減速箱體說明書
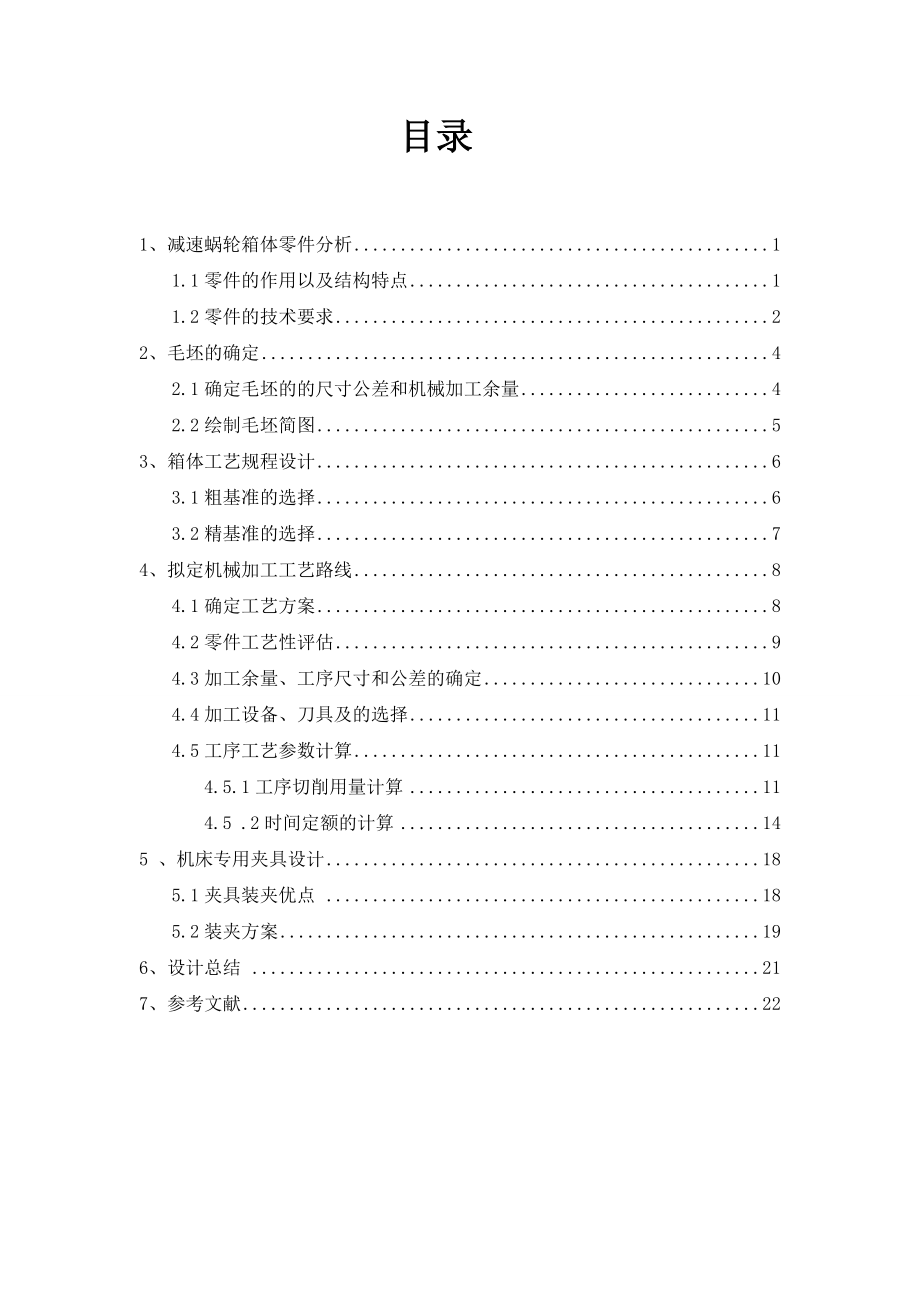


《減速箱體說明書》由會員分享,可在線閱讀,更多相關《減速箱體說明書(24頁珍藏版)》請在裝配圖網(wǎng)上搜索。
1、 目錄 1、減速蝸輪箱體零件分析 1 1.1零件的作用以及結構特點 1 1.2零件的技術要求 2 2、毛坯的確定 4 2.1確定毛坯的的尺寸公差和機械加工余量 4 2.2繪制毛坯簡圖 5 3、箱體工藝規(guī)程設計 6 3.1粗基準的選擇 6 3.2精基準的選擇 7 4、擬定機械加工工藝路線 8 4.1確定工藝方案 8 4.2零件工藝性評估 9 4.3加工余量、工序尺寸和公差的確定 10 4.4加工設備、刀具及的選擇 11 4.5工序工藝參數(shù)計算 11 4.5.1工序切削用量計算 11 4.5 .2時間定額的計算 14 5 、機床
2、專用夾具設計 18 5.1夾具裝夾優(yōu)點? 18 5.2裝夾方案 19 6、設計總結? 21 7、參考文獻 22 1、減速蝸輪箱體零件分析 1.1零件的作用以及結構特點 零件圖如下: 圖1小型蝸輪箱體的零件圖 減速器的箱體是傳動零件的底座和基礎,也是減速器重要扥組成部分,起固定箱體內零件的作用。它將機器或部件中的軸套、渦輪等相關的零件組成一個整體,使他們之間保持正確的相互位置,并按照一定的傳動關系傳遞運動或動力,并對內部零件起到清潔、潤滑和保護的作用。因此,箱體的加工質量將直接影響機器的或部件
3、的精度、性能和壽命。 減速器的箱體必須具備足夠的強度和剛度,以保證足夠的支撐力。此外由于渦輪蝸桿機構是一個發(fā)熱大的傳動機構,還應要求箱體具備較好的散熱能力。因此箱體鑄造通常使用灰鑄鐵或鑄鋼。整個箱體外表面的粗糙度和尺寸要求不高,但是對于箱體上兩孔端面的粗糙度要求較高,大孔和小孔的尺寸大小和孔內粗糙度有明確的要求,并且對兩孔的中心距也有較高的要求,箱體兩端孔都有明確的同軸度要求。 1.2零件的技術要求 孔的端面有較高的粗糙度要求,需要銑床加工達到技術要求,以打孔的端面作為粗基準,加工其他表面,大孔和小孔內表面都有較高的尺寸要求和粗糙度要求,應該用鏜床加工,分粗鏜
4、和精鏜并且可以用專用機夾具裝夾以達到技術要求,箱體的兩端孔都有較高的同軸度要求,可以用心軸定位,加工時要特別注意,大孔和小孔的中心線有較高的垂直度要求。這些孔和面的加工精度直接影響機器的裝配精度、使用性能和使用壽命。加工時特別注意。 零件圖上的技術要求: 1、 鑄件不得有砂眼、疏松等缺陷。 2、 非加工表面涂防銹漆。 3、 鑄件人工時效處理。 4、 箱體做沒有滲漏實驗。 5、 材料HT200。 表1 各加工表面技術要求 加工表面 尺寸及偏差mm 公差及精
5、度等級 CT 表面粗糙度um 形位公差 mm 箱體頂面 210x130 IT13 12.5 箱體底面 210x130 IT13 12.5 Φ120mm凸臺 Φ120mm IT8 3.2 Φ205mm凸臺 Φ205mm IT8 3.2 Φ90mm軸承孔 Φ IT7 1.6 同軸度0.06 Φ180mm軸承孔 Φ IT7 1.6 同軸度0.06 垂直度0.06 5xM16螺紋孔 M16 IT13 12.5 4xM6螺紋孔 M6 IT13 12.5 16xM8螺紋孔 M8 IT13 12.5
