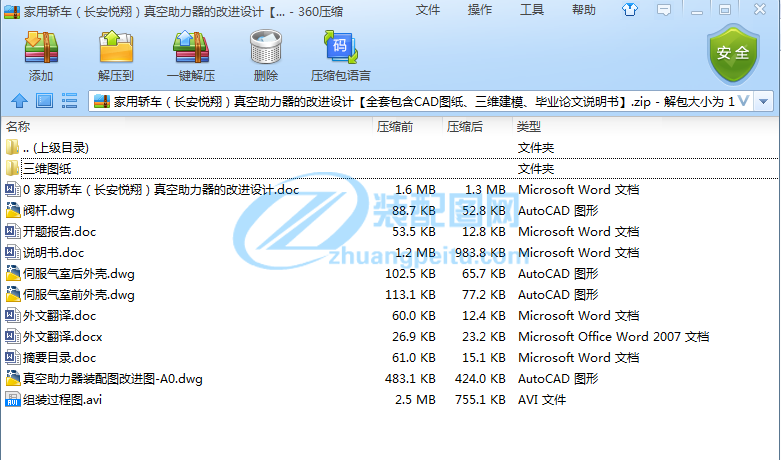
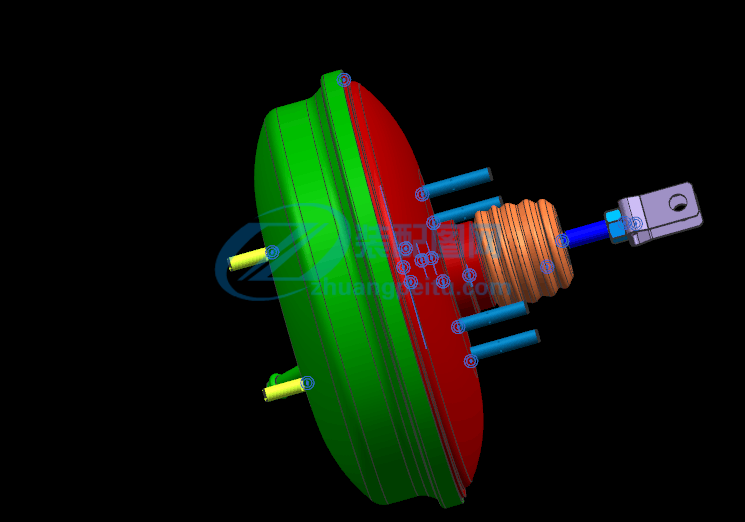
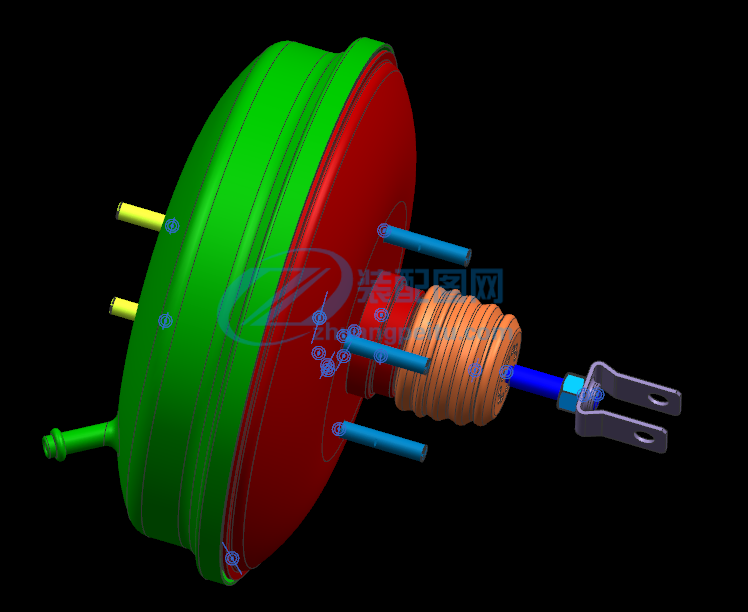

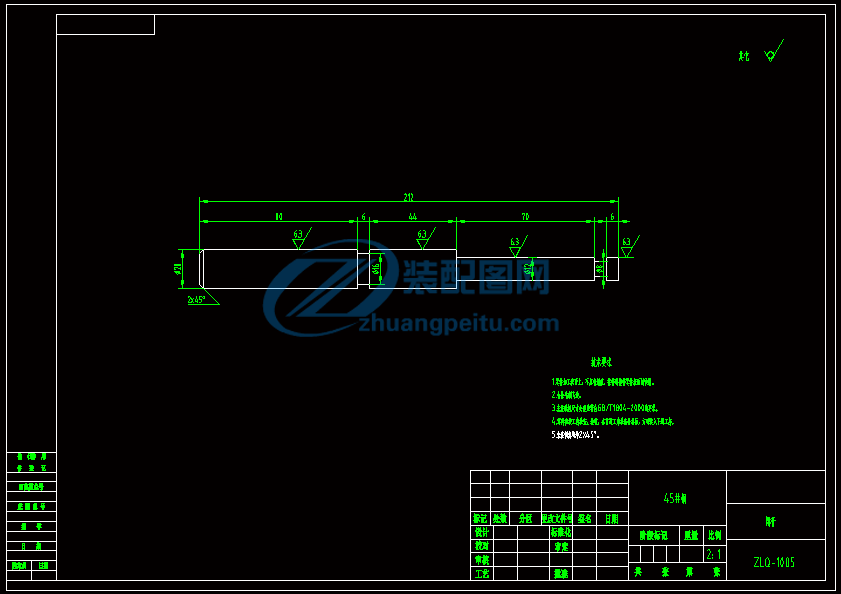
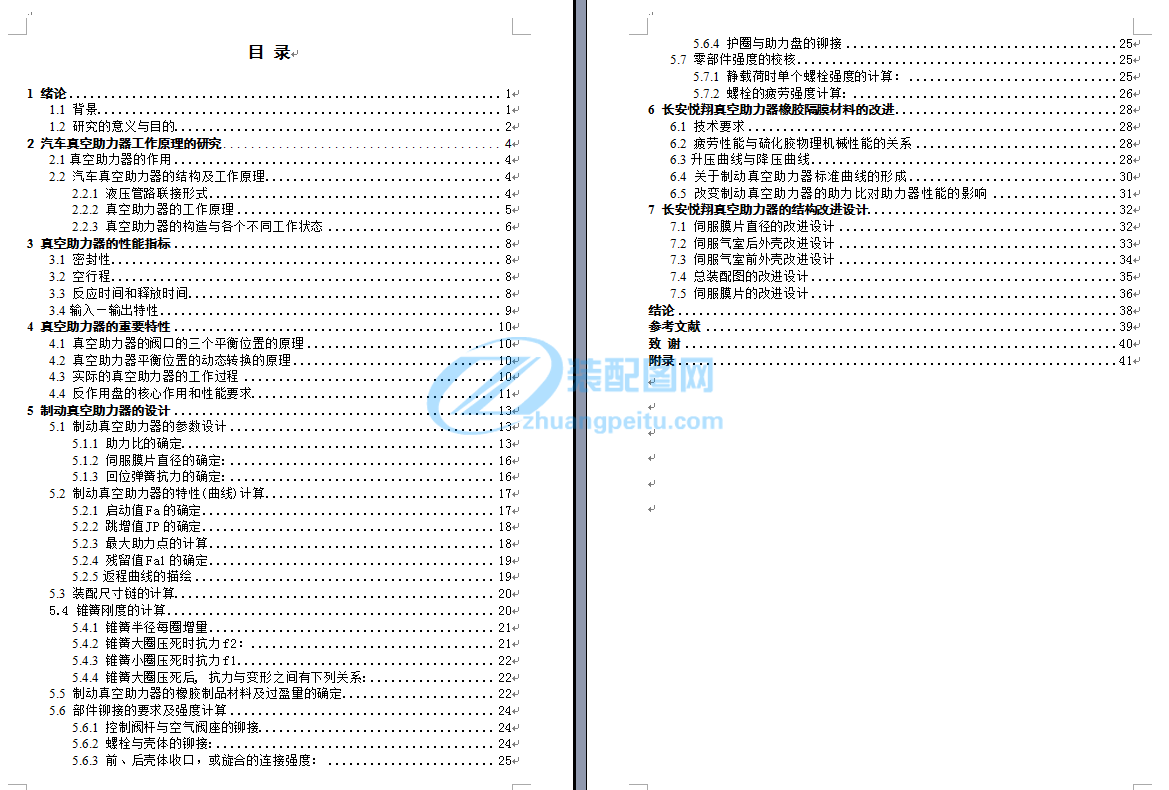
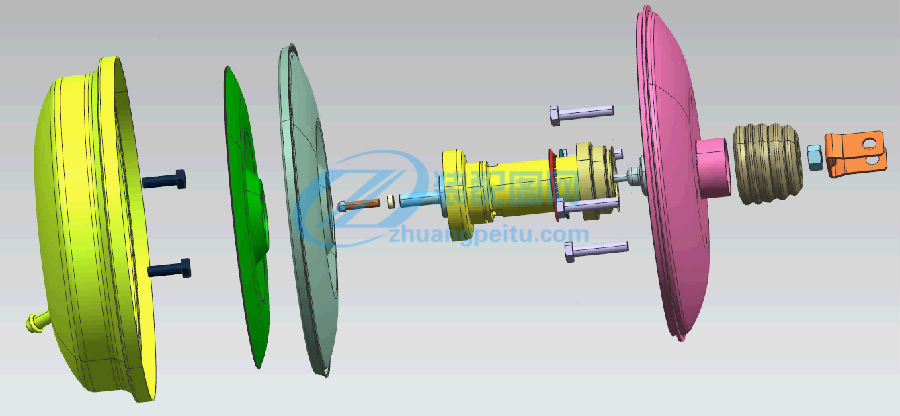
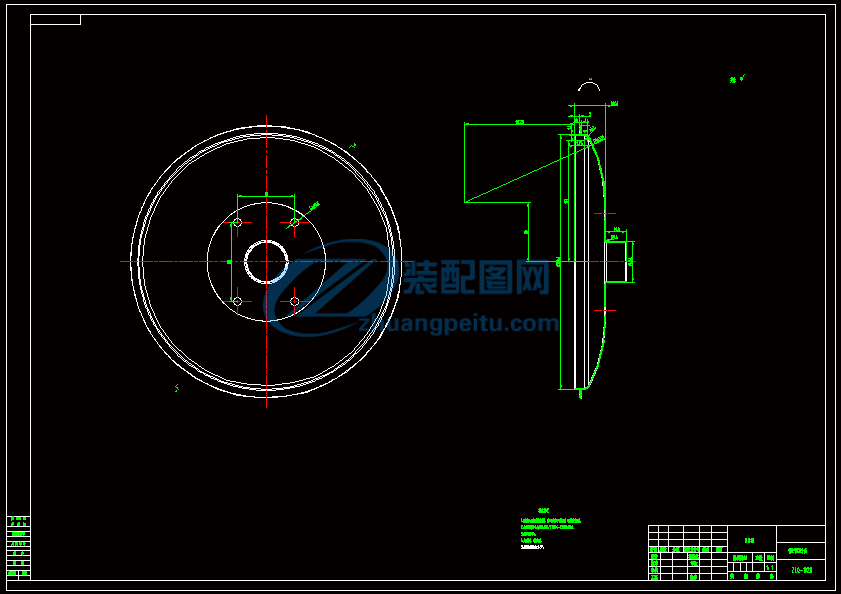
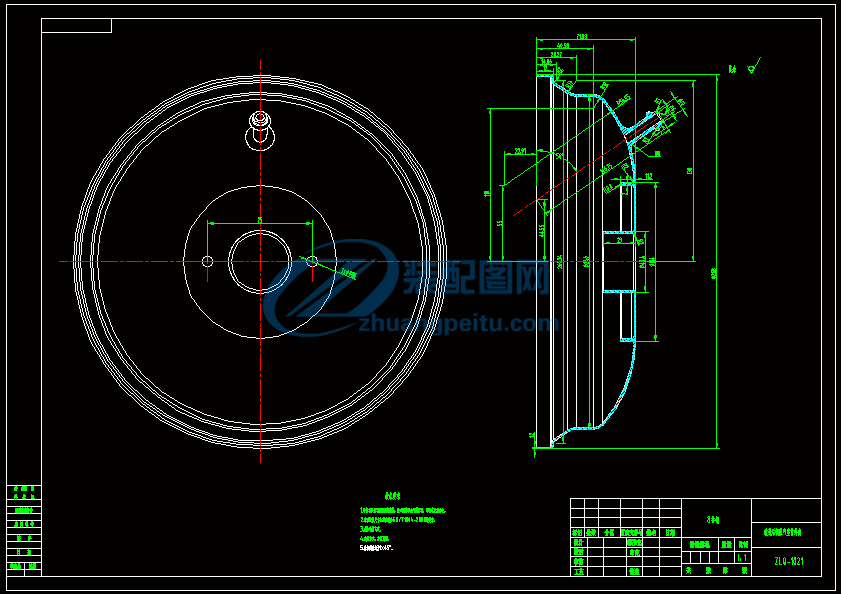

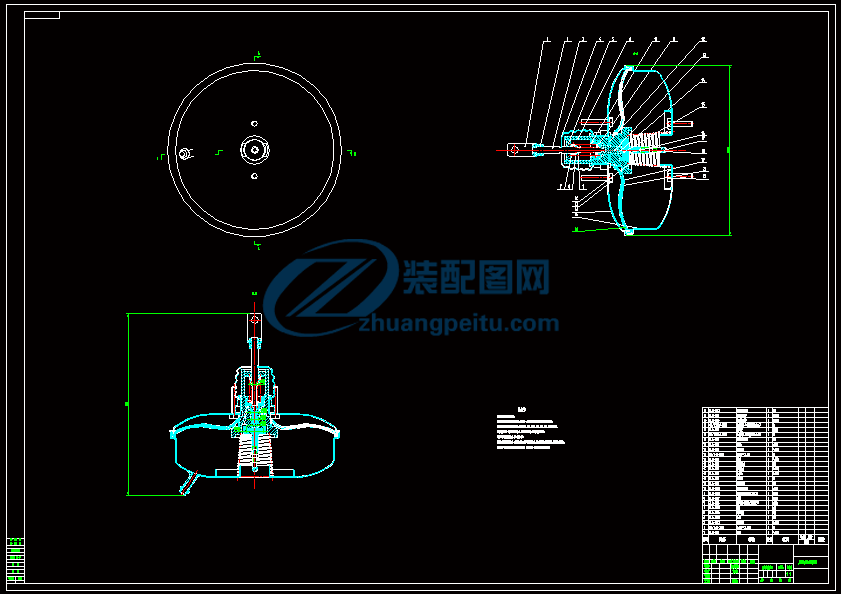
真空助力器工作原理在非工作的狀態(tài)下,控制閥推桿回位彈簧將控制閥推桿推到右邊的鎖片鎖定位置, 真空閥口處于開啟狀態(tài),控制閥彈簧使控制閥皮碗與空氣閥座緊密接觸,從而關(guān)閉了空氣閥口。此時助力器的真空氣室和應(yīng)用氣室分別通過活塞體的真空氣室通道與應(yīng)用氣室通道經(jīng)控制閥腔處相通,并與外界大氣相隔絕。發(fā)動機啟動后, 發(fā)動機的進氣歧管處的真空度(發(fā)動機的負壓)將上升至-0.0667MPA(即氣壓值為 0.0333MPA,與大氣壓的氣壓差為 0.0667MPA)。隨之,助力器的真空、應(yīng)用氣室的真空度均上升至-0.0667MPA,并處于隨時工作的準(zhǔn)備狀態(tài)。當(dāng)進行制動時,制動踏板被踏下,踏板力經(jīng)杠桿放大后作用在控制閥推桿上。首先, 控制閥推桿回位彈簧被壓縮,控制閥推桿連同空氣閥柱前移。當(dāng)控制閥推桿前移到控制閥皮碗與真空閥座相接觸的位置時,真空閥口關(guān)閉。此時,助力器的真空、應(yīng)用氣室被隔開。此時,空氣閥柱端部剛好與反作用盤的表面相接觸。隨著控制閥推桿的繼續(xù)前移,空氣閥口將開啟。外界空氣經(jīng)過濾氣后通過打開的空氣閥口及通往應(yīng)用氣室的通道,進入到助力器的應(yīng)用氣室(右氣室),伺服力產(chǎn)生。由于反作用盤的材質(zhì)(橡膠件)有受力表面各處的單位壓強相等的物理屬性要求,使得伺服力隨著控制閥推桿輸入力的逐漸增加而成固定比例(伺服力比)增長。由于伺服力資源的有限性,當(dāng)達到最大伺服力時,即應(yīng)用氣室的真空度為零時(即一個標(biāo)準(zhǔn)大氣壓),伺服力將成為一個常量,不再發(fā)生變化。此時,助力器的輸入力與輸出力將等量增長;取消制動時,隨著輸入力的減小,控制閥推桿后移。當(dāng)達到最大助力點時,真空閥口開啟后,助力器的真空、應(yīng)用氣室相通,應(yīng)用氣室的真空度將下降,伺服力減小,活塞體后移。就這樣隨著輸入力的逐漸減小,伺服力也將成固定比例(伺服力比)的減少,直至制動被完全解除。真空助力器的核心尺寸鏈在助力器的設(shè)計中,核心尺寸鏈的設(shè)計是保證助力器工作性能的關(guān)鍵,其中最為關(guān)鍵的尺寸配合是空氣閥柱長度 與真空閥座到反饋盤主面的距離 (對于雙膜片的助力器來說, 是指真空閥口到活塞體凸臺上端面的距離與軸套同凸臺相接觸的端面到軸套同反饋盤表面相接觸的端面距離之和)和控制閥的真空閥口處的形變量 之間的配合關(guān)系。在上述的理想狀態(tài)工作過程的敘述中,我們可以注意到在理想的工作狀態(tài)下的當(dāng)空氣閥口到達打開的瞬間位置時,空氣閥柱端部應(yīng)剛好與反作用盤接觸,可以看出在理論上成立的狀態(tài)在現(xiàn)實中是不可能實現(xiàn)的。第一,每個零件的尺寸是有它的尺寸公差帶;第二,大量部件的生產(chǎn)是符合統(tǒng)計規(guī)律的,實際的尺寸區(qū)間是一個公差帶,而理想的位置只是在公差帶上的一個點而已。那么,在實際設(shè)計中,是如何處理這個矛盾的。其核心的尺寸鏈的配合采取的是間隙配合。也就是說,當(dāng)空氣閥口打開的時候,空氣閥柱的端部沒有到達反作用盤的接觸面上,存在一定的間隙。在實際設(shè)計中,為取得良好的始動力和釋放力等技術(shù)參數(shù),采用了間隙配合。真空助力器的三個重要的工作原理目前關(guān)于真空助力器的文獻中,都只是提到了真空助力器的三個工作狀態(tài),即應(yīng)用狀態(tài)、維持狀態(tài)、釋放狀態(tài)。并指出在這三種狀態(tài)下,真空閥口和空氣閥口的處于開或合的狀態(tài)。除了在上述提到的基本原理以外, 又發(fā)現(xiàn)了在國內(nèi)文獻中未曾提及的幾個重要原理, 即, 三個平衡位置的原理、平衡位置的動態(tài)轉(zhuǎn)換的原理和反作用盤的核心作用。真空助力器的閥口的三個平衡位置的原理汽車真空助力器在工作過程中存在著三個平衡位置,在加載時(或制動時)空氣閥口處于若即若離狀態(tài),此時控制閥在空氣閥口處無形變,而真空閥口處于關(guān)閉狀態(tài),控制閥在真空閥口處有形變;在卸載時(或取消制動時)真空閥口處于若即若離的狀態(tài),此時控制閥在真空閥口處無形變,而空氣閥口處于關(guān)閉狀態(tài),控制閥在空氣閥口處有形變;當(dāng)制動穩(wěn)定在某一時刻,輸入力不再變化時(即助力器處于無運動趨勢的狀態(tài)),空氣閥口和真空閥口均處關(guān)閉狀態(tài),控制閥在真空閥口處和空氣閥口處均有形變。這就是助力器在工作狀態(tài)下的三個平衡位置。真空助力器平衡位置的動態(tài)轉(zhuǎn)換的原理助力器在工作過程中的平衡位置的動態(tài)轉(zhuǎn)換的原理。這是一個極容易被忽視的原理,也是在結(jié)構(gòu)和工藝設(shè)計時必須考慮到的重要原理。當(dāng)加載結(jié)束的瞬間,助力器將由加載平衡位置向制動穩(wěn)定態(tài)平衡位置轉(zhuǎn)換,即控制閥在空氣閥口由無形變向有形變轉(zhuǎn)換。