【溫馨提示】壓縮包內(nèi)含CAD圖有下方大圖片預(yù)覽,下拉即可直觀呈現(xiàn)眼前查看、盡收眼底縱觀。打包內(nèi)容里dwg后綴的文件為CAD圖,可編輯,無水印,高清圖,壓縮包內(nèi)文檔可直接點(diǎn)開預(yù)覽,需要原稿請自助充值下載,所見才能所得,請見壓縮包內(nèi)的文件及下方預(yù)覽,請細(xì)心查看有疑問可以咨詢QQ:11970985或197216396
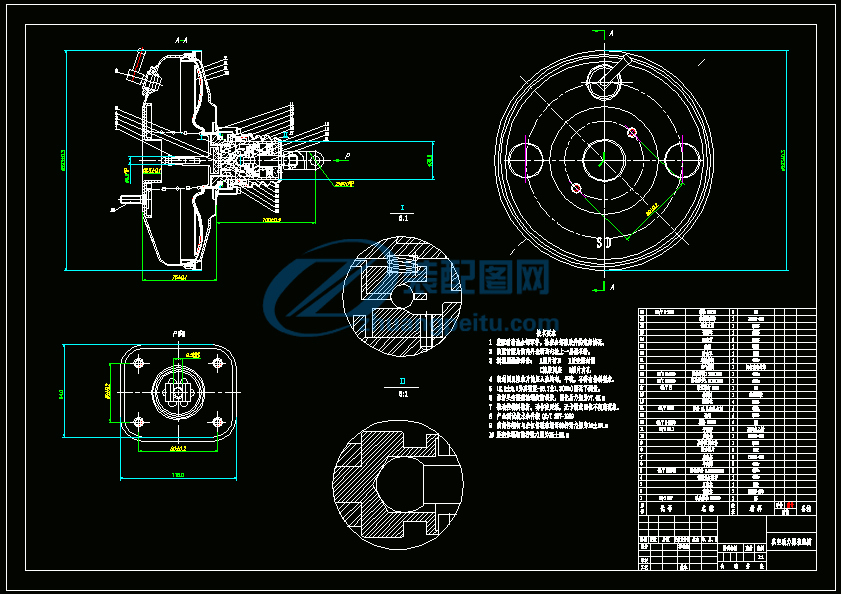
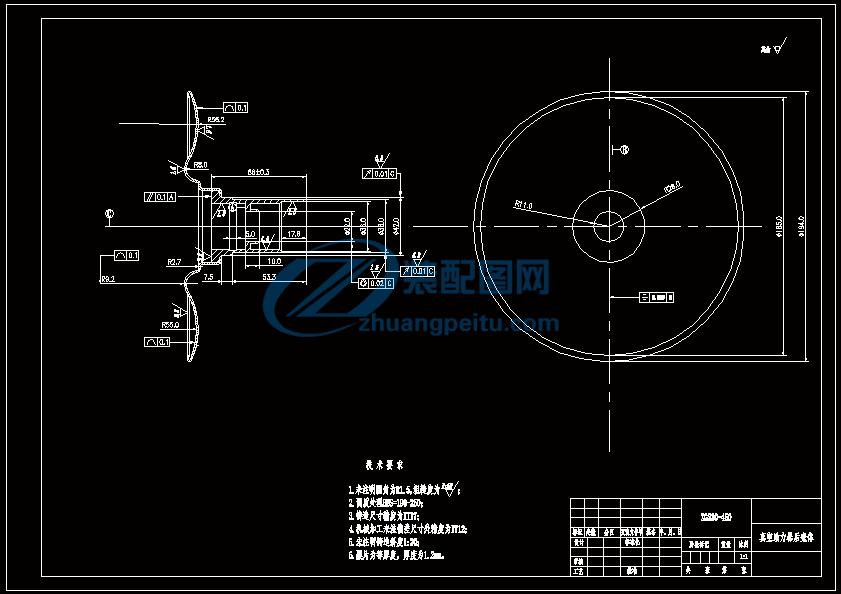



畢 業(yè) 設(shè) 計(jì)(論 文)任 務(wù) 書
設(shè)計(jì)(論文)題目: 轎車輔助制動(dòng)系統(tǒng)設(shè)計(jì)
學(xué)生姓名:
?! I(yè):
所在學(xué)院:
指導(dǎo)教師:
職 稱:
發(fā)任務(wù)書日期: 年 12 月 30 日
任務(wù)書填寫要求
1.畢業(yè)設(shè)計(jì)(論文)任務(wù)書由指導(dǎo)教師根據(jù)各課題的具體情況填寫,經(jīng)學(xué)生所在專業(yè)的負(fù)責(zé)人審查、系(院)領(lǐng)導(dǎo)簽字后生效。此任務(wù)書應(yīng)在畢業(yè)設(shè)計(jì)(論文)開始前一周內(nèi)填好并發(fā)給學(xué)生。
2.任務(wù)書內(nèi)容必須用黑墨水筆工整書寫,不得涂改或潦草書寫;或者按教務(wù)處統(tǒng)一設(shè)計(jì)的電子文檔標(biāo)準(zhǔn)格式(可從教務(wù)處網(wǎng)頁上下載)打印,要求正文小4號宋體,1.5倍行距,禁止打印在其它紙上剪貼。
3.任務(wù)書內(nèi)填寫的內(nèi)容,必須和學(xué)生畢業(yè)設(shè)計(jì)(論文)完成的情況相一致,若有變更,應(yīng)當(dāng)經(jīng)過所在專業(yè)及系(院)主管領(lǐng)導(dǎo)審批后方可重新填寫。
4.任務(wù)書內(nèi)有關(guān)“學(xué)院”、“專業(yè)”等名稱的填寫,應(yīng)寫中文全稱,不能寫數(shù)字代碼。學(xué)生的“學(xué)號”要寫全號,不能只寫最后2位或1位數(shù)字。
5.任務(wù)書內(nèi)“主要參考文獻(xiàn)”的填寫,應(yīng)按照《金陵科技學(xué)院本科畢業(yè)設(shè)計(jì)(論文)撰寫規(guī)范》的要求書寫。