6、 2、毛坯的確定 2.1確定毛坯的的尺寸公差和機械加工余量 按技術要求蝸輪減速器箱體的材料是HT200,其毛坯是鑄件。材料抗拉強度為200N/,抗彎強度為400N/,硬度為HB170-241。 鑄鐵容易成型、切削性能好、價格低廉,并且具有良好的耐磨性和減振性,也是其它一般箱體常用的材料。箱體結構復雜,箱壁薄,故選用鑄造方法制造毛坯。產(chǎn)類型為大批生產(chǎn),可采用采用金屬模機器造型。此時毛坯的精度較高,加工余量可適當減低,則平面余量為5~10mm?,孔(半徑上)的余量為7~12mm?。機器造型,內腔安放型芯。鑄件需要人工實效處理。大批量生產(chǎn)的毛坯鑄件
7、的公差等級,確定毛坯鑄件的公差等級CT=10。由 “毛坯鑄件典型的機械加工余量等級”選取毛坯零件的機械加工余量等級為G。(R=FRAMCT/2 )(RAM:要求的機械加工余量)根據(jù)蝸輪減速器箱體零件最大輪廓尺寸(290mm),要求的鑄件機械加工余量確定該鑄件機械加工余量為3.5mm?,F(xiàn)將蝸輪減速器箱體毛坯尺寸公差與加工余量的計算結果列于下表: 表2蝸輪減速器箱體毛坯尺寸及加工余量 加工表面 毛坯尺寸公差等級 鑄件尺寸公差 (mm) 機械加工余量 (mm) 毛坯尺寸及公差 (mm) 箱體長215mm 10 4 3.5 2232 箱體高290mm 10
8、 4.4 3.5 2982.2 箱體寬135mm 10 3.6 3.5 1421.8 Φ180mm軸承孔 10 4 3.5 172.41.6 Ф90mm軸承孔 10 3.2 3.5 80.41.6 2.2繪制毛坯簡圖 圖1毛坯零件圖 3、箱體工藝規(guī)程設計 3.1粗基準的選擇 按照有關零件的粗基準的選擇原則:當零件有不加工表面時,應選擇這些不加工的表面作為粗基準,當零件有很多個不加工表面的時候,則應當選擇與加工表面要求相對位置精度較高的不加工表面作為粗基準。箱體粗基準選擇要求:
9、 (1) 在保證各加工表面均有加工余量的前提下,使主要孔加工余量均勻。 (2)若工件每個表面都有加工要求,為了保證各表面都有足夠的加工余量,應選擇加工量較少的表面為粗基準。 (3)若工件必須保證每個加工表面與加工表面之間的尺寸或位置要求,則應選擇某個加工面為粗基準。 (4)選擇基準的表面應盡可能平整,沒有鑄造飛邊,澆口,冒口或其他缺陷。粗基準一般只允許使用一次。 (5)裝入箱體內的旋轉零件應與箱體內壁有足夠的間隙。 (6)應保證定位、夾緊可靠。 一般箱體零件的粗基準都用它上面的重要孔和另一個相距較遠的孔作為粗基準,以保證孔加工時余量均勻。蝸輪減速器箱體加工選擇以重要表面孔Ф9
10、0mm及Ф180mm為粗基準,通過劃線的方法確定第一道工序加工面位置,盡量使各毛坯面加工余量得到保證,即采用劃線裝夾,按線找正加工即可。 3.2精基準的選擇 選擇精基準時,應從整個工藝過程來考慮如何保證工件的尺寸精度和位置精度,并要達到使用起來方便可靠。一般按下列原則來選擇: (1)基準重合原則:選擇設計基準作為定位基準。 (2)基準統(tǒng)一原則:盡可能在多數(shù)工序中選用統(tǒng)一的定位基準來加工其它各表面,可以避免基準轉換過程所產(chǎn)生的誤差,并可使各工序所使用的夾具結構相同或相似,從而簡化夾具的設計和制造。 (3)自為基準原則:有些精加工或光整加工工序要求加工余量小而均
