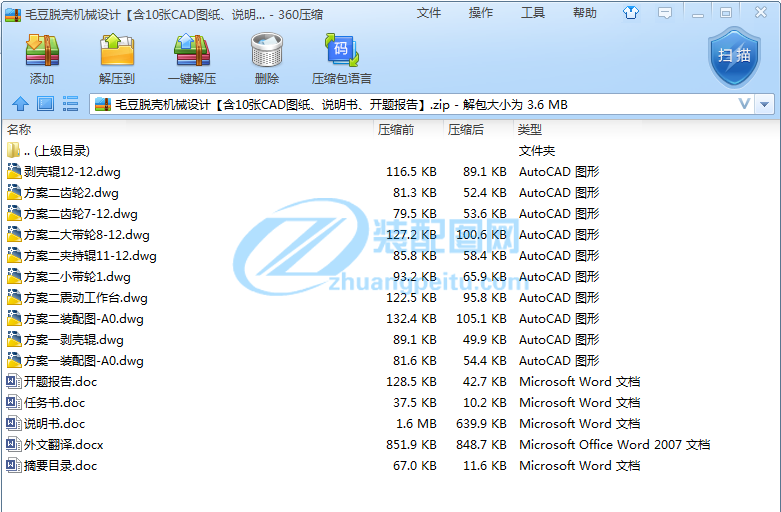
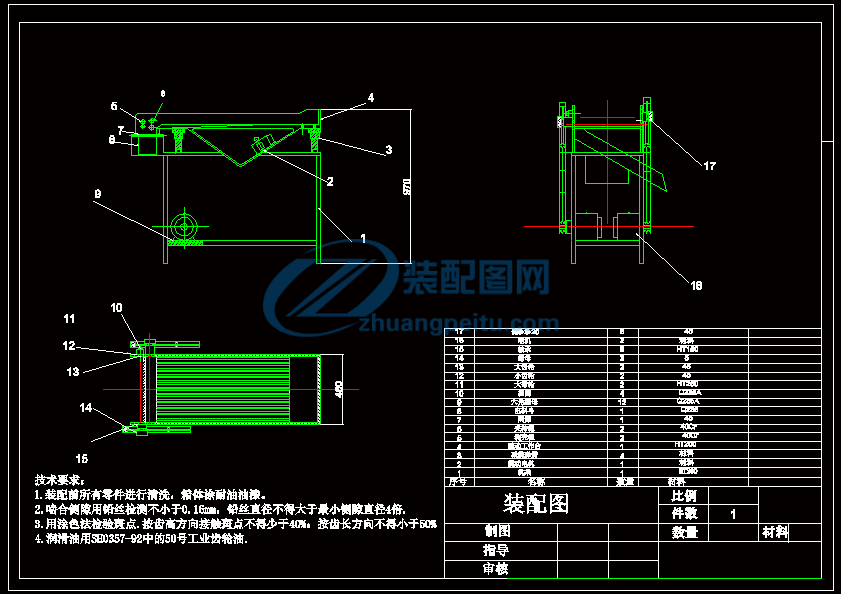
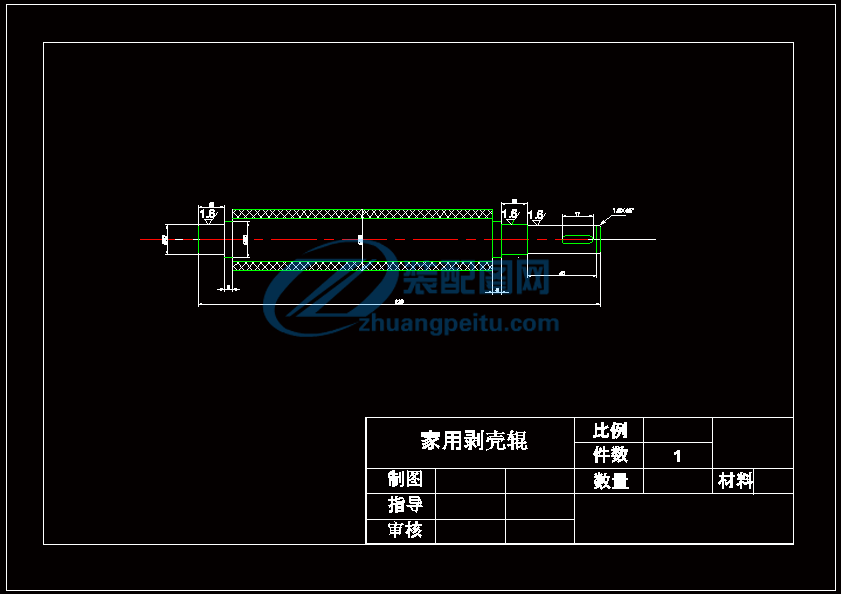
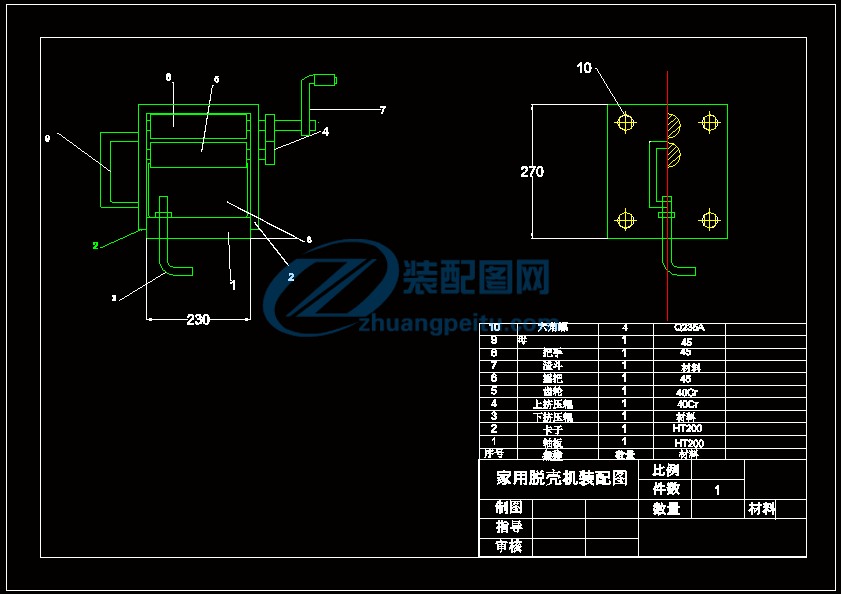
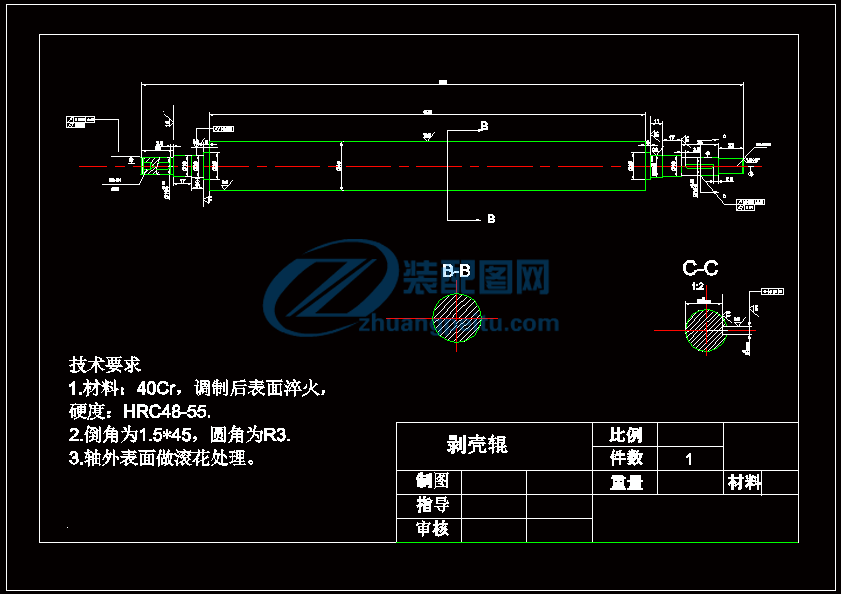
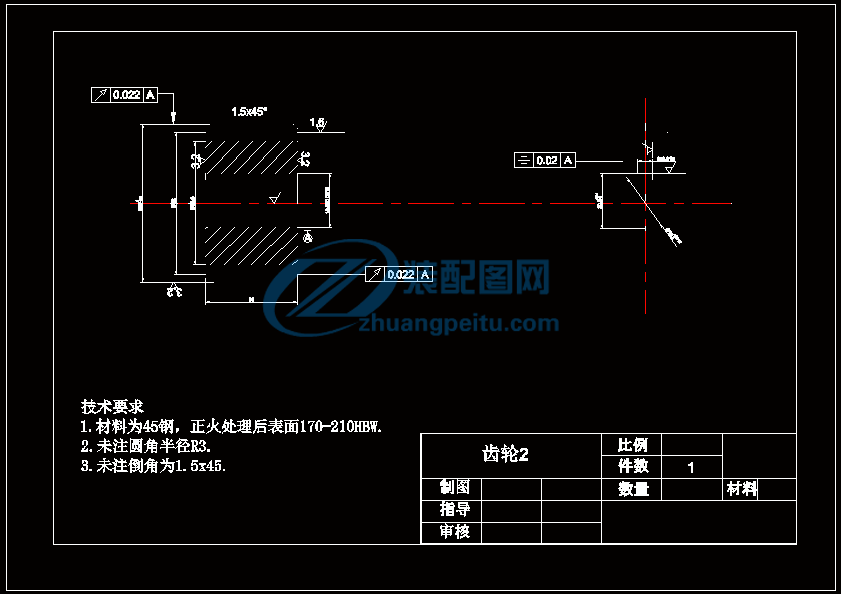
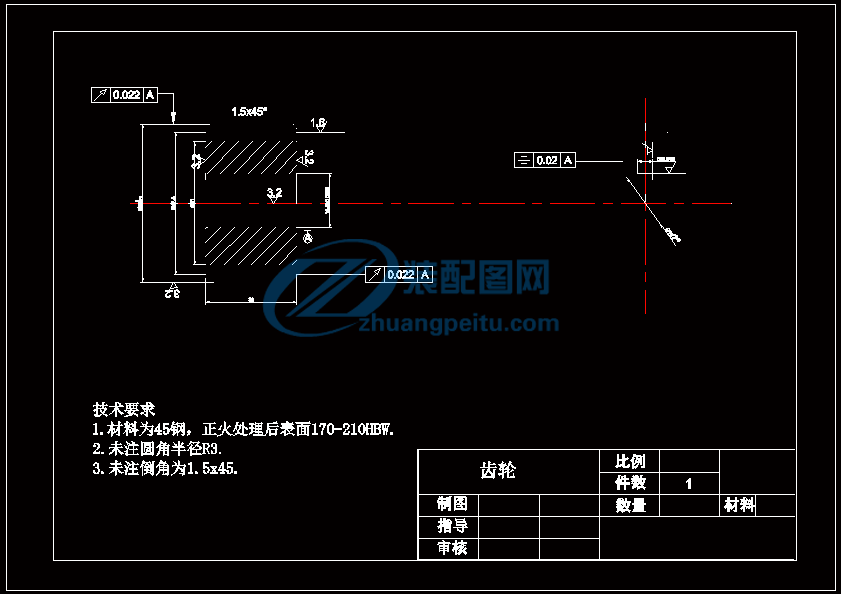
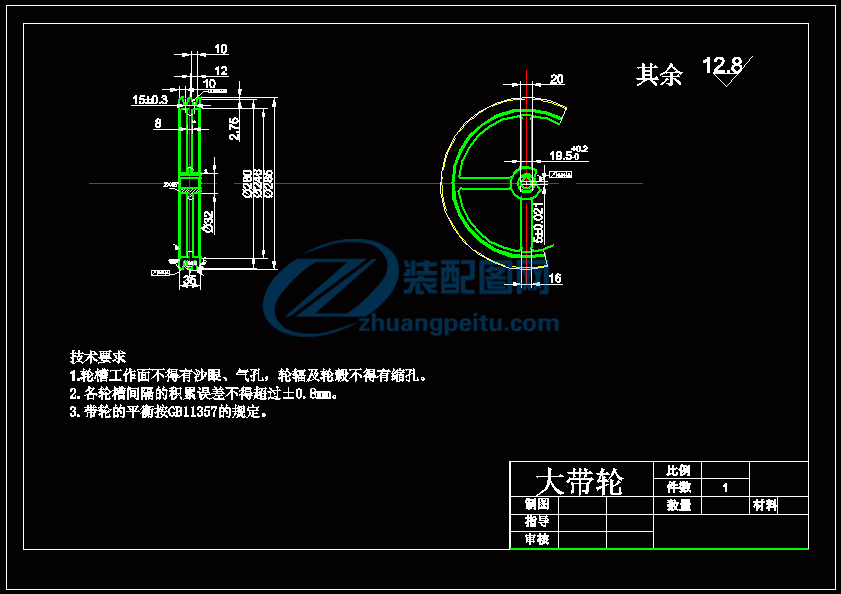
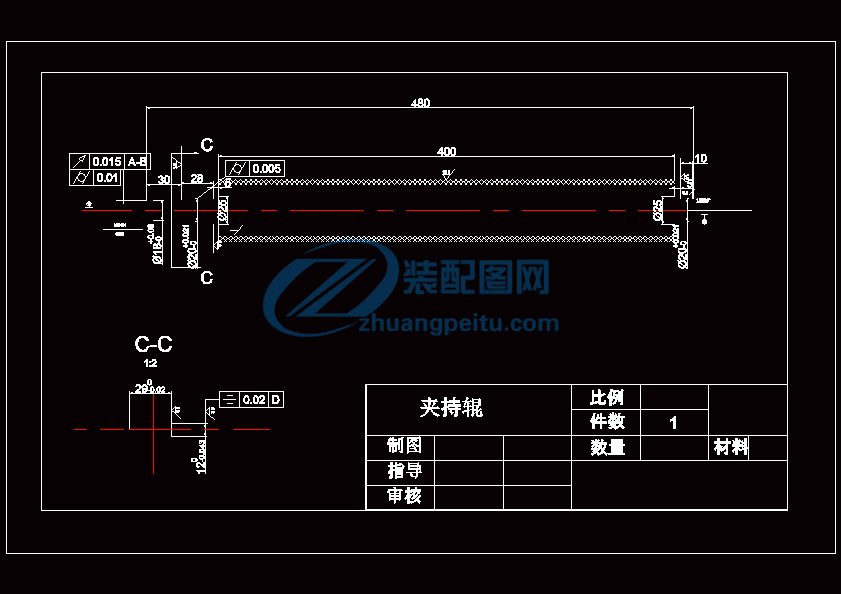
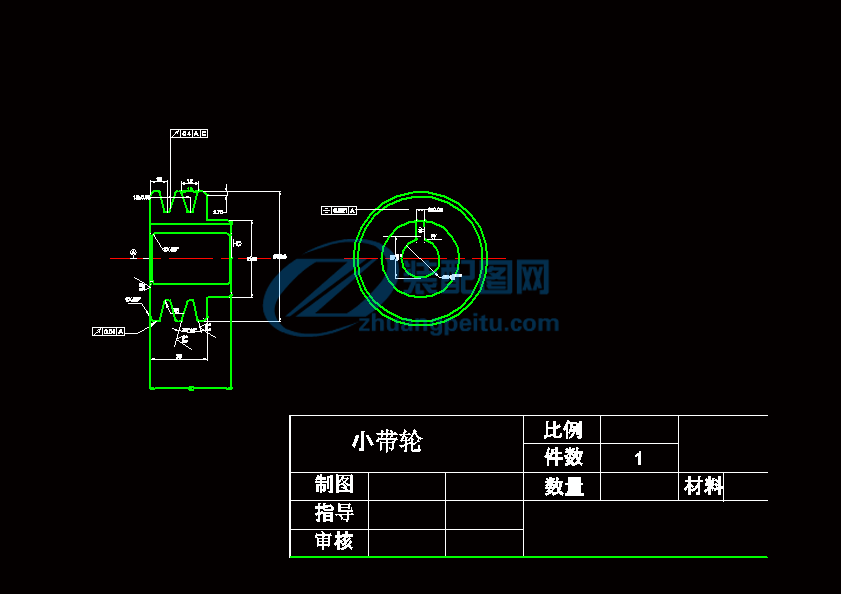
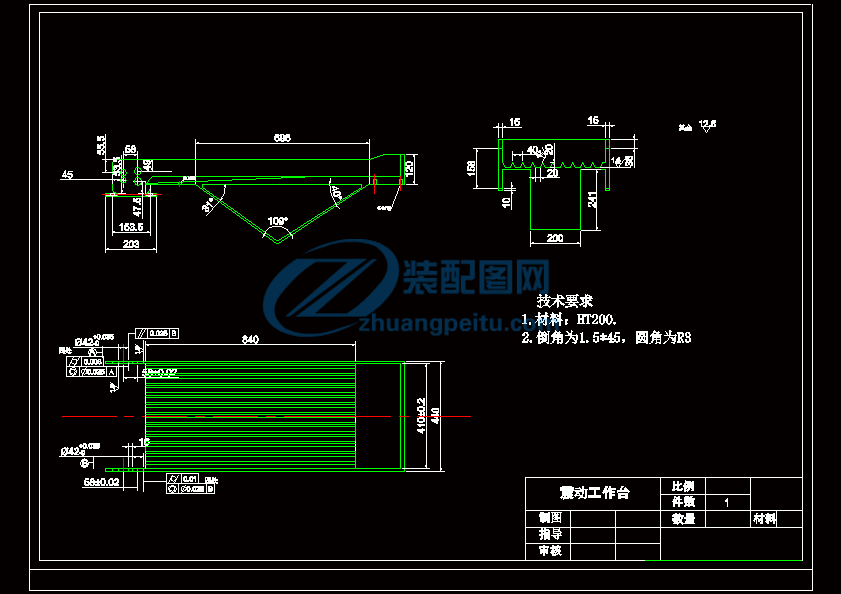
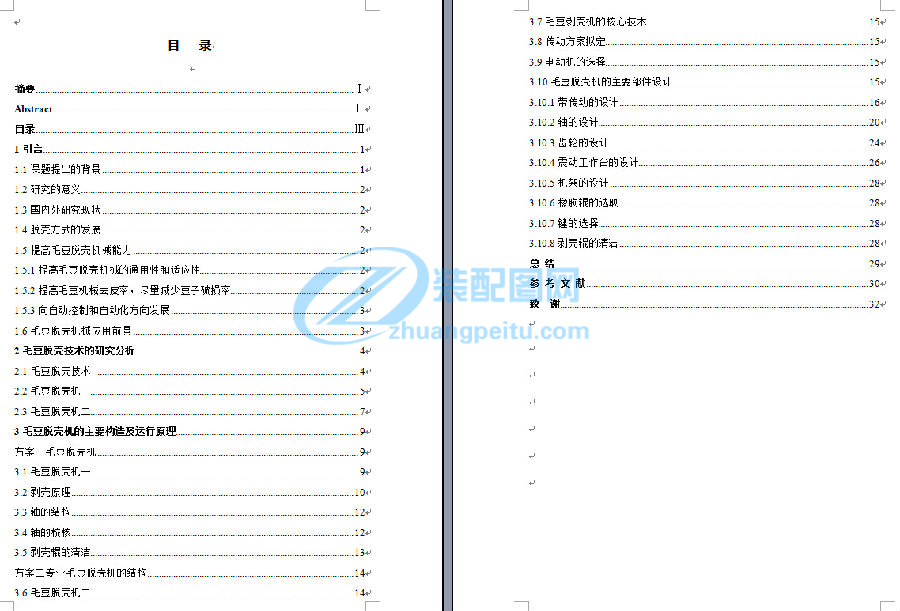
(Cooperative Institutinal Research Program 協(xié)作機構研究規(guī)劃 )CIRP 編年史一制造技術物理上一種仿真模型純鈦合金正交切削的分段芯片的形成關鍵詞: 加工 造型 分段芯片切削模擬的精度取決于微觀物理的知識,包括在切削過程的本體和微觀組織演化模型。