【溫馨提示】壓縮包內(nèi)含CAD圖有下方大圖片預覽,下拉即可直觀呈現(xiàn)眼前查看、盡收眼底縱觀。打包內(nèi)容里dwg后綴的文件為CAD圖,可編輯,無水印,高清圖,壓縮包內(nèi)文檔可直接點開預覽,需要原稿請自助充值下載,所見才能所得,請見壓縮包內(nèi)的文件及下方預覽,請細心查看有疑問可以咨詢QQ:11970985或197216396
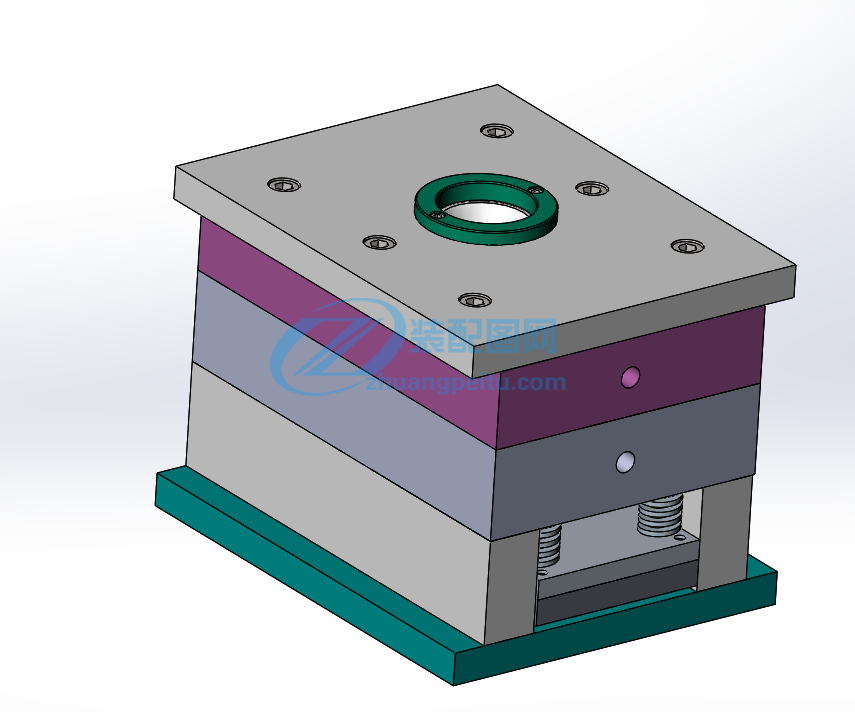
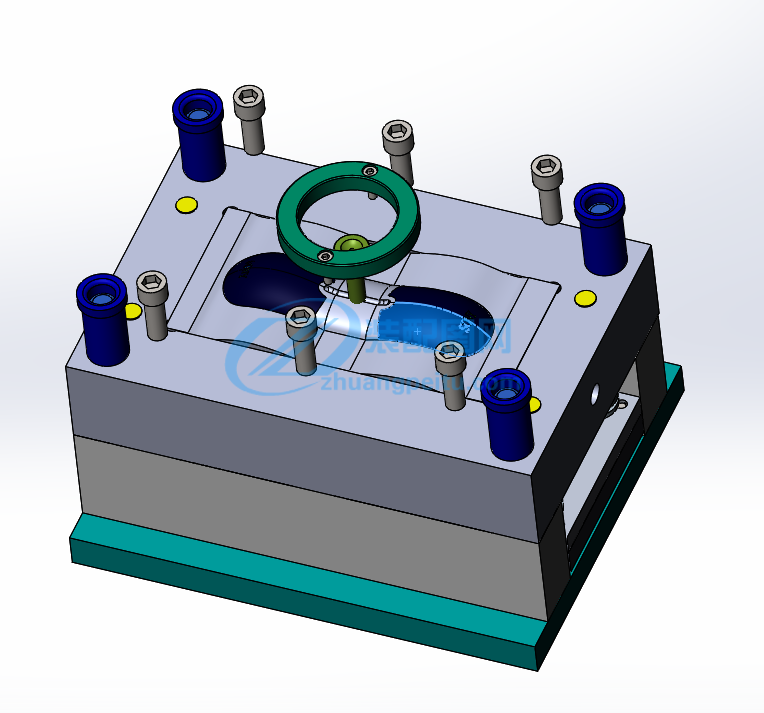
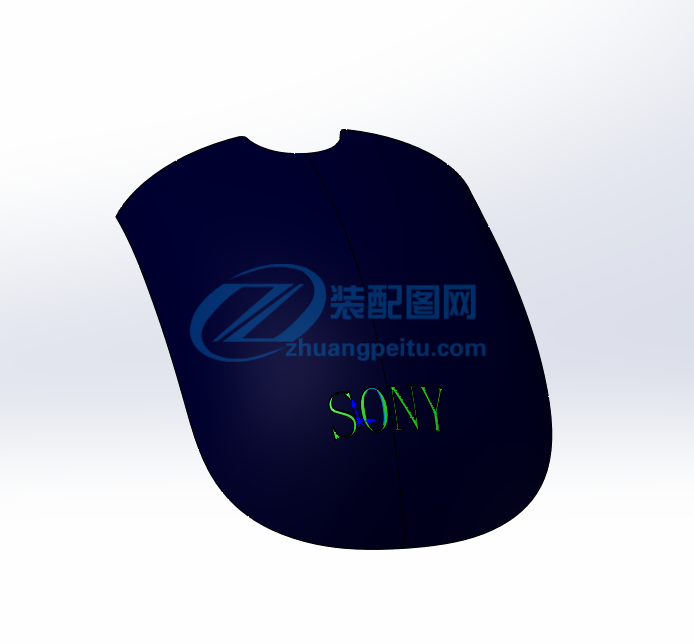
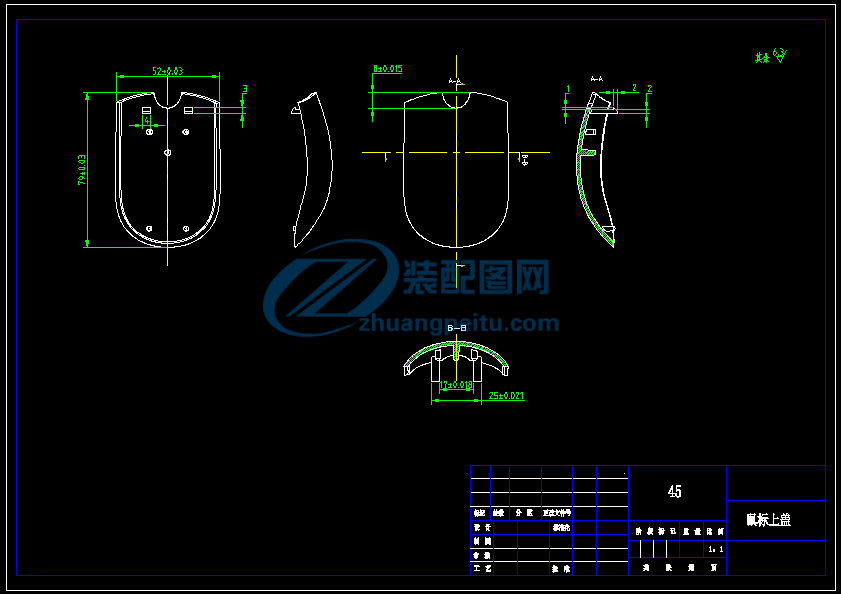
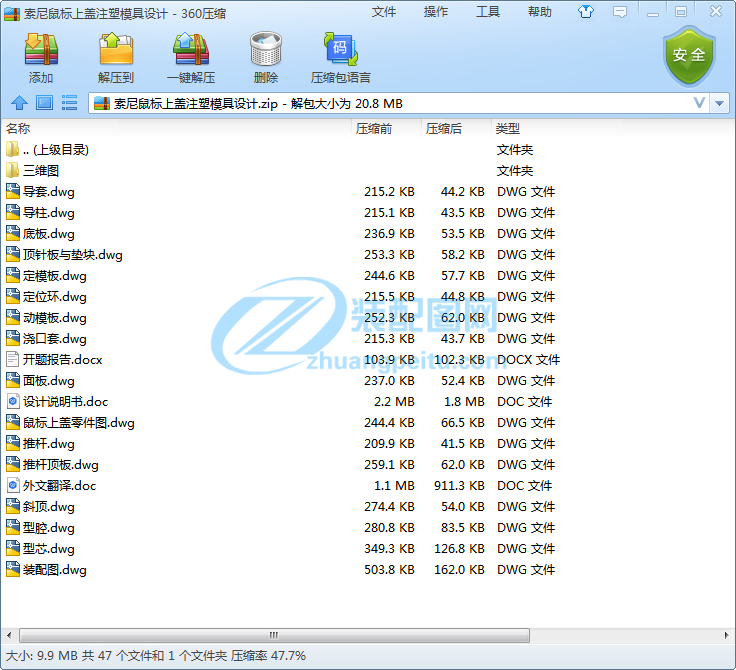
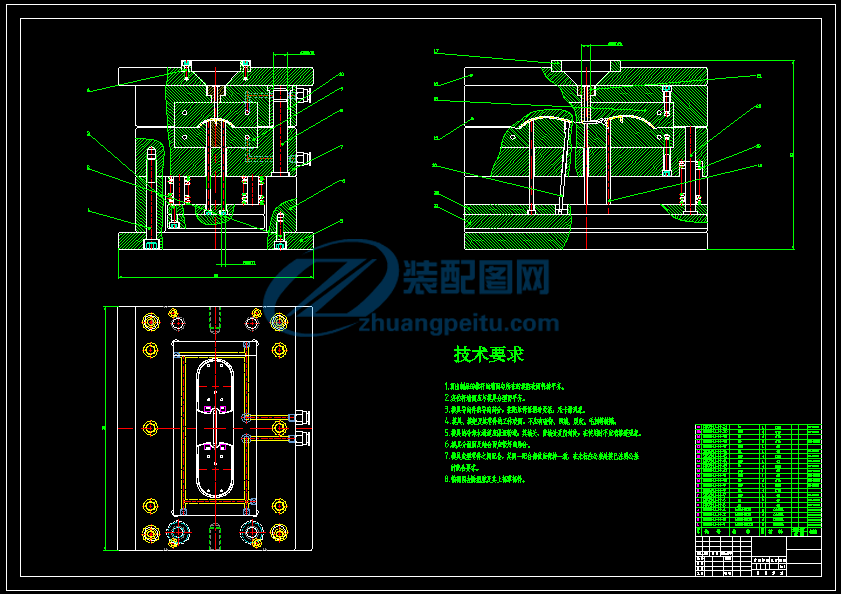
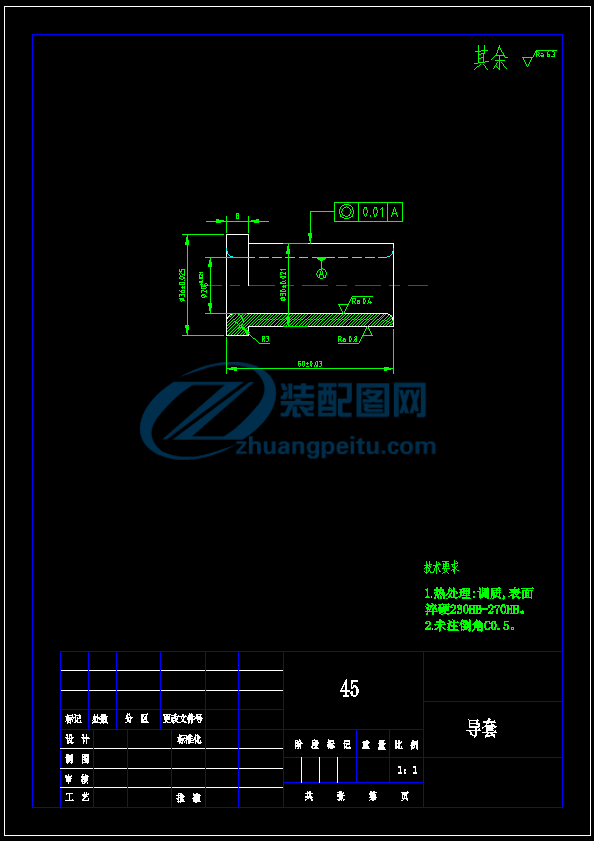
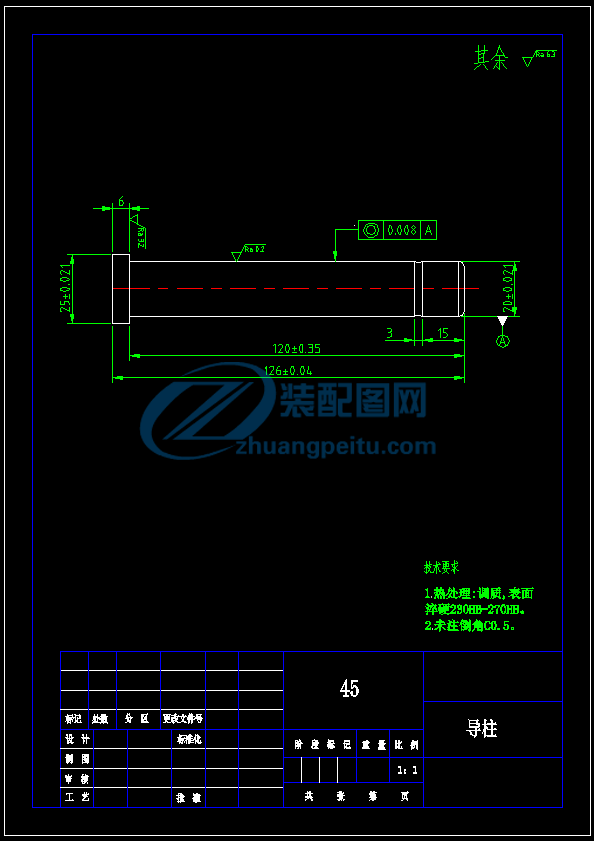
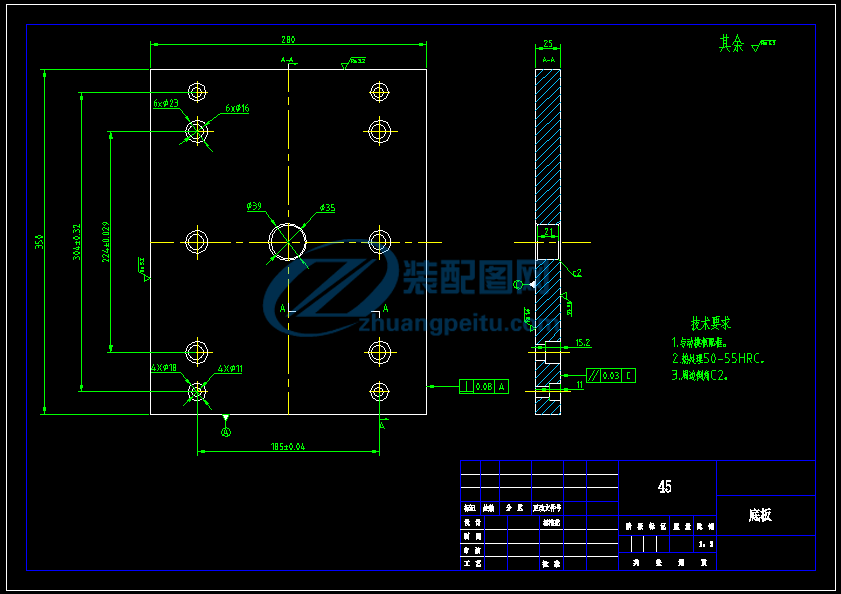
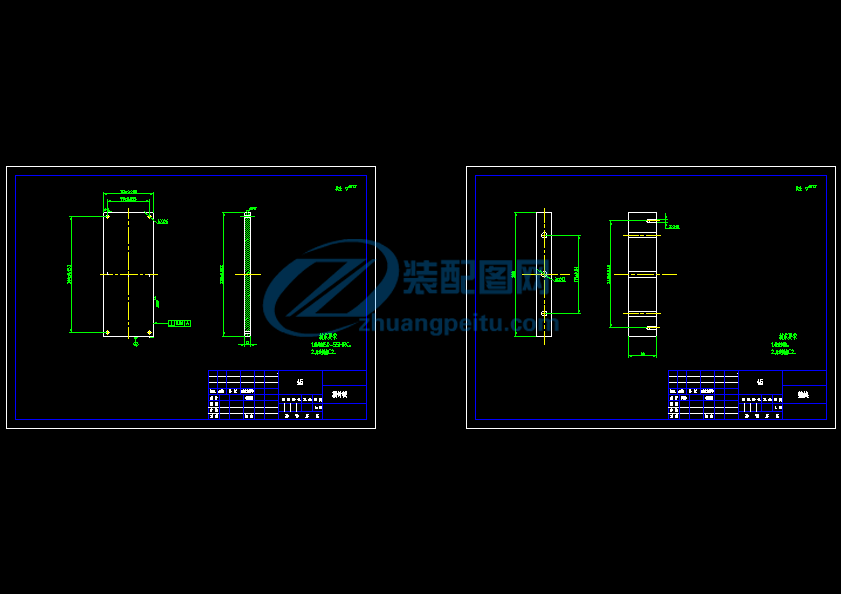
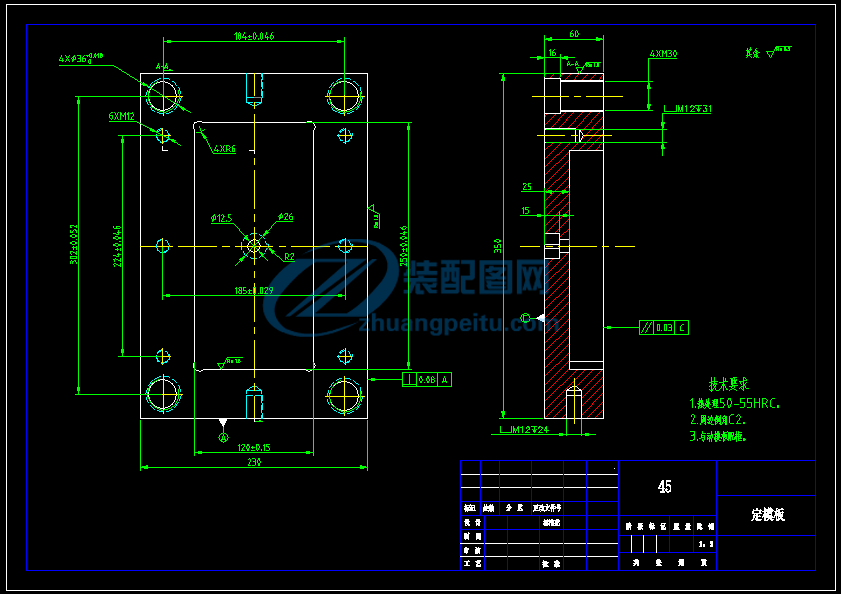
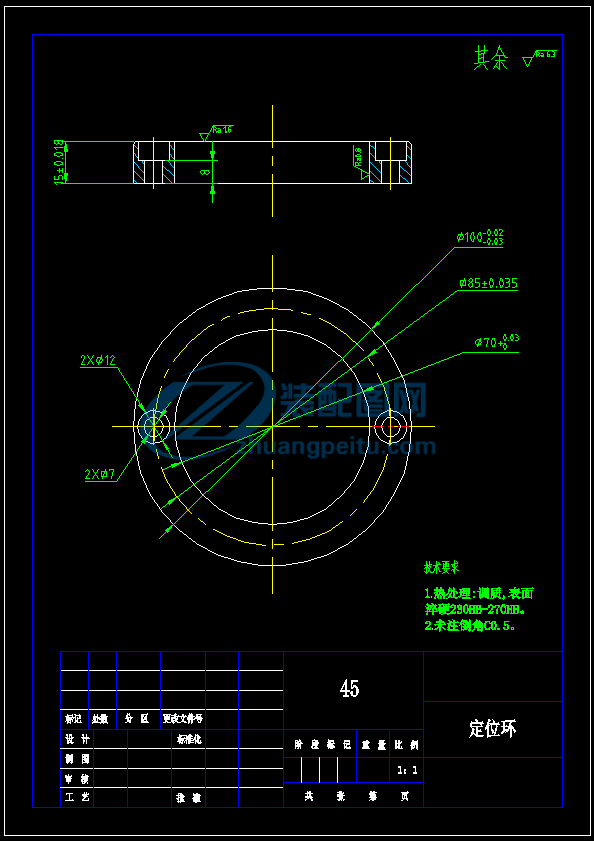
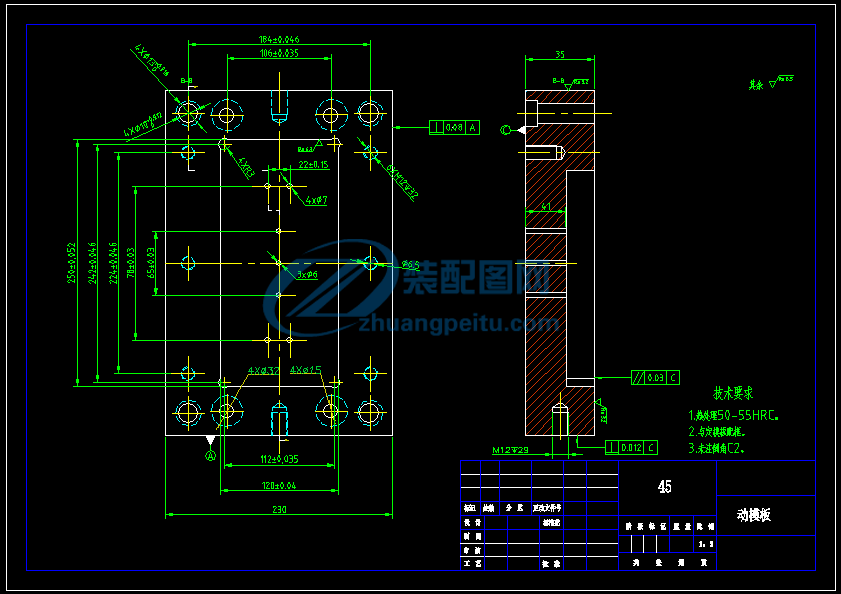
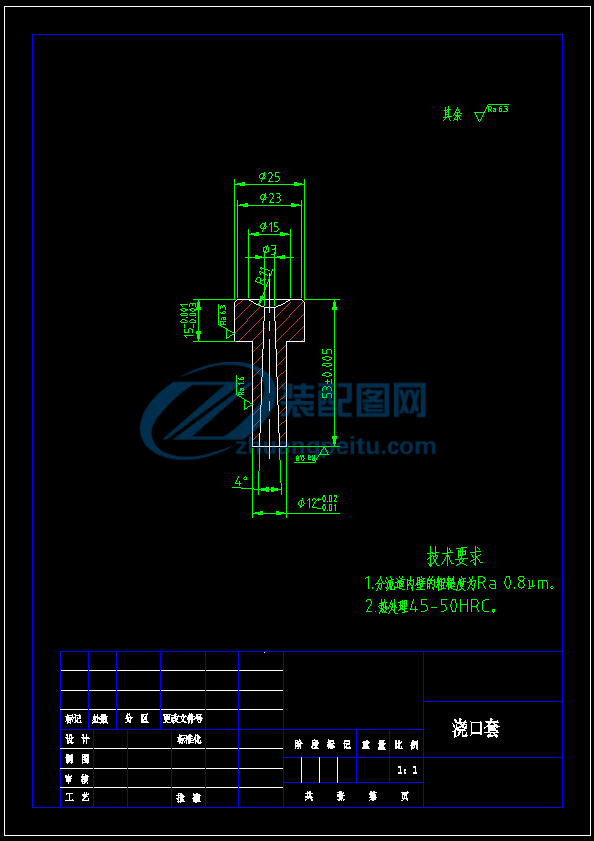
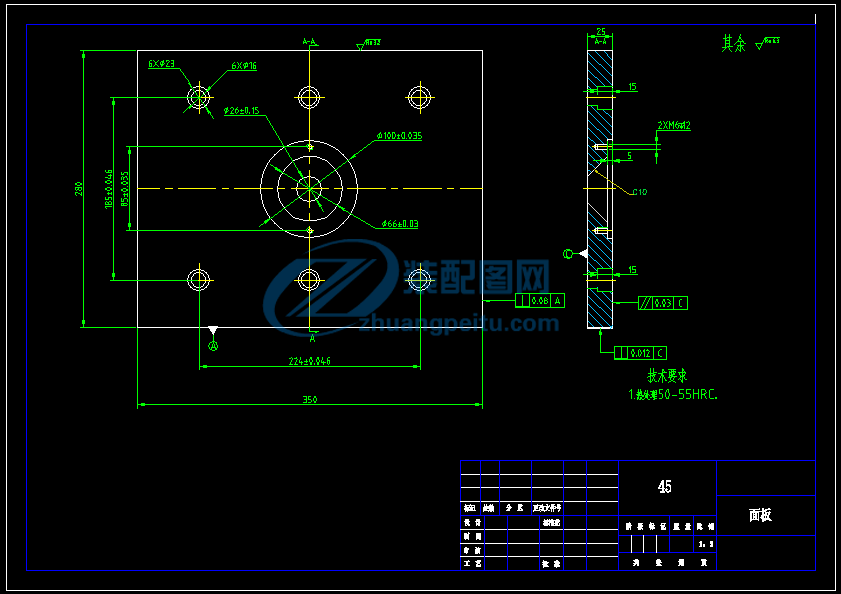
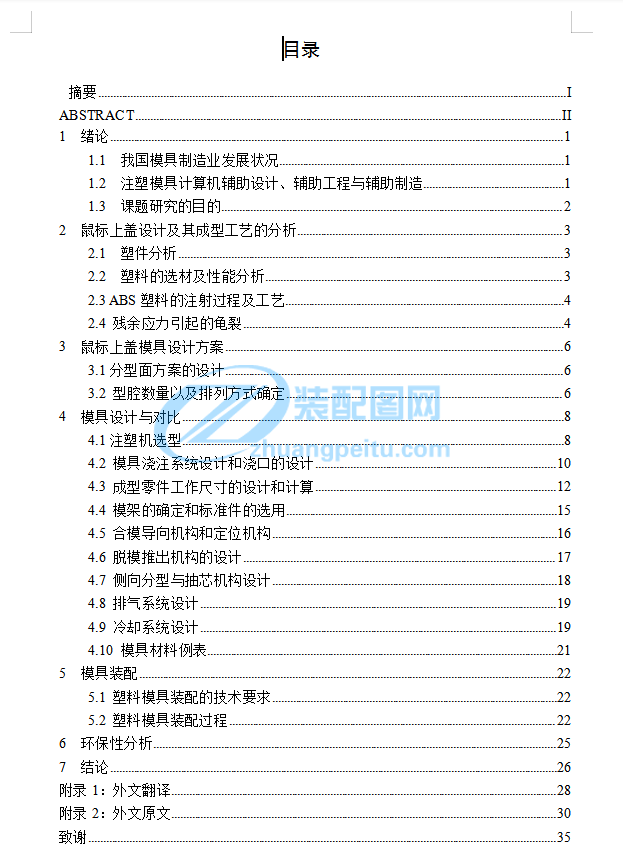
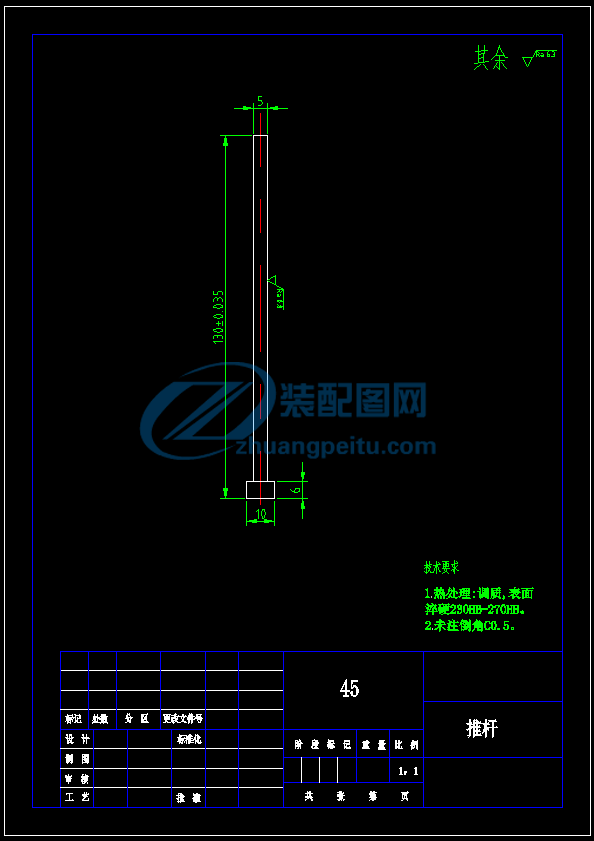
