某臥式車床主軸零件的加工工藝分析說明書刪減版.doc
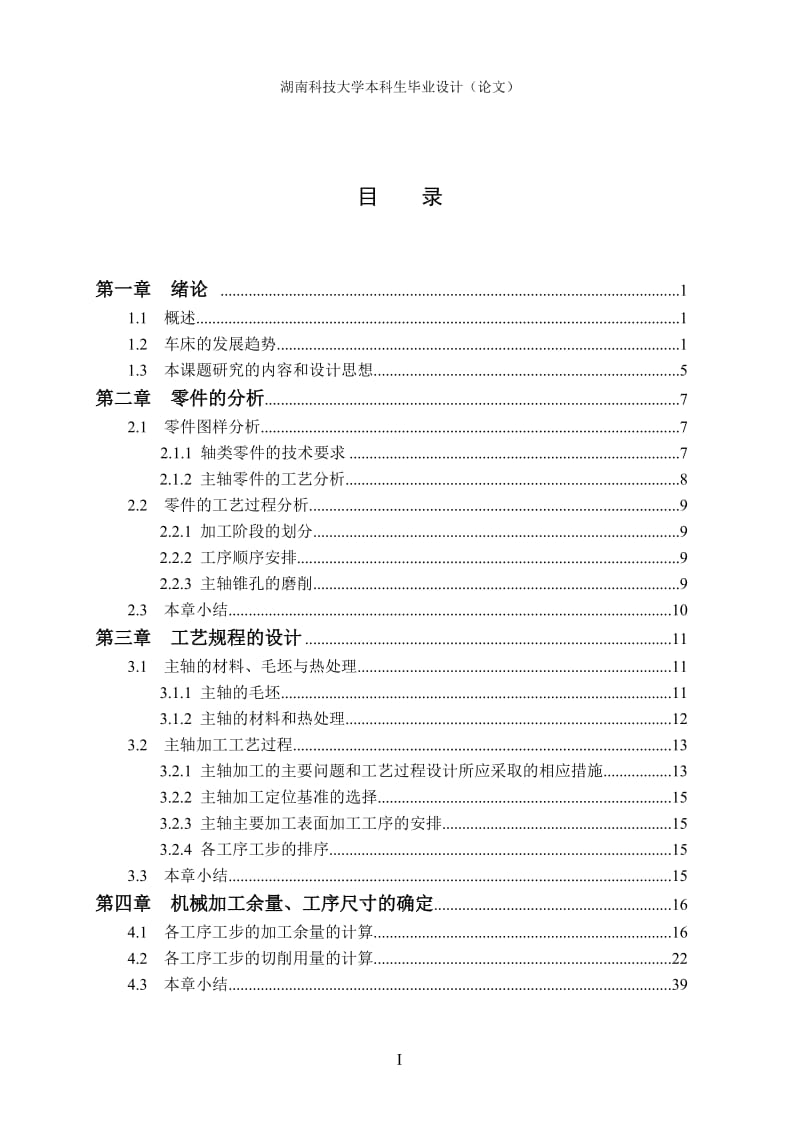


《某臥式車床主軸零件的加工工藝分析說明書刪減版.doc》由會(huì)員分享,可在線閱讀,更多相關(guān)《某臥式車床主軸零件的加工工藝分析說明書刪減版.doc(26頁(yè)珍藏版)》請(qǐng)?jiān)谘b配圖網(wǎng)上搜索。
1、湖南科技大學(xué)本科生畢業(yè)設(shè)計(jì)(論文) 目 錄 第一章 緒論 1 1.1 概述 1 1.2 車床的發(fā)展趨勢(shì) 1 1.3 本課題研究的內(nèi)容和設(shè)計(jì)思想 5 第二章 零件的分析 7 2.1 零件圖樣分析 7 2.1.1 軸類零件的技術(shù)要求 7 2.1.2 主軸零件的工藝分析 8 2.2 零件的工藝過程分析 9 2.2.1 加工階段的劃分 9 2.2.2 工序順序安排 9 2.2.3 主軸錐孔的磨削 9 2.3 本章小結(jié)
2、 10 第三章 工藝規(guī)程的設(shè)計(jì) 11 3.1 主軸的材料、毛坯與熱處理 11 3.1.1 主軸的毛坯 11 3.1.2 主軸的材料和熱處理 12 3.2 主軸加工工藝過程 13 3.2.1 主軸加工的主要問題和工藝過程設(shè)計(jì)所應(yīng)采取的相應(yīng)措施 13 3.2.2 主軸加工定位基準(zhǔn)的選擇 15 3.2.3 主軸主要加工表面加工工序的安排 15 3.2.4 各工序工步的排序 15 3.3 本章小結(jié) 15 第四章 機(jī)械加工余量、工序尺寸的確定 16 4
3、.1 各工序工步的加工余量的計(jì)算 16 4.2 各工序工步的切削用量的計(jì)算 22 4.3 本章小結(jié) 39 I 第五章 專用夾具的設(shè)計(jì) 40 5.1 鉆床夾具的設(shè)計(jì) 41 5.1.1 鉆床夾具的分析 41 5.1.2 切削力的計(jì)算 41 5.2 磨床夾具的設(shè)計(jì) 41 5.2.1 夾緊裝置及夾具體設(shè)計(jì) 41 5.2.2 磨削力的計(jì)算 42 5.3 本章小結(jié) 42 第六章 結(jié)論 43 參考文獻(xiàn) 44 致謝 45 附錄A:外文資料翻譯譯文 附錄B:銑鍵槽數(shù)控加工程序編制 附錄C
4、:磨錐孔夾具裝配圖 附錄D:磨錐孔前支架零件圖 附錄E:鉆孔夾具裝配圖 附錄F:某臥式車床主軸零件簡(jiǎn)圖 附錄G:某臥式車床主軸毛坯圖 附錄H:快換鉆套零件圖 附錄I:鉆模板零件圖 附錄J:機(jī)械加工工藝過程 第一章 緒 論 1.1 概述 精密機(jī)床有進(jìn)給系統(tǒng),進(jìn)給系統(tǒng):進(jìn)給伺服系統(tǒng)是數(shù)控裝置和機(jī)床的中間聯(lián)接環(huán)節(jié),是數(shù)控系統(tǒng)的重要組成部分,同樣的主軸系統(tǒng)也是現(xiàn)代機(jī)床的重要部分,而相對(duì)于不同滾動(dòng)導(dǎo)軌或者滾動(dòng)支承等功能元件的應(yīng)用遍,也使進(jìn)給箱和滑板箱的構(gòu)造變得簡(jiǎn)化。 1.2 車床的發(fā)展趨勢(shì) 科學(xué)技術(shù)的發(fā)展以及世界先進(jìn)制造技術(shù)的興起和不斷成熟,對(duì)數(shù)控加工技術(shù)提
5、出了更高的要求;超高速切削、超精密加工等技術(shù)的應(yīng)用,對(duì)數(shù)控機(jī)床的數(shù)控系統(tǒng)、伺服性能、主軸驅(qū)動(dòng)、機(jī)床結(jié)構(gòu)等提出了更高的性能指標(biāo);FMS的迅速發(fā)展和CIMS的不斷成熟,又將對(duì)數(shù)控機(jī)床系統(tǒng)的性能日臻完善,數(shù)控技術(shù)的應(yīng)用領(lǐng)域日益擴(kuò)大。當(dāng)今數(shù)控機(jī)床正在不斷采用最新的、高精度 (1) 高精度化 現(xiàn)代科學(xué)技術(shù)的發(fā)展、新材料以及新零件的出現(xiàn),對(duì)精密加工技術(shù)不斷提出新的要求,提高加工精度,。其精度已從微米到亞米級(jí)別,乃至納米級(jí)。提高數(shù)控機(jī)床的加工精度,一般可通過減少的誤差和采用機(jī)床誤差補(bǔ)償技術(shù)來實(shí)現(xiàn)。在減少CNC系統(tǒng)控制誤差方面,通常采用提高數(shù)控系統(tǒng)的分辨率、提高位置檢測(cè)精度、在位置伺服系統(tǒng)中采用前饋控
6、制與非線性控制等方法。在機(jī)床誤差補(bǔ)償技術(shù)方面,除采用齒隙補(bǔ)償、絲杠螺距已由10μm提高到 5μm,精密級(jí)加工中心的加工精度則從(3~5)μm,提高到(1~1.5)μm (2) 高速化 提高生產(chǎn)率是數(shù)控機(jī)床追求的基本目標(biāo)之一。數(shù)控機(jī)床高速化可充分發(fā)揮現(xiàn)代刀具材料的性能,不但可以大幅度提高加工效率,降低加工成本,而且還可以提高理念的表面加工質(zhì)量和精度,對(duì)制造業(yè)實(shí)現(xiàn)高效、優(yōu)質(zhì)、低成本生產(chǎn)具有廣泛的適用性。要實(shí)現(xiàn)數(shù)控設(shè)備高速化對(duì)由微小程序段構(gòu)成的加工程序進(jìn)行高速處理,以計(jì)算出伺服電動(dòng)機(jī)的移動(dòng)間。告訴數(shù)控加工源于20世紀(jì)90年代初,以電主軸(實(shí)現(xiàn)高主軸轉(zhuǎn)速)和只想電動(dòng)機(jī)(實(shí)現(xiàn)高直線移動(dòng)速度)的應(yīng)用為
