
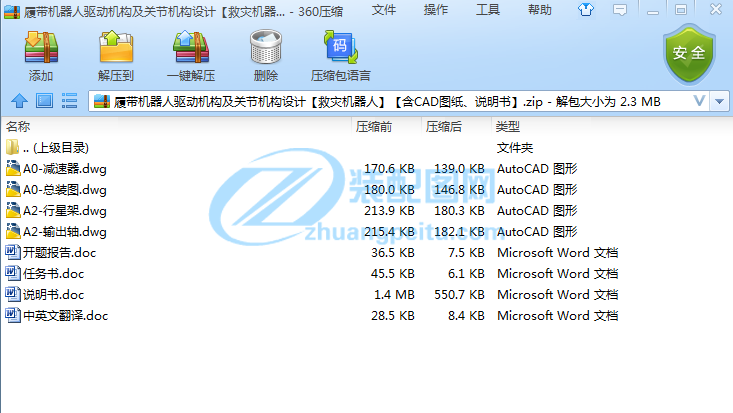


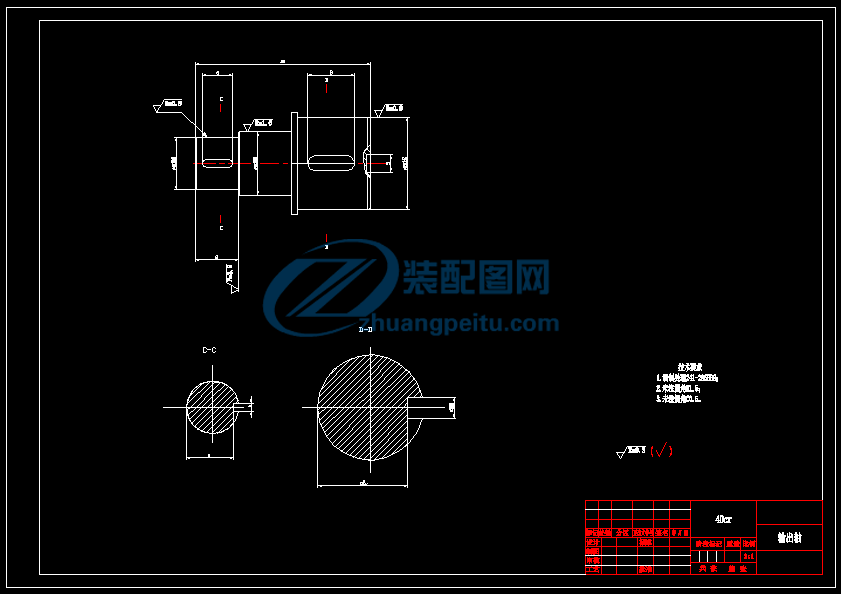
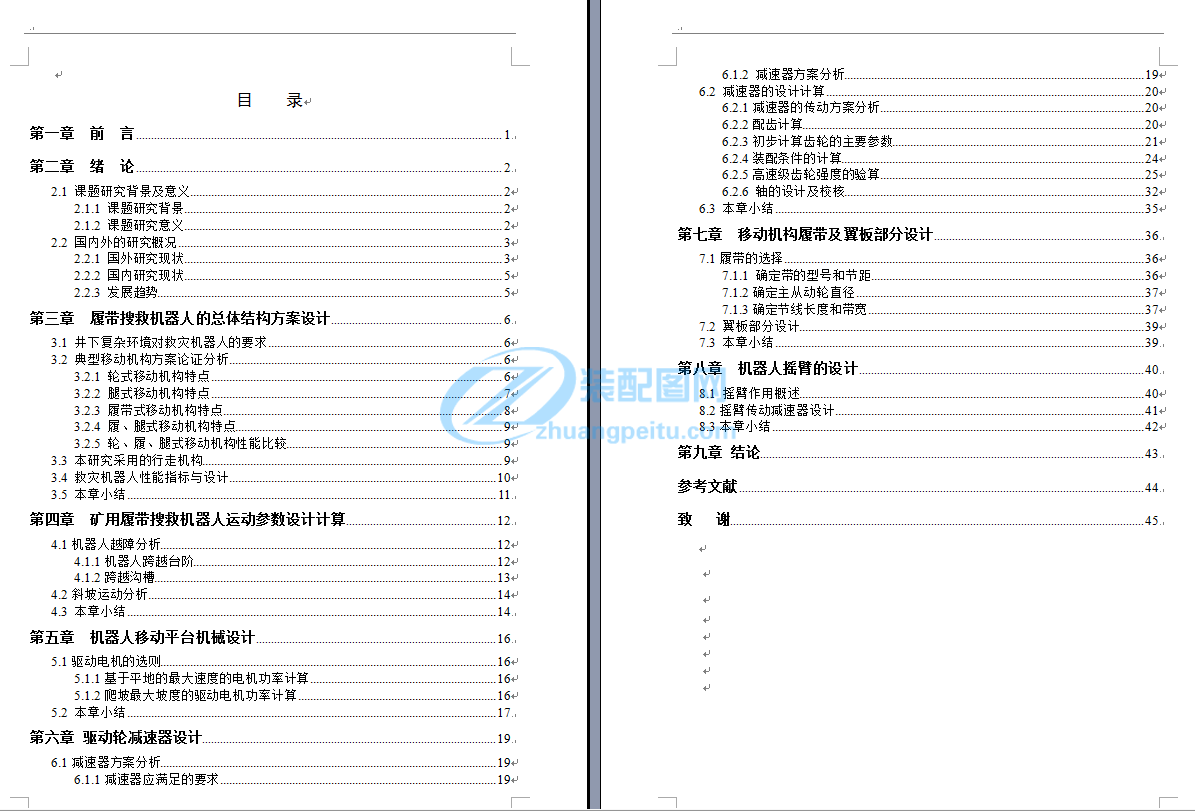
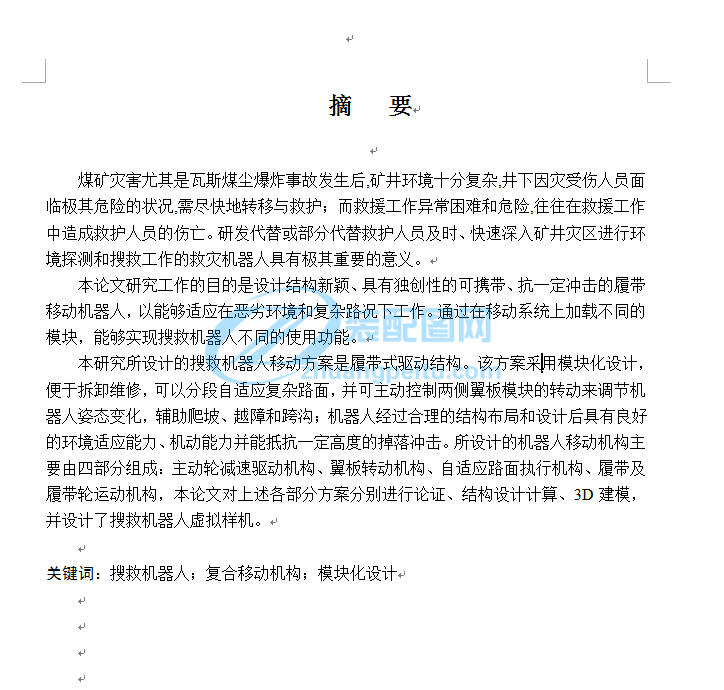
英文文獻翻譯學 生 姓 名:學 院:專 業(yè) 及 班 級 :學 號:指 導 教 師:Simple structure pipe inspection robotThis article describes the architecture of the original pipe inspection robot. The robot contains two universal joints by the hinge portion. Part of the parallel movement along the pipeline axis wheel drive, while the other part is forced to follow the axis of rotation of the wheel and the inclined pipe spiral motion related. A single motor is placed between the two institutions motion generated. All wheels mounted on the suspension, in order to adapt to changing curve pipe. The robot has its own battery and a wireless link. Four different diameters respectively of 170,70 and 40 mm. For smaller diameters, battery, radio receiver can be placed in any extra bodies. This architecture is very simple, its rotational motion can be used to scrub or inspection tasks.Keywords: autonomous mobile robot in pipeline inspection, spiral motionPipeline inspection robot has been studied for a long time, many of the original motion ideas have been proposed to solve the many technical difficulties in pipe diameter, curve and change-related energy supply. Although an exhaustive review of the literature is impossible, according to the limited space available, several major categories can be identified several broad categories:1 For a small number of projects to follow the earthworm principles: the central part axial movement, and both ends of the connected equipment with barrier pipes. This concept has been proposed pneumatic version,But they need the power cord. For