有凸緣圓筒形件端蓋拉深成形沖壓工藝及模具設(shè)計【落料拉深復(fù)合模含14張CAD圖】
【需要咨詢購買全套設(shè)計請加QQ1459919609】圖紙預(yù)覽詳情如下:



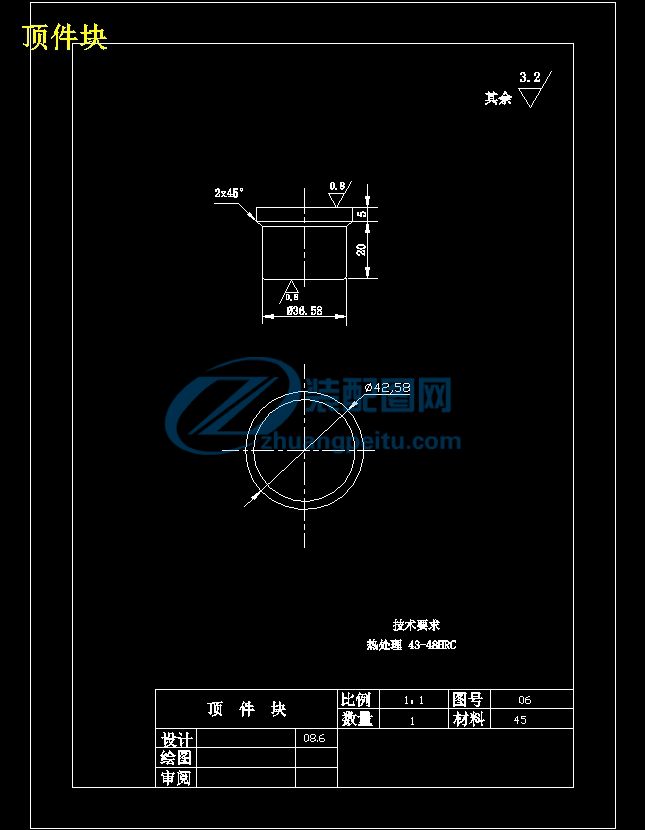

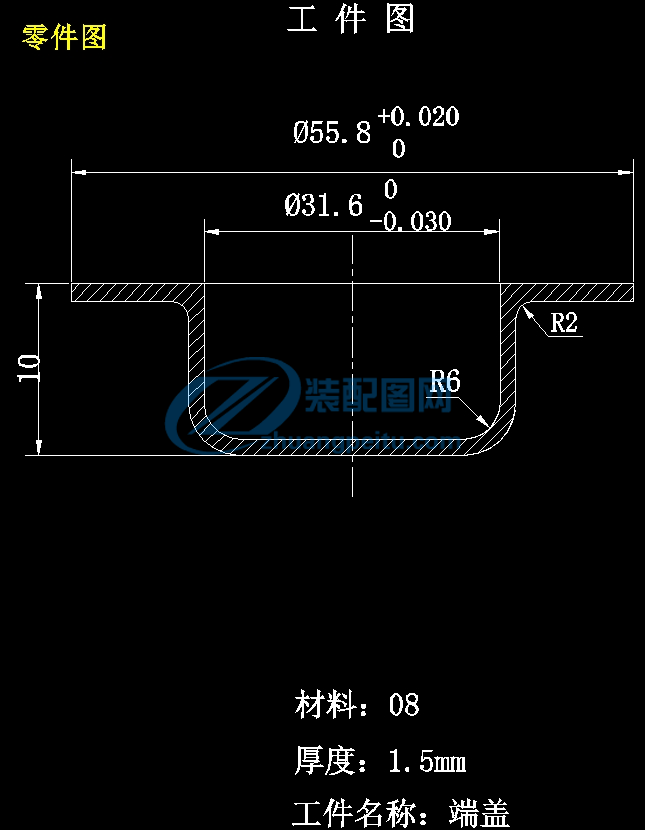


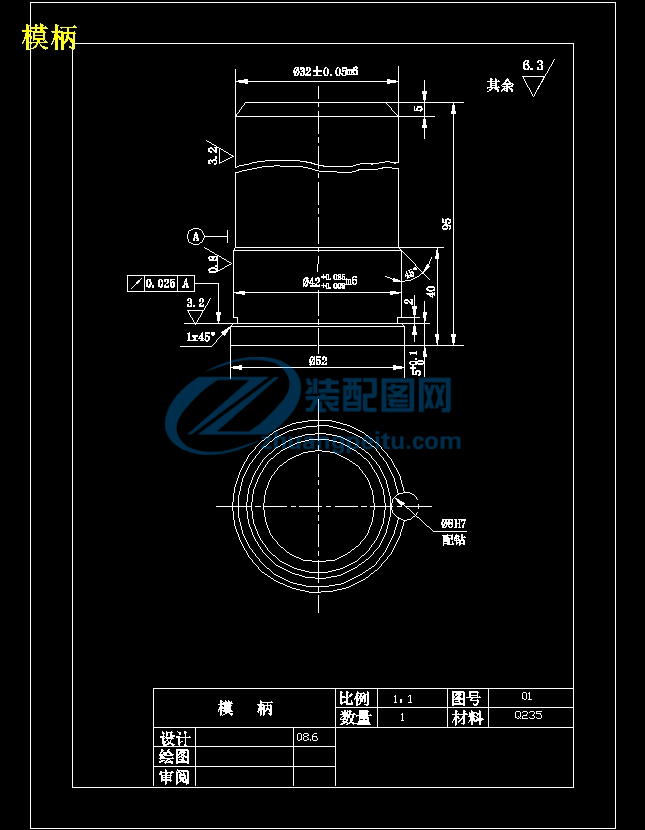

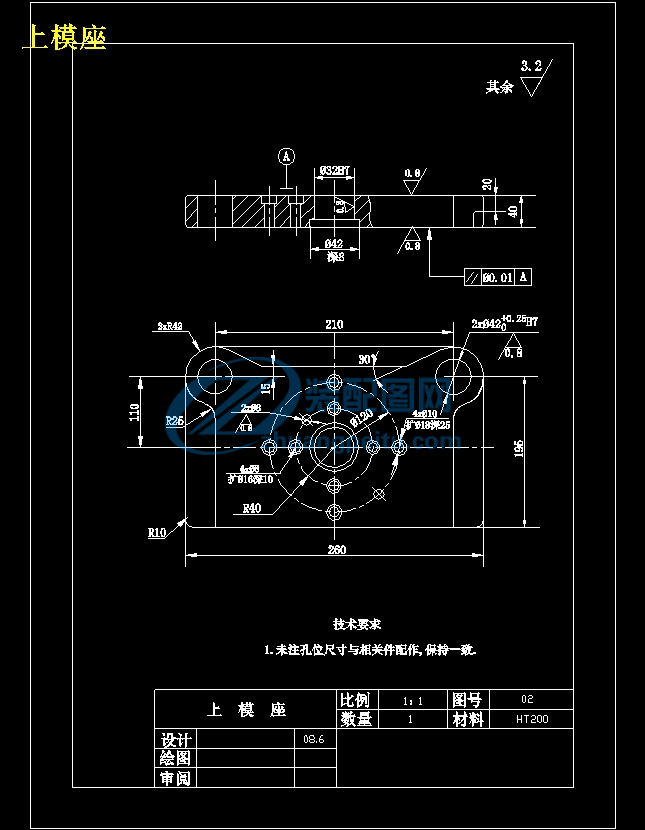


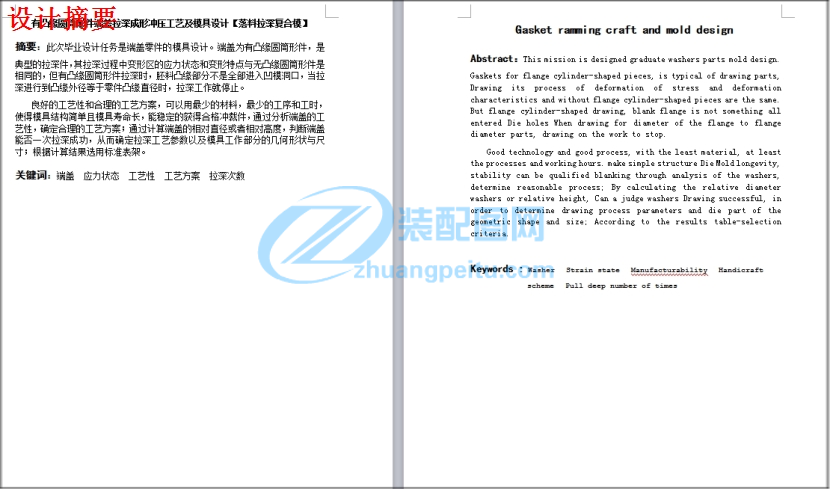

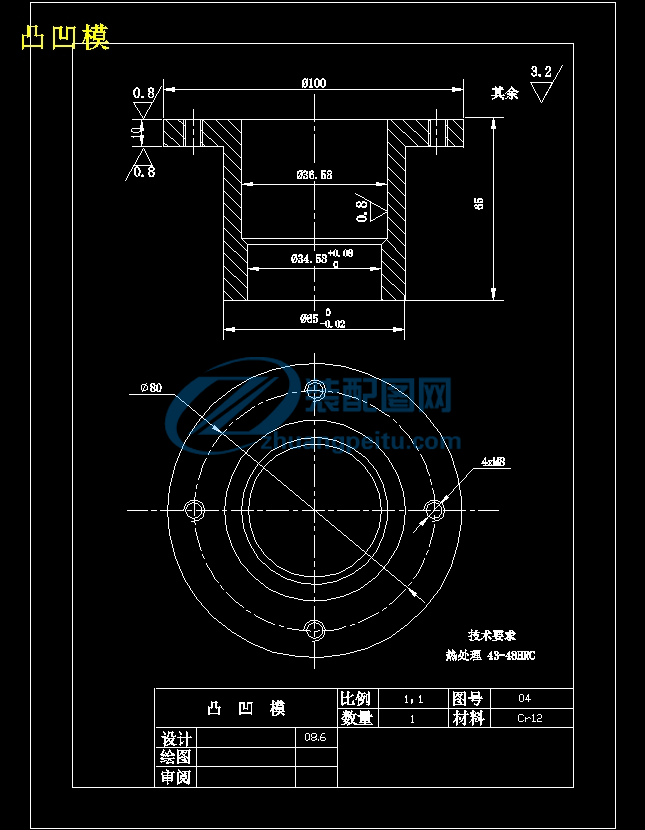
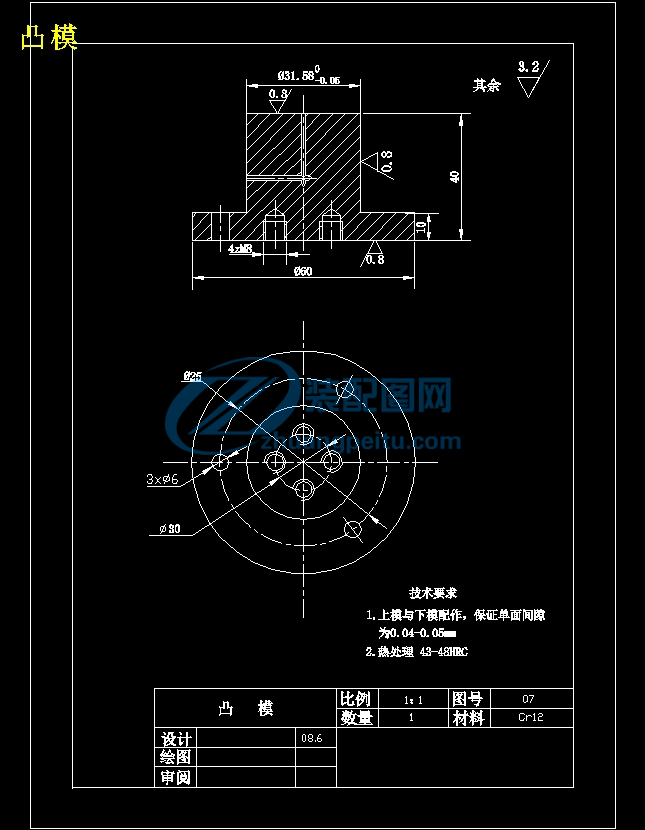
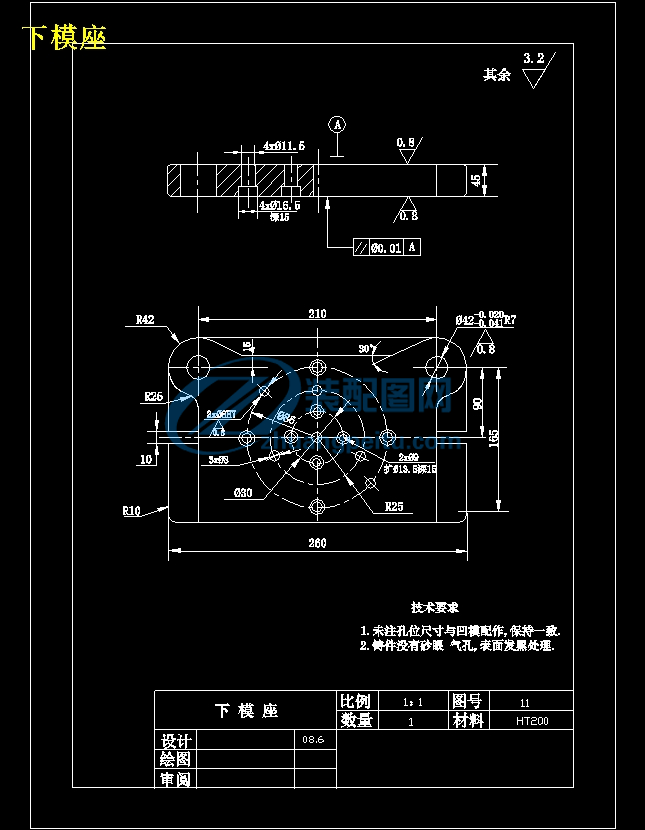

01 緒論目前,我國沖壓技術(shù)與工業(yè)發(fā)達國家相比還相當(dāng)?shù)穆浜?,主要原因是我國在沖壓基礎(chǔ)理論及成形工藝、模具標(biāo)準(zhǔn)化、模具設(shè)計、模具制造工藝及設(shè)備等方面與工業(yè)發(fā)達的國家尚有相當(dāng)大的差距,導(dǎo)致我國模具在壽命、效率、加工精度、生產(chǎn)周期等方面與工業(yè)發(fā)達國家的模具相比差距相當(dāng)大。1.1 國內(nèi)模具的現(xiàn)狀和發(fā)展趨勢1.1.1 國內(nèi)模具的現(xiàn)狀我國模具近年來發(fā)展很快,據(jù)不完全統(tǒng)計,2003 年我國模具生產(chǎn)廠點約有 2 萬多家,從業(yè)人員約 50 多萬人,2004 年模具行業(yè)的發(fā)展保持良好勢頭,模具企業(yè)總體上訂單充足,任務(wù)飽滿,2004 年模具產(chǎn)值 530 億元。進口模具 18.13 億 美元,出口模具4.91 億美元,分別比 2003 年增長 18%、32.4%和 45.9%。進出口之比 2004 年為3.69:1,進出口相抵后的進凈口達 13.2 億美元,為凈進口量較大的國家。在 2 萬多家生產(chǎn)廠點中,有一半以上是自產(chǎn)自用的。在模具企業(yè)中,產(chǎn)值過億元的模具企業(yè)只有 20 多家,中型企業(yè)幾十家,其余都是小型企業(yè)。 近年來, 模具行業(yè)結(jié)構(gòu)調(diào)整和體制改革步伐加快,主要表現(xiàn)為:大型、精密、復(fù)雜、長壽命中高檔模具及模具標(biāo)準(zhǔn)件發(fā)展速度快于一般模具產(chǎn)品;專業(yè)模具廠數(shù)量增加,能力提高較快;"三資"及私營企業(yè)發(fā)展迅速;國企股份制改造步伐加快等。雖然說我國模具業(yè)發(fā)展迅速,但遠遠不能適應(yīng)國民經(jīng)濟發(fā)展的需要。我國尚存在以下幾方面的不足:第一,體制不順,基礎(chǔ)薄弱。 “三資”企業(yè)雖然已經(jīng)對中國模具工業(yè)的發(fā)展起了積極的推動作用,私營企業(yè)近年來發(fā)展較快,國企改革也在進行之中,但總體來看,體制和機制尚不適應(yīng)市場經(jīng)濟,再加上國內(nèi)模具工業(yè)基礎(chǔ)薄弱,因此,行業(yè)發(fā)展還不盡如人意,特別是總體水平和高新技術(shù)方面。 第二,開發(fā)能力較差,經(jīng)濟效益欠佳.我國模具企業(yè)技術(shù)人員比例低,水平較低,且不重視產(chǎn)品開發(fā),在市場中經(jīng)常處于被動地位。我國每個模具職工平均年創(chuàng)造產(chǎn)值約合 1 萬美元,國外模具工業(yè)發(fā)達國家大多是 15~20 萬美元,有的高達 25~30 萬美元,與之相對的是我國相當(dāng)一部分模具企業(yè)還沿用過去作坊式管理,真正實現(xiàn)現(xiàn)代化企業(yè)管理的企業(yè)較少。 1第三,工藝裝備水平低,且配套性不好,利用率低.雖然國內(nèi)許多企業(yè)采用了先進的加工設(shè)備,但總的來看裝備水平仍比國外企業(yè)落后許多,特別是設(shè)備數(shù)控化率和CAD/CAM 應(yīng)用覆蓋率要比國外企業(yè)低得多。由于體制和資金等原因,引進設(shè)備不配套,設(shè)備與附配件不配套現(xiàn)象十分普遍,設(shè)備利用率低的問題長期得不到較好解決。裝備水平低,帶來中國模具企業(yè)鉗工比例過高等問題。第四,專業(yè)化、標(biāo)準(zhǔn)化、商品化的程度低、協(xié)作差. 由于長期以來受“大而全”“小而全”影響,許多模具企業(yè)觀念落后,模具企業(yè)專業(yè)化生產(chǎn)水平低,專業(yè)化分工不細,商品化程度也低。目前國內(nèi)每年生產(chǎn)的模具,商品模具只占 45%左右,其馀為自產(chǎn)自用。模具企業(yè)之間協(xié)作不好,難以完成較大規(guī)模的模具成套任務(wù),與國際水平相比要落后許多。模具標(biāo)準(zhǔn)化水平低,標(biāo)準(zhǔn)件使用覆蓋率低也對模具質(zhì)量、成本有較大影響,對模具制造周期影響尤甚。 第五,模具材料及模具相關(guān)技術(shù)落后.模具材料性能、質(zhì)量和品種往往會影響模具質(zhì)量、壽命及成本,國產(chǎn)模具鋼與國外進口鋼相比,無論是質(zhì)量還是品種規(guī)格,都有較大差距。塑料、板材、設(shè)備等性能差,也直接影響模具水平的提高。