6.有關(guān)年月日等日期的填寫,應(yīng)當(dāng)按照國標(biāo)GB/T 7408—94《數(shù)據(jù)元和交換格式、信息交換、日期和時(shí)間表示法》規(guī)定的要求,一律用阿拉伯?dāng)?shù)字書寫。如“2002年4月2日”或“2002-04-02”。
畢 業(yè) 設(shè) 計(jì)(論 文)任 務(wù) 書
1.本畢業(yè)設(shè)計(jì)(論文)課題應(yīng)達(dá)到的目的:
本畢業(yè)設(shè)計(jì)課題主要是轎車輔助制動(dòng)系統(tǒng)設(shè)計(jì)。目的是培養(yǎng)學(xué)生綜合運(yùn)用所學(xué)的基礎(chǔ)理論、專業(yè)知識和專業(yè)基本技能分析以及解決實(shí)際問題,訓(xùn)練初步工程設(shè)計(jì)的能力。根據(jù)車輛工程專業(yè)的特點(diǎn),著重培養(yǎng)以下幾方面能力:
1.調(diào)查研究、中外文獻(xiàn)檢索、閱讀與翻譯的能力;
2.綜合運(yùn)用基礎(chǔ)理論、專業(yè)理論和知識分析解決實(shí)際問題的能力;
3.查閱和使用專業(yè)設(shè)計(jì)、維修等手冊的能力;
4.設(shè)計(jì)、計(jì)算與繪圖的能力,包括使用計(jì)算機(jī)進(jìn)行繪圖的能力;掌握一定的測試技術(shù),進(jìn)行性能分析;
5.撰寫設(shè)計(jì)說明書(論文)的能力。
2.本畢業(yè)設(shè)計(jì)(論文)課題任務(wù)的內(nèi)容和要求(包括原始數(shù)據(jù)、技術(shù)要求、工作要求等):
當(dāng)遇到緊急情況,百分之九十的駕駛?cè)藛T在進(jìn)行制動(dòng)操作時(shí)缺乏果斷,以至于不能及時(shí)踩下制動(dòng)踏板或踩踏力度不夠,造成剎車距離過長。所以要求必須加裝輔助制動(dòng),但現(xiàn)有的加裝會對汽車進(jìn)行較大的改造。本課題對轎車輔助制動(dòng)系統(tǒng)進(jìn)行設(shè)計(jì),對制動(dòng)性能進(jìn)行分析,利用二維及三維設(shè)計(jì)軟件進(jìn)行建模,繪制工程圖。
本畢業(yè)設(shè)計(jì)課題的要求:
1.通過查閱資料,按時(shí)完成開題報(bào)告書。
2.按時(shí)完成畢業(yè)設(shè)計(jì)外文參考資料。
3.對輔助制動(dòng)系統(tǒng)建模分析。
4.能夠完成指導(dǎo)老師布置的課題任務(wù),體現(xiàn)一定的創(chuàng)新性。
5.撰寫畢業(yè)論文,按時(shí)參加答辯,在答辯前各項(xiàng)規(guī)定的資料要齊全。
畢 業(yè) 設(shè) 計(jì)(論 文)任 務(wù) 書