7、特征,是進(jìn)給的加速度達(dá)到(1~2)g m/s。目前車削和銑度,當(dāng)分辨率為1μm時(shí),達(dá)到100m/min(有的到200m/min)以上;當(dāng)分辨率為0.1μm時(shí),達(dá)到24m/min以上。自動(dòng)換刀速度在1s以內(nèi),小線段插補(bǔ)進(jìn)給速度達(dá)到12m/min。 同樣的現(xiàn)代車床也想著高柔性化、高自、模式識(shí)別技術(shù))、復(fù)合化、高可靠性、網(wǎng)絡(luò)化、開放式體系結(jié)構(gòu)。 1.3 本課題研究的內(nèi)容和設(shè)計(jì)思想 軸的構(gòu)造影響要素有:軸在設(shè)配中裝置地位及方式;軸上裝置的零件的品種、數(shù)量、尺寸、以及軸銜接的方較大。軸端部和軸承過盈配合,端部外表要求精度偏高。軸向定位用軸肩,與軸上零件相配合。其余軸向定位均采納鍵連
8、接的方式,以滿足傳遞扭矩的需求。 保證主軸前端軸頸的位置精度,還有支承軸頸之間的位置精度,普遍使用組合磨削法,在裝夾中加工這些外表面。 按照主軸的工藝分析可知,在主軸上最好能找到一個(gè)合適的定位基準(zhǔn),保證滿足個(gè)表面間的位置精度。為了達(dá)到這個(gè)要求,在主軸加工時(shí)經(jīng)常采用雙頂尖定位來體現(xiàn)主軸的軸線,既符合“采用雙頂尖定位時(shí),背吃刀量不宜太大,因此在粗加工時(shí)因?yàn)榍邢饔嗔看?,故一般只能采用外圓表面及主軸在深孔加工時(shí),由于切除量很大,一般也只能采用外院作為定位基準(zhǔn)(即一夾一托的定位方式)。 主軸的莫氏錐孔需與支承軸頸同軸,故在加工莫氏錐孔時(shí)應(yīng)以支承軸頸為定位基準(zhǔn),以打消基準(zhǔn)不重合所引起的定位
9、誤差。 主軸是帶孔的零件,在加工過程錐堵頭適用在主軸孔錐度較小時(shí)(如莫氏錐孔)使用,當(dāng)錐孔的錐度較大時(shí)(如銑床主軸前端錐孔)或圓柱孔時(shí),可采用錐套心軸,采用錐堵頭或錐套心軸定位時(shí),錐堵頭及錐套心軸上的定位基準(zhǔn)面必須與該軸上的兩頂尖同軸,在使用時(shí)應(yīng)盡量減少拆裝誤差對(duì)定位精度的影響。 對(duì)車床主軸的精確要求有多高,就體和夾緊。 在機(jī)械加工中,對(duì)夾具本體的一般要求,主要有下列幾點(diǎn):1、夾具的構(gòu)造應(yīng)與其用途及生產(chǎn)規(guī)模相適應(yīng):夾具的用的工藝范圍,以達(dá)到保證產(chǎn)品質(zhì)量為主要目的。在大批量生產(chǎn)中,夾具的作用,除夾緊裝置等高效夾具及自動(dòng)化夾具。2、保證工件精度:正確設(shè)計(jì)定位件及夾緊裝置,以保證工件在夾具中的
10、定位精度,并應(yīng)注意夾緊力的方向、大小和作用點(diǎn)的合理選擇,防止工件的夾緊變形或損傷。正確設(shè)計(jì)刀具導(dǎo)引件,以保證在加工過程中正確的導(dǎo)引刀具,或在加工之前校正刀具的位置。正確設(shè)計(jì)夾具與機(jī)床相連接的元件,使夾具在機(jī)過程中振動(dòng)。3、保證使用方便和安全,在設(shè)計(jì)夾具時(shí),必須為工人著想,主要應(yīng)注部分,在設(shè)計(jì)時(shí)就應(yīng)考慮到調(diào)整方便,必要時(shí)應(yīng)設(shè)置便于調(diào)整的輔助基準(zhǔn)面或輔助裝置。便于測(cè)量,設(shè)計(jì)夾具時(shí)應(yīng)考慮到便。如果留足夠的空隙便于量具的進(jìn)入;在某些情處理作用了的平衡問題:對(duì)夾具上各種作用力的平衡問題要處理得當(dāng),不能使夾具在加工時(shí)發(fā)生振動(dòng),影響表面加工的光潔度,也不能因此而使夾具或工件發(fā)生變形,主要尺寸和技術(shù)條件一般應(yīng)
11、按誤差分析來確定,并應(yīng)該注意便于檢驗(yàn)。還要注意結(jié)構(gòu)應(yīng)便于裝配和裝配工藝的合理性。6、注意夾具與機(jī)床、輔助工具、刀具、量具之間的聯(lián)系:為了生產(chǎn)出合格的產(chǎn)品,在所有生存工具,如機(jī)床設(shè)備、夾具、輔助工具、刀具、量具等都是冷卻液的流通和切削的帶走,為此,對(duì)于大型銑床夾具,有時(shí)可將本體底板的上表面當(dāng)作斜面,或者 - 23 - 第2章 零件的分析 2.1 零件圖樣分析 如圖2.1車床主軸的零件要表面有:支承軸頸、配合軸頸、莫氏錐孔、前端圓錐面及端面和鎖緊螺紋、帶滑動(dòng)齒輪的花鍵等表面。 圖2.1 某臥式車床主軸零件簡(jiǎn)圖 車床主軸部件是機(jī)床的驅(qū)動(dòng)力等載荷的作用。各類機(jī)床的主軸部件都要
12、保證主軸在一定的載荷和轉(zhuǎn)速下,能帶動(dòng)以對(duì)主軸部件有旋轉(zhuǎn)精度、主軸剛度、抗震性、熱變形、耐磨性這方面有一定的要求。 2.1.1 軸類零件的技術(shù)要求 1)尺寸精度 方式與滾動(dòng)軸承頸處的尺軸承的精度等級(jí)選取。凡是與齒輪相配的軸頸處的尺寸精度,應(yīng)按高精度等級(jí)查取。這些主要表面IT5~IT8級(jí) 2) 形狀精度 軸頸處的集合形狀與精度主要是柱度,一般應(yīng)限制在尺寸公差之內(nèi)。凡與滾動(dòng)輪查取。一般常取3~8μm,并用框格標(biāo)注。 3)位置精度 軸類零件是旋轉(zhuǎn)零件,軸上裝有傳動(dòng)件,希望其轉(zhuǎn)動(dòng)穩(wěn)定,無震動(dòng)和噪聲,這就是要求軸上跳動(dòng)來標(biāo)注。 4)表面粗糙度 支承軸頸處表面粗糙度取Ra0.16
13、~0.63μm,配合表面的粗糙度取Ra0.63~2.5μm 2.1.2 主軸零件的工藝分析 支承軸頸與滾動(dòng)軸承相配,向圓跳動(dòng)和斜向圓跳動(dòng)。其圓度誤差同樣會(huì)影響主軸的旋轉(zhuǎn)精度,產(chǎn)生徑向圓跳動(dòng),因此對(duì)其應(yīng)提出較高的精度與表面粗糙度要求。 主軸前端的莫氏錐孔是用來安同軸也是機(jī)床出廠的主要檢驗(yàn)要求,反映了整臺(tái)機(jī)床的精度。此外要保證錐孔與頂尖間接觸良好,其精度要求見下表 2.1.3 表2.1.3 莫氏錐孔的精度要求(mm) 項(xiàng)目 莫氏錐孔對(duì)主軸支承軸頸的徑向圓跳動(dòng) 莫氏錐孔接
