60萬(wàn)ta煤制甲醇項(xiàng)目co變換工段初步設(shè)計(jì) 設(shè)計(jì)說(shuō)明書(shū)
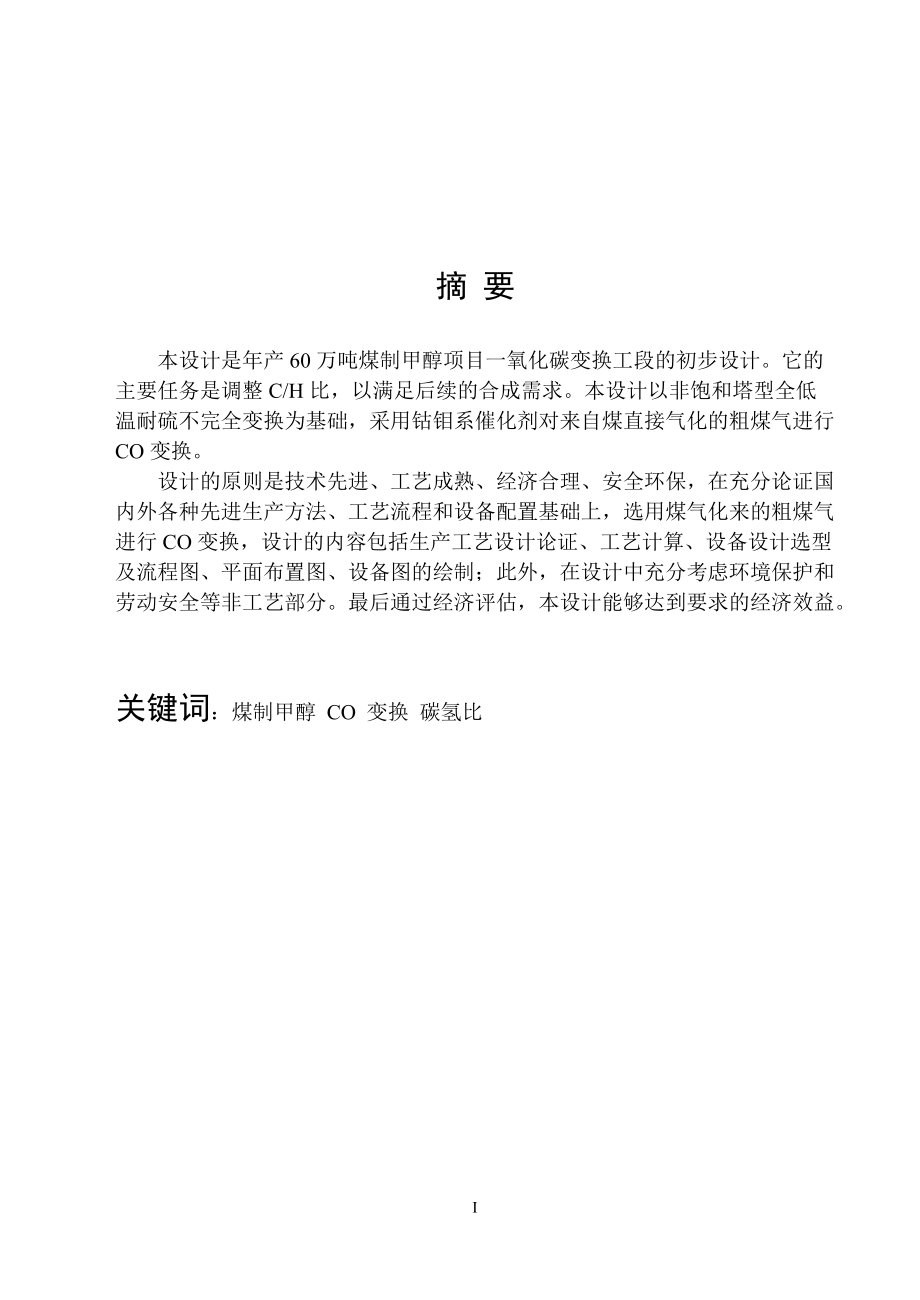


《60萬(wàn)ta煤制甲醇項(xiàng)目co變換工段初步設(shè)計(jì) 設(shè)計(jì)說(shuō)明書(shū)》由會(huì)員分享,可在線閱讀,更多相關(guān)《60萬(wàn)ta煤制甲醇項(xiàng)目co變換工段初步設(shè)計(jì) 設(shè)計(jì)說(shuō)明書(shū)(69頁(yè)珍藏版)》請(qǐng)?jiān)谘b配圖網(wǎng)上搜索。
1、摘 要 本設(shè)計(jì)是年產(chǎn)60萬(wàn)噸煤制甲醇項(xiàng)目一氧化碳變換工段的初步設(shè)計(jì)。它的主要任務(wù)是調(diào)整C/H比,以滿足后續(xù)的合成需求。本設(shè)計(jì)以非飽和塔型全低溫耐硫不完全變換為基礎(chǔ),采用鈷鉬系催化劑對(duì)來(lái)自煤直接氣化的粗煤氣進(jìn)行CO變換。 設(shè)計(jì)的原則是技術(shù)先進(jìn)、工藝成熟、經(jīng)濟(jì)合理、安全環(huán)保,在充分論證國(guó)內(nèi)外各種先進(jìn)生產(chǎn)方法、工藝流程和設(shè)備配置基礎(chǔ)上,選用煤氣化來(lái)的粗煤氣進(jìn)行CO變換,設(shè)計(jì)的內(nèi)容包括生產(chǎn)工藝設(shè)計(jì)論證、工藝計(jì)算、設(shè)備設(shè)計(jì)選型及流程圖、平面布置圖、設(shè)備圖的繪制;此外,在設(shè)計(jì)中充分考慮環(huán)境保護(hù)和勞動(dòng)安全等非工藝部分。最后通過(guò)經(jīng)濟(jì)評(píng)估,本設(shè)計(jì)能夠達(dá)到要求的經(jīng)濟(jì)效益。 關(guān)鍵詞:煤制甲醇 CO 變換
2、碳?xì)浔? Abstract This design is the annual output of 60 million tons of coal methanol carbon monoxide shift conversion section of the preliminary design. Its main task is to adjust the C / H ratio, the synthesis of the follow-up to meet demand. The design process for the work of
3、all non-saturated low-temperature sulfur-tolerant tower is not completely transformed into discussion, the use of cobalt-molybdenum catalysts Gasification of coal directly from coal gas for CO conversion. Design principles are technologically advanced, mature technology, economical, safe environ
4、ment, fully demonstrated at home and abroad in a variety of advanced production methods, process and device configuration based on the use of coal gasification to transform the crude gas to CO, the design includes production process design argument, process calculation, equipment selection and desig
5、n of flow charts, floor plans, equipment, mapping; In addition, full consideration in the design of environmental protection and labor safety and other non-process part. Finally, economic evaluation, designed to meet the requirements of the economic benefits. Keywords: coal to methanol carbon mo
6、noxide transform ratio of carbon and hydrogen 64 目 錄 摘 要 I Abstract II 第1章 總 論 1 1.1 概述 1 1.1.1 煤制甲醇的可行性 1 1.1.2 設(shè)計(jì)的目的和意義 1 1.1.3 變換氣的要求 2 1.2 工藝比較 3 1.2.1 全低變工藝 3 1.2.2 無(wú)飽和塔型變換工藝 7 1.2.3 Shell粉煤氣化制甲醇一氧化碳變換工藝 9 1.2.4 變換兼COS水解工藝 10 1.2.5 變換兼硫化物加氫工藝 11 1.2.6 小
7、結(jié) 12 1.3 設(shè)計(jì)范圍、裝置組成及建設(shè)規(guī)模 12 1.3.1 設(shè)計(jì)的范圍 12 1.3.2 生產(chǎn)裝置組成 13 1.3.3 建設(shè)規(guī)模 13 第2章 工藝詳述 14 2.1 一氧化碳變換系統(tǒng)流程 14 2.2 一氧化碳變換系統(tǒng)影響因素 15 2.2.1 壓力 15 2.2.2 溫度 16 2.2.3 水汽比 16 2.2.4 空速 17 2.2.5 CO2的影響 17 2.2.6 副反應(yīng)的影響 17 2.2.7 入口溫度 18 2.2.8 催化劑活性 18 2.2.9 煤氣中CO的含量 18 2.3 操作制度 19 2.3
8、.1 入口溫度的控制 19 2.3.2 床層溫度的控制 19 2.3.3 出口CO指標(biāo)的控制 19 2.3.4 變換爐壓差 20 2.4 一氧化碳變換系統(tǒng)中存在的問(wèn)題 20 第3章 工藝計(jì)算 21 3.1 原始數(shù)據(jù) 21 3.2 變換爐工藝參數(shù)計(jì)算 21 3.2.1 1#變換爐工藝參數(shù)計(jì)算 21 3.2.2 2#變換爐工藝參數(shù)計(jì)算 24 3.2.3 3#變換爐工藝參數(shù)計(jì)算 26 3.3 物料衡算及熱量衡算 27 3.3.1 變換爐物料衡算及熱量衡算 27 3.3.2 氣體增濕器物料衡算及熱量衡算 30 3.3.3 廢熱鍋爐物料衡算及熱量
9、衡算 31 第4章 主要設(shè)備的工藝計(jì)算和設(shè)備選型 34 4.1 變換爐的工藝計(jì)算 34 4.1.1 已知條件 34 4.1.2 1#變換爐 35 4.1.3 2#變換爐 37 4.1.4 3#變換爐 39 4.2 廢熱鍋爐的工藝計(jì)算 42 4.2.1 筒體內(nèi)徑的計(jì)算 42 4.2.2 傳熱系數(shù)的計(jì)算 43 4.3 氣體增濕器的確定 47 4.4 開(kāi)工加熱器的確定 47 4.5 原料氣預(yù)熱器的確定 47 4.6 預(yù)變換爐的確定 47 4.7 蒸汽預(yù)熱器的確定 47 4.8 甲烷化入口加熱器 48 4.9 CO變換工段設(shè)備一覽表 4
10、8 第5章 車(chē)間布置說(shuō)明 50 5.1 車(chē)間布置原則 50 5.2 哈爾濱地區(qū)的自然條件 50 5.2.1 氣象條件 51 5.2.2 地震烈度 51 5.3 車(chē)間布置的方案 52 5.3.1 廠房的平立面布置 52 5.3.2 車(chē)間輔助室和生活室的布置 52 5.3.3 設(shè)備的布置方案 52 第6章 非工藝部分要求 54 6.1 公用工程 54 6.1.1 土建 54 6.1.2 給排水及熱力 54 6.1.3 電力、電信系統(tǒng) 55 6.1.4 自控儀表 55 6.2 環(huán)境保護(hù)及安全衛(wèi)生 55 6.2.1 三廢處理 55 6
