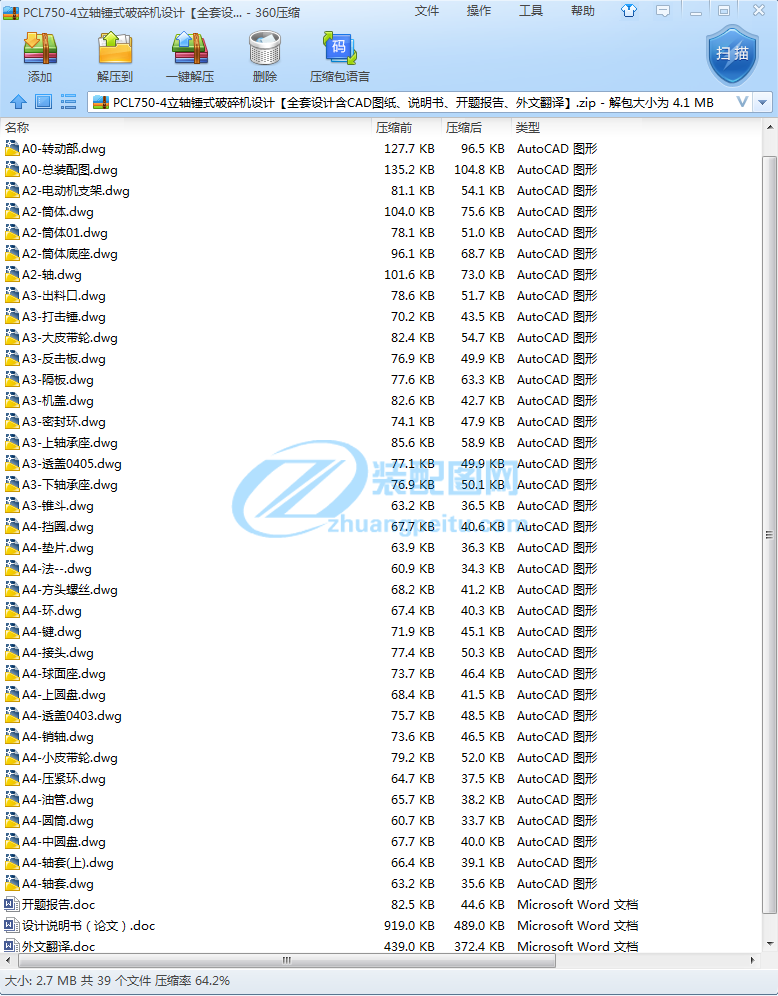
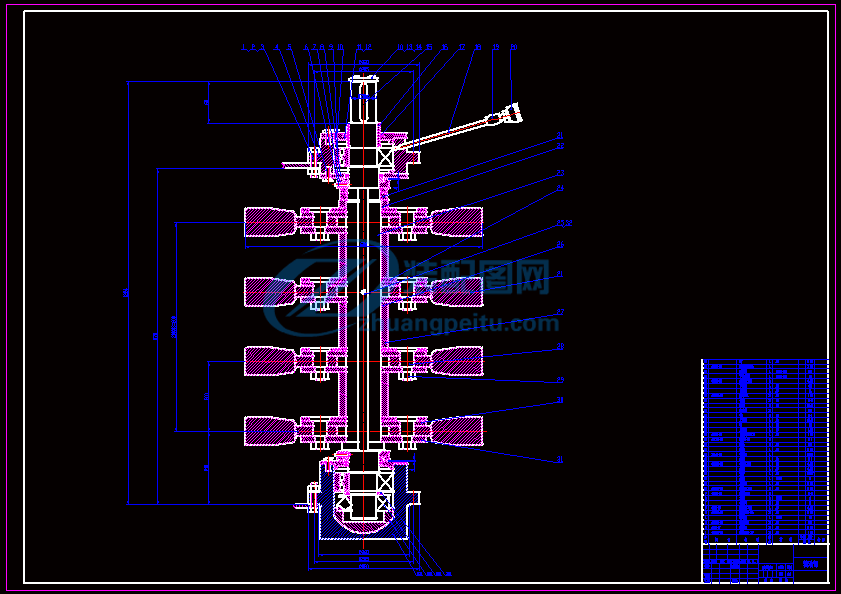
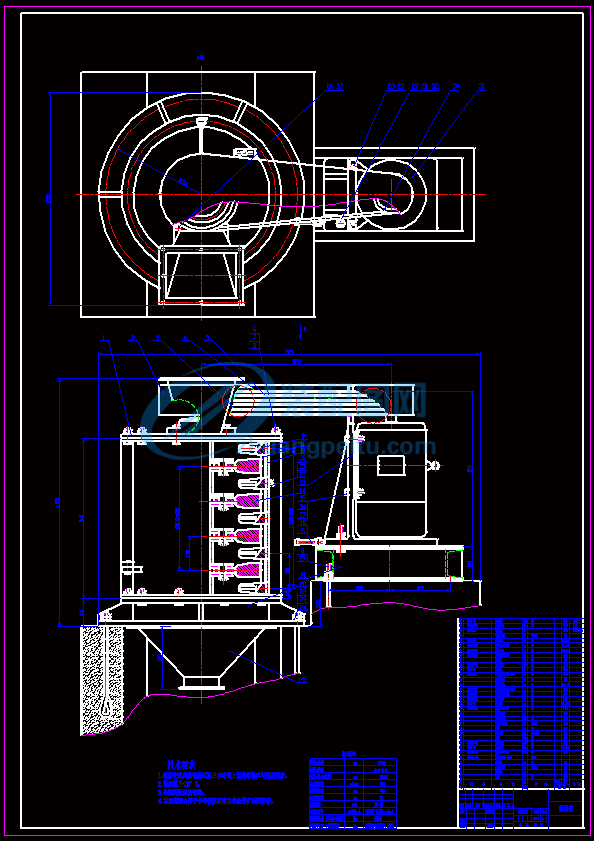
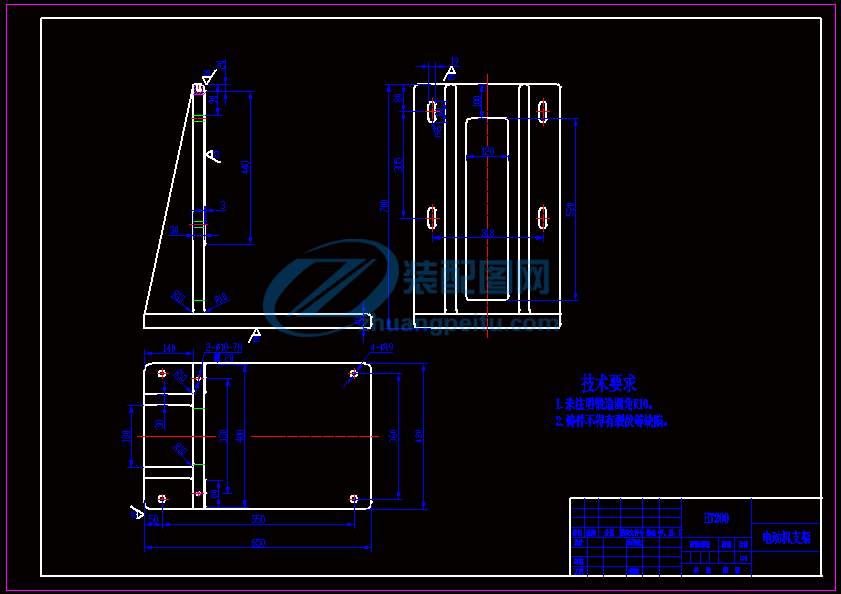
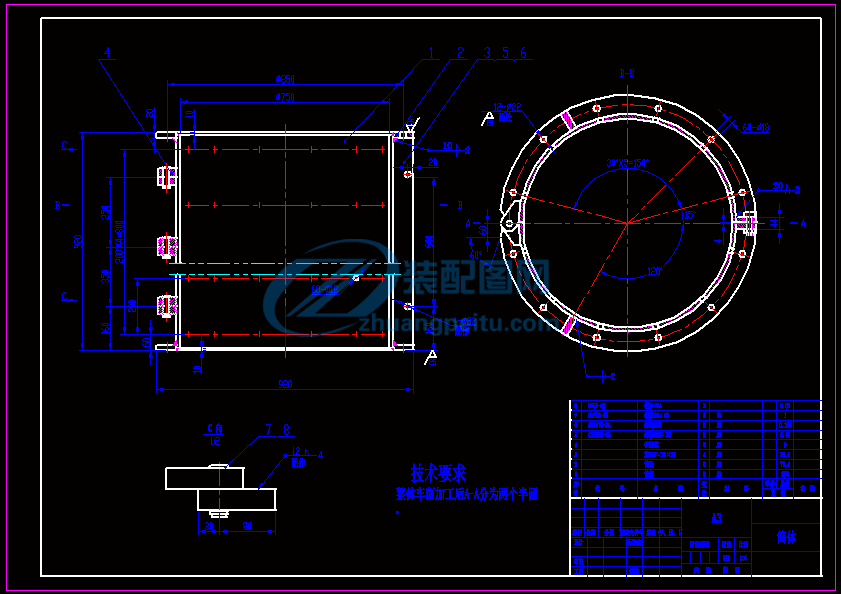
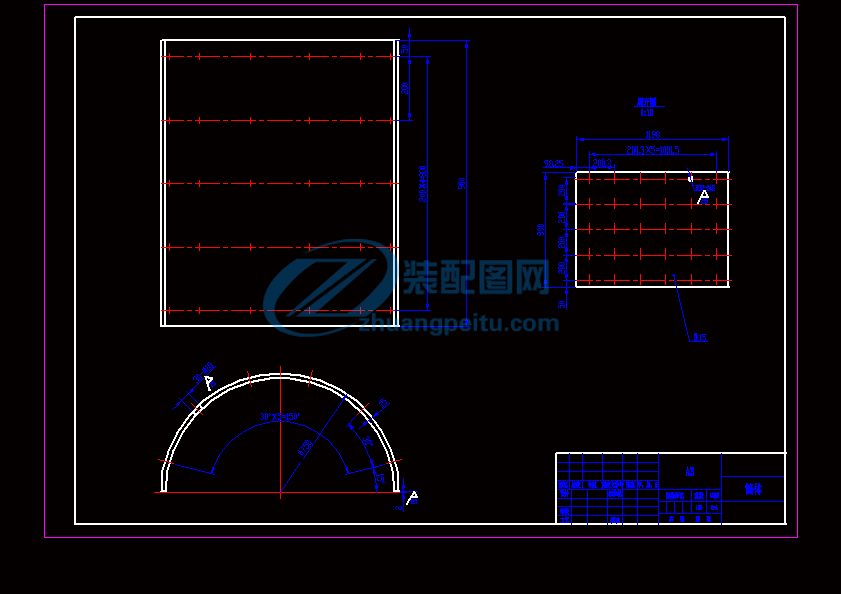
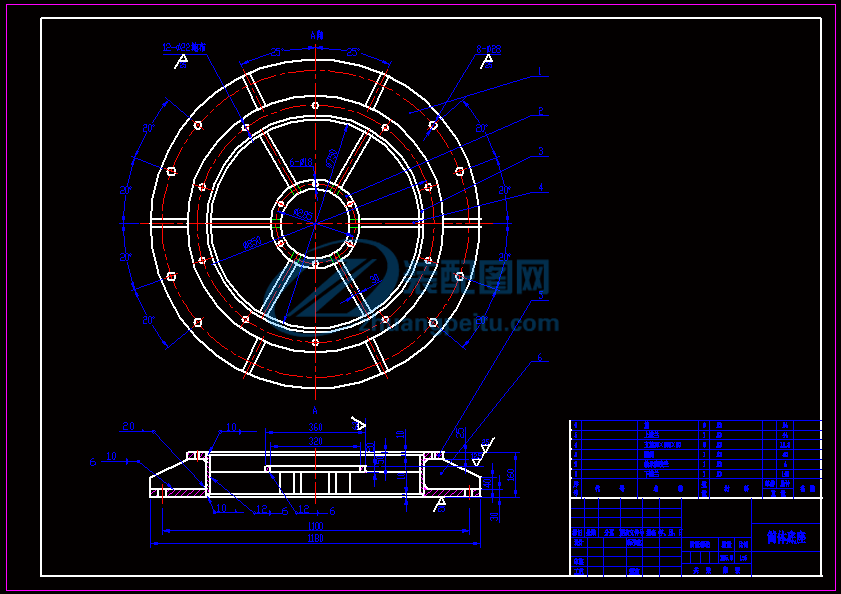
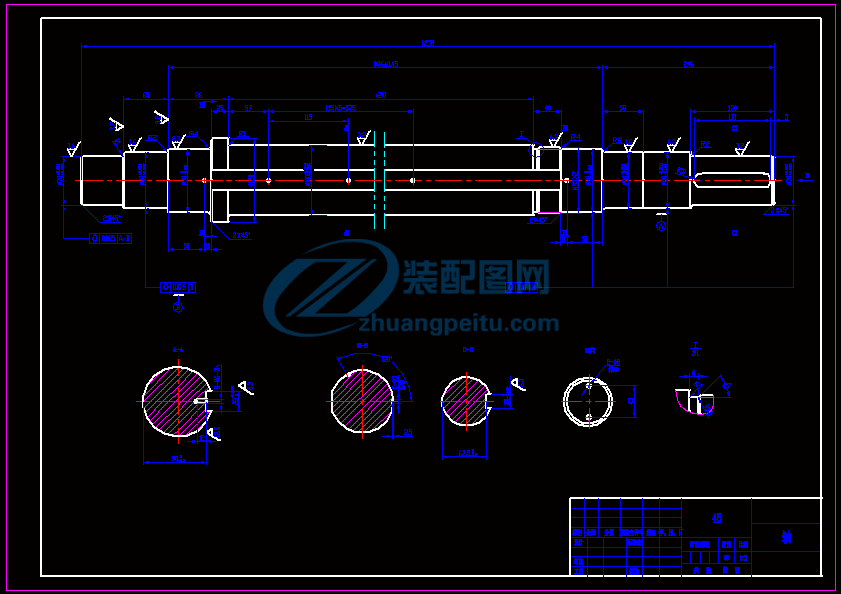
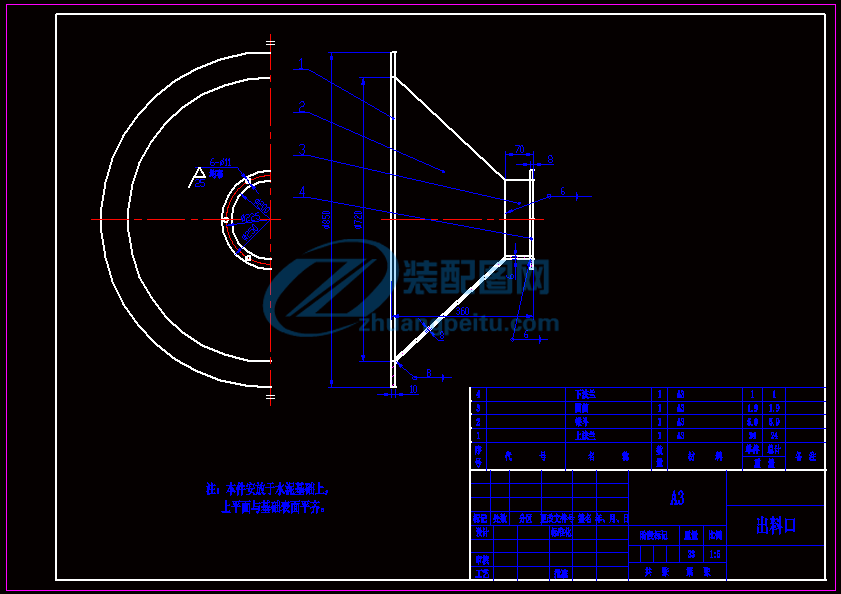

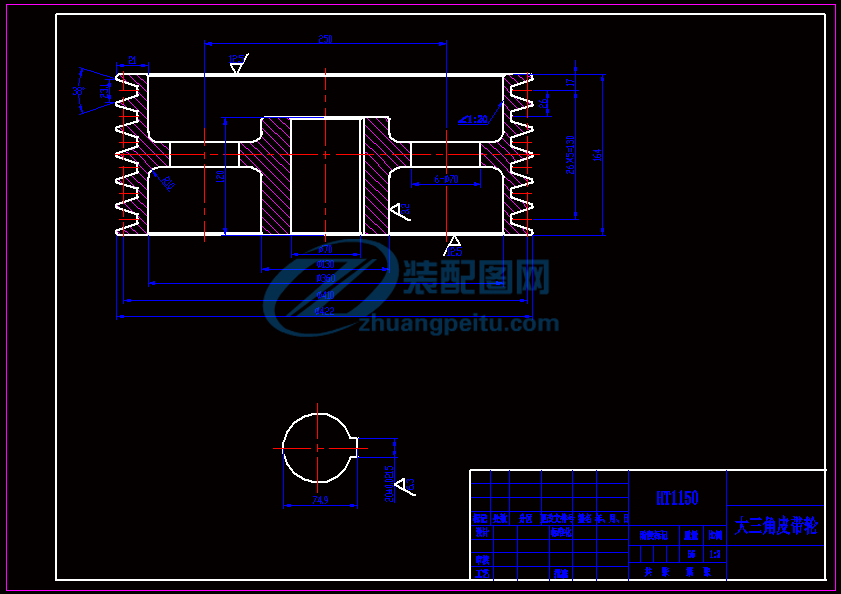
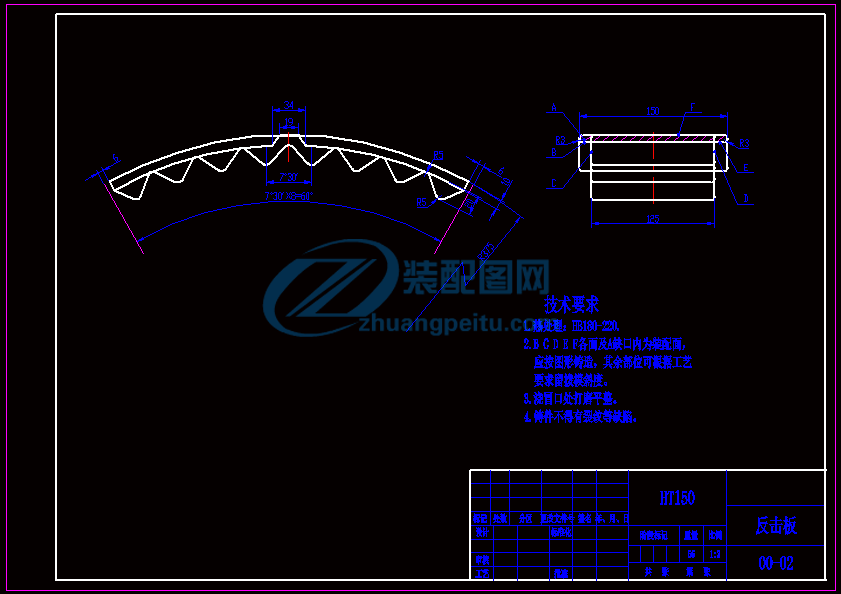
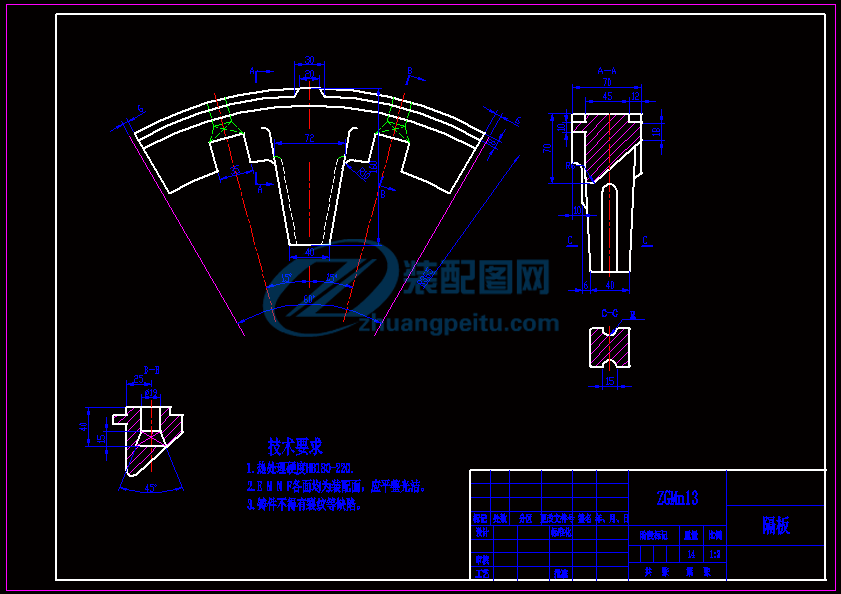
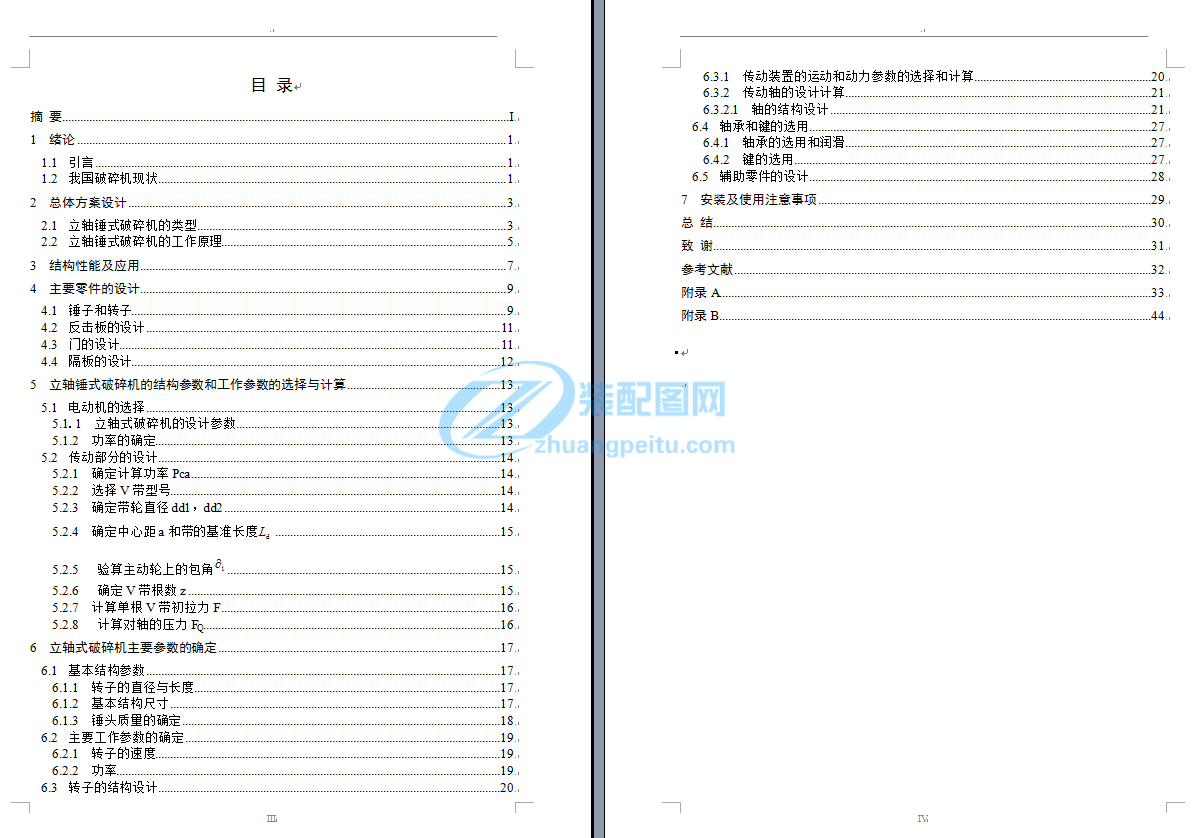
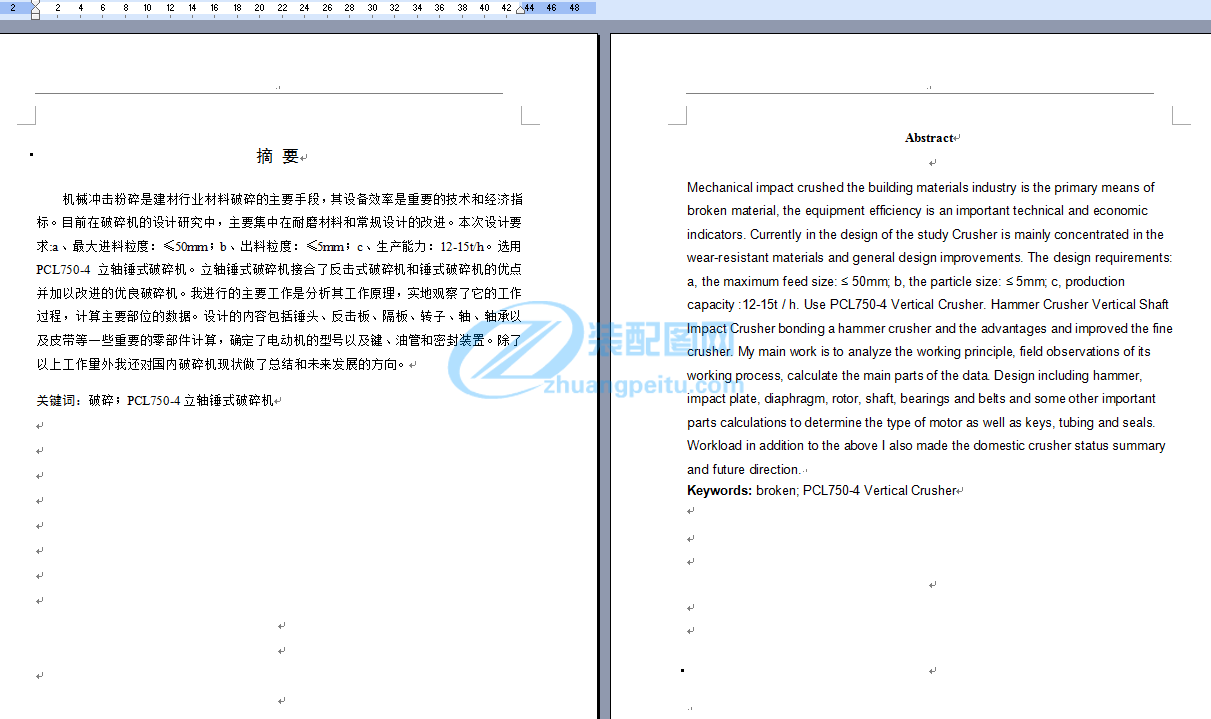
附錄 A6 PLANER6.1 DEFINITIONA planer is a machine tool which is used for machining flat metallic surfaces by means of single-point cutting tool. The job (fitted on its table) moves against a fixed cutting tool. This process of machining is called planning. The table travels slower during the cutting stroke and faster during the reverse stroke.6.2 DIFFERENCE BETWEEN SHAPER, SLOTTER AND PLANERAll the three machine tools generally machine flat metallic surfaces by means of single-point cutting tools. The main difference between a shaper, a slotter and a planer are given in Table 6.1.6.3 TYPES OF PLANING MACHINESThere are two types of planers in general use, namely, the double-column planer and the openside planer.6.3.1 Double-Column PlanerThe double-column planer has two columns which support the crossrail and house the elevating screw and controls for the machine (Fig. 6.1).圖 6.16.3.2 Openside PlanerAn openside planer has only one column or housing to support the crossrail and toolheads. This change in design makes this planer suitable to handle irregular shaped workpieces, which could extend outwards over the other side of the table. The rest of the parts of an openside planer are the same as those of a double-column planer.此處有表格 6.16.4 PLANER SIZEThe size of the planer is determined by the maximum length of the table stroke, width of the table, and the maximum gap between the table and the housing or the crossrail or the height of the work which can pass through the housing and underneath the crossrail. An openside planer can generally handle a job of a large size than its height. Its size is given in terms of its crossrail height and length of table stroke.6.5 BASIC PARTS OF A PLANERThe basic parts of a planer are bed, column, crossrail, table, tool head and table drive mechanism (Figs. 6.1 and 6.2).The basic parts of a double-column planer are the same as those of an openside planer.6.5.1 BedThe bed of a planer (Figs.6.1 and 6.2) is extremely heavy and made by a rigid casting. The bed supports the column/columns and all moving parts of the machine. It has accurately finished bed-ways on which the table slides.6.5.2 ColumnA double-column