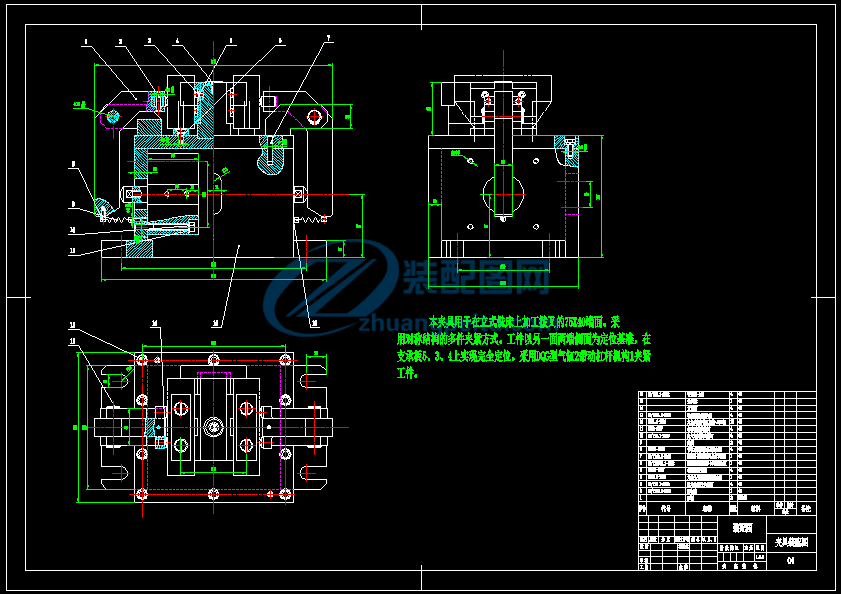
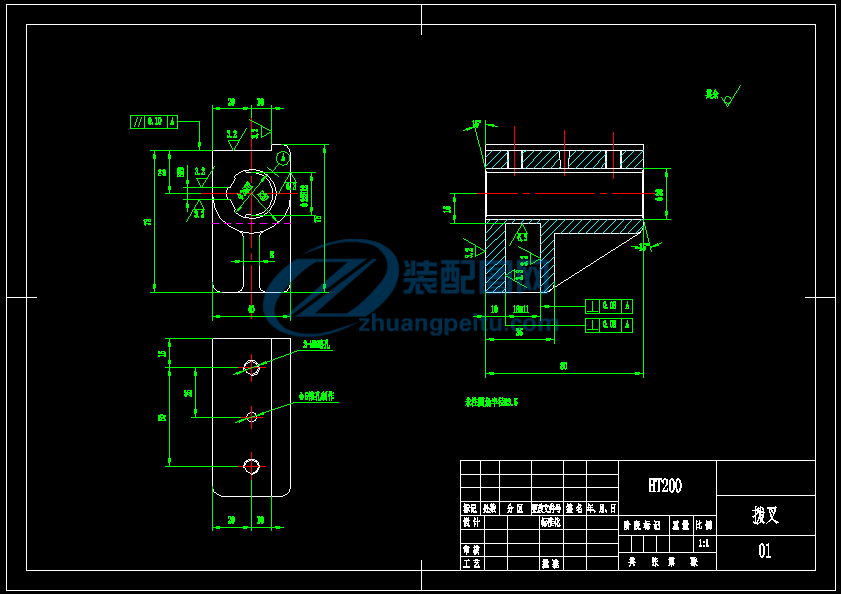
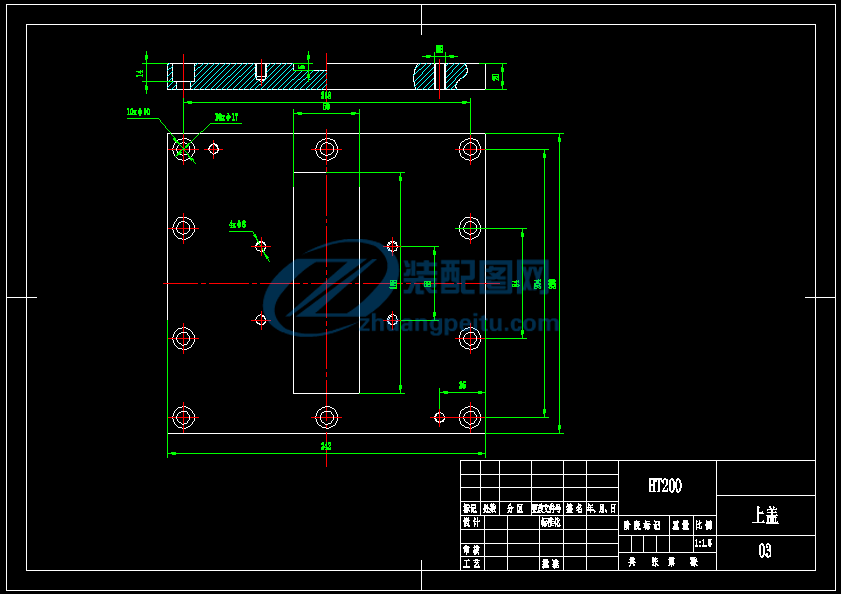
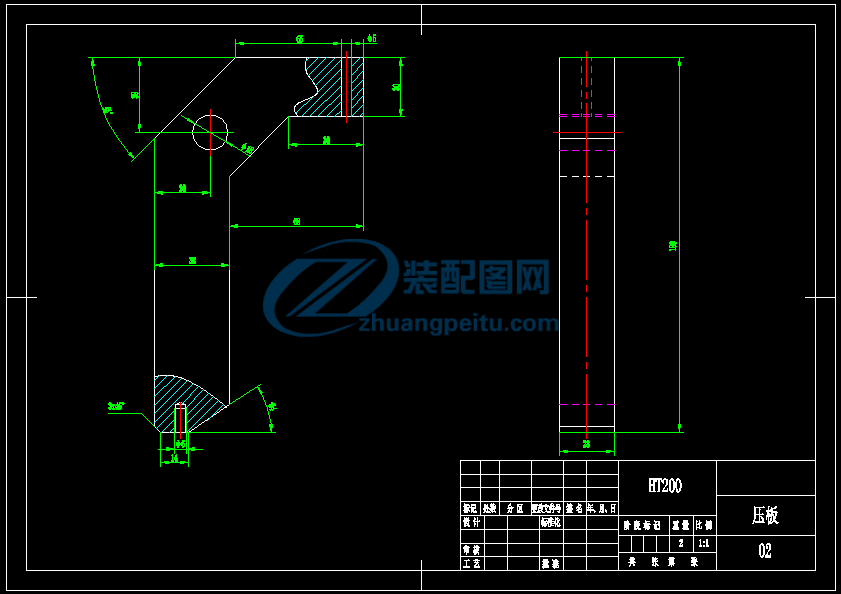
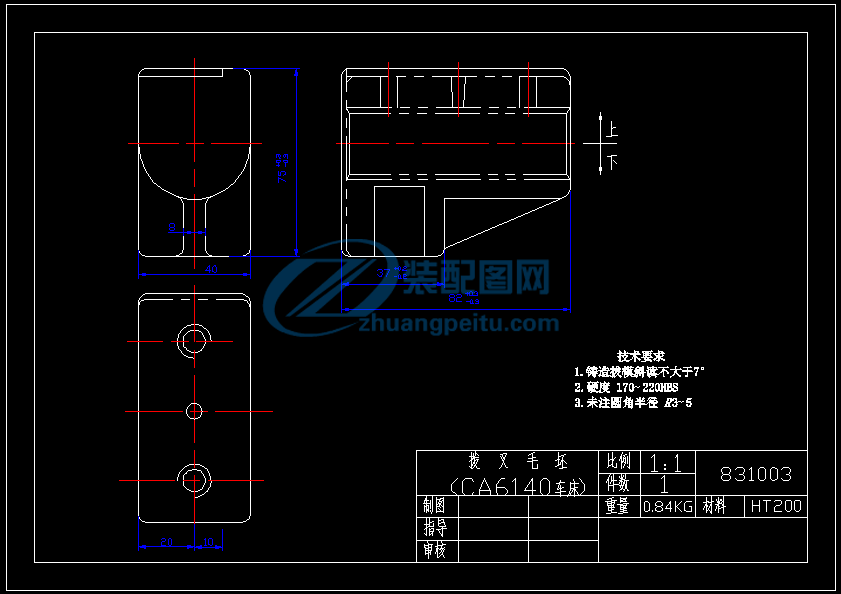


機械制造工藝學課程設(shè)計說明書設(shè)計題目: 設(shè)計“CA6140 車床拔叉”零件的機械加工工藝規(guī)程及工藝裝備(大批生產(chǎn))設(shè) 計 者 陳遠平指導教師 蔣克榮合肥學院2008.7.1目錄前 言 3一、零件的分析 3(一)零件的作用 3(二)零件的工藝分析 4二、工藝規(guī)程設(shè)計 4(一)確定毛坯的制造形式 4(二)基準面的選擇 4(三)制定工藝路線 4(四) 、機械加工余量、工序尺寸及毛坯尺寸的確定: 5(五)確定切削用量及基本工時 6工序一:鑄造毛坯 6工序二:粗、半精銑左端面 75×40 面即 C 面 .6工序三 鉆 Φ22 花鍵底孔,擴花鍵底孔 Φ22 倒 2×75o倒角 .7工序四 拉花鍵孔 9工序五 粗、精銑 80×30 面 .9工序六 鉆兩 M8 底孔及攻螺紋 11工序七 銑 18H11 的槽 12三、夾具設(shè)計 13一、 問題的提出 14二、 夾具設(shè)計 141、定位基準的選擇 142、.夾緊機構(gòu) 143.對刀裝置 144.夾具與機床連接元件 145.使用說明 146. 結(jié)構(gòu)特點 14參考文獻 14前 言通過所學的專業(yè)課知識(《公差與配合》 、 《工程材料》 、 《機械原理》 、 《機械設(shè)計制造》 、 《機械制造技術(shù)基礎(chǔ)》等)和金工實習使我們對機械設(shè)計制造有了一定的感性和理性認識。這次機床工藝及夾具設(shè)計讓我們對所學的專業(yè)課得以復習、鞏固和應用。是理論和實踐相結(jié)合的有效手段。不僅為大四的畢業(yè)設(shè)計做準備,而且為以后的工作打下一定的基礎(chǔ)。在這次設(shè)計中,我們主要設(shè)計 C6140 撥叉的夾具。在設(shè)計中閱讀大量的參考資料并且得到老師的指導由于能力有限在設(shè)計中難免有不足之處,懇請各位老師、同學批評指正。一、零件的分析(一)零件的作用題目給定的零件是 C6140 撥叉(見附圖 1)它位于車床變速機構(gòu)中,主要其換擋作用。通過撥叉的撥動使車床滑移齒輪與不同的齒輪嚙合從而達到要求的主軸轉(zhuǎn)速。寬度為 30mm 的面的尺寸精度要求很高,在撥叉工作工程中,和如果撥叉和槽的配合尺寸精度不高或者它們之間的空隙很大時?;讫X輪就達不到很高的定位精度,這樣滑移齒輪就不能很好的與其他齒輪進行正確有效的嚙合。從而影響整個傳動系統(tǒng)的工作。所以撥叉寬度為 30mm 的面和槽之間要達到很高的配合精度。(二)零件的工藝分析CA6140 撥叉共有兩組加工表面:1、這一組加工表面包括:A 端面和軸線與 A 端面相垂直的 花鍵底孔2、這一組加工表面包括: 六個方齒花鍵孔,及 Φ25mm 花鍵底孔兩端的2×75°倒角。對于兩組加工表面可先加工一組表面,再用專用夾具加工另一組表面。二、工藝規(guī)程設(shè)計(一)確定毛坯的制造形式此次所設(shè)計的撥叉材料為 HT200,根據(jù)材料成型工藝可知用金屬型鑄造。該零件能夠承受較大載荷和沖擊載荷,能夠滿足使用要求。因為生產(chǎn)綱領(lǐng)為大批量生產(chǎn)。因為零件形狀簡單故毛坯形狀需與零件的形狀盡量接近,又因內(nèi)孔很小,可不鑄出。毛坯零件圖見附圖 2。 (二)基準面的選擇1、粗基準的選擇:因為要保證花鍵的中心線垂直于撥動滑移齒輪的右端面。所以以 Φ40 的外圓表面為粗基準。2、精基準的選擇:為了保證定位基準和加工工藝基準重合,所以選擇零件的左端面為精基準。(三)制定工藝路線工藝路線方案一:工序一:鑄造毛坯;工序二:粗、半精銑左端面 C 面,工序三:鉆孔并擴花鍵底孔 Φ22 并锪 2×75°倒角;工序四:拉花鍵 Φ25H7工序五:粗、半精銑底面 D 面;工序六:鉆配作孔、螺紋孔;工序七:粗、半精銑槽;工序八:去毛刺;工序九:終檢,入庫。工藝路線方案二:工序一:鑄造毛坯;工序二:粗、半精銑左端面 C 面,工序三:終檢,入庫。