庫(kù)存補(bǔ)貨買賣雙方易腐農(nóng)產(chǎn)品的建模畢業(yè)論文文獻(xiàn)翻譯
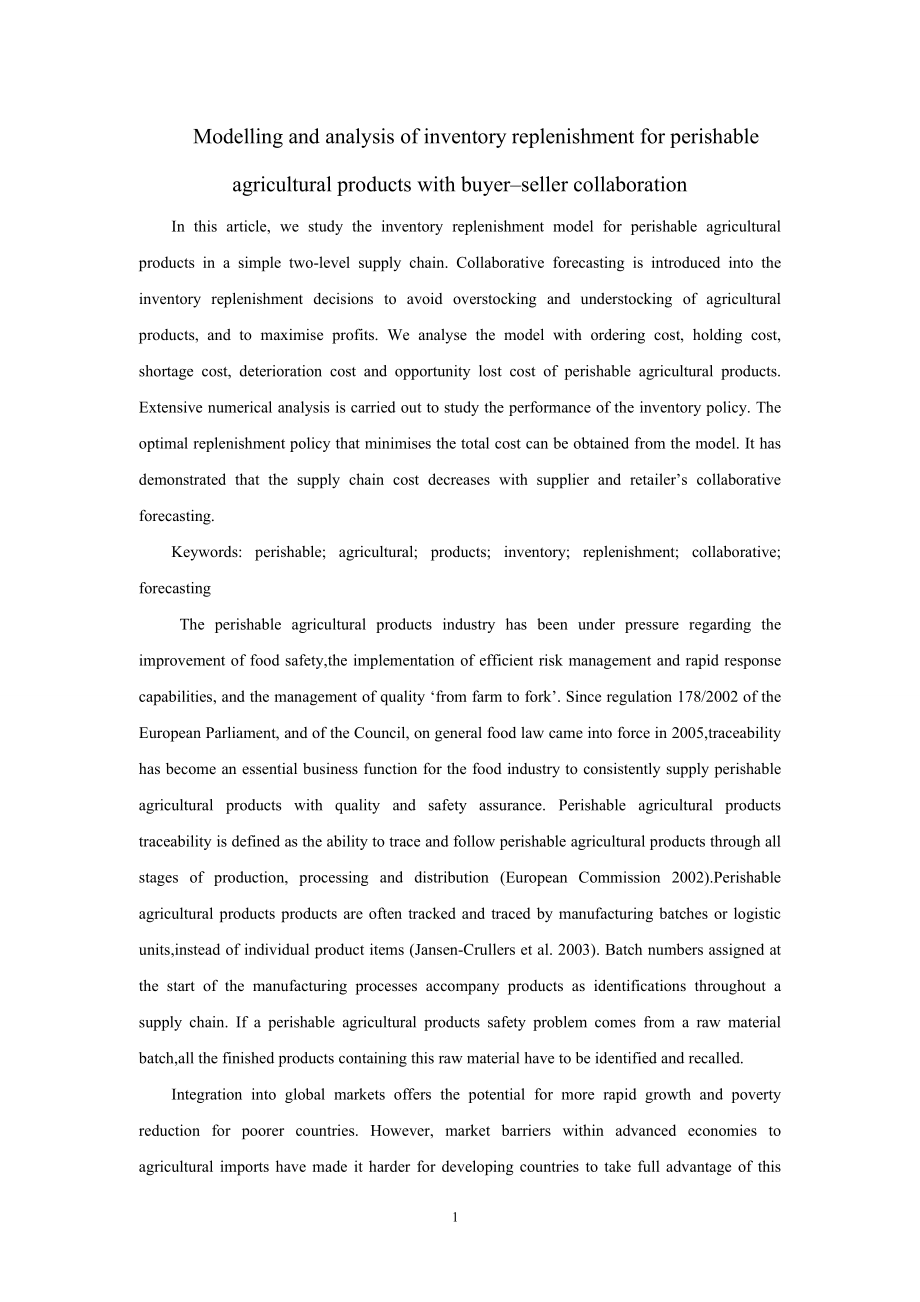


《庫(kù)存補(bǔ)貨買賣雙方易腐農(nóng)產(chǎn)品的建模畢業(yè)論文文獻(xiàn)翻譯》由會(huì)員分享,可在線閱讀,更多相關(guān)《庫(kù)存補(bǔ)貨買賣雙方易腐農(nóng)產(chǎn)品的建模畢業(yè)論文文獻(xiàn)翻譯(13頁(yè)珍藏版)》請(qǐng)?jiān)谘b配圖網(wǎng)上搜索。
1、 Modelling and analysis of inventory replenishment for perishable agricultural products with buyer–seller collaboration In this article, we study the inventory replenishment model for perishable agricultural products in a simple two-level supply chain. Collaborative forecasting is introduced
2、into the inventory replenishment decisions to avoid overstocking and understocking of agricultural products, and to maximise profits. We analyse the model with ordering cost, holding cost, shortage cost, deterioration cost and opportunity lost cost of perishable agricultural products. Extensive nume
3、rical analysis is carried out to study the performance of the inventory policy. The optimal replenishment policy that minimises the total cost can be obtained from the model. It has demonstrated that the supply chain cost decreases with supplier and retailer’s collaborative forecasting. Keywords: p
4、erishable; agricultural; products; inventory; replenishment; collaborative; forecasting The perishable agricultural products industry has been under pressure regarding the improvement of food safety,the implementation of efficient risk management and rapid response capabilities, and the manage
5、ment of quality ‘from farm to fork’. Since regulation 178/2002 of the European Parliament, and of the Council, on general food law came into force in 2005,traceability has become an essential business function for the food industry to consistently supply perishable agricultural products with quality
6、 and safety assurance. Perishable agricultural products traceability is defined as the ability to trace and follow perishable agricultural products through all stages of production, processing and distribution (European Commission 2002).Perishable agricultural products products are often tracked and
7、 traced by manufacturing batches or logistic units,instead of individual product items (Jansen-Crullers et al. 2003). Batch numbers assigned at the start of the manufacturing processes accompany products as identifications throughout a supply chain. If a perishable agricultural products safety probl
8、em comes from a raw material batch,all the finished products containing this raw material have to be identified and recalled. Integration into global markets offers the potential for more rapid growth and poverty reduction for poorer countries. However, market barriers within advanced economies to
9、agricultural imports have made it harder for developing countries to take full advantage of this opportunity. This article examines the impact of increasing demands for food safety and quality by European food retailers, and how the fundamental structure and culture of supplier organizations require
