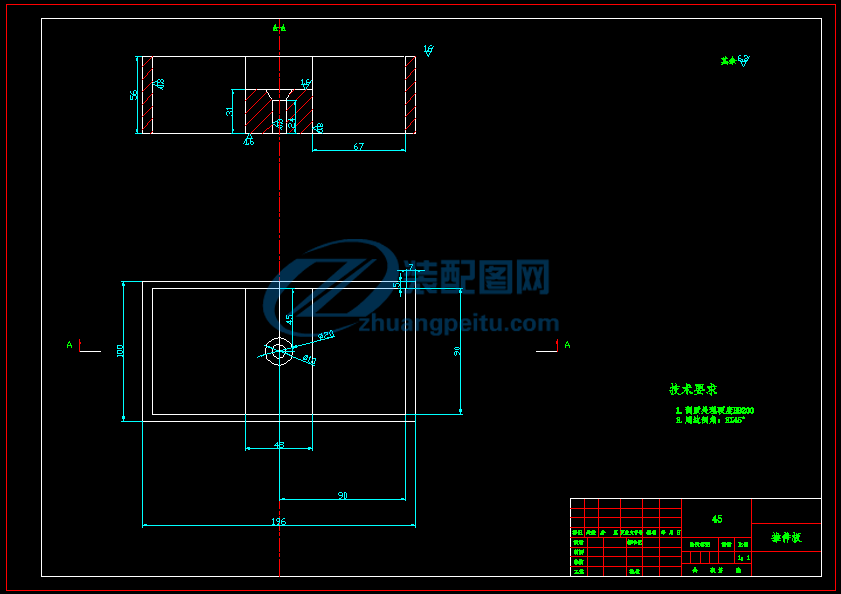
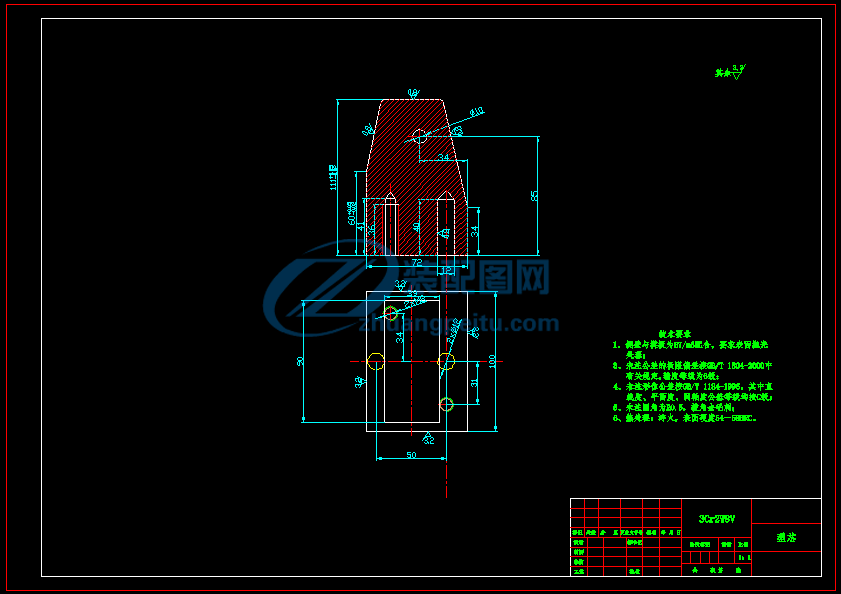
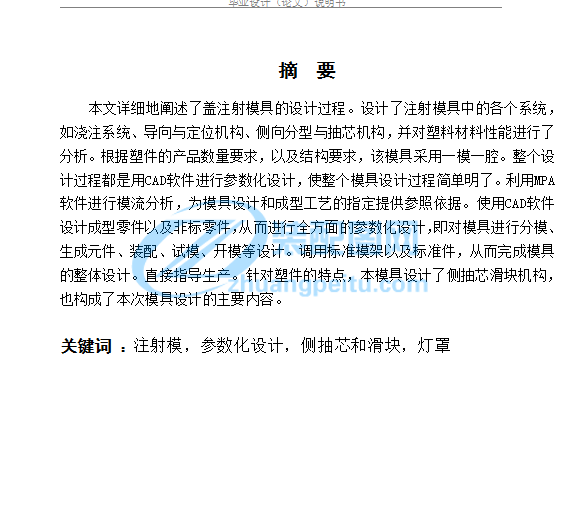
畢業(yè)設(shè)計翻譯原文題目名稱:摩托車后燈罩注塑模具模具設(shè)計 院系名稱: 班 級: 學(xué) 號: 學(xué)生姓名: 指導(dǎo)教師: 年 03 月畢業(yè)設(shè)計(論文)譯文- 1 -Temperature is to be deduced from measurement of the EMF generated. Standard material combinations are copper-constantan (60%Cu–40%Ni), chromel (10% Cr–90%Ni)-alumel (2%Al–90%Ni-Si-Mn) and platinum–rhodium. In metal machining applications, it is possible to embed such a standard thermocouple combination in a tool but it is difficult to make it small enough not to disturb the temperature distribution to be measured. One alter-native is to embed a single standard material, such as a wire, in the tool, to make a junction with the tool material or with the chip material at the tool/chip interface. By moving the junction from place to place, a view of the temperature distribution can be built up. Another alternative is to use the tool and work materials as A and B, with their junction at the chip/tool interface. By this means, the average contact temperature can be deduced. This application is considered first, with its difficulties stemming from the presence of intermediate metals across which there may be some temperature drop.Tool–work thermocouple measurementsFigure 5.14 shows a tool–work thermocouple circuit for the turning process. The 畢業(yè)設(shè)計(論文)譯文- 2 -hot junction is the chip/tool interface. To make a complete circuit, also including an EMF recorder, requires wires to be connected between the recorder and the tool and the recorder and the work. In the latter case, because the work is rotating, the wire must pass through some slip ring device. If the junctions A, B and C, between the work and slip ring, the slip ring and recorder wire and the tool and the recorder wire, are all at the same (cold junction) temperature, the circuit from A to C is all intermediate and has no effect on the EMF. But this is often not the case.Dry slip rings, with their rubbing interface, frequently create an EMF. The solution is to use a liquid mercury contact. If an indexable insert is used as the cutting edge, the distance from the hot junction to the cold junction C may be only 10 mm. In this case, to eliminate error due to C heating up, either the measurement time must be kept very short, or the insert must be extended in some way – for example by making the connection at C from the same material as the insert (but this is often not practical) – or the heating must be compensated. Figure 5.15 shows a cold junction compensation circuit and its principle. The single wire connection at C is replaced by a standard thermocouple pair of wires which are terminated across a potentiometer in a region where the temperature is not affected by the cutting. The connection to the EMF recorder is then taken from the potentiometer slider. The thermocouple wire materials are chosen so that the tool material has an intermediate EMF potential 畢業(yè)設(shè)計(論文)譯文- 3 -between them, relative to some third material, for example platinum. The slider is set at the point of interior division of the potentiometer, at the same ratio a/b as the tool material potential is intermediate between the two thermocouple materials. Copper and constantan are found suitable to span the potentials of most tool materials.Tool–work thermocouple calibrationThe EMF measured in cutting must be converted to temperature. Generally, the EMF temperature relation for tool–work thermocouples is non-linear. It can even vary between nominally the same tool and work materials. It is essential to calibrate the tool–work thermocouple using the same materials as in the cutting test. Figure 5.16 shows one calibration arrangement and Figure 5.17 shows its associated measurement circuit. In this arrangement, the tool–work thermocouple EMF is not measured directly. Instead, the EMF between the tool and a chromel wire is measured at the