14、觸面積 近主軸端 距軸端300mm處 普通機(jī)床 0.005~0.01 0.01~0.03 65%~80% 精密機(jī)床 0.002~0.005 0.005~0.01 >85% 主軸前端的圓錐面和端面是安裝夾具的定位基面,該圓錐面軸向必須與支承軸頸的軸線同軸,端面必須與支承軸頸軸線垂直,否則會(huì)產(chǎn)生定位誤差,影響夾具的定位精度,使工件產(chǎn)生形狀主軸上的螺紋表面中心線也必須與支承軸頸的軸線同軸,否則會(huì)使裝配上的螺母端面產(chǎn)生端面圓跳動(dòng),導(dǎo)致與其線纜的滾動(dòng)軸承內(nèi)圈中心線傾斜,
15、引起主軸徑向圓跳動(dòng)和端面圓跳動(dòng),并使時(shí),會(huì)使主軸產(chǎn)生軸向竄動(dòng),使工件產(chǎn)生端面的平面度誤差,在加工螺紋時(shí)又會(huì)產(chǎn)生螺距誤差。 主軸上安裝傳動(dòng)件的表面也應(yīng)與支承軸頸同軸,否則在高速運(yùn)轉(zhuǎn)時(shí),傳動(dòng)件會(huì)產(chǎn)生振動(dòng)和噪聲而影響齒輪的傳動(dòng)精裝中加工完成,以滿足他們之間的位置精度要求。而加工主軸前端的莫氏錐孔又應(yīng)采用基準(zhǔn)重合的原則,即以支承軸頸為定位基準(zhǔn)加工錐孔,以減少定位誤差,提高定位 2.2 零件的工藝過程分析 2.2.1 加工階段的劃分 加工過程可劃分為以下步驟: 由于主軸是帶孔的階梯軸成個(gè)表面的粗加工,再完成各個(gè)表面的半精加工,最后完成精加工。對(duì)尺寸精度、表面粗糙度要求特別高的軸頸,還應(yīng)安排光
16、整加工。主要表面的精加工應(yīng)放在最后進(jìn)行。 這樣安排的優(yōu)點(diǎn)是 2.2.2 工序順序安排 工序順序的安排主要根據(jù)先粗后精、基面先行、先主后次的原則,在軸類零件的熱處理工序一般有三種形工具的前錐面與錐孔,在精加工之前安排表面淬火,以提高耐磨性。 1) 如果深孔經(jīng)過一次鉆削而成時(shí),應(yīng)安排在調(diào)質(zhì)后進(jìn)行,因?yàn)檎{(diào)質(zhì)處理會(huì)引起主軸的彎曲變形,既影響棒料的通過,又會(huì)引起主軸高速轉(zhuǎn)動(dòng)的不平衡,影響旋轉(zhuǎn)精度。如果深孔鉆削后加一道鏜孔工序,則鉆孔可安排在調(diào)質(zhì)處理之前,熱處理彎曲變形后可在鏜孔工序加以修正。 2) 深孔加工應(yīng)安排在安排在較后的工序,可避免一開始就采用雙中心孔作為定位基面,所以深孔加工安
17、排在較后對(duì)剛性影響不大時(shí),可采用由小到大的加工順序。 3) 次要表面的加工,如銑鍵槽或粗磨之后、精加工之前進(jìn)行。因?yàn)槿绻才旁诰囈郧般婃I槽,則在精車時(shí)由于斷續(xù)切削產(chǎn)生振動(dòng),既影響加工質(zhì)量,又容易損壞刀具;另一方面,鍵槽的支承軸頸的軸線的同軸度精度,因此螺紋精加工應(yīng)在表面淬火之后進(jìn)行。 2.2.3主軸的錐孔磨削半精加工應(yīng)安排在深孔加工之后進(jìn)行,以便能采用錐堵頭后繼續(xù)進(jìn)行外圓加工。錐孔的精加工則安排在主軸的支承軸頸的精加工之后,并以支精加工要采用專用夾具,使主軸的兩支承軸頸定位在夾具的定位元件上,并且使工件的中心用浮動(dòng)連接,只是帶動(dòng)工件的旋轉(zhuǎn),以保證工件的定位精度不受內(nèi)圓磨床床頭回轉(zhuǎn)
18、主軸的回轉(zhuǎn)運(yùn)動(dòng)誤差的影響,也可以減少機(jī)床本身振動(dòng)對(duì)床的一個(gè)重要的精度要求。 2.3 本章小結(jié) 本章主要介紹了主軸的作用,以及它在加工中的工藝分析。 第三章 工藝規(guī)程的設(shè)計(jì) 3.1 主,或直徑相差較大的階梯軸,均應(yīng)采用鍛件,因?yàn)殄懠梢杂休^高的抗拉、抗扭和抗彎的性能,對(duì)不重要的光軸或直徑相差不大的階梯軸,可采用熱軋棒料或者冷拉棒料,并且適合用于小批量生產(chǎn)。自由鍛一般用在小批量生產(chǎn),模鍛件一般用在大批量生產(chǎn),同時(shí)在大批量生產(chǎn)時(shí)如果使用被貫穿孔的無縫鋼管毛坯還會(huì)節(jié)省材料和減少人力損耗。生產(chǎn)時(shí)余量小。它適于在大批量條件下鍛造特殊并且對(duì)精度要求較高的主軸,所以在選擇毛坯時(shí)應(yīng)選擇鍛件毛
19、坯。 3.1.2 主軸的材料和熱處理 主軸的材料應(yīng)根據(jù)旋轉(zhuǎn)精度、剛度、抗震性、溫升和熱變形、精度保持性來選擇。主軸的剛性可通過彈性模量E值反映。鋼的E值較大,所以,主軸材料首選鋼材。值得注意的是,鋼的彈性模量E的數(shù)值和鋼的種類及熱處理方式無關(guān),即無論選擇的是普通鋼或者合金鋼,其E值基本上是一樣的。所以在選擇材料上應(yīng)該選擇中碳鋼(價(jià)格實(shí)惠較為便宜),只是在載荷特別大和有較大沖擊時(shí),或者精密機(jī)床主軸,才考慮選用合金鋼。熱處理對(duì)硬,但是為了提高基礎(chǔ)剛度,防止裝拆軸承時(shí)敲碰損傷軸頸的配合表面,多數(shù)主軸軸頸仍進(jìn)行調(diào)質(zhì)或局部淬火處理。單采用滑動(dòng)軸承時(shí),為了減少磨損,軸頸必須有很高的硬度。 一般軸類零