工序四:拉花鍵 Φ25H7工序五:粗銑底面 D 面及 18H11 槽;工序六:半精銑底面 D 面及 18H11 槽;工序七:鉆配作孔、螺紋孔;工序八:去毛刺;工序九:鉆孔并擴花鍵底孔 Φ22 并锪 2×75°倒角;比較兩種工序加工方案,考慮到加工過程中粗精銑同一面可用同一夾具和刀具,為了減少換夾具及刀具的時間,縮短加工工時提高加工效率,故采用第一種加工方案。(四) 、機械加工余量、工序尺寸及毛坯尺寸的確定:C6140 撥叉材料為 HT200 毛坯質(zhì)量為 0.84kg,δ b=220MPa,HBS=157。根據(jù)上述原始資料和加工工藝,分別確定各個加工表面的機械加工余量,工序尺寸以及毛坯尺寸。根據(jù)零件圖計算輪廓尺寸,長 40mm,寬為 80mm,高為 75mm,故零件最大輪廓尺寸為 80mm。選取公差等級 CT 由《機械制造技術(shù)基礎(chǔ)課程設(shè)計指南 》中表 5-1 可查得毛坯件的公差等級為 8~10 級, ,取為 10 級。求鑄件尺寸公差 根據(jù)加工面的基本尺寸和鑄件公差等級 CT,由《機械制造技術(shù)基礎(chǔ)課程設(shè)計指南》中表 5-3 可查得尺寸公差為 CT=3.2mm求機械加工余量由《機械制造技術(shù)基礎(chǔ)課程設(shè)計指南》表 5-5 查得機械加工余量等級范圍為 D~F,取為 E 級求 RAM(要求的機械加工余量)對所有的加工表面取同一數(shù)值,由《機械制造技術(shù)基礎(chǔ)課程設(shè)計指南》表 5-4 查得最大輪廓尺寸為 80mm、機械加工余量為 E 級,得 RAM 數(shù)值為 0.7mm。求毛坯尺寸 2-M8 通孔和 Φ5 錐孔較小鑄成實心; C、D面單側(cè)加工,應由《機械制造技術(shù)基礎(chǔ)課程設(shè)計指南》式 5-2 求出,即: R=F+RAM+CT/2=80+0.7+3.2/2=82.3mmD 面為單側(cè)加工,毛坯尺寸由機械制造技術(shù)基礎(chǔ)課程設(shè)計指南》式 5-1求出,即:R=F+RAM+CT/2=72+0.7+3.2/2=74.3mm為了簡化鑄件的形狀取 R=75mm鑄件毛坯尺寸公差與加工余量見下表:項目 C 面 D 面公差等級 CT 10 10加工面基本尺寸 80 72鑄件尺寸公差 3.2 3.2機械加工余量等級 E ERAM 0.7 0.7毛坯基本尺寸 82.3 751、C 面的單邊總加工余量為 Z=2.3mm。查《機械制造技術(shù)基礎(chǔ)課程設(shè)計指南》表 5-49 精加工余量故粗加工余量為 Z=1.3m2、D 面精加工余量同 C 面 Z=1mm 故 D 面粗加工余量 Z=2mm3、花鍵孔要求以花鍵外徑定心,故采用拉削加工內(nèi)空尺寸為 。由《機械制造技術(shù)基礎(chǔ)課程設(shè)計指南》表 5-42 卻定12H?孔的加工余量分配:鉆孔: 20mm擴孔: 22mm?拉花鍵孔(6- 25H7* *6H9)12H?4、銑 18H11 槽由《機械制造技術(shù)基礎(chǔ)課程設(shè)計指南》表 5-41 查得粗銑后半精銑寬度余量Z=3mm 粗銑后公差為+0.18~+0.27 半精銑后公差為+0.11(IT11)(五)確定切削用量及基本工時工序一:鑄造毛坯工序二:粗、半精銑左端面 75×40 面即 C 面一、 粗銑面 75×40 面1、 背吃刀量的確定因為切削余量較小故一次切削就可切除所有余量故 a10=z=1.3mm。2、 進給量的確定。選用硬質(zhì)合金端銑刀刀具材料為 YG6 銑刀直徑為 8mm 齒數(shù)為 10,選用 X5032,立式升降臺銑床,功率為 7.5KW。由 《實用機械加工工藝手冊》表 11-92 可查得每齒進給量 fz=0.14~0.24mm 取fz=0.2mm/z3、 銑削速度的確定。由《實用機械加工工藝手冊》表 11-94 可查得灰鑄鐵的硬度為150~225HBS,查得 Vc=60~10m/min。則主軸轉(zhuǎn)速為n=1000Vc/ D=238.8~437.9r/min ?。V f=f zZn=477.6~875.6r/mm。故取 n=300r/min ,V f=480mm/min。切削工時:由《切削用量簡明手冊》表 3.26 可查得入切量及超切量Y+ =12mm。故?t= fVYL??= 4801275=0.18mim。二、 精銑 75×40 面1、 背吃刀量的確定由《實用機械加工工藝手冊》表 6-30 查得半精銑的銑削用量為 1mm ,即 ap=1mm。