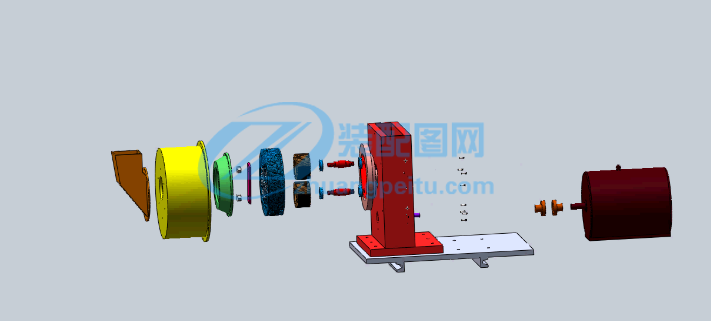
畢 業(yè) 設(shè) 計(jì)(論 文)外 文 參 考 資 料 及 譯 文
譯文題目:Wet granulation in a batch high shear mixer
學(xué)生姓名:
學(xué) 號(hào):
專 業(yè):
所在學(xué)院:
指導(dǎo)教師:
職 稱:
abstract
This study deals with the wet granulation in a high shear mixer. The experimental apparatus is a laboratory scale ”L?dige” granulator,with a maximum volume of 20 l, equipped with a chopper and a pneumatic spraying system. The main objective of the study is to point out the effect of physico-chemical properties and operating conditions on the growth mechanisms and kinetics in this type of granulation device. Two kinds of alumina with different particle size distributions (alumina SH100 and alumina SH30) were granulated using various Newtonian liquids having different surface tension, viscosity, binder concentration, density, etc. (water, aqueous solutions of polyethyleneglycol or polyvinyl alcohol). Experimental results showed that the granulation process generally proceeds through three distinct growth regimes independent of the nature of the powder, the binder liquid or the operating conditions. However, the transition between different regimes depends on the physico-chemical properties of the solids and liquids, on operating conditions and on the experimental procedure. For the alumina powder used in this study the transition occurs when a degree of liquid saturation of about 68% is reached.
Keywords: wet granulation machine; growth mechanism; high shear mixer; L?dige; alumina
1. Introduction
Granulation is a size enlargement process widely used in several branches of the chemical industry. The aim of this operation could be to improve flowability, appearance or proportioning of powders or to avoid dust production,etc.
Among all existing size enlargement operations, wet granulation in high shear mixers is particularly interesting as it allows one to obtain regular shaped granules with a high degree of compaction. The process uses a liquid species, called the binder, to hold particles together while they are mixed by mechanical agitation.
Since the pioneering works of Newitt and Conway-Jones (1958) and Capes and Danckwerts (1965) wet granulation has been a subject of fundamental and applied research.
Number of books and review papers are available, which summarise the state of the knowledge in this field (e.g. Iveson et al., 2001; Kapur, 1978, Capes, 1980; Pietsch, 1991;Ennis et al., 1991; Hoornaert et al., 1998; Rumpf, 1962; Leuenberger et al., 1979, Kristensen et al., 1985a,b). The various mechanisms involved in wet granulation are known to be wetting and nucleation; consolidation and growth; and breakage and attrition. However, the theoretical aspects of the granulation are not sufficiently understood to quantitatively predict the effect of physico-chemical properties and operating conditions on the growth rate and dominant mechanism.
Leuenberger et al. (1979) was the first to find an agreement between the tensile strength as a function of the degree of saturation and the power consumption profile ofthe mixer motor when adding progressively a liquid to the powder mass.
Nevertheless, Ennis et al. (1991) recently found that capillary forces play the principal role only in low viscosity systems. For more viscous binder liquids the viscosity should be recognised as an important parameter in controlling granulation behaviour. These authors developed a microlevel-based model to take into account the effect of viscous dissipation on the strength of a dynamic pendular bridge formed by a Newtonian liquid.