1.1.2 國內(nèi)模具的發(fā)展趨勢巨大的市場需求將推動中國模具的工業(yè)調(diào)整發(fā)展。雖然我國的模具工業(yè)和技術(shù)在過去的十多年得到了快速發(fā)展,但與國外工業(yè)發(fā)達國家相比仍存在較大差距,尚不能完全滿足國民經(jīng)濟高速發(fā)展的需求。未來的十年,中國模具工業(yè)和技術(shù)的主要發(fā)展方向包括以下幾方面: 1) 模具日趨大型化; 2)在模具設(shè)計制造中廣泛應(yīng)用 CAD/CAE/CAM 技術(shù); 3)模具掃描及數(shù)字化系統(tǒng); 4)在塑料模具中推廣應(yīng)用熱流道技術(shù)、氣輔注射成型和高壓注射成型技術(shù); 5)提高模具標(biāo)準(zhǔn)化水平和模具標(biāo)準(zhǔn)件的使用率; 6)發(fā)展優(yōu)質(zhì)模具材料和先進的表面處理技術(shù); 7)模具的精度將越來越高; 8)模具研磨拋光將自動化、智能化; 29)研究和應(yīng)用模具的高速測量技術(shù)與逆向工程; 10)開發(fā)新的成形工藝和模具。1.2 國外模具的現(xiàn)狀和發(fā)展趨勢模具是工業(yè)生產(chǎn)關(guān)鍵的工藝裝備,在電子、建材、汽車、電機、電器、儀器儀表、家電和通訊器材等產(chǎn)品中,60%-80%的零部件都要依靠模具成型。用模具生產(chǎn)制作表現(xiàn)出的高效率、低成本、高精度、高一致性和清潔環(huán)保的特性,是其他加工制造方法所無法替代的。模具生產(chǎn)技術(shù)水平的高低,已成為衡量一個國家制造業(yè)水平高低的重要標(biāo)志,并在很大程度上決定著產(chǎn)品的質(zhì)量、效益和新產(chǎn)品的開發(fā)能力。近幾年,全球模具市場呈現(xiàn)供不應(yīng)求的局面,世界模具市場年交易總額為 600~650 億美元左右。美國、日本、法國、瑞士等國家年出口模具量約占本國模具年總產(chǎn)值的三分之一。 國外模具總量中,大型、精密、復(fù)雜、長壽命模具的比例占到 50%以上;國外模具企業(yè)的組織形式是"大而專"、"大而精"。2004 年中國模協(xié)在德國訪問時,從德國工、模具行業(yè)組織--德國機械制造商聯(lián)合會(VDMA)工模具協(xié)會了解到,德國有模具企業(yè)約 5000 家。2003 年德國模具產(chǎn)值達 48 億歐元。其中(VDMA)會員模具企業(yè)有 90 家,這 90 家骨干模具企業(yè)的產(chǎn)值就占德國模具產(chǎn)值的 90%,可見其規(guī)模效益。 隨著時代的進步和技術(shù)的發(fā)展,國外的一些掌握和能運用新技術(shù)的人才如模具結(jié)構(gòu)設(shè)計、模具工藝設(shè)計、高級鉗工及企業(yè)管理人才,他們的技術(shù)水平比較高.故人均產(chǎn)值也較高.我國每個職工平均每年創(chuàng)造模具產(chǎn)值約合 1 萬美元左右,而國外模具工業(yè)發(fā)達國家大多 15~20 萬美元,有的達到 25~30 萬美元。國外先進國家模具標(biāo)準(zhǔn)件使用覆蓋率達 70%以上,而我國才達到 45%.1.3 端蓋拉深件模具設(shè)計與制造方面1.3.1 端蓋拉深模具設(shè)計的設(shè)計思路拉深是沖壓基本工序之一,它是利用拉深模在壓力機作用下,將平板坯料或空心工序件制成開口空心零件的加工方法。它不僅可以加工旋轉(zhuǎn)體零件,還可以加工盒形零件及其他形狀復(fù)雜的薄壁零件,但是,加工出來的制件的精度都很底。一般情況下,拉深件的尺寸精度應(yīng)在 IT13 級以下,不宜高于 IT11 級。3只有加強拉深變形基礎(chǔ)理論的研究,才能提供更加準(zhǔn)確、實用、方便的計算方法,才能正確地確定拉深工藝參數(shù)和模具工作部分的幾何形狀與尺寸,解決拉深變形中出現(xiàn)的各種實際問題,從而,進一步提高制件質(zhì)量。圓筒件是最典型的拉深件,其工作過程很簡單就一個拉深,根據(jù)計算確定它不能一次拉深成功.因此,需要多次拉深。在最后的一次拉深中由于制件的高度太高,根據(jù)計算的結(jié)果和選用的標(biāo)準(zhǔn)模架,判斷此次拉深不能采用標(biāo)準(zhǔn)的模架。為了保證制件的順利加工和順利取件,模具必須有足夠高度。要改變模具的高度,只有從改變導(dǎo)柱和導(dǎo)套的高度。導(dǎo)柱和導(dǎo)套的高度可根據(jù)拉深凸模與拉深凹模工作配合長度決定.設(shè)計時可能高度出現(xiàn)誤差,應(yīng)當(dāng)邊試沖邊修改高度。1.3.2 端蓋落料拉深模具設(shè)計的進度1.了解目前國內(nèi)外沖壓模具的發(fā)展現(xiàn)狀,所用時間 10 天;2.確定加工方案,所用時間 2 天;3.模具的設(shè)計,所用時間 10 天;4.模具的調(diào)試.所用時間 3 天.2 工藝分析4工件名稱:端 蓋生產(chǎn)批量:小批量材料:08 號鋼厚度:1.5mm工件簡圖如圖 1 所示:圖 1 端 蓋2.1 沖壓零件的工藝性分析圖示零件材料為 08 號鋼板,具有良好的沖壓性能,能夠進行一般的沖壓加工,市場上也容易得到這種材料,價格適中。2.1.1 外形落料的工藝性:該工件尺寸較小,料厚 1.5mm,外形簡單,尺寸精度要求一般,因此可采用落料工藝獲得。2.1.1 拉深的工藝性:此工件為有凸緣圓筒形工件,要求內(nèi)形尺寸,沒有厚度不變的要求,尺寸精度要求一般,且該工件的形狀滿足拉深的工藝要求,故可采用拉深工序加工。此工件只有外形落料和拉深兩個工序。圖示零件尺寸 mm、 03.61??mm,按慣例取 IT12 級,符合一般級進沖壓的經(jīng)濟精度要求,模具精度取02.85??IT10 級即可。