same time as that of achromel-alumel thermocouple at the same temperature. Thus, the tool–chromel EMF versus temperature characteristic is calibrated against the chromel–alumel standard. This repeated for the work–chromel combination. The tool–work EMF versus temperature relation is the difference between the tool–chromel and work–chromel relations.Figure 5.16 shows an overview of the tool or work in contact with the chromel–alumel thermocouple (detail in Figure 5.17). The contact is made at one focus of an infrared heating furnace with reflecting walls, shaped as an ellipsoid of revolution, with a 1kW halogen lamp at the other focus. The chromel–alumel thermocouple is fixed to the furnace body and the tool or work is pressed on to it by a spring. It is necessary to prepare the tool and work materials as rods in this method, but it is possible to heat the hot junction to 1000?C in about 10 s: the lengths of the rods, to avoid the need for cold junction compensation circuitry, need only be sufficient to be beyond the heat diffusion distance over this time. Example results, for a P10 carbide tool and a 0.45% plain carbon steel work, are given in Figure 5.18. Even at 1000?C the EMF is only 10mV,so a high sensitivity recorder is needed.Inserted thermocouple measurements畢業(yè)設(shè)計(論文)譯文- 4 -畢業(yè)設(shè)計(論文)譯文- 5 -Figure 5.19 shows two further possibilities of tool temperature measurement. In Figure 5.19(a),a small diameter hole has been bored in the tool and a fine standard thermocouple has been inserted in it. It has the advantage that a precise measurement of temperature at the bottom of the hole can be made, relying on the standard thermocouple, but a disadvantage that the hole may disturb the temperature gradients in the tool. If it is desired to measure the temperature distribution in the tool, while only boring one hole, the rake and clearance faces of the tool may be progressively ground away, to vary the position of the hole relative to the cutting edge.A finer hole may be bored if only one wire is to be inserted in it. Figure 5.19(b) shows a single wire, for example chromel, or in this case platinum, making contact with the work at the chip–tool interface. In this way, the temperature at a specified point can be measured, but it is necessary to calibrate the thermocouple, as was done with the tool–work thermocouple.畢業(yè)設(shè)計(論文)譯文- 6 -5.3.2 Radiation methodsInserted thermocouple methods require special modifications to the cutting tools. The tool–work thermocouple method only determines average contact temperatures; and cannot be used if the tool is an insulator. Thermal imaging methods, measuring the radiation from a surface, have a number of attractions, if surface temperatures are of interest.畢業(yè)設(shè)計(論文)譯文- 7 -The laws of electromagnetic energy radiation from a black body are well known. The power radiated per unit area per unit wavelength W depends on the absolute temperature l T and wavelength l according to Planck’s law:= (5.5)?W52?hc??1?kTche?where h (Planck’s constant) = 6.626 ×10 Js, c (speed of light) = 2.998 × 10 m/s 34 8and k (Boltmann’s constant) = 1.380 ×10 J/K.2Equation (5.5) can be differentiated to find at what wavelength the peak ?maxpower is radiated (or absorbed), or integrated to find the total power W. Wien’s displacement la and the Stefan–Boltzmann law result:(5.6) mKT??8.297max???41065TW???Figure 5.20 shows the characteristic radiation in accordance with these laws. Temperatures measured in industry are usually 2000K or less. Most energy is radiated in the infrared range (0.75mm to 50mm). Therefore, infrared measurement techniques are needed. Much care, however, must be taken, as real materials like cutting tools and work materials are not black bodies. The radiation from these materials is some fraction a of the black body value. a varies with surface roughness, state of oxidation and other factors. Calibration under the same conditions as cutting is necessary.