11、.2.2 安全生產(chǎn) 56 6.3 節(jié)能 57 結(jié)束語(yǔ) 58 致 謝 59 參考文獻(xiàn) 60 第1章 總 論 1.1 概述 1.1.1 煤制甲醇的可行性 甲醇的原料來(lái)源早期是木材。木材的主要成分是纖維、半纖維和木質(zhì)素。 把木材置入密閉的設(shè)備中,隔絕空氣加熱可生成木炭、一氧化碳、甲醇、醋酸等產(chǎn)品。隨著木材資源的愈來(lái)愈寶貴,各國(guó)科學(xué)家都在尋求制造甲醇的新方法和新原料。1923年德國(guó)開(kāi)發(fā)出在高溫、高壓以及鋅絡(luò)催化劑的作用下,用CO和H2合成甲醇的方法,并實(shí)現(xiàn)了工業(yè)化生產(chǎn)。隨著技術(shù)的進(jìn)步和研究的深入,中溫、中壓催化合成和低溫低壓催化合成甲醇等新
12、技術(shù)和新工藝,節(jié)約了能耗,擴(kuò)大了單系列裝置的生產(chǎn)能力,為煤制甲醇的產(chǎn)業(yè)化、規(guī)?;峁┝思夹g(shù)基礎(chǔ)。 50年代初,石油的大量發(fā)現(xiàn)和開(kāi)發(fā),天然氣成為制取甲醇的主要原料,煤制甲醇技術(shù)一度停滯。但隨著時(shí)間的推移,70年代的石油危機(jī)和現(xiàn)今的原油價(jià)格的直線飚升,給依賴(lài)石油和天然氣生產(chǎn)甲醇帶來(lái)了困難,因而甲醇原料的來(lái)源又轉(zhuǎn)向了蘊(yùn)藏豐富、價(jià)格低廉的煤炭資源,而且任何品種的煤,都可生產(chǎn)甲醇。在科學(xué)技術(shù)的不斷進(jìn)步下,更新改造的新型氣化爐(水煤漿加壓氣化的德士古爐、粉煤加壓氣化的謝爾爐等)為各種煤的氣化提供了先進(jìn)的設(shè)備;液相超臨界萃取、納米高活性高選擇性催化劑,為提高甲醇轉(zhuǎn)化率和甲醇下游產(chǎn)品的合成提供了技術(shù)
13、條件;甲醇汽車(chē)的研制成功和逐步推廣,為煤制甲醇提供了巨大的潛在市場(chǎng)。因此,煤炭成為生產(chǎn)甲醇的主要的、可靠的、經(jīng)濟(jì)的原料,煤制甲醇在經(jīng)濟(jì)和技術(shù)上都是可行的[1]。 1.1.2 設(shè)計(jì)的目的和意義 1. 設(shè)計(jì)目的 變換工段的主要目的:(1)調(diào)節(jié)氫碳比使(H2-CO2)/(CO+CO2)=2左右。是指甲醇合成時(shí)新鮮合成氣的氫碳比,也就是凈化之后、合成之前的氫碳比,該比例的達(dá)到還要借助于凈化工段二氧化碳的吸收、排除(以水煤漿等煤氣化的)或補(bǔ)充(以焦?fàn)t煤氣或天然氣為原料的),單是在變換工段達(dá)不到此比例。(2)將合成氣中的有機(jī)硫變成無(wú)機(jī)硫(H2S)更有利于其吸收。 2. 設(shè)計(jì)意義
14、 變換工段的主要意義:變換在煤化工行業(yè)中無(wú)論是甲醇還是合成氨都是必須的,因?yàn)樵鞖獠豢赡軟](méi)有CO,對(duì)于合成氨和甲醇來(lái)說(shuō)這種氣體的成分是有限制的。所以大多會(huì)結(jié)合自己工藝的特點(diǎn)選擇深度和淺度變換。對(duì)于甲醇廠或聯(lián)醇單位由于適當(dāng)?shù)腃O可以增加企業(yè)效益以及節(jié)約蒸汽,降低產(chǎn)品的能耗,以及耐硫低變催化劑的工業(yè)化生產(chǎn),所以現(xiàn)在全低變工藝比較流行。不過(guò)在實(shí)際的生產(chǎn)中,如果是聯(lián)醇,如果甲醇工號(hào)的觸媒活性好,同時(shí)甲醇市場(chǎng)特別好,比如前段時(shí)期,甲醇價(jià)格到4000左右時(shí),可以適當(dāng)降低變換負(fù)荷,提高出口的CO,增加甲醇產(chǎn)量,來(lái)達(dá)到最大的企業(yè)利益。 1.1.3 變換氣的要求 由水煤漿、天然氣、渣油、制取的粗原料氣中,
15、總是含有一定量的CO,例如,水煤漿、重油氣化制得的半水煤氣含一氧化碳40%~45%,天然氣蒸汽轉(zhuǎn)化法制得的半水煤氣含一氧化碳12%~14%,固體燃料氣化制得的半水煤氣含一氧化碳25%~40%,但因原料氣的用途不同,對(duì)CO的含量要求也不同。這就需要通過(guò)一氧化碳變換工藝來(lái)調(diào)整原料氣中CO的比例。一氧化碳變換是指一氧化碳與水蒸氣反應(yīng)生成氫氣的過(guò)程。即 CO+H2O→CO2+H2+41.17KJ/mol 反應(yīng)后的氣體稱(chēng)為變換氣。這樣,既能把一氧化碳變?yōu)橐子谇宄亩趸?,同時(shí)又能制得與反應(yīng)了的一氧化碳等摩爾的氫,而所消耗的只是廉價(jià)的水蒸氣。 工業(yè)上CO變換反應(yīng)都是在催化劑存在條件下進(jìn)行,六十年代
16、以前,在合成氨工業(yè)中,都是將原料氣中的H2S和SO2等硫化物在被脫除的情況下,用以Fe2O3為主體的催化劑,在350℃~550℃的條件下進(jìn)行變換反應(yīng),但約有2%~4%的CO存在于變換氣中。六十年代以后,研究出了活性更高的一氧化碳變換催化劑,但這些催化劑的抗毒性差。隨著渣油、水煤漿氣化工藝的發(fā)展,針對(duì)直接回收熱能的激冷流程,如果仍然用傳統(tǒng)的先脫硫、后脫碳的方法,勢(shì)必將以蒸汽狀態(tài)回收的大量熱能損失掉。為了充分發(fā)揮利用水煤漿氣化反應(yīng)熱,有必要使一氧化碳變換直接串于水煤漿加壓氣化制取原料氣之后,而將硫在一氧化碳變換之后脫除。因而開(kāi)發(fā)了活性更高的以Co-Mo系為主體的中溫變換催化劑,操作溫度在220℃~
17、450℃的條件下進(jìn)行變換反應(yīng)[2]。 1.2 工藝比較 隨著甲醇應(yīng)用市場(chǎng)的開(kāi)拓,化工企業(yè)對(duì)甲醇生產(chǎn)的投入逐步加大,舊裝置的改造、新裝置的建成,甲醇產(chǎn)量日益增加。從1912年將鐵系催化劑應(yīng)用于變換反應(yīng),從而實(shí)現(xiàn)工業(yè)化生產(chǎn),它在工業(yè)上的應(yīng)用顯得更為重要。開(kāi)始人們只不過(guò)把變換得氫氣用于點(diǎn)燈、焊接、冶煉等方面。隨著合成氨、合成甲醇、合成汽油等工業(yè)的發(fā)展,變換反應(yīng)就成為制備廉價(jià)氫氣和調(diào)節(jié)CO和H2的比例的主要方法和手段。 20世紀(jì)80年代中期以前,國(guó)內(nèi)設(shè)計(jì)的變換工藝均為中溫(高溫)變換,隨著1986-1987年湖北省化學(xué)研究院和上?;ぱ芯吭合嗬^開(kāi)發(fā)出CO-MO系低溫催化劑,變換工藝發(fā)展為中串低
18、,現(xiàn)在又發(fā)展中低低工藝,使得變換工段進(jìn)行變革有了物質(zhì)基礎(chǔ)。傳統(tǒng)的變換工藝全部使用Fe-Cr系中變催化劑,由于起活溫度高(一般為280-300℃),因此該工藝存在能耗高及凈化度低等問(wèn)題。為了改變這種狀況,經(jīng)過(guò)近20年的不斷開(kāi)發(fā)與工業(yè)實(shí)踐,以下兩類(lèi)較為先進(jìn)的中變串低變和全低變工藝已基本取代了傳統(tǒng)的高溫變換工藝[3]。實(shí)際上中低低是全低變工藝上得一種改良,因全低變需要有脫氧、脫水的保護(hù)層,而中低低工藝可避免全低變的這樣的要求。因此,現(xiàn)在大多數(shù)企業(yè)使用的是節(jié)能的中低低工藝或是全低變工藝,而且多數(shù)中小氮肥廠使用的是熱水塔流程,大,中化肥廠使用的是換熱器流程。我國(guó)是煤豐富的國(guó)家, 甲醇原料采用天然氣和煤的
19、較多。目前產(chǎn)量幾乎各占一半。生產(chǎn)工藝有單產(chǎn)甲醇和聯(lián)產(chǎn)甲醇兩種。聯(lián)產(chǎn)甲醇除在合成氨裝置聯(lián)產(chǎn)甲醇外, 還可利用化工廠尾氣或結(jié)合城市煤氣聯(lián)產(chǎn)甲醇。 1.2.1 全低變工藝 1.高串低或高低低工藝 流程設(shè)置原理 由于一氧化碳變換反應(yīng)是放熱反應(yīng),顯然低溫有利于反應(yīng)的進(jìn)行和節(jié)能降耗,催化劑的終態(tài)溫度又是反應(yīng)的鍵因素和設(shè)計(jì)的重要技術(shù)指標(biāo)。當(dāng)變換氣中CO含量為3%時(shí),終態(tài)溫度與蒸汽用量的關(guān)系見(jiàn)表1-1。 表1-1 變換氣中CO為3%時(shí)不同溫度下蒸汽用量 出口溫度(℃) 220 250 300 350 400 入爐汽氣比(R) 0.307 0.