此時,空氣閥口的結(jié)構(gòu)設(shè)計及加工質(zhì)量是否能夠保證密封性的要求將受到嚴(yán)格的考驗;當(dāng)卸載開始的瞬間,助力器將由制動穩(wěn)定態(tài)平衡位置向卸載平衡位置轉(zhuǎn)換,即控制閥在真空閥口由有形變向無形變轉(zhuǎn)換。此時,真空閥口的結(jié)構(gòu)設(shè)計及加工質(zhì)量是否能夠保證密封性的要求將受到嚴(yán)格的考驗。 實際的真空助力器的工作過程由上述的闡述可以看到,實際的工作過程與理想的工作過程是有所不同的。在核心尺寸鏈為間隙配合的條件下,結(jié)合工作狀態(tài)的三個平衡位置的理論。真空助力器的實際的工作過程是:制動時,制動踏板被踏下。踏板力經(jīng)過杠桿的放大后作用在控制閥推桿上。首先,推桿回位彈簧被壓縮,控制閥推桿連同空氣閥柱前移。當(dāng)控制閥推桿前移到控制閥皮碗與真空閥座相接觸的位置時,真空閥口關(guān)閉,控制閥的真空閥口處從剛剛接觸直到產(chǎn)生形變。此時,真空、應(yīng)用氣室被隔開,控制閥推桿繼續(xù)前移使得空氣閥口處于即將開啟狀態(tài)。此時,控制閥的空氣閥口處已經(jīng)沒有形變。此處是助力器升壓時的平衡位置,此時空氣閥柱端部還沒有與反作用盤的主面相接觸。隨著控制閥推桿的繼續(xù)前移,空氣閥將開啟。外界空氣經(jīng)過濾氣后通過打開的空氣閥口及通過到應(yīng)用氣室的通道,進入到助力器的應(yīng)用氣室(右氣室),伺服力產(chǎn)生。由于反作用盤的主面沒有與控制閥的端部接觸,因此,助力器還沒有達到平衡。而空氣進入到應(yīng)用氣室產(chǎn)生的伺服力使得反作用盤的副面受力,于是反作用盤的主面隆起,直到副面上產(chǎn)生的伺服力的大小使得主面隆起的高度達到與控制閥的端面接觸時,助力器初始平衡位置建立。然后,隨控制閥推桿輸入力的逐漸增加而伺服力成固定比例(伺服力比)增長。由于伺服力資源的有限性,當(dāng)達到最大伺服力時,即應(yīng)用氣室的真空度為零時(應(yīng)用氣室氣壓為一個大氣壓),伺服力將不再發(fā)生變化。此時助力器的輸入力與輸出力將等量增長,隆起的主面將在控制閥力的作用下,逐漸減小隆起的高度,當(dāng)達到足夠到的輸入力時,反作用盤的主面甚至開始下凹,此時的空氣閥口處打開的間隙越來越大,助力器的應(yīng)用氣室與外界空氣完全相通;取消制動時,隨著輸入力的減小,控制閥推桿后移,伺服力仍然是個固定值,控制閥口開啟的間隙越來越小直到退后到空氣閥口剛好關(guān)閉并隨之產(chǎn)生形變。注意此處的位置并不是降壓過程的平衡位置。隨著輸入力的繼續(xù)減小,真空閥口將處于即將開啟的狀態(tài),此時的真空助力器的控制閥才處于降壓過程中的平衡位置。我們注意到升壓時的平衡位置與降壓時的平衡位置存在一個的差值,這個差值就是控制閥在真空閥口和空氣閥口處的兩個形變值的和,即 。由于核心尺寸鏈?zhǔn)情g隙配合,此差值使得反作用盤在助力器降壓過程中需要更大隆起高度來實現(xiàn)平衡。真空閥口開啟后,助力器的真空、應(yīng)用氣室相通,應(yīng)用氣室的真空度將下降,伺服力減小,活塞體后移。在連續(xù)的降壓過程中,控制閥的空氣閥口處始終有形變,而控制閥的真空閥口一直處于無形變(即若即若離的狀態(tài))。直到反作用盤的主面作用力接近為零。此時,助力器達到了最后的平衡位置。如果控制閥推桿繼續(xù)后退,助力器的平衡被打破,恢復(fù)到初始的狀態(tài)。這就是真空助力器的一次密封檢驗(或者說,一次常規(guī)的制動過程)中真空助力器工作的詳細過程,了解這個過程對于理解真空助力器的特性曲線的各性能參數(shù)的理解是至關(guān)重要的。在第 3 章的真空助力器的性能參數(shù)的計算中,就是依據(jù)此過程來得到的。而沒有使用間隙配合的真空助力器的性能參數(shù)的計算和曲線以及產(chǎn)生的后果將在第 4 章中作詳細的討論。應(yīng)該特別注意的兩個概念是:在一臺設(shè)計合理的真空助力器實際工作過程中,應(yīng)該存在初始平衡位置和最后平衡位置這兩個概念。在輸入力-輸出力的特性曲線中,兩個平衡位置的力學(xué)關(guān)系的體現(xiàn)分別對應(yīng)的是始動力和釋放力處跳躍值變化的過程。真空助力器兩個平衡位置的概念初始平衡位置的概念:在升壓過程中,空氣閥口開啟的同時,空氣閥柱端部未能觸到反作用盤上,即合理的間隙配合。這樣空氣閥口打開,應(yīng)用氣室進氣,伺服力產(chǎn)生。于是,反作用盤的副面受力,反作用盤發(fā)生形變,主面將隆起,直到隆起的主面與空氣閥端部接觸,才達到一個穩(wěn)定的平衡。在此過程中由于伺服力的增大,使輸出力(或液壓)在輸入力不變的情況下增加。最后平衡位置的概念:在降壓過程的末期,隨著輸入力的降低,當(dāng)反作用盤主面的受力幾乎為零時,助力器的輸出力完全是由伺服力產(chǎn)生的。這個伺服力同時又保證著反作用盤的形變。此時,如果控制閥推桿繼續(xù)后移,由于制動主缸不能產(chǎn)生足夠的抗力與殘留的伺服力相平衡,使反作用盤不能產(chǎn)生足夠的起補償作用的形變量,以保持助力器的平衡,則助力器將失去平衡狀態(tài)。其后,真空閥口將被打開,伺服力被釋放,反作用盤上的形變消失,助力器恢復(fù)到起始狀態(tài)。由于加載時和卸載時的控制閥閥口的平衡位置轉(zhuǎn)變,可以知道,助力器釋放力處的跳躍值應(yīng)該大于始動力時的跳躍值。反作用盤的核心作用和性能要求 在真空助力器的工作過程中,反作用盤起著極其重要的作用。真空助力器的工作原理要求,當(dāng)空氣閥口開啟的瞬間,空氣閥柱端面要剛好觸到反作用盤的主面上。又由于反作用盤的材質(zhì)有要求受力表面各處壓強相等的特性,使得伺服力隨著控制閥推桿輸入力的逐漸變化而成固定比例(伺服力比)關(guān)系變化。反作用盤的主面與副面同時受力,且受力的大小與主面和副面的面積成正比。此時,助力器的隨動性最好,反作用盤的使用壽命長。但是,這種理想狀態(tài)在現(xiàn)實中是很難實現(xiàn)的。設(shè)計合理的助力器(間隙配合)的反作用盤又起到了補償作用。當(dāng)空氣閥口開啟的瞬間,空氣閥柱端面沒能觸到反作用盤的主面上,它們之間還有一定的間隙。