由以上分析可知,圖示零件具有比較好的沖壓工藝性,適合沖壓生產(chǎn)。2.2 排樣設(shè)計2.2.1 確定零件的排樣方案5設(shè)計模具時,條料的排樣很重要。有凸緣園筒工件的形狀簡單,且對稱,故可采用直排。圖 2 條料的排樣2.2.2 條料寬度的計算查表取得搭邊值為 1.0mm 和 1.2mm。 計算毛坯直徑 如上圖所示,d =55.8mm, d=(31.6+1.5)mm=33.1mm, 工件的相對直徑t= =1.67。根據(jù)相對直徑查表得t 1.385修邊余量 △h=2.0mm 。由表 4.3.3 序號 11 查得有凸緣圓筒形件的毛坯尺寸計算公式為:D= 23421212221 56.482 drdrhrd ??????將 d =(d + △h )mm=(55.8+2)mm=57.8mm, h=6.5mm, r =2mm , r =6mm4t 12d =33.1mm , d =38.6mm , d =19.6mm231代入上式,即得毛坯的直徑為:D=56mm條料寬度的計算:擬采用無側(cè)壓裝置的送料方式,由 b-Δ =〔D+2a +c1〕 - Δ 0D—條料寬度方向沖裁件的最大尺寸a—側(cè)搭邊值c1—導(dǎo)料板與最寬條料之間的間隙代入數(shù)據(jù)計算,取得條料寬度為 60mm。導(dǎo)尺間距離的計算:由 s=D+2(a+c1),代入數(shù)據(jù)計算得導(dǎo)尺間距離為 61 mm。2.2.3 材料利用率的計算根據(jù)一般的市場供應(yīng)情況,原材料選用 1000 mm×2000 mm×1.5mm 的冷軋薄鋼板。6每塊可剪 2000mm ×60 mm 規(guī)格條料 16 條,材料剪切利用率達 94.5%。由文獻﹝2﹞ 材料利用率通用計算公式 =?%10?SBnA式中 A—一個沖裁件的面積,mm 2;n—一個進距內(nèi)的沖裁件數(shù)量;B—— 條料寬度,mm; S——進距, mm且 A= D +2( t= ×3.14 56 +2×(57.5-34.6)×1.5 mm2= 41?2)dt?41?22530.46mm2代入上式 得 = =70%?%1064.53?2.3 工藝方案的確定工藝方案的確定手柄零件所需的基本沖壓工序為落料和拉深,可擬訂出以下三種工藝方案。 方案一:先落料后沖孔。采用單工序模生產(chǎn)。方案二:落料--沖孔復(fù)合生產(chǎn),采用復(fù)合模生產(chǎn)。方案三:沖孔--落料連續(xù)沖壓,采用級進模生產(chǎn)。 方案一,模具結(jié)構(gòu)簡單,但需兩道工序兩副模具,生產(chǎn)率較低,難以滿足該零件的年產(chǎn)量要求。方案二只需一副模具,沖壓件的形位精度和尺寸精度容易保證,且生產(chǎn)率也高。盡管模具結(jié)構(gòu)較方案一復(fù)雜,但由于零件的幾何尺寸簡單對稱,模具制造并不困難。方案三也只需一副模具,生產(chǎn)率也很高,且易實現(xiàn)操作的機械化和自動化,但零件的沖壓精度稍差。欲保證沖壓件的形位精度,需要在模具上設(shè)置導(dǎo)正銷導(dǎo)正,故模具制造,安裝較復(fù)合模復(fù)雜。通過對上述三種方案的分析比較,該件的沖壓生產(chǎn)采用方案二為最佳。查表得,首次拉深凹模圓角半徑 r 凹=0.8 ,??tdD?式中 r 凹—— 凹模圓角半徑 (mm)D —— 毛坯直徑 (mm)d —— 凹模內(nèi)徑 (mm)t —— 材料厚度 (mm)故 r 凹=5 mm, r 凸=(0.6~1), r 凹=3~5mm, 工件底部圓角半徑 r=6mm,7大于拉深凸模圓角半徑 r 凸=3~5mm ,滿足首次拉深對圓角半徑的要求。尺寸 Φ55.8mm、 mm ,由公差查公差表得模具制造精度為 IT10,滿足拉深工序?qū)?2.?03.61??對工件等級的要求。3 模具結(jié)構(gòu)形式的選擇與確定3.1 正倒裝結(jié)構(gòu):根據(jù)上述分析,本零件的沖壓包括落料和拉深兩個工序,為操作方便,8能自動卸料,既能提高生產(chǎn)效率又能保證生產(chǎn)安全, ,采用正裝結(jié)構(gòu),即拉深凸模和落料凹模都安排在下模。3.2 送料方式:因是小批量生產(chǎn),零件尺寸較小,采用手工送料方式。3.3 定位裝置:本工件在復(fù)合模中尺寸是較小的,又是小批量生產(chǎn),采用固定擋料銷定位。3.4 導(dǎo)向方式:為確保零件的質(zhì)量,提高模具精度、壽命以及節(jié)省調(diào)試模具的時間,選用導(dǎo)柱、導(dǎo)套導(dǎo)向。為送料方便,采用后側(cè)導(dǎo)柱式模架。導(dǎo)柱過盈裝在下模,導(dǎo)套過盈裝在上模,可防止灰塵落入導(dǎo)套影響導(dǎo)向精度。當(dāng)模具合攏時,配合高度>15~20mm;沖壓完畢(合模時)導(dǎo)柱不能凸出上模板的上平面。導(dǎo)柱與上、下模座之間的關(guān)系如圖 3 所示:圖 3 導(dǎo)柱長度與上下模座的關(guān)系3.5 卸料方式:本模具采用正裝結(jié)構(gòu),工件易留在凹??锥粗校瑸榱撕喕>呓Y(jié)構(gòu),采用剛性推件裝置,在凸凹模內(nèi)安裝一頂件塊和推桿,推件力由模柄傳給推桿和推件塊,使工件從孔洞中落下(其結(jié)構(gòu)如圖 3 所示) 。工件厚度為 1.5mm,為了簡化模具結(jié)構(gòu)和達到可靠的卸料力,使操作簡便且安全,選用剛卸料板來卸下條料廢料, 既起卸料作用又起壓料作用。9圖 4 剛性推件裝置104. 沖壓力與壓力中心的計算,初選壓力機4.1 沖裁工序力的計算由工件結(jié)構(gòu)和前面所定的沖壓方案可知,本工件的沖裁力包括以下部分。