
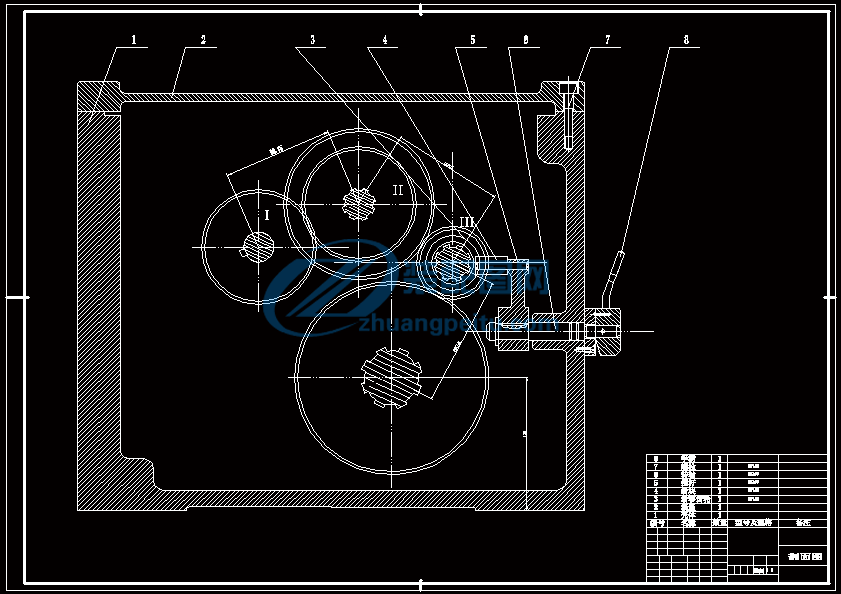

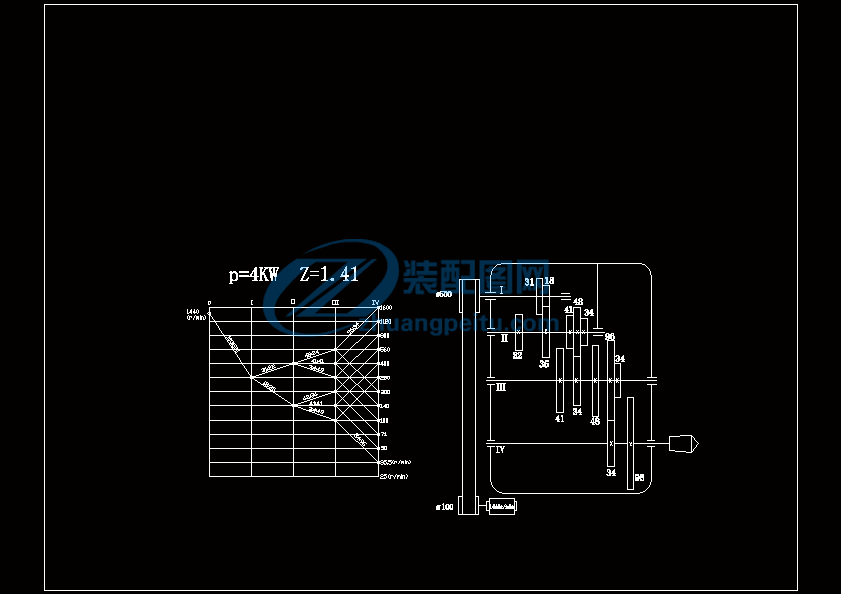
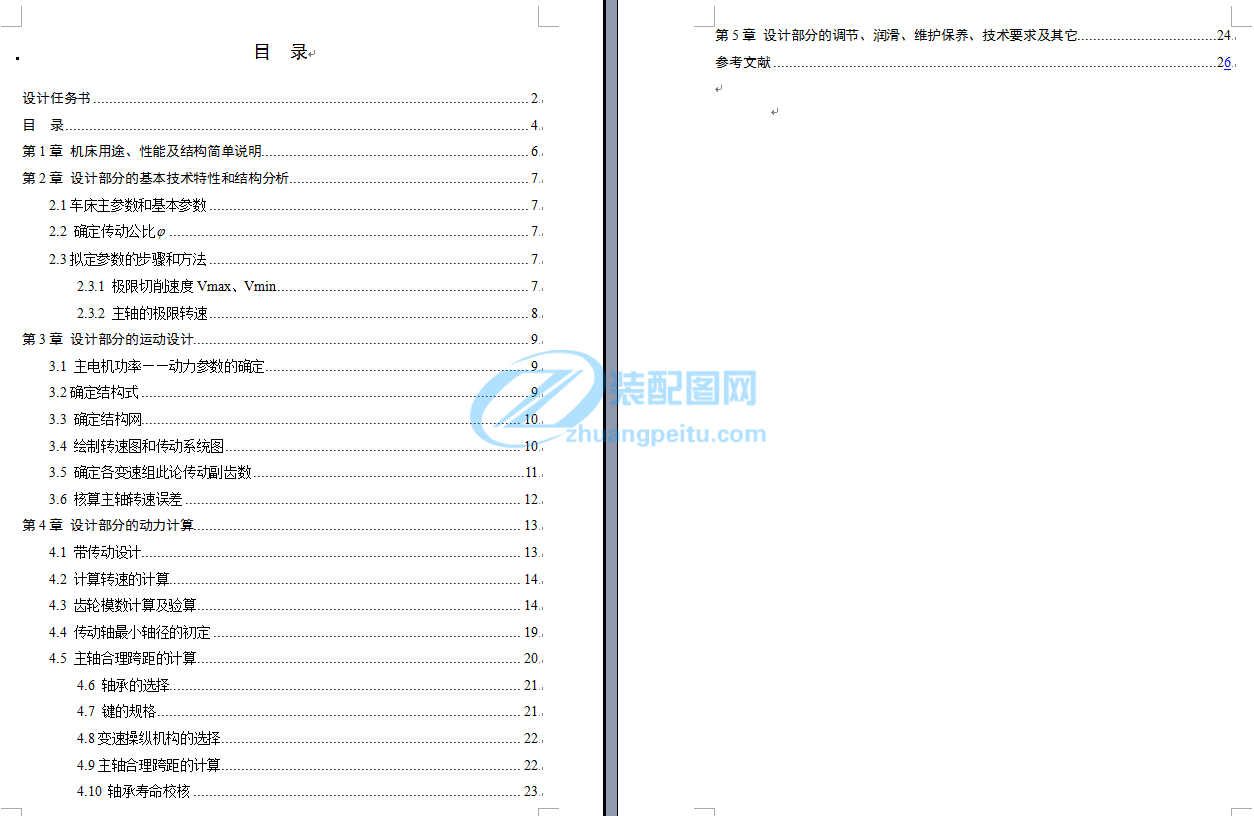
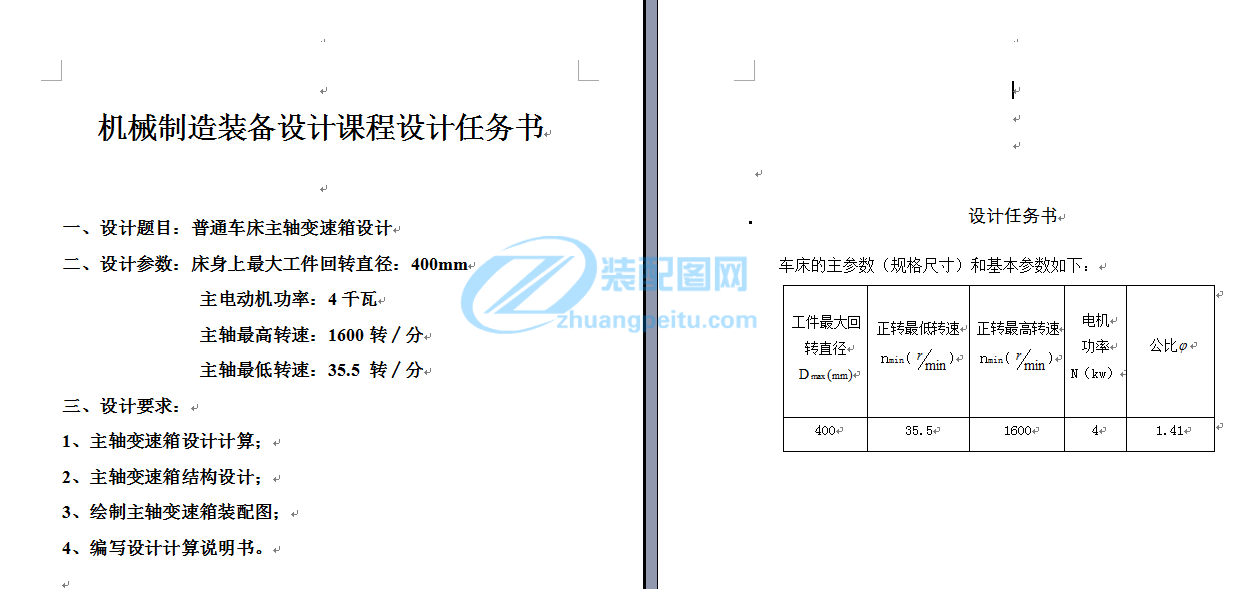
1機械制造裝備設(shè)計課程設(shè)計任務書1、設(shè)計題目:普通車床主軸變速箱設(shè)計2、設(shè)計參數(shù):床身上最大工件回轉(zhuǎn)直徑:400mm主電動機功率:4 千瓦主軸最高轉(zhuǎn)速:1600 轉(zhuǎn)∕分主軸最低轉(zhuǎn)速:35.5 轉(zhuǎn)∕分3、設(shè)計要求:1、主軸變速箱設(shè)計計算;2、主軸變速箱結(jié)構(gòu)設(shè)計;3、繪制主軸變速箱裝配圖;4、編寫設(shè)計計算說明書。專 業(yè):機械設(shè)計制造及其自動化(2 班)學生姓名學 號2指導教師設(shè)計任務書車床的主參數(shù)(規(guī)格尺寸)和基本參數(shù)如下:工件最大回轉(zhuǎn)直徑D (mm)max正轉(zhuǎn)最低轉(zhuǎn)速nmin( )mir正轉(zhuǎn)最高轉(zhuǎn)速nmin( )ir電機功率N(kw)公比 ?400 35.5 1600 4 1.411目 錄設(shè)計任務書.2目 錄.4第 1 章 機床用途、性能及結(jié)構(gòu)簡單說明.6第 2 章 設(shè)計部分的基本技術(shù)特性和結(jié)構(gòu)分析.72.1 車床主參數(shù)和基本參數(shù) .72.2 確定傳動公比 7?2.3 擬定參數(shù)的步驟和方法 .72.3.1 極限切削速度 Vmax、Vmin .72.3.2 主軸的極限轉(zhuǎn)速 .8第 3 章 設(shè)計部分的運動設(shè)計.93.1 主電機功率—— 動力參數(shù)的確定 93.2 確定結(jié)構(gòu)式 .93.3 確定結(jié)構(gòu)網(wǎng) 103.4 繪制轉(zhuǎn)速圖和傳動系統(tǒng)圖 103.5 確定各變速組此論傳動副齒數(shù) 113.6 核算主軸轉(zhuǎn)速誤差 12第 4 章 設(shè)計部分的動力計算.134.1 帶傳動設(shè)計 134.2 計算轉(zhuǎn)速的計算 144.3 齒輪模數(shù)計算及驗算 144.4 傳動軸最小軸徑的初定 194.5 主軸合理跨距的計算 204.6 軸承的選擇 214.7 鍵的規(guī)格 214.8 變速操縱機構(gòu)的選擇 .224.9 主軸合理跨距的計算 .224.10 軸承壽命校核 232第 5 章 設(shè)計部分的調(diào)節(jié)、潤滑、維護保養(yǎng)、技術(shù)要求及其它.24參考文獻.263第 1 章 機床用途、性能及結(jié)構(gòu)簡單說明機床技術(shù)參數(shù)有主參數(shù)和基本參數(shù),他們是運動傳動和結(jié)構(gòu)設(shè)計的依據(jù),影響到機床是否滿足所需要的基本功能要求,參數(shù)擬定就是機床性能設(shè)計。主參數(shù)是直接反映機床的加工能力、決定和影響其他基本參數(shù)的依據(jù),如車床的最大加工直徑,一般在設(shè)計題目中給定,基本參數(shù)是一些加工件尺寸、機床結(jié)構(gòu)、運動和動力特性有關(guān)的參數(shù),可歸納為尺寸參數(shù)、運動參數(shù)和動力參數(shù)。通用車床工藝范圍廣,所加工的工件形狀、尺寸和材料各不相同,有粗加工又有精加工;用硬質(zhì)合金刀具又用高速鋼刀具。因此,必須對所設(shè)計的機床工藝范圍和使用情況做全面的調(diào)研和統(tǒng)計,依據(jù)某些典型工藝和加工對象,兼顧其他的可能工藝加工的要求,擬定機床技術(shù)參數(shù),擬定參數(shù)時,要考慮機床發(fā)展趨勢和同國內(nèi)外同類機床的對比,使擬定的參數(shù)最大限度地適應各種不同的工藝要求和達到機床加工能力下經(jīng)濟合理。機床主傳動系因機床的類型、性能、規(guī)格和尺寸等因素的不同,應滿足的要求也不一樣。設(shè)計機床主傳動系時最基本的原則就是以最經(jīng)濟、合理的方式滿足既定的要求。在設(shè)計時應結(jié)合具體機床進行具體分析,一般應滿足的基本要求有:滿足機床使用性能要求。首先應滿足機床的運動特性,如機床主軸油足夠的轉(zhuǎn)速范圍和轉(zhuǎn)速級數(shù);滿足機床傳遞動力的要求。主電動機和傳動機構(gòu)能提供足夠的功率和轉(zhuǎn)矩,具有較高的傳動效率;滿足機床工作性能要求。主傳動中所有零部件有足夠的剛度、精度和抗震性,熱變形特性穩(wěn)定;滿足產(chǎn)品的經(jīng)濟性要求。傳動鏈盡可能簡短,零件數(shù)目要少,以便節(jié)約材料,降低成本。4第 2 章 設(shè)計部分的基本技術(shù)特性和結(jié)構(gòu)分析2.1 車床主參數(shù)和基本參數(shù)車床的主參數(shù)(規(guī)格尺寸)和基本參數(shù)如下:工件最大回轉(zhuǎn)直徑D (mm)max正轉(zhuǎn)最低轉(zhuǎn)速nmin( )mir正轉(zhuǎn)最高轉(zhuǎn)速nmin( )ir電機功率N(kw)公比 ?400 35.5 1600 4 1.412.2 確定傳動公比 ?根據(jù)【1】 公式(3-2)因為已知 , , =1.4178P 07.45.316minax??R??znR?∴Z= +1=12?lgnR根據(jù)【1】 表 3-5 標準公比 。這里我們?nèi)藴使认盗?=1.417P??因為 =1.41=1.066,根據(jù)【1】 表 3-6 標準數(shù)列。首先找到最小極限轉(zhuǎn)速 35.5,再7P每跳過 5 個數(shù)取一個轉(zhuǎn)速,即可得到公比為 1.41 的數(shù)列:35.5,50,71,100,140,200,280,400,560,800,1120,16002.3 擬定參數(shù)的步驟和方法2.3.1 極限切削速度 Vmax、Vmin根據(jù)典型的和可能的工藝選取極限切削速度要考慮:允許的切速極限參考值如下:表 1.1加 工 條 件 Vmax(m/min) Vmin(m/min)硬質(zhì)合金刀具粗加工鑄鐵工件 30~50硬質(zhì)合金刀具半精或精加工碳 150~3005鋼工件螺紋加工和鉸孔 3~82.3.2 主軸的極限轉(zhuǎn)速計算車床主軸極限轉(zhuǎn)速時的加工直徑,則主軸極限轉(zhuǎn)速應為結(jié)合題目條件,取標準數(shù)列數(shù)值,=25r/minmin取 41.??考慮到設(shè)計的結(jié)構(gòu)復雜程度要適中,故采用常規(guī)的擴大傳動。各級轉(zhuǎn)速數(shù)列可直接從標準的數(shù)列表中查出,按標準轉(zhuǎn)速數(shù)列為:35.5,50,71,100,140,200,280,400,560,800,1120,16006第 3 章 設(shè)計部分的運動設(shè)計3.1 主電機功率——動力參數(shù)的確定合理地確定電機功率 N,使機床既能充分發(fā)揮其性能,滿足生產(chǎn)需要,又不致使電機經(jīng)常輕載而降低功率因素。根據(jù)題設(shè)條件電機功率為 4KW??蛇x取電機為:Y112M-4 額定功率為 4KW,滿載轉(zhuǎn)速為 1440r/min。