本文提出了一種增強的物理材料模型,表現(xiàn)了微觀結構演變引起的流動軟化在臨界晶粒尺寸下的逆霍爾取效應。這個模型能通過有限元模擬和實驗評價模擬分段芯片的正交切削中剪切帶的形成與晶粒細化鈦。結果顯示良好的預測切割和推力,切屑形態(tài)和分割頻率的精度。1 簡介一個分段芯片通常是在切削材料中,具有低的熱導率(例如鈦及其合金)。低導熱系數(shù)產(chǎn)生的熱積累在主剪切帶,這會導致局部軟化,剪切定位和芯片分割。這反過來又會導致不希望的振蕩,多余的切削力和相關的振動,這回抑制刀具壽命和降低量產(chǎn)加工特征的表面質量和尺寸精度。分段芯片的形成已被模擬的幾個采用不同的建模方法,以及記錄在最近的主題論文[ 2 ] CIRP 研究?;诩羟袔е械目障逗土芽p觀測,烏爾曼等人。[ 3 ]模擬分段切屑形成的韌性模型中的斷裂機制。華和希沃布里[ 4 ]用基于能量的韌性斷裂準則模擬分段切屑在切割 ti-gal-4v 形成。最近,calamaz 等人。[ 5 ]提出了一個現(xiàn)象學對流行的約翰遜庫克流動應力模型模擬切割 ti-gal-4v 芯片分割現(xiàn)象的修改。奧斯并對這一模型進行了進一步的細化。 [6 7]他的同事研究不同的應用。路路達和 umbrello [8]使用一種類似的流動應力模型隨著晶粒尺寸和硬度變化的演化方程由于動態(tài)再結晶的微觀結構變化預測(DRX)在干燥和低溫加工 ti-gal-4v 。calamaz 等人[ 5 ]還指出,應變軟化可以歸結為由動態(tài)恢復引起的微觀結構的變化(DRV)和動態(tài)再結晶過程的主動在嚴重的塑性變形。