11、勻,應選擇加工表面本身來作為定位基準。 (4)互為基準原則:對于相互位置精度要求高的表面,可以采用互為基準,反復加工的方法。 經(jīng)分析零件圖可知,箱體底面或頂面是高度方向的設計基準, 中心軸線是長度和寬度方向的設計基準。箱體零件常以裝配基準或專門加工的一面兩孔定位,使得基準統(tǒng)一。 蝸輪減速器箱體中Ф90軸承孔和Ф180軸承孔有一定的尺寸精度和位置精度要求,其尺寸精度均為IT7級,位置精度包括:Ф90軸承孔對Ф90軸承孔軸線的同軸度公差為Ф0.05、 Ф180軸承孔對Ф180軸承孔軸線的同軸度公差為Ф0.06、 Ф180軸承孔軸線對Ф90軸承孔軸線的垂直度公差為0.06。為了保證以
12、上幾項要求,加工箱體頂面時應以底面為精基準,使頂面加工時的定位基準與設計基準重合;加工兩對軸承孔時,仍以底面為主要定位基準,這樣既符合“基準統(tǒng)一”的原則,也符合“基準重合”的原則,有利于保證軸承孔軸線與裝配基準面的尺寸精度。 4、擬定機械加工工藝路線 4.1確定工藝方案 通過對零件圖的結構、技術要求、工藝分析以及毛坯的分析,歸納出一下表格所示的加工工藝: 表3加工工藝路線 工序號 工序名稱 工序內容 工藝裝備 1 鑄 鑄造清砂?熱處理人工時效處理涂底漆 2 劃線 劃φ180.0+0.035 0m
13、m、φ90+0.027 0mmmm孔加工線,劃上、下平面加工線 3 銑工 以頂面毛坯定位,按線找正,粗銑底面? X51 4 銑工 以底面定位裝夾工件,粗銑頂面,保證尺寸為290mm X51 5 銑工 以底面定位,壓緊頂面按線銑φ90mm兩孔側面凸臺,保證尺寸為217mm?,表面粗糙度為3.2 X51 6 銑工 以底面定位,壓緊頂面按線找正,銑φ180.0mm兩孔側面,保證尺寸為137mm? X51 7 粗鏜 以底面定位,按φ90+0.027 0mm孔端面找正,壓緊頂面,粗鏜φ90+0.027 0孔至尺寸為φ88+0.5 0mm粗刮平面保
14、證總長尺寸215mm為216mm,刮φ90+0.027 0mm內端面,保證尺寸35.5mm加工φ180.0+0.035 0mm孔尺寸至φ1780 -0.5-mm T68 8 半精鏜 工作臺不動,以底面為精基準,壓緊工件,同時注意φ180.0孔中心與底面的相對高度,半精鏜φ180.0+0.035 0mm至Φ179.3+0.16 0mm,半精鏜Φ90+0.054 0mm至Φ89.4+0.14 0mm。 T68 9 精鏜 將機床上工作臺旋轉回零位,調整工件壓緊力(工件不動),精鏜φ90+0.027 0mm至圖樣尺寸,精
15、刮兩端面至尺寸215mm。精鏜φ180.0+0.035 0mm孔至圖樣尺寸,精刮兩側面保證總厚135mm,保證與φ90+0.027 0mm孔距尺寸1000.12mm,內表面粗糙度為1.6 T68 10 劃線 劃兩處16xM8、5xM16、4xM6各螺紋孔加工線 11 鉆 鉆頂面底面M16螺紋,攻絲 Z3032 12 鉆 鉆側面M8螺紋,攻絲 Z3032 13 鉗工 ?修毛刺?煤油滲漏試驗 14 檢驗 按圖樣檢查工件各部尺寸及精度 15 入庫 上油入庫 4.2零件工藝性評估 工藝分析?: ?1)在加工前,安排
16、劃線工藝是為了保證工件壁厚均勻,并及時發(fā)現(xiàn)鑄件的缺陷,減少廢品。? ??? ?2)該工件體積小,壁薄,加工時應注意夾緊力的大小,防止變形。精鏜前要求對工件壓緊力進行適當?shù)恼{整,也是確保加工精度的一種方法。? ???? 3)mm與+mm兩孔的垂直度0.06mm要求,由T68機床分度來保證。? ??? 4)+mm與+mm兩孔孔距100±0.12mm,可采用裝心軸的方法。 由零件圖可知,渦輪兩端的軸承孔的端面有較高的表面要求,與蝸桿軸承孔的相對精度很高,并在軸向方向上均高于相鄰表面,因此需采用銑床加工,這樣可以,提高生產(chǎn)率,同樣,為了保證渦輪蝸桿安置在基座上的穩(wěn)定性,并盡可能