2. Experimental
2.1. Experimental set-up
Experimental apparatus used in this study were 1 represents. This means having a total volume of 20L batch L?dige mixing equipment and is equipped with a water flow downward pneumatic spray system. All parts are made of stainless steel. The mixing chamber is a bedroom cylindrical bowl. Four radial mixing impeller driven by a motor shaft support level distribution at 90 degree angle mounted on the ploughshare shovel. Stirring speed of the impeller can be transferred from 0-230. On the bowl is also equipped with an installed base of tulip shaped rotary chopper. In operation, the chopper speed at 2800 rpm, the opening at the top of the bowl allows loading and emptying the mixer. After the required amount of powder and loading hatch cover to prevent dust distribution. In addition, the cover support atomizer system is an internal two-fluid nozzle flat jet produced as 80 degrees.
Creep pump from the reservoir for storing (kept at 25 degrees) to the nozzle feed granulation liquid.
figure 1
2,2 material
Experiments using two commercial alumina granulator for type SH100 and sh30 were two products they include non-porous and irregular shaped particles. Before granulating machine experiment, particle size distribution and density prior to using Malvern Mastersizer analyzer and helium pycnometer Determination, some details are provided in Table 1 against the two products physical properties.
Table 1
Several Newtonian liquid adhesive is to be used. Their properties are summarized in Table 2. Use pycnometer liquid density measurement. Using a capillary rheometer to measure liquid viscosity. The surface tension of the liquid and solid - liquid contact angle is measured using a krypton üSS K1 tension Wilhelmy plate method and Washburn meter capillary rise method used.
Table 2
2,3 Experimental Procedure
Before granulator experiments, the powder is introduced into the mixer granulator and to the same conditions of use in a mixed state. A complete granulation process consists of two steps:
he amount of granulation liquid required during ? "crush" or wetting step at a constant flow rate control and sprayed into the mixer.
"Mature" maintained by the pulverization step after mixing components. It should be noted that only a limited number of mature step study experimental operation.
After each operation, the entire granulated product is removed from the mixer and tested to determine the following standard granulators: the intensity distribution within the particle porosity and saturation (DLS).
2,3,1 particle size distribution
The wet granules are screened for analysis, allowing determination of the particle size distribution of the mass, which in turn is estimated to be allowed.
? mass median diameter D50mm, an average diameter of the particles, which is found in 50% of the flour mass smaller diameter particles. The diameter is calculated from the cumulative particle size distribution come.
? fine, intermediate and rough parts are arbitrarily defined. While most of the size of the particles are smaller than 0.315mm, 0.315mm and between 3.15mm, greater than 3.15mm, the middle part of it is the corresponding products for the market
In addition, the particle diameter distribution of the particles measured by the number of subdivisions established Malvern Mastersizer analyzer using a dry method.
2,3,2 The average particle density and performance of intermediate porosity
We point out that the performance of the particle density is a non-binder particles include the proportion of the volume and quality voids within the particles. To measure this parameter, first, a wet granulation is screened through a sample was distilled into the narrow sections, each separately be analyzed according to the order of about: wet granules significant samples (at least 250) to calculate and dried in 60 ° oven 24 coax hour. Assuming a uniform density and particle filter diameter spherical particles, the apparent density of the particles is calculated by the following equation:
(1)
wherein n is the number of particles in the analysis sample, c is the dry granulation liquid may contain in mass fraction (solute), dˉ study population average particle size of the particle, mw and md are wet and oven-dried sample weight .
Then with particle porosity within the computing
(2) where s is the true density of the dried powder, which is measured with a helium pycnometer experimentally determined.
2,3,3 liquid saturation
DLS particle is defined as the granulation liquid occupies a whole section of the particles within the space, this parameter is calculated by the following formula:
(3)Where is the density of the liquid granulator.
It is worth noting that saturation must be distinguished from liquid / solid ratio, L / S, which is the introduction of the total mass of the liquid and powder ratio definition.
3. Results and discussion
A series of operating conditions are summarized in Table 3. In this study experiments. Note that, a series of experiments including an increase of granulation liquid (ceteris paribus) the number of runs, resulting in a longer time scale of the development of the data generation of particles.
table 3
3,1 granulated Profile
Figure 2 shows the particle size distribution of the liquid / solids ratio of the function of the evolution of a typical, L / S, the data presented in Figure 2 can be seen from, L / S ratios as high as the distribution size distribution 20.7% w / w of the particles did not change significantly, more than the value of the particles gradually accelerating growth, reducing the number of segments, the size distribution of the ratio L / S of nearly 24% by wide until the "lumps" or too wet phenomenon.
