注塑模具外文翻譯原文
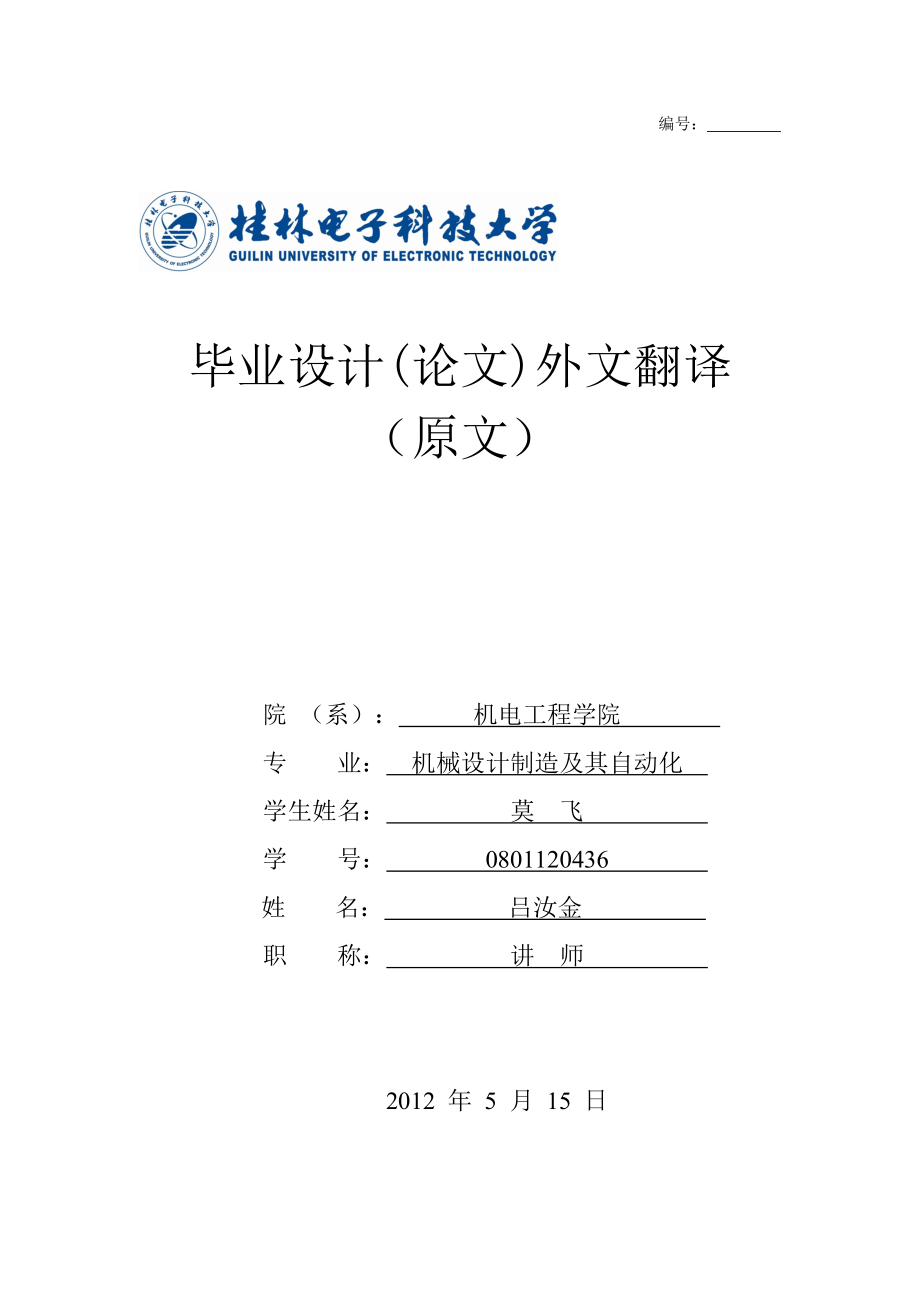


《注塑模具外文翻譯原文》由會(huì)員分享,可在線閱讀,更多相關(guān)《注塑模具外文翻譯原文(22頁珍藏版)》請?jiān)谘b配圖網(wǎng)上搜索。
1、桂林電子科技大學(xué)畢業(yè)設(shè)計(jì)(論文)報(bào)告用紙 編號: 畢業(yè)設(shè)計(jì)(論文)外文翻譯 (原文) 院 (系): 機(jī)電工程學(xué)院 專 業(yè): 機(jī)械設(shè)計(jì)制造及其自動(dòng)化 學(xué)生姓名: 莫 飛 學(xué) 號: 0801120436 姓 名: 呂汝金 職 稱: 講 師
2、2012 年 5 月 15 日 21 The Injection Molding The present situation that the mould makes at present and trend The mold is at the core of a plastic manufacturing process because its cavity gives a part its shape. This makes the mold at least as critical-and many cases more so-for the quality of
3、the end product as, for example, the plasticiting unit or other components of the processing equipment. The mould is important handicraft equipment,occupies decisive position in industrid departments such as consumer goods,electrical equipment electron,automobile , aircraft fabrication. The mould i
4、s important handicraft equipment , occupies decisive position in industrid departments such as consumer goods,electrical equipment electron,automobile , aircraft fabrication. Industrial product part rough process 75%, the finish machining 50% and plastic part 90% will be completed from the mould. Th
5、e Chinese mould market demand already reaches scale of 500 hundred million yuan at present. The automobile mould , the annual growth rate covering piece of mould especially will exceed 20 %; Also prompt building material mould development,various heterotype material the mould,wall surface and floor
6、mould become new mould growth point, plastic doors and windows and plastic drain-pipe increase to exceeding 30 by in the upcoming several years %; The home appliance mould annual growth rate will exceed 10 %; The IT industry year increases % speed equally exceeding 20,the need to the mould accounts
7、for 20 of mould marketplace %.2004 annual Chinese machine tools implements industry output value. Will continue to increase. Our country mould fabrication market potential is enormous. The basis data counts, in recent years,our country mould year gross output value reaches 3 billion U. S. dollar,en
8、trance exceeds 1 billion U. S. dollar,exceed 100 million U. S. dollar outlet. Increase by from 25% to increase to 2005 50% of 1995. The expert foretells that abroad: Asia portion being occupied by in mould fabrication in the whole world, will from 25% to increase to 2005 50% of 1995. Chinese mould
9、industry has been expanding by leaps and bounds,has formed east China and two big South China bases, and has expanded gradually arriving at other province. In 2002 (Shandong,Anhui,Sichuan) in 1996,mould manufacturing industry output value annual average growth 14% , grows by 25% in 2003. In 2003 our
10、 country mould output value is 45 billion RMB. The gross product place occupies the world the 3rd,exports a mould increases 33.5% compared to last year 336,800,000 U. S. dollar. But, contents low our country technology moulds already pile up in excess of requirement,very most support of accurate,com
11、plicated top grade mould imports. Every year the entrance mould exceeds 1 billion U. S. dollar. Exceed 100 million U. S. dollar outlet. Precise mould accuracy requires that 3 mu ms,large-scale moulds require that 8000 satisfied kN agree well with model force injection machine request in 2 ~;The min