2、 進給量的確定選用與粗銑刀同樣的刀具與機床,由《實用機械加工工藝手冊》表11-92 要求表面粗糙度為 3.2 查得每轉(zhuǎn)進給量為 0.5~1.0 故取0.5mm/r3、 銑削速度的確定由《實用機械加工工藝手冊》查得銑削速度為 60~110m/min 則機床主軸轉(zhuǎn)速 n=1000Vc/ D=238.8~437.9r/mim 取 n= 300r/min,則?Vf=150mm/min。4、 計算切削工時由《切削用量簡明手冊》表 3.26 查得入切量和超切量Y+ =12mm。則?t= fVYL??= 15028=0.61mim工序三 鉆 Φ22 花鍵底孔,擴花鍵底孔 Φ22 倒 2×75o倒角1、 鉆 Φ20 的孔。1) 決定進給量由《切削用量簡明手冊》表 2.7 選擇高速鋼麻花鉆頭其直徑do=20mm。鑄鐵的硬度大于 200HBS 查得進給量 f=0.43~0.53mm/r 由于Yd=80/20=4 查得修正系數(shù) Ktf=0.95 則 f=0.41~0.50mm/r。由《切削用量簡明手冊》表 2.8 可查得鉆頭強度允許的進給量為f=1.75mm/r 。由《切削用量簡明手冊》表 2.9 可知機床進給機構(gòu)強度所允許的鉆削進給量。選用 Z525 鉆床由表 2.35 查得進給機構(gòu)允許的最大抗力Fmax=8830N,d o 20.5,查 f=0.93mm/s,故取 f=0.48 由《切?削用量簡明手冊》表 2.19 查得高速鋼鉆頭鉆孔的軸向力F=5510N 小于 Fmax,故可用。2) 確定鉆頭的磨鈍標準及壽命。由《切削用量簡明手冊》表 2.12 查的鉆頭后刀面最大磨損量取0.6mm,壽命為 T=15mim。 3) 確定切削速度odvn?10?2*4.38=286.6r/min由《切削用量簡明手冊》表 2.35 取 n=272r/min 則實際切削速度Vc= = =17.1 m/min。10Dn?01.74)檢驗機床扭矩及功率 由《切削用量簡明手冊》表 2.20 可查得 f 0.5 mm/r 時,Mc=76.81Nm。當?nc= 272r/min 時由《切削用量簡明手冊 》表 2.35 可查得 Mm=144.2Nm。由《切削用量簡明手冊》表 2.23 查得 Pc=1.1 kw。Pe=2.6×0.81=7.76 kw。因為 Mc Mm,Pc Pe,故所選切削用量可用。?f= 0.48mm/r ,n=n c=272r/min。Vc=17m/min。計算基本工時:tm= fL由《切削用量簡明手冊》表 2.29 查得入切量與超切量分別為 10mm 和 10mm。故:tm= = =0.69 mim。nfL48.0*271?二、擴 20 孔。?1、確定背吃刀量由《切削用量簡明手冊》查得背吃刀量為 2mm。2、確定進給量由《切削用量簡明手冊》查的 f=0.6~0.7mm/r。根據(jù)機床說明書取f=0.62mm/r3、計算切削速度1.7*3~2312?????????????Vn=5.7~8.5 m/min由此可知主軸的的轉(zhuǎn)速為:n=82.5r/min根據(jù)機床說明書取 n=140r/min,則實際切削速度v= =9.67 m/min104V?4、計算切削工時由《切削用量簡明手冊》表 2.5 可查得 Kv= 30~60,取 Kv=45。 由《機械加工工藝手冊》表 3.5.1 查得 tm= ,式中各參數(shù):fnL21?L=80mm,L 1=1.707~2.107 ,取 L1=2mm。故tm=0.8min工序四 拉花鍵孔由《機械加工工藝手冊》表 4.1-42 拉刀的齒開量查得矩形花鍵拉刀,工件材料鑄鐵的齒開量為 0.04~0.1mm,取齒開量為 0.06mm。拉削速度由《機械加工工藝手冊》表 4.1-65 查得表面粗糙度要切 Ra= 1.25~2.5,拉削速度為 級?的花鍵拉削速度為Vc=4.5~3.5 m/min 取 Vc=3 m/min拉削級別由《機械加工工藝手冊》表 4.1-66 查得。拉削加工工時t= zvfkLZb10?式中 Zb 為單面余量 Zb = =1.5 mm25?L 為拉削表明長度 L=80 mm為拉削系數(shù),取 =1.2??K 考慮機床返回行程系數(shù)取 k=1.4v 為拉削速度fz 為拉刀單面齒開量z 為拉刀同時工作齒數(shù) z= L/PP 為拉刀齒距 P=(1.25~1.5) =1.3580=12 mm所以拉刀同時工作齒數(shù)為z=L/P=80/12 7?所以t= *06.3141285.=0.16 min工序五 粗、精銑 80×30 面一、粗銑 80×30 面1、加工余量的確定由前面可知粗加工加工余量為 2 mm,加工余量較小故采用一次切削故ap=2 mm。2、切削用量的確定由《機械加工工藝手冊》表 2.1-20 選擇高速鋼立銑刀,銑刀直徑為 16 mm 齒數(shù)為 3。