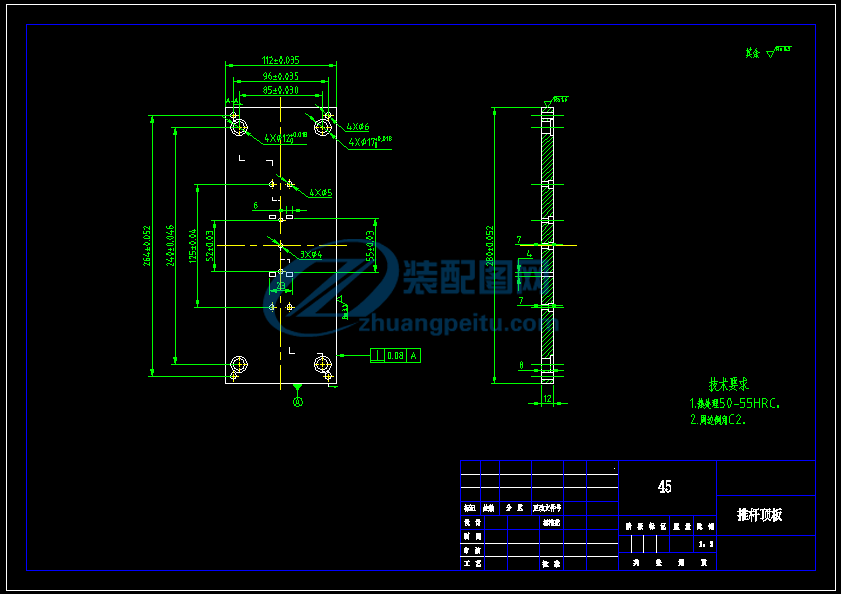
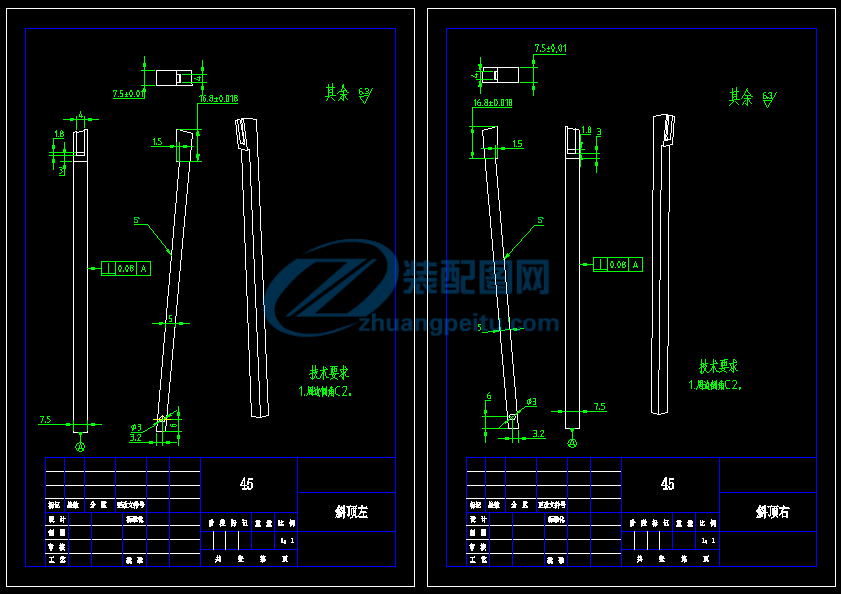
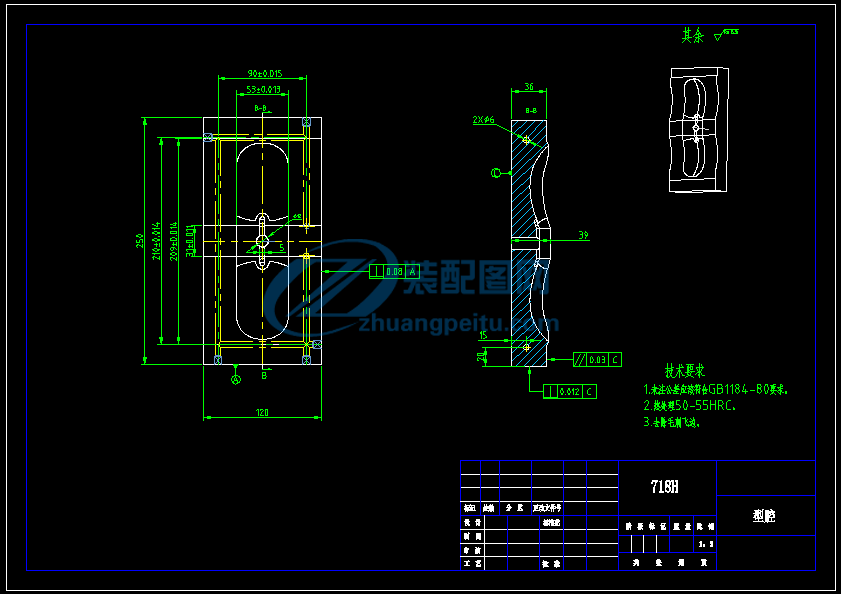
鼠標上蓋注塑模具設計
附錄1:外文翻譯
注塑成型模具的新設計特點
——減少廢料
1.介紹
過去一個世紀觀察到塑料的迅速增長及其向所有市場的擴散。根據(jù)世界原材料消耗量的重量,塑料是最高的與其他舊材料相比鋁,鋼,橡膠,銅和鋅,由其性能和降低生產(chǎn)成本[1,2]。注塑是塑料制品生產(chǎn)中最重要的工藝之一,約占三分之一的所有塑料通過注塑成型工藝轉化成零件[3]。注塑成型的應用工藝在許多行業(yè)如包裝,航空航天和建筑中顯著增加建筑,汽車部件和家用物品[1,3,4]。注射部件的最終質(zhì)量成型取決于材料特性,模具設計和工藝條件[4-6]。有三種注塑成型的基本操作。首先,塑料顆粒將轉變成熔體。然后,熔融塑料將通過澆道,澆道和澆口系統(tǒng)在壓力下注入模腔中最后,模具工具將被打開以將部件從空腔[1,7,8]中排出。
將評估注射部件的質(zhì)量的參數(shù)之一是流道系統(tǒng)。 流道系統(tǒng)是一個澆口和澆口之間的連接線。流道系統(tǒng)的主要目的是轉移熔融塑料澆口到門。在冷流道系統(tǒng)中,廢料的主要來源是在澆注之后來自澆道和澆口系統(tǒng)的廢料。因此,將評估不同的規(guī)則用于轉輪系統(tǒng)設計,以證明轉輪的重要性注塑成型中的系統(tǒng)如(a)較小的流道尺寸以最小化廢料; (b)容易從模具中取出工具和從模制部件中移除; (c)用最小的凹痕和熔接線快速填充空腔[9-12]。將被認為是流道系統(tǒng)設計的基本參數(shù)的三個因素是橫截面流道形狀,直徑和腔體布局[9]。轉輪的橫截面形狀有7種系統(tǒng)為不同的應用[9,10,13]。最后,根據(jù)要求,不同類型的轉輪交叉可以推薦[14]。