20、件常用45鋼,采用相應(yīng)的調(diào)質(zhì)處理后,可獲得一定的強(qiáng)度、韌度和耐磨性。對(duì)中等精度而有較高應(yīng)力工序,并且安排在粗磨之后進(jìn)行,是因?yàn)闈B氮變形小,且滲氮層較薄之故。 1.主軸熱處理 (1)減少鍛造應(yīng)力、防止變形和開裂 主軸毛坯在鍛造過程中,加工溫度過高時(shí),則會(huì)使金屬內(nèi)部組織的晶粒變得粗大;而鍛造溫度如果過低時(shí),又會(huì)有過大的殘余應(yīng)力和組織不均勻,甚至材料會(huì)開裂。這兩種情況都會(huì)致使主軸強(qiáng)度降低,同時(shí)由于表面泠硬而不易切削。所以先進(jìn)行熱處理再粗加工,退火和正火都屬于(2)預(yù)備熱處理 常用預(yù)備熱處理工藝方法有三大類:退火、正火及調(diào)質(zhì)。剛才通過預(yù)備熱處理可以細(xì)化晶粒、均勻成分及組織、消除內(nèi)應(yīng)力,為最終
21、熱處理做好組織準(zhǔn)備。因此,預(yù)備熱處理是減少應(yīng)力、防較大及正火后硬度偏高的零件,應(yīng)采用退火工藝。共析鋼及過共析鋼多采用球化退化;亞共析鋼則應(yīng)采用完全退火(一般用等溫退火代替);對(duì)毛坯中成分偏析嚴(yán)重的零件應(yīng)采用高溫?cái)U(kuò)散退火均勻其成分及組織;需較徹底消除內(nèi)應(yīng)力時(shí)應(yīng)采用去應(yīng)力退火;對(duì)零件綜合力學(xué)性調(diào)質(zhì)作為預(yù)先熱處理。 (3)最終熱處理 最終熱處理工藝方法很多,主要包括淬火、回火、表面淬火及化學(xué)熱處理等。通過最終熱處理,工件可獲得所需組織及性能,滿足使用要求。 ①淬火方法選擇:一般根據(jù)工件的材料類別、形狀尺寸、淬透性大小及硬度要求等選擇合適的淬火方法。對(duì)于形狀簡(jiǎn)單的淬火;而合金鋼件多采用單介質(zhì)油
22、冷淬火;為了減小淬火內(nèi)應(yīng)力淬火、雙介質(zhì)淬火、分級(jí)淬火、等溫淬火等方法;對(duì)于某些只需局部硬化的工件可進(jìn)行局部淬火;對(duì)于精密零件和②回火方法選擇:淬火后的工件必須及時(shí)進(jìn)行回火,而且回火應(yīng)充分。對(duì)于要求高硬度、高耐磨性的工件應(yīng)采用低溫回火;對(duì)于要求較高韌性、較高強(qiáng)度的工件應(yīng)進(jìn)行中溫回火;而對(duì)于要求具有良好綜合力學(xué)性能的工件則要進(jìn)行高溫回火。 ③表面處理及化學(xué)熱處理方法選擇;當(dāng)應(yīng)的表面熱處理方法。對(duì)于表層要求高的硬度、強(qiáng)度、耐磨性及疲勞強(qiáng)度,而心碳工藝;對(duì)于承載不大,但精度要求較高的合金鋼,多采用滲氮處理。為了提高化學(xué)熱狐貍中還可以采用低溫及中溫氣體碳氮共滲。另外,還可根據(jù)需要對(duì)工件進(jìn)行其他滲金屬或
23、非金屬處理;為了提高工件的抗高溫氧化性可以滲鋁;為了提高覆其他超硬、耐蝕材料。 當(dāng)然,在實(shí)際生產(chǎn)過程中,由于聽見毛坯的類型及加工工藝過程的不同,再具體確定熱處理方法及安排工藝則,而應(yīng)根據(jù)實(shí)際情況進(jìn)行靈活調(diào)整。 3.2 主軸加工工藝過程 3.2.1 主軸加工的主要問題和在加工過程中需要采取的一些措施 主軸加工中主要需要解決的問題是如何保證主軸支承軸頸四個(gè)要點(diǎn),其要點(diǎn)分別是:形狀、尺寸、位置精度和表面粗糙度,其次是主軸前端內(nèi)、外錐的表面粗糙度、形狀、位置精度。零件的精度件超過尺寸公差的1主軸支承軸頸的形狀、尺寸和表面粗糙度的條件相對(duì)較高所以應(yīng)采用精密磨削的辦法來滿足,通過精密磨削的零件表面
24、有效接觸面積可達(dá)85%~90%,另外需要注意的是一定要在磨削前提高精基準(zhǔn)的精度。 同時(shí)精密磨削的辦法也同樣可以滿足主軸表面粗度也可以達(dá)到要求。組合磨削法可和支承軸頸之間的位置精度,而且采用組合磨削法可以在同一次裝夾過程中加工這些表面。如圖3.1所磨削在兩個(gè)工位上同時(shí)進(jìn)行,另外機(jī)床上帶有兩個(gè)獨(dú)立的砂輪架,兩個(gè)工位分別精磨前、后軸頸錐面,后者用角度成形砂輪,從而精密磨削前端支承面和主軸短錐面。 圖3.1 磨削組合 主軸錐孔的定位基準(zhǔn)通常采用支承軸頸A、B作為定位基準(zhǔn)來得出相對(duì)于支承軸頸的位置精度,而讓被加工主軸以防精度上的影響;因?yàn)楸患庸ぶ鬏S零件和磨床頭架主軸只是柔性連接帶動(dòng)工件
25、A、B的精度。軸頸A和B應(yīng)該要達(dá)到一定的精度在精磨前端錐孔之前,主軸錐孔的磨削采用錐堵和錐套心軸,如圖3.2所示。 圖3.2 錐堵與錐套心軸 在主軸外圓磨削時(shí),工件的中心孔是磨削加工的定位基準(zhǔn),它比車削工件中心孔有更為嚴(yán)格的要求。60中心孔內(nèi)錐面圓動(dòng)要控制在1μm之內(nèi)。60內(nèi)錐表面粗糙度值一,應(yīng)有保護(hù)錐。對(duì)于特殊要求淬火前要修研中心孔。在主軸通孔上加工完畢時(shí),一定要用帶頂尖孔的工件錐度在不斷的提高,作為可以起到附加定位的工藝錐堵也應(yīng)該得到相應(yīng)的提高。 雖然主軸上的通孔的加工忽視的問題,所以排屑方式也需要解決。另外加工主軸深孔的時(shí)候應(yīng)該考慮把這一過程安排在工藝過程的開始,因?yàn)樗鼘儆诖旨?/p>
26、工。 外圓磨削中常見的缺陷的產(chǎn)生原因和消除方法是: 1、 工件表面出現(xiàn)直波形振紋,螺過大等。需要保持砂輪平衡,修正好砂輪;保持磨床精度,選用合適的磨削用量等。 2、 工件表面產(chǎn)生燒傷。產(chǎn)生運(yùn)用主要是砂輪磨料粒度,砂輪硬度選擇不當(dāng),磨削用量選擇不當(dāng),砂輪太鈍。磨削液供給不不合要求;工件剛度差,中心孔形狀不正確,砂輪過鈍,調(diào)整好機(jī)床,減少機(jī)床、工件的彈性變形,選擇合理磨削用量,修正好砂輪。 在加工完內(nèi)孔時(shí)最好進(jìn)行內(nèi)孔的精度檢測(cè),內(nèi)孔的精度檢測(cè)有三大類:尺寸精度的檢測(cè):1、用塞規(guī)檢驗(yàn) 2、 用內(nèi)徑百分表檢驗(yàn)??椎男螤罹葯z測(cè):1、圓度誤差檢驗(yàn) 2、圓柱度誤差檢驗(yàn)。孔的同軸度誤差檢驗(yàn):