20、338 0.424 0.569 0.794 入爐蒸汽用量(kg﹒t) 838.8 925.5 1158.4 1554.6 2169.4 顯然,變換反應(yīng)出口溫度愈低,對(duì)平衡愈有利,蒸汽用量也愈低。傳統(tǒng)的變換流程為高溫變換工藝,在流程設(shè)置上一般是一個(gè)變換爐,爐內(nèi)裝填Fe—Cr系催化劑,分兩段或三段,半水煤氣從上到下依次通過(guò)各段催化劑后即完成變換過(guò)程,變換爐入口溫度一般控制在300~420℃。由于催化劑的終態(tài)溫度較高,蒸汽消耗也就很大。為此利用Co-Mo系催化劑的低溫活性好的性能開(kāi)發(fā)了部分低溫變換工藝,在原高變降溫后串上Co-Mo催化劑的高串低工藝,根據(jù)催化劑的低溫性能,
21、低變爐(段)入口氣體溫度一般可控制在180~230℃左右,出口在210~260℃。這樣由于催化劑的終態(tài)溫度降低,可以減少蒸汽添加量,達(dá)到節(jié)能效果。低變后氣體中一氧化碳含量比傳統(tǒng)的中變工藝可降低一個(gè)百分點(diǎn),從而減輕了后工段(如銅洗)凈化負(fù)荷。另外,由于變換率的提高,合成氨的產(chǎn)量可相對(duì)增加。顯然Co-Mo催化劑的低溫性能愈好,進(jìn)口溫度愈低,其節(jié)能效果也愈好。 2.高串低 在高變后串一個(gè)低變爐(段)也稱(chēng)高串低。中變爐有冷激則低變爐可直接串在主熱交換器后;中變爐有中間換熱則在主熱交換器后配置一個(gè)調(diào)溫水加熱器,再串上低變爐。該法處理簡(jiǎn)單,可隨時(shí)進(jìn)行,將低變爐、調(diào)溫水加熱器配置好,并入
22、系統(tǒng)即可。該流程也稱(chēng)為爐外串低變。另一種高串低是將高變爐的第三段作低變段用,將主熱交位置從三段移至二段出口,一、二段為水冷激則熱交出口直接進(jìn)三段(低變段),否則增設(shè)一個(gè)調(diào)溫水加。該法省去一個(gè)低變爐.投資省,但改造費(fèi)時(shí),需要在大修時(shí)進(jìn)行。由于高變催化劑的空速較大,要注意對(duì)高變催化劑的維護(hù),該流程也稱(chēng)為爐內(nèi)串低變。中串低工藝串一個(gè)低變爐(段)也稱(chēng)中串低,在原中變爐的后面串上一個(gè)低變爐,中變爐有冷激可直接串在主熱交換器后,中變爐為中間換熱則在主熱交后配置一個(gè)調(diào)溫水加熱器,再串上低變爐,該法處理簡(jiǎn)單,可隨時(shí)進(jìn)行,將低變爐、調(diào)溫水加配置好,并人系統(tǒng)即可。該流程也稱(chēng)為爐外串低變。 3.中串低工藝
23、 串一個(gè)低變爐(段)也稱(chēng)中串低,在原中變爐的后面串上一個(gè)低變爐,中變爐有冷激可直接串在主熱交換器后,中變爐為中間換熱則在主熱交后配置一個(gè)調(diào)溫水加熱器,再串上低變爐,該法處理簡(jiǎn)單,可隨時(shí)進(jìn)行,將低變爐、調(diào)溫水加配置好,并人系統(tǒng)即可。該流程也稱(chēng)為爐外串低變。 另一種中串低是將中變爐的第三段作低變段用,將主熱交位置從三段移至二段出口,一、二段為水冷激則熱交出口直接進(jìn)三段(低變段),否則要增設(shè)一個(gè)調(diào)溫水加。該法省去一個(gè)低變爐,投資省,但改造費(fèi)時(shí),需要在大修時(shí)進(jìn)行,由于中變催化劑的空速較大,要注意對(duì)中變催化劑的維護(hù),該流程也稱(chēng)為爐內(nèi)串低變。 4.中低低工藝 中低低工藝一般為一段或兩段中
24、變,兩段低變。變換爐可做成一個(gè)或兩個(gè),具體地說(shuō)就是一段中變,兩段低變并用一個(gè)反應(yīng)器,這是以一段中變?yōu)樘卣鞯闹械偷凸に囋O(shè)計(jì)。如霍州化肥廠的7 萬(wàn)t/a合成氨變換設(shè)計(jì)及蘭花科創(chuàng)化工公司8 萬(wàn)t/a氨醇公司變換設(shè)計(jì)。此類(lèi)設(shè)計(jì)突出的優(yōu)點(diǎn)是設(shè)備投資小,設(shè)備占地面積少。缺點(diǎn)是一段中變,床層一旦偏流易造成中變床層漏氧,致使一低變催化劑易于失活。另外就是兩個(gè)爐子,兩段中變及兩段低變,由于中變分段,可有效地防止偏流,從而避免半水煤氣中的氧等有害雜質(zhì)漏入第一低變,造成一低變催化劑的快速失活。中變段間最好噴水,但對(duì)水質(zhì)有嚴(yán)格要求,如若水質(zhì)不好,可采用煤氣冷激,但不如噴水增濕節(jié)能。 5.全低變工藝 全低變
25、工藝目前大致可分為噴水增濕型和調(diào)溫水加熱器。全低變工藝一般為三段,為一個(gè)或兩個(gè)變換爐。如采用一低變出口噴水增濕降溫,一般在變換爐前設(shè)置一個(gè)預(yù)變爐,上部裝填保護(hù)劑和抗毒催化劑,下部裝填不銹鋼填料,噴水在此段進(jìn)行,后設(shè)置一個(gè)主反應(yīng)器(變換爐)。這種工藝比較節(jié)能,幾乎不需要外加蒸汽,若采用調(diào)溫水加熱器來(lái)調(diào)入口溫度,一般不設(shè)置預(yù)變爐,主反應(yīng)器為一個(gè)或兩個(gè),這種工藝由于是間接換熱,不如噴水型節(jié)能,耗蒸汽量為150kg~200kg。 “全低變”工藝與中低低工藝相比的優(yōu)點(diǎn)[4]: (1)原中變催化劑量減少一半以上,降低了床層阻力,提高了變換爐的設(shè)備能力; (2)床層溫度下降了100~200℃,氣體體積
26、縮小25%,降低系統(tǒng)阻力,減少壓縮機(jī)功率消耗; (3)與中串低或中低低相比全低變的有效能損失較少,從而提高了熱回收效率,進(jìn)一步降低蒸汽消耗; (4)杜絕了生成乙炔的反應(yīng),減少銅液的消耗,從而也防止了“帶液”現(xiàn)象; (5)減少換熱面積一半左右; (6)從根本上解決了中變催化劑的粉化問(wèn)題,改善了催化劑的裝卸勞動(dòng)衛(wèi)生條件; (7)提高有機(jī)硫的轉(zhuǎn)化能力,在相同操作條件和工況下,全低變工藝比中串低或中低低工藝有機(jī)硫轉(zhuǎn)化率提高5個(gè)百分點(diǎn); (8)操作容易,起動(dòng)快,增加了有效時(shí)間; (9)降低了對(duì)變換爐的材質(zhì)要求,改善了設(shè)備維修條件; (10)催化劑壽命長(zhǎng),一般可用5年左右,最長(zhǎng)的用了7年;
27、 (11)放寬了一次脫硫指標(biāo),從而降低脫硫費(fèi)用; (12)可取消飽和塔,并可降低蒸汽消耗。 “全低變”工藝在使用過(guò)程中,也發(fā)現(xiàn)一些問(wèn)題。主要是一段Co-Mo催化劑比較“嬌氣”,在管理不太好的情況下,催化劑容易老化,使用壽命縮短,系統(tǒng)阻力升高較快。其原因?yàn)閇5]: (1)Co-Mo系催化劑對(duì)煤氣帶入的毒物比較敏感,特別是氧,容易使CoS、MoS2硫酸化,即氧化為鈷、鉬的硫酸鹽而失去活性。硫酸鈷、硫酸鉬只有在高溫下才能被還原,在正常生產(chǎn)的條件是難以恢復(fù)活性的,成為永久性失活。許多廠為了保護(hù)一段催化劑,在一段催化劑上部加上一層吸附劑,起到保護(hù)作用,但對(duì)管理不善的廠家也難以徹底解決問(wèn)題。 (