這時空氣閥口開啟,助力器的應(yīng)用氣室進氣,產(chǎn)生伺服力,反作用盤的副面受力,主面將隆起。當(dāng)主面隆起的高度能夠補償了空氣閥柱與反作用盤主面之間的間隙時,助力器達到了平衡狀態(tài)。反之,設(shè)計不合理助力器當(dāng)空氣閥柱端面觸到反作用盤主面上時, 空氣閥未能開啟,這時反作用盤的主面由于受力而凹下,而副面相對隆起,直到反作用盤的副面隆起的高度能夠使空氣閥口開啟時, 助力器才達到平衡狀態(tài)。 反作用盤材質(zhì)具有的這種即要求受力表面各處壓強相等又能夠產(chǎn)生形變的材質(zhì)特征是真空助力器工作原理的核心原理之一。因此,對反作用盤的性能要求如下:①良好的密封性。反作用盤的過盈量要適當(dāng),過盈量太小不能保證密封性;過盈量太大,反作用盤側(cè)面的摩擦力加大,影響助力器的工作性能。②良好的形變能力。反作用盤的材質(zhì)和形狀要有利于反作用盤的變形。The working principle of the vacuum boosterIn non-working condition, putting control valve return spring to push the valve push rod to the lock lock on the right position, the vacuum valve is fully open, the control valve spring make close contact with the air valve seat, valve skin bowl to shut down the air valve port. At this time of booster air chamber and a gas chamber, respectively, by the piston body true air chamber air chamber channel and application of channel by the valve cavity are interlinked, and isolated atmosphere with the outside world. The engine starts, the engine intake manifold of vacuum negative pressure (engine) will rise to 0.0667 MPA (i.e. air pressure value of 0.0333 MPA, the pressure difference between the atmospheric pressure and 0.0667 MPA). Then, booster air chamber the vacuum degree of vacuum, the application of up to 0.0667 MPA, and work at any time in the ready state.When carries on the brake, the brake pedal is stepped down, pedal force after leverage amplification effect on control valves putter. First of all, putting control valve return spring is compressed, control valves putter along with air valve column moved forward. When the control valve putting forward to the location of the control valve seat contact cup and vacuum, vacuum valve mouth closed. At this point, the vacuum booster, application chamber was separated. At this point, the air valve column end just and reaction plate surface in contact. As control valves putter continues forward, the air valve port will open. Outside air by opening the air valve port after filtered air and access to the developments in the application of air chamber into the application of the booster air chamber air chamber (right), servo power is generated. As a result of the reaction plate force around the surface of the material (rubber) have unit of pressure equal to the physical properties of a request, make the servo as control valves putter input forces increase gradually and become a fixed ratio (servo power ratio). Servo force due to the limited resources, when the maximum servo power, namely the application of air chamber of the vacuum is zero (that is, a standard atmospheric pressure), servo power will become a constant, no longer