12、itype mould needs the request satisfying the diameter 1 mm silent stock tube. At present, adopt quick-cutting to produce a mould already becoming the general trend that the mould makes, a few moulds have produced a manufacturer in abroad,high-speed machine tool large area has substituted the electri
13、c spark machine tool,quick-cutting has improved the mould efficacy greatly. Machine tool enterprise aims at mould manufacturing enterprises,some treating centres 60% all above of the machine tool producing a factory sells treating enterprise to a mould. The mould fabrication enterprise substituting
14、the electric spark finish machining mould gradually in abroad has adopt quick-cutting already commonly , quick-cutting has produced a mould already becoming the general trend that the mould makes gradually,has improved the mould efficacy and mass greatly. Adopt quick-cutting to replace electric spar
15、k producing a mould , can get on the stick obviously , improves mould accuracy,life time growing. 1. The Introduction of Injection Moulds. Plastic, which is one of the most versatile in the modern age, is widely used in many products throughout the world. Due to its ability to produce com
16、plex-shape plastic parts with good dimensional accuracy and very short cycle times, injection moulding has become the most important process for manufacturing plastic parts in the plastic industry today. However, the current plastics industry is under great pressure, due to the globalization of the
17、market, the short life cycle of product development, increasing product diversity, high demand of product quality. To meet such requirements, it is very important for this trade to adopt various advanced technologies which include information and Internet technology, CAD/CAE/CAM integration technolo
18、gy, concurrent engineering, artificial intelligence, and so on, to effectively aid the development of injection-moulded product. In injection moulding, the design of a mould is of critical importance for product quality and efficient processing. In most cases, quality of mould is responsible for th
19、e economics of the entire process. Injection mould design involves extensive empirical knowledge (heuristic knowledge) about the structure and functions of the components of the mould. Nowadays, mould design faces with increasing deadline pressures and the design itself is predominantly based upon e
20、xperience of the mould designer. Mould designers are required to possess thorough and broad experience, because detailed decisions require the knowledge of the interaction among various parameters. Unfortunately, it is presently impossible to cover the growing demand for such experienced designers.
21、 Therefore, intelligent CAD tools that can assist in the various tasks of the mould design process are very important to the productivity of the mould -making industry. The growing trend in global manufacturing is to a large extent supported by Internet, information technologies and global marketin
22、g. Nowadays, it is common to see that design, manufacturing and final assembly of a product are made in companies located in different parts of the world. The various parties concerned would need to share their expertise and experiences during the product development process. The current progress of