28、2)由于一段上層催化劑的溫度較低,煤氣中未被除盡的焦油、壓縮機(jī)潤(rùn)滑油不能被分解,而被催化劑表面吸附,結(jié)成大“油餅”,阻力急劇增加。對(duì)于單顆催化劑則成“油球”,表面被覆蓋而市區(qū)活性。為了避免油被催化劑吸附,“全低變”工藝強(qiáng)調(diào)壓縮機(jī)二段出口要冷卻,加強(qiáng)除油,并提高一段入口溫度,以便使油分解,但往往也難以奏效。 (3)由于一段氣體中的汽氣比相對(duì)較高、溫升較大,出口溫度可達(dá)360~390℃,而且隨煤氣進(jìn)入變換爐的有機(jī)硫尚未來(lái)得及大量轉(zhuǎn)化為H2S,故H2S的濃度相對(duì)低,故若控制不好,其催化劑極易出現(xiàn)反硫化現(xiàn)象而失去活性。近年為了緩解這一現(xiàn)象,將添加蒸汽的位置改在一段出口處,但由于蒸汽添加量較少,一段汽
29、氣比只能降低0.1左右,為避免反硫化,一段入口仍需維持較高的H2S含量。 (4)由于對(duì)半水煤氣的硫含量要求較高,為后工段增加麻煩。有的還要增加變換氣脫硫,增加了投資和消耗。在“中變串低變”條件下使用的Co-Mo催化劑,只要管理得當(dāng),H2S濃度不太低,催化劑就可以維持較長(zhǎng)的壽命,一般能使用3~5年。由于煤氣中帶水、油及O2等有毒的成分均可先由中變催化劑“吃掉”, Co-Mo催化劑受到保護(hù);另一方面,經(jīng)過(guò)三段中變后,煤氣中的蒸汽已消耗掉很大一部分,汽氣比已相應(yīng)降低,而且大部分有機(jī)硫轉(zhuǎn)化為H2S,使氣體中H2S濃度有所提高,再說(shuō)低變爐的反應(yīng)溫度也比較低,一般稍高于200℃。這三者均有利于抑制反硫化
30、反應(yīng)的進(jìn)行,維護(hù)低變催化劑的活性。然而“全低變”系統(tǒng)中,特別是一段催化劑則首當(dāng)其沖地面對(duì)氧化、中毒、油污染、反硫化等惡劣條件,必定影響其催化劑使用壽命。而當(dāng)一段催化劑老化、失活、穿透后還必將殃及二段、三段催化劑,因此,若要使“全低變”系統(tǒng)穩(wěn)定生產(chǎn)、降低汽耗、延長(zhǎng)催化劑壽命,必須加強(qiáng)管理,加強(qiáng)對(duì)凈化的要求,對(duì)操作要求也更嚴(yán)。 1.2.2 無(wú)飽和塔型變換工藝 由于低變催化劑的應(yīng)用,特別是全低變工藝的應(yīng)用,變換氣中過(guò)量水蒸氣已很少,也就是說(shuō),利用飽和熱水塔回收潛熱的意義也就不大了。計(jì)算表明,當(dāng)變換出口CO含量為12%時(shí),飽和塔可回收的潛熱為200kg蒸汽/t;而當(dāng)聯(lián)醇工藝變換出口CO含
31、量為4%時(shí),飽和塔可回收的潛熱僅為65kg蒸汽/t。假如在流程上用噴水增濕來(lái)代替水加熱器回收變換氣的顯熱,而用外加蒸汽代替回收的潛熱,即聯(lián)醇工藝噸氨蒸汽消耗增加65kg,這樣聯(lián)醇工藝完全可取消飽和熱水塔,而出口CO含量為12%的變換工藝的噸氨蒸汽消耗增加約200kg,其潛熱可設(shè)法用其他方式回收。取消飽和熱水塔的工藝已在國(guó)內(nèi)國(guó)家工廠得到應(yīng)用,如湖北金凱化工股份有限公司(公安化肥廠)已應(yīng)用兩年,且效果良好(簡(jiǎn)稱(chēng)“非飽和塔型”)。 非飽和塔型全低工藝 如圖1-1所示, 30℃的半水煤氣經(jīng)油水分離器、焦炭過(guò)濾器后進(jìn)入煤氣換熱器管內(nèi), 經(jīng)與管間230℃的變換氣換熱至180℃進(jìn)入中間換熱器管內(nèi),再經(jīng)與
32、管間378℃的變換氣換熱至310℃去增濕器, 用90℃脫鹽水增濕至200℃ ,與添加的過(guò)熱蒸汽一起進(jìn)入一變爐反應(yīng)至200℃ ,去中間換熱器管間與180℃的煤氣換熱至267℃ ,去增濕器用90℃脫鹽水增濕至180℃,入二變換爐一段反應(yīng)至267℃(CO約11.5%),用90℃水增濕至180℃經(jīng)二變(換)爐二段反應(yīng)至230℃(CO約6%), 經(jīng)煤氣換熱器管間與30℃的煤氣換熱至132℃ , 經(jīng)水加熱器與30℃的脫鹽水換熱至90℃后出“全低變”工段去脫碳工段[6]。 圖1-1 非飽和塔型全低工藝 由上述流程中不難看出, 在非飽和塔型全低變工藝中設(shè)有油水分離器、焦炭過(guò)濾器、兩級(jí)增濕器等裝置。這
33、些裝置亦是近年來(lái)在國(guó)內(nèi)不少氮肥企業(yè)的變換工藝中經(jīng)常采用的, 尤其是油水分離器、活性炭過(guò)濾器對(duì)于除去煤氣中的油與細(xì)微粉塵及硫化物具有明顯的作用, 因?yàn)榻固坎粌H價(jià)廉易得而且還有很好的機(jī)械強(qiáng)度、耐壓、耐磨、耐水浸、大空速、低壓降、比表面積大。北京化工實(shí)驗(yàn)廠等的實(shí)踐表明, 變換觸媒使用壽命可延長(zhǎng)一倍以上, 且仍在使用,活性尚好。與熱水飽和塔相比, 非飽和塔型全低變工藝對(duì)于煤氣的凈化作用更勝一籌。 從煤氣凈化效果來(lái)看, 非飽和塔型全低變工藝流程完全可以滿足國(guó)內(nèi)尚有的部分氮肥企業(yè)將沒(méi)有熱水飽和塔型裝置的中溫變換工藝改造為全低變工藝的要求。該流程因無(wú)飽和塔似應(yīng)增加昂貴的蒸汽費(fèi)用, 其實(shí)不然, 因?yàn)樵摿鞒膛c
34、帶有熱水飽和塔的流程在本質(zhì)上是相同的。兩種工藝流程都對(duì)變換反應(yīng)熱實(shí)施了回收、對(duì)煤氣進(jìn)行了增濕, 前者采用兩級(jí)增濕器直接增濕后者是通過(guò)水加熱器間接換熱方式, 效率不如前者高, 且增加了龐大的熱水與飽和裝置、泵與電機(jī)等運(yùn)轉(zhuǎn)設(shè)備, 對(duì)管路、閥門(mén)、塔器的材質(zhì)要求也比較高。飽和熱水塔型全低變工藝與非飽和塔型全低變工藝相比多增加的設(shè)備有飽和熱水塔1臺(tái);循環(huán)水泵2臺(tái);補(bǔ)水泵2臺(tái)。 小結(jié):綜上所述,飽和熱水塔型全低變工藝雖然具有節(jié)省蒸汽的優(yōu)點(diǎn), 但是其基建投資大、回收期長(zhǎng), 投資費(fèi)用與操作費(fèi)用的綜合經(jīng)濟(jì)性差。非飽和塔型全低變工藝投資少、易操作, 操作費(fèi)用雖有些增加, 但與帶有飽和熱水塔型全低變工藝相比微不足
35、道。 1.2.3 Shell粉煤氣化制甲醇一氧化碳變換工藝 河南龍宇煤化工有限公司(簡(jiǎn)稱(chēng)龍宇煤化工)50萬(wàn)t/ a甲醇項(xiàng)目是國(guó)內(nèi)首套采用殼牌粉煤氣化制甲醇的裝置,其煤氣凈化裝置分為變換和低溫甲醇洗2部分:第1部分為部分耐硫變換裝置,把氣化裝置送出粗煤氣中一部分一氧化碳與水蒸氣反應(yīng)生成二氧化碳?xì)怏w和氫氣,以降低粗煤氣中一氧化碳?xì)怏w含量,同時(shí)得到原料氫氣;第2部分是低溫甲醇洗裝置對(duì)變換氣體進(jìn)行脫硫、脫碳后,送到甲醇合成裝置。 1.變換裝置設(shè)計(jì)思路 龍宇煤化工是目前國(guó)內(nèi)外首套采用Shell粉煤氣化制甲醇的大型生產(chǎn)裝置,粗煤氣中的CO含量高達(dá)65%以上。根據(jù)粗
36、煤氣中CO含量高的特點(diǎn),變換裝置采用寬溫部分耐硫變換(2臺(tái)爐)串聯(lián)低溫部分耐硫變換(1臺(tái)爐)工藝、段間激冷流程。該工藝流程的設(shè)計(jì)思路是:第1變換爐按照反應(yīng)動(dòng)力學(xué)進(jìn)行設(shè)計(jì),而第2、第3變換爐按照反應(yīng)熱力學(xué)進(jìn)行設(shè)計(jì),最終通過(guò)調(diào)整進(jìn)入3臺(tái)變換爐入口的煤氣量來(lái)實(shí)現(xiàn)CO的部分變換。其中一變爐和二變爐采用國(guó)外進(jìn)口催化劑K8 - 11,Dypor 607作為保護(hù)劑;第3變換爐采用國(guó)產(chǎn)催化劑QDB - 04,QXB - 01作為保護(hù)劑。為有效防止甲烷化副反應(yīng)的發(fā)生,整個(gè)工藝流程的水汽比較高,第1、第2、第3變換爐的設(shè)計(jì)水汽比分別為1. 02、0. 52、0. 37。 2.工藝流程 來(lái)自煤氣化裝置的粗煤氣,