27、孔的同軸度是指被測(cè)圓柱面軸線,對(duì)基準(zhǔn)軸線不共軸的程度。 3.2.2 主軸加工定位基準(zhǔn)的選擇 主軸加工中,在選擇定位基準(zhǔn)時(shí)應(yīng)遵循兩個(gè)主要準(zhǔn)則,一個(gè)是“互為基準(zhǔn)準(zhǔn)則”一個(gè)則是“基準(zhǔn)重合”這樣才能夠保證各個(gè)主要表面間的相互位置精度,所以只要有可能,就在同一次裝夾中盡量加工合的原出來,有利于保證加工面之間的位置精度。所以有必要在實(shí)心軸在粗加工之前先打頂尖孔。對(duì)于空心軸便是以外圓定位,加工通孔,同時(shí)在兩端孔口加工出內(nèi)60度的錐堵或帶有錐堵的心軸裝夾工件。 為了確保主軸內(nèi)錐面與支承軸頸的同軸度要求,最好按“互為基準(zhǔn)”的原則選擇基準(zhǔn)面。比如車大端莫氏6號(hào)內(nèi)錐磨莫氏6號(hào)內(nèi)錐孔時(shí),再以兩圓柱面為定位基準(zhǔn)面
28、;粗、精磨兩個(gè)支承軸頸的1:12錐面時(shí),仍然用錐堵頂尖孔定位;精磨莫氏6號(hào)內(nèi)錐孔不能放在最初加工,在最后加工時(shí),不能間接以精加工后前支承軸頸和另一圓柱面定位。定位基準(zhǔn)每多轉(zhuǎn)換一次,都會(huì)使主軸的加工精度進(jìn)步一點(diǎn)。 3.2.3 主軸主要加工表面加工工序的安排 要滿足高精度要求,在機(jī)粗磨精磨。 主軸的加工工藝過程可劃為三個(gè)加工,半精車外圓,錐孔、車錐面,精車外圓,鉆大頭端面各孔等);精加工階段(包括粗、精磨外圓、錐孔、錐面,精銑鍵槽等)。 車床主軸的表面的加工順序有如下幾種計(jì)劃: 1.圓表面粗加工(用頂尖孔定位)外圓表面半精加工(還是用頂尖孔定位)鉆通孔(用半精加工之后外圓定位, 錐孔精加
29、工(用精加工之后外圓表面定位)。 2.通孔 (用毛坯外圓定位,加工之后配錐堵)外圓外表粗加工(用錐堵頂尖孔定位)錐孔粗加工(用半精加工之后外圓定位,加工之后配錐堵)外圓精加工(用錐堵頂尖孔定位)錐孔粗加工用精加工之后的外圓定位)。 3.外圓表面粗加工(用頂尖孔來精加工之后外圓表面來定位,加工之后配錐堵)外圓表面精加(用錐堵頂尖孔來定位)錐孔精加工(用精加工外圓表面來定位)。 4. 外圓表面粗加工(用頂尖孔來定位)外圓表面半精加工(用頂尖孔來定位)鉆通孔(用半精加工之后外圓表面來定位)錐孔粗加工(用精加工之后外圓表面來定位)錐孔精加工(用精加工之后外圓表面來定位,加工之后配錐堵)外圓表面精
30、加(用錐堵頂尖孔來定位)相應(yīng)較大,所合適,然而在關(guān)于實(shí)心軸在成批生產(chǎn)情況下是可行的。 計(jì)劃2:錐孔粗加工的過程在外圓表面精加工之后,錐孔粗加工時(shí)用精加工外圓表面定位時(shí),會(huì)導(dǎo)致外圓表面一些);另外在精加工外圓時(shí)用錐堵頂尖孔來定位,有一定幾率破壞錐孔精度,另一方面錐堵的加工誤差還會(huì)導(dǎo)致內(nèi)錐和表面外圓表面產(chǎn)生比較大的同軸誤差,所以不采用此方案。 計(jì)劃4:錐孔精加工過程在外不會(huì)影響或破壞外圓表面的精度。另外,用外圓表面定位,定位也相對(duì)穩(wěn)定而可靠,相對(duì)而言此方案為最佳。 當(dāng)非次要表面的加工先后擬定后,就要正當(dāng)?shù)膮⑴c非主要表面加工工序。對(duì)主軸而言非主要表面一般指的是鍵槽、螺孔、螺紋等。這些非主要表面
31、的加工一般不易出現(xiàn)殘次品,所以如果可以盡量安排在工序后邊進(jìn)行,因?yàn)橹饕砻婕庸ひ坏┏隽藦U品,非主要表面也就沒必要加工了,這樣可以避免時(shí)間上的浪費(fèi)。 同時(shí)也不能將它就直接放在最后,為了防止在加工非主要表面過程中損害了已精加工過的主要表面精度。 對(duì)凡是需要在淬硬表面上進(jìn)行加工的鍵槽、螺孔等,都理應(yīng)安排在淬火前加工完成,否則一旦表面淬硬后就以保證。而主軸螺紋,因它和主軸支承軸頸間有一定的同軸度上的要求,所以螺紋加工應(yīng)放在最終的熱處理之后的精加工工序時(shí)進(jìn)行,那么半精加工之后的殘余應(yīng)力重新分布所導(dǎo)致的變形和熱處理之后的變形,就不會(huì)干擾螺紋的加工精度了。,為的是讓后續(xù)車間內(nèi)生產(chǎn)出的廢品不會(huì)被誤認(rèn)為是前
32、車間產(chǎn)生的。在主軸全部加工工序結(jié)束以后要經(jīng)過整個(gè)的檢驗(yàn)方可入庫(kù)。 3.2.4 各工序工步的排序 工序1 銑端面打中心孔 安裝1:工步1 粗銑右端面,保證尺寸486mm;工步2 打中心孔。 安裝2:工步1 粗銑左端面,保證總尺寸874mm;工步2 打中心孔。 工序2粗車外圓 3.3 本章小結(jié) 本章主要為了介紹主軸材料的前期加工和在加工過程中使用的措施和相應(yīng)的加工序。 第四章 機(jī)械加工余量、工序尺寸的確定 4.1 各工序工步的加工余量的計(jì)算 主軸零件材料為45鋼HBS207~241,生產(chǎn)類型為小批生產(chǎn),采用模鍛毛坯。 根據(jù)上述原始資料及加工工藝,分別確
33、定各加工表面的機(jī)械加工余量、工序尺寸及毛坯尺寸如下: (1)小端端面加工余量 總余量10 機(jī)械設(shè)計(jì)工藝軟件版 工序尺寸36.3 半精車余量1.3 《機(jī)械制造工藝金屬切削機(jī)床設(shè)計(jì)手冊(cè)》附表1.2-4 粗車余量Z=10-1.3=8.7 毛坯尺寸45 ( 粗車余量22.5-0.5-1.25-1.8=18.95,毛坯尺寸Φ131 (15)外圓M1151.5-2 總余量16,磨削余量0.3,工序尺寸Φ115 精車余量1.25,工序尺寸Φ115.3 半精車余量9.25,工序尺寸Φ116.