10、d by European retail chains are a major entry barrier for developing.Mediterranean fresh produce exporting countries, and for developing countries in general. The long-term solution for such countries to sustain an international demand for their products lies in structural, strategic and procedural
11、initiatives that build up the trust and confidence of importers/retailers in the quality and safety assurance mechanisms for their produce. Market failure to deliver the level of safety to meet public health requirements and consumer demands constitutes economic grounds for public policy interventi
12、on (Unevenness and Jensen, 1999). The lack, or high cost, of information, and the resulting consequences for public health are the fundamental justifications for public intervention to improve food safety. However, allocating food chain safety responsibilities from ‘farm to table’ has created a new
13、paradigm for stakeholder relationships characterized by complex interactions between public and private modes of regulation. The increasing globalization of food production and consumption make it difficult for national governments to exert comprehensive controls over the entire supply chain, and to
14、 identify the roots of quality problems in foreign countries, or end of pipe management (Spiller, 2002). The resulting shift of responsibility towards the private sector has created a more complex and demanding ‘policy space’ involving public and private sector incentives and controls. The interacti
15、on between self-regulation and public regulation could provide a superior outcome, as industry and firms are more knowledgeable regarding product quality, and public regulation can generate reputation-based incentives to monitor quality, in the form of public exposure. However, increasing deman
16、ds for food safety by developed countries have raised concerns about likely food regulatory impacts on international trade, particularly in the case of developing countries (Trotski et al., 2001; Henson and Loader, 2001;Henson et al., 2000; Unevenness, 2000). It is recognised that developing countri
17、es are likely to have difficulties in meeting requirements associated with the implementation of high level sanitary or phytosanitary measures which come in connection with technical regulations, standards and conformity tests (IMF/World Bank, 2002; Garcia Martinez et al., 2002; Garcia Martinez and
18、Poole, 2004; Wilson and Abiosis, 2003). As the commercial and institutional infrastructure develops, there is the risk that new regulatory barriers will be erected. This is of particular concern for developing countries, where existing technical and institutional capacity to control and ensure comp
19、liance may not allow for the adjustments needed to meet new requirements. Most of the current debate has focused on the impact of public national and supranational (e.g. European Union) regulatory demands on market access for developing countries (see for example, Reardon et al., 1999; Busch et al.
