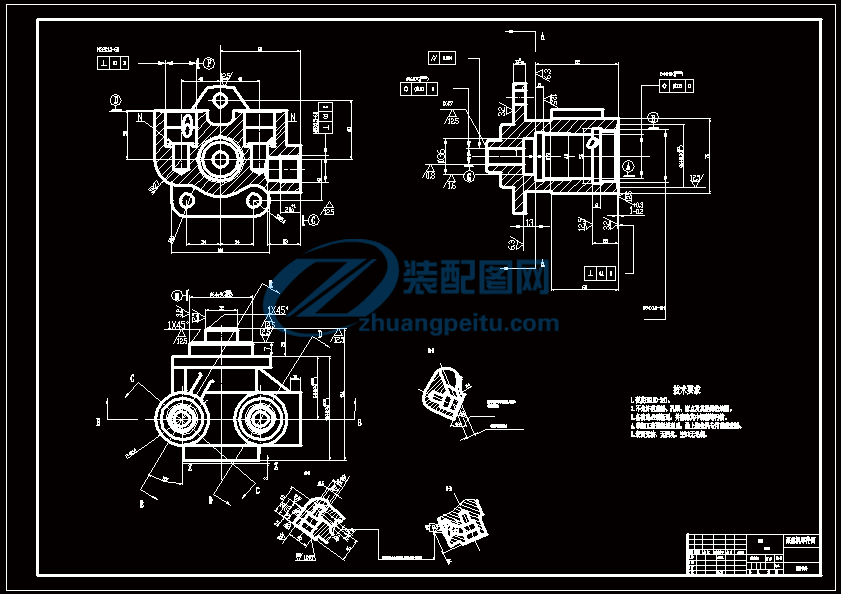

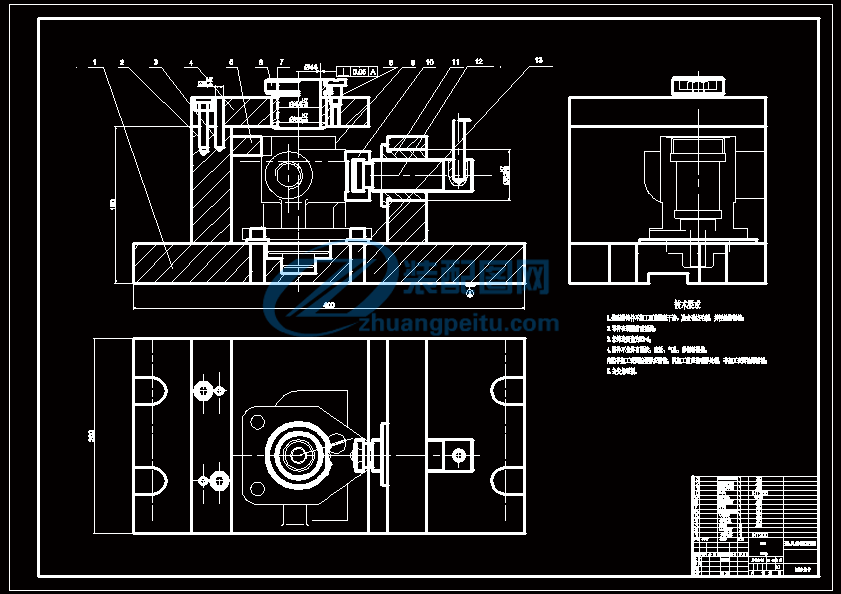




畢 業(yè) 設(shè) 計(jì)(論 文)外 文 參 考 資 料 及 譯 文
譯文題目: Mechanical processing and fixture design 論如何提高機(jī)械加工精度
學(xué)生姓名:
Mechanical processing and fixture design
Have a shape as a processing method, all machining process for the production of the most commonly used and most important method. Machining process is a process generated shape, in this process, Drivers device on the work piece material to be in the form of chip removal. Although in some occasions, the workpiece under no circumstances, the use of mobile equipment to the processing, However, the majority of the machining is not only supporting the workpiece also supporting tools and equipment to complete.
Machining methods roughly in the following situations:
1) vehicles, milling, planing, drilling, grinding and other general machining parts, and then necessary bench repair, assembly into component parts.
2) high precision parts, only ordinary machining to ensure high machining accuracy, and thus requires the use of precision machine tools for processing.