planer has two vertical columns, one on each side of the bed (Fig.6.1). They support the crossrail and also house the elevating screws and controls for the machine. An openside planer has only one column.6.5.3 CrossrailThe crossrail is supported on the columns (Fig.6.1) and it carries the saddle and the tool head. It is a rigid casting and provides guides for transverse travel of the saddle. The feed rod screw for controlling the movement of the cutting tool is also located in the crossrail.The crossrail can be adjusted vertically by means of vertical screws (Fig.6.1) housed in each of the column. The crossrail when clamped should be parallel to the table, because the accuracy of the surface depends upon the accuracy of the movement of the cutting tool. Figure 6.3 shows the position of the crossrail and the table when they are parallel (in full lines, position 1) and also when they are not parallel(in dotted lines, position 2).To check parallelism, hold a dial indicator in the tool post with its point touching the table. Now move the tool head crosswise. No change in the reading of the dialindicator means that the crossrail and the table are parallel. A change in reading means that the crossrail and the table are not parallel to each other.6.5.4 TableThe planer table is in the form of a thick plate (Figs.6.1and 6.2).It is machined with precision. The table travels on bed-ways which are also machined with precision. The table has T-slots for fixing the workpieces on it with the help of T-bolts. It also has accurately reamed noles for locating stops. These stops actuate the reverse lever and hence reverse the motion of the table.T-slots as well as holes should be kept free from nicks and burrs. he shanks of the stops should never be forced into the holes with a hammer as this will result in the surface of the table getting upset and table accuracy destroyed.6.5.5 Tool HeadThe tool head or head of a planer is similar to that of a shaper, both in construction and in operation (Fig.6.1and6.2).The tool is first inserted in the slot with packings and then tightened. The tool head is moved by means of a feed screw. It can also be swiveled for making angular cuts. It can be set over in either direction to provide tool clearance, while making vertical or angular cuts.6.6 TABLE DRIVE MECHANISMSThe table drive of a planer can be obtained by rack and spur gears, spiral rack and worm wheel, crank arrangements and hydraulic transmission.6.6.1 Rack and Spur Gear Table DriveThe basic diagram of a rack and spur gear table drive is given in Fig.6.4.This table consists of a compound gear train with two intermediate compound gears(1st intermediate gear and 2nd intermediate gear).The driving pinion is situated on one end