20、, 2000;Weather spoon and Reardon, 2003; Unevenness, 2000). The critical focus now needs to shift from such public regulatory standards, or Tats (technical barriers to trade), towards the increasing importance of food safety regulations imposed over and above public standards by private sector (comme
21、rcial) firms, and their potential impact on agricultural and food product exports from developing countries. Opportunities and threats both arise from the growth of such private standards,which can be termed ‘commercial barriers to trade’。 Unsurprisingly, the safety of food products has been a topi
22、c of debate for centuries. The first known law pertaining to the purity of food products, known as the “German Beer Purity Law” or Reinfestation,dates as far back as 1516 (Dornbusch, 1997). Today we have a myriad of laws, regulations, standards, processes, tools and technologies intended to ensure f
23、ood safety. Nevertheless, food safety scandals still occur on an all too regular basis. Table 1 presents some high profile food safety incidents that have occurred in several countries. From a safety perspective, food supply chains have a number of vulnerabilities (Whipple et al., 2009). First, the
24、y deal with natural products, many of which are perishable and could become harmful to consumers if not managed in a timely and safe manner (Akkerman et al., 2010). Secondly, food supply chains tend to be long, global and highly interconnected, leading to greater risk exposure (Henson and Reardon, 2
25、005; Roth et al., 2008; Triene kens and Zuricher, 2008; Whipple et al., 2009). Third, food and beverage products are at risk of intentional or unintentional adulteration and could even be the target of terrorist threats (Wei n and Lou, 2005;Whipple et al., 2009). According to Harl (2002), among seve
26、n general areas of vulnerability to terrorism in the US, five are related to the food supply chain. Careful management across the entire supply chain is necessary to ensure that-products reaching the final consumer are safe to eat and drink. Research by Voss et al. (2009) explores the tradeoffs amo
27、ng price, delivery, quality and safety in selecting suppliers in the food supply chains of the U.S. Their research concludes that, in general,safety considerations tend to be less important in selecting suppliers when compared to quality, delivery and price. They argue that this lower priority could
28、 be a factor behind the frequency of food safety incidents. However, their results also indicate that safety is more important under certain circumstances, particularly when products are sourced from abroad. Failures in food safety can have serious negative consequences not only for consumers, but a
29、lso for the companies involved. The worst case scenario occurs when incidents lead to deaths or illness (Trienekens and Zuurbier,2008). According to Thomsen and McKenzie (2001) millions of people around the world become ill every year as a result of unsafe foods. It has been estimated that in the U.