smaller diameter (10 mm or less), according to the principle of inchworm, or driven by a sawtooth voltage based on inertial motion, or in combination with the differential coefficient of friction vibration fin, the piezoelectric drive.2 For a variety of medium-sized pipes, depending on the diameter of adaptability and cornering ability classical electromechanical systems have been proposed various structures involved in the wheel tracks and kinematics.3 For large pipes, pipe crawling walk has also been proposed.Four mobile robot proposed in this paper belongs to the second category, the liquidity of their tube diameter from 40 to 170mm, the design attempts to use a single drive to reduce the complexity of the realization of the machine along the tube, even though our research efforts can be seen as an independent to result. But this spiral theory seems to have been studied.The robot is divided into two parts, the stator and rotor, including a DC connection, motor and gearhead, universal joints. The stator is equipped with a set of wheels to help movement parallel; in this case, the constraint along the tube axis of the stator, the rotor wheel only along the helical path, the axial velocity and the relationship between the rotational speed of the robotWherein R is the pipe radius, a is the inclination angle of the wheel. Stator and rotor must ensure stability, to ensure that the pipeline and sufficient contact force between the robot to adapt to changes and obstacles pipe diameter and allows travel in a curved pipe. For larger robot (D -170), the robot is rigidly connected to the motor shaft to ensure stability. For smaller diameter, bend the need for greater freedom, requires twice the number