17、減少底座平面的機械加工面積,箱體座不采用完整的平面;直徑180mm和直徑90mm的兩個大小軸承孔的端面為平面,可保證加工過程中鉆頭的位置精度,不用過于復雜的定位,可以速度按加工時間,除主要工作表面外,其余表面的加工精度較低,不需要高精度機床加工;雖然主要工作表面雖然加工精度高,但也可以在正常的條件下生產(chǎn),并且較經(jīng)濟而且質量地加工。由此可見,該箱體零件的工藝性較好。 4.3加工余量、工序尺寸和公差的確定 表4工序尺寸及公差計算表 (單位:mm ) 部位 工序 加工余量 基本尺寸 精度等級 工序尺寸 箱體290m
18、m上、下端面 粗銑箱體下端面 4 290 IT13(0.81) 2900 -0.081 粗銑箱體上端面 4 294 IT13(0.81) 2940 -0.081 毛坯 8 298 CT10(4.4) 2982.2 箱體215mm左、右端面 精銑(左端面) 1.0 215 IT8(0.063) 2150 -0.063 精銑(右端面) 2.0 217 IT8(0.063) 2160 -0.063 粗銑(左端面) 2.0 219 IT13(0.63) 2190 -0.063 粗銑(右端面) 2.0 221
19、 IT13(0.63) 2210 -0.063 毛坯 8 223 CT10(4) 2232 箱體135mm前、后端面 精銑(前端面) 1.0 135 IT8(0.063) 1350 -0.063 精銑(后端面) 1.0 136 IT8(0.063) 1360 -0.063 粗銑(前端面) 2.5 137 IT13(0.72) 1370 -0.072 粗銑(后端面) 2.5 139.5 IT13(0.72) 139.50 -0.072 毛坯 7 142 CT10(3.6) 1421.8 箱體Ф90
20、 mm孔 精鏜 -0.6 Φ90 IT8(0.054) Φ90+0.054 0 半精鏜 -1.2 Φ89.4 IT10(0.14) Φ89.4+0.14 0 粗鏜 -5.8 Φ88.2 IT12(0.35) Φ88.10 +0.35 毛坯 -7.6 Φ80.4 CT10(3.2) Φ80.41.6 箱體Ф180 mm孔 精鏜 -0.6 180 IT8(0.063) Φ180+0.063 0 半精鏜 -1.2 Φ179.3 IT10(0.16) Φ179.3+0.16 0 粗鏜 -5.8 Φ178.2 IT
21、12(0.40) Φ178.2+0.40 0 毛坯 7.6 Φ172.4 CT10(3.2) Φ172.41.6 4.4加工設備、刀具及的選擇 加工設備與工藝設備 工序4精銑底面和粗銑底面,因定位基準相同。故選用立銑床選擇X51立銑床。 工序6、7、8、9銑兩側至圖樣要求,宜采用立銑床,選擇X51立銑床。 工序10、11、12粗鏜、半精鏜、精鏜孔Φ90mm和Φ180mm選用T68臥式銑鏜。 工序14鉆、攻各螺紋選用Z3032立式鉆床。 4.5工序工藝參數(shù)計算 4.5.1工序切削用量計算 1、工序4切削用量的計算: 背吃刀量的確定:每一工步