37、首先進(jìn)入原料氣分離器,分離出夾帶的水分,然后進(jìn)入原料氣過(guò)濾器,除去固體機(jī)械雜質(zhì)。從原料氣過(guò)濾器出來(lái)的粗煤氣被分成3股: 1股(約35% )進(jìn)入煤氣預(yù)熱器,與來(lái)自第3變換爐出口的變換氣換熱到210℃,之后進(jìn)入蒸汽混合器,與加入的263℃蒸汽混合,再進(jìn)入煤氣換熱器,與來(lái)自第1變換爐出口的氣體換熱到260℃后,進(jìn)入第1變換爐進(jìn)行變換反應(yīng)。出第1變換爐的變換氣進(jìn)入煤氣換熱器換熱后,與來(lái)自原料氣過(guò)濾器的另1股粗煤氣(約30%)相混合,進(jìn)入1#淬冷過(guò)濾器,氣體經(jīng)噴水降溫后,進(jìn)入第2變換爐進(jìn)行變換反應(yīng)。第2變換爐出口的氣體與粗煤氣中剩余35%的氣體(來(lái)自原料過(guò)濾器的第3股粗煤氣)混合后,進(jìn)入2#淬冷過(guò)濾器,
38、噴水降溫后進(jìn)入第3變換爐發(fā)生變換反應(yīng)。第3變換爐出口的變換氣進(jìn)入煤氣預(yù)熱器進(jìn)行換熱后,依次經(jīng)過(guò)各臺(tái)換熱器、分離器進(jìn)行降溫、分離冷凝水后,出界區(qū)去低溫甲醇洗裝置[7]。 變換裝置工藝流程見(jiàn)圖1-2。 圖1-2 Shell粉煤氣化變換裝置工藝流程圖 小結(jié):該工藝,目前各臺(tái)變換爐的出口一氧化碳含量均滿足生產(chǎn)要求,催化劑床層熱點(diǎn)溫度均控制在正常范圍內(nèi),滿足了高負(fù)荷生產(chǎn)的要求。最關(guān)鍵的是變換裝置的蒸汽用量低,節(jié)約了蒸汽用量,達(dá)到節(jié)能降耗的要求;同時(shí)還大大延長(zhǎng)催化劑的使用壽命,收到良好的經(jīng)濟(jì)效益。 1.2.4 變換兼COS水解工藝[8] 1.COS水解的平衡濃度 COS水解反應(yīng)
39、為:COS+H2O=CO2+H2S △H= -35.5KJ/mol 通常變換爐出口的水解氣體濃度:進(jìn)口 COS-5ppm;H2S-150mg/Nm3; CO2-29%;汽氣比:0.18 根據(jù)COS水解的平衡常數(shù),計(jì)算各溫度下的COS水解的平衡濃度:即未脫硫、脫碳的變換氣其水解反應(yīng)在≤200℃下,其平衡的COS都能~0.1ppm。 2.流程優(yōu)點(diǎn) (1)充分利用COS水解催化劑的高溫活性極高的特點(diǎn),大幅度節(jié)省了催化劑的投資;盡管反應(yīng)溫度高,平衡COS濃度也較高,但其汽氣比為低溫反應(yīng)的10倍左右,有利于降低平衡COS濃度。 (2)由于水解爐設(shè)置在變換爐后,變換氣
40、中氧含量為約零,催化劑不易引起硫沉積及表面硫酸鹽化失活,延長(zhǎng)使用壽命。 3.國(guó)外類(lèi)似工藝[9~10] 如圖1-3所示 圖1-3 TVA煤基合成氣的催化裝置 國(guó)外托普索公司1982年在美國(guó)田納西流域管理局(TVA)建設(shè)了煤基德士古爐合成氨裝置,將耐硫變換催化劑與水解催化劑置于一套系統(tǒng) 1.2.5 變換兼硫化物加氫工藝 1.COS、CS2、噻吩加氫反應(yīng) COS加氫反應(yīng)為:COS+H2═CO+H2S △H=10.7 kJ/mol 通常變換爐中變(或全低變一變)出口的氣體組分: 進(jìn)口 COS-5ppm;H2S-100mg/Nm3;CO-
41、5%;汽氣比:0.18 有機(jī)硫氫解平衡常數(shù)隨溫度升高而下降,但其數(shù)值較大,即使在500℃下平衡常數(shù)仍較大。對(duì)較難脫除的噻吩,雖采用較高的操作溫度,但不會(huì)因化學(xué)平衡限制而影響脫硫效果。 2.流程具體應(yīng)用 在變換爐的高溫處(≥350℃)添加湖北省化學(xué)研究所的有機(jī)硫加氫催化劑。該有機(jī)硫加氫催化劑,為φ4~6球形,活性組分為鈷鉬,使用時(shí)采用自然硫化即可。 中低低流程放置在中變底部,全低變流程放置在一變或二變底部。根據(jù)工藝及要求選擇空速,一般取~12000h-1,即4萬(wàn)t合成氨需1.5m3。出口的COS~1ppm,檢測(cè)不到噻吩及CS2,特別適合于有機(jī)硫偏高的變換工藝
42、,顯著降低了精脫硫的負(fù)擔(dān),延長(zhǎng)了精脫硫催化劑的壽命。 3.工業(yè)應(yīng)用 該工藝流程目前在湖北荊門(mén)中天集團(tuán)單醇系統(tǒng)2.0 MPa變換系統(tǒng)中得到應(yīng)用,該廠改造前流程采用一段中變催化劑,由于需要出口CO≥20%,反應(yīng)汽氣比較低,使中變催化劑發(fā)生過(guò)度還原及硫中毒。造成催化劑粉化,床層阻力上升,嚴(yán)重影響正常生產(chǎn),同時(shí)COS的轉(zhuǎn)化率也不高,出口COS~20ppm,極大影響后續(xù)的精脫硫效果,為此,采用全低變流程,以達(dá)到根除中變催化劑過(guò)度還原及硫中毒問(wèn)題,并在后面添加有機(jī)硫加氫催化劑及高溫水解催化劑,出口COS~0.5ppm。未檢測(cè)到CS2及噻吩,達(dá)到預(yù)期效果。山西原平化肥廠10萬(wàn)t,2002年1月應(yīng)
43、用,取得預(yù)期效果[11]。 1.2.6 小結(jié) 通過(guò)以上幾種變換工藝的比較,目前國(guó)內(nèi)外比較節(jié)能、成熟的是非飽和塔型變換工藝,根據(jù)新型催化劑的研發(fā),由以前的中、高溫變換逐步過(guò)渡到低溫變換工藝。與此同時(shí)還將COS、CS2、噻吩加氫工藝兼顧,使得整個(gè)工藝節(jié)能、高效。 1.3 設(shè)計(jì)范圍、裝置組成及建設(shè)規(guī)模 1.3.1 設(shè)計(jì)的范圍 (1)年產(chǎn)60萬(wàn)t煤制甲醇CO變換生產(chǎn)工藝流程的設(shè)計(jì) (2)物料衡算、熱量衡算 (3)主要生產(chǎn)設(shè)備設(shè)計(jì)計(jì)算與選型 (4)環(huán)保措施 (5)編寫(xiě)設(shè)計(jì)說(shuō)明書(shū) (6)繪制設(shè)計(jì)圖紙 1.3.2 生產(chǎn)裝置組成 設(shè)生產(chǎn)車(chē)間1個(gè),是一氧化
44、碳變換車(chē)間,生產(chǎn)裝置有預(yù)變換爐、變換爐、增濕器、廢熱鍋爐、換熱器、加熱器、預(yù)熱器、泵。 動(dòng)力:包括供排水、鍋爐供熱、軟水脫鹽水、供電,由總廠提供。 輔助室、生活室。 1.3.3 建設(shè)規(guī)模 生產(chǎn)能力: 年產(chǎn)60萬(wàn)噸煤制甲醇,年開(kāi)工日為330天,日產(chǎn)為1818.18噸,75.76噸/小時(shí)。 工作制度: 變換車(chē)間日工作小時(shí)為24小時(shí),每日3班輪流替換,每班8小時(shí)連續(xù)生產(chǎn),共4個(gè)班。 第2章 工藝詳述 對(duì)以上工藝的分析比較,非飽和塔型工藝是比較節(jié)能經(jīng)濟(jì)的,低溫變換能夠很大程度的提高變換率,因此本次設(shè)計(jì)采用“非飽和塔型全低變”工藝,以當(dāng)今耐硫變換催化