of the gear train while the driven bull gear is situated at the other end. This bull gear drives the rack which is fitted at the bottom of the table. Hence the table moves. The pinion gets its drive from the electric motor through a belt drive. The cutting stroke is at a slower speed than the return stroke. The quick return of the table is achieved by means of adjustable stops on the sides of the table. These stops come in contact with a level at the end of each cutting stroke and engage high speed gears in the driving train of gears.此處圖 6.46.6.2 Rack and Worm Gear DriveIn this method the rack on the underside of the planer table is driven by a worm gear. The axis of the shaft of the worm gear is at an angle to the centerline of the table. The rest of the drive is similar to that already explained in Section 6.6.1.6.6.3 Hydraulic DriveIn this system the table of a planer gets its reciprocating motion from a piston which moves to and fro with hydraulic power. Oil is used as a working fluid and the hydraulic pressure is generated by a variable-delivery electric pump. The speed of the piston is changed by adjusting the amount of oil delivered by the pump.A schematic diagram of a hydraulic drive is given in Fig.6.5.Oil from the pump flows through port B in the valve through discharge line E to the cylinder. Hence the piston is moved to the left. When the table reaches the end of its stroke, a dog or trip moves the valve to the right so that valve ports A and B come in alignment with the lines D and S. In this position the piston moves to the right. The oil in the head end of the cylinder returns through lines S and valve port B to the oil reservoir.6.7 SPEEDS AND FEEDS IN PLANINGSpeeds of cutting metals on a planning machine and feeds of the tool or the depths of cut, are very important for all operation. The conditions vary from shop to shop, and therefore, the values of speeds and feeds cannot be exact. Table 6.2 gives the values of planning speeds and feeds for high-speed steel tools. These values can act as a guide for the selection of speeds and feeds for planning different metals.此處表 6.2 表 6.3Higher speeds with finer feeds are possible on a planer for tungsten-carbide-tipped tools. The speeds can increase say up to 50-70 m/min. Table 6.3 gives the speeds and feeds for planning with tungsten-carbide-tipped tools.6.8 PLANER TOOLSCutting tools used on a planer (Fig.6.6) are similar in shape to those used on a lathe machine (Figs.8.1to 8.4), but are somewhat larger in size (see also Chapter 8).A planer machines flat surfaces while a lathe turns circular jobs. During the cutting operation, a lathe tool springs away from the work when it is set at exact centre height, but in the case of a planer the tool digs into the work if its cutting edge is set in advance of the plane of support (Fig.6.7). This digging in of the tool is avoided by forging the cutting tool in such a way that its cutting edge is located behind the plane of support (Fig.6.7). The choice of tool depends upon the type of operation to be performed.