落外型料的力 F1,向下推出工件的力 F2,拉深力 F,壓邊力 FQ,由彈性卸料板卸條料的廢料的力不是壓力機提供的,故不用計算在內(nèi)??紤]到模具刃部被磨損、凸凹模間隙不均勻和波動、材料力學(xué)性能及材料厚度偏差等因素的影響,實際計算沖裁力時按下面公式:F=KLtτ﹝3﹞式中 F—沖裁力(kN)L—沖裁件剪切周邊長度(mm)t—沖裁件材料厚度(mm)τ—被沖材料的抗剪強度(MPa)K—系數(shù),一般取 1.3。上式中抗剪強度 τ 與材料種類和坯料的原始狀態(tài)有關(guān),可在手冊中查詢。為方便計算,可取材料的 τ=0.8σ b,故沖裁力表達式又可表示為:P=1.3Ltτ≈Ltσ b式中 σ b—被沖材料抗拉強度(MPa)。查手冊﹝1﹞表 8—7 得 08 鋼的 σ b=350MPaF1=175.84×1.5×350=92.32kN計算推件力 F2=nKtFKt—推件力系數(shù),由手冊查得 Kt=0.055n—同時卡在凹模的工件(或廢料)數(shù)F2= =5.08kN05.316.9?計算壓邊力由 4.46 確定壓邊力的計算公式為:FQ= ????prdD224凹???式中, , D=56mm, d=31.6mm,由表查得 p=2.8MPa.mr6?凹把各已知數(shù)據(jù)代入上式,得壓邊力為:FQ= =6665.215N≈6.67 KN????N8.26.31542????11計算拉深力由 4.4.8 確定拉深力的計算公式為: F=k d?bt?已知 m=0.56, 由表查得 k=0.75,10 鋼的強度極限 =380MPa將已知數(shù)據(jù)代入上式得F=(33.1×3.14×1.5×380×0.75)N=44431.785N≈44.43KN工序總力 Fz=F1+F2+F+FQ =92.32+5.07+6.67+44.43=148.49kN故壓力機的公稱壓力要大于 148.49KN4.2 初選壓力機查文獻[4]開式雙柱可傾壓力機參數(shù)初選壓力機型號為 J23-16 和J23-25,見表一。表 一 所選擇壓力機的相關(guān)參數(shù)型號 公稱壓力 /kN 滑塊行程 /mm最大封閉高度/mm工作臺尺寸/mm滑塊底面尺寸/mm可傾斜角/·封閉高度調(diào)節(jié)量/mmJ23-16 55 10~120 220 300×45038×500 35 45J23-25 65 15~160 270 370×56046×650 30 554.3 壓力中心的計算模具的壓力中心就是沖壓力合力的作用點。為了保證壓力機和模具的正常工作,應(yīng)使模具的壓力中心與壓力機的中心滑塊中心線重合。否則,沖壓時滑塊就會承受偏心載荷,導(dǎo)致滑塊導(dǎo)軌與模具的導(dǎo)向部分不正常的磨損,還會使合理的間隙得不著保證,從而影響制件的質(zhì)量和降低模具的壽命,甚至損壞模具。該工件形狀對稱,壓力中心位于其對稱中心線的交點,即幾何中心上。 125 主要零件和主要工作機構(gòu)的設(shè)計與標(biāo)準(zhǔn)化5.1 工作零件的尺寸計算5.1.1 判斷拉深次數(shù)有凸緣圓筒形件的拉深系數(shù)取決于有關(guān)尺寸的三個相對比值即凸緣的相對直徑、零件的相對高度 、相對圓角半徑 。其中以 dt影響最大,次之 ,dt dhdRdh影響較小。 t和 越大,表示拉深時毛坯變形區(qū)的寬度大,拉深成形時的難RR度也越大。當(dāng) 和 超過一定值時,便不能一次拉深。t凸緣的相對直徑 = =1.6, 毛坯的相對厚度dt 6.3485。查表得,有凸緣圓筒形件的第一次拉深時的極限拉深系027.65.1??mDt數(shù)為 0.46。有因為零件的相對高度 dh= =0.24,零件的相對高度 小于端蓋.5dh第一次拉深時的極限拉深系數(shù),所以端蓋可以一次拉深5.1.2 拉深模的間隙由表查得拉深模的單邊間隙為 mtZ5.12?則拉深模的間隙 Z=2×1.5mm=3mm5.1.3 拉深模的圓角半徑 凹模的圓角半徑 表 4.8.2 選取, =5mm。凸模的圓角半經(jīng)等于等于工件的凹r凹r內(nèi)圓角半徑,即 = r=6mm凸5.1.4 拉深凸、凹模工作部分的尺寸和公差。 由于工件要求內(nèi)形尺寸,則以凸模為設(shè)計基準(zhǔn)。凸模的計算公式為:??0min4.TdT?????式中 : —— 凸模的尺寸d—— 拉深件的內(nèi)徑的最小極限尺寸min△ —— 零件的公差—— 凸模的制造公差T?13查表得 ,凸模制造公差 , 把 31.57mm, △=0.03mm, mT05.???mind代入上式,則模尺寸為 mmmT05.?? ??05.05.8314.731????d間隙取在凹模上,則凹模的計算公式為:??AZdA?0min4.?式中 : —— 凸模的尺寸—— 拉深件的內(nèi)徑的最小極限尺寸min△ —— 零件的公差—— 凸模的制造公差A(yù)?Z —— 拉深模的雙面間隙查表得 凸模制造公差 =0.08mm, 把 31.57mm, △=0.03mm , A??mind=0.08mm 代入上式, 得A?=34.58 mm??08.3.4057.31????Ad 08.?5.1.5 落料凸模、凹模刃口尺寸的計算因此落料件為簡單形狀的制件,所以利用凸凹模配合法,這種方法有利于獲得最小的合理間隙,放寬對模具的加工設(shè)備的精度要求。采用配作法,計算凹模的刃口尺寸,首先是根據(jù)凹模磨損后輪廓變化情況正確判斷出模具刃口各個尺寸在磨損過程中是變大還是變小,還是不變這三種情況,然后分別按不同的計算公式計算。a、凹模磨損后會增大的尺寸------- 第一類尺寸 A第一類尺寸:A j=(Amax-x△) 0+0.25△ b、凹模磨損后會減小的尺寸------- 第二類尺寸 B第二類尺寸:B j=(Bmax+x△) 0-0.25△c、凹模磨損后會保持不變的尺寸 第三類尺寸 C第三類尺寸:C j=(Cmin+0.5△)? 