34、25 粗車余量16-0.3-1.25-9.25=5.2,毛坯尺寸Φ131 (16)外圓Φ112 總余量19,切槽余量12,工序尺寸Φ112 半精車余量1.8,工序尺寸Φ124 粗車余量19-12-1.8=5.2,毛坯尺寸Φ131 (17)外圓Φ120 總余量11,半精車余量5.8,工序尺寸Φ120 粗車余量11-5.8=5.2,毛坯尺寸Φ131 (18)外圓尺寸Φ198 總余量10,半精車余量4.8,工序尺寸Φ202.8 粗車余量10-4.8=5.2,毛坯尺寸Φ208 (19
35、)外短錐Φ106.373 總余量101.627,精磨余量0.1,工序尺寸106.373 粗磨余量0.507,工序尺寸106.473 精 (26)銑花鍵Φ89y6 粗銑160123.68,精銑160143.68 4.2 各工序工步的切削余量的計(jì)算 ㈠已知毛坯小端長(zhǎng)度方向上的加工余量為10mm,粗車時(shí)分兩次加工,ap=0.46mm;毛坯大端長(zhǎng)度方向的加工余量為13mm,粗車時(shí)分三次加工ap=3.05mm。 ㈡進(jìn)給量f,根據(jù)《機(jī)械加工工藝設(shè)計(jì)手冊(cè)》表得: 當(dāng)?shù)稐U的尺寸為16mm25mm時(shí),ap為3時(shí),以及工件的直徑為100m
36、m時(shí),f=0.5 r=0.5mm/f ㈢計(jì)算切削速度 按《機(jī)械加工工藝手冊(cè)》 v=m/min. (4.1) 當(dāng)f≦0.7時(shí),其中=242,Xv=0.15,yv=0.35,m=0.2T=60 ⒈ 對(duì)小端端面有 v=108.2(m/min) 確定機(jī)床轉(zhuǎn)速: (4.2) 按《機(jī)械加工工藝手冊(cè)》表得:v=135.2(m/min) n=320(r/min) 因n=344.6(r/min
37、)與之相近的機(jī)床轉(zhuǎn)速為315r/min和430r/min,選取n=430(r/min),如果選315r/min,則速度損失太大 所以實(shí)際切削速度: 切削深度:?jiǎn)芜呌嗔縜=3mm,共進(jìn)3刀; 進(jìn)給量:根據(jù)《機(jī)械加工工藝手冊(cè)》表可得:f=0.6mm/r 計(jì)算切削速度: 確定主軸轉(zhuǎn)速: 按機(jī)床選取n=430r/min,所以實(shí)際切削速度: ⑸粗車外圓φ89f6外圓: 切削深度:?jiǎn)芜呌嗔縜=2mm,共進(jìn)2刀; 進(jìn)給量:根據(jù)《機(jī)械加工工藝手冊(cè)》表可得:f=0.6mm/r 計(jì)算切削速度: 確定主軸轉(zhuǎn)速: 按機(jī)床選取n=
38、430r/min,所以實(shí)際切削速度: ⑹粗車外圓φ90外圓: 切削深度:?jiǎn)芜呌嗔縜=2.82mm,共進(jìn)5刀; 進(jìn)給量:根據(jù)《機(jī)械加工工藝手冊(cè)》表可得:f=0.8mm/r>0.7mm/r, 故 計(jì)算切削速度: 確定主軸轉(zhuǎn)速: 按機(jī) 進(jìn)給量:《機(jī)械加工工藝手冊(cè)》表得:選用f=0.7mm/r; 計(jì)算切削速度: 確定主軸轉(zhuǎn)速: 按機(jī)床選取n=160r/min,所以實(shí)際切削速度: ⑵半精車φ198外圓: 切削深度:?jiǎn)芜呌嗔縜=2.4mm,共進(jìn)2刀; 進(jìn)給量:根據(jù)《機(jī)械加工工藝手冊(cè)》表可得:f=0.8mm
39、/r>0.7mm/r, 故 計(jì)算切削速度: 確定主軸轉(zhuǎn)速: 按機(jī)床選取n=160r/min,所以實(shí)際切削速度: ⑶半精車φ106.373外圓 切削深度: 單邊余量a=0.9mm,共進(jìn)2刀; 進(jìn)給量:根據(jù)《機(jī)械加工工藝手冊(cè)》表得:選用f=0.8mm/r; 計(jì)算切削速度: 確定主軸轉(zhuǎn)速: 按機(jī)床選取n=160r/min,所以實(shí)際切削速度: 6. 仿形車小端各部 按機(jī)床選取n=900r/min,所以實(shí)際切削速度: ⑵仿形31.6m/min 確定主軸轉(zhuǎn)速:n 按機(jī)床選取n=560r/min,所以實(shí)際切削
40、速度: ⑷仿形車φ75.25外圓且錐度為1:12 由《機(jī)械加工工藝實(shí)用手冊(cè)》表可知錐度為1:12的圓錐角為 44618′8″。 切削深度:?jiǎn)芜呌嗔縜=0.925mm,共進(jìn)刀2次; 進(jìn)給量根據(jù)《機(jī)械加工工藝實(shí)用手冊(cè)》表得:當(dāng)Ra=3.2μm時(shí),選用f=0.7mm/r, 計(jì)算切削速度:=122.4m/min 確定主軸轉(zhuǎn)速:n 按機(jī)床選取n=560r/min,所以實(shí)際切削速度: ⑸仿形車φ80h5外圓 切削深度:?jiǎn)芜呌嗔縜=0.9mm,共進(jìn)刀1次; 進(jìn)給量:選用f=0.5mm/r; 計(jì)算切削速度:=138.1m/min 確定主軸轉(zhuǎn)速:n
41、 按機(jī)床選取n=560r/min,所以實(shí)際切削速度: ⑹仿形車φ89f5外圓 切削深度:?jiǎn)芜呌嗔縜=1mm,共進(jìn)刀1次; 進(jìn)給量:選用f=0.5mm/r; 計(jì)算切削速度:=136m/min 確定主軸轉(zhuǎn)速: 按機(jī)床選取n=560r/min,所以實(shí)際切削速度: ⑺仿形車φ90g5外圓 切削深度:?jiǎn)芜呌嗔縜=0.85mm,共進(jìn)刀1次; 進(jìn)給量:選用f=0.5mm/r; 計(jì)算切削速度:=134.2m/min 確定 ⒏ 車小端錐孔(配1:20錐堵) 切削深度:?jiǎn)芜呌嗔縜=1mm,走2刀; 進(jìn)給量:根據(jù)《機(jī)械加工工藝實(shí)用手冊(cè)》表選用f=0.5mm/r; 計(jì)算切削速度
42、:根據(jù)《機(jī)械加工工藝手冊(cè)》表得: =136m/min 確定主軸轉(zhuǎn)速: 按機(jī)床選取n=1000r/min,所以實(shí)際切削速度: 9. 車大端面錐孔(配莫氏6號(hào)錐堵)外短錐及端面 ⑴車大端錐孔(配莫氏6號(hào)錐堵) 切削深度:?jiǎn)芜呌嗔縜=2.4mm,走3刀; 進(jìn)給量:根據(jù)《機(jī)械加工工藝實(shí)用手冊(cè)》選用f=0.5mm/r; 計(jì)算切削速度:根據(jù)《機(jī)械加工工藝手冊(cè)》表得: =118.3m/min 確 11. 精車M1051.5-2,φ100h6外圓 ⑴精車M1051.5外圓 切削深度:?jiǎn)芜呌嗔縜=0.5mm,共進(jìn)刀1次; 進(jìn)給量:選用f=0.5mm/r;