3.2 確定結(jié)構(gòu)式已知 Z= x3b2aa,b 為正整數(shù),即 Z 應可以分解為 2 和 3 的因子,以便用 2、3 聯(lián)滑移齒輪實現(xiàn)變速。對于 Z=13,可以按照 12=2×3×2 傳動式(剔除最小的一級) ,有 6 種結(jié)構(gòu)式和對應的結(jié)構(gòu)網(wǎng)。分別為:, , ,??????????????????????由于本次設(shè)計的機床 I 軸裝有摩擦離合器,在結(jié)構(gòu)上要求有一齒輪的齒根圓大于離合器的直徑。初選 的方案。1263從電動機到主軸主要為降速變速,若使變速副較多的變速組放在較接近電動機處可使小尺寸零件多些,大尺寸零件少些,節(jié)省材料,也就是滿足變速副前多后少的原則,因此取 12=2×3×2 方案為好。設(shè)計車床主變速傳動系時,為避免從動齒輪尺寸過大而增加箱體的徑向尺寸,在降速變速中,一般限制限制最小變速比 ;為避免擴大傳動誤差,減少震動噪41min?u聲,在升速時一般限制最大轉(zhuǎn)速比 。斜齒圓柱齒輪傳動較平穩(wěn),可取2ax?。因此在主變速鏈任一變速組的最大變速范圍5.2max?u。在設(shè)計時必須保證中間變速軸的變速范圍??)10~8(5.)2~(minax?uR最小。綜合上述可得:主傳動部件的運動參數(shù) , =35.5, Z=12 =1.41160maxmin?73.3 確定結(jié)構(gòu)網(wǎng)根據(jù)“前多后少”,“先降后升”,前密后疏,結(jié)構(gòu)緊湊的原則易知第二擴大組的變速范圍 r=φ (P3-1)x=1.414=3.95〈8,滿足要求.圖 2-1 結(jié)構(gòu)網(wǎng) 1263??3.4 繪制轉(zhuǎn)速圖和傳動系統(tǒng)圖(1)選擇電動機:采用 Y 系列封閉自扇冷式鼠籠型三相異步電動機。(2)繪制轉(zhuǎn)速圖:8(3)畫主傳動系統(tǒng)圖。根據(jù)系統(tǒng)轉(zhuǎn)速圖及已知的技術(shù)參數(shù),畫主傳動系統(tǒng)圖如圖 2-3:1-2 軸最小中心距:A 1_2min1/2(Zmaxm+2m+D)軸最小齒數(shù)和:S zmin(Zmax+2+D/m)3.5 確定各變速組此論傳動副齒數(shù)(1)Sz 100-124,中型機床 Sz=70-100?(2)直齒圓柱齒輪 Zmin 18-24,m 4??9圖 2-3 主傳動系統(tǒng)圖(7)齒輪齒數(shù)的確定。變速組內(nèi)取模數(shù)相等,據(jù)設(shè)計要求 Zmin≥18~24,齒數(shù)和Sz≤100~124,由表 4.1,根據(jù)各變速組公比,可得各傳動比和齒輪齒數(shù),各齒輪齒數(shù)如表 2-2。表 2-2 齒輪齒數(shù)基本組 第一擴大組 第二擴大組傳動比1.41:1 1:2 1.41:1 1:1 1:1.41 2.8:1 1:2.8代號 Z1Z 'Z 2Z 'Z3Z 'Z4Z ’ Z5 Z5’ Z6Z 'Z7 Z7’齒數(shù) 31 22 18 35 48 34 41 41 34 48 96 34 34 963.6 核算主軸轉(zhuǎn)速誤差實際傳動比所造成的主軸轉(zhuǎn)速誤差,一般不應超過±10( -1)%,即?〈10( -1)%=4.1%n標 準 轉(zhuǎn) 速標 準 轉(zhuǎn) 速實 際 轉(zhuǎn) 速 ?10第 4 章 設(shè)計部分的動力計算4.1 帶傳動設(shè)計輸出功率 P=4kw,轉(zhuǎn)速 n1=1440r/min,n2=280r/min(1)確定計算功率:按最大的情況計算 P=4kw ,K 為工作情況系數(shù),查[1]表 3.5. 取 K=1.1pd=kAP=1.1X4=4.4kw(2)選擇 V 帶的型號:根據(jù) pd,n1=1440r/min 參考[1] 圖表 3.16 及表 3.3 選小帶輪直徑,查表選擇 A 型 V帶 d1=100mm(3)確定帶輪直徑 d1,d2小帶輪直徑 d1=100mm驗算帶速 v= d1n1/(60X1000)= X100X2880/(60X1000)=12.6m/s??從動輪直徑 d2=n1d1/n2=2880X100/2400=236mm 取 d2=224mm 查[1]表 3.3計算實際傳動比 i=d2/d1=224/100=2.24(4)定中心矩 a 和基準帶長 Ld[1]初定中心距 a00.7(d1+d2) a0 2(d1+d2))?226.8 a0 648 取 ao=300mm[2]帶的計算基準長度Ld0≈2a0+ /2(d1+d2)+(d2-d1)2/4a0?≈2x300+ /2(10+224)+(224-100)2/4X300≈650mm查[1]表 3.2 取 Ld0=630mm[3]計算實際中心距a≈a0+(Ld-Ld0)/2=300+(630-650)=290mm[4]確定中心距調(diào)整范圍amax=a+0.03Ld=290+0.03X630=308.9mmamin=a-0.015Ld=290-0.015X630=240.55mm11(5)驗算包角: 1=1800-(d 2-d1)/aX57.3 0=1800-(180-90)/290X57.30=17241240?(6)確定 V 帶根數(shù):確定額定功率:P 0由查表并用線性插值得 P0=0.15kw查[1]表 37 得功率增量 P0=0.13kwA查[1]表 38 得包角系數(shù) K =0.99?查[1]表 3 得長度系數(shù) Kl=0.81確定帶根數(shù):Z=P /{(P +△P )×K ×K }C0?L=3.65/(1.05+0.13)X0.99X0.81=2.89 取 Z=34.2 計算轉(zhuǎn)速的計算(1)主軸的計算轉(zhuǎn)速n j,由公式 n =n 得,主軸的計算轉(zhuǎn)速n j=735r/min,jmi)13/(??z取800 r/min。(2). 傳動軸的計算轉(zhuǎn)速 軸3=1250 r/min 軸2=2400 r/min,軸1=2400r/min。(2)確定各傳動軸的計算轉(zhuǎn)速。各計算轉(zhuǎn)速入表 3-1。表 3-1 各軸計算轉(zhuǎn)速(3) 確定 齒輪副的計算轉(zhuǎn)速。齒輪 Z 裝在主軸上其中只有 800r/min 傳遞全功率,故 Z j=800 r/min。'6 '6依次可以得出其余齒輪的計算轉(zhuǎn)速,如表 3-2。表 3-2 齒輪副計算轉(zhuǎn)速序號 Z1Z 2Z3Z `4Z5n j2400 2400 2400 1250 8004.3 齒輪模數(shù)計算及驗算(1)模數(shù)計算。一般同一變速組內(nèi)的齒輪取同一模數(shù),選取負荷最重的小齒輪,按軸 號 Ⅰ 軸 Ⅱ 軸 Ⅲ 軸計算轉(zhuǎn)速 r/min 2400 2400 125012簡化的接觸疲勞強度公式進行計算,即 mj=16338 可得各組的模數(shù),如321][)(jjmnuzP???表 3-3 所示。根據(jù) 和 計算齒輪模數(shù),根據(jù)其中較大值取相近的標準模數(shù):jmw=16338 =16338 mmj321][)(jjnuzP???????3213JmsniZKu????——齒輪的最低轉(zhuǎn)速 r/min;N——頂定的齒輪工作期限,中型機床推存: =15~24T T——轉(zhuǎn)速變化系數(shù); nk——功率利用系數(shù);N——材料強化系數(shù)。 q——(壽命系數(shù))的極值skmaxinssk,齒輪等轉(zhuǎn)動件在接取和彎曲交邊載荷下的疲勞曲線指數(shù) m 和基準順環(huán)次數(shù) C0——工作情況系數(shù)。