由《機械加工工藝手冊》表 2.1-96 查得加工材料為灰鑄鐵,銑削寬度為aw=d o/4,銑刀的銑削速度為 v=18.29m/min,每齒進給量為 0.063~0.102 mm/z則主軸轉(zhuǎn)速為n= =358.3~577.2 r/minD?10取 n=460r/min,由此可得 Vf= =0.09×3×460zn=124.2 mm/min3、銑削加工工時的計算由《機械加工工藝手冊》表 2.1-94 可查得t= ivlLwf21?式中i 為次給次數(shù) i= 8?430od=0.5d o+(0.5~1.0)=9 mm1l=1~2 mm 取 =2 mml則t= =5.86 min.4980?精銑 80×30 面1、加工背吃刀量 ap 的確定由前面可知道精銑的加工余量為 1 mm,故 ap=1 mm2、進給量的確定由《精銑加工工藝手冊》表 2.1-72 查得高速鋼立銑刀直徑為 16 mm,選用與粗銑時同一銑刀和機床。銑削寬度為 aw=3 mm 是的每齒進給量為 0.08~0.05 mm/z,因為表精度要求較高故 fz= 0.06 mm/z3、切削用量的確定由《機械加工工藝手冊》表 2.1-75 查得銑刀磨鈍標準查得后刀面最大磨損限度為 0.2~0.25 mm。由《機械加工工藝手冊》表 2.1-76 限度壽命查得限度壽命 T=60min。由《機械加工工藝手冊》表 2.1-92 查得 Vc=22 m/min,則銑床的主軸轉(zhuǎn)速:n= =437.9 r/minodv?10?取 n=460 r/min。 則 Vf=f z*z*n=0.06*3*460=82.8 mm/min4、計算銑削加工工時由上面可知t= ivlLwf21?式中、 、 與上述所相同。wl12l=30/3=10i將各參數(shù)代入上式可得:t= ×108.290?=11 min工序六 鉆兩 M8 底孔及攻螺紋1、選擇切削用量選擇高速鋼直柄麻花鉆直徑為 Φ7,鉆頭形狀為雙錐修磨橫刃。由《切削用量簡明手冊》表 2.7 查得進給量 f=0.36~0.44mm/r,由《切削用量簡明手冊》表 2.83 和鉆頭允許的進給量確定進給量 f=0.86mm/r。由《切削用量簡明手冊》表 2.9 機床進給機構(gòu)所允許的鉆削進給量查得 f=1.6mm/r。故由 Z525型立式鉆創(chuàng)說明書取 f=0.36mm/r。2、確定鉆頭磨鈍標準及壽命由《切削用量簡明手冊》表 2.12 查得磨鈍標準為 0.5~0.8 壽命為T=35min。3、確定切削速度由《切削用量簡明手冊》表 2.15 查得切削速度為 V=18m/min。則主軸轉(zhuǎn)速為 n= =818.9 r/min。Dv?10由 Z525 鉆床說明書由就近原則取 n=680 r/min。故實際切削速度為v=14.9 m/min4、校核機床扭矩及功率由《切削用量簡明手冊》表 2.20 查得FyZoFf kfdC?MKcdMcVP30?=420, =1 =0.8, =0.206, 2.0, =0.8FCFZFyCMZy=420×7 2×0.360.8×1f=1298.3 NMc=0.206×7 2×0.360.8×1=4.5 NmPc= =0.32 KW7*309.145根據(jù) Z525 機床說明書可知 Mm=42.2 Nm, Pe=2.8*0.81=2.26 KW, Fmax=8830 N 由于上面所算出的的數(shù)據(jù)都小于機床的各個相應的參數(shù),故機床符合要求。5、計算鉆削加工工時由《切削用量簡明手冊》表 2.29 查得入切量和超切量 y+ 的值為 6 mm。?故t= =nfyL??680*3.1=0.07 min因為表面存在倆加工孔故加工工時為 T=2t=0.14 min。二、攻 M8 螺紋由《機械加工工藝手冊》表 7.2-4 選用 M8 細柄機用絲錐,在普通鉆床上攻絲。由《機械加工工藝手冊》表 7.2-13 在普通鉆床上攻絲切削速度表查得Vc=11~12 m/min。故鉆床主軸的轉(zhuǎn)速為:我 n= =437.9 ~477.7 r/minDVc?10由 Z525 的說明書的參數(shù)可取 n=392 r/min。故實際切削速度為Vc=9.8 mm/min攻螺紋機動實際的計算我 tm= ????????11npl其中: :工件螺紋的長度 =10 mm。ll:絲錐切削長度 =22 mm。11:攻螺紋是的超切量 =(2~3)P 取 =3。???:攻螺紋是的轉(zhuǎn)速 =392 r/min。nn:絲錐退出時的轉(zhuǎn)速 =680 r/min。1 1P:螺距。