0.125△式中 、 、 ——基準(zhǔn)件尺寸(mm)jAjBj、 、 ——工件極限尺寸(mm)minimin14△ ——工件制造公差(mm)X ——因數(shù)(mm)其落料凹模的基本尺寸計算如下:圖 5 落料凹模刃口部分尺寸第一類尺寸:磨損后增大的尺寸:A1=(Amax- x△) 0+0.25△將 △=0.03mm,x=0.75 代入上式 得A1= (56-0.75×0.03) 0+0.25×0.43=55.980+0.12落料凸模的基本尺寸與凹模相同,為 55.98mm,不必標(biāo)注公差,但要在技術(shù)條件中注明:凸模實際刃口尺寸與落料凹模配制,保證最小雙面合理間隙值 Zmin=0.22(查表得)。15圖 6 落料凸模刃口尺寸5.2 工作零部件的設(shè)計與標(biāo)準(zhǔn)化5.2.1 拉深的凸模,為了增加凸模的強度與剛度,應(yīng)將凸模非工作部分直徑應(yīng)設(shè)計成階梯形式如圖 6 所示:圖 7 拉深凸模的結(jié)構(gòu)形式凸模長度一般是根據(jù)結(jié)構(gòu)上的需要而確定的,工藝方案采用落料拉深正裝復(fù)合模,即落料凸模設(shè)計在下模,其工作部分的長度等于無凸緣圓筒件的高度和壓邊圈厚度的和。凸模長度用下列公式計算:L=h1+h2+h式中 L—凸模長度, mmh1—圓筒形件的高度,mmh2—壓邊圈的高度,mmh—附加高度,一般取 15~20mm故拉深凸模的長度 L=10mm+10mm+15mm=35mm在工件拉深過程中,由于空氣壓力的作用或潤滑油的粘性等因素,是工件很容易粘附在凸模上。為使工件不至于緊貼在凸模上,在設(shè)計凸模時應(yīng)有通氣孔。差查表得拉16深凸模的通氣孔直徑為 5mm.?圖 8 整體式凹模的局部結(jié)構(gòu) 5.2.2 落料凹模采用整體式凹模如圖 7 所示 凹模直接裝于下模座上,由于下模座孔口較大因而使工作時承受彎曲力矩,若凹模高度 H 及模壁厚度 C 不足時,會使凹模產(chǎn)生較大變形,甚至破壞。但由于凹模受力復(fù)雜,凹模高度可按經(jīng)驗公式計算,即凹模高度 H=KB凹模壁厚 C=(1.5~2)H式中 B----凹??椎淖畲髮挾?,mm 但 B 不小于 15mmC-----凹模壁厚,mm 指刃口至凹模外形邊緣的距離;K=系數(shù),查表取 0.3凹模高度 H=KB=0.3×56=16.8mm 按表取標(biāo)準(zhǔn)值 20mm凹模壁厚 C=1.5H = 1.5×20=30mm 查表得凹模刃口高度 h 為 6mm凹模上螺孔到凹模外緣的距離一般?。?.7~2.0)d, 圖 9 凹模上的螺孔設(shè)計與選用d 為螺孔的距離,由于凹模厚度為 15mm,所以根據(jù)表 2.46﹝2﹞ 查得螺孔選用 4×M10的螺釘固定在下模座。故選用如圖 8: 螺孔到凹模外緣的最小距離 a2=1.5d=1.5×8=12mm17a3=1.13d≈9mm凹模上螺孔間距由表 2.47 查得最小間距為 40mm,最大間距為 90mm。 螺孔到銷孔的距離一般取 b>2d,所以 b 應(yīng)大于 16mm。根據(jù)上述方法確定凹模外形尺寸須選用圓形凹模板 116 ×20(JB/T7643.1)?確定凹模組件的尺寸和示意圖凹模采用整體式凹模,各沖裁的凹模孔均采用線切割加工,安排凹模在模架上的位置時,要依據(jù)計算的壓力中心的數(shù)據(jù),使壓力中心與模柄中心重合。圖 10 整體式凹模的尺寸凹模的長度選取要考慮以下因素:a)保證有足夠的安裝剛性卸料板的位置。b)便于導(dǎo)尺發(fā)揮作用,保證送料粗定位精度。凹模材料選用 Cr12 制造,熱處理硬度為 58~62HRC。5.2.3 外形落料凸模各尺寸及其組件的確定和標(biāo)準(zhǔn)化(包括外形尺寸和厚度)落料凸模的設(shè)計:落料凸模亦為拉深凹模,落料凸模用線切割機床加工成直通式凸模,用四個 M18 的螺釘固定在上模座上,由于采用彈定卸料板,凸模按下式計算:L=h1+h2+h3+h其中: h1為工件高度(10mm),h2為卸料板厚度(15mm),h3為落料凹模高度(20mm),h為附加長度(mm),主要考慮凸模進入凹模的深度(1mm)及模具閉合狀態(tài)下卸料板到凸模固定板間的安全距離(15mm~20mm)等因素。所以:L=10+15+20+1+19=65mm 查表得 復(fù)合模的凸、凹模最小壁厚為 m8.3??凸模的固定有三種形式:機械固定:螺釘緊固,鉚接18物理固定:低熔點合金固定(重復(fù)利用)化學(xué)固定:有機、無機粘結(jié)劑粘結(jié)(加熱時有害氣體放出)落料凸模采用機械固定,用螺釘和銷釘直接將落料凸模固定在上模座上,從而簡化了模具結(jié)構(gòu),如圖(b)所示:圖(a) 圖(b)5.3 定位裝置的設(shè)計與標(biāo)準(zhǔn)化5.3.1 始用擋料塊的設(shè)計與標(biāo)準(zhǔn)化(尺寸、位置、標(biāo)準(zhǔn)與示意圖) (包括順沖和掉頭沖兩個始用導(dǎo)料銷) 淬 硬圖 11 始用擋料銷的設(shè)計擋料塊標(biāo)記: 45?6 GB/T2866.1—81材料:45 鋼 GB/699—88熱處理:硬度 43~48HRC技術(shù)條件:按 GB2870—815.3.2 固定擋料銷的設(shè)計與標(biāo)準(zhǔn)化19固定擋料銷的設(shè)計根據(jù)標(biāo)準(zhǔn)件,選用此擋料銷如圖圖 12 固定擋料銷的結(jié)構(gòu)選用直徑 φ6mm,h=4mm 材料為 45 鋼 A 型固定擋料銷(JB/T7649.10—94)根據(jù)分析選用廢料孔前端定位時擋料銷位置如圖 廢料孔前端定位時擋料銷位置圖 13 固定擋料銷的位置=C-( )+0.1l2dr?