中等中級的主運動: 1——動載荷系數(shù);2k——齒向載荷分布系數(shù);3——齒形系數(shù); Y根據(jù)彎曲疲勞計算齒輪模數(shù)公式為: 式中:N——計算齒輪轉(zhuǎn)動遞的額定功率 N=? dwNk——計算齒輪(小齒輪)的計算轉(zhuǎn)速 r/minjn——齒寬系數(shù) ,m?mb/??8Z1——計算齒輪的齒數(shù),一般取轉(zhuǎn)動中最小齒輪的齒數(shù):——大齒輪與小齒輪的齒數(shù)比, = ;(+)用于外嚙合, (-)號用i i12?Z于內(nèi)嚙合: 命系數(shù); sTNnqkk?::工作期限 , = ; TTmCn0613= =3.49Tk接 310256?= =1.8T彎 96=0.84 =0.58 nknk接=0.90 =0.55 =0.72 彎 q接 qk彎=3.49 0.84 0.58 0.55=0.94sk接 ??=1.8 0.84 0.90 0.72=0.99 時,取 = ,當 時,取 = ;s?minskmaxskminskmin= =0.85 =1.5; kax1=1.2 =1 =0.378 23Y許用彎曲應力,接觸應力,( )paM=354 =1750 ??W?pa??J?6 級材料的直齒輪材料選;24 熱處理 HRC59irTC31-2 軸由公式 mj=16338 可得 mj=3.28mm,取 m=3.5mm321][)(jjmnuzP??2-3 軸由公式 mj=16338 可得 mj=2.85mm,取 m=3.5mm321][)(jj?由于一般同一變速組內(nèi)的齒輪盡量取同一模數(shù),所以為了統(tǒng)一和方便如下取:根據(jù)有關(guān)文獻,也為了便于統(tǒng)一,在這里傳動齒輪統(tǒng)一取 m=3.5表 3-3 模數(shù)(2)基本組齒輪計算?;窘M齒輪幾何尺寸見下表組號 基本組 第一擴大組模數(shù) mm 3.5 3.514齒輪 Z1 Z1` Z2 Z2`齒數(shù) 31 22 18 35分度圓直徑 108.5 77 63 122.5齒頂圓直徑 115.5 84 70 129.5齒根圓直徑 99.75 68.25 54.25 113.75齒寬 24 24 24 24按基本組最小齒輪計算。小齒輪用 40Cr,調(diào)質(zhì)處理,硬度 241HB~246HB,平均取260HB,大齒輪用 45 鋼,調(diào)質(zhì)處理,硬度 229HB~246HB ,平均取 240HB。計算如下:① 齒面接觸疲勞強度計算:接觸應力驗算公式為??jfsj MPauBnNKzm??????)()1(02832彎曲應力驗算公式為:??wswPaBYnz?????)(109235式中 N----傳遞的額定功率(kW) ,這里取 N 為電動機功率,N=5kW;-----計算轉(zhuǎn)速( r/min). =800(r/min);jnjm-----初算的齒輪模數(shù)(mm), m=3.5(mm);B----齒寬(mm);B=24(mm);z----小齒輪齒數(shù);z=21;u----小齒輪齒數(shù)與大齒輪齒數(shù)之比,u=1.6;-----壽命系數(shù);sK=sTnNKq15----工作期限系數(shù);TKmTCn016?T------齒輪工作期限,這里取 T=15000h.;-----齒輪的最低轉(zhuǎn)速(r/min), =500(r/min)1n1n----基準循環(huán)次數(shù),接觸載荷取 = ,彎曲載荷取 =0C0C70C612?m----疲勞曲線指數(shù),接觸載荷取 m=3;彎曲載荷取 m=6;----轉(zhuǎn)速變化系數(shù),查【5】2 上,取 =0.60nKnK----功率利用系數(shù),查 【5】2 上,取 =0.78N N-----材料強化系數(shù),查【5】2 上, =0.60q q-----工作狀況系數(shù),取 =1.13K3K-----動載荷系數(shù),查【5】2 上,取 =12------齒向載荷分布系數(shù),查【5】2 上, =1 1 1KY------齒形系數(shù),查 【5】2 上,Y=0.386;----許用接觸應力(MPa),查【4】 ,表 4-7,取 =650 Mpa;??j? ??j?---許用彎曲應力( MPa) ,查【4】 ,表 4-7,取 =275 Mpa;w w根據(jù)上述公式,可求得及查取值可求得:=635 Mpa j????j?=78 Mpaww(3)第一擴大組齒輪計算。擴大組齒輪幾何尺寸見下表 齒輪 Z3 Z3` Z4 Z4` Z5 Z5`16齒數(shù) 48 34 41 41 34 48分度圓直徑 168 119 143.5 143.5 119 168齒頂圓直徑 175 126 150.5 150.5 126 175齒根圓直徑 159.25 110.25 134.75 134.75 110.25 159.25齒寬 24 24 24 24 24 24(4)第二擴大組齒輪計算。擴大組齒輪幾何尺寸見下表 齒輪 Z6 Z6` Z7 Z7`齒數(shù) 96 34 34 96分度圓直徑 336 119 119 336齒頂圓直徑 343 126 126 343齒根圓直徑 327.25 110.25 110.25 327.25齒寬 24 24 24 24按擴大組最小齒輪計算。小齒輪用 40Cr,調(diào)質(zhì)處理,硬度 241HB~246HB,平均取 260HB,大齒輪用 45 鋼,調(diào)質(zhì)處理,硬度 229HB~246HB ,平均取 240HB。同理根據(jù)基本組的計算,查文獻【6】 ,可得 =0.62, =0.77, =0.60, =1.1,nKNqK3=1, =1,m=3.5, =355;2K1j可求得:=619 Mpa j????j?=135Mpa ww174.4 傳動軸最小軸徑的初定由【5】式 6,傳動軸直徑按扭轉(zhuǎn)剛度用下式計算:d=1.64 (mm)??4?Tn或 d=91 (mm)4njN式中 d---傳動軸直徑(mm)Tn---該軸傳遞的額定扭矩(N*mm) T=9550000 ;JnN?N----該軸傳遞的功率(KW)----該軸的計算轉(zhuǎn)速jn---該軸每米長度的允許扭轉(zhuǎn)角, == 。??????01各軸最小軸徑如表 3-3。表 3-3 最小軸徑4.5 主軸合理跨距的計算由于電動機功率 P=3kw,根據(jù)【1】表 3.24,前軸徑應為 60~90mm。初步選取d1=80mm。后軸徑的 d2=( 0.7~0.9)d 1,取 d2=60mm。根據(jù)設(shè)計方案,前軸承為NN3016K 型,后軸承為圓錐滾子軸承。定懸伸量 a=124mm,主軸孔徑為 30mm。軸承剛度,主軸最大輸出轉(zhuǎn)矩 T=9550 =9550× =424.44N.mnP904設(shè)該機床為車床的最大加工直徑為 400mm。床身上最常用的最大加工直徑,即經(jīng)濟加工直徑約為最大回轉(zhuǎn)直徑的 50%,這里取 75%,即 180mm,故半徑為 0.09m;軸 號 Ⅰ 軸 Ⅱ 軸最小軸徑 mm 35 4018切削力(沿 y 軸) Fc= =4716N09.42背向力(沿 x 軸) Fp=0.5 Fc=2358N總作用力 F= =5272.65N2pC?此力作用于工件上,主軸端受力為 F=5272.65N。先假設(shè) l/a=2,l=3a=240mm。前后支承反力 RA 和 RB 分別為RA=F× =5272.65× =7908.97Nla?2401?RB=F× =5272.65× =2636.325Nl根據(jù) 文獻【1】式 3.7 得:Kr=3.39 得前支承的剛度:K A= 1.0Fr8.La9.0)(iza.1cos1689.69 N/ ;K B= 785.57 N/ ; = =2.15m?m?BAK57.6主軸的當量外徑 de=(80+60)/2=70mm,故慣性矩為I= =113.8×10-8m464)03.7.