本文在考慮現(xiàn)有不同橫截面形狀之后的貢獻是定義流道系統(tǒng)的橢圓幾何形狀作為有效橫截面形狀。我們的基本目標設計和使用本文定義的橢圓形橫截面形狀基本上是具有較小的流道尺寸以最小化廢料,減少注射的總循環(huán)時間并且容易地從模具中彈出部件。除了我們的預期,檢測到與工藝參數(shù)和新的相關的顯著現(xiàn)象將在另一篇論文中討論的轉輪系統(tǒng)的幾何形狀。對于本文,將介紹流道系統(tǒng)的橢圓形或橫截面形狀的設計標準,并進行流道系統(tǒng)的圓形和半橢圓形之間的比較。作者最好的知識,在注塑中已經(jīng)對工藝參數(shù)和材料進行了許多嘗試特征,然而對于包括澆道,澆口和澆道的注射系統(tǒng),存在一些出版物,但沒有提及分析和模擬流道系統(tǒng)的橢圓形橫截面形狀。在本文中,簡單介紹了轉輪系統(tǒng)的結構,并對橢圓轉輪的優(yōu)點進行了評價。然后,注塑部件帶澆道和澆口系統(tǒng)是通過SolidWorks設計的。為了得到準確的仿真結果,通過SolidWorks Plastic有限元法進行考慮。
2.流道系統(tǒng)的橫截面形狀
流道系統(tǒng)的主要目的是通過澆口將熔融塑料從澆口轉移到所有腔體。有流道系統(tǒng)的不同橫截面形狀和它們中的每一種具有不同的應用[13]。設計師應評估不同因素,為特定產(chǎn)品選擇適當?shù)牧鞯老到y(tǒng)形狀。最多兩板模具具有最高效率的流道系統(tǒng)的流行形狀是圓形。適用于Threeplate工具,梯形和修改的梯形是最好的選擇,如果跑步只有在制造一半的模板,但仍然是不能接受的,因為門不能放在一條線上中心流[10]。從具有矩形,正方形和多邊形形狀的腔中推出流道系統(tǒng)具有挑戰(zhàn)性的。它是從不同橫截面的現(xiàn)有拐角產(chǎn)生的。壓降導致如果設計者沒有完全填充空腔和高水平的熱傳遞到模具壁將發(fā)生確定流道系統(tǒng)的適當橫截面形狀及其尺寸[9,13,15]。因此,不同可以考慮流道系統(tǒng)的橫截面來調(diào)節(jié)熔融塑料的流速。最后,形狀和通道的長度對于具有最佳流動和因此具有較少缺陷的最佳產(chǎn)品是重要的[16]。