3.對本畢業(yè)設(shè)計(jì)(論文)課題成果的要求〔包括圖表、實(shí)物等硬件要求〕:
1.外文參考資料譯文(附原文)不少于3000字;
2.有結(jié)構(gòu)完整、合理可靠的技術(shù)方案,對轎車輔助制動(dòng)系統(tǒng)進(jìn)行三維建模,完成合計(jì)不少于2張0號圖紙的工作量;
3.按期完成符合《金陵科技學(xué)院本科生畢業(yè)設(shè)計(jì)(論文)工作條例》要求的畢業(yè)設(shè)計(jì)論文,不少于1萬字,能詳細(xì)說明設(shè)計(jì)步驟和思路。
4.主要參考文獻(xiàn):
[1] 陳家瑞.汽車構(gòu)造 [M].北京:機(jī)械工業(yè)出版社,2012.
[2] 余志生.汽車?yán)碚?[M].北京:機(jī)械工業(yè)出版社,2012.
[3] 王望予.汽車設(shè)計(jì) [M].北京:機(jī)械工業(yè)出版社,2011.
[4] 喻凡,林逸.汽車系統(tǒng)動(dòng)力學(xué)[M].北京:機(jī)械工業(yè)出版社,2013.
[5] 濮良貴,紀(jì)名剛.機(jī)械設(shè)計(jì) [M].北京:高等教育出版社,2012.
[6] 徐石安.汽底盤工程[M].北京:清華大學(xué)出版社,2008.
[7] 王國權(quán),龔國慶.汽車設(shè)計(jì)課程設(shè)計(jì)指導(dǎo)書[M].北京:機(jī)械工業(yè)出版社,2010.
[8] 劉濤.汽車設(shè)計(jì)[M].北京:北京大學(xué)出版社.2008.
[9] 張忐忑.山地丘陵果園綜合作業(yè)車設(shè)計(jì) [D].重慶:西南大學(xué),2014.
[10] 李德華.簾布車車架有限元分析及優(yōu)化設(shè)計(jì) [D].江蘇:江蘇大學(xué),2012.
[11] 劉平安.AutoCAD2011中文版機(jī)械設(shè)計(jì)實(shí)例教程[M].北京:機(jī)械工業(yè)出版社,2010.
[12] 林清安.完全精通Pro/ENGINEER野火5.0中文版零件設(shè)計(jì)基礎(chǔ)入門[M].北京:電子工業(yè)出版社,2010.
[13] 王登峰.CATIA V5機(jī)械(汽車)產(chǎn)品CAD/CAE/CAM全精通教程[M].北京:人民交通出版社,2007.
[14] 陳立德.機(jī)械設(shè)計(jì)基礎(chǔ)[M].北京:機(jī)械工業(yè)出版社,2013.
[15] 馮健.摩托車發(fā)動(dòng)機(jī)一軸式平衡技術(shù)的研究[D].重慶:重慶大學(xué),2004.