45、劑的主體鈷鉬系變換催化劑為催化劑QCS-03,其組分為1%~5%CoO,8%~15%MoO3/γ/A12O3[12~13]。采用氣體增濕器、預(yù)變換爐、變換爐、加熱器、廢熱鍋爐等設(shè)備。 2.1 一氧化碳變換系統(tǒng)流程 煤氣化裝置制得的粗煤氣中,除含有氫外,一氧化碳含量(干基,下同)高達(dá)60%左右,同時(shí)H2S含量高、氣體流量大,為了適應(yīng)煤氣化送來(lái)的高硫粗煤氣工藝條件和滿足后序甲烷化精制工藝的要求,采用分段(三段)變換工藝。先在預(yù)變換爐較高溫度下,將其中大部分一氧化碳變換,再在低溫變換爐中于較低溫度下將一氧化碳變換。因?yàn)樵谳^低溫度下反應(yīng),剩余的一氧化碳含量可以達(dá)到足夠低的程度,一般可降到
46、低于4% 。在傳統(tǒng)合成氨工藝中,一氧化碳變換通常是在鐵-鉻和銅-鋅變換催化劑的存在下進(jìn)行的,但硫是這兩種催化劑的毒物,因此在高硫氣氛下,現(xiàn)有的甲醇裝置、合成氨裝置選用耐高溫的鈷-鉬耐硫變換催化劑。 由煤氣化工段送來(lái)的160℃、3.7MPa的粗煤氣進(jìn)入氣體增濕器,氣體增濕器頂部的工藝氣與來(lái)自界區(qū)外過(guò)熱中壓蒸汽、本工序中壓廢熱鍋爐副產(chǎn)的中壓蒸汽及本工序汽提后的少量工藝?yán)淠夯旌现良s200℃后,進(jìn)入原料氣預(yù)熱器升溫至250℃進(jìn)入預(yù)變換爐,爐內(nèi)裝填有活性組分較低的耐硫變換保護(hù)劑,主要用于阻擋煤粉塵、炭黑等固體雜質(zhì),吸附As、Cl等對(duì)催化劑有毒害作用的組分,以保護(hù)耐硫變換催化劑;同時(shí)進(jìn)行適度變換反應(yīng),
47、反應(yīng)溫升應(yīng)控制在30℃以?xún)?nèi)。離開(kāi)預(yù)變換爐(約280℃)的變換氣進(jìn)入1#變換爐進(jìn)行深度一氧化碳變換反應(yīng),出口氣中CO含量約15.13%。離開(kāi)1#變換爐(約450℃)的高溫中變氣分3路:一路進(jìn)入1.1 MPa低壓蒸汽過(guò)熱器的管側(cè);一路進(jìn)入調(diào)整換熱器,與進(jìn)入甲烷化爐的氫氮?dú)鈸Q熱;另一路進(jìn)入中壓廢熱鍋爐的管側(cè),把熱量傳給來(lái)自工藝?yán)淠浩崴岷蟮睦淠海碑a(chǎn)4.0MPa的中壓蒸汽,經(jīng)壓力控制調(diào)節(jié)閥調(diào)節(jié)壓力后送預(yù)變換爐前作為工藝蒸汽使用。 氣體出低壓蒸汽過(guò)熱器、調(diào)整換熱器和中壓廢熱鍋爐后,經(jīng)工藝?yán)淠捍憷湓鰸?,溫度降?30℃,進(jìn)入2#變換爐,反應(yīng)后出口溫度為350℃,氣體中CO含量降至5.83%。
48、2#變換爐出口變換氣進(jìn)入低壓蒸汽廢熱鍋爐的管側(cè),傳熱給鍋爐水,副產(chǎn)1.1 MPa的蒸汽,經(jīng)壓力控制調(diào)節(jié)閥調(diào)節(jié)壓力后進(jìn)入低壓蒸汽過(guò)熱器過(guò)熱。氣體溫度降至220℃后進(jìn)入3#變換爐,反應(yīng)后出口氣體中CO含量降為2.63%,此變換氣進(jìn)入低壓廢鍋管側(cè),傳熱給鍋爐水,副產(chǎn)0.45MPa低壓蒸汽。變換系統(tǒng)流程如圖2-1。 圖2-1 變換系統(tǒng)流程 1-氣體增濕器 2-原料氣預(yù)熱器 3-開(kāi)工加熱器 4-預(yù)變換爐A 5-預(yù)變換爐B 6-1#變換爐 7-蒸汽預(yù)熱器 8-甲烷化入口加熱器 9-1#廢熱鍋爐 10-2#變換爐 11-2#廢熱鍋爐 12-3#變換爐 13-3#廢熱鍋爐
49、 2.2 一氧化碳變換系統(tǒng)影響因素 2.2.1 壓力 一氧化碳變換反應(yīng)前后氣體的分子數(shù)相同,若為理想氣體,壓力對(duì)于反應(yīng)的平衡沒(méi)有影響。目前的工業(yè)操作條件下:壓力4.0 MPa氣壓下,溫度為200~500 ℃時(shí),壓力對(duì)于變換反應(yīng)沒(méi)有顯著的影響。但是在較高壓力下,反應(yīng)物濃度增加,分子間的有效碰撞次數(shù)增加,可以加快變換反應(yīng)速度,提高催化劑的生產(chǎn)能力。且各種氣體與理想氣體有一定的偏差,必須根據(jù)各氣體組分的逸度計(jì)算KP,因此壓力對(duì)CO的變換反應(yīng)有一定的影響。 2.2.2 溫度 溫度對(duì)變換反應(yīng)的影響較大:溫度升高,反應(yīng)速度加快。從化學(xué)平衡來(lái)看,降低反應(yīng)溫度,增加蒸汽用量,有利于反應(yīng)
50、向生成氫氣和二氧化碳的方向進(jìn)行,可以提高CO平衡轉(zhuǎn)化率。在變換反應(yīng)的初期,反應(yīng)物濃度高,提高反應(yīng)溫度,可加快正反應(yīng);在變換反應(yīng)的后一階段,二氧化碳和氫氣的濃度增加,逆反應(yīng)速度加快,因此,須設(shè)法降低反應(yīng)溫度,使逆反應(yīng)速度減慢,這樣可以得到較高的變換率。但降低溫度也減慢了反應(yīng)速度,降低了催化劑的生產(chǎn)能力,應(yīng)綜合考慮。對(duì)于一氧化碳含量較高的半水煤氣,開(kāi)始反應(yīng)時(shí),為了加快反應(yīng)速度,一般要在較高的溫度下進(jìn)行,而在反應(yīng)的后一階段,為了使反應(yīng)比較完全,就必須使溫度降低一些,工業(yè)上采取的兩段中溫變換就是根據(jù)這一概念設(shè)計(jì)確定的。對(duì)于一氧化碳含量在2%~4%的中溫變換氣體,只需要在230 ℃左右,用低溫變換催化劑
51、進(jìn)行低溫變換。此外,反應(yīng)溫度與催化劑的活性有很大的關(guān)系,一般工業(yè)用的變換催化劑低于某一溫度反應(yīng)便不能正常進(jìn)行,而高于某一溫度也會(huì)損壞催化劑,因此一氧化碳變換反應(yīng)必須在催化劑的適用溫度范圍內(nèi)選擇合理的工藝條件。 綜合各方面因素,變換溫度條件一般這樣來(lái)決定: (1)應(yīng)在觸媒的活性溫度范圍來(lái)操作。運(yùn)行中床層熱點(diǎn)不要超過(guò)溫度上限。 (2)在觸媒使用初期或觸媒活性較好的情況下,應(yīng)盡量控制在較低的溫度,既可以達(dá)到反應(yīng)要求,又可以起到防止催化劑過(guò)早衰老的效果。而在觸媒使用后期或觸媒活性下降后,就應(yīng)逐漸提高反應(yīng)溫度,以反應(yīng)速度的提高來(lái)彌補(bǔ)活性的下降,最終達(dá)到變換率的要求。 (3)為了盡可能接近最佳溫度
52、線進(jìn)行反應(yīng),可采用分段冷卻。這也是設(shè)置三個(gè)低變爐的原因之一。對(duì)于低變爐,值得注意的是,操作溫度不僅受到觸媒活性溫度的限制,而且還必須高于氣體在該壓力和水氣比下的露點(diǎn)溫度以上20℃。 2.2.3 水汽比 一般指水蒸汽的摩爾數(shù)同干原料氣的摩爾數(shù)之比,水汽比的提高有利于提高CO反應(yīng)的變換率,并加速變換反應(yīng)的進(jìn)行,防止副反應(yīng)的發(fā)生,同時(shí)有利于床層溫度的控制。但過(guò)高的水汽比,不但經(jīng)濟(jì)上不合理,且使催化劑床層的阻力增加,CO停留時(shí)間縮短,余熱回收設(shè)備負(fù)荷加重,且會(huì)使Co-Mo觸媒反硫化,并影響設(shè)備的生產(chǎn)能力。因此,要根據(jù)原料氣成份、變換率、反應(yīng)溫度及催化劑的活性等合理控制蒸汽比例,變換的水氣