change. At this point, the booster of the input force and output force will increase amount; Cancel brake, with the decrease of the input power, control valves putter move backward. When the maximum power point, vacuum valve mouth open, after the vacuum booster air chamber interlinked, application, the application of air chamber vacuum will decline, servo power decreases, and the piston body backwards. So as the input force decreases, servo power will also be a fixed ratio (servo power ratio) reduction, until the brake is completely released.The core of the vacuum booster dimension chainIn the design of booster, the design of the core dimension chain is the key for ensuring the performance of the booster, is one of the most critical dimensions with air valve tray column length and the vacuum valve seat to feedback the distance of the primary side (for double diaphragm of the booster, is refers to the vacuum valve port to the end of the piston body convex platform distance convex platform in contact with shaft sleeve end to the shaft sleeve with feedback plate of the sum of transverse distance between the contact surface) and the control valve of the vacuum valve the cooperate relationship between the variables in the shape of mouth.In the working process of the ideal status of the above description, we can notice under the working state of ideal reversal valve to open the mouth of the moment, the air valve column should end just contact and reaction plate, it can be seen in theory established state in reality is impossible. First, the size of each part is it the size of the tolerance zone; Second, a large number of production of a part is in conformity with the statistical rule, the size of the actual interval is a tolerance zone, and the ideal position just in tolerance with a point. So, in the practical design, is how to deal with this contradiction. Its core with the dimension chain's clearance fit. That is to say, the reversal valve opens mouth, air valve column that failed to reach the end of reaction plate contact surface, there is a certain gap. In actual design, to achieve good technical parameters such as dynamic and release force, adopted the clearance fit.The three important working principle of vacuum boosterThe current literature about vacuum booster, is mentioned three working state of the vacuum booster, namely, application state, maintain state, release status. And points out that in the condition of the three, vacuum valve and air valve opening is in a state of open or closed.In addition to the basic principle of the above mentioned, and found in domestic literature mentioned several important principle, that