工序七 銑 18H11 的槽一、粗銑 18H11 槽1、選擇與加工 80×30 平面同一規(guī)格的銑刀,同一銑床。因為槽深為 35 mm 故銑 18H11 槽時底邊留有 5 mm 的加工余量,精銑以達到圖紙所規(guī)定的表面粗糙度的要求故 ap=30 mm2、切削用量的確定由《機械加工工藝手冊》表 2.1-96 查得切削速度為V=18~29 m/min 每齒進給量為 fz=0.063~0.102 mm/z 取 fz=0.09 mm/z。則銑床主軸轉(zhuǎn)速為n= =358.3~577.2 r/minD?10根據(jù)機床說明書可取 n=460 r/min。則實際轉(zhuǎn)速為Vf=f znz=0.09×3×460=124.2 mm/min3、切削加工工時由《機械加工工藝手冊》表 2.1-99 查得iVlltfwm21??= .490=0.82 min二、半精銑 18H11 槽1、選取與粗銑 18H11 槽同一規(guī)格的銑刀,背吃刀量 ap=5 mm。2、確定進給量由《機械加工工藝手冊》表 2.1-72 查得每齒進給量為 fz=0.05~0.08 mm/z 取 fz=0.06 mm/z。由《機械加工工藝手冊》表 2.1-75 查得后刀面最大磨損限度為0.22~0.25 mm。由表 2.1-76 查得銑刀壽命為 T=60 min3、切削用量的確定由《機械加工工藝手冊》表 2.1-92 查得 V=22 m/min,則主軸轉(zhuǎn)速n= =437.9 r/minDV?10根據(jù)機床的說明書確定主軸轉(zhuǎn)速為 n=460 r/min。則 Vf=f znz=82.8 mm/min4、計算切削工時由《機械加工工藝手冊》表 2.1-99 查得iVlltfwm21??*8.940=1.2 min2.夾具結(jié)構(gòu)設(shè)計2.1 定位機構(gòu)圖 2-1-1 大平面、擋板和支承釘在夾具設(shè)計中,定位方案不合理,工件的加工精度就無法保證。工作定位方案的確定是夾具設(shè)計中首先要解決的問題。根據(jù)工序圖給出的定位元件方案,按有關(guān)標準正確選擇定位元件或定位的組合。在機床夾具的使用過程中,工件的批量越大,定位元件的磨損越快,選用標準定位元件增加了夾具零件的互換性,方便機床夾具的維修和維護。設(shè)計夾具是原則上應選該工藝基準為定位基準。無論是工藝基準還是定為基準,均應符合六點定位原理。由于該零件的加工是銑40X70的端面并以下底面作為定位面,屬面定位類型,因此本次設(shè)計采用的定位機構(gòu)為大平面與支承釘相結(jié)合。定位的形式很多,大平面限制X,Y方向的轉(zhuǎn)動及Z方向的移動;小平面限制Y方向的移動;在用另一個小平面限制X方向移動和Z軸轉(zhuǎn)動,來實現(xiàn)完全定位。裝夾工件時,通過夾緊機構(gòu)壓板將夾緊工件。本次設(shè)計的定位平面與平面相結(jié)合,分別限制工件的X、Y方向的移動及轉(zhuǎn)動自由度以及Z方向的旋轉(zhuǎn)自由度。心軸定位的特點為結(jié)構(gòu)簡單、制造容易、夾緊可靠,自鎖性好,夾緊動作慢、效率低。2.2夾緊機構(gòu)圖 2-2-1 工件放置方式1.夾緊的目的:使工件在加工過程中保持已獲得的定位不被破壞,同時保證加工精度。2 .夾緊力的方向的確定:1)夾緊力的方向應有利于工件的準確定位,而不能破壞定位,一般要求主夾緊力應垂直于第一定位基準面。2)夾緊力的方向應與工件剛度高的方向一致,以利于減少工件的變形。3)夾緊力的方向盡可能與切削力、重力方向一致,有利于減小夾緊力。3 .夾緊力的作用點的選擇:1)夾緊力的作用點應與支承點“點對點”對應,或在支承點確定的區(qū)域內(nèi),以避免破壞定位或造成較大的夾緊變形。2)夾緊力的作用點應選擇在工件剛度高的部位。3)夾緊力的作用點和支承點盡可能靠近切削部位,以提高工件切削部位的剛度和抗振性。4)夾緊力的反作用力不應使夾具產(chǎn)生影響加工精度的變形。4. 選擇夾緊機構(gòu):設(shè)計夾緊機構(gòu)一般應遵循以下主要原則:1)夾緊必須保證定位準確可靠,而不能破壞定位。2)工件和夾具的變形必須在允許的范圍內(nèi)。3)夾緊機構(gòu)必須可靠。夾緊機構(gòu)各元件要有足夠的強度和剛度,手動夾緊機構(gòu)4)必須保證自鎖,機動夾緊應有聯(lián)鎖保護裝置,夾緊行程必須足夠。5)夾緊機構(gòu)操作必須安全、省力、方便、迅速、符合工人操作習慣。6)夾緊機構(gòu)的復雜程度、自動化程度必須與生產(chǎn)綱領(lǐng)和工廠的條件相適應。