丁和 shin[9]提出了一種基于物理的材料模型利用位錯密度作為唯一的影響因素內部狀態(tài)變量。然而,他們只是模擬連續(xù)芯片的形成與模型。在臺灣的論文,最近開發(fā)出基于物理概念的模型[ 10 ],這是出于克服對移動位錯的相互作用的力學與微觀結構的障礙,通過將一個額外的變形機制,允許擴展在工業(yè)純鈦切削分段芯片形成準確的模擬(CP-Ti)。具體而言,為了描述超細晶粒的材料行為是純鈦切削過程中剪切帶中形成的,模型中引入了反Hall-Petch 效應(ihpe),通常歸因于晶界滑動 [ 11 ],這是材料一種臨界晶粒尺寸下的流軟化模型。這使材料低于臨界晶粒尺寸。該模型是作為一個用戶定義的子程序在一個基于有限元的加工仿真軟件 AdvantEdge 實施(第三波系統(tǒng),美國)和模擬 cp-ti。正交切削試驗,以確定切削力和芯片特性,以仿真結果來評估性能的增強的模型。2。基于物理的本構模型一部分簡要總結了以前開發(fā)的本構模型[ 10 ]的關鍵環(huán)節(jié),這與連續(xù)的切屑形成的模擬交易,并討論了 ihpe 模型增強。熱激活理論[ 12 ],一個金屬的流動強度進行塑性變形的制定.對于熱應力的疊加錯位的熱應力 如下的幅度的大小,取決于移動位錯與短距離的障礙,如晶格摩擦和溶質原子的th?相互作用的強度。這部分是仿照使用 Mecking 和 KOCKS【13 ]提出了如下的公式:其中,k 是玻爾茲曼常數(shù),T 是絕對溫度,G0 是歸一化的活化能在 0k, 是溫?