(???η= = =0.143aKEA6381.980.2??查【1】圖 3-38 得 =2.0,與原假設(shè)接近,所以最佳跨距 =124×2.0=240mml0 0l合理跨距為(0.75-1.5) ,取合理跨距 l=360mm。0l根據(jù)結(jié)構(gòu)的需要,主軸的實際跨距大于合理跨距,因此需要采取措施增加主軸的剛度,增大軸徑:前軸徑 D=100mm,后軸徑 d=80mm。前軸承采用雙列圓柱滾子軸承,后支承采用背對背安裝的角接觸球軸承。4.6 軸承的選擇I軸:與帶輪靠近段安裝雙列角接觸球軸承代號7007C 另一安裝深溝球軸承6012II軸:對稱布置深溝球軸承6009III軸:后端安裝雙列角接觸球軸承代號7015C 另一安裝端角接觸球軸承代號7010C19中間布置角接觸球軸承代號7012C4.7 鍵的規(guī)格I軸安裝帶輪處選擇普通平鍵規(guī)格:BXL=10X56 II軸選擇花鍵規(guī)格:N d =8X36X40X7 III軸選擇鍵規(guī)格:BXL=14X90 4.8 變速操縱機構(gòu)的選擇選用左右擺動的操縱桿使其通過桿的推力來控制II軸上的三聯(lián)滑移齒輪和二聯(lián)滑移齒輪。4.9 主軸合理跨距的計算設(shè)機床最大加工回轉(zhuǎn)直徑為?400mm,電動機功率P=4kw,,主軸計算轉(zhuǎn)速為800r/min。已選定的前后軸徑為: 定懸伸量a=85mm。162dm?1(0.7~85)dm?軸承剛度,主軸最大輸出轉(zhuǎn)矩:= 63.79.50=54N??設(shè)該車床的最大加工直徑 400mm。床身上最常用的最大加工直徑,即經(jīng)濟加工直徑約為最大回轉(zhuǎn)直徑的 50%,這里取 45%,即 125mm切削力(沿 y 軸) F c=250.346/0.125=2781N背向力(沿 x 軸) F p=0.5 Fc=1390N20總作用力 F= =3109N2pCF?此力作用于工件上,主軸端受力為 F=3109N。先假設(shè) l/a=2,l=3a=255mm。前后支承反力 RA和 RB分別為RA=F× =3109× Nla?852415??RB=F× =3109× Nl036根據(jù)《主軸箱設(shè)計》得: =3.39 得前支承的剛度:K A= rK1.0F8.La0.91.()cosiz?1376.69 N/ ;K B= 713.73 N/ ; = =1.93m?m?BA376.主軸的當量外徑 de=(85+65)/2=75mm,故慣性矩為I= =1.55×10-6m440.756??η= = =0.383aKEA16325098??查《主軸箱設(shè)計》圖 得 =2.5,與原假設(shè)接近,所以最佳跨距 =85×2.5=212.5mml0 0l合理跨距為(0.75-1.5) ,取合理跨距 l=250mm。0l根據(jù)結(jié)構(gòu)的需要,主軸的實際跨距大于合理跨距,因此需要采取措施增加主軸的剛度,增大軸徑:前軸徑 D=85mm,后軸徑 d=55mm。后支承采用背對背安裝的角接觸球軸承。4.10 軸承壽命校核由 П 軸最小軸徑可取軸承為 7008c 角接觸球軸承,ε=3;P=XF r+YFaX=1,Y=0 。對Ⅱ軸受力分析21得:前支承的徑向力 Fr=2642.32N。由軸承壽命的計算公式:預期的使用壽命 [L10h]=15000hL10h= × = × = h≥[L 10h]n1670?)PC(180673)28.10(?367.10()284.9524??=15000h軸承壽命滿足要求。第 5 章 設(shè)計部分的調(diào)節(jié)、潤滑、維護保養(yǎng)、技術(shù)要求及其它1、為了減少車床磨損,延長使用壽命,保證工件加工精度,應對車床的所有摩擦部位進行潤滑,并注意日常的維護保養(yǎng)。2、車床的潤滑形式常用以下幾種,(1)澆油潤滑:常用于外露的滑動表面,如導軌面和滑板導軌面等。(2)濺油潤滑:常用于密閉的箱體中。如車床的主軸箱中的傳動齒輪將箱底的潤滑油濺射到箱體上部的油槽中,然后經(jīng)槽內(nèi)油孔流到各潤滑點進行潤滑。(3)油繩導油潤滑:常用于進給箱和溜板箱的油池中。利用毛線即吸油又滲油的特性,通過毛線把油引入潤滑點,間斷地滴油潤滑。(4)彈子油杯注油潤滑:常用于尾座、中滑板搖手柄及三杠(絲杠、光杠、開關(guān)杠)支架的軸承處。定期的用油槍端頭油嘴壓下油杯上的彈子,將油注入。油嘴撤去,彈子又回復原位,封住注油口,以防塵屑入內(nèi)。(5)黃油杯潤滑:常用于交換齒輪箱掛輪架的中間軸或不經(jīng)常潤滑處。事先在黃油杯中加滿鈣基潤滑脂,需要潤滑時,擰進油杯蓋,則杯中的油脂就被擠壓到潤滑點中去。(6)油泵輸油潤滑:常用于轉(zhuǎn)速高、需要大量潤滑油連續(xù)強制潤滑的場合。如主22軸箱內(nèi)許多潤滑點就是采用這種方式。3、車床的潤滑要求: (1)車床上一般都有潤滑系統(tǒng)圖,應嚴格按照潤滑系統(tǒng)圖進行潤滑。(2)換油時,應先將廢油放盡,然后用煤油把箱體內(nèi)沖洗干凈后,在注入新機油,注油時應用網(wǎng)過濾,且油面不得低于油標中心線。主軸箱內(nèi)零件用油泵潤滑或飛濺潤滑。箱內(nèi)潤滑油一般三個月更換一次。主軸箱體上有一個油標,若發(fā)現(xiàn)油標內(nèi)無油輸出,說明油泵輸油系統(tǒng)有故障,應立即停車檢查斷油的原因,并修復。(3)進給箱上部油繩導油潤滑的儲油槽,每班應給該儲油槽加一次油。(4)交換齒輪箱中間齒輪軸軸承是黃油杯潤滑,每班一次,7 天加一次鈣基脂。(5)彈子油杯潤滑每班潤滑一次。導軌工作前后擦凈用油槍加油。5、車床日常保養(yǎng)要求:(1)每天工作后,切斷電源,對車床各表面、各罩殼、導軌面、絲杠、光杠、各操縱手柄和操縱桿進行擦拭,做到無油污、無鐵屑、車床外表整潔。(2)每周要求保養(yǎng)床身導軌面和中小滑板導軌面及轉(zhuǎn)動部位的整潔、潤滑。要求油眼暢通、油標清晰,清洗油繩和護床油毛氈,保持車床外表清潔和工作場地整潔。6、車床一級保養(yǎng)要求:車場運行 500 小時后,須進行一級保養(yǎng)。其保養(yǎng)以操作工人為主,在維修工人的配合下進行。保養(yǎng)時必須先切斷電源,然后按下述順序和要求進行。(1)主軸箱的保養(yǎng):a、清洗濾油器、使其無雜物b、檢查主軸鎖緊螺母有無松動,緊定螺釘是否擰緊。c、調(diào)整制動器及離合器摩擦片間隙。(2)交換齒輪箱的保養(yǎng):a、清洗齒輪、軸套,并在油杯中注入新油脂。b、調(diào)整齒輪嚙合間隙。c、檢查軸套有無晃動現(xiàn)象(3)滑板和刀架的保養(yǎng):拆洗刀架和中、小滑板,洗凈擦干后重新組裝,并調(diào)整中、小滑板與鑲條的間隙。23(4)尾座的保養(yǎng):搖出尾座套筒,并擦凈涂油,以保證內(nèi)外清潔。(5)潤滑系統(tǒng)的保養(yǎng)a、清洗冷卻泵、濾油器和成液盤。b、保證油路暢通,油孔、油繩、油氈清潔無鐵屑c、檢查油質(zhì),保持良好,油杯齊全,油槽清晰。(6)電器的保養(yǎng):a、清掃電動機、電氣箱上的塵屑。b、電器裝置固定整齊。(7)外表的保養(yǎng):a、清洗車床外表及各罩蓋,保持其內(nèi)外整潔,無銹蝕、無油污。b、清洗三杠c、檢查并補齊各螺釘、手柄球、手柄。參考文獻1.段鐵群.《主軸箱設(shè)計》 ,科學出版社;2.于惠力,向敬忠,張春宜.《機械設(shè)計》 ,科學出版社;3.潘承怡,蘇相國. 