——擋料銷與導(dǎo)正銷的間距,mm lC——連續(xù)模的步距,mmdr——導(dǎo)正銷的直徑,mmd——擋料銷頭部直徑,mm=61-( )+0.1=61.1mml281.?5.4 標(biāo)準(zhǔn)模架的選用選取模架尺寸時要根據(jù)凹模的輪廓尺寸考慮,一般在長度及寬度上都應(yīng)比凹模大30~40mm。模板的厚度一般等于凹模的 1~1.5 倍。20凹模周界L=116mm,B=116mm,閉合高度 h1=220mm材料為 ZG45(ZG310-570),0I 級精度的后側(cè)導(dǎo)柱模架。導(dǎo)柱標(biāo)記:22?160 GB/T2861.1—90導(dǎo)套標(biāo)記:42?90?38 GB/T2861.6—90上模座標(biāo)記:250?160?40 GB/T2855.1—90下模座標(biāo)記:250?160?45 GB/T2855.2—90模柄標(biāo)記:A32?95 JB/T 7646.1圖 14 后側(cè)導(dǎo)柱模架示意圖模柄與上模座的聯(lián)接采用壓入式的結(jié)構(gòu)如圖 17 所示。圖 15 壓入式的模柄215.5 卸料裝置的設(shè)計與標(biāo)準(zhǔn)化在前面已經(jīng)確定了采用彈性卸料板和頂件塊,設(shè)計卸料板為一整體板。本模具的卸料板不僅有卸料作用,還具有外形凸模的導(dǎo)向作用, 。卸料板的邊界尺寸經(jīng)查手冊 [2]表 15.28 得:卸料板直徑 =150mm 厚度 h0=15mm?此模具中,卸料板對落料拉深復(fù)合模起導(dǎo)向和卸料作用,卸料板和凸模按 H7/h6配合制造5.6 聯(lián)接件的選用與標(biāo)準(zhǔn)化本模具采用螺釘固定,銷釘定位。具體講內(nèi)六角螺釘標(biāo)記:35 鋼 M8?65 GB70—8535 鋼 M8?35 GB70—85螺釘標(biāo)記:35 鋼 M8?45 GB68—76圓柱銷釘標(biāo)記:35 鋼 6?65 GB 119—86 ?35 鋼 6?45 GB 119—86止動圓柱銷標(biāo)記:35 鋼 6?6 GB119—865.7 模具裝配圖前面各節(jié)已經(jīng)設(shè)計好了無凸緣圓筒形件的落料拉深復(fù)合模各零件,根據(jù)前面的設(shè)計,無凸緣圓筒形件的落料拉深復(fù)合模的總裝圖如下226 壓力機的選擇與校核Hmin=160mm,Hmax=180mm模具的閉合高度 H 閉 =H+H 上 +H 凹 +H 卸 +H 下 =15+40+45+10+45=155mm式中:H 凹 —凹模厚度,H 凹 =45mm;H 卸 —壓邊圈的厚度,H 卸 =10mm;H —凸模的凸緣高度,H=15 mm由此可見模具的實際閉合高度小于所采用模架的最大閉合高度。查標(biāo)準(zhǔn)件的資料。結(jié)果發(fā)現(xiàn)模具的實際閉合高度還是遠遠大于其它標(biāo)準(zhǔn)的最大閉合高度。所以此制件不能采用標(biāo)準(zhǔn)模架。為了節(jié)省加工時間,只有在模具標(biāo)準(zhǔn)模架的基礎(chǔ)上進行修改。因為模具的封閉高度 H 應(yīng)該介于壓力機的最大封閉高度 Hmax 和最小封閉高度 Hmin 之間,一般取: Hmax-5mm≥H≥Hmin+10mm由此可以看出,要想讓制件順利加工和從模具上取出,只有使模具有足夠的封閉高度:Hmax≥H+5mm=155+5=160mmHmin≤H-10mm=155-10=145mm要使模具具有足夠的封閉高度,只有改變導(dǎo)柱和導(dǎo)套的高度:為了使模座有足夠的強度,上,下模座的厚度應(yīng)該再增加一些。前面已經(jīng)初選了壓力機。由 5.4 可知,模座外形尺寸 260 mm×160mm,閉合高度160mm,有文獻[4] 中,JC23 —35 型壓力機工作臺尺寸為 300×450mm,最大閉合高度為220mm,連桿調(diào)節(jié)長度為 45mm,所以在工作臺上加一 10~35mm 的墊板,即可安裝。模柄孔尺寸也于本副模具所選模柄尺寸相符。237 模具工件零件的加工工藝7.1 沖裁模凸、凹模的技術(shù)要求及加工特點沖裁屬于分離工序,沖裁模凸、凹模帶有鋒利刃口,凸、凹模之間的間隙較小,其加工具有如下特點:①凸、凹模材質(zhì)一般是工具鋼或合金工具鋼,熱處理后的硬度一般為58∽64HRC,凹模比凸模稍硬一些。②凸、凹模精度主要根據(jù)沖裁件精度決定,一般尺寸精度在IT6∽IT9,工作表面粗糙度在Ra值為1.6∽0.4μm。③凸、凹模工作端帶有鋒利刃口,刃口平直(斜刃除外) ,安裝固定部分要符合配合要求。④凸、凹模裝配后應(yīng)保證均勻的最小合理間隙。⑤凸模的加工主要是外形加工,凹模的加工主要是孔(系)加工。凹模型孔加工和臺階式凸模加工常用線切割方法。 【1】7.2 凸、凹模加工的工藝路線有以下幾種方案:方案一:下料→鍛造→退火→毛坯外形加工(包括外形粗加工、精加工、基面磨削)→劃線→刃口輪廓粗加工→刃口輪廓精加工→螺孔、銷孔加工→淬火與回火→研磨或拋光;方案二:下料→鍛造→退火→毛坯外形加工(包括外形粗加工、精加工、基面磨削)→劃線→刃口輪廓粗加工→螺孔、銷孔加工→淬火與回火→采用成形磨削進行刃口輪廓精加工→研磨或拋光;方案三:下料→鍛造→退火→毛坯外形加工→螺孔、銷孔、穿絲孔加工→淬火與回火→磨削加工上、下面及基準(zhǔn)面→線切割加工→鉗工修整;具體分析:方案一,鉗工工作量大,技術(shù)要求高,適用于形狀簡單,熱處理變形小的零件;方案二,能消除熱處理變形對模具精度的影響,使凸、凹模的加工精度容易保證,可用于熱處理變形大的零件;方案三,主要用于以線切割加工為主要工藝的凸、凹模加工,尤其適用形狀復(fù)雜,熱處理變形大的直通式凸模、凹模零件。