23、 Internet and information technologies can provide a solution to support and facilitate collaborative product developments among different geographically distributed enterprises. Developing an Internet-based intelligent mould design system as one of the module of a collaborative product development
24、system can provide an effective and feasible tool to aid the collaborative development of injection moulds in the small- and medium-sized enterprises to satisfy the stringent requirements of nowadays competitive global market. This paper presents an Internet-based intelligent mould design system us
25、ing Internet technology and knowledge-based approach. The system can shorten the design cycle of injection mould and can effectively aid the design and development works of injection moulds in the small-and medium-sized enterprises to meet the increasing pressure of the current competitive world mar
26、ket. The rest of the paper is organized as follows. Section 2 gives a brief introduction of injection mould design. Section 3 introduces earlier research works on mould design and related fields. The architecture of the Internet-based mould design system is presented in section 4. The knowledge-bas
27、ed part of the mould design system is described in section 5. Section 6 discusses the development of the system. 2. Injection mould design The basic features of an injection mould consist of cavity number and layout, feed system, cooling system, ejection system and mould construction. 2.1. Des
28、ign rules There are many rules for designing molds. These rules and standard practices are based on logic, past experience, convenience, and economy. For designing, mold making, and molding, it is usually of advantage to follow the rules. But occasionally, it may work out better if a rule is igno
29、red and an alternative way is selected. In this text, the most common rules are noted, but the designer will learn only from experience which way to go. The designer must ever be open to new ideas and methods, to new molding and mold materials that may affect these rules. A mould design project nor
30、mally starts with economic considerations, namely the question of how many parts can and should be produced in one mould in one shot in order to meet the delivery date and other requirements. This is follow by consideration of the arrangements of the cavities in the mould frame, which might directly
31、 include thoughts on the ease of ejection and subsequently, the connection between mouldings and runners and part quality (number, position and shape of gates). The feed system accommodates the molten plastic material coming from the injection nozzle of the moulding machine and distributes it into e
32、ach cavity. To remove the heat from the moulding, it is necessary to provide the mould with a cooling system. After the moulding has solidified and cooled down, it has to be removed from the mould by the ejection system. Mould is normally constructed by stacking several metal plates to form a rigid
33、body. It has to house various mould components in correct positions for the proper functioning of the mould. Mould construction normally involves the selection of mould bases and standard mould parts. For complicated plastic parts, some other mechanisms such as slides, unscrewing device, etc, might
34、also be involved in the whole mould structure. 2.2. Mold Material Depending on the processing parameters for the various processing methods as well as the length of the production run, the number of finished products to be produced, molds for plastics processing must satisfy a great variety of req