《機械設(shè)計課程設(shè)計》 ,哈爾濱理工大學;4.戴署.《金屬切削機床設(shè)計》 ,機械工業(yè)出版社;5.陳易新, 《金屬切削機床課程設(shè)計指導書》 ; 241機械制造裝備設(shè)計課程設(shè)計任務書1、設(shè)計題目:普通車床主軸變速箱設(shè)計2、設(shè)計參數(shù):床身上最大工件回轉(zhuǎn)直徑:400mm主電動機功率:4 千瓦主軸最高轉(zhuǎn)速:1600 轉(zhuǎn)∕分主軸最低轉(zhuǎn)速:35.5 轉(zhuǎn)∕分3、設(shè)計要求:1、主軸變速箱設(shè)計計算;2、主軸變速箱結(jié)構(gòu)設(shè)計;3、繪制主軸變速箱裝配圖;4、編寫設(shè)計計算說明書。專 業(yè):機械設(shè)計制造及其自動化(2 班)學生姓名學 號2指導教師設(shè)計任務書車床的主參數(shù)(規(guī)格尺寸)和基本參數(shù)如下:工件最大回轉(zhuǎn)直徑D (mm)max正轉(zhuǎn)最低轉(zhuǎn)速nmin( )mir正轉(zhuǎn)最高轉(zhuǎn)速nmin( )ir電機功率N(kw)公比 ?400 35.5 1600 4 1.411目 錄設(shè)計任務書.2目 錄.4第 1 章 機床用途、性能及結(jié)構(gòu)簡單說明.6第 2 章 設(shè)計部分的基本技術(shù)特性和結(jié)構(gòu)分析.72.1 車床主參數(shù)和基本參數(shù) .72.2 確定傳動公比 7?2.3 擬定參數(shù)的步驟和方法 .72.3.1 極限切削速度 Vmax、Vmin .72.3.2 主軸的極限轉(zhuǎn)速 .8第 3 章 設(shè)計部分的運動設(shè)計.93.1 主電機功率—— 動力參數(shù)的確定 93.2 確定結(jié)構(gòu)式 .93.3 確定結(jié)構(gòu)網(wǎng) 103.4 繪制轉(zhuǎn)速圖和傳動系統(tǒng)圖 103.5 確定各變速組此論傳動副齒數(shù) 113.6 核算主軸轉(zhuǎn)速誤差 12第 4 章 設(shè)計部分的動力計算.134.1 帶傳動設(shè)計 134.2 計算轉(zhuǎn)速的計算 144.3 齒輪模數(shù)計算及驗算 144.4 傳動軸最小軸徑的初定 194.5 主軸合理跨距的計算 204.6 軸承的選擇 214.7 鍵的規(guī)格 214.8 變速操縱機構(gòu)的選擇 .224.9 主軸合理跨距的計算 .224.10 軸承壽命校核 232第 5 章 設(shè)計部分的調(diào)節(jié)、潤滑、維護保養(yǎng)、技術(shù)要求及其它.24參考文獻.263第 1 章 機床用途、性能及結(jié)構(gòu)簡單說明機床技術(shù)參數(shù)有主參數(shù)和基本參數(shù),他們是運動傳動和結(jié)構(gòu)設(shè)計的依據(jù),影響到機床是否滿足所需要的基本功能要求,參數(shù)擬定就是機床性能設(shè)計。主參數(shù)是直接反映機床的加工能力、決定和影響其他基本參數(shù)的依據(jù),如車床的最大加工直徑,一般在設(shè)計題目中給定,基本參數(shù)是一些加工件尺寸、機床結(jié)構(gòu)、運動和動力特性有關(guān)的參數(shù),可歸納為尺寸參數(shù)、運動參數(shù)和動力參數(shù)。通用車床工藝范圍廣,所加工的工件形狀、尺寸和材料各不相同,有粗加工又有精加工;用硬質(zhì)合金刀具又用高速鋼刀具。因此,必須對所設(shè)計的機床工藝范圍和使用情況做全面的調(diào)研和統(tǒng)計,依據(jù)某些典型工藝和加工對象,兼顧其他的可能工藝加工的要求,擬定機床技術(shù)參數(shù),擬定參數(shù)時,要考慮機床發(fā)展趨勢和同國內(nèi)外同類機床的對比,使擬定的參數(shù)最大限度地適應各種不同的工藝要求和達到機床加工能力下經(jīng)濟合理。機床主傳動系因機床的類型、性能、規(guī)格和尺寸等因素的不同,應滿足的要求也不一樣。設(shè)計機床主傳動系時最基本的原則就是以最經(jīng)濟、合理的方式滿足既定的要求。在設(shè)計時應結(jié)合具體機床進行具體分析,一般應滿足的基本要求有:滿足機床使用性能要求。首先應滿足機床的運動特性,如機床主軸油足夠的轉(zhuǎn)速范圍和轉(zhuǎn)速級數(shù);滿足機床傳遞動力的要求。主電動機和傳動機構(gòu)能提供足夠的功率和轉(zhuǎn)矩,具有較高的傳動效率;滿足機床工作性能要求。主傳動中所有零部件有足夠的剛度、精度和抗震性,熱變形特性穩(wěn)定;滿足產(chǎn)品的經(jīng)濟性要求。傳動鏈盡可能簡短,零件數(shù)目要少,以便節(jié)約材料,降低成本。4第 2 章 設(shè)計部分的基本技術(shù)特性和結(jié)構(gòu)分析2.1 車床主參數(shù)和基本參數(shù)車床的主參數(shù)(規(guī)格尺寸)和基本參數(shù)如下:工件最大回轉(zhuǎn)直徑D (mm)max正轉(zhuǎn)最低轉(zhuǎn)速nmin( )mir正轉(zhuǎn)最高轉(zhuǎn)速nmin( )ir電機功率N(kw)公比 ?400 35.5 1600 4 1.412.2 確定傳動公比 ?根據(jù)【1】 公式(3-2)因為已知 , , =1.4178P 07.45.316minax??R??znR?∴Z= +1=12?lgnR根據(jù)【1】 表 3-5 標準公比 。這里我們?nèi)藴使认盗?=1.417P??因為 =1.41=1.066,根據(jù)【1】 表 3-6 標準數(shù)列。首先找到最小極限轉(zhuǎn)速 35.5,再7P每跳過 5 個數(shù)取一個轉(zhuǎn)速,即可得到公比為 1.41 的數(shù)列:35.5,50,71,100,140,200,280,400,560,800,1120,16002.3 擬定參數(shù)的步驟和方法2.3.1 極限切削速度 Vmax、Vmin根據(jù)典型的和可能的工藝選取極限切削速度要考慮:允許的切速極限參考值如下:表 1.1加 工 條 件 Vmax(m/min) Vmin(m/min)硬質(zhì)合金刀具粗加工鑄鐵工件 30~50硬質(zhì)合金刀具半精或精加工碳 150~3005鋼工件螺紋加工和鉸孔 3~82.3.2 主軸的極限轉(zhuǎn)速計算車床主軸極限轉(zhuǎn)速時的加工直徑,則主軸極限轉(zhuǎn)速應為結(jié)合題目條件,取標準數(shù)列數(shù)值,=25r/minmin取 41.??考慮到設(shè)計的結(jié)構(gòu)復雜程度要適中,故采用常規(guī)的擴大傳動。各級轉(zhuǎn)速數(shù)列可直接從標準的數(shù)列表中查出,按標準轉(zhuǎn)速數(shù)列為:35.5,50,71,100,140,200,280,400,560,800,1120,16006第 3 章 設(shè)計部分的運動設(shè)計3.1 主電機功率——動力參數(shù)的確定合理地確定電機功率 N,使機床既能充分發(fā)揮其性能,滿足生產(chǎn)需要,又不致使電機經(jīng)常輕載而降低功率因素。根據(jù)題設(shè)條件電機功率為 4KW??蛇x取電機為:Y112M-4 額定功率為 4KW,滿載轉(zhuǎn)速為 1440r/min。3.2 確定結(jié)構(gòu)式已知 Z= x3b2aa,b 為正整數(shù),即 Z 應可以分解為 2 和 3 的因子,以便用 2、3 聯(lián)滑移齒輪實現(xiàn)變速。