22、的加工余量為4mm,參照表4每一個工步背吃刀量分別為:a1=2mm,a2=2mm 進給量的確定:機床功率5~10kw工件夾具系統(tǒng)剛度為中等條件選取,該工序的每齒進給量fz =0.2mm/r。 銑削速度的計算:鑲齒銑刀、d/z=125/14的條件選取,銑削速度可取為34.6m/min。由公式可得工序銑刀轉速n=1000x34.6/(125xπ)=91.82r/min立式銑床的主軸轉速,取轉速100r/min??汕蟪鲈摴ば虻膶嶋H銑削速度:v=nπd/1000=80r/minxπx125mmx1000m/min=31.4m/min 2、工序5切削用量的計算: 粗精銑Φ90mm兩孔側面凸
23、臺。 背吃刀量的確定:參照表4,每一個工步中的背吃刀量為3mm 進給量的確定:,按機床功率5~10kw工件夾具系統(tǒng)剛度為中等條件選取,該工序的每齒進給量fz=0.2mm/z 銑削速度的計算:按d/z=120/16的條件選取,銑削速度v可取為41.4m/min由公式n=1000v/πd可得工序銑刀轉速n=109.4r/min,取轉速120r/min??汕蟪鲈摴ば虻膶嶋H銑削速度:v=nπ d/1000=80r/minx160mmx1000=40.212m/min 精銑Φ90mm兩孔側面凸臺。 背吃刀量的確定:每一工步的加工余量為1.0mm,每一個工步中的背吃
24、刀量為:ɑp==1.0mm . 進給量的確定:由表4,按表面粗造度Ra2.5um的條件選取,該工序的進給量f=1mm/r 銑削速度的計算:按鑲齒銑刀d/z=120/16、fz=0.06mm/z的條件選取,銑削速度v可選取為59.4m/min。由公式n=1000v/πd可求得該工序銑刀轉速=157.6r/mm,取主軸轉速160r/min??汕蟪鲈摴ば虻膶嶋H銑削速度:v=nπ d/1000=80r/minx320mmx1000=148.6m/min 3、工序5切削用量計算: 粗銑Φ180mm孔側面凸臺。背吃刀量的確定:每一工步的加工余量為2.5mm,參照表6,每一個工步中的背
25、吃刀量為2.5。 進給量的確定:按機床功率5~10kw工件夾具系統(tǒng)剛度為中等條件選取,該工序的每齒進給量fz=0.2mm/z。 . 銑削速度的計算:d/z=120/16的條件選取,銑削速度可取為41.4m/min。由公式n=1000v/πd可得工序銑刀轉速。n=1000x41.4/(πx160)=109.4r/min立式銑床的主軸轉速,取轉速120r/min??汕蟪鲈摴ば虻膶嶋H銑削速度: v=nπ d/1000=80r/minx160mmx1000=40.212m/min 精銑Φ180mm兩孔側面和凸臺。背吃刀量的確定 :每一工步的加工余量為1.0mm,每一個工步中的背
26、吃刀量為:mm 進給量的確定:按表面粗造度Ra2.5um的條件選取,進給量取f=0.15mm/r。 銑削速度的計算:按鑲齒銑刀d/z=160/16、fz=f/z=0.06mm/z的條件選取,銑削速度v可選取為59.4m/min。由公式n=1000v/πd可求得該工序銑刀轉速n=1000x59.4/(πx160)=157.2r/min參照立式銑床的主軸轉速,取轉速160r/mm。可求出該工序的實際銑削速度:v=nπd/1000=60r/minx160mmx1000=80m/min 4、工序7 切削用量的計算: 粗鏜Φ90mm孔和Φ180mm。背吃刀量為:ɑ1=2.