度依賴的剪切模量,b 是漢堡的幅度向量,是一個參考應變率,分析所需的壓力克服短距離障礙在 0k, p 和 q 是定義與短距離相關的能量障礙的形狀障礙的參數(shù)無熱應力 應力之和的代表,所需克服的阻力位錯運動由晶界提供a?Pq 的強度與參數(shù)有關,P 和 G 是移動位錯晶界強度相關參數(shù)和位錯林相互作用2 種變量的位錯密度的內部狀態(tài)。P,是平均晶粒尺寸, D 的演化與變形在晶界的貢獻來看,Q 在式(3),參數(shù) G 等于一個常數(shù) C,這在變形機制在傳統(tǒng) Hall-Petch 效應是積極的是獨立的晶粒尺寸。臨界晶粒尺寸小于(D ),它是溫度的函數(shù),該 ihpe 是許多金屬伴隨著減少流動應力隨晶粒尺寸的變化(圖 1)。為了捕捉到這個軟化,用唯象方程建模:D 和 V 是溫度依賴性形式的參數(shù)如表格 2,對于這種組合 D 和 V,得到 D 在,室溫為 10nm,這是根據(jù)協(xié)議與價值的報道中的各種金屬而決定的[ 14 }。圖中傳統(tǒng)的 Hall-Petch 效應反 Hall-Petch 效應進化(Refinement )的晶粒尺寸, D,由于連續(xù)動態(tài)再結晶;這發(fā)生在嚴重的塑性變形鈦[ 15 ],模型如下£一和 B 是溫度和應變率相關的參數(shù),D }d 是最初的晶粒尺寸和 df 是最終的結晶晶粒尺寸定義為 Zener-Hollomon 參數(shù)的函數(shù)Cz M 是材料相關的參數(shù)。