對于 Z=13,可以按照 12=2×3×2 傳動式(剔除最小的一級) ,有 6 種結(jié)構(gòu)式和對應的結(jié)構(gòu)網(wǎng)。分別為:, , ,??????????????????????由于本次設(shè)計的機床 I 軸裝有摩擦離合器,在結(jié)構(gòu)上要求有一齒輪的齒根圓大于離合器的直徑。初選 的方案。1263從電動機到主軸主要為降速變速,若使變速副較多的變速組放在較接近電動機處可使小尺寸零件多些,大尺寸零件少些,節(jié)省材料,也就是滿足變速副前多后少的原則,因此取 12=2×3×2 方案為好。設(shè)計車床主變速傳動系時,為避免從動齒輪尺寸過大而增加箱體的徑向尺寸,在降速變速中,一般限制限制最小變速比 ;為避免擴大傳動誤差,減少震動噪41min?u聲,在升速時一般限制最大轉(zhuǎn)速比 。斜齒圓柱齒輪傳動較平穩(wěn),可取2ax?。因此在主變速鏈任一變速組的最大變速范圍5.2max?u。在設(shè)計時必須保證中間變速軸的變速范圍??)10~8(5.)2~(minax?uR最小。綜合上述可得:主傳動部件的運動參數(shù) , =35.5, Z=12 =1.41160maxmin?73.3 確定結(jié)構(gòu)網(wǎng)根據(jù)“前多后少”,“先降后升”,前密后疏,結(jié)構(gòu)緊湊的原則易知第二擴大組的變速范圍 r=φ (P3-1)x=1.414=3.95〈8,滿足要求.圖 2-1 結(jié)構(gòu)網(wǎng) 1263??3.4 繪制轉(zhuǎn)速圖和傳動系統(tǒng)圖(1)選擇電動機:采用 Y 系列封閉自扇冷式鼠籠型三相異步電動機。(2)繪制轉(zhuǎn)速圖:8(3)畫主傳動系統(tǒng)圖。根據(jù)系統(tǒng)轉(zhuǎn)速圖及已知的技術(shù)參數(shù),畫主傳動系統(tǒng)圖如圖 2-3:1-2 軸最小中心距:A 1_2min1/2(Zmaxm+2m+D)軸最小齒數(shù)和:S zmin(Zmax+2+D/m)3.5 確定各變速組此論傳動副齒數(shù)(1)Sz 100-124,中型機床 Sz=70-100?(2)直齒圓柱齒輪 Zmin 18-24,m 4??9圖 2-3 主傳動系統(tǒng)圖(7)齒輪齒數(shù)的確定。變速組內(nèi)取模數(shù)相等,據(jù)設(shè)計要求 Zmin≥18~24,齒數(shù)和Sz≤100~124,由表 4.1,根據(jù)各變速組公比,可得各傳動比和齒輪齒數(shù),各齒輪齒數(shù)如表 2-2。表 2-2 齒輪齒數(shù)基本組 第一擴大組 第二擴大組傳動比1.41:1 1:2 1.41:1 1:1 1:1.41 2.8:1 1:2.8代號 Z1Z 'Z 2Z 'Z3Z 'Z4Z ’ Z5 Z5’ Z6Z 'Z7 Z7’齒數(shù) 31 22 18 35 48 34 41 41 34 48 96 34 34 963.6 核算主軸轉(zhuǎn)速誤差實際傳動比所造成的主軸轉(zhuǎn)速誤差,一般不應超過±10( -1)%,即?〈10( -1)%=4.1%n標 準 轉(zhuǎn) 速標 準 轉(zhuǎn) 速實 際 轉(zhuǎn) 速 ?10第 4 章 設(shè)計部分的動力計算4.1 帶傳動設(shè)計輸出功率 P=4kw,轉(zhuǎn)速 n1=1440r/min,n2=280r/min(1)確定計算功率:按最大的情況計算 P=4kw ,K 為工作情況系數(shù),查[1]表 3.5. 取 K=1.1pd=kAP=1.1X4=4.4kw(2)選擇 V 帶的型號:根據(jù) pd,n1=1440r/min 參考[1] 圖表 3.16 及表 3.3 選小帶輪直徑,查表選擇 A 型 V帶 d1=100mm(3)確定帶輪直徑 d1,d2小帶輪直徑 d1=100mm驗算帶速 v= d1n1/(60X1000)= X100X2880/(60X1000)=12.6m/s??從動輪直徑 d2=n1d1/n2=2880X100/2400=236mm 取 d2=224mm 查[1]表 3.3計算實際傳動比 i=d2/d1=224/100=2.24(4)定中心矩 a 和基準帶長 Ld[1]初定中心距 a00.7(d1+d2) a0 2(d1+d2))?226.8 a0 648 取 ao=300mm[2]帶的計算基準長度Ld0≈2a0+ /2(d1+d2)+(d2-d1)2/4a0?≈2x300+ /2(10+224)+(224-100)2/4X300≈650mm查[1]表 3.2 取 Ld0=630mm[3]計算實際中心距a≈a0+(Ld-Ld0)/2=300+(630-650)=290mm[4]確定中心距調(diào)整范圍amax=a+0.03Ld=290+0.03X630=308.9mmamin=a-0.015Ld=290-0.015X630=240.55mm11(5)驗算包角: 1=1800-(d 2-d1)/aX57.3 0=1800-(180-90)/290X57.30=17241240?(6)確定 V 帶根數(shù):確定額定功率:P 0由查表并用線性插值得 P0=0.15kw查[1]表 37 得功率增量 P0=0.13kwA查[1]表 38 得包角系數(shù) K =0.99?查[1]表 3 得長度系數(shù) Kl=0.81確定帶根數(shù):Z=P /{(P +△P )×K ×K }C0?L=3.65/(1.05+0.13)X0.99X0.81=2.89 取 Z=34.2 計算轉(zhuǎn)速的計算(1)主軸的計算轉(zhuǎn)速n j,由公式 n =n 得,主軸的計算轉(zhuǎn)速n j=735r/min,jmi)13/(??z取800 r/min。(2). 傳動軸的計算轉(zhuǎn)速 軸3=1250 r/min 軸2=2400 r/min,軸1=2400r/min。(2)確定各傳動軸的計算轉(zhuǎn)速。各計算轉(zhuǎn)速入表 3-1。表 3-1 各軸計算轉(zhuǎn)速(3) 確定 齒輪副的計算轉(zhuǎn)速。齒輪 Z 裝在主軸上其中只有 800r/min 傳遞全功率,故 Z j=800 r/min。'6 '6依次可以得出其余齒輪的計算轉(zhuǎn)速,如表 3-2。表 3-2 齒輪副計算轉(zhuǎn)速序號 Z1Z 2Z3Z `4Z5n j2400 2400 2400 1250 8004.3 齒輪模數(shù)計算及驗算(1)模數(shù)計算。一般同一變速組內(nèi)的齒輪取同一模數(shù),選取負荷最重的小齒輪,按軸 號 Ⅰ 軸 Ⅱ 軸 Ⅲ 軸計算轉(zhuǎn)速 r/min 2400 2400 125012簡化的接觸疲勞強度公式進行計算,即 mj=16338 可得各組的模數(shù),如321][)(jjmnuzP???表 3-3 所示。根據(jù) 和 計算齒輪模數(shù),根據(jù)其中較大值取相近的標準模數(shù):jmw=16338 =16338 mmj321][)(jjnuzP???????3213JmsniZKu????——齒輪的最低轉(zhuǎn)速 r/min;N——頂定的齒輪工作期限,中型機床推存: =15~24T T——轉(zhuǎn)速變化系數(shù); nk——功率利用系數(shù);N——材料強化系數(shù)。 q——(壽命系數(shù))的極值skmaxinssk,齒輪等轉(zhuǎn)動件在接取和彎曲交邊載荷下的疲勞曲線指數(shù) m 和基準順環(huán)次數(shù) C0——工作情況系數(shù)。