27、9mm,ɑ2=2.9mm 進給量的確定:參照表4,按表背吃刀量ap =3mm條件選取,該工序的進給量f=0.5mm/r。 鏜削削速度的計算:按加工方法和刀具材料、刀具類型以及被加工零件材料選取鏜速度:v=0.6m/s=36m/min由于粗鏜后孔的直徑分別為Φ88.1mm和Φ178.2mm,根據(jù)公式n=1000v/πd得:n1=130r/min n2=64.2 根據(jù)T68主軸轉速標準,選取主軸轉速分別為n1=125r/min n2=65r/min 5、工序9用量的計算: 本工序為精鏜Φ90mm孔和Φ180mm孔。該工序分為兩個工步,工步1是精鏜Φ90mm孔。工步2
28、是把工作臺旋轉90°精鏜Φ180mm孔。 背吃刀量的確定 :鏜Φ90mm的加工余量為0.6mm,粗鏜Φ180的加工余量為0.6mm。每一個工步中的背吃刀量為:ɑ1=0.3mm,ɑ=0.3mm 進給量的確定:由表4,按加工方法和刀具材料、刀具類型以及被加工零件材料選取該工序的進給量f=0.4mm/r 鏜削削速度的計算:按加工方法和刀具材料、刀具類型以及被加工零件材料選取鏜速度:v=1.2m/s=72m/min 精鏜后孔的直徑分別為Φ90mm和Φ180mm,根據(jù)公式n=1000v/πd得: n1=1000x72/(3.14x90)=255r/min n2=1000x72/(3
29、.14x180)=127r/min 根據(jù)T68主軸轉速標準,選取主軸轉速為r/min r/min 6、工序11切削用量的計算: 本工序要求之一為鉆8xM8、4×M16螺紋孔,攻螺紋 確定進給量f :由于孔徑和深度都不大,宜采用手動進給。 確定切削速度V :取鉆底孔Φ8的切削速度為,由此算出轉速:n=1000v/πd=1000x21/(3.15x6.8)=980r/min. 按機床實際轉速取n=1000r/min。 取攻絲時的切削速度為:v=0.04m/s=2.52m/min.由此算出轉速: n=1000v/πd=1000x2.52/(3.14x8
30、)=100r/min 按機床實際轉速取n=125r/min 4.5 .2時間定額的計算 1、工序3時間定額計算: 本工序為粗銑蝸輪箱體底面和頂面。由表5-43[1],采用面銑刀對稱銑削時,該工序的基本時間計算公式為:tj=(l+l1+l2)/fmz [fmz=fxn=fzxZxn] 當主偏角kr=90度時 當主偏角kr<90度時 本工序中:1=215x4=860mm(該工序包含2個工步) d=160mm ɑg=140mm fz=0.2mm/r n=80r/min Z=16 l2=2mm。 將上述結果帶入式中,則該工序的 基本時間: tj=(l+l
31、1+l2)/fmz =3.53min 輔助時間:tf=(0.15~0.2)tj=0.17x3.53=0.56min 服務時間:tw=0.05(tf+tj)=0.21min 單件時間:tdj=tf+tw+tj=3.53+0.21+0.56=4.3min 2、工序4時間定額計算: 本工序為粗銑Φ90mm兩孔側面凸臺。本工序中:(該工序包含2個工步d=160mmɑg=120mm fz=0.2mm/r n=80r/min Z=16 l2=2mm。 將上述結果帶入式中,則該工序的 基本時間:tj=(l+l1+l2)/fmz =1.11min 輔助時間:tf=(0.15~0.2)tj=
32、0.16x1.11=0.18min 服務時間:tw=0.05(tf+tj)=0.065min 單件時間:tdj=tf+tw+tj=1.11+0.065+0.18=1.35min 粗銑Φ180mm兩孔側面凸臺時間定額計算: 由表5-43[1],采用不對稱銑削。tj=(l+l1+l2)/fmz式中 C0=(0.03-0.05)dl2=3-5C0 本工序中:l=410mm(該工序包含2個工步)d=160mmfz=0.2mm/r n=80r/min Z=16C0=8mm l2=4mm。 將上述結果帶入式中,則該工序的 基本時間: tj=(l+l1+l2)/fmz=1.80min
33、 輔助時間:t f=(0.15~0.2)t j=0.16x1.80=0.29min 服務時間:t w=0.05(t f+t j)=0.10min 單件時間:t dj=tf+tw+tj=1.80+0.1+0.29=2.19min 精銑Φ90mm兩孔側面凸臺工序時間定額計算:采用對稱銑削。 本工序中:l=240mm(該工序包含2個工步) d=160mm ɑg=120mm fz=0.06mm/r n=125r/min Z=16 。 將上述結果帶入式中,則該工序的 基本時間: tj=(l+l1+l2)/fmz=2.25min 輔助時間:tf=(0.15~0.2)tj=0.16x2.