3) in order to make parts especially complex shape punch and concave model hole and cavity machining becomes more automated, reduce fitter repair workload, requires the use of CNC machine tools (such as three coordinate CNC milling machine, machining center, NC grinder equipment processing parts.
Machining know the process has two aspects. Small group of low-cost production. For casting, forging and machining pressure, every production of a specific shape of the workpiece, even a spare parts, almost have to spend the high cost of processing. Welding to rely on the shape of the structure, to a large extent, depend on effective in the form of raw materials. In general, through the use of expensive equipment and without special processing conditions, can be almost any type of raw materials, mechanical processing to convert the raw materials processed into the arbitrary shape of the structure, as long as the external dimensions large enough, it is possible. Because of a production of spare parts, even when the parts and structure of the production batch sizes are suitable for the original casting, Forging or pressure processing to produce, but usually prefer machining.
Strict precision and good surface finish, machining the second purpose is the establishment of the high precision and surface finish possible on the basis of. Many parts, if any other means of production belonging to the large-scale production, Well Machining is a low-tolerance and can meet the requirements of small batch production. Besides, many parts on the production and processing of coarse process to improve its general shape of the surface. It is only necessary precision and choose only the surface machining. For instance, thread, in addition to mechanical processing, almost no other processing method for processing. Another example is the blacksmith pieces keyhole processing, as well as training to be conducted immediately after the mechanical completion of the processing.
Mechanical processing is the most important part of the high speed machining. High-speed machining is contemporary advanced manufacturing technology an important component of the high-efficiency, High-precision and high surface quality, and other features. This article presents the technical definition of the current state of development of China''s application fields and the demand situation.
High-speed machining is oriented to the 21st century a new high-tech, high-efficiency, High-precision and high surface quality as a basic feature, in the automobile industry, aerospace, Die Manufacturing and instrumentation industries gained increasingly widespread application, and has made significant technical and economic benefits. contemporary advanced manufacturing technology an important component part.
HSC is to achieve high efficiency of the core technology manufacturers, intensive processes and equipment packaged so that it has a high production efficiency. It can be said that the high-speed machining is an increase in the quantity of equipment significantly improve processing efficiency essential to the technology. High-speed machining is the major advantages : improve production efficiency, improve accuracy and reduce the processing of cutting resistance.
The high-speed machining of meaning, at present there is no uniform understanding, there are generally several points as follows : high cutting speed. usually faster than that of their normal cutting 5 -10 times; machine tool spindle speed high, generally spindle speed in -20000r/min above 10,000 for high-speed cutting; Feed at high velocity, usually 15 -50m/min up to 90m/min; For different cutting materials and the wiring used the tool material, high-speed cutting the meaning is not necessarily the same; Cutting process, bladed through frequency (Tooth Passing Frequency) closer to the "machine-tool - Workpiece "system the dominant natural frequency (Dominant Natural Frequency), can be considered to be high-speed cutting. Visibility high-speed machining is a comprehensive concept.
1992. Germany, the Darmstadt University of Technology, Professor H. Schulz in the 52th on the increase of high-speed cutting for the concept and the scope, as shown in Figure 1. Think different cutting targets, shown in the figure of the transition area (Transition), to be what is commonly called the high-speed cutting, This is also the time of metal cutting process related to the technical staff are looking forward to, or is expected to achieve the cutting speed.
High-speed machining of machine tools, knives and cutting process, and other aspects specific requirements. Several were from the following aspects : high-speed machining technology development status and trends.
At this stage, in order to achieve high-speed machining, general wiring with high flexibility of high-speed CNC machine tools, machining centers, By using a dedicated high-speed milling, drilling. These equipment in common is : We must also have h igh-speed and high-speed spindle system feeding system, Cutting can be achieved in high-speed process. High-speed cutting with the traditional cutting the biggest difference is that "Machine-tool-workpiece" the dynamic characteristics of cutting performance is stronger influence. In the system, the machine spindle stiffness, grip or form, a long knife set, spindle Broach, torque tool set, Performance high-speed impact are important factors.