30、S. alone, foodborne pathogens account for 76 million illnesses and 5000 deaths (Mead et al., 1999). Thomsen and McKenzie (2001) argue that human error and the limitations of food safety technology mean that,from time to time, consumers will face food safety risks. High profile incidents such as the
31、Salmonella outbreak caused by peanut butter paste sold by the Peanut Corporation of America in 2008 (Layton and Miroff, 2009), or the adulteration of powdered milk with melamine in China in the same year (Spencer, 2009), have made the headlines due to their scale and severity. In both cases the con
32、sequences for those involved have been serious. The Peanut Corporation of America filed for bankruptcy in February 2009 (Layton and Miroff, 2009). In the Chinese case, Sanlu, the company responsible,has been closed down, the general manager and a number of company officials are in jail, and two have
33、 been sentenced to death (Spencer, 2009). Most food safety incidents do not lead to death or illness, and in many cases products can be recalled before they reach the consumer. However, recalls can be complex and costly (Thomsen and McKenzie, 2001; Whipple et al., 2009), they can damage a firm’
34、s reputation (Hornibrook et al., 2005; Thomsen and McKenzie, 2001;Whipple et al., 2009), and ultimately affect the consumers’ perception of an entire product category (Henson and Reardon, 2005;Trienekens and Zuurbier, 2008). All of these factors can contribute to shareholder losses. A study by Thoms
35、en and McKenzie (2001) uses event analysis to evaluate the impact of product recalls on shareholder loses. They conclude that in cases where the product recalled poses a serious threat to consumers’ health, there is a loss in shareholder wealth of between 1.5% and 3%. However, they also conclude tha
36、t recalls involving less serious infringements have no negative impact on shareholder wealth. One of the important characteristics of agricultural products, such as eggs, milk, dairy products and vegetables is their biotic energy. The period of time for which their quality remains acceptable
37、is very short,which means they are easily perishable in the course of transportation and storage. However, we human beings rely on the good condition of agricultural products to stay alive and healthy. Therefore, it is crucial that the inventory of agricultural products is managed properly. On the o
38、ne hand, the price of agricultural products is time-sensitive, implying that the price decreases dramatically as the end of the product’s life approaches. On the other hand, a shortage of agricultural products while there is demand for the product may result in significant loss of revenue. Establish
39、ing an efficient and effective inventory system to obtain the right quantity of products of the right quality, from the right source,and to have the products delivered to the right place at the right price can have a positive influence on a company’s profitability and competitive advantage. However,
40、 achieving this is constrained by issues ofcompetition, profitability, product harvest and other relevant conditions. As a major input to the agricultural inventory system, inventory replenishment is a major criterion for guaranteeing sales and reducing costs.Replenishment cost and inventory cost c
41、an be regarded as the two most important cost items, which account for the majority of the overall cost. A reduction in these two costs can lead to a significant decrease in operational cost. The value of agricultural products drops with passage of time. Therefore, while taking the inventory cost of
42、 agricultural products into account, one has to consider not only the inventory holding cost but also the inventory depreciation cost. However,conventional inventory systems encounter problems, such as difficulty in sharing information,empiricism in purchase decision making, unstable cooperative rel
43、ationships between purchasers and suppliers, the impossibility of tracking purchases, and the waste arising from the decay of agricultural products because of over-purchasing. These factors result in slow reactions to client demand, poor adjustment to demand fluctuation, probable overstocking or pro