35、uirements. It is therefore not surprising that molds can be made from a very broad spectrum of materials, including-from a technical standpoint-such exotic materials as paper matched and plaster. However, because most processes require high pressures, often combined with high temperatures, metals st
36、ill represent by far the most important material group, with steel being the predominant metal. It is interesting in this regard that, in many cases, the selection of the mold material is not only a question of material properties and an optimum price-to-performance ratio but also that the methods u
37、sed to produce the mold, and thus the entire design, can be influenced. A typical example can be seen in the choice between cast metal molds, with their very different cooling systems, compared to machined molds. In addition, the production technique can also have an effect; for instance, it is oft
38、en reported that, for the sake of simplicity, a prototype mold is frequently machined from solid stock with the aid of the latest technology such as computer-aided (CAD) and computer-integrated manufacturing (CIM). In contrast to the previously used methods based on the use of patterns, the use of C
39、AD and CAM often represents the more economical solution today, not only because this production capability is available pin-house but also because with any other technique an order would have to be placed with an outside supplier. Overall, although high-grade materials are often used, as a rule st
40、andard materials are used in mold making. New, state-of-the art (high-performance) materials, such as ceramics, for instance, are almost completely absent. This may be related to the fact that their desirable characteristics, such as constant properties up to very high temperatures, are not required
41、 on molds, whereas their negative characteristics, e. g. low tensile strength and poor thermal conductivity, have a clearly related to ceramics, such as sintered material, is found in mild making only to a limited degree. This refers less to the modern materials and components produced by powder met
42、allurgy, and possibly by hot isocratic pressing, than to sintered metals in the sense of porous, air-permeable materials. Removal of air from the cavity of a mold is necessary with many different processing methods, and it has been proposed many times that this can be accomplished using porous meta
43、llic materials. The advantages over specially fabricated venting devices, particularly in areas where melt flow fronts meet, I, e, at weld lines, are as obvious as the potential problem areas: on one hand, preventing the texture of such surfaces from becoming visible on the finished product, and on
44、the other hand, preventing the microspores from quickly becoming clogged with residues (broken off flash, deposits from the molding material, so-called plate out, etc.). It is also interesting in this case that completely new possibilities with regard to mold design and processing technique result f
45、rom the use of such materials. 2.3. The basic mold 2.3.1. Mold cavity space The mold cavity space is a shape inside the mold, “excavated” in such a manner that when the molding material is forced into this space it will take on the shape of the cavity space and, therefore, the desired product.