圖 2-2-2 夾緊機構(gòu)選用壓板夾緊機構(gòu)來對被加工工件進行夾緊。壓板夾緊機構(gòu)的特點:①結(jié)構(gòu)簡單,制造方便加緊可靠施力范圍大;②自鎖性能好操;③擴力比 80 以上,行程 S 不受限制;④加緊工作慢,效力低。2.3 機床夾具的總體形式機床夾具的總體形式一般應根據(jù)工件的形狀、大小、加工內(nèi)容及選用機床等因素來確定。夾具的組成歸納為:1)定位元件及定位裝置 用于確定工件正確位置的元件或裝置。2)夾緊元件及夾緊裝置 用于固定元件已獲得的正確位置的元件或裝置。3)導向及對刀元件 用于確定工件與刀具相互位置的元件。4) 動力裝置在成批生產(chǎn)中,為了減輕工人勞動強度,提高生產(chǎn)率,常采用氣動、液動等動力裝置。5) 夾具體用于將各種元件裝置連接在一體,并通過它將整個夾具安裝在機床上。6)其他元件及裝置 根據(jù)加工需要來設(shè)置的元件或裝置。2.4.1 確定夾具體:夾具體上一般不設(shè)定位和定向裝置,特別是臺鉆、立鉆和搖臂鉆上使用時,但夾具體底板上一般都設(shè)有翻邊或留一些平臺面,以便夾具在機床工作臺上固定。夾具體一般是設(shè)計成平板式(有些夾具體鑄造成特殊形狀) ,保證具有足夠的剛性。它用來固定定位元件、加緊機構(gòu)和聯(lián)接體,并于機床可靠聯(lián)接。2.4.2 確定聯(lián)接體:聯(lián)接體是將導向裝置與夾具體聯(lián)接的工件,設(shè)計時主要考慮聯(lián)接體的剛性,合理布置聯(lián)接體的位置,給定位元件、夾緊機構(gòu)留出空間。此夾具體的聯(lián)接裝置通過內(nèi)六角螺栓和圓柱銷來定位,考慮到剛性問題,在相對應的位置上在用一個聯(lián)接體支承鉆套板,同樣用內(nèi)六角螺栓定位。2.4.3 夾具體的總體設(shè)計圖:2.5 繪制夾具零件圖對裝配圖中需加工的零件圖均應繪制零件圖,零件圖應按制圖標準繪制。視圖盡可能與裝配圖上的位置一致。1.零件圖盡可能按 1:1.5 繪制。2.零件圖上的尺寸公差、形位公差、技術(shù)要求應根據(jù)裝配圖上的配合種類、位置精度、技術(shù)要求而定。3.零件的其他尺寸,如尺寸、形狀、位置、表面粗糙度等應標注完整。4.零件圖名稱:零件圖 1 壓板零件圖 2 上蓋2.6 繪制夾具裝配圖1.裝配圖按 1:1.5 的比例繪制,用局部剖視圖完整清楚地表示出夾具的主要結(jié)構(gòu)及夾具的工作原理。2.視工件為透明體,用雙點劃線畫出主要部分(如輪廓、定位面、夾緊面和加工表面) 。畫出定位元件、夾緊機構(gòu)、導向裝置的位置。3.按夾緊狀態(tài)畫出夾緊元件和夾緊機構(gòu)。4.畫出夾具體及其它聯(lián)接用的元件(聯(lián)接體、螺釘?shù)龋?,將夾具各組成元件聯(lián)成一體。此機床夾具要用到的零件如下:(1)壓板(2)圓柱銷(3)內(nèi)六角圓柱頭螺釘(4)六角頭頭部帶槽螺栓 A 級(5)輕型彈簧墊圈(6)精密機械用緊固件十字槽螺釘 B 型(7)圓柱銷-淬硬鋼和馬氏體不銹鋼(8)帶孔球面圓柱頭螺釘 C 型(9)彈簧(10)內(nèi)六角圓柱頭螺釘(11)標準型彈簧墊圈(12)六角頭螺桿帶孔螺栓-A 和 B 級(13)軸用彈性擋圈 A 型(14)支承釘(15)夾具體(16)平墊圈5.標注必要的尺寸、配合、公差等(1)夾具的外形輪廓尺寸,所設(shè)計夾具的最大長、寬、高尺寸。(2)夾具與機床的聯(lián)系尺寸,即夾具在機床上的定位尺寸。如車床夾具的莫氏硬度、銑床夾具的對定裝置等。(3)夾具與刀具的聯(lián)系尺寸,如用對刀塊塞尺的尺寸、對刀塊表面到定位表面的尺寸及公差。(4)夾具中所有有配合關(guān)系的元件間應標注尺寸和配合種類。(5)各定位元件之間,定位元件與導向元件之間,各導向元件之間應標注裝配后的位置尺寸和形位公差。6.夾具裝備圖上應標注的技術(shù)要求(1)定位元件的定位面間相互位置精度。(2)定位元件的定位表面與夾具安裝基面、定向基面間的相互位置精度。(3)定位表面與導向元件工作面間的相互位置精度。(4)各導向元件的工作面間的相互位置精度。(5)夾具上有檢測基準面的話,還應標注定位表面,導向工作面與該基準面間的位置精度。對于不同的機床夾具,對于夾具的具體結(jié)構(gòu)和使用要求,應進行具體分析,訂出具體的技術(shù)要求。設(shè)計中可以參考機床夾具設(shè)計手冊以及同類的夾具圖樣資料。7.對零件編號,填寫標題欄和零件明細表:每一個零件都必須有自己的編號,此編號是唯一的。