Figure 2
To understand the mechanism of production of particles, there are three types of evolution: thin (less than 0.315mm), coarse (greater than 3.15mm) and the intermediate particles in Figure 3 shows the average diameter. When the ratio L / S increases three consecutive Trend Watch: wherein when the ratio of fine and coarse particles substantially constant first public method, followed by the second method, the second method in which the proportion of fine particles and other reduction of two match. However, the median diameter and L / S no major development. As well as a sharp increase in the proportion of the ratio of the value of the average particle diameter and L / S Finally, the third method is observed large particles.
It is noteworthy that, unfortunately, can not be studied at low L / S ratio of granulated behavior because of low mechanical strength of the particles in the screening process, resulting in a high turnover rate. However, taking into account the maximum size of less than SH100 alumina particles 40 microns, which can be evidenced by the zero method granulator previously existing "core" steps are appropriate.
Introduction described herein three pellet mill is all experimental observation of unrelated powder, liquid adhesive, or operating conditions. However, the conversion between different methods depending on the liquid adhesive and the environment created by the mixer (i.e. impeller speed, chopper operation or not operation, etc.). Also important is the transition zone L / S ratio Note that the second and third methods of narrow spacing between places. The reason is that the second method occurs later we can see a small saturation range (75-90%).
3,2 granulation mechanism
image 3
In fact, the conversion between different mechanisms is obvious, and their growth trend is clearly different, suggesting a variety of mechanisms have different primary mechanism components. To point out that these mechanisms are useful inspection, in addition to the distribution, the interior of the porous particles change in particle size, DLS (FIG. 4) as well as the thickness dimension granulated in a granulator distribution (FIG. 5).
3,2,1 a mechanism
Figure 4 illustrates a first mechanism, the intra-particle porosity decrease almost linearly with increasing liquid saturation. On the other hand, FIG. 6 shows an SEM image of the obtained intermediate particles corresponding to the L / S ratio of the first three different mechanisms, 14.3%, 17.1% and 20.0%. As can be seen, in the first mechanism, the shape and orientation of the particles is not largely different. Thus, it can be concluded in the first mechanism is the main mechanism under shear agitation impeller of a particle densification. This conclusion is supported by the fact that, whether partial or intermediate average diameter of the particles in the first mechanism remains unchanged (Fig. 3).
However, densification is not the only mechanism leading growth, because it can not explain the fine surface also gathered in the L / S ratio is greater than 17.1% of the median particle surface. Thus, in the first mechanism in L / S ratio increases at a high value of densification, agglomeration occurs between the intermediate and fine particles. However, a surprising phenomenon in the first part of the mechanism of fine particles does not change a lot, which means to produce fine particles mainly of fine particles from the broken left intermediate equilibrium particles. As it can be seen from Figure 5, the L / S ratio of at least bimodal particle size distribution. The larger the number of focus 100 microns, but more sophisticated model number from the L / S ratio of 30 microns to 50 microns 14.3% of the L / S ratio of 17.1%. When L / S ratio increases, however small feature reduces the increase in the proportion of the second part features. In view of the SEM image shows fine characteristics of the second level is not caused by the finer particles; we can conclude that, from the characteristics of the second intermediate particle breakage portion. As a first characteristic, since the median particle group promotions, it disappears, this conclusion is confirmed by scanning electron microscopy (FIG. 6), which indicates that the adhesion of fine particles in the intermediate size is close to the first level. Please note that this phenomenon does not affect the average porosity of the particles in the liquid and saturation (Figure 4). The results showed that the wettability and having a particle densification occurs in all classes and in a similar manner. This balance between the two phenomena (by preferentially binds to disappear by forming a first characteristic and a second characteristic of the particle fracture) reported with the experimental described here by chance, can not be generalized. In fact, as we can see in the back, as at higher impeller speed, the relative amount of the second characteristic of fine particles of the first characteristic is growth.