The machining process is the soul, the core and key manufacturing technology, is the most active factor in production. The process is the metal cutting tool or grinding and other processing methods to processing the workpiece, the workpiece to achieve the required shape, size, surface rough degree and the mechanical and physical properties of, and become qualified parts. The machining process planning is the process documents of products or parts machining process and operation method, all relevant production personnel should strictly enforce discipline, conscientiously implement the file . The fixture is a device of machine tool clamping workpiece, its role is to enable the workpiece relative to the machine tool and cutter has a correct position, and keep this position unchanged in the process. Use jig can effectively guarantee the processing quality, improve production efficiency, reduce production costs, expanding the scope of machine tool technology, reduces the labor intensity of the workers, to guarantee the safety in production and therefore fixture in machinery manufacturing occupies important position . Considering the machining process planning and fixture used in the production of pump body directly affects the processing quality and production efficiency, so the research subject of pump body of machining process and fixture design has a very important significance.
Automatic Fixture Design
Assembly equipment used in the traditional synchronous fixture put parts of the fixture mobile center, to ensure that components from transmission from the plane or equipment plate placed after removal has been scheduled for position. However, in certain applications, mobile mandatory parts of the center line, it may cause parts or equipment damage. When parts vulnerability and may lead to a small vibration abandoned, or when their location is by machine spindle or specific to die, Tolerance again or when the request is a sophisticated, it would rather let the fixture to adapt to the location of parts, and not the contrary. For these tasks, Elyria, Ohio, the company has developed Zaytran a general non-functional data synchronization West category FLEXIBILITY fixture. Fixture because of the interaction and synchronization devices is independent; the synchronous device can use sophisticated equipment to replace the slip without affecting the fixture force. Fixture specification range from 0.2 inches itinerary, 5 pounds clamping force of the six-inch trip, 400-inch clamping force. The characteristics of modern production are becoming smaller and smaller quantities and product specifications biggest changes. Therefore, in the final stages of production, assembly of production, quantity and product design changes appear to be particularly vulnerable. This situation is forcing many companies to make greater efforts to rationalize the extensive reform and the previously mentioned case of assembly automation. Despite flexible fixture behind the rapid development of flexible transport and handling devices, such as backward in the development of industrial robots, it is still expected to increase the flexibility fixture. In fact the important fixture devices -- the production of the devices to strengthen investment on the fixture so that more flexibility in economic support holders.
According to their flexibility and fixture can be divided into: special fixture, the fixture combinations, the standard fixture, high flexible fixture. Flexible fixture on different parts of their high adaptability and the few low-cost replacement for the characteristic.
Forms can transform the structure of the flexible fixture can be installed with the change of structure components (such as needle cheek plate, Multi-chip components and flake cheek plate), a non-standard work piece gripper or clamping elements (for example: commencement standard with a clamping fixture and mobile components fixture supporting documents), or with ceramic or hardening of the intermediary substances (such as : Mobile particle bed fixture and heat fixture tight fixture). To production, the parts were secured fixture, the need to generate clamping function, its fixture with a few unrelated to the sexual submissive steps.
According to the processing was part of that foundation and working characteristics to determine the work piece fixture in the required position, then need to select some stability flat combination, These constitute a stable plane was fixed in the work piece fixture set position on the clamp-profile structure, all balanced and torque, it has also ensured that the work features close to the work piece. Finally, it must be calculated and adjusted, assembly or disassembly be standard fixture components required for the position, so that the work piece firmly by clamping fixture in China. In accordance with this procedure, the outline fixture structure and equipped with the planning and recording process can be automated control.
Structural modeling task is to produce some stable flat combination, Thus, these plane of the work pieces clamping force and will fixture stability. According to usual practice, this task can be human-machine dialogue that is almost completely automated way to completion. A man-machine dialogue that is automated fixture structure modeling to determine the merits can be conducted in an organized and planning fixture design reduce the amount of the design, shortening the study period and better distribution of work conditions. In short, can be successfully achieved significantly improve fixture efficiency and effectiveness.
Fully prepared to structure programs and the number of material circumstances, the completion of the first successful assembly can save up to 60% of the time.
Therefore fixture process modeling agencies is the purpose of the program has appropriate documents.