7.3 本副模具工件零件加工方案的確定本副沖裁模具設(shè)計,模具零件加工的關(guān)鍵在工作零件。由于本副模具的工作零件24形狀相對比較簡單,凸凹模,落料凹模熱處理變形大,故采用方案三;拉深凸模和落料凸模形狀簡單,且熱處理變形小,故采用方案一。例如:表(7—1)拉深凸模加工工藝過程、表(7—2)凹模加工工藝過程。模具典型零件機械加工工序卡零件圖號 08 零件名稱 沖孔凸模II工序號 工序名稱 工序內(nèi)容 設(shè)備1 備料 將毛坯鍛成圓棒φ65mm×45mm2 熱處理 退火3 車削 按圖車全形,單邊留0.2mm精加工余量車床4 熱處理 按熱處理工藝,淬火、回火達到58∽62HRC5 磨削 磨外圓,兩端面達到設(shè)計要求磨床6 鉗工精修 全面達到設(shè)計要求7 檢驗表(7—1)沖孔凸模II加工工藝過程模具典型零件機械加工工序卡零件圖號 11 零件名稱 凹模工序號 工序名稱 工序內(nèi)容 設(shè)備1 備料 將毛坯鍛成圓柱形 125mm×50mm?空氣錘2 熱處理 退火3 車外圓 車外圓直徑達到116mm×50mm車床4 熱處理 調(diào)質(zhì)255 磨平面 磨兩端面 磨床6 鉗工劃線 劃出各孔位置線,型孔輪廓線7 銑漏料孔 達到設(shè)計要求 銑床8 加工螺釘孔、銷釘孔及穿絲孔按位置加工螺釘孔、銷釘孔及穿絲孔鉆床9 熱處理 按熱處理工藝,淬火、回火達到60∽64HRC10 磨平面 磨光上、下平面 磨床11 線切割 按圖紙切割型孔達到尺寸要求電火花線切割機床12 鉗工精修 全面達到設(shè)計要求13 檢驗表(7—2)凹模加工工藝過程268 深圓筒模具的安裝與調(diào)試8.1 深圓筒模具的安裝8.1.1 拉深模的安裝要求1.上模座上平面對下模座下平面的平行度,導(dǎo)柱軸心線對下模座下平面的垂直度和導(dǎo)套孔軸心線對上模座上平面的垂直度均應(yīng)達到規(guī)定的精度要求。2.模架的上模沿導(dǎo)柱上、下移動應(yīng)平穩(wěn),無阻滯現(xiàn)象。3.裝配好的拉深模,其封閉高度應(yīng)符合圖樣規(guī)定的要求。4.拉深凸模和拉深凹模之間的配合間隙應(yīng)符合圖樣的要求,周圍的間隙應(yīng)均勻一致。5.模具應(yīng)在生產(chǎn)的條件下試驗,進行零件試沖,然后調(diào)試,直到符合圖樣要求。6.安裝模具的螺栓及螺母和壓板,應(yīng)采用專用件,最好不要代用。7.用壓板將下模緊固在工作臺上時,其緊固用的螺栓擰入螺孔中的長度大于螺栓直徑的 1.5~2 倍。8.壓板的壓置應(yīng)使壓板的基面平行于壓力機的工作臺面,不準(zhǔn)偏斜。9.拉深凸模的中心線應(yīng)與凹模的工作平面垂直。10.拉深凸模和凹模的間隙應(yīng)該均勻。8.1.2 拉深模的安裝本模具屬于帶有壓邊圈的拉深模,應(yīng)對壓邊力進行適當(dāng)調(diào)整。這是因為壓邊力過大,則制件易被拉裂;壓邊力過小,又易于起皺。因此,在裝置模具時,應(yīng)邊試驗,邊調(diào)整,直到合適為止。下面是具體的安裝過程:1.開動壓力機,把壓力機滑塊上升到極點;2.把壓力機滑塊底面、壓力機的臺面和模具的上下面擦試干凈;3.把模具放在壓力機臺面規(guī)定的位置上,用壓力機行程尺檢查壓力機滑塊底面至模具上平面之間距離是否大于壓力機的行程。必要時,調(diào)節(jié)滑塊高度,以保證該距離27大于壓力機行程。因本模具有打桿,所以應(yīng)先按圖樣位置將其插入壓力機臺面的孔內(nèi),并把模具位置放正。4.將滑塊降下到極點,并調(diào)節(jié)滑塊高度,使其與拉深模上平面接觸。5.通過壓板、墊塊和螺釘?shù)?,將上模緊固在壓力機的滑塊上,并將下模初步固定在壓力機的臺面上。 〔不要壓的太緊〕6.將滑塊稍微往上調(diào)一點〔以免模具頂死〕 ,然后開動壓力機,把滑塊上升到上極點,松開下模的安裝螺絲,讓滑塊空行程數(shù)次,再把滑塊下降到下極點停止。7.擰緊下模的安裝螺釘。再開動壓力機使滑塊上升到上極點位置。8.在導(dǎo)柱上加潤滑油,并檢查拉深模工作部分有無異物,然后開動壓力機,再使滑塊空行程數(shù)次,從中檢查導(dǎo)柱和導(dǎo)套的配合情況。若發(fā)現(xiàn)導(dǎo)柱不垂直或者導(dǎo)套配合不合適時,應(yīng)拆下模具進行修理。9.進行試?yán)?,并逐步調(diào)節(jié)滑塊到所需的高度。10.調(diào)節(jié)壓力機上的打料螺栓到適合的高度,使打料桿能正常工作。11.如果拉深模使用氣墊,則應(yīng)調(diào)節(jié)壓縮空氣到合適壓力。12.重新檢查模具及壓力機,無誤后可進行試?yán)睢?.2 模具的調(diào)試模具按圖紙技術(shù)要求加工與裝配后,必須在符合實際生產(chǎn)條件的環(huán)境中進行試?yán)睿梢园l(fā)現(xiàn)模具設(shè)計與制造的缺陷,找出產(chǎn)生原因,對模具進行適當(dāng)?shù)恼{(diào)整和修理后再進行試?yán)?,直到模具能正常工作,才能將模具正式交付生產(chǎn)使用。8.2.1 拉深模的調(diào)試要點8.2.1.1 進料阻力的調(diào)整拉深模進料阻力很大,易使制件被拉裂;進料阻力很小時,易使制件產(chǎn)生皺紋。故在調(diào)整模具時,關(guān)鍵是調(diào)整好拉深阻力的大?。骸?