3.具有橢圓形橫截面形狀的轉輪系統(tǒng)
在注塑成型中,流道系統(tǒng)最常見的截面形狀是圓形。在選擇輪形狀對于特定零件設計,應評估的三個主要元素是(a)較小的流道尺寸,以最小化廢料; (b)更容易從模具中彈出; (c)用最小的凹痕快速填充空腔,焊接線和沒有短射。 [9-11]。因此,考慮用于流道系統(tǒng)的新幾何形狀以最小化廢料,以與門的中央流動流成直線,適當?shù)靥畛湟粋€或多個腔,并且彈出該部分容易從模具工具是本文的目標。最后,考慮橢圓形橫截面形狀轉輪系統(tǒng)。
為了得到具有最小塑料缺陷的注塑部件,進行準確的比較需要在轉輪系統(tǒng)的圓形和橢圓形橫截面形狀之間。為了證明轉子的橢圓形橫截面形狀的意義及其選擇的原因在模具設計中的重要問題,評估其他幾何形狀的澆道系統(tǒng)是必要的。最好的幾何截面來比較圓和橢圓是矩形和正方形。矩形是一種有不同的正方形寬度。根據(jù)不同的應用,將選擇具有不同寬度比的矩形澆道系統(tǒng)。與正方形相比,矩形形狀的優(yōu)點之一是最小化流道系統(tǒng)的廢料,并且更容易從模具中彈出,但是壓降是將會發(fā)生的缺點之一減小方形的寬度[13]。
圓和橢圓之間具有與正方形和矩形相同的結構。 D是圓的直徑,a是長軸長度,b是橢圓的短軸長度。主軸長度固定,短軸長度具有不同的速率,這取決于不同的工業(yè)應用。雖然為減少廢料,更容易將部件排出腔外,并且減少循環(huán)時間,最好減少次要的長度軸,這取決于零件設計。因此,b的不同比率取決于部件設計的許多因素,例如尺寸和厚度。減少廢料,更容易將部件排出腔,循環(huán)時間減少和中心流動的澆口系統(tǒng)與圓形相比具有橢圓形橫截面形狀的優(yōu)點。