is, the equilibrium position of the three principle, the equilibrium position of the principle of dynamic conversion and the core of the reaction plate.Vacuum booster valve mouth of the three principle of equilibrium positionAutomobile vacuum booster in the process of work there are three equilibrium position, at the time of loading (or braking) the air valve port in the state of brinkmanship, the control valve in the air valve port intangible changes, and vacuum valve closed, control valve in the vacuum valve mouth deformation; When unloading or cancel when braking vacuum valve mouth is in a state of half, the control valve in the vacuum valve mouth intangible changes, and the air valve mouth closed, control valves in the air valve port deformation; When braking stability at some point, the input force no longer changes (i.e., booster is in a state of no movement trend), air valve and vacuum valve are closed, the control valve in the vacuum valve and air valve port in deformation. This is the booster in the working status of the three equilibrium position.The principle of vacuum booster equilibrium position of the dynamic transformationBooster in the working process of the equilibrium position of the principle of dynamic transformation. This is a very easy to be ignored principle, is also in the structure and process design must consider the important principle. When the moment, the end of the load to brake booster will load equilibrium position by steady-state equilibrium position transformation, namely the control valve in the air valve port from intangible variable to have deformation. At this point, the air valve port structure design and processing quality is to meet the requirements of sealing will be subject to strict test; When unloading began to moment, booster will balance position to uninstall from braking stability state equilibrium position transformation, namely the control valve in the vacuum valve port has a deformation by intangible variable transformation. At this point, the vacuum valve structure design and processing quality is to meet the requirements of sealing will be subject to strict test.The actual working process of the vacuum boosterBy the paper as you can see, the working process of the actual and ideal working process is different. Under the condition of the core dimension chain for the clearance fit, combined with the working state of the three theory of equilibrium position. The actual work process of vacuum booster is: brake, the brake pedal is stepped down. Pedal force after leverage amplification effect on control valves putter. First of all, the push rod return spring is compressed, control valves