of wheels.Diameter of 70 mm or more robots provide nine cells, located in the stator. Tests showed that the smaller diameter, this configuration is not possible. First by the rotor, and the second one includes a motor and gear, and the third is the stator wheel to the axle, energy supply and telecommunications networks. Two schemes were investigated 70mm diameter. In the first, a motor and a battery mounted on the stator, but can not be used in the second scenario, if the robot using a power cable.中文翻譯:簡單結構管道檢測機器人本文介紹了管道檢測機器人的原始架構。該機器人由包含兩個萬向節(jié)鉸接部分。一部分是沿管道平行移動的軸車輪盤,而另一部分則是被迫遵循與螺旋運動有關的軸線旋轉的車輪傾斜管。單臺電動機被放置在兩個機構之間產(chǎn)生的運動。所有車輪安裝在懸架上,以適應不斷變化的曲線管道。該機器人有其自己的電池和無線鏈路。四種不同管徑分別為的 170,70 和 40 毫米。對于較小的直徑,電池,無線電接收器,可放置在其他額外的機構中。這種架構非常簡單,其旋轉運動可以被利用來進行擦洗或檢驗任務。關鍵詞:自主移動機器人,在管道檢測,螺旋運動管道檢測機器人已經(jīng)被研究了很長一段時間,許多原來的運動觀念被提出來解決在管道直徑,曲線和能源供應變化中有關的許多技術困難。雖然一個詳盡的文獻回顧是不可能的,根據(jù)有限的可用空間,幾大類別,可確定幾大類別:1 對于小規(guī)模,許多項目遵循蚯蚓原則:中央部分組成軸向移動,而兩端連接的設備具有阻隔管道。這一概念已經(jīng)提出氣動版本,但他們需要電力臍帶。對于較小的直徑(10 毫米或更?。?,根據(jù)尺蠖的原則,或根據(jù)慣性運動由鋸齒波電壓驅動,或使用與微分摩擦系數(shù)振動鰭,則采用壓電驅動。2 對于各種中型管道,根據(jù)直徑的適應性和轉彎能力古典機電系統(tǒng)已提出各種涉及車輪和軌道運動學結構。3 對于大型管道,管道爬行走路也已提出。文中提出的四個移動機器人屬于第二類,他們的管直徑從 40 到 170mm,該設計嘗試使用單一驅動器減少機器的復雜性實現(xiàn)沿管的的流動性,即使我們的研究可看作一個獨立努力地結果。但此螺旋論似乎已經(jīng)被研究過。該機器人主要分為兩部分,定子和轉子,包括一個 DC 連接,馬達與減速機,萬向節(jié)。定子配備了一套輪子,有助于運動平行; 在這種情形下,定子約束沿著管軸,而轉子的車輪只能沿著螺旋軌跡,該機器人之間的軸向速度和旋轉速度的關系 。?tgRwv??其中 R 為管道半徑, a 是車輪傾斜角度。定子和轉子必須保證穩(wěn)定性,以保證機器人之間的管道和足夠的接觸力,以適應管道直徑的變化和障礙,并允許在彎曲的管道中行駛。對于更大型的機器人(D -170) ,機器人是硬性連接到電機軸上來確保穩(wěn)定性。對于規(guī)模較小的直徑,彎管需要更大程度的自由,需要兩倍的數(shù)量的輪子。直徑 70 毫米以上的機器人提供了 9 個電池,分布在電機定子上。試驗表明,對于規(guī)模較小的直徑,這個配置是不可能的。第一個由轉子組成,第二個包括電機和減速器,第三個是定子車輪與軸,能源供應和電信網(wǎng)絡。兩個方案進行了 70mm 直徑的調(diào)查。在第一個中,馬達和電池安裝在定子上,但卻無法用在第二個方案中,如果機器人使用纜索電源。