畢 業(yè) 設(shè) 計(jì)(論 文)任 務(wù) 書
5.本畢業(yè)設(shè)計(jì)(論文)課題工作進(jìn)度計(jì)劃:
起 訖 日 期
工 作 內(nèi) 容
2015.12.05-2016.01.15
2016.01.16-2016.02.25
2016.02.26-2016.04.15
2016.04.16-2016.05.05
2016.05.06-2016.05.13
2016.05.13-2016.05.26
確定選題,填寫審題表;指導(dǎo)教師下發(fā)任務(wù)書,學(xué)生查閱課題相關(guān)參考文獻(xiàn)、資料,撰寫開題報(bào)告。
提交開題報(bào)告、外文參考資料及譯文、畢業(yè)設(shè)計(jì)(論文)大綱;開始畢業(yè)設(shè)計(jì)(論文)。
具體設(shè)計(jì)或研究方案實(shí)施,提交畢業(yè)設(shè)計(jì)(論文)草稿,填寫中期檢查表。
完成論文或設(shè)計(jì)說明書、圖紙等材料,提交畢業(yè)設(shè)計(jì)(論文)定稿,指導(dǎo)老師審核。
提交畢業(yè)設(shè)計(jì)紙質(zhì)文檔,學(xué)生準(zhǔn)備答辯;評閱教師評閱學(xué)生畢業(yè)設(shè)計(jì)(論文)。
根據(jù)學(xué)院統(tǒng)一安排,進(jìn)行畢業(yè)設(shè)計(jì)(論文)答辯。
所在專業(yè)審查意見:
負(fù)責(zé)人:
2016年 1 月 14 日
畢 業(yè) 設(shè) 計(jì)(論 文)外 文 參 考 資 料 及 譯 文
譯文題目:Design of Breke Assist System for Car
方程式賽車的空氣動(dòng)力制動(dòng)裝置
學(xué)生姓名:
?! I(yè):
所在學(xué)院:
指導(dǎo)教師:
職 稱:
2016年1月20日
Aerodynamic Brake for Formula Cars
By Robert
Abstract: In the last years, in formula racing cars championships, the aerodynamic had reached an ever more important stance as a performance parameter. In the last four seasons, Red Bull Racing Technical Officer had designed their Formula 1 car with the specific aim to generate the optimal down force, in relation to the car instantaneous setup. However, this extreme research of higher down force brings some negative effects when a car is within the wake of another car; indeed, it is well known that under these condition the aerodynamic is disturbed, and it makes difficult to overtake the leading car. To partially remedy this problem, Formula 1 regulations introduced the Drag Reduction System (DRS) in 2011, which was an adjustable flap located on the rear wing; if it is flattened, allowing to reduce the down force, increasing significantly the velocity and, therefore, the chances to overtake the leading car. Vice versa, when the flap is closed, it ensures a higher grip, which is very useful especially in medium-slow speed turns. Keeping the focus on the rear wing, but by shifting attention from the increased top speed to increase the grip in the middle and slow speed curves, we decided to study a similar device to the DRS, but with the opposite effect. The aim is to design an aerodynamic brake integrated with the rear wing. In particular, the project idea was to sculpt, on the upper surface of the wing (pressure side), a series of "C" shaped cavity, normally covered by adequate sliding panels. These cavities, when they are discovered, at the beginning of the braking phase, produce a turbulence and additional increase down force, lightening the load on the braking system and allowing the pilot to substantially reduce slippage and to delay the braking. Since it seems that the regulations adopted by the FIA Formula 1 Championship do not allow such a device, it has been decided to apply the concept on a Formula 4 vehicle. This paper describes the design and analyzes the effects of these details on a standard wing cavity, using CFD software.
Keywords: Aerodynamic Brake; Cavity; Dynamic Effects; Fluid Dynamic Simulation
1 Problem Formulation
In this paper, the realization of an aerodynamic brake integrated in a rear wing of a formula car has been considered. The first step consists in the choice of an appropriate aerodynamic appendix. In particular, it was decided to study an Italian Formula 4 race car [1], being a category in the first stages of development. Also, the regulation of this championship is easy to find and the car is characterized by uniformity of the mechanics and the air-foils. Therefore, taken note of the technical regulation on FIA website, it was decided to study the upper airfoil, of which was shown a dimensioned drawing (Figure 1). It is an aluminum alloy wing, with a chord line of 237.9 mm and a height of 54.2 mm.
Formula 4 championship will provide the use of a 4T heat engine(Otto/Beau de cycle): it can be naturally aspirated or turbocharged, with maximum power in the order of 120 kW (160 HP). Considering the weight of the car and the race tracks of the championship, it is predicted a maximum speed of 230 km/h (64 m/s). Regarding the operating conditions, an air temperature of 300K was assumed at atmospheric pressure.