53、比例一般為1.0~1.5之間[14]。 2.2.4 空速 空速是指單位時(shí)間通過(guò)單位體積觸媒的氣體量??账龠^(guò)大,則氣體和觸媒的接觸時(shí)間短,CO來(lái)不及反應(yīng)就離開(kāi)了觸媒層,變換率低;過(guò)小,則通過(guò)觸媒層的氣量小,降低生產(chǎn)強(qiáng)度,形成浪費(fèi)。一般在催化劑活性好時(shí),反應(yīng)速度快,可以采用較大的空速,充分發(fā)揮設(shè)備的生產(chǎn)能力。在生產(chǎn)后期,觸媒活性較差時(shí),適當(dāng)降低空速,以保證出口CO的含量。由于進(jìn)料速度大小直接反映了系統(tǒng)生產(chǎn)能力的高低, 因而, 催化劑對(duì)高空速的適應(yīng)能力也是衡量催化劑性能優(yōu)劣的一個(gè)重要標(biāo)志。 2.2.5 CO2的影響 在變換反應(yīng)過(guò)程中,如果能將生成的CO2除去,就可以使變換
54、反應(yīng)向右移動(dòng),提高CO的變換率,此方法一般在氮肥工業(yè)裝置中使用,本設(shè)計(jì)由于變換屬于部分變換,所以無(wú)須采用此方法。 2.2.6 副反應(yīng)的影響 CO變換過(guò)程中,可能發(fā)生CO分解析出C和生成CH4等副反應(yīng),其反應(yīng)式如下: 副反應(yīng)不僅消耗原料氣中有效成分H2和CO,增加了無(wú)用成分CH4的含量,而且CO分解后析出的游離碳極容易附著在催化劑表面上,使催化劑的活性降低。以上這些副反應(yīng)均為體積減小的放熱反應(yīng),因此提高溫度、降低壓力可抑制副反應(yīng)的進(jìn)行。但在實(shí)際生產(chǎn)中所采用的工藝條件下,這些副反應(yīng)一般不容易發(fā)。 2.2.7 入口
55、溫度 操作中根據(jù)催化劑活性情況,開(kāi)始使用催化劑時(shí),催化劑活性比較高,可控制變換爐入口比較低的溫度,隨著使用時(shí)間增加,催化劑活性降低時(shí),可適當(dāng)提高變換爐入口溫度。一般地操作中根據(jù)催化劑活性情況,讓下一段的溫度較上一段低5~15℃,這樣每一段的平衡CO含量就能依次降低,就保證把CO含量降至低的程度。 2.2.8 催化劑活性 & B/ |1 _, X$ O& o開(kāi)始使用催化劑時(shí),催化劑活性比較高,床層熱點(diǎn)溫度在床層上部,隨著使用時(shí)間增加,催化劑活性降低時(shí),床層熱點(diǎn)溫度逐漸下移。目前變換裝置都采用耐硫鈷鉬系變換催化劑,這種催化劑有較寬的耐硫區(qū)間。它的有效成分為:1%~5%CoO,8%
56、~15%MoO3/γ/A12O3[15]。 2.2.9 煤氣中CO的含量 3.2.333煤氣中CO的含量越高,反應(yīng)熱就越多,床層溫度也就越高,反之就低.應(yīng)通過(guò)負(fù)荷,汽氣比等來(lái)調(diào)節(jié)床層溫度,防止超溫和析碳的發(fā)生。 綜上所述變換反應(yīng)該在一下條件下進(jìn)行: 1.CO干基每降低1%,溫度上升8.3℃,在實(shí)際中,只有5℃左右,因?yàn)樗羝獛ё叽罅康臒?,也就是為什么在床層溫度上升的時(shí)候,會(huì)考慮加大蒸汽。 2.壓力越高的話,溫度越高。一般操作壓力是由前系統(tǒng)的操作壓力決定。 3.負(fù)荷,減負(fù)荷的時(shí)候溫度升高,是因?yàn)闅饬窟^(guò)小,帶走熱量少。加負(fù)荷時(shí),溫度上升,因?yàn)樵蠚舛?,反?yīng)熱大。所以加減負(fù)荷不能太頻
57、繁,這樣爐溫一定超。負(fù)荷波動(dòng)時(shí),要及時(shí)調(diào)節(jié)水蒸汽和入口溫度。 4.# [9 e" f. K/ |( B- e( v4444入口溫度是為了保持床層熱點(diǎn)溫度在一定范圍。這是一個(gè)經(jīng)驗(yàn)值。一般在催化劑初期使用時(shí)期較低,到后期較高。一般溫度在220℃~280℃。 5.水氣比是根據(jù)工藝決定。當(dāng)然在生產(chǎn)時(shí),選擇什么樣的工序,都會(huì)影響水汽比。比如氣化爐使用水冷壁降溫,則氣體會(huì)比較干燥,這需要在進(jìn)入變換爐之前就加入適量的蒸汽。如果前系統(tǒng)直接用水噴淋冷卻,工藝氣進(jìn)變換為部分飽和或飽和,需要分離除水。 2.3 操作制度 2.3.1 入口溫度的控制 影響入口溫度的因素:系統(tǒng)壓力、
58、氣量、變換爐系統(tǒng)溫度、氣體帶水等。入口溫度的控制是變換爐操作的關(guān)鍵。 2.3.2 床層溫度的控制 影響因素:氣量、水汽比、入口溫度、氣體中的CO含量及催化劑的活性等。 控制方法:正常生產(chǎn)中,一般是通過(guò)控制進(jìn)口溫度,達(dá)到控制熱點(diǎn)溫度的目的。若入口CO含量高、反應(yīng)熱過(guò)大,造成熱點(diǎn)長(zhǎng)期超標(biāo),可通過(guò)氣化調(diào)整。 2.3.3 出口CO指標(biāo)的控制 影響因素:氣量、床層溫度、催化劑的活性、水氣比、煤氣加熱器的設(shè)備情況等。 控制方法:主要是穩(wěn)定入口溫度、熱點(diǎn)溫度在指標(biāo)范圍之內(nèi),要求氣化應(yīng)確保水氣比在指標(biāo)之內(nèi)。若催化劑使用后期,可適當(dāng)提高入口溫度,以達(dá)到降低出口CO含量的目的,若催化劑失活
59、則需要再硫化或停車(chē)更換。若煤氣加熱器內(nèi)漏,則會(huì)造成變化爐出口氣中CO含量上升,內(nèi)漏量較小時(shí),可維持生產(chǎn),內(nèi)漏量較大時(shí),則要停車(chē)處理。 2.3.4 變換爐壓差 造成床層壓差上升的因素:負(fù)荷過(guò)大,氣體中粉塵含量多,催化劑結(jié)皮或粉化、儀表測(cè)量不準(zhǔn)。 控制及處理方法:一般正常生產(chǎn)中應(yīng)穩(wěn)定氣量,減少開(kāi)停車(chē)次數(shù)。負(fù)荷的增加雖然使壓差上升,但一般均在正常范圍內(nèi),煤氣中粉塵量大,催化劑結(jié)皮或粉化,一般是在一個(gè)較長(zhǎng)時(shí)間內(nèi)逐漸上升,若阻力過(guò)大會(huì)影響生產(chǎn),則應(yīng)利用停車(chē)時(shí)間降溫鏟除結(jié)皮或過(guò)篩。因此生產(chǎn)負(fù)荷的長(zhǎng)期穩(wěn)定是對(duì)催化劑的最好保護(hù)。 2.4 一氧化碳變換系統(tǒng)中存在的問(wèn)題 催化劑的反硫化和失活是本
60、工藝中存在的一個(gè)重要問(wèn)題,根據(jù)動(dòng)力學(xué)的研究和催化劑表征認(rèn)為,在含硫半水煤氣中催化劑的硫化和反硫化處于動(dòng)態(tài)平衡,鈷鉬耐硫變換催化劑在活性組分處于硫化狀態(tài)下具有活性,因此對(duì)工藝氣中硫含量對(duì)下限有嚴(yán)格的指標(biāo),要求使用的原料中含硫量不能低于200PPm,否則將出現(xiàn)反硫化現(xiàn)象而引起催化劑的失活。因此,應(yīng)避免已硫化的催化劑在無(wú)硫情況下操作。 鈷鉬系觸媒的反硫化主要是觸媒中的活性組分MoS2的反硫化,其化學(xué)方程式為:MoS2+2H2O → MoO2+2H2S-Q 在一定的反應(yīng)溫度、蒸汽量和H2S濃度下,會(huì)導(dǎo)致反應(yīng)向右進(jìn)行,使MoS2逐步轉(zhuǎn)變成MoO2,表現(xiàn)為催化劑的失活,生產(chǎn)中一旦發(fā)生反硫化現(xiàn)