putter along with air valve column moved forward. When the control valve putting forward to the location of the control valve seat contact cup and vacuum, vacuum valve mouth shut, control valve of the vacuum valve mouth from just contact to produce deformation. At this point, the vacuum, the application of air chamber is separated, control valves putter continue forward air valve in the open. At this point, the control valve of the air valve mouth has no deformation. Here is the equilibrium position, when booster booster valve column end haven't the space and time and the reaction plate of the primary side of the contact. As the control valves putter continue forward, air valve will open. Outside air after filtering air by opening the air valve port and through to the channel of the air chamber, into the application of the booster air chamber air chamber (right), servo power is generated. As a result of the reaction plate of primary side without contact with the end of control valve, therefore, booster haven't reached balance. And air chamber into the application of servo force makes the reaction plate side force, so the reaction of primary side uplift, until the servo force produced by vice on the size of the primary side uplift altitude to come in contact with the end face of valve, booster to establish initial equilibrium position. Then, along with the increasing of control valves putter input force servo force into a fixed ratio (servo power ratio). Servo force due to the limited resources, when the maximum servo power, namely the application of air chamber of the vacuum is zero (application of gas chamber pressure for an atmospheric pressure), servo power will no longer be changed. Booster at this time of the input force and output force will increase amount, uplift of the primary side will be under the action of force control valve, gradually reduce the height of the uplift, when enough to the input power, reaction plate of the primary side and even began to sink, the air valve mouth opened the gap is more and more big, the application of the booster air chamber air completely interlinked with the outside world; Cancel brake, with the decrease of the input power, control valves putter move backward, servo power is still a fixed value, control valve mouth open gap smaller and smaller until back to the air valve port just shut down and the resulting deformation. Note here the position of the equilibrium position is not step-down process. As the input force continued to reduce, vacuum valve port will open in the state of vacuum booster valve just at this time in the equilibrium position in the process of decompression. We