43、 計(jì)算切削速度:=151m/min 確定主軸轉(zhuǎn)速: ⑵精車φ100h6外圓時(shí)與①精車M1001.5外圓相同 12. 切槽 ⑴切51.5槽(φ70h6-M741.5之間) 刀具:高速鋼切槽刀《機(jī)床加工工藝手冊(cè)》表 切削深度:?jiǎn)芜呌嗔縜=0.5mm,共進(jìn)刀1次; 進(jìn)給量:選用f=0.1mm/r; 計(jì)算切削速度:=34.5m/min 確定主軸轉(zhuǎn)速: ⑵切51.5槽(M741.5-φ75h5之間) 切削深度:?jiǎn)芜呌嗔縜=1mm,共進(jìn)刀1次; 進(jìn)給量:選用f=0.2mm/r; 計(jì)算切削速度:=21.8m/min 確定主
44、 ⑷切51.5槽(φ77.5-φ80h5之間) 切削深度:?jiǎn)芜呌嗔縜=1.75mm,共進(jìn)刀1次; 進(jìn)給量:選用f=0.2mm/r; 計(jì)算切削速度:=21.8m/min 確定主軸轉(zhuǎn)速: ⑸切51.5槽(φ80h5-φ89f5之間) 切削深度:?jiǎn)芜呌嗔縜=0.5mm,共進(jìn)刀1次; 由《機(jī)械加工工藝實(shí)用手冊(cè)》表可知砂輪的轉(zhuǎn)速為1130r/min 故最大切削速度:選擇 選取n=40m/min,工件的軸向進(jìn)給量f時(shí),橫向進(jìn)給量《機(jī)械制造工藝金屬切削機(jī)床設(shè)計(jì)指導(dǎo)》表得 工件切削余量,每次切削深度f,切削次數(shù)為1次 16. 磨削莫氏6錐孔 機(jī)床:M212
45、0內(nèi)圓磨床《機(jī)械加工工藝設(shè)計(jì)實(shí)用手冊(cè)》表得 工件的轉(zhuǎn)速范圍:120 砂輪軸的轉(zhuǎn)速:4000 砂輪:選取白鋼玉60錐磨頭《機(jī)械加工工藝設(shè)計(jì)實(shí)用手冊(cè)》表得 D=30,а=30 B=20mm 由《機(jī)械加工工藝設(shè)計(jì)實(shí)用手冊(cè)》表得 工件速度工件轉(zhuǎn)速,砂輪的轉(zhuǎn)速為5000r/min 故最大切削速度:選擇 工件的軸向進(jìn)給量=10mm時(shí),橫向進(jìn)給量《機(jī)械制造工藝金屬切削機(jī)床設(shè)計(jì)指導(dǎo)》表得 工件切削余量,每次切削深度,切削次數(shù)為1次。 17. 粗銑、精銑花鍵 ⑴粗銑 刀具:高速鋼三面刃銑刀 根據(jù)《機(jī)械加工工藝設(shè)計(jì)手冊(cè)》表 銑削深度一次走刀切除。 每齒進(jìn)給量: V=
46、0.48m/s=28.8r/min 計(jì)算主軸轉(zhuǎn)速: n=1000v/πd=(1000x28.8)/(πx105)=92r/min 按機(jī)床選取n=100r/min,所以實(shí)際切削速度: V=πdrn/1000=32m/min 取切入深度l1=3mm 20. 磨削兩處1:12外錐面,D面,以及短錐面 機(jī)床:MB/332B外圓磨床 砂輪:GB2485-84 B=25mm ⑴磨削小端1:12錐面 工件速度V=0.22 工件轉(zhuǎn)速n=0.87 故最大的切削速度:v=πx450x5000/6x104=160m/min
47、選擇工件速度n=72m/min 工件的縱向進(jìn)給量f=0.5 B=10mm時(shí),橫向進(jìn)給量f=0.17mm/dst 工件的切削余量z=0.5mm,每次切削深度f=0.25mm,切削次數(shù)為1次. ⑵磨大端1:12錐面 工件轉(zhuǎn)速nn=0.62 砂輪最大的切削速度:160m/min,選擇工件轉(zhuǎn)速n=42m/min,根據(jù)手冊(cè)n=50m/min 工件的縱向進(jìn)給量fab=0.5 B=10mm時(shí),橫向進(jìn)給量f1=10.6m/min 工件的切削余量Zh=0.4mm,每次切削深度fn=0.1mm,切削次數(shù)為2次. ⑶磨Φ106.3730.013 外圓 工件轉(zhuǎn)速n
48、n=0.62 砂輪最大的切削速度:160m/min,選擇工件轉(zhuǎn)速nw=42m/min,根據(jù)手冊(cè)n=50m/min 工件的縱向進(jìn)給量fab=0.5 B=10mm時(shí),橫向進(jìn)給量fc=10.6m/min 工件的切削余量Zf=0.4mm,每次切削深度Fb=0.1mm,切削次數(shù)為2次. ⑷磨削D面 工件速度VW=0.25 工件轉(zhuǎn)速Nw=0.4 砂輪的最大的切削速度:160m/min 選擇工件回轉(zhuǎn)速度nn=22m/min,由手冊(cè)選取n=50m/min 工件的縱向進(jìn)給量fab=0.5 B=10mm時(shí),橫向進(jìn)給量fc=1.73mm/dst 工件的切削
49、余量Zh=0.4mm.每次切削深度fb=0.1mm,切削次數(shù)為4次. 21. 磨削莫氏6錐孔 機(jī)床:M2120內(nèi)圓磨床 工件的轉(zhuǎn)速范圍:120r/min 砂輪軸的轉(zhuǎn)速:4000r/min 砂輪:選取白剛玉60錐磨頭D=30,a=30,B=20mm 工件速度Vw=0.5 工件轉(zhuǎn)速nw=2.65 選取砂輪主軸轉(zhuǎn)速為5000r/min 故最大的切削速度:v=πx30x5000/6x104=7.8m/min 選擇工件轉(zhuǎn)速nn=180m/min 工件的縱向進(jìn)給量FB=32mm時(shí),橫向進(jìn)給量fb=0.0024mm/dst 工件的
50、切削余量Zh=0.1.mm,每次切削深度Fb=0.05mm,切削次數(shù)為1次 4.3 本章小結(jié) 本章主要介紹了從毛坯開始各個(gè)工序工步加工用量和切削余量的計(jì)算。 第五章 專用夾具的設(shè)計(jì) 為了提高勞動(dòng)生產(chǎn)率,保證加工質(zhì)量,需要設(shè)計(jì)專用夾具。經(jīng)過與指導(dǎo)教師協(xié)商,決定設(shè)計(jì)第13道4個(gè)23mm的孔的鉆床夾具和第27道精磨莫氏6號(hào)錐孔的磨床夾具。 5.1 鉆床夾具的設(shè)計(jì) 5.1.1 鉆床夾具的分析 具加工時(shí)主要應(yīng)考慮如何保證其尺寸精度要求和表面粗糙度要求,以及如何提高勞動(dòng)生產(chǎn)率,降低勞動(dòng)強(qiáng)度。夾具簡(jiǎn)圖如5.1圖所示: 圖5.1 鉆床夾具簡(jiǎn)圖 1.底座;2.前支架;3.后
51、支架;4.鋼球;5.錐堵;6.鉆模板;7.鉆套;8.尖錐絲桿;9.手柄支座;1求: ①定位表面對(duì)夾具安裝基面的垂直度或平行度; ②定位表面的直線度和平面度或等高性; ③定位表面和導(dǎo)套軸線對(duì)校正基面的垂直度或平行度。 5.1 (5.1) 軸向鉆削力: (5.2) 式中:d為鉆頭直徑 f為每轉(zhuǎn)進(jìn)給量 修正系數(shù) 由《簡(jiǎn)明機(jī)床夾具手冊(cè)》得: 修正系數(shù): 又