61、象,催化劑的活性下降。在生產(chǎn)中,為了保證CO變化率,又必須增加蒸汽用量及提高反應(yīng)溫度,而蒸汽用量的增加和反應(yīng)溫度的提高雖暫保證了工藝要求,但又進(jìn)一步促進(jìn)了反硫化反應(yīng),失活進(jìn)一步加深,以致必須重新硫化催化,嚴(yán)重影響生產(chǎn)。 根據(jù)熱力學(xué)方程可知,反硫化反應(yīng)平衡常數(shù)Kp隨著溫度的提高而急劇增加,因此降低CO變換反應(yīng)溫度,有利于防止反硫化反應(yīng)的發(fā)生。 由反硫化的反應(yīng)方程式可以看出,水蒸汽量的增加會(huì)使反硫化反應(yīng)的發(fā)生,亦即是水氣比越大,會(huì)有利于反硫化反應(yīng)的進(jìn)行。H2S濃度越高,越促使氧化態(tài)物質(zhì)向硫化態(tài)方向反應(yīng),即生成活性組分的動(dòng)力越大。因此H2S濃度越高,可抑制反硫化反應(yīng),從而使活性區(qū)域越大[16]。
62、 因此,變換裝置在生產(chǎn)中首先要考慮到催化劑性能。在所有的生產(chǎn)中,以考慮催化劑性能參數(shù)為基點(diǎn),選擇合適的壓力、溫度、水汽比、入口溫度、處理量來(lái)進(jìn)行科學(xué)的生產(chǎn)。這樣才能實(shí)現(xiàn)變換的目標(biāo),實(shí)現(xiàn)最優(yōu)生產(chǎn)。 第3章 工藝計(jì)算 3.1 原始數(shù)據(jù) 1.干粗煤氣成分見(jiàn)表3-1。 表3-1 干氣成分 成分 H2 CO CO2 O2 N2 CH4 合計(jì) % 34.30 45.43 18.98 1.06 0.18 0.05 100 2.每小時(shí)粗煤氣量327200m3/h 3.粗煤氣溫度:160℃。 4.在預(yù)變爐中CO的轉(zhuǎn)化爐中CO的轉(zhuǎn)化率為41.62%,則預(yù)變換氣
63、組成見(jiàn)表3-2。 表3-2 預(yù)變換氣組成 成分 H2 CO CO2 O2 N2 CH4 合計(jì) % 43.87 26.52 28.32 1.00 0.24 0.05 100 5.觸媒型號(hào):QCS-03[17]。其性能見(jiàn)表3-3。 表3-3 QCS-03性能 項(xiàng)目 指標(biāo) 項(xiàng)目 指標(biāo) 活性組分 MoO3、CoO 堆比重 780~880kg/m3 載體 TiO2-MgO-Al2O3 三元載體 使用壓力 1.0~10.0 MPa 助劑 混合稀土 溫度范圍 220 ~500 ℃ 外觀形狀 灰綠色,條形 適應(yīng)水/氣 0.3~2
64、.0 mol/mol 尺寸 Φ3.5-4.0 mm 使用壽命 3~5年,可再生回用 破碎密度 ≥140 N/cm 工藝氣硫含量 200 ppm 3.2 變換爐工藝參數(shù)計(jì)算 3.2.1 1#變換爐工藝參數(shù)計(jì)算 1.1#變換爐進(jìn)、出口溫度的估計(jì) 根據(jù)QCS-03觸媒的活性溫度,選取混合濕粗煤氣進(jìn)1#變換爐溫度為280℃。 2.蒸汽比選擇 因采用水激冷,蒸汽比可以稍低一些,選擇1.4,則每立方米干粗煤氣中應(yīng)加入蒸汽量為 0.26521.4=0.372m3 3.加入蒸汽后的混合濕氣組成 4
65、.1#變換爐平衡曲線計(jì)算[18],見(jiàn)表3-4。 式中A、B、C、D——預(yù)變換氣中CO、H2O、CO2、H2起始濃度(%)。 令 表3-4 平衡曲線計(jì)算 t(℃) 280 320 360 400 440 460 T(K) 553 593 633 673 713 733 KP 51.576 29.518 18.129 11.798 8.057 6.763 w=KP-1 50.576 28.518 17.129 10.798 7.057 5.763 u=K
66、P(A+B)+(C+D) 24.478 14.234 8.945 6.005 4.268 3.667 v=KPAB-CD 2.637 1.481 0.884 0.552 0.356 0.288 8.105 5.802 4.410 3.495 2.858 2.609 0.837 0.765 0.685 0.601 0.517 0.475 5.1#變換爐操作線計(jì)算 1#變換爐出口溫度取為450℃。450℃時(shí)反應(yīng)熱-△HR=8990kcal/mol,濕粗氣由280℃升至450℃,平均溫度365℃,則混合氣真實(shí)分子比熱為 CP=0.31987.02+0.19337.35+0.206411.50+0.00737.68+0.00177.26+0.000413.10+ 0.27119.15=8.59kcal/mol﹒℃ 1#變換爐熱損失溫降為15℃,按操作線方程式 變換掉的 CO=0.19330.429=0.0829 出1#變換爐氣體組成 H2:0.3198+0.0829-
- 溫馨提示:
1: 本站所有資源如無(wú)特殊說(shuō)明,都需要本地電腦安裝OFFICE2007和PDF閱讀器。圖紙軟件為CAD,CAXA,PROE,UG,SolidWorks等.壓縮文件請(qǐng)下載最新的WinRAR軟件解壓。
2: 本站的文檔不包含任何第三方提供的附件圖紙等,如果需要附件,請(qǐng)聯(lián)系上傳者。文件的所有權(quán)益歸上傳用戶所有。
3.本站RAR壓縮包中若帶圖紙,網(wǎng)頁(yè)內(nèi)容里面會(huì)有圖紙預(yù)覽,若沒(méi)有圖紙預(yù)覽就沒(méi)有圖紙。
4. 未經(jīng)權(quán)益所有人同意不得將文件中的內(nèi)容挪作商業(yè)或盈利用途。
5. 裝配圖網(wǎng)僅提供信息存儲(chǔ)空間,僅對(duì)用戶上傳內(nèi)容的表現(xiàn)方式做保護(hù)處理,對(duì)用戶上傳分享的文檔內(nèi)容本身不做任何修改或編輯,并不能對(duì)任何下載內(nèi)容負(fù)責(zé)。
6. 下載文件中如有侵權(quán)或不適當(dāng)內(nèi)容,請(qǐng)與我們聯(lián)系,我們立即糾正。
7. 本站不保證下載資源的準(zhǔn)確性、安全性和完整性, 同時(shí)也不承擔(dān)用戶因使用這些下載資源對(duì)自己和他人造成任何形式的傷害或損失。
最新文檔
- 第七章-透射電子顯微鏡
- 群落的結(jié)構(gòu)(課件)
- 焊接基礎(chǔ)知識(shí)
- 水文地質(zhì)學(xué)課件
- 某公司員工工傷安全管理規(guī)定
- 消防培訓(xùn)課件:安全檢修(要點(diǎn))
- 某公司安全生產(chǎn)考核與獎(jiǎng)懲辦法范文
- 安全作業(yè)活動(dòng)安全排查表
- 某公司危險(xiǎn)源安全辨識(shí)、分類(lèi)和風(fēng)險(xiǎn)評(píng)價(jià)、分級(jí)辦法
- 某公司消防安全常識(shí)培訓(xùn)資料
- 安全培訓(xùn)資料:危險(xiǎn)化學(xué)品的類(lèi)別
- 中小學(xué)寒假學(xué)習(xí)計(jì)劃快樂(lè)度寒假充實(shí)促成長(zhǎng)
- 紅色插畫(huà)風(fēng)輸血相關(guān)知識(shí)培訓(xùn)臨床輸血流程常見(jiàn)輸血不良反應(yīng)
- 14.應(yīng)急救援隊(duì)伍訓(xùn)練記錄
- 某公司各部門(mén)及人員安全生產(chǎn)責(zé)任制
相關(guān)資源
更多