在工廠的生產(chǎn)活動中,生產(chǎn)部件按零件編號生產(chǎn)、查找工作。完整填寫標題欄,如裝配圖號、名稱、單位、設(shè)計者、比例等。完整填寫明細表,一般來說,加工工件填寫在明細表的下方,標準件、裝配件填寫在明細表的上方。注意,不能遺漏加工工件和標準件、配套件。8.機床夾具應滿足的基本要求包括下面幾方面:1)保證加工精度 這是必須做到的最基本要求。其關(guān)鍵是正確的定位、夾緊和導向方案,夾具制造的技術(shù)要求,定位誤差的分析和驗算。2)夾具的總體方案應與年生產(chǎn)綱領(lǐng)相適應 在大批量生產(chǎn)時,盡量采用快速、高效的定位、夾緊機構(gòu)和動力裝置,提高自動化程度,符合生產(chǎn)節(jié)拍要求。在中、小批量生產(chǎn)時,夾具應有一定的可調(diào)性,以適應多品種工件的加工。3)安全、方便、減輕勞動強度 機床夾具要有工作安全性考慮,必要時加保護裝置。要符合工人的操作位置和習慣,要有合適的工件裝卸位置和空間,使工人操作方便。大批量生產(chǎn)和工件笨重時,更需要減輕工人勞動強度。4)排屑順暢 機床夾具中積集切屑會影響到工件的定位精度,切屑的熱量使工件和夾具產(chǎn)生熱變形,影響加工精度。清理切屑將增加輔助時間,降低生產(chǎn)率。因此夾具設(shè)計中要給予排屑問題充分的重視。5)機床夾具應有良好的強度、剛度和結(jié)構(gòu)工藝性 機床夾具設(shè)計時,要方便制造、檢測、調(diào)整和裝配,有利于提高夾具的制造精度。3.定位誤差設(shè)計3.1 誤差分析3.1.1 定位誤差工件的加工誤差,是指工件加工后在尺寸,形狀和位置三個方面偏離理想工件的大小,它是由三部分因素產(chǎn)生的:1)工件在夾具中的定位、夾緊誤差。2)夾具帶著工件安裝在機床上,夾具相對機床主軸(或刀具)或運動導軌的位置誤差,也稱對定誤差。3)加工過程中誤差,如機床幾何精度,工藝系統(tǒng)的受力、受熱變形、切削振動等原因引起的誤差。其中定位誤差是指工序基準在加工方向上的最大位置變動量所引起愛的加工誤差。3.1.2 產(chǎn)生定位誤差的原因1.基準不重合來帶的定位誤差:夾具定位基準與工序基準不重合,兩基準之間的位置誤差會反映到被加工表面的位置上去,所產(chǎn)生定位誤差稱之為基準轉(zhuǎn)換誤差。2.間隙引起的定位誤差在使用心軸、銷、定位套定位時,定位面與定位元件間的間隙可使工件定心不準產(chǎn)生定位誤差。3.與夾具有關(guān)的因素產(chǎn)生的定位誤差1)定位基準面與定位元件表面的形狀誤差。2)導向元件、對刀元件與定位元件間的位置誤差,以及其形狀誤差導致產(chǎn)生的導向誤差和對刀誤差。3)夾具在機床上的安裝誤差,即對定誤差導致工件相對刀具主軸或運動方向產(chǎn)生的位置誤差。4)夾緊力使工件與定位元件間的位置誤差,以及定位元件、對刀元件、導向元件、定向元件等元件的磨損。 3.2 定位誤差的計算1.定位誤差,此項主要是定位孔∮8H6 與定位銷∮8f5 的間隙產(chǎn)生,最大間隙為-0.028mm。2.鉆模板襯套中心與定位銷中心距誤差,裝配圖標注尺寸為15.3±0.015mm,誤差為 0.03mm。3.鉆套與襯套的配合間隙,有∮18H7/h6 可知最大間隙為 0.024mm。4.鉆套內(nèi)孔與外圓得同軸度誤差,對于標準鉆套,精度較高,此項可以忽 略。5.鉆頭與鉆套間隙的間隙會引偏刀具,產(chǎn)生中心距誤差 e,由下式求出:e=( H/2 + h + b )△max/He----刀具引偏量 (mm)H----鉆套導向高度(mm)h----鉆套下斷面與工件間的空間高度(mm)△max----刀具與鉆套的最大間隙刀具與鉆套的配合為∮30H7/r6,可知△max=0.028mm;將 H=36mm, h=20, B=30mm 代入,可求得 e=0.05mm。由于上述各項都是按最大誤差計算,實際上各項也不可能同時出現(xiàn)最大值,各誤差方向也很可能不一致,因此,其最和誤差可按概率法求和:220.8.30.4.50.24m??????該項誤差大于中心距允差 0.1mm 的 2/3,可用。結(jié)論在這次歷時兩個禮拜的課程設(shè)計中,發(fā)現(xiàn)自己在理論與實踐中有很多的不足,自己知識中存在著很多漏洞,看到了自己的實踐經(jīng)驗還是比較缺乏,理論到實踐的能力還急需提高。讓我認識到了仔細認真的重要性。這次課程設(shè)計讓我們更能注意到細枝末節(jié)。這次課設(shè)使我對機床夾具設(shè)計有了更深刻的理解,特別使其中的技術(shù)要求。