在這一術語中,代表了位錯林的貢獻 p,位錯密度的演化模型如下PHA 是由于滑移引起的位錯密度硬化和動態(tài)恢復過程(但在沒有 DRX)和由封閉的形式表達:P0 是初始的位錯密度,A 和 B 是硬化和動態(tài)恢復參數(shù)。PA 在完全再結晶的相應的位錯密度晶粒結構。隨著塑性應變的增加,位錯消耗在動態(tài)再結晶形成新的細胞/晶界過程[ 16},這是仿照(7 )式。在高應變率變形是受粘性阻力影響,阻礙了運動位錯[ 17 ]。因此,流動的位錯阻力分量應力為藍本如下[ 10 }:D 是位錯(粘性)阻力系數(shù)3 模型的校準從文學和/或從材料中使用的 12 被稱為純鈦材料參數(shù)和常數(shù)實驗,在表 1 中列出,其余十一個自由參數(shù),這是不可用的在文獻中,校準使用在[ 18 }和表 2 中給出的可用數(shù)據(jù)。已知的材料參數(shù)和常數(shù) CP Ti參數(shù) 價值屬性 出自裁定校準模型參數(shù) CP Ti4 實驗正交管切割實驗在一個哈丁 t-42 SP 數(shù)控車床進行的采用工業(yè)純鈦(2 級)一個接收顯微結構等軸 α 相晶粒平均直徑的 40 微米為保證平面應變條件下,管壁厚度僅限于 2 毫米。要探索一個寬范圍的應變和應變率,三個提供 t= 0.1,0.2,0.3 毫米)和五個切削速度(V }。= 20,80 ,100 ,140,180 米/分鐘)使用。每個測試條件被重復兩次。