noticed that the equilibrium position when booster and step-down the equilibrium position when there is a difference, this difference is the control valve in the vacuum valve and air valve and two deformation value of the mouth, namely. As the core dimension chain is clearance fit, the difference makes the reaction plate in the process of booster step-down need more bulge height to achieve balance. After vacuum valve mouth open, the vacuum booster, the application of air chamber are interlinked, vacuum will decline the application of air chamber, servo power decreases, and the piston body backwards. In the process of continuous decompression, the control valve of air valve mouth always have deformation, vacuum valve and control valve mouth has been invisible (state) of brinkmanship. Until the primary side reaction plate force close to zero. At this point, the booster has reached the final equilibrium position. If the valve push rod continues to retreat, booster balance is broken, restore to the original state.This is a sealed vacuum booster test (or, a routine braking process) in the detailed process of vacuum booster work, get to know the process to understand the characteristic curve of the performance parameters of the vacuum booster understanding is very important. In chapter 3 of the calculation of performance parameters of vacuum booster, is based on the process to get. Without the use of clearance fit the calculation of performance parameters of the vacuum booster and curve, and the consequences will be discussed in detail in chapter 4.Should pay special attention to the two concepts are: on a reasonable design of the actual working process of the vacuum booster, there should be the initial equilibrium position and the final equilibrium position of these two concepts. In the characteristic of input - output forces, the embodiment of the two the mechanics relation between the equilibrium position correspond as starting power and release force jump value change process.The concept of vacuum booster two equilibrium positionThe concept of initial equilibrium position: in the process of booster, the air valve port open at the same time, the air valve department failed to touch at the end of the reaction plate, namely the reasonable clearance fit. This air valve to open the mouth, a gas chamber inlet, servo power is generated. Vice surface stress and reaction plate, reaction plate deformation occurs, god will uplift, until the uplift of the primary side in contact with the air valve ends, to reach a stable equilibrium. In this process because of the servo power increase, make the output force (or hydraulic) under the condition