Figure 4
Finally, and most importantly, when the particles to achieve high dynamic light scattering (≈68%), the conversion will take place the first and second methods. At such a high saturation, while some of the free liquid surface is available, the particles may grow further back. Another interesting phenomenon is the liquid saturation and L / S ratio is not linear increases. This is because, in addition to wetting, the densification phenomenon helps to increase saturation.
Figure 5
3.2.2 Mechanism of two
Observation showed that the particle size distribution, particle reduction second mechanism portion and the intermediate portion of the corresponding
Figure 6 A(17.1%) B(20.0%) C(20.7%)
Figure 7
increase. Furthermore, the intermediate SEM image (FIG. 7) clearly shows the presence of the size in the 50-200 micron agglomerates of fine particle surface. However, the shape of the agglomerates remained spherical. These results indicate that the primary mechanism to the second mechanism between the particle growth of the fine particles and the second characteristic intermediate characteristic are present in proportions of randomly agglomerated clumps. The transition between the second and third mechanism occurs when the fine particle fraction is almost completely consumed.
Mechanism of 3,2,3 three
In the L / S ratio SEM image of the resulting sample is higher than 22.1% (Figure 8) showed that these intermediate particles are composed of several fragments and "raspberry" structure, in the region of irregular particle shape, surface less smooth. This evolution is evident particle size distribution, increasing coarse content of fine particles damage, and damage to a higher degree of intermediate particles. In addition, the particle size distribution of the intermediate portion sizes from small to high dimensional translation. Increasing the average median diameter of the intermediate portion resulting from this change, the mechanism is reduced to the intermediate portion of the mechanism in the third, the results can be seen from Figure 3 due to the growth achieved by the merger. From the observation can be concluded, the growth mechanism of the third mechanism is the dominant priority to the proportion of fine particles is loaded into a combination of intermediate or coarse particles.
Figure 8
4 .Conclusion
The main objective of this work is, first, to understand the mechanism of the granulator, followed by a number of high-shear mixer L?DIGE noted physicochemical properties and operating conditions on the growth mechanism and kinetics of the main objectives of this work is to first to understand the mechanism of the granulator, followed by a number of high-shear mixer L?DIGE noted physicochemical properties and operating conditions on the mechanism and kinetics of growth. Powder binders have been several studies (powder: liquid two-alumina of different particle size distributions: water, aqueous polyethylene glycol, and polyvinyl alcohol aqueous solution, alcohol) affected. Powder binders have been several studies (powder: liquid two-alumina of different particle size distributions: water, aqueous polyethylene glycol, and polyvinyl alcohol aqueous solution, alcohol).
Experimental data show that due to the increased amount of liquid, the granulation process regardless of the nature of the powder, liquid binder or operating conditions through the use of three different growth mechanisms. The presence of these three mechanisms granulator profile show up each by a different mechanism of growth mechanisms.
In different time intervals, samples were removed from the granulator analysis showed that the growth mechanism includes a sample of each method was determined to be the following. In the first stage, the mechanism of the granulator nuclear primary particles (zone 0), which follows the first mechanism, does not create new species cohesion. In this method, which consists of a balance of wear and tear, to create a good particles or agglomerates and growth mechanism of fine particles (agglomeration, stratification); on the other hand, in the second mechanism, the random stratified fine aggregate particulate matter adsorbed on the growth of other species. This mechanism between the first and the second transition management densification and binder particles to the surface of the particle transport phenomena. The results showed that the powder for use in this study, the first transition occurs in a liquid saturation of 68% of independent operating conditions. Finally, when the fine aggregate is completely exhausted, there area a third of small and large particles in a granulating mechanism is perfect coalescence mechanism.
Finally, amplification tests showed that industrial-scale granulator (130L) was confirmed in a laboratory-scale granulator observed granulator outline three methods.
參考文獻(xiàn)
1. Capes, C.E., 1980. Handbook of Powder Technology: vol. 1, Particle Size Enlargement. Elsevier, Amsterdam.
2. Capes, C.E., Danckwerts, P.V., 1965. Granule formation by the agglomeration o