此外,每個測試使用 0°前角工具和一個新的涂層的鎢硬質合金刀片(ennametal tcmw3251,一個鋒利的切削刃(10 微米。無切削液使用。切削力,f 推力、FT、測定使用壓電測力儀(我的 模型 9257B)。切屑在環(huán)氧樹脂中冷裝在一個 0.05 微米中完成。用 1 mL 氫氟酸的混合物酸(HF, 40%),2 毫升硝酸(硝酸,40 })和 247 mL 去離子水,用于蝕刻和顯示芯片的微觀結構。5 有限元模型為了模擬正交切削,二維有限元模型內置 advantedgetm(第三波系統(tǒng),美國),一個基于物理的機械加工仿真代碼。增強本物理模型,介紹了在軟件中實現(xiàn)的用戶通過 —在 FORTRAN 編碼定義屈服面常規(guī)。接觸工具/ 芯片接口的條件為藍本使用庫侖摩擦定律。摩擦系數(shù)的平均 貝塔,在每個模擬工具/ 芯片接口(表 3)是從測得 f 和 FT 和方程計算圖 3模擬中使用的摩擦系數(shù)6 結果在圖 2 模擬 f 和 FT 與實驗結果進行了比較測量 f 和 FT 隨 V }減少在圖 2。平均和變異的實驗(EXP)和模擬(SIM)切割和推力不同切削條件下PICTURE 3圖 3。平均和變異的實驗(EXP )和平均模擬(SIM )峰(s1)和山谷(s2)不同切削加工的切屑厚度條件。說明:由于在芯片幾何,平均估計和不規(guī)則平均使用方法計算了 s1 和 s2 估計方差適用于 10-15 數(shù)據(jù)分片模擬結果顯示了類似的趨勢5%預測錯誤 10-20 的錯誤在 f 在英尺的誤差更高是應為是由于簡單的庫侖摩擦模型的使用在有限元模型中的刀具磨損的情況下,這總是在切削鈦。