附錄2:外文原文
Available online at www.sciencedirect.com
ScienceDirect
Procedia Manufacturing 2 (2015) 241 – 245
2nd International Materials, Industrial, and Manufacturing Engineering Conference, MIMEC2015, 4-6 February 2015, Bali Indonesia
New Design Feature of Mold in Injection Molding For Scrap
Reduction
Mehdi Moayyediana,*Kazem Abharya, Romeo Mariana
aUniversity of South Australia, School of Engineering, Mawson Lakes Campus
Abstract
This paper presents a new cross sectional shape of runner system in the injection molding. The aim of the new geometry is to reduce the scrap and cycle time and also the easier ejection of runner system from mold tools. Short shot defect in the plastic part during the injection molding process is analyzed by SolidWorks Plastic to validate the new proposed geometry. Runner system with elliptical cross section is proposed with different ratio for two circular flat plates with thickness of 1mm. Finite Element Method (FEM) is employed in SolidWorks Plastic for simulation of injected part. Filling time, melt temperature, mold temperature, pressure holding time, and pure cooling time are chosen as input for the injection machine. The contribution of this study is the design of new geometry of cold runner system for reduction in scrap and cycle time and also easier ejection of runner system in injection molding. This study outcomes show no short shot defect with the new geometry. Also, it was shown the significant reduction in scarp and cooling time. 25% and 2.5% reduction in scrap and cooling time were achieved compared to round cross section, respectively. Reduction in contact surface of runner system with mold walls improved the easier ejection of runner system out of the cavity as well.