46、 The principle of a mold is almost as old as human civilization. Molds have metals into sand forms. Such molds, which are still used today in foundries, can be used only once because the mold is destroyed to release the product after it has solidified. Today, we are looking for permanent molds that
47、can be used over and over. Now molds are made from strong, durable materials, such as steel, or from softer aluminum or metal alloys and even from certain plastics where a long mold life is not required because the planned production is small. In injection molding the plastic is injected into the ca
48、vity space with high pressure, so the mold must be strong enough to resist the injection pressure without deforming. 2.3.2. Number of cavities Many molds, particularly molds for larger products, are built for only cavity space, but many molds, especially large production molds, are built with 2
49、or more cavities. The reason for this is purely economical. It takes only little more time to inject several cavities than to inject one. For example, a 4-cavity mold requires only one-fourth of the machine time of a single-cavity mold. Conversely, the production increases in proportion to the numbe
50、r of cavities. A mold with more cavities is more expensive to build than a single-cavity mold, but not necessarily 4 times as much as a single-cavity mold. But it may also require a larger machine with larger platen area and more clamping capacity, and because it will use 4 times the amount of plast
51、ic, it may need a large injection unit, so the machine hour cost will be higher than for a machine large enough for the smaller mold. 2.3.3. Cavity shape and shrinkage The shape of the cavity is essentially the “negative” of the shape of the desired product, with dimensional allowance added to a
52、llow for shrinking of the plastic. The shape of the cavity is usually created with chip-removing machine tools, or with electric discharge machining, with chemical etching, or by any new method that may be available to remove metal or build it up, such as galvanic processes. It may also be created b
53、y casting certain metals in plaster molds created from models of the product to be made, or by casting some suitable hard plastics. The cavity shape can be either cut directly into the mold plates or formed by putting inserts into the plates. 2.4. Cavity and core By convention, the hollow porti
54、on of the cavity space is called the cavity. The matching, often raised portion of the cavity space is called the core. Most plastic products are cup-shaped. This does not mean that they look like a cup, but they do have an inside and an outside. The outside of the product is formed by the cavity, t
55、he inside by the core. The alternative to the cup shape is the flat shape. In this case, there is no specific convex portion, and sometimes, the core looks like a mirror image of the cavity. Typical examples for this are plastic knives, game chips, or round disks such as records. While these items a
56、re simple in appearance, they often present serious molding problems for ejection of the product. The reason for this is that all injection molding machines provide an ejection mechanism on the moving platen and the products tend to shrink onto and cling to the core, from where they are then ejected
57、. Most injection molding machines do not provide ejection mechanisms on the injection side. 2.5. Polymer Processing Polymer processing, in its most general context, involves the transformation of a solid (sometimes liquid) polymeric resin, which is in a random form (e.g., powder, pellets, beads
58、), to a solid plastics product of specified shape, dimensions, and properties. This is achieved by means of a transformation process: extrusion, molding, calendaring, coating, thermoforming, etc. The process, in order to achieve the above objective, usually involves the following operations: solid t