此處圖 6.7Figure 6.8 shows a gang planer tool which is especially adapted for surfacing large castings. The tool holder holds a number of cutting tools set in such a way that each tool makes a light cut. Hence, a gang planer tool carries a feed and depth of cut much greater than that is possible with a single tool point. In this case there is a lesser tendency to break out at the end of the cut.此處圖 6.86.9 PLANER OPERATIONSThe workpice is clamped on to the planer table, before any planning operation starts. Clamping involves the use of such item as nuts, bolts, T-bolts, studs, washers, shims, step blocks, toe dogs, stops, strap clamps, C-clamps, etc.Any type of planer operation can be split in a suitable combination of the operations such as horizontal surfacing, planning at an angle and making a groove. These operations will be discussed in detail here.6.9.1 Planing Horizontal SurfacesTake, for example, a flanged cast-iron cover for horizontal planing (Fig.6.9). It is easy to clamp it on a planer table with the flanged side resting on the table. Now adjust the crossrail ti the correct height and set up the clamp screws.此處圖 6.9Place the roughing tool in the tool holder so that it is perpendicular to the work. The tool should be placed against two clamping bolts on the side to avoid the shifting of the tool due to lateral thrust. Tighten the cutting tool bolts so that the clamps are parallel with the clapper. (It should be kept in mind that clamps must not be tilted with reference to the clapper.)Position and set the stroke for machining surface A (Fig.6.9). Adjust the depth of cut so that the metal dose not break and leave a ragged edge at the end of the stroke .This condition is checked at the end of the first stroke. If the metal is teared off, reduce the depth of cut. The machining is completed in a number of cuts until about 0.5 mm metal is left for finishing. Prepare the work for finishing by breaking the front edge of the surface (the edge at which the finishing tool begins to cut) with a coarse double-cut file. This is done to remove the scale on the outer surface of the casting as the scale spoils the cutting edge of the finishing tool.The job should be finishing in more than one cut and also to the required size. It is better to use smaller cuts than one larger cut, as a larger cut may lead to an undersized job in case the cut is set deeper than required.Now turn the job so that the