? 2015 The Authors. Published by ElsevierB.V. This is an open access article under the CC BY-NC-ND license
? . by B.V.
(http://creativecommons.org/licenses/by-nc-nd/4.0/).
Selection and Peer-review under responsibility of the Scientific Committee of MIMEC2015.
Selection and Peer-review under responsibility of the Scientific Committee of MIMEC2015
Keywords:Injection molding process, Mold design, Runner geometry, Short shot defect
1. Introduction
The past century has observed the rapid increase of plastics and their proliferation into all markets. According to world consumption of raw materials by weight, plastic is the highest in comparison with other old materials such as aluminum, steel, rubber, copper, and zinc, resulting from its properties and lower production cost [1, 2]. Injection
* Mehdi Moayyedian. Tel.: +61883025561
E-mail address: Mehdi.moayyedian@unisa.edu.au
2351-9789 ? 2015 The Authors. Published by Elsevier B.V. This is an open access article under the CC BY-NC-ND license (http://creativecommons.org/licenses/by-nc-nd/4.0/).
Selection and Peer-review under responsibility of the Scientific Committee of MIMEC2015 doi:10.1016/j.promfg.2015.07.042
242 Mehdi Moayyedian et al. / Procedia Manufacturing 2 (2015) 241 – 245
molding is one of the most significant processes for manufacturing of plastic products and approximately one-third of all plastics are converted into parts using injection molding processes [3]. The application of injection molding processes is increasing significantly in many industries like packaging, aerospace and aviation, building and construction, automotive parts and household articles [1, 3, 4] . the final quality of injected parts in injection molding depends on the material characteristics, the mold design and the process conditions [4-6]. There are three fundamental operations in injection molding. First, the Plastic granules will be converted into a melt. Then, the molten plastic will be injected into the mold cavity or cavities under pressure via sprue, runner and gate systems and finally, the mold tools will be opened to eject the part from the cavities [1, 7, 8].
One of the parameters which will assess the quality of injected part is Runner system. Runner system is a connection line between sprue and gates. The main purpose of runner system is to transfer the molten plastic from sprue to gates. In cold runner system, the main source of scrap is the scrap from runner and gate system after de-gating. Hence, different rules will be evaluated for runner system design to demonstrate the significance of runner systems in the injection molding such as (a) smaller runner size to minimize the scrap; (b) easy ejection from mold tools and removal from molded parts; (c) filling the cavities quickly with minimum sink marks and weld lines [9-12]. Three factors which will be considered as fundamental parameters for runner system design are cross sectional shape of runner, the diameter and the cavity layout [9]. There are 7 types of cross sectional shapes for runner systems for different applications [9, 10, 13]. Finally, depending on the requirements, different types of runner cross sections can be recommended [14].
The contribution of this paper after the consideration of existing different cross sectional shapes is to define the elliptical geometry for runner system as an effective cross sectional shape. Our fundamental objectives, for designing and using the elliptical cross sectional shape defined in this paper, are basically to have smaller runner size to minimize the scrap, to reduce the total cycle time of injection and to eject the part easily from the mold tools. Further than our anticipation, remarkable phenomena was detected which are related to process parameters and new geometry of runner system that will be discussed in another paper.
For this paper, the design criteria of elliptical or cross sectional shape for runner system will be introduced, and a comparison between round shape and semi-elliptical shape of runner system will be conducted. To the authors best of knowledge, many attempts have been taken in injection molding for process parameters and material characteristics, however for injection system which includes runner, gate, and sprue, there are a few publications, but there is no reference to analyze and simulate the elliptical cross sectional shape of runner system. In this paper, the structure of runner system is simply introduced and advantages of elliptical runner will be evaluated. Then, the injected part with runner and gate system is designed via SolidWorks. For accurate result of simulation, FEM is considered via SolidWorks Plastic.
2. Cross sectional shape of runner system
The main purpose of runner system is to transfer the molten plastic from sprue to all cavities via gate. There are different cross sectional shapes of runner systems and each of them have different applications [13]. A designer should evaluate different factors for selecting the right shape of runner system for a specific product. The most popular shape of runner system which has the highest efficiency for two plates mold tools is round shape. For Three-plate tools, the trapezoidal and modified trapezoidal are the best options if the runner is to be manufactured only in one half of the mold plates, but still they are not acceptable because the gate cannot be positioned in line with the central flow stream [10]. Ejecting a runner system from the cavity with rectangular, square, and polygon shape is challenging. It has resulted from the existing corners of different cross sections. Pressure drop which leads to incomplete filling of cavities and high level of heat transfer to the mold walls will occur if a designer does not determine the appropriate cross sectional shape of runner system and their dimensions[9, 13, 15]. Hence, different cross-sections of runner system can be considered to regulate the flow rate of molten plastic. Finally, the shape and the length of the channel are significant to have an optimal flow and therefore the best product with less defects [16].
3. Runner system with elliptical cross sectional shape
6
In injection molding, the most common cross section shape for runner system is round shape. In selecting the round shape for specific part design, three main elements which should be evaluated are (a) smaller runner size to
Mehdi Moayyedian et al. / Procedia Manufacturing 2 (2015) 241 – 245
243
minimize the scrap; (b) easier ejection from mold tools; (c) filling the cavity quickly with minimum sink marks, weld lines and no short shot. [9-11]. Hence, consideration of new geometry for runner system to minimize the scrap, to be positioned in line with the central flow stream of gate, fill the cavity or cavities properly, and eject the part easily from mold tools is the goal of this paper. Finally, elliptical cross sectional shape is taken into account for runner system. In order to yield an injection-molded part with minimal plastic defects, an accurate comparison between round and elliptical cross sectional shape of runner system is necessary.