中等中級的主運動: 1——動載荷系數(shù);2k——齒向載荷分布系數(shù);3——齒形系數(shù); Y根據(jù)彎曲疲勞計算齒輪模數(shù)公式為: 式中:N——計算齒輪轉(zhuǎn)動遞的額定功率 N=? dwNk——計算齒輪(小齒輪)的計算轉(zhuǎn)速 r/minjn——齒寬系數(shù) ,m?mb/??8Z1——計算齒輪的齒數(shù),一般取轉(zhuǎn)動中最小齒輪的齒數(shù):——大齒輪與小齒輪的齒數(shù)比, = ;(+)用于外嚙合, (-)號用i i12?Z于內(nèi)嚙合: 命系數(shù); sTNnqkk?::工作期限 , = ; TTmCn0613= =3.49Tk接 310256?= =1.8T彎 96=0.84 =0.58 nknk接=0.90 =0.55 =0.72 彎 q接 qk彎=3.49 0.84 0.58 0.55=0.94sk接 ??=1.8 0.84 0.90 0.72=0.99 時,取 = ,當 時,取 = ;s?minskmaxskminskmin= =0.85 =1.5; kax1=1.2 =1 =0.378 23Y許用彎曲應力,接觸應力,( )paM=354 =1750 ??W?pa??J?6 級材料的直齒輪材料選;24 熱處理 HRC59irTC31-2 軸由公式 mj=16338 可得 mj=3.28mm,取 m=3.5mm321][)(jjmnuzP??2-3 軸由公式 mj=16338 可得 mj=2.85mm,取 m=3.5mm321][)(jj?由于一般同一變速組內(nèi)的齒輪盡量取同一模數(shù),所以為了統(tǒng)一和方便如下取:根據(jù)有關(guān)文獻,也為了便于統(tǒng)一,在這里傳動齒輪統(tǒng)一取 m=3.5表 3-3 模數(shù)(2)基本組齒輪計算?;窘M齒輪幾何尺寸見下表組號 基本組 第一擴大組模數(shù) mm 3.5 3.514齒輪 Z1 Z1` Z2 Z2`齒數(shù) 31 22 18 35分度圓直徑 108.5 77 63 122.5齒頂圓直徑 115.5 84 70 129.5齒根圓直徑 99.75 68.25 54.25 113.75齒寬 24 24 24 24按基本組最小齒輪計算。小齒輪用 40Cr,調(diào)質(zhì)處理,硬度 241HB~246HB,平均取260HB,大齒輪用 45 鋼,調(diào)質(zhì)處理,硬度 229HB~246HB ,平均取 240HB。計算如下:① 齒面接觸疲勞強度計算:接觸應力驗算公式為??jfsj MPauBnNKzm??????)()1(02832彎曲應力驗算公式為:??wswPaBYnz?????)(109235式中 N----傳遞的額定功率(kW) ,這里取 N 為電動機功率,N=5kW;-----計算轉(zhuǎn)速( r/min). =800(r/min);jnjm-----初算的齒輪模數(shù)(mm), m=3.5(mm);B----齒寬(mm);B=24(mm);z----小齒輪齒數(shù);z=21;u----小齒輪齒數(shù)與大齒輪齒數(shù)之比,u=1.6;-----壽命系數(shù);sK=sTnNKq15----工作期限系數(shù);TKmTCn016?T------齒輪工作期限,這里取 T=15000h.;-----齒輪的最低轉(zhuǎn)速(r/min), =500(r/min)1n1n----基準循環(huán)次數(shù),接觸載荷取 = ,彎曲載荷取 =0C0C70C612?m----疲勞曲線指數(shù),接觸載荷取 m=3;彎曲載荷取 m=6;----轉(zhuǎn)速變化系數(shù),查【5】2 上,取 =0.60nKnK----功率利用系數(shù),查 【5】2 上,取 =0.78N N-----材料強化系數(shù),查【5】2 上, =0.60q q-----工作狀況系數(shù),取 =1.13K3K-----動載荷系數(shù),查【5】2 上,取 =12------齒向載荷分布系數(shù),查【5】2 上, =1 1 1KY------齒形系數(shù),查 【5】2 上,Y=0.386;----許用接觸應力(MPa),查【4】 ,表 4-7,取 =650 Mpa;??j? ??j?---許用彎曲應力( MPa) ,查【4】 ,表 4-7,取 =275 Mpa;w w根據(jù)上述公式,可求得及查取值可求得:=635 Mpa j????j?=78 Mpaww(3)第一擴大組齒輪計算。擴大組齒輪幾何尺寸見下表 齒輪 Z3 Z3` Z4 Z4` Z5 Z5`16齒數(shù) 48 34 41 41 34 48分度圓直徑 168 119 143.5 143.5 119 168齒頂圓直徑 175 126 150.5 150.5 126 175齒根圓直徑 159.25 110.25 134.75 134.75 110.25 159.25齒寬 24 24 24 24 24 24(4)第二擴大組齒輪計算。擴大組齒輪幾何尺寸見下表 齒輪 Z6 Z6` Z7 Z7`齒數(shù) 96 34 34 96分度圓直徑 336 119 119 336齒頂圓直徑 343 126 126 343齒根圓直徑 327.25 110.25 110.25 327.25齒寬 24 24 24 24按擴大組最小齒輪計算。小齒輪用 40Cr,調(diào)質(zhì)處理,硬度 241HB~246HB,平均取 260HB,大齒輪用 45 鋼,調(diào)質(zhì)處理,硬度 229HB~246HB ,平均取 240HB。同理根據(jù)基本組的計算,查文獻【6】 ,可得 =0.62, =0.77, =0.60, =1.1,nKNqK3=1, =1,m=3.5, =355;2K1j可求得:=619 Mpa j????j?=135Mpa ww174.4 傳動軸最小軸徑的初定由【5】式 6,傳動軸直徑按扭轉(zhuǎn)剛度用下式計算:d=1.64 (mm)??4?Tn或 d=91 (mm)4njN式中 d---傳動軸直徑(mm)Tn---該軸傳遞的額定扭矩(N*mm) T=9550000 ;JnN?N----該軸傳遞的功率(KW)----該軸的計算轉(zhuǎn)速jn---該軸每米長度的允許扭轉(zhuǎn)角, == 。??????01各軸最小軸徑如表 3-3。表 3-3 最小軸徑4.5 主軸合理跨距的計算由于電動機功率 P=3kw,根據(jù)【1】表 3.24,前軸徑應為 60~90mm。初步選取d1=80mm。后軸徑的 d2=( 0.7~0.9)d 1,取 d2=60mm。根據(jù)設(shè)計方案,前軸承為NN3016K 型,后軸承為圓錐滾子軸承。定懸伸量 a=124mm,主軸孔徑為 30mm。軸承剛度,主軸最大輸出轉(zhuǎn)矩 T=9550 =9550× =424.44N.mnP904設(shè)該機床為車床的最大加工直徑為 400mm。床身上最常用的最大加工直徑,即經(jīng)濟加工直徑約為最大回轉(zhuǎn)直徑的 50%,這里取 75%,即 180mm,故半徑為 0.09m;軸 號 Ⅰ 軸 Ⅱ 軸最小軸徑 mm 35 4018切削力(沿 y 軸) Fc= =4716N09.42背向力(沿 x 軸) Fp=0.5 Fc=2358N總作用力 F= =5272.65N2pC?此力作用于工件上,主軸端受力為 F=5272.65N。先假設(shè) l/a=2,l=3a=240mm。前后支承反力 RA 和 RB 分別為RA=F× =5272.65× =7908.97Nla?2401?RB=F× =5272.65× =2636.325Nl根據(jù) 文獻【1】式 3.7 得:Kr=3.39 得前支承的剛度:K A= 1.0Fr8.La9.0)(iza.1cos1689.69 N/ ;K B= 785.57 N/ ; = =2.15m?m?BAK57.6主軸的當量外徑 de=(80+60)/2=70mm,故慣性矩為I= =113.8×10-8m464)03.7.