52、 鉆削力矩: 軸向鉆削力: 5.2 磨床夾具的設(shè)計(jì) 5.2.1 夾緊裝置及夾具體設(shè)計(jì) 此夾具采用的壓緊元件為可分拆式半圓蓋和壓緊螺母,取下可開式半圓蓋和松開彈性?shī)A套,工件裝入定位銅套上,實(shí)現(xiàn)徑向定位,再將70外圓壓入彈性?shī)A套內(nèi),實(shí)現(xiàn)軸向定位,最后擰緊螺母夾緊工件。 此夾具設(shè)計(jì)剛性較好,可以保證高的加工精度,并且壓緊可靠,還能使工件裝卸方便,在保證加工質(zhì)量的情況下,省時(shí)省力。夾具結(jié)構(gòu)簡(jiǎn)圖如圖5.2所示: 圖5.2 磨床夾具簡(jiǎn)圖 磨床頭 由《簡(jiǎn)明機(jī)床夾具手冊(cè)》得: (5
53、.3) (5.4) 且 故: 總切削力: 5.3 本章小結(jié)術(shù)要求,以及裝夾方法。 第六章 結(jié) 論 以上就是關(guān)于主軸工藝與夾具的設(shè)計(jì)全部?jī)?nèi)容,本次設(shè)計(jì)基本完成了車床主軸 另?外?有?全?套?圖?紙?和?C?A?D?原?件?(?一?共?是?3?.?5?張?A?0?圖?,?嫌?多?可?自?己?刪?除?了?裝?配?圖?以?外?的?零?件?圖?)?,?甚?至?包?括?答?辯?有?關(guān)?問?題?的?解?答?,?以?及?答?辯?時(shí)?要?做?的?P?P?T?和?工?藝?過?程?卡?,?工?序?卡
54、?,?進(jìn)?度?表?等?一?系?列?所?有?東?西?。?另?外?還?有?其?他?機(jī)?械?課?題?的?全?套?論?文?有?意?聯(lián)?系?Q?Q?: 948962923? ?備?注?:?論?文?答?辯 參 考 文 獻(xiàn) [1] 陳宏鈞,方向明等.典型零件機(jī)械加工生產(chǎn)實(shí)例[M].第二版.北京:機(jī)械工業(yè)出版社,2004.8 [2] 王季琨,沈中偉,劉錫珍等.機(jī)械制造工藝學(xué)[M].天津:天津大學(xué)出版社,2004.1 [3] 王光斗,王春福等.機(jī)床夾具設(shè)計(jì)手冊(cè)[M].第三版.上海:上??茖W(xué)技術(shù)出版社,2000.11 [4] 李洪.機(jī)械加工工藝手冊(cè)[M].北京:北京出版社,1996.1 [5] 貴
55、州工學(xué)院機(jī)械制造工藝教研室編.機(jī)床夾具結(jié)構(gòu)圖冊(cè)[M].貴州:貴州人民出版社,1983.6 [6] 陳宏鈞.機(jī)械加工工藝裝備設(shè)計(jì)員手冊(cè)[M].北京:機(jī)械工業(yè)出版社,2008.5 [7] 胡忠舉,陸名彰.機(jī)械制造技術(shù)基礎(chǔ)[M].第二版.長(zhǎng)沙:中南大學(xué)出版社,2011.8 [8] 李必文等.機(jī)械精度設(shè)計(jì)與檢測(cè)[M].第二版.長(zhǎng)沙:中南大學(xué)出版社,2012.9 [9] 大連理工大學(xué)工程圖學(xué)教研室.機(jī)械制圖[M].第六版.北京:高等教育出版社,2007.7 [10] 關(guān)慧貞,馮辛安.機(jī)械制造裝備設(shè)計(jì)[M].第三版.北京:機(jī)械工業(yè)出版社,2009.11 [11] 高為國(guó),鐘利萍.機(jī)械工程材料[
56、M].第二版.長(zhǎng)沙:中南大學(xué)出版社,2012.9 [12] 陳紅霞.機(jī)械制造工藝學(xué)[M].北京:北京大學(xué)出版社,2010.7 [13] 王永章,杜君文,程國(guó)權(quán).數(shù)控技術(shù)[M].北京:高等教育出版社,2001.12 致 謝 本次畢業(yè)設(shè)計(jì)從課題選題、課題設(shè)計(jì)一直到最終的論文編寫過程中,得到了張光業(yè)老師的悉心教導(dǎo)和大力幫助。設(shè)計(jì)之中的每一點(diǎn)內(nèi)容無不凝聚著老師的心血和汗水。在我的畢業(yè)設(shè)計(jì)期間,張老師就課題本身的關(guān)鍵內(nèi)容和技術(shù)難題方面都給了我很大的支持和幫助,張老師態(tài)度和睦、專業(yè)嚴(yán)謹(jǐn)、知識(shí)淵博。在有了張老師的幫助下使我受益匪淺,這也必將積極的鼓勵(lì)我在今后的學(xué)習(xí)和工作中不斷的前進(jìn)。至此論文完成之際,謹(jǐn)向張老師表示最誠(chéng)摯的感謝和由衷的尊敬。 同時(shí)在此向在畢業(yè)設(shè)計(jì)期間給予我許多幫助的其他老師和同學(xué)表示深深的謝意。
- 溫馨提示:
1: 本站所有資源如無特殊說明,都需要本地電腦安裝OFFICE2007和PDF閱讀器。圖紙軟件為CAD,CAXA,PROE,UG,SolidWorks等.壓縮文件請(qǐng)下載最新的WinRAR軟件解壓。
2: 本站的文檔不包含任何第三方提供的附件圖紙等,如果需要附件,請(qǐng)聯(lián)系上傳者。文件的所有權(quán)益歸上傳用戶所有。
3.本站RAR壓縮包中若帶圖紙,網(wǎng)頁(yè)內(nèi)容里面會(huì)有圖紙預(yù)覽,若沒有圖紙預(yù)覽就沒有圖紙。
4. 未經(jīng)權(quán)益所有人同意不得將文件中的內(nèi)容挪作商業(yè)或盈利用途。
5. 裝配圖網(wǎng)僅提供信息存儲(chǔ)空間,僅對(duì)用戶上傳內(nèi)容的表現(xiàn)方式做保護(hù)處理,對(duì)用戶上傳分享的文檔內(nèi)容本身不做任何修改或編輯,并不能對(duì)任何下載內(nèi)容負(fù)責(zé)。
6. 下載文件中如有侵權(quán)或不適當(dāng)內(nèi)容,請(qǐng)與我們聯(lián)系,我們立即糾正。
7. 本站不保證下載資源的準(zhǔn)確性、安全性和完整性, 同時(shí)也不承擔(dān)用戶因使用這些下載資源對(duì)自己和他人造成任何形式的傷害或損失。
最新文檔
- 6.煤礦安全生產(chǎn)科普知識(shí)競(jìng)賽題含答案
- 2.煤礦爆破工技能鑒定試題含答案
- 3.爆破工培訓(xùn)考試試題含答案
- 2.煤礦安全監(jiān)察人員模擬考試題庫(kù)試卷含答案
- 3.金屬非金屬礦山安全管理人員(地下礦山)安全生產(chǎn)模擬考試題庫(kù)試卷含答案
- 4.煤礦特種作業(yè)人員井下電鉗工模擬考試題庫(kù)試卷含答案
- 1 煤礦安全生產(chǎn)及管理知識(shí)測(cè)試題庫(kù)及答案
- 2 各種煤礦安全考試試題含答案
- 1 煤礦安全檢查考試題
- 1 井下放炮員練習(xí)題含答案
- 2煤礦安全監(jiān)測(cè)工種技術(shù)比武題庫(kù)含解析
- 1 礦山應(yīng)急救援安全知識(shí)競(jìng)賽試題
- 1 礦井泵工考試練習(xí)題含答案
- 2煤礦爆破工考試復(fù)習(xí)題含答案
- 1 各種煤礦安全考試試題含答案