To demonstrate the significance of elliptical cross sectional shape of runner and the reason it is selected as a significant issue in mold design, evaluation of other geometries of runner system is necessary. The best geometry of cross section to compare the circle and ellipse is rectangle and square. Rectangle is a kind of square with different width. According to different applications, rectangular runner system with different ratios of width will be chosen. One of the advantages of rectangular shape in comparison with square is in minimizing the scrap of runner system, and easier ejection from mold tools, but pressure drop is one of the disadvantages which will be happen by decreasing the width of the square [13].
The comparison between circle and ellipse has the same structure with square and rectangle. D is the diameter of circle, a is major axis length, and b is minor axis length of ellipse. Major axis length is fixed and the minor axis length has different rates which depend on different industrial applications. Although for reducing the scrap, easier ejection of part out of cavity, and reduction in cycle time it is better to reduce the length of the minor axis, it depends to the part design. Hence, different ratio of b depends on many factors of part design such as size and thickness. Reduction in scrap, easier ejection of part out of cavity, cycle time reduction, and central flow stream of gate with runner system are the advantages of elliptical cross sectional shape in comparison with round shape.
4. Simulation
After designing two circular parts as two samples for this application, the next step is to simulate the part using SolidWorks Plastic. For simulation part, defining the injection system is necessary. Hence, designing the sprue, runner with b=0.7a and gate system is considered as shown in Fig. 1a. To make sure that the analysis results are accurate, Finite Element Analysis (FEM) will play a significant role in simulation as shown in Fig. 1b. According to the geometry of samples, the triangle shape of surface meshes for finite element analysis will be chosen. The selected material for this simulation is polypropylene (P.P). Different sizes were evaluated for the surface mesh and finally surface mesh size of 1mm are chosen for injected part but for the injection system which include sprue, runner and gate, smaller sizes were considered, resulting from the sensitivity of injection system as a critical area of this simulation. Hence, surface mesh size of 0.3mm for sprue and runner and 0.2mm for gate are selected for both elliptical and round cross sectional shape of runner in SolidWorks Plastic. The runner and gate length in total is 28mm for two circular parts with diameter of 100mm. Also, the sprue has 60 mm length with draft angle 1.5°.
(a) (b)
Fig.1 (a) Finalized part with sprue, runner and gate system; (b) Finite element analysis of finalized part
The next step is to define the process parameters. Based on the selected materials and injection machine, filling time is 0.59 sec , melt temperature is 230°C, mold temperature is 50°C, pressure holding time is 2.04 sec, and pure cooling time is 3.9 sec. The geometry and size of the injection system are evaluated as significant criteria whose effect the operation cycle time, cooling time, different defects such as sink mark and short shot. The main factors to check if the new runner system is acceptable in terms of new geometry and size, are ease of fill, filling time analysis, sink mark analysis, and injection pressure at the end of injection. As shown in Fig. 2a, ease of fill for elliptical cross section is at green area which is in the most acceptable level. Another common defect which is related to gate and runner dimension and geometry is sink marks. A sink mark is the depression on the surface of
244 Mehdi Moayyedian et al. / Procedia Manufacturing 2 (2015) 241 – 245
injection molded plastic which occur during the cooling process [17]. As shown in Fig. 2b, there is no sink marks for the injected part except for the sprue which is not in a critical region and also the surface quality of sprue and runner are not significant because they consider as scrap at the end of the injection. Therefore the surface quality of injected part for both round and elliptical cross section is the same.
(a)
(b)
Fig. 2 (a) Easy filling of injected part with elliptical cross; (b) Sinks marks simulation for elliptical cross sectional shape of runner system
One of the common defects in injection molding is short shot. Short shot will occur far from the gate if there are long flow distances or on thin walls [17]. According to the simulation result, this part can be successfully filled and even the filling time for elliptical cross sectional shape of runner is lower than that of for the round cross sectional shape as shown in Fig. 3.
(a) (b)
Fig. 3 Filling time for (a) Elliptical cross section and (b) Round cross section
Another parameter to make sure that there is no short shot for the injected part is to evaluate the flow front central temperature which represents the flow front temperature at every region of injected part. SolidWorks Plastic recently added this module which is suitable for short shot analysis. As shown in Fig. 4, based on SolidWorks Plastic simulation, the flow front central temperature in every region of the injected part is 230.15°C for both elliptical cross sectional shape of runner and round cross sectional shape. It means that the possibility of short shot in the cavities is low for both geometries.
(a) (b)
Fig. 4 Flow front central temperature for (a) Elliptical cross section and (b) Round cross section
One of the most significant parameter which is necessary to evaluate for determination of the right size of runner and gate system is the maximum inlet pressure. This part can be successfully filled with injection pressure 42.1 MPa. The injection pressure is less than 66% of the maximum injection pressure limit which is satisfactory as shown in Fig. 5. The injection pressure for round cross section is 39.655 MPa which is close to elliptical cross
Mehdi Moayyedian et al. / Procedia Manufacturing 2 (2015) 241 – 245
245
section.
50
Pressure
40
30
MaximumInlet
(Mpa)
Round
20
10
Elliptical
0
0
0.5
1
Time(Sec)
Fig. 5 Injection pressure for both round and elliptical cross section shape of runner system
5. Conclusion
The main reason of scrap in cold runner system of injection molding is the feeding system which consists of sprue, runner and gate system. Runner has different cross sections for different applications. In this study, new geometry of runner system with elliptical cross section in comparison with round cross section was successfully developed for injecting two circular plates with thickness 1mm. filling time, melt temperature; mold temperature; pressure holding time and pure cooling time are evaluated as process parameters.
Elliptical cross section in comparison with round cross section which has the highest efficiency among current geometries of cross section has 25% reduction in scrap and 2.5% in cooling time for injected parts. The result from simulation demonstrates that the elliptical cross sectional shape of runner is an effective geometry to reduce the scrap and total cycle time and also the easy ejection of molded part out of the cavity. It demonstrates the robustness of new geometry of runner system. Further than our anticipation, remarkable phenomena was detected which is related to process parameters and new geometry of runner system that will be discussed in another paper. The experimental set up will be conducted to justify the simulation result.
References
1. Zhou, H., Computer Modeling For Injection Molding. 2013: A John Wiley & Sons, Inc., Publication.
2. Salimi, A., et al., prediction of flow length in injection molding for engineering plastics by fuzzy logic under different processign conditions. 2013.
3. Tang, S.H., et al., Design and thermal analysis of plastic injection mould. Journal of Materials Processing Technology, 2006: p. 259-267.
4. Altan, M., Reducing shrinkage in injection moldings via the Taguchi, ANOVA and neural network methods. 2010: p. 599-604.
5. Khoshooee, N. and P.D. Coates, Application of the Taguchi method for consistent polymer melt production in injection moulding.
1998: p. 611-620.
6. ShijunNi, Reducing shrinkage and warpage for printer parts by injection molding simulation analysis. 2002: p. 177-186.
7. Dai, W., P. Liu, and X. Wang, An Ipproved Mold Pin Gate And Its Flow Pattern In The Cavity. journal of injection moulding technology, 2002: p. 115-119.
8. Hassan, H.