machined surface touches the table. No leveling of the job is required in this case. After clamping, machine this side. The surface will automatically come parallel to the first machined surface. The other surfaces are also planed in the same manner, after properly clamping the job in position.Care has to be taken while finishing thin castings. They are planed rough on all sides to remove the scale, which in turn also reduces the internal stresses developed during the cooling process of the casting. Thereafter, the casting is machined to the required dimensions. The vertical sides, or the sides at 90°,are planed by using the tool feed.Planing at an Angle and Grooving Workpieces can be planed at an angle for inclined surfaces or dovetails or for V-shaped grooves, etc. The tool head assembly is swung around the centre axis, with respect to the saddle, to the required inclination or angle. The angle could be set with the help of the graduations on the circular part. It is recommended that the set inclination should be checked with the help of a dial-gauge as shown in Fig.6.10. This is done to take care of the error induced due to wear and tear of the graduated parts.To check the angle setting, mount the dial-indicator in the tool holder (Fig.6.10). Set the protractor at the desired angle and clamp it to the table of the planer. Take the reading when the dial is in contact with the protractor in position A. Now bring the tool holder down to position B and note the reading. If both the reading, (i.e. at A and B) are the same, then the setting is correct.Now clamp the job on the table and plane it. The surface will be planed at the desired angle by feeding the tool. A V-block job has been taken to explain the process of planing at an angle or groove planing on a planer (Fig.6.11). The horizontal and vertical sides of the V-block are planed as explained earlier in Section 6.9.1.此處圖 6.10The V-groove of the V-block is symmetrical about its axis and is at 45°to it (Fig.6.11). Set the tool head at 45°,according to the procedure explained earlier, clamp it in position by tightening the bolt A. Set the tool block at an angle less than 45°and clamp it in position by tightening bolt B. The tool block is set at less than 45°to prevent the cutting tool dragging over the planed surface on the return stroke.Clamp the V-block on the table so that the V-groove is on the top (Fig 6.11). The saddle should be moved into position for the first roughing cut on the V-block. Start the cut with the hand feed, moving downward. While doing this the saddle should remain in the same position on the crossrail .Complete the rough cutting and the finishing cut on one side of V.Now, without disturbing the tool setting, reverse the V-block (turn it by 180°) and clamp it again. The projection of the V-block in the table slot aligns the job lengthwise. Now repeat the roughing cuts and the finishing cuts. The reversing of the job ensures machining at the same angle and alignment of the V with the centre axis of the tongue.