Briefing Description of Airfoil Behavior
Considering an airfoil, there are several elements that have a specific nomenclature:
1) Mean camber line: locus of points halfway between the upper and lower surface as measured perpendicular to the mean chamber line itself;
2) Leading edge: the most forward point of the mean camber line;
3) Trailing edge: the rearmost point of the mean camber line;
4) Chord: the straight line joining the leading edge with the trailing edge;
5) Upper surface: the upper boundary of the profile;
6) Lower surface: the lower boundary of the profile;
7) Thickness: the distance between the lower surface and the upper surface.
The different airfoil shapes are marked by a logical numbering system which was introduced by the U.S. federal agency NACA. This system consists of four digits which have a definite meaning: the first digit indicates the maximum camber in hundredths of chord; the second digit represents the location of maximum camber along the chord from leading edge in tenths of chord; the third and fourth give the maximum thickness in hundredths of chord.
When an airfoil is moving relative to the air, it generates an aerodynamic force, in a rearward direction at an angle with the direction of relative motion. This aerodynamic force is commonly resolved into two components: lift and drag. Lift is the force component perpendicular to the direction of relative motion while Drag is the force component parallel to the direction of relative motion. These forces are studied at different angles of attack which is the angle at which an airfoil cleaves fluid. The experimental data show that CL varies with the angle of attack: more precisely, at low angles of attack the lift coefficient CL varies linearly with α. In a region characterized by a linear trend, the flow moves smoothly over the airfoil and is attached to the back of the wing. As soon as α increases, the flow tends to separate from the surface of the airfoil, creating a region of “dead air” behind the profile. A briefing flow analysis of the physical phenomenon in question in order to understand better what is happening in the latter case is reported. It is clear from Figure 2 that the speed at the trailing edge tends to increase, with a strong reduction of the pressure, while in the stagnation point the speed tends to be zero and pressure rises sharply. It creates an adverse pressure gradient, thus particles of fluid move from the trailing edge to the stagnation point, and then it has a rapid separation of the boundary layer below. Stagnation point does not have a stable position in these conditions because there is not pressure recovery. The recirculation generated by
the detachment of the boundary layer creates first vortex that causes a wake vortex. It is necessary to study the turbulent behavior of the fluid that meets the wing, through the Navier-Stokes equations in order to consider the stall of the wing:
where u(x, t) is the instantaneous velocity, ρ the medium density, μ the viscosity and f the applied force.
This system of equations is a system of partial differential equations that describe the behavior of a Stokesian fluid: the fluid can be considered to be continuous. There is an analytical solution only in simplified cases, while solutions in the other cases can be obtained using simplified methods of numerical analysis. The most straightforward method for the numerical simulation of turbulent flows is direct numerical simulation DNS which discretizes the Navier-Stokes equations. It resolves the entire range of turbulent length scales thus the description of the flow is so detailed that the validity of the simulation is similar to an experiment. The computational cost is proportional to Re3, thus it is necessary to use a different solution studying turbulent flows at high Reynolds, because the computational resources required by a DNS would exceed the capacity of the most powerful computer currently available. In practical applications, the knowledge of the average quantities is enough to solve the problem of a turbulent flow; the basic idea of the technique RANS (Reynolds Averaged Navier-Stokes Equations) is to derive only the average parameters (mediated in time) from Navier-Stokes equations, reducing the enormous computational cost required by DNS. In practice, the turbulent motion consists of a mean motion and fluctuation over time. Using the decomposition of Reynolds:
Where u( x, t) is the instantaneous velocity, u( x, t) is the average velocity u′( x, t) is the speed fluctuating, through Navier-Stokes equations it’s possible to obtain the Reynolds averaged equations. The equations for the mean motion obtained are similar to Navier-Stokes equations with the exception of the divergence of the stress tensor Reynolds: the system resulting from the Navier-Stokes equations is closed, while the system resulting from the RANS simulation is not open because Reynolds tensor introduces 6 additional unknowns. The problem mentioned is known as the problem of closure of turbulence which is solved by introducing models for the turbulent fluctuations which have to reproduce the action of fluctuating terms on mean motion.
The K-ε model is one of the most common models of turbulence, even if it is not appropriate in the case of strong adverse pressure gradients. It is a model with two equations: it includes two additional transport equations to represent properties of the turbulent flow and effects such as convection and diffusion of turbulent energy. The first variable transported is the turbulent kinetic energy, k. The second variable transported is the turbulent dissipation, ε; the second variable determines the scale of turbulence, while the first variable k determines the energy in the turbulence. There are two formulations of the K-ε models: the standard k-epsilon model and the RNG k-epsilon model.