The current national standard parts and components of the existing fixture in China: GB/T2148~T2259 - 91 and all kinds of general fixture fixture standard, etc.. The fixture is conducive to the standardization of commercial production fixture, shorten production preparation period and reduce the total cost of production. 2, precision: with precision mechanical products is increasing, will increase the accuracy requirements of the fixture. 3, efficiency: efficient fixture is mainly used to reduce the processing time and auxiliary time, to improve labor productivity, reduce labor intensity recognized.. Efficient common clip has high-speed automated fixture fixture and fixture device with clamping force. At present, in addition to the production line, automatic line configuration corresponding efficient automated fixtures and, in CNC machine tools, especially on the machining center appeared a variety of automatic clamping fixture and jig automatic replacement device, give full play to the efficiency of NC machine tool. 4, flexible, flexible and flexible machine tool fixture is similar, it refers to the fixture by adjusting the combination, etc., in order to adapt to the capability of the process variable factors. The new type of fixture with flexible features are: combination fixture, universal adjustable fixture, fixture, modular fixture, NC fixture etc.. In order to meet the needs of modern mechanical industry, many varieties, small batch production, expand the fixture flexible degree of change of special fixture for non detachable structure, the development of adjustable clamp, and will be the main direction of the current fixture development in [7]. In summary, fixture in mechanical machining process plays an important role, the development of fixture is in order to meet the needs of modern machinery processing technology, it can be said is the needs of social development, production drives the development of fixture, the development process is inevitable.
機(jī)械加工及其夾具設(shè)計(jì)