此處圖 6.11Use of Jigs and Fixtures on a PlanerPlaning Curved Surfaces A concave surface could be planed on a planer with the help of a fixture. The fixture in this case consists of a radial arm pivoted on a bracket (Fig.6.12). The bracket is fixed on the cross member on the housing of the planer. The feed screw of the slide is removed and the slide is fastened to the radial arm.The cross feed causes the saddle to traverse the crossrail during the planing operation. At the same time the tool, which is being guided by the radial arm, planes a curved concave surface. The height of the cutting edge of the tool is determined by the angular position of the cross arm (Fig.6.12 position A and B). The locus of the different positions of the cutting edge of the tool is indicated by the arc AB. Hence, a similar surface is planed.此處圖 6.12Planing a Helix A helix with a long pitch may be difficult to plane on some milling machines but it can be easily cut on a planer with the help of a fixture (Fig.6.13). During this operation the work is mounted between the planer centres. The fixture consists of a clamp with a weight and inclined bar. Its upper end A is attached to the planer housing and the lower end B is fixed to the planer bed. The pitch of the helix depends upon the inclination of the inclined bar.The table with the clamp bar moves near the lower end of the inclined bar. As the clamp bar is being guided in the angular position, it gradually rises as the work turns clockwise through a small arc. Thus the cutting tool cuts a helix as shown in Figure 6.13.此處圖 6.13 附錄 B電刨6.1 定義刨床是一種用于金屬表面加工使其平坦所采用的單刃刀具的機(jī)床。在其表上安裝一個(gè)固定的切割工具進(jìn)行往復(fù)運(yùn)動(dòng)。這一加工過程稱為刨。該表面在切割過程中運(yùn)行較慢在反向進(jìn)程中運(yùn)行較快。6.2 成型機(jī)、開槽和刨床的區(qū)別三個(gè)機(jī)床一般都是通過單點(diǎn)切削工具作用于金屬表面使其平整。成型機(jī)、開槽和刨床的區(qū)別參見表 6.16.3 刨床的類型在一般使用當(dāng)中,刨床通常分為兩種類型即雙柱刨床和部分開放刨床6.3.1 雙柱刨床雙柱刨床是指有兩列立柱,用以支撐橫梁和穩(wěn)定上升螺絲,控制機(jī)器的刨床(圖 6.1)6.3.2 Openside 刨床一個(gè) openside 刨床只有一列立柱支撐橫木和工具頭的穩(wěn)定。這種設(shè)計(jì)上的變化適合于處理不規(guī)則形狀的工件,可擴(kuò)展到工作臺(tái)外部的另一端。它其余的部分與雙柱刨床相同。此處有表格 6.16.4 刨床尺寸該刨床的尺寸取決于行程表的最大長(zhǎng)度,工作臺(tái)的寬度,以及工作臺(tái)和箱體、橫梁之間的最大差距,或者是可以通過箱體和橫梁下方產(chǎn)品的高度。一個(gè) openside 刨床一般可以處理比它的高度高的零件。它的大小取決于橫梁高度和工作臺(tái)沖程的長(zhǎng)度。6.5 一個(gè)電刨基礎(chǔ)件一個(gè)刨床的基本部分是床身、立柱、橫梁、工作臺(tái)、工具頭和工作臺(tái)驅(qū)動(dòng)機(jī)制(圖 6.1和 6.2) 。雙柱刨床的基本部分與 openside 刨床相同。6.5.1 床身一個(gè)刨床(表 6.1 和 6.2)的床身非常沉,用剛性鑄件制成。該床身支撐單個(gè)或多個(gè)立柱和機(jī)器的所有運(yùn)動(dòng)部件。它按照床身軌道通過床身滑動(dòng)準(zhǔn)確地完成。