In the standard k-epsilon model, eddy viscosity is determined by single length scale turbulence, so the turbulent diffusion is calculated only through a specified scale, whereas in reality all scales of motion will contribute to turbulent diffusion.
The approach RNG (Re-Normalisation Group), a mathematical technique that can be used to obtain a model similar to the k-epsilon turbulence, presents a modified equation ε, which attempts to explain the different scales of turbulence through changes at the term of production of turbulence. The equations used are:
a) Kinematic Eddy Viscosity
b) Turbulence Kinetic Energy
c) Dissipation Rate
Closure coefficient for standard k-epsilon model:
1. Project Description
The purpose of this project is to improve the race performance, reducing the breaking distance and increasing the bending speed.So, we decided to intervene on the drag generated by the wing during the breaking, and also on the grip provided by downforce, function of velocity. To explain the lift, and then the downforce, reference may be made to the wing of an airplane, observing its section. The latter is asymmetric, the top has a profile longer than the bottom: when the wing moves, it separates the relative flow in two parts, so the air layers scroll faster in the top. The outflow over the wing undergoes a boost and then is aerodynamic brake for formula cars accelerated towards the tail at a higher velocity than the air under the wing, which follows a shorter path. So the two currents are reunited in the tail after a same time interval, without creating imbalances. This is not just the facts, but as a first approximation, we can refer to this model. In reference to the Bernoulli trinomial law, since in the lower flow velocity is lower than in the upper, the pressure under the wing has to be greater than that above the wing. Therefore, the difference between the two pressures generates a resultant directed upwards, that is the lift, which holds the aircraft in the air. In detail, lift can be expressed as:
where:
ρ is the medium density;
V is the air velocity;
A is the reference surface;
Clis a lift dimensionless coefficient;
α is the wing angle of attack.
In racing cars, the wing is mounted upside down and the vertical thrust towards the ground (downforce): this is correlated to the tires grip coefficient. The running resistance depends on its front section, its forward speed, the density of the medium and a drag coefficient. The drag coefficient (Cd) depends on the object shape and size of the object, the medium density and viscosity, the surface roughness, and the object velocity. The aerodynamic resistance (in general fluid dynamics), or drag, is related to a large number of factors, as shown by the formula:
where:
? ρ is the medium density of the;
? V is the air velocity;
? A is the reference surface (in case of aircraft is the wing surface, the car front surface);
? Cd is a drag dimensionless coefficient;
? α is the wing angle of attack.
The overall resistance opposed by a fluid medium to the object forward movement is given, in first approximation, by the sum of the frictional resistance, the wake resistance and the induced resistance of lift. In particular, for a tapered body, the flow resistance is given by friction (laminar and/or turbulent), that is the rubbing of the surface against the medium. For this purpose we introduce the concept of boundary layer: it’s the dynamic range, laminar or turbulent, in which internal current speed is subject to strong gradients (continuous changes), due to the viscosity of the fluid. It can be considered as the area that undergoes a disorder, and the velocity is zero on the layer surface (Figure 3).
The thickness of the boundary layer is very small, and it is of one order of magnitude lower than the overall dimensions of the object, that generates the viscose perturbation. Then, inside the boundary layer, the tangential shear stress is “dense”. For this reason in the layer is exerted an intense dissipative braking action, converting part of the movement in thermal agitation. The dissipative action limits the relative velocity between the object and the fluid, which surrounds it. In a turbulent boundary layer, the viscous stresses are added also the stresses, due to the exchange of transverse momentum; these actions increase with the fluid density. The chaos of the turbulent fluid motions implies higher thermal dissipation, so the braking opposing force, in turbulent flow conditions, is greater than that of the laminar regime. The resistance generated, in this way, is affected by the surface roughness: moreover, the rougher surfaces ignite earlier and more easily the turbulent condition in the flow, and then, determine higher resistances. Therefore, it was decided to design some ducts, on the pressure side of the wing, initially covered by special sliding plates, for increasing the aerodynamic drag and downforce [2].