〕調(diào)節(jié)壓力滑塊的壓力,使之正常;〔2〕調(diào)節(jié)壓邊圈的壓邊面配合松緊;28〔3〕凹模圓角半徑要適中;〔4〕采用良好的潤滑劑,調(diào)整潤滑次數(shù)。8.2.1.2 拉深深度及間隙調(diào)整1.調(diào)整時,先將較淺的一段調(diào)整后,再往下調(diào)整,直到所需深度。2.因本模具是對稱的。所以在調(diào)整時,可先將上模緊固在壓力機滑塊上,下模放在工作臺上,先不緊固。在凸模上放置樣件,再使上、下模吻合對中后,即可保證間隙的均勻性。調(diào)整好閉合位置后,再把下模固緊在工作臺上。8.2.2 調(diào)整方法8.2.2.1 拉深時的破裂拉深時,材料變形所需要的拉深力超過了材料的強度極限時,即形成破裂。拉深時的破裂部位多發(fā)生在鄰近凸模圓角處的筒壁處。防止拉深破裂的工藝措施有:增大凹模圓角、增大凸模和凹模之間的間隙、提高凹模工作表面和凹模圓角半徑處的表面質(zhì)量、調(diào)整壓邊力、選用塑性好的材料和進行適當(dāng)?shù)臐櫥取?.2.2.2 拉深高度不夠制件拉深結(jié)束后,結(jié)果高度達不到圖樣要求。其產(chǎn)生原因有拉深間隙太大、凸模圓角半徑太小。防止拉深高度不夠的措施有:調(diào)整拉深間隙、加大凸模圓角半徑。8.2.2.3 制件底部被拉脫制件在拉深過程中由于凹模圓角半徑太小,使材料被處于切割狀態(tài)以至于制件底部被拉脫。防止制件底部被拉脫的措施有:加大凹模圓角半徑。298.2.2.4 制品口緣折皺制件在拉深過程中由于凹模圓角半徑太大、壓邊圈不起壓邊作用,造成制件口緣折皺。防止制件口緣折皺的措施有:減小凹模圓角半徑、調(diào)整壓邊圈結(jié)構(gòu),加大壓邊力。8.2.2.5 拉深高度太大制件拉深結(jié)束后,結(jié)果發(fā)現(xiàn)制件的高度達不到圖樣的要求。其產(chǎn)生原因有拉深間隙太小、凸模圓角半徑太大。防止拉深高度太大的措施有:加大拉深間隙、減小凸模圓角半徑。8.2.2.6 零件拉深后壁厚與高度不均零件拉深后發(fā)現(xiàn)壁厚與高度不均,其造成原因有凸模與凹模不同心,向一面偏斜、定位不正確、凸模不垂直、壓邊力不均、凹模形狀不對。防止零件拉深后壁厚與高度不均的措施有:調(diào)整凸模與凹模位置,使之間隙均勻、調(diào)整定位零件、重新裝配凹模、調(diào)整壓邊力、更換凹模。309 結(jié)束語有凸緣圓筒形件屬于簡單拉深件,分析其工藝性,并確定工藝方案。根據(jù)計算確定本制件是一次拉深成的,然后相應(yīng)選取各次拉深時的壓力機。本設(shè)計主要是最后一次拉深模具設(shè)計,需要計算拉深時的間隙、工作零件的圓角半徑、尺寸和公差,并且還需要確定模具的總體尺寸和模具零件的結(jié)構(gòu),然后根據(jù)上面的設(shè)計繪出模具的總裝圖。由于在零件制造前進行了預(yù)測,分析了制件在生產(chǎn)過程中可能出現(xiàn)的缺陷,采取了相應(yīng)的工藝措施。因此,模具在生產(chǎn)零件的時候才可以減少廢品的產(chǎn)生。有凸緣圓筒形件的形狀結(jié)構(gòu)較為簡單,但是高度太高不適合選用標(biāo)準(zhǔn)模架。要保證零件的順利加工和取件,必須有足夠的高度,因此需要改變導(dǎo)柱、導(dǎo)套的長度,以達到要求。模具工作零件的結(jié)構(gòu)也較為簡單,它可以相應(yīng)的簡化了模具結(jié)構(gòu)。便以以后的操作、調(diào)整和維護。有凸緣圓筒形件模具的設(shè)計,是理論知識與實踐有機的結(jié)合,更加系統(tǒng)地對理論知識做了更深切貼實的闡述。也使我認(rèn)識到,要想做為一名合理的模具設(shè)計人員,必須要有扎實的專業(yè)基礎(chǔ),并不斷學(xué)習(xí)新知識新技術(shù),樹立終身學(xué)習(xí)的觀念,把理論知識應(yīng)用到實踐中去,并堅持科學(xué)、嚴(yán)謹(jǐn)、求實的精神,大膽創(chuàng)新,突破新技術(shù),為國民經(jīng)濟的騰飛做出應(yīng)有的貢獻。31致謝沖壓技術(shù)是材料加工技術(shù)中不可缺少的重要加工手段之一,目前在國內(nèi)正處于蓬勃發(fā)展時期,具有廣泛的發(fā)展前景。在大學(xué)三年學(xué)習(xí)即將結(jié)束之際,能夠按照老師的指導(dǎo)并綜合運用三年來的所學(xué)所知設(shè)計一套沖壓模具,必將為日后的獨立工作創(chuàng)造一個良好的開始。在畢業(yè)設(shè)計過程中于余智宏老師一直扮演著導(dǎo)向者的角色,從接到設(shè)計題目那一刻起就給我指明了方向,讓我明白了設(shè)計要求、設(shè)計流程、設(shè)計中可能遇到的問題以及解決方法等,并不厭其煩的糾正設(shè)計中的錯誤,詳細檢查設(shè)計中的細節(jié)及重點,對設(shè)計方案提出了寶貴的修正意見,一步步完善了我的設(shè)計。在此對原老師表示衷心的感謝!此外在設(shè)計過程中參考了一些同學(xué)的設(shè)計實例,并向他們請教,得到他們的大力幫助,為我提供了許多有關(guān)設(shè)計的資料,在此一并表示深深的謝意!32參考文獻(1) 王孝培主編,沖壓手冊,機械工業(yè)出版社,1988 年 2 月(2) 郝濱海編著,沖壓模具簡明設(shè)計手冊,化學(xué)工業(yè)出版社,2005 年 1 月(3) 楊玉英主編,實用沖壓工藝及模具設(shè)計手冊,機械工業(yè)出版社,2005 年 1 月(4) 中國機床總公司編著,全國機床產(chǎn)品供貨目錄,機械工業(yè)出版社,2002 年 6 月(5) 史鐵梁主編,冷沖模設(shè)計指導(dǎo),機械工業(yè)出版社,1996 年 7 月33