同時感覺到了細節(jié)的重要性。有時候我們我們錯的并不是理論,而是我們很容易忽略的線型和該刪掉的線我們沒有刪掉。作為一個設(shè)計者不僅應掌握良好的專業(yè)知識,有一個認真仔細的心態(tài),還有有一個冷靜的心態(tài),遇到問題不能慌亂,不知所措首先根據(jù)工件的加工要求,我選擇了銑床,因此加工方向式垂直與水平面的。然后工件主要定位部分底面和兩側(cè)端面,限制 6 個自由度。滿足六個自由度的要求,但是不影響機床夾具的工作。因為被加工件需要銑平面限制 6 個自由度會增進效率。最后是將定位銷和支承板固定在夾具體上,利用銷定位、螺柱、螺母和內(nèi)六角螺釘進行定位、夾緊。這樣將工件穩(wěn)固的夾緊在機床上,能更方便,準確的進行面加工。通過以上這些步驟,此機床夾具可以正常工作,此項設(shè)計方案可實施。通過精度驗算可知,此項機床夾具可施行。工件的定位、夾緊符合要求。在設(shè)計的過程中,雖然感覺到了我的不足之處,但是我也學到了不少東西。在一定程度上,使我對以前學習過的東西有了加深理解和熟練操作。課程設(shè)計是機械專業(yè)學習的一個重要的、總結(jié)性的理論和實踐相結(jié)合的教學環(huán)節(jié),是綜合運用所學知識和技能的具體實踐過程。通過本次夾具設(shè)計,我對所學的專業(yè)知識有了更深刻的理解和認識。課程設(shè)計內(nèi)容源于生產(chǎn)實踐,使得課程設(shè)計和實踐得到了充分的結(jié)合,有利于培養(yǎng)解決工程實際問題的能力。上學期在長春一汽進工廠實習或參觀的時候?qū)A具也有所了解,而這次課程設(shè)計的經(jīng)歷,使我對夾具有了更深刻的認識我們在這次的學習實踐中看到了自己的不足,同時發(fā)現(xiàn)到自己的一個不足,意味著我們成長了一點,如果我們每天成長一點點,那么我們會穩(wěn)扎穩(wěn)打的走向成功。致謝為期兩周的課程設(shè)計轉(zhuǎn)眼就過去了。通過這兩個星期的課程設(shè)計,使我綜合的運用了幾年所學的專業(yè)知識。在課程設(shè)計中,發(fā)現(xiàn)自己在理論與實踐中有很多的不足,自己知識中存在著很多漏洞,看到了自己的實踐經(jīng)驗還是比較缺乏,理論到實踐的能力還急需提高。首先,感謝學校給我們提供這次難得的實習機會,這讓我真切的體會到理論與實際相結(jié)合的意義,為我今后的機械制造技術(shù)設(shè)計思路奠定了基礎(chǔ)。從次課程設(shè)計中能讓我們學習到一些課本中不能引起我們注意的細節(jié)東西,感謝學校為我們提供的寶貴學習機會!我非常感謝我的指導教師張福老師和張海華老師。兩周來,我時刻體會著兩位老師嚴肅的科學態(tài)度,嚴謹?shù)闹螌W精神,精益求精的工作作風,不論天氣有多么的炎熱,都會在我們身邊細心指導。在課外時間,我們不明白一些設(shè)計的問題和有關(guān)畫圖方面的問題時,每次去老師那里,老師都會在百忙之中給我們足夠的時間去問問題,有時還會和我坐下來一起討論設(shè)計的方案。當我的提出的方案不是經(jīng)濟實用的時候老師會細心講解給予更好的意見。整個過程,兩位老師都傾注了大量的心血。正是在老師科學、嚴謹?shù)闹笇?,我的課程設(shè)計才能順利進行,這篇論文也才得以順利完成。兩位老師不僅在學習上對我嚴格要求,在我們的思想行為上都給予了教育與指導。這次課程設(shè)計雖然我完成的不是很成熟,但是通過老師的幫助和自己的努力完成課程設(shè)計還是讓我有一種自豪感,這是我自己真的去思考,設(shè)計,查詢資料得來的成果。在這次課程設(shè)計結(jié)束的時候,我感到有一種輕松感,不是因為課程設(shè)計不用再做了,而是因為我從這次課程設(shè)計中獲得了知識,有所學、有所用。更加知道我們將來能做什么,會做什么,該做什么。讓我們對行業(yè)有了了解,讓我們對自己的未來有了規(guī)劃。感謝兩位老師的細心指導!老師辛苦了!謝謝!參考文獻[1] 作者:吳宗澤,羅圣國,書名《機械設(shè)計課程設(shè)計手冊》 ,出版者:高等教育出版社,出版年:1999,引用部分起止頁:37~46。[2] 作者:李慶余,書名《機械制造裝備設(shè)計》 ,出版者:機械工業(yè)出版社,出版年:2008 年,版次:2 版 [3] 作者:張海華,書名《機械制造裝備設(shè)計指導書》 ,出版者:機械工程系,引用部分起止頁:44~46 頁。[4] 作者:薛源順,書名《機床夾具圖冊》 ,出版者:機械工業(yè)出版社, 出版年 2003 年,版次:1 版