of invariable in the input force increases.The final equilibrium position of concept: in the late step-down process, with the loss of the input force, when the stress of the reaction plate of primary side almost to zero, the output of the booster force is produced by the servo power. The servo power at the same time guarantee the reaction plate deformation. At this point, if the valve push rod continues to move backward, because the brake master cylinder does not produce enough resistance and residual servo power phase equilibrium, the reaction plate does not produce enough compensation effect of variables, to maintain the balance of the booster, the booster will lose balance. Followed by vacuum valve will open mouth, servo power is released, the reaction plate deformation disappear, booster recovery to the initial state. Because at the time of loading and unloading valve valve mouth of the equilibrium position shift, can know, booster release force of the dynamic value should be greater than the starting time of the value of jumping.The core of the reaction plate of function and performance requirementsIn the process of the vacuum booster, reaction plate plays an extremely important role. The working principle of vacuum booster, reversal valve mouth open, air valve column face to just touch the reaction on the primary side. And as a result of the reaction plate material has asked stress the characteristics of surface pressure equal everywhere makes servo force with the gradual change of control valves putter input force into a fixed ratio (servo power ratio). Reaction of primary side and the side force at the same time, and the size of the force is proportional to the primary side and the vice area below. At this point, the booster of follow-up, the best reaction plate of long service life. However, this ideal state is difficult to achieve in reality. Reasonable design of booster (clearance) of the reaction plate and had compensation effect. Reversal valve mouth open, air valve column face could not touch the reaction plate on the primary side of, there is still a gap between them. The space-time valve mouth open, and the application of the booster air chamber inlet, servo power, reaction plate side force, god will uplift. When the height of the primary side uplift can compensate the gap between air valve column and reaction plate of primary side, the booster to the state of equilibrium. On the other hand, the unreasonable design of booster reversal valve column end touching the reaction plate on the primary side, the air valve failed to open, the reaction of primary side concave, due to stress and relative uplift side, until t