6.5.2 立柱一個(gè)雙柱刨床有兩個(gè)垂直立柱,床身沒變各一個(gè)(圖 6.1) 。他們支持的橫梁,穩(wěn)定上升螺絲,控制機(jī)器。一個(gè) openside 刨床只有一個(gè)立柱。6.5.3 橫梁橫梁由多個(gè)立柱支撐(圖 6.1) ,它承載著座板和工具頭。這是一個(gè)鋼性鑄件,并為座板的橫向移動(dòng)提供指導(dǎo)??刂频毒咭苿?dòng)的供料桿螺絲也被安裝在橫梁上。該橫梁可以利用垂直螺絲(圖 6.1)在每個(gè)立柱上進(jìn)行垂直方向的調(diào)整。當(dāng)橫梁鉗緊時(shí),應(yīng)平行于工作臺(tái),因?yàn)楸砻娴臏?zhǔn)確性取決于刀具運(yùn)動(dòng)時(shí)的準(zhǔn)確性。圖 6.3 顯示了橫梁的位置,它們平行時(shí)(全行,位置 1)和不平行時(shí)(在虛線,位置 2)工作臺(tái)的情況。為了檢查平行性,把握工具架上針盤指示表隨著觸碰工作臺(tái)產(chǎn)生的點(diǎn)數(shù)。現(xiàn)在橫向移動(dòng)工具頭。當(dāng)針盤指示表讀數(shù)沒有變化時(shí),意味著橫梁和工作臺(tái)是平行的。當(dāng)讀數(shù)變化時(shí)則意味著橫梁和表是不平行于對(duì)方。6.5.4 工作臺(tái)刨床工作臺(tái)是以板(表.6.1 和 6.2)的形式存在。它屬于精密加工。工作臺(tái)沿著車床軌道運(yùn)行,這也是精密加工方法。工作臺(tái)有用于幫助固定 T 型螺栓工件的 T 型槽。它也有準(zhǔn)確用于定點(diǎn)的鉸大孔。這些點(diǎn)啟動(dòng)換向手柄,因此改變了工作臺(tái)的運(yùn)轉(zhuǎn)。T 型槽以及孔應(yīng)保持無缺口和毛刺。他不能強(qiáng)制與鐵錘一起進(jìn)入孔中,因?yàn)檫@將導(dǎo)致工作臺(tái)表面混亂甚至直接被毀壞。6.5.5 工具頭在建造和運(yùn)行中,工具頭或刨床頭類似于一個(gè)成型機(jī)(表 6.1 和 6.2) 。首先用工具把填料填入槽中,然后擰緊。工具頭依靠給料螺旋運(yùn)輸機(jī)運(yùn)行,也可以轉(zhuǎn)進(jìn)行角度切割。在進(jìn)行垂直或角度切割時(shí),為了提供工具的徑向間隙,工具頭可以在任意方向調(diào)整轉(zhuǎn)換。6.6 工作臺(tái)驅(qū)動(dòng)機(jī)制一個(gè)刨床的工作臺(tái)靠齒條和直尺圓柱齒輪,螺旋齒條和蝸輪,曲柄軸布置和液體傳動(dòng)裝置組成6.6.1 齒條和齒輪工作臺(tái)驅(qū)動(dòng)齒條和蝸輪工作臺(tái)驅(qū)動(dòng)的基礎(chǔ)線圖見表 6.4。該工作臺(tái)由帶有兩個(gè)中型混合齒輪(第一和第二中型齒輪)的混合齒輪系列組成。驅(qū)動(dòng)軸齒輪位于齒輪系列的一端,而驅(qū)動(dòng)大驅(qū)動(dòng)齒輪位于另一端。大齒輪驅(qū)動(dòng)安裝在工作臺(tái)底部的齒條,從而使工作臺(tái)移動(dòng)。通過傳送帶的傳送,電動(dòng)機(jī)驅(qū)動(dòng)軸齒輪。與返回行程相比,切閑程速度較慢。工作臺(tái)的快速返回是依靠工作臺(tái)另一端的調(diào)整點(diǎn)來實(shí)現(xiàn)的。這些點(diǎn)與同一水平的每個(gè)切閑程相聯(lián)系并且使高速齒輪在齒輪驅(qū)動(dòng)過程中能夠咬合。此處圖 6.46.6.2 齒條和渦輪驅(qū)動(dòng)在這種方法中,刨床工作臺(tái)底部上的齒條靠渦輪驅(qū)動(dòng)。渦輪軸的軸線是相對(duì)于工作臺(tái)中心線的角度。該驅(qū)動(dòng)器的其余部分與 6.6.1 節(jié)已經(jīng)出現(xiàn)的解釋相似。6.6.3 液壓傳動(dòng)在這個(gè)系統(tǒng)中刨床的工作臺(tái)會(huì)利用活塞的來回移動(dòng)與液壓動(dòng)力做往復(fù)運(yùn)動(dòng)。石油被當(dāng)作工綴體來使用,液壓則是靠變量傳遞電動(dòng)泵產(chǎn)生。活塞的速度靠泵運(yùn)送石油的調(diào)整量改變。液壓傳動(dòng)原理圖見表 6.5。石油從泵流出通過端口 B,在活口處通過排出線 E 到達(dá)氣缸。因此,活塞移動(dòng)到左邊。當(dāng)工作臺(tái)到行程另一端時(shí),a dog 或流程移動(dòng)活門到右側(cè),以便使閥口 A 和 B 與線 D 和 S 校直。在這個(gè)位置上活塞移動(dòng)到右側(cè)。石油在汽缸的頂部停止通過線 S 和閥門 B 返回到達(dá)油壺。6.7 速度和進(jìn)料器計(jì)劃編制 在刨床上切割材料的速度和工具的供給或者切割的厚度對(duì)于整個(gè)造作至關(guān)重要。由于車間與車間的情況不同,因此速度和進(jìn)料的數(shù)值不能精確。表 6.2 指出刨削加工速度的數(shù)值和高速鋼化工具的供給。這些數(shù)值能夠作為一個(gè)速度的選擇性的指導(dǎo)和加工不同材料的供給。此處表 6.2 表 6.3用鎢硬質(zhì)合金工具的刨床可能會(huì)產(chǎn)生更高的速率和更精細(xì)的供給。速度可以提高到 50-70m/min。表 6.3 給出了鎢硬質(zhì)合金工具的速度和加工的供給。6.8 電刨工具刨床用的切割工具(表 6.6)與用于車床機(jī)器的工具(表 8.1 到 8.4)在形狀上是相似的,但是尺寸稍大(也見于第 8 章) 。車床輪流循環(huán)工作時(shí)刨床使表面變平。在切割操作運(yùn)行過程中,當(dāng)它設(shè)置中央精確高度時(shí)車床工具遠(yuǎn)離機(jī)件。至于刨床,如果它的切割邊緣設(shè)置在支撐的刨子前面,則工具用于機(jī)件。該挖掘在工具上被位于支撐刨床后方的鍛造型切割工具避免(表 6.7).關(guān)于工具的選擇取決于要執(zhí)行的操作類型。此處圖 6.7圖 6.8 顯示了全套刨床工具特別適用于大型鑄件表面。該工具持有人持有一定數(shù)量的刀具,并且對(duì)每個(gè)工具的輕型切割方式進(jìn)行設(shè)置。