(???η= = =0.143aKEA6381.980.2??查【1】圖 3-38 得 =2.0,與原假設(shè)接近,所以最佳跨距 =124×2.0=240mml0 0l合理跨距為(0.75-1.5) ,取合理跨距 l=360mm。0l根據(jù)結(jié)構(gòu)的需要,主軸的實際跨距大于合理跨距,因此需要采取措施增加主軸的剛度,增大軸徑:前軸徑 D=100mm,后軸徑 d=80mm。前軸承采用雙列圓柱滾子軸承,后支承采用背對背安裝的角接觸球軸承。4.6 軸承的選擇I軸:與帶輪靠近段安裝雙列角接觸球軸承代號7007C 另一安裝深溝球軸承6012II軸:對稱布置深溝球軸承6009III軸:后端安裝雙列角接觸球軸承代號7015C 另一安裝端角接觸球軸承代號7010C19中間布置角接觸球軸承代號7012C4.7 鍵的規(guī)格I軸安裝帶輪處選擇普通平鍵規(guī)格:BXL=10X56 II軸選擇花鍵規(guī)格:N d =8X36X40X7 III軸選擇鍵規(guī)格:BXL=14X90 4.8 變速操縱機構(gòu)的選擇選用左右擺動的操縱桿使其通過桿的推力來控制II軸上的三聯(lián)滑移齒輪和二聯(lián)滑移齒輪。4.9 主軸合理跨距的計算設(shè)機床最大加工回轉(zhuǎn)直徑為?400mm,電動機功率P=4kw,,主軸計算轉(zhuǎn)速為800r/min。已選定的前后軸徑為: 定懸伸量a=85mm。162dm?1(0.7~85)dm?軸承剛度,主軸最大輸出轉(zhuǎn)矩:= 63.79.50=54N??設(shè)該車床的最大加工直徑 400mm。床身上最常用的最大加工直徑,即經(jīng)濟加工直徑約為最大回轉(zhuǎn)直徑的 50%,這里取 45%,即 125mm切削力(沿 y 軸) F c=250.346/0.125=2781N背向力(沿 x 軸) F p=0.5 Fc=1390N20總作用力 F= =3109N2pCF?此力作用于工件上,主軸端受力為 F=3109N。先假設(shè) l/a=2,l=3a=255mm。前后支承反力 RA和 RB分別為RA=F× =3109× Nla?852415??RB=F× =3109× Nl036根據(jù)《主軸箱設(shè)計》得: =3.39 得前支承的剛度:K A= rK1.0F8.La0.91.()cosiz?1376.69 N/ ;K B= 713.73 N/ ; = =1.93m?m?BA376.主軸的當量外徑 de=(85+65)/2=75mm,故慣性矩為I= =1.55×10-6m440.756??η= = =0.383aKEA16325098??查《主軸箱設(shè)計》圖 得 =2.5,與原假設(shè)接近,所以最佳跨距 =85×2.5=212.5mml0 0l合理跨距為(0.75-1.5) ,取合理跨距 l=250mm。0l根據(jù)結(jié)構(gòu)的需要,主軸的實際跨距大于合理跨距,因此需要采取措施增加主軸的剛度,增大軸徑:前軸徑 D=85mm,后軸徑 d=55mm。后支承采用背對背安裝的角接觸球軸承。4.10 軸承壽命校核由 П 軸最小軸徑可取軸承為 7008c 角接觸球軸承,ε=3;P=XF r+YFaX=1,Y=0 。對Ⅱ軸受力分析21得:前支承的徑向力 Fr=2642.32N。由軸承壽命的計算公式:預期的使用壽命 [L10h]=15000hL10h= × = × = h≥[L 10h]n1670?)PC(180673)28.10(?367.10()284.9524??=15000h軸承壽命滿足要求。第 5 章 設(shè)計部分的調(diào)節(jié)、潤滑、維護保養(yǎng)、技術(shù)要求及其它1、為了減少車床磨損,延長使用壽命,保證工件加工精度,應對車床的所有摩擦部位進行潤滑,并注意日常的維護保養(yǎng)。2、車床的潤滑形式常用以下幾種,(1)澆油潤滑:常用于外露的滑動表面,如導軌面和滑板導軌面等。(2)濺油潤滑:常用于密閉的箱體中。如車床的主軸箱中的傳動齒輪將箱底的潤滑油濺射到箱體上部的油槽中,然后經(jīng)槽內(nèi)油孔流到各潤滑點進行潤滑。(3)油繩導油潤滑:常用于進給箱和溜板箱的油池中。利用毛線即吸油又滲油的特性,通過毛線把油引入潤滑點,間斷地滴油潤滑。(4)彈子油杯注油潤滑:常用于尾座、中滑板搖手柄及三杠(絲杠、光杠、開關(guān)杠)支架的軸承處。定期的用油槍端頭油嘴壓下油杯上的彈子,將油注入。油嘴撤去,彈子又回復原位,封住注油口,以防塵屑入內(nèi)。(5)黃油杯潤滑:常用于交換齒輪箱掛輪架的中間軸或不經(jīng)常潤滑處。事先在黃油杯中加滿鈣基潤滑脂,需要潤滑時,擰進油杯蓋,則杯中的油脂就被擠壓到潤滑點中去。(6)油泵輸油潤滑:常用于轉(zhuǎn)速高、需要大量潤滑油連續(xù)強制潤滑的場合。如主22軸箱內(nèi)許多潤滑點就是采用這種方式。3、車床的潤滑要求: (1)車床上一般都有潤滑系統(tǒng)圖,應嚴格按照潤滑系統(tǒng)圖進行潤滑。(2)換油時,應先將廢油放盡,然后用煤油把箱體內(nèi)沖洗干凈后,在注入新機油,注油時應用網(wǎng)過濾,且油面不得低于油標中心線。主軸箱內(nèi)零件用油泵潤滑或飛濺潤滑。箱內(nèi)潤滑油一般三個月更換一次。主軸箱體上有一個油標,若發(fā)現(xiàn)油標內(nèi)無油輸出,說明油泵輸油系統(tǒng)有故障,應立即停車檢查斷油的原因,并修復。(3)進給箱上部油繩導油潤滑的儲油槽,每班應給該儲油槽加一次油。(4)交換齒輪箱中間齒輪軸軸承是黃油杯潤滑,每班一次,7 天加一次鈣基脂。(5)彈子油杯潤滑每班潤滑一次。導軌工作前后擦凈用油槍加油。5、車床日常保養(yǎng)要求:(1)每天工作后,切斷電源,對車床各表面、各罩殼、導軌面、絲杠、光杠、各操縱手柄和操縱桿進行擦拭,做到無油污、無鐵屑、車床外表整潔。(2)每周要求保養(yǎng)床身導軌面和中小滑板導軌面及轉(zhuǎn)動部位的整潔、潤滑。要求油眼暢通、油標清晰,清洗油繩和護床油毛氈,保持車床外表清潔和工作場地整潔。6、車床一級保養(yǎng)要求:車場運行 500 小時后,須進行一級保養(yǎng)。其保養(yǎng)以操作工人為主,在維修工人的配合下進行。保養(yǎng)時必須先切斷電源,然后按下述順序和要求進行。(1)主軸箱的保養(yǎng):a、清洗濾油器、使其無雜物b、檢查主軸鎖緊螺母有無松動,緊定螺釘是否擰緊。c、調(diào)整制動器及離合器摩擦片間隙。(2)交換齒輪箱的保養(yǎng):a、清洗齒輪、軸套,并在油杯中注入新油脂。b、調(diào)整齒輪嚙合間隙。c、檢查軸套有無晃動現(xiàn)象(3)滑板和刀架的保養(yǎng):拆洗刀架和中、小滑板,洗凈擦干后重新組裝,并調(diào)整中、小滑板與鑲條的間隙。23(4)尾座的保養(yǎng):搖出尾座套筒,并擦凈涂油,以保證內(nèi)外清潔。(5)潤滑系統(tǒng)的保養(yǎng)a、清洗冷卻泵、濾油器和成液盤。b、保證油路暢通,油孔、油繩、油氈清潔無鐵屑c、檢查油質(zhì),保持良好,油杯齊全,油槽清晰。(6)電器的保養(yǎng):a、清掃電動機、電氣箱上的塵屑。b、電器裝置固定整齊。(7)外表的保養(yǎng):a、清洗車床外表及各罩蓋,保持其內(nèi)外整潔,無銹蝕、無油污。b、清洗三杠c、檢查并補齊各螺釘、手柄球、手柄。參考文獻1.段鐵群.《主軸箱設(shè)計》 ,科學出版社;2.于惠力,向敬忠,張春宜.《機械設(shè)計》 ,科學出版社;3.潘承怡,蘇相國. 《機械設(shè)計課程設(shè)計》 ,哈爾濱理工大學;4.戴署.《金屬切削機床設(shè)計》 ,機械工業(yè)出版社;5.陳易新, 《金屬切削機床課程設(shè)計指導書》 ; 24