2. Wing Design
The first phase of the design is to draw the profile of the wing with a CAD software. In this way, it is possible to make a CFD simulation, to evaluate the aerodynamic performance of the wing, in terms of downforce and drag, and estimate the useful angles of attack before stall phenomenon occurs [3]. In fluid dynamics the stall is a reduction of the lift coefficient due to an increase of the angle of attack or due to the incident velocity decrease on an aerodynamic profile, such as an airfoil, a propeller blade or a turbomachinery rotor. The minimum value of the angle of attack for which the stall occurs is called critical angle of attack. This value which corresponds to the maximum lift coefficient, changes significantly, depending on the particular profile or on the considered Reynolds number [4]. Similarly, the profile of the active cavities has been reported, and appropriate simulations were performed. In this way it was possible to estimate the sizes and configurations to achieve the project target.
Based on the data collected, the application of these cavities on the wing is studied, evaluating the performance on the different possible arrangements of these cavities. At this moment only 2D simulations have been performed, and a 3D series is considered as future improvement of the project. The models, the different configurations and the results obtained from all the cases mentioned above, will be shown in detail in the following paragraphs.
Geometry Modeling
To approximate the operating conditions of the wing, a control conduit with the dimensions shown in Figure 4(a)
has been chosen. Regarding to the active cavity, the geometry is illustrated in Figure 4(b). The space surrounding the geometry of the aerodynamic and the cavities was discretized using a special dedicated software available as ANSYS package. Furthermore, to observe the progress of the boundary layer, it was built on a reference mesh of 5 layers, with growth factor 1.1, starting from the adjacent profiles of height 0.18 mm (Figure 5). To this purpose, a sizeable set of data was created by means of sufficiently accurate numerical simulations, to derive initial values. The simulations were performed on 3-D models in kinematic similarity using a commercial CFD simulation code, ANSYS/Fluent. The turbulence model was the k-ε realizable, with second order accuracy. Each model was meshed to ensure a y+max~ 5, a necessary condition for adopting the enhanced wall treatment, since the quality of the grid has a relevant importance on the accuracy and stability of the numerical simulation.
Commercial software allows the “plastering” of cell layers to the critical boundaries of the control volume, which are obviously, in this case, the wall surfaces of the hub, casing and blades. In these zones the usual practice is that of creating a completely structured boundary layer, specifying whenever possible both the height of the first row of cells and the “growth ratio”, i.e. the rate that determines the height of the successive cells. In this process, the height of the first row of cells is usually determined via an empirical formula that gives the value of a wall-based local Reynolds number, denoted by y+ (y+ = u*·y/v where u*= (τwall/ρ)1/2, with τwall being the wall shear stress). For the wing analysis control volume was split in several smaller sub-volumes, to achieve a more consistent set of faces and to better exploit the possibility of creating a locally more refined grid. The choice of the boundary conditions was made as follows: it was performed heuristically, starting from the preliminary sizing data, calibrating them by means of a first simulation, adjusting the values by iteratively resetting the outlet static pressure on the near-wake radial area downstream of the trailing edge. Through subsequent simulations the values of the inlet total pressure and temperature were refined as well in order to ensure conservation of the mass flow rate (the so-called “mass flow inlet condition” was adopted). The turbulent parameters were the turbulence intensity I =( k) U . Rotational periodicity was imposed on all lateral channel surfaces. The number of cells is about 65,000 elements. Finally, the starting boundary conditions are:
? fluid: it is considered air as an ideal gas at constant viscosity;
? input data: the pressure of 101325 Pa and temperature of 300 K represent the operating conditions. boundary conditions:
? inlet → mass flow rate;
? outlet → pressure outlet;
? for both, the conditions relating to the model were set on intensity and length scales, with values of 5% and 0.03 m (?1/10 of the rope)respectively;
? on the upper and lower walls of the duct it has set the periodicity condition;
? for wing, are set on the condition stationary wall and no slip;
? for the solution a simple high order term and relaxation has been chosen, by setting for all variables a relaxation factor of 0.25.
3. Conclusions and Possible Improvements
The CFD simulations indicate the effectiveness of active cavities, practiced on a formula car rear wing, in order to achieve an aerodynamic brake. Specifically, we can assert that the configuration with the best balance between downforce and drag is that with extended ducts over the entire top surface of the aerodynamic (Fl= ?365.172N, Fd= 65.88N). Finally, by exploiting the