機(jī)械加工是所有制造過(guò)程中最普遍使用的而且是最重要的方法。機(jī)械加工過(guò)程是一個(gè)產(chǎn)生形狀的過(guò)程,在這過(guò)程中,驅(qū)動(dòng)裝置使工件上的一些材料以切屑的形式被去除。盡管在某些場(chǎng)合,工件無(wú)承受情況下,使用移動(dòng)式裝備來(lái)實(shí)現(xiàn)加工,但大多數(shù)的機(jī)械加工是通過(guò)既支承工件又支承刀具的裝備來(lái)完成。
機(jī)械加工方法大致有以下幾種情況:
(1)用車、銑、刨、鉆、磨等通用機(jī)床加工零件,然后進(jìn)行必要的鉗工修配,裝配成各種組合零件。
(2)精度要求高的零件,只用普通機(jī)床加工難以保證高的加工精度,因而需要采用精密機(jī)床進(jìn)行加工。
(3)為了使零件特別是形狀復(fù)雜的凸模、凹模型孔和型腔的加工更趨自動(dòng)化,減少鉗工修配的工作量,需采用數(shù)控機(jī)床(如三坐標(biāo)數(shù)控銑床、加工中心、數(shù)控磨床等設(shè)備)加工零件。
機(jī)械加工過(guò)程中具備兩方面。小批生產(chǎn)低費(fèi)用。對(duì)于鑄造、鍛造和壓力加工,每一個(gè)要生產(chǎn)的具體工件形狀,即使是一個(gè)零件,幾乎都要花費(fèi)高額的加工費(fèi)用??亢附觼?lái)產(chǎn)生的結(jié)構(gòu)形狀,在很大程度上取決于有效的原材料的形式。一般來(lái)說(shuō),通過(guò)利用貴重設(shè)備而又無(wú)需特種加工條件下,幾乎可以以任何種類原材料開始,借助機(jī)械加工把原材料加工成任意所需要的結(jié)構(gòu)形狀,只要外部尺寸足夠大,那都是可能的。因此對(duì)于生產(chǎn)一個(gè)零件,甚至當(dāng)零件結(jié)構(gòu)及要生產(chǎn)的批量大小上按原來(lái)都適于用鑄造、鍛造或者壓力加工來(lái)生產(chǎn)的,但通常寧可選擇機(jī)械加工。
嚴(yán)密的精度和良好的表面粗糙度,機(jī)械加工的第二方面用途是建立在高精度和可能的表面粗糙度基礎(chǔ)上。許多零件,如果用別的其他方法來(lái)生產(chǎn)屬于大批量生產(chǎn)的話,那么在機(jī)械加工中則是屬于低公差且又能滿足要求的小批量生產(chǎn)了。另一方面,許多零件靠比較粗糙的生產(chǎn)加工工藝制造其表面形狀,而僅僅是在需要高精度的且選擇過(guò)的表面才進(jìn)行機(jī)械加工。例如內(nèi)螺紋,除了機(jī)械加工之外,幾乎沒(méi)有別的加工方法能進(jìn)行加工。又如已鍛工件上的小孔加工,也是被鍛后緊接著進(jìn)行機(jī)械加工才完成的。
機(jī)械加工中最主要的是高速切削加工。 高速切削加工是當(dāng)代先進(jìn)制造技術(shù)的重要組成部分,擁有高效率、高精度及高表面質(zhì)量等特征。本文介紹此技術(shù)的定義、發(fā)展現(xiàn)狀、適用領(lǐng)域以及中國(guó)的需求情況。
高速切削加工是面向21世紀(jì)的一項(xiàng)高新技術(shù),它以高效率、高精度和高表面質(zhì)量為基本特征,在汽車工業(yè)、航空航天、模具制造和儀器儀表等行業(yè)中獲得了愈來(lái)愈廣泛的應(yīng)用,并已取得了重大的技術(shù)經(jīng)濟(jì)效益,是當(dāng)代先進(jìn)制造技術(shù)的重要組成部分。
高速切削是實(shí)現(xiàn)高效率制造的核心技術(shù),工序的集約化和設(shè)備的通用化使之具有很高的生產(chǎn)效率??梢哉f(shuō),高速切削加工是一種不增加設(shè)備數(shù)量而大幅度提高加工效率所必不可少的技術(shù)。高速切削加工的優(yōu)點(diǎn)主要在于:提高生產(chǎn)效率、提高加工精度及降低切削阻力。
有關(guān)高速切削加工的含義,目前尚無(wú)統(tǒng)一的認(rèn)識(shí),通常有如下幾種觀點(diǎn):切削速度很高,通常認(rèn)為其速度超過(guò)普通切削的5-10倍;機(jī)床主軸轉(zhuǎn)速很高,一般將主軸轉(zhuǎn)速在10000-20000r/min以上定為高速切削;進(jìn)給速度很高,通常達(dá)15-50m/min,最高可達(dá)90m/min;對(duì)于不同的切削材料和所釆用的刀具材料,高速切削的含義也不盡相同;切削過(guò)程中,刀刃的通過(guò)頻率(Tooth Passing Frequency)接近于“機(jī)床-刀具-工件”系統(tǒng)的主導(dǎo)自然頻率(Dominant Natural Frequency)時(shí),可認(rèn)為是高速切削??梢姼咚偾邢骷庸な且粋€(gè)綜合的概念。