分段芯片模擬峰值(S1)、谷(S2)厚度的 RU TU 4與測量結果圖 3 相比請注意,只有充分形成剪切帶被包含才可測量。一般情況下,測得的芯片厚度的增加 vc 而減小 tu 模擬值顯示了類似的趨勢,但往往高估厚度,特別是 S2 對于大多數(shù)的切削條件原因是缺乏韌性斷裂機制的驗證經(jīng)??梢栽谧杂杀砻嬗^察到裂縫模型在剪切帶附近的芯片(見圖 1))詳細的芯片形態(tài)的比較如圖 4 所示段芯片的被模擬捕獲圖 4。測量和模擬芯片形狀的比較圖 5 對比實驗( EXP)和模擬(SIM)芯片分割頻率)圖 5 顯示了實驗和模擬的比較芯片分割頻率計算從平均峰值 —峰值距離和切割速度。仿真結果捕捉測得的趨勢,這表明分割頻率增加幾乎呈線性關系。和隨vc 增加 T為了評估模型的能力,定性模型預測的微觀結構中的機械加工芯片,四個具體在芯片中的位置,標記為 A-D 圖 1(1 ),被選中。A 位置一個位于遠離剪切帶,B 是在邊界,C 是內部的剪切帶,D 在尖端的剪切帶。晶粒尺寸與位錯的對應分布密度在四個位置如圖克(B 和 C)。TU 6 在實際的芯片微結構光學顯微剪切帶區(qū)域模擬(b )和(c)晶粒位錯密度分布位置標記 a-d 晶粒尺寸 位錯密度位置 a 上(見圖( 6)),晶粒細化小。這個圖(b)的模擬也顯示了一個較小的細化晶粒尺寸在一個在這一地區(qū)的較低的塑性應變(見圖 4)。然而,該應變足以引起位錯密度的增加與初始值相比(見圖))。