34、25=0.36min 服務時間:tw=0.05(tf+tj)=0.13min 單件時間:tdj=tf+tw+tj=0.13+0.36+2.25=2.74min 3、工序7時間定額計算: 本工序為粗鏜Φ90mm孔和Φ180mm孔。由表5-39[1]鏜孔基本時間的計算: tj=Lxi/fn=(l+l1+l2)i/fn式中、l3——單件大批生產(chǎn)時的試切附加長度備注:①加工到臺階時②的值見表5-40 ③主偏角kr=90度時④為進給次數(shù) (1)粗鏜Φ90mm孔時,l=70mm l1=7mm l2 =4mm f=0.7mm/r n=125r/min i=1。 把以上數(shù)據(jù)代入公式可得粗鏜
35、Φ90mm孔時基本時間: tj1=Lxi/fn=(l+l1+l2)i/fn=0.92min (2)粗鏜Φ180mm孔時,l=20mm l1=7mm l2 =4mm f=0.7mm/r n=65r/min i=1。 把以上數(shù)據(jù)代入公式可得粗鏜Φ90mm孔時基本時間:tj2=Lxi/fn=(l+l1+l2)i/fn=0.68min 基本時間:tj=ti1+tj2=1.6min 輔助時間:tf=(0.15~0.2)tj=0.17x1.6=0.27min 服務時間:tw=0.05(tf+tj)=0.1min 單件時間:tdj=tf+tw+tj=3.53+0.21+0.56=1.96m
36、in 4、工序9時間定額計算: 本工序為精鏜Φ90mm孔和Φ180mm孔。 ①精鏜Φ90mm孔時,l=70mm l1=7mm l2 =4mm f=0.4mm/r n=250r/min i=1。把以上數(shù)據(jù)代入公式可得粗鏜Φ90mm孔時基本時間: tj1=Lxi/fn=(l+l1+l2)i/fn=0.81min ②精鏜Φ180mm孔時,l=70mm l1=7mm l2 =4mm f=0.7mm/r n=125r/min i=1。 把以上數(shù)據(jù)代入公式可得粗鏜Φ90mm孔時基本時間:tj2=Lxi/fn=(l+l1+l2)i/fn=0.62min 基本時間:tj=ti1+tj
37、2=1.43min 輔助時間:tf=(0.15~0.2)t j=0.17x1.43=0.24min 服務時間:tw=0.05(tf+tj)=0.08min 單件時間:tdj=tf+tw+tj=1.43+0.08+0.24=1.8min 5、工序11時間定額計算: 本工序要求之一為鉆16xM8螺紋孔,攻螺紋16xM8,刀具選用錐柄階梯麻花鉆,直徑d=6mm,以及機用絲錐。鉆床選用Z3032立式鉆床,使用切削液。由表5-41[1],鉆孔時基本時間:tj=Lxi/fn=(l+l1+l2)i/fn式中 注:鉆中心孔和盲孔時;為孔徑()由表5-46[1],用絲錐攻螺紋時的基本時間:式中
38、注:為絲錐或工件回程的每分鐘轉數(shù)();為使用絲錐的數(shù)量;為工件或絲錐的每分鐘轉數(shù)();為工件螺紋螺距。 ①鉆孔時: (由表4-7[1]選取)。 所以鉆16xM8螺紋孔基本時間: tj1=Lxi/fn=(l+l1+l2)i/fn=1.44min ②攻螺紋時: (由表4-7[1]選取)。所以攻16xM8螺紋孔基本時間: tj2=Lxi/fn=(l+l1+l2)i/fn=0.81min=14.4min 基本時間:tj=ti1+tj2=1.43min=15.84min 輔助時間:tf=(0.15~0.2)tj=0.17x15.84=2.7min 服務時間:tw=0.05(