59、ransport, compression, heating, melting, mixing, shaping, cooling, solidification, and finishing. Obviously, these operations do not necessarily occur in sequence, and many of them take place simultaneously. Shaping is required in order to impart to the material the desired geometry and dimensio
60、ns. It involves combinations of viscoelastic deformations and heat transfer, which are generally associated with solidification of the product from the melt. Shaping includes: two-dimensional operations, e.g. die forming, calendaring and coating; three-dimensional molding and forming operations.
61、 Two-dimensional processes are either of the continuous, steady state type (e.g. film and sheet extrusion, wire coating, paper and sheet coating, calendaring, fiber spinning, pipe and profile extrusion, etc.) or intermittent as in the case of extrusions associated with intermittent extrusion blow mo
62、lding. Generally, molding operations are intermittent, and, thus, they tend to involve unsteady state conditions. Thermoforming, vacuum forming, and similar processes may be considered as secondary shaping operations, since they usually involve the reshaping of an already shaped form. In some cases,
63、 like blow molding, the process involves primary shaping (pair-son formation) and secondary shaping (pair son inflation). Shaping operations involve simultaneous or staggered fluid flow and heat transfer. In two-dimensional processes, solidification usually follows the shaping process, whereas s
64、olidification and shaping tend to take place simultaneously inside the mold in three dimensional processes. Flow regimes, depending on the nature of the material, the equipment, and the processing conditions, usually involve combinations of shear, extensional, and squeezing flows in conjunction with
65、 enclosed (contained) or free surface flows. The thermo-mechanical history experienced by the polymer during flow and solidification results in the development of microstructure (morphology, crystallinity, and orientation distributions) in the manufactured article. The ultimate properties of the
66、 article are closely related to the microstructure. Therefore, the control of the process and product quality must be based on an understanding of the interactions between resin properties, equipment design, operating conditions, thermo-mechanical history, microstructure, and ultimate product properties. Mathematical modeling and computer simulation have been employed to obtain an understanding of these interactions. Such an approach has gained more importance in view of the expanding utilizatio
- 溫馨提示:
1: 本站所有資源如無特殊說明,都需要本地電腦安裝OFFICE2007和PDF閱讀器。圖紙軟件為CAD,CAXA,PROE,UG,SolidWorks等.壓縮文件請下載最新的WinRAR軟件解壓。
2: 本站的文檔不包含任何第三方提供的附件圖紙等,如果需要附件,請聯(lián)系上傳者。文件的所有權(quán)益歸上傳用戶所有。
3.本站RAR壓縮包中若帶圖紙,網(wǎng)頁內(nèi)容里面會(huì)有圖紙預(yù)覽,若沒有圖紙預(yù)覽就沒有圖紙。
4. 未經(jīng)權(quán)益所有人同意不得將文件中的內(nèi)容挪作商業(yè)或盈利用途。
5. 裝配圖網(wǎng)僅提供信息存儲(chǔ)空間,僅對用戶上傳內(nèi)容的表現(xiàn)方式做保護(hù)處理,對用戶上傳分享的文檔內(nèi)容本身不做任何修改或編輯,并不能對任何下載內(nèi)容負(fù)責(zé)。
6. 下載文件中如有侵權(quán)或不適當(dāng)內(nèi)容,請與我們聯(lián)系,我們立即糾正。
7. 本站不保證下載資源的準(zhǔn)確性、安全性和完整性, 同時(shí)也不承擔(dān)用戶因使用這些下載資源對自己和他人造成任何形式的傷害或損失。
最新文檔
- 2023年六年級數(shù)學(xué)下冊6整理和復(fù)習(xí)2圖形與幾何第7課時(shí)圖形的位置練習(xí)課件新人教版
- 2023年六年級數(shù)學(xué)下冊6整理和復(fù)習(xí)2圖形與幾何第1課時(shí)圖形的認(rèn)識與測量1平面圖形的認(rèn)識練習(xí)課件新人教版
- 2023年六年級數(shù)學(xué)下冊6整理和復(fù)習(xí)1數(shù)與代數(shù)第10課時(shí)比和比例2作業(yè)課件新人教版
- 2023年六年級數(shù)學(xué)下冊4比例1比例的意義和基本性質(zhì)第3課時(shí)解比例練習(xí)課件新人教版
- 2023年六年級數(shù)學(xué)下冊3圓柱與圓錐1圓柱第7課時(shí)圓柱的體積3作業(yè)課件新人教版
- 2023年六年級數(shù)學(xué)下冊3圓柱與圓錐1圓柱第1節(jié)圓柱的認(rèn)識作業(yè)課件新人教版
- 2023年六年級數(shù)學(xué)下冊2百分?jǐn)?shù)(二)第1節(jié)折扣和成數(shù)作業(yè)課件新人教版
- 2023年六年級數(shù)學(xué)下冊1負(fù)數(shù)第1課時(shí)負(fù)數(shù)的初步認(rèn)識作業(yè)課件新人教版
- 2023年六年級數(shù)學(xué)上冊期末復(fù)習(xí)考前模擬期末模擬訓(xùn)練二作業(yè)課件蘇教版
- 2023年六年級數(shù)學(xué)上冊期末豐收園作業(yè)課件蘇教版
- 2023年六年級數(shù)學(xué)上冊易錯(cuò)清單十二課件新人教版
- 標(biāo)準(zhǔn)工時(shí)講義
- 2021年一年級語文上冊第六單元知識要點(diǎn)習(xí)題課件新人教版
- 2022春一年級語文下冊課文5識字測評習(xí)題課件新人教版
- 2023年六年級數(shù)學(xué)下冊6整理和復(fù)習(xí)4數(shù)學(xué)思考第1課時(shí)數(shù)學(xué)思考1練習(xí)課件新人教版