1992年,德國(guó)Darmstadt工業(yè)大學(xué)的H. Schulz教授在CIRP上提出了高速切削加工的概念及其涵蓋的范圍,如圖1所示。認(rèn)為對(duì)于不同的切削對(duì)象,圖中所示的過(guò)渡區(qū)(Transition)即為通常所謂的高速切削範(fàn)圍,這也是當(dāng)時(shí)金屬切削工藝相關(guān)的技術(shù)人員所期待或者可望實(shí)現(xiàn)的切削速度。
高速切削加工對(duì)機(jī)床、刀具和切削工藝等方面都有一些具體的要求。下面分別從這幾個(gè)方面闡述高速切削加工技術(shù)的發(fā)展現(xiàn)狀和趨勢(shì)。
現(xiàn)階段,為了實(shí)現(xiàn)高速切削加工,一般釆用高柔性的高速數(shù)控機(jī)床、加工中心,也有釆用專用的高速銑、鉆床。這些設(shè)備的共同之處是:必須同時(shí)具有高速主軸系統(tǒng)和高速進(jìn)給系統(tǒng),才能實(shí)現(xiàn)材料切削過(guò)程的高速化。高速切削與傳統(tǒng)切削最大的區(qū)別是,“機(jī)床-刀具-工件”系統(tǒng)的動(dòng)態(tài)特性對(duì)切削性能有更強(qiáng)的影響力。在該系統(tǒng)中,機(jī)床主軸的剛度、刀柄形式、刀長(zhǎng)設(shè)定、主軸拉刀力、刀具扭力設(shè)定等,都是影響高速切削性能的重要因素。
機(jī)械加工工藝是制造技術(shù)的靈魂、核心和關(guān)鍵,是生產(chǎn)中最活躍的因素。其過(guò)程是采用金屬切削刀具或磨具及其他加工方法來(lái)加工工件,使工件達(dá)到所要求的形狀、尺寸、表面粗糙度和力學(xué)物理性能,從而生產(chǎn)成為合格零件。而機(jī)械加工工藝規(guī)程是規(guī)定產(chǎn)品或零件機(jī)械加工工藝過(guò)程和操作方法等的工藝文件,是一切有關(guān)生產(chǎn)人員都應(yīng)嚴(yán)格執(zhí)行、認(rèn)真貫徹的紀(jì)律性文件[8]。機(jī)床夾具是機(jī)床上裝夾工件的一種裝置,其作用是使工件相對(duì)于機(jī)床和刀具有一個(gè)正確的位置,并在加工過(guò)程中保持這個(gè)位置不變。使用夾具可以有效的保證加工質(zhì)量,提高生產(chǎn)效率,降低生產(chǎn)成本,擴(kuò)大機(jī)床的工藝范圍,減輕工人勞動(dòng)強(qiáng)度,保證安全生產(chǎn)等,因此,夾具在機(jī)械制造中占有重要的地位[10]??紤]到機(jī)械加工工藝安排及夾具的使用在泵體的生產(chǎn)中直接影響到其加工質(zhì)量和生產(chǎn)效率等,所以研究泵體的機(jī)械加工工藝及夾具設(shè)計(jì)的課題有著十分重要的意義。
自動(dòng)夾具設(shè)計(jì)
用做裝配設(shè)備的傳統(tǒng)同步夾具把零件移動(dòng)到夾具中心上,以確保零件從傳送機(jī)上或從設(shè)備盤上取出后置于已定位置上。然而在某些應(yīng)用場(chǎng)合、強(qiáng)制零件移動(dòng)到中心線上時(shí),可能引起零件或設(shè)備破壞。當(dāng)零件易損壞而且小小振動(dòng)可能導(dǎo)致報(bào)廢時(shí),或當(dāng)其位置是由機(jī)床主軸或模具來(lái)具體時(shí),再或者當(dāng)公差要求很精密時(shí),那寧可讓夾具去適應(yīng)零件位置,而不是相反。為著這些工作任務(wù),美國(guó)俄亥俄州Elyria的Zaytran公司已經(jīng)開發(fā)了一般性功能數(shù)據(jù)的非同步西類柔順性?shī)A具。因?yàn)閵A具作用力和同步化裝置是各自獨(dú)立的,該同步裝置可以用精密的滑移裝置來(lái)替換而不影響夾具作用力。夾具規(guī)格范圍是從0.2英寸行程,5英鎊夾緊力到6英寸行程、400英寸夾緊力。
現(xiàn)代生產(chǎn)的特征是批量變得越來(lái)越小而產(chǎn)品的各種規(guī)格變化最大。因此,生產(chǎn)的最后階段,裝配因生產(chǎn)計(jì)劃、批量和產(chǎn)品設(shè)計(jì)的變更而顯得特別脆弱。這種情形正迫使許多公司更多地致力于廣泛的合理化改革和前面提到過(guò)情況那樣裝配自動(dòng)化。盡管柔性?shī)A具的發(fā)展很快落后與柔性運(yùn)輸處理裝置的發(fā)展,如落后于工業(yè)機(jī)器人的發(fā)展,但仍然試圖指望增加夾具的柔順性。事實(shí)上夾具的重要的裝置——生產(chǎn)裝置的專向投資就加強(qiáng)了使夾具更加柔性化在經(jīng)濟(jì)上的支持。