44、duct shortages and so on. These factors, in turn, have serious effects on profits from sale of agricultural products. Moreover, under certain circumstances, inventory depreciation cost is a key factor in determining operational costs. However, inventory costs can be controlled by appropriate repleni
45、shment decisions. In other words, replenishment is the core of agricultural inventory control.Collaborative planning, forecasting and replenishment(CPFR) is proving to be one of the most successful mechanisms in transforming relationships between partners into a win-win situation where customer sati
46、sfaction, costs and revenues can all improve simultaneously. It bui lds upon efficientconsumer response (ECR) principles including vendor managed inventory (VMI), jointly managed inventory(JMI), continuous repl enishment (CRP)and category management. The global commerce initiative (GCI),the global s
47、corecard,categorises CPFR in its integrator group of initiatives. However, owing to many unique characteristics of agricul tural products, such as their biological, seasonal,unstable and peris hable nature, the CPFR process needs to be improved to reflect these charact eristics when it is appli
48、ed to agricultural product purchasing management. On acco unt of perishability issues,agricultural industry buyers tend to make frequent purchases of small quantities of a product. In additio n,critical issues, such as consistency in delivery and quality are extr emely variable. Considering the freq
49、uent and uncertain distrib ution of agricultural produc ts,collaborative transport management (CTM) is appl ied to the purchasing process and distributi on forecasting is also added in order to assign distribution resources effectively. Given the quick response (QR) required in agricultural product
50、purchasing, supply and demand forecasts are to be made simultaneously by upstream and downstream enterprises; only then a collaborative forecast will be reached, which will shorten the overall forecasting time adequately. Du, Leung, Zhang, and Lai (2009) developed a procurement model for agricul tur
51、al products on the framework of CPFR.With the model construction and the case study, they showed that their proposed model with CPFR helps to minimise waste in products and to reduce cost and risk in agricultural indust ry. In an agricultural product supply chain, retailers can judge demand because
52、 they deal with consumers directly and suppliers can estimate their delivery abilities accurately because they are familiar with the supply situation. So, suppliers offer the stock, production estimates and related information at the supply end to downstream enterprises, while downstream enterprises
53、 transmit demand information to upstream enterprises. The final order is made after a collaborative demand fore cast is drawn, taking into account a series of promotions and unexpected events.In this article, we incorporate the collaborative forecasting into the inventory management of a two-level s
54、upply chain dealing with perishable agricultural products. With respect to the main components of suppl y chain cost, this article tries to develop an optimal repleni shment policy to avoid overstocking and understocking of agric ultural products, and to minimise the total cost of supply chain. In
55、this article, we incorporate the collaborative forecasting into the inventory management of a two-level supply chain dealing with perishable agricultural products. With respect to the main components of supply chain cost, this article tries to develop an optimal repleni shment policy to avoid overst
56、ocking and understocking of agricultural products, and to minimise the total cost of supply chain. The article is organized as follows. Some relevant literature is reviewed in Section 2. In Section 3, the model for buyer–seller calla borazon is introduced and the demand distribution function condit
57、ioned on collaborative forecasting is formulated. Then, the inventory replan ish ment model for perishable agricultural products with the demand fun-ct ion based on collabor ative forecasting is presented in Section 4. A numerical illustrative example is used to demonstr ate our model in Sec tigon 5