因此,全套刨床工具帶動(dòng)的進(jìn)料器和切割的厚度可能比單點(diǎn)工具完成的更好。在這種情況下,在切割的末尾被破壞的傾向會(huì)更少。此處圖 6.86.9 刨床操作在任何規(guī)劃操作開始前,工件要鉗緊在刨床工作臺(tái)上。夾緊涉及這些項(xiàng)目使用的螺母,螺栓,T 型螺栓,螺柱,墊圈,墊片,刻度器,坡腳,活塞,帶狀卡和 C -夾等任何刨床的操作類型都可分成適當(dāng)?shù)牟僮鹘M合,如堆焊,規(guī)劃角度并且制作凹槽。這些操作將在此詳細(xì)討論。6.9.1 刨水平表面舉個(gè)例子,凸緣生鐵覆蓋的水平刨(表.6.9)。凸緣邊依靠于工作臺(tái)和鉗緊在刨床工作臺(tái)上很容易?,F(xiàn)在調(diào)整橫木鈦的準(zhǔn)確高度,并安裝夾緊螺釘。此處圖 6.9將未加工的工具放置在刀柄,以便垂直加工。該工具應(yīng)該放在一邊對(duì)著兩個(gè)夾緊螺栓,以避免由于該工具的側(cè)向推力使工具轉(zhuǎn)向。擰緊切割工具螺栓,使螺絲鉗與鈴錘平行。(應(yīng)該牢記,螺絲鉗不能參照鈴錘傾斜。)設(shè)置位置并為機(jī)器表面 A 設(shè)置行程(表.6.9)。調(diào)整切割深度,使金屬劑量不破壞,留下毛邊在沖程的邊緣。這種情況是在第一次沖程結(jié)束后被檢查。如果金屬被去掉,則減少切削深度。加工完成大量的切割工作直到留下大約 0.5mm 的金屬材料。機(jī)器準(zhǔn)備通過破壞粗質(zhì)雙切割銼刀表面的正面邊緣(在完成工具開始切割的邊緣)來完成。這樣做是為了消除對(duì)鑄件外表面的規(guī)模作為規(guī)模廢品的精加工刀具的切削刃。這項(xiàng)工作應(yīng)有多個(gè)加工并且削減到所需的大小。與使用大一號(hào)的切刀相比,使用較小的切割工具更好,因?yàn)檩^大的切割工具可能導(dǎo)致工作中小尺寸工件的切割深度大于所需的要求。轉(zhuǎn)動(dòng)工件,使機(jī)器表面觸碰到工作臺(tái)。在這種情況下沒有作業(yè)需要的水準(zhǔn)。夾緊后,用機(jī)器做本側(cè)。表面會(huì)自動(dòng)進(jìn)入到與之平行的第一個(gè)加工表面。作業(yè)在正確的位置夾緊后,另外表面也以相同的方式進(jìn)行加工。加工薄鑄件時(shí)要注意。他們?cè)诟髅娑技庸とコ植诘某叽?,這反過來使鑄件在冷卻過程中也降低了內(nèi)部壓力。此后,鑄造加工成所需的尺寸。垂直的兩側(cè),或在 90 °的兩側(cè),是通過使用工具供給進(jìn)行加工。6.9.2 刨削的角度和切槽對(duì)于傾斜的表面或楔形榫頭或者 V 形溝槽等工件可以進(jìn)行角度刨削。該工具頭組件是圍繞中心軸擺動(dòng),關(guān)于刀座鞍,調(diào)整到所需要的傾斜或角度。這個(gè)角度可以在環(huán)形部分設(shè)定刻度上的幫助。建議設(shè)置的傾角應(yīng)利用刻度盤幫助檢查,如 Fig.6.10。這樣做是為了處理由于磨損和完成部分的撕裂而導(dǎo)致的錯(cuò)誤。為了檢查角度的設(shè)置,在刀架(表 6.10)上安裝針盤指示表。在理想的角度設(shè)置量角器并且夾緊在刨床工作臺(tái)上。當(dāng)表盤接觸到量角器的位置 A 時(shí)讀取數(shù)據(jù)。現(xiàn)在把刀架降低到量角器的位置 B 并注意讀取數(shù)據(jù)。如果同時(shí)閱讀,(即在 A 和 B)是相同的,那么該設(shè)置是正確的。將工件鉗緊在工作臺(tái)并且用刨子刨平。表面會(huì)利用提供的工具刨出所需要的角度。 V型塊工作已經(jīng)采取對(duì)刨子刨出某一角度的過程或在刨床(表.6.11)上開槽的過程進(jìn)行解釋。 V 型塊的水平和垂直方都用刨子加工正如 6.9.1 節(jié)前的內(nèi)容。此處圖 6.10采用 V 型塊的 V 型槽繞其軸線對(duì)稱,并成 45 °角(表 6.11)。設(shè)定工具頭成 45 °,根據(jù)早前對(duì)程序的解釋,將螺栓 A 擰緊在位置上. 設(shè)置在工具塊上的角度小于 45 °,將螺栓 B 擰緊在位置上。工具塊設(shè)置小于 45 °以防止切割工具在反復(fù)敲擊中妨礙刨具所加工的表面。鉗緊 V-型塊在刨床上,以便 V 型槽置于頂部(圖 6.11)。刀座鞍應(yīng)被轉(zhuǎn)移到 V 型塊中第一粗加工位置上。開始手動(dòng)進(jìn)料切割,向下移動(dòng)。這樣做的同時(shí)刀座鞍會(huì)留在橫梁上的同一位置。在 V 一側(cè)完成的粗加工和精加工現(xiàn)在,沒有令人不安的工具設(shè)置,扭轉(zhuǎn) V 型塊(轉(zhuǎn) 180 度)后再夾緊。工作臺(tái)槽上 V型塊的突出部分把縱長(zhǎng)的工件排成直線?,F(xiàn)在進(jìn)行重復(fù)粗加工和精加工。換向工作確保在同一角度, “V”型校準(zhǔn)和舌狀物中心線的加工。 此處圖 6.116.9.3 機(jī)床夾具和夾具在刨床上的使用依靠夾具的幫助,在刨床上刨平曲凹表面。在這種情況下夾具由旋臂組成,并在支架(表 6.12)上以旋臂為進(jìn)行中心旋轉(zhuǎn)。該支架固定交叉構(gòu)件在車床外罩上。移動(dòng)滑道的進(jìn)給螺桿并將滑道固定在旋臂上。在刨具操作過程中交叉供給導(dǎo)致刀座鞍妨礙橫梁。同時(shí),旋臂引導(dǎo)下的工具刨平彎曲凹面。該刀具的切削刃的高度是由交叉臂(表 6.12 位置 A 和 B)的角位置決定的?;B 指示工具切割邊緣的不同位置的軌跡。因此,類似的表面用刨子刨平。此處圖 6.12刨一個(gè)螺旋的螺距螺旋線很長(zhǎng),可能難以在一些銑床加工,但它可以輕松地在夾具(表.6.13)的幫助下載刨床上進(jìn)行切割。在這次操作中的工件安裝在兩個(gè)車床中心之間。夾具由一個(gè)重型螺絲鉗和一個(gè)斜桿夾組成。它的上端 A 附屬于車床外罩,低端 B固定在刨床床。該螺距取決于斜桿傾斜的角度。工作臺(tái)隨著螺絲鉗橫杠移動(dòng)到傾斜橫杠附近。在角度位置的指導(dǎo)下,螺絲鉗橫杠通過一個(gè)小弧線作為順時(shí)針輪流逐漸上升。因此,刀具切割螺旋段如圖 6.13 所示。此處圖6.13