在位置(圖克(圖))的一些精少量的晶粒結構表明在這里發(fā)生足夠大的塑性變形。圖中相應的模擬(乙)也表示了更多該地區(qū)的細化晶粒尺寸。內部的剪切帶(位置),模擬產(chǎn)生的超細晶粒(圖 G(B))由于動態(tài)再結晶和 ihpe 模型中的機制。預測平均晶粒尺寸為 50-70 納米的剪切帶區(qū)域。在高溫下的剪切帶,超細晶粒產(chǎn)生的逆霍爾 —佩奇效應,導致材料軟化。此外,較低的位錯密度(相比,a 和 b)預測的剪切帶(圖)(圖),與超細晶粒一致圖(b)。剪切下位錯密度的降低可以由位錯湮滅/ 使用說明 —過程活躍在DRX,與已知的一致 DRX [ 1 6}。注意小韌性裂紋位置 D 如圖 6 中常看到。由于材料強度的損失,由于延性模型中不包括骨折,模擬無法復制這種觀察。7 結論本文提出了一種增強的基于物理的本構分段切屑形成的數(shù)學模型工業(yè)純鈦(CP Ti)。模型結合反 Hall-Petch 效應(ihpe)描述軟化效應細晶結構在剪切帶內的物質流動強度。流動強度是一個晶粒尺寸位錯密度隨變形而變化的函數(shù)。為了驗證仿真結果,正交實驗進行了一系列的材料和不同速度。模型模擬產(chǎn)生合理準確的預測切割力(<5 }錯誤),推力(10-20 }錯誤),分割頻率和芯片形態(tài)。此外,該模型能夠模擬晶粒尺寸和位錯的空間分布密度,這被證明是在良好的定性協(xié)議所觀察到的芯片微結構。未來的工作將集中于在模型中加入韌性斷裂機制來捕捉裂紋剪切帶區(qū)域的形成。