58、. Finally, some concluding remarks are given in Section 6. There has been a lot of research on inventory replenishment manage ment of perishable products under the supply chain environment. Many researchers have classified agricultural produc ts as perishable goods. They focus mainly on development
59、 of then inventory replenishm ent models for agricultural goods. The value of inventories of agricultural products is highly time dependent. Quality of stored inventory is easily affected by environ mental conditions, such as temperature, humidity and ventilation. Therefore,when developing a model,
60、 it is difficult to represent the deterioration process mathematically. God, Green-berg, and Matsu (1993) initiated the development of a two-stage inventory model for perishable products. The first stage represents the period of fresh ness, while the second stage represents the period of decay, duri
61、ng which the products still have a certain value. Lean and Lin (1999) developed the muti dimensional Markov chain to simulate the inventory process and derive a prime-cost function and to build a discrete-time inventory model for perishable goods. Chare and Schrieffer (1963) studied the effect of pe
62、rishing of goods in the inventory process and developed an inventory model accordingly. In this model, decay an deman d rates are constant. Covert and Phillip (1973) and Taklamakan (1978) expanded Geare and Schrieffer’s model and changed the decay rate from a constant to a function. Thereafter, Dave
63、 and Patel (1981) changed the demand rate to a linear function and formulated an inventory model for perishable products. Sac-han (1984) further enhanced Dave and Patel’s model and developed the (T, Si)-policy inventory model for perishable products, which allows shortages. Dat-ta and Pal (1988) dev
64、eloped the economic order quantity (EOQ) model which requires a variation in the deteriorat ion rate and the demand function to be exponentially distributed. Go swami and Chaud froid (1991), Svarabhakti and Chaudfroid (1997), Harish and Al-Alan (1997) and Frontbe ncher (1995)studied an inventory mod
65、el for time-dependent demand for perishable products, allowing for shortages and back orders. In recent years, Bunia and Haiti (1999) considered a finite time horizon and developed an inventory model for deteriorating products with time de-pen dent dema nd. The model assumed that cost per replenishm
66、ent is linearly dependent on the lot-size of that replenishment. Turning to the impact of price on purchasing decisions, Ballymoney (1971) stud ied a single-item mufti-period inventory model with stochastic price. Due to the stochastic nature of and variations in supply and demand, future prices of commodi ties fluctuate widely; they can be resolved by a Markovian stochastic process. The model was developed to determinethe form and bounds of optimal policies for finite and infinite planning hori
- 溫馨提示:
1: 本站所有資源如無(wú)特殊說(shuō)明,都需要本地電腦安裝OFFICE2007和PDF閱讀器。圖紙軟件為CAD,CAXA,PROE,UG,SolidWorks等.壓縮文件請(qǐng)下載最新的WinRAR軟件解壓。
2: 本站的文檔不包含任何第三方提供的附件圖紙等,如果需要附件,請(qǐng)聯(lián)系上傳者。文件的所有權(quán)益歸上傳用戶所有。
3.本站RAR壓縮包中若帶圖紙,網(wǎng)頁(yè)內(nèi)容里面會(huì)有圖紙預(yù)覽,若沒有圖紙預(yù)覽就沒有圖紙。
4. 未經(jīng)權(quán)益所有人同意不得將文件中的內(nèi)容挪作商業(yè)或盈利用途。
5. 裝配圖網(wǎng)僅提供信息存儲(chǔ)空間,僅對(duì)用戶上傳內(nèi)容的表現(xiàn)方式做保護(hù)處理,對(duì)用戶上傳分享的文檔內(nèi)容本身不做任何修改或編輯,并不能對(duì)任何下載內(nèi)容負(fù)責(zé)。
6. 下載文件中如有侵權(quán)或不適當(dāng)內(nèi)容,請(qǐng)與我們聯(lián)系,我們立即糾正。
7. 本站不保證下載資源的準(zhǔn)確性、安全性和完整性, 同時(shí)也不承擔(dān)用戶因使用這些下載資源對(duì)自己和他人造成任何形式的傷害或損失。
最新文檔
- 起搏器護(hù)理查房?jī)?yōu)選ppt資料
- 基于用戶行為相似好友推薦系統(tǒng)課件
- 人教a版高考數(shù)學(xué)(理)一輪課件44函數(shù)yasin(ωxφ)的圖象及三角函數(shù)模型的簡(jiǎn)單應(yīng)用
- 如何合理使用高血壓藥物專題宣講
- 廢棄紙張的危害課件
- 第8課 鳥語(yǔ)花香(1)
- 廣告投放模板
- 七年級(jí)英語(yǔ)下冊(cè) Unit 6 I’m watching TV Self check 課件 (新版)人教新目標(biāo)版
- 小學(xué)數(shù)學(xué)教學(xué)課件第7課時(shí)-約分
- 真北方說(shuō)課模版課件
- 小學(xué)五年級(jí)語(yǔ)文下冊(cè)第四單元青山處處埋忠骨作業(yè)課件新人教版3
- 看清“三股勢(shì)力”的真實(shí)面目主題團(tuán)會(huì)課件
- 人琴俱亡(教育精品)
- 新員工入安全培訓(xùn)課件
- 九年級(jí)政治全冊(cè) 第10課 第2站 培育民族精神課件2 北師大版
相關(guān)資源
更多