根據(jù)它們?nèi)犴樞?,夾具可以分為:專用夾具、組合夾具、標(biāo)準(zhǔn)夾具、高柔性?shī)A具。柔性?shī)A具是以它們對(duì)不同工件的高適應(yīng)性和以少更換低費(fèi)用為特征的。
結(jié)構(gòu)形式可變換的柔性?shī)A具裝有可變更結(jié)構(gòu)排列的零件(例如針形頰板,多片式零件和片狀頰板),標(biāo)準(zhǔn)工件的非專用夾持或夾緊元件(例如:?jiǎn)?dòng)標(biāo)準(zhǔn)夾持夾具和帶有可移動(dòng)元件的夾具配套件),或者裝有陶瓷或硬化了的中介物質(zhì)(如:流動(dòng)粒子床夾具和熱夾具緊夾具)。為了生產(chǎn),零件要在夾具中被緊固,需要產(chǎn)生夾緊作用,其有幾個(gè)與夾具柔順性無(wú)關(guān)的步驟:
根據(jù)被加工工件基礎(chǔ)的部分和工作特點(diǎn),確定工件在夾具中的所需的位置,接著必須選擇若干穩(wěn)定平面的組合,這些穩(wěn)定平面就構(gòu)成工件被固定在夾具中確定位置上的夾具上,均衡所有的力和力矩,而且保證接近工件工作特點(diǎn)。最后,必須計(jì)算、調(diào)整、組裝可拆裝的或標(biāo)準(zhǔn)夾具元件的所需位置,以便使工件牢牢地被夾緊在夾具中。依據(jù)這樣的程序,夾具的輪廓結(jié)構(gòu)和裝合的規(guī)劃和記錄過(guò)程可以進(jìn)行自動(dòng)化控制。
結(jié)構(gòu)造型任務(wù)就是要產(chǎn)生若干穩(wěn)定平面的組合,這樣在這些平面上的各夾緊力將使工件和夾具穩(wěn)定。按慣例,這個(gè)任務(wù)可用人—機(jī)對(duì)話即幾乎完全自動(dòng)化的方式來(lái)完成。一人—機(jī)對(duì)話即以自動(dòng)化方式確定夾具結(jié)構(gòu)造型的優(yōu)點(diǎn)是可以有組織有規(guī)劃進(jìn)行夾具設(shè)計(jì),減少所需的設(shè)計(jì)人員,縮短研究周期和能更好地配置工作條件。簡(jiǎn)言之,可成功地達(dá)到顯著提高夾具生產(chǎn)效率和效益。
在充分準(zhǔn)備了構(gòu)造方案和一批材料情況下,在完成首次組裝可以成功實(shí)現(xiàn)節(jié)約時(shí)間達(dá)60%。
因此夾具機(jī)構(gòu)造型過(guò)程的目的是產(chǎn)生合適的編程文件。
目前我國(guó)已有夾具零件及部件的國(guó)家標(biāo)準(zhǔn):GB/T2148~T2259—91以及各類通用夾具、組合夾具標(biāo)準(zhǔn)等。機(jī)床夾具的標(biāo)準(zhǔn)化有利于夾具的商品化生產(chǎn),有利于縮短生產(chǎn)準(zhǔn)備周期,降低生產(chǎn)總成本。2、精密化:隨著機(jī)械產(chǎn)品精度的日益提高,勢(shì)必相應(yīng)提高了對(duì)夾具的精度要求。3、高效化:高效化夾具主要用來(lái)減少工件加工的基本時(shí)間和輔助時(shí)間,以提高勞動(dòng)生產(chǎn)率,減輕公認(rèn)的勞動(dòng)強(qiáng)度。。常見的高效化夾具有自動(dòng)化夾具、高速化夾具和具有夾緊力裝置的夾具等。目前,除了在生產(chǎn)流水線、自動(dòng)線配置相應(yīng)的高效、自動(dòng)化夾具外,在數(shù)控機(jī)床上,尤其是在加工中心上出現(xiàn)了各種自動(dòng)裝夾工件的夾具以及自動(dòng)更換夾具的裝置,充分發(fā)揮了數(shù)控機(jī)床的效率。4、柔性化:機(jī)床夾具的柔性化與機(jī)床的柔性化相似,它是指機(jī)床夾具通過(guò)調(diào)整、組合等方式,以適應(yīng)工藝可變因素的能力。具有柔性化特征的新型夾具種類主要有:組合夾具、通用可調(diào)夾具、成組夾具、模塊化夾具、數(shù)控夾具等。為適應(yīng)現(xiàn)代機(jī)械工業(yè)多品種、中小批量生產(chǎn)的需要,擴(kuò)大夾具的柔性化程度,改變專用夾具的不可拆結(jié)構(gòu),發(fā)展可調(diào)夾具,將是當(dāng)前夾具發(fā)展的主要方向[7]。 綜上所述,夾具在機(jī)械加工生產(chǎn)過(guò)程中起著重大的作用,夾具的發(fā)展是為了滿足當(dāng)代機(jī)械加工工藝的需要,可以說(shuō)是社會(huì)發(fā)展、生產(chǎn)的需要帶動(dòng)著夾具的發(fā)展,其發(fā)展過(guò)程是必然的。論如何提高機(jī)械加工精度
加工精度是指零件加工后的實(shí)際幾何參數(shù)(尺寸、形狀和位置)……