39、tf+tj)=0.93min 單件時間:tdj=tf+tw+tj=15.84+2.7+0.93=19.5min 5 、機床專用夾具設計 5.1夾具裝夾優(yōu)點? ? 對工件進行機械加工時,為了保證加工要求,首先要使工件相對于機床有正確的位置,并使這個位置在加工過程中不因外力的影響而變動。為此,在進行機械加工前,先要將工件裝夾好。用夾具裝夾工件有下列優(yōu)點: 1)?能穩(wěn)定的保證工件的加工精度??用夾具裝夾工件時,工件相對于道具及機床的位置精度由夾具保證,不受工人技術水平的影響,使一批工件的加工極度趨于一致。? 2)?能提
40、高勞動生產(chǎn)率?使用夾具裝夾工件方便、快捷,工件不需要劃線找正,可顯著的減少輔助工時,提高勞動生產(chǎn)率;工件在夾具中裝夾后提高了工件的剛性,因此可加大切屑用量,提高勞動生產(chǎn)率;可使用多件、多工位裝夾工件的夾具,并可采用高效夾緊機構,進一步提高勞動生產(chǎn)率。? 3)?能擴大機床的使用范圍?? 4)?能降低成本?在批量生產(chǎn)中使用夾具后,由于勞動生產(chǎn)率的提高、使用技術等級較低的工人以及廢品率下降等原因,明顯得降低了生產(chǎn)成本。夾具制造成本分攤在一批工件上。每個工件增加的成本時極少的,遠遠小于由于提高勞動生產(chǎn)率而降低的成本。 工件批量愈大,使用夾具所取得的經(jīng)濟效益就愈顯著
41、。? 夾具上的各種裝置和元件通過夾具體連接成一個整體。 因此,夾具體的形狀及尺寸取決于夾具上各種裝置的布置及夾具于機床的連接。對于夾具體有以下幾點要求:? 1)?有適當?shù)木群统叽绶€(wěn)定性???夾具體上的重要表面,應有適當?shù)某叽绾托螤罹龋鼈冎g應有適當?shù)奈恢镁取? 2)?有足夠的強度和剛度???加工過程中,夾具體要承受較大的切屑力和夾緊力。為保證夾具體不產(chǎn)生不允許的變形和震動,夾具體應有足夠的強度和剛度。? 3)?結構工藝性好???夾具體應便于制造、裝配和檢驗。鑄造夾具體上安裝各種元件的表面應鑄出凸臺,以減少加工面積。夾具體結構形式應便于工件
42、的裝卸。? 4)?排屑方便???切屑多時,夾具體上應考慮排屑結構。? 5)?在機床上安裝穩(wěn)定可靠???夾具在機床上的安裝都是通過夾具體上的安裝基面與機床上相應表面的接觸或配合實現(xiàn)的。當夾具在機床工作臺上安裝時,夾具的重心應盡量低,重心越高則支撐面應越大;夾具底面四邊應凸臺,使夾具體的安裝基面與機床的工作臺面接觸良好。 5.2裝夾方案 對于箱體類零件而言,一般常采用三平面的定位方式:本次夾具設計為精加工Ф180軸承孔的裝夾方案如下圖所示,該夾具體在加工過程中,夾具體要承受較大的切屑力和夾緊力。 該夾具體有足夠的強度和剛度,不產(chǎn)生不允許的變形和震動。該夾
43、具體結構為鑄造件,結構簡單,安裝各種元件的表面都鑄出凸臺,減少了加工面積。夾具體便于制造、裝配和檢驗,夾具體結構形式便于工件的裝卸,工藝性較好。此外在設計的過程中,考慮到切屑較多,設有容屑槽。夾具在機床上的安裝都是通過夾具體上的安裝基面與機床上相應表面的接觸或配合實現(xiàn)的。該夾具在機床工作臺上安裝時,夾具的重心應較低,夾具底面四邊設有凸臺,使夾具體的安裝基面與機床的工作臺面接觸良好。 本次課設的題目是小型蝸輪減速器箱體,且為大批量生產(chǎn),綜合考慮經(jīng)濟以及加工效率,故采用專用夾具裝夾,采用短圓柱大平面定位銷應用于左側直徑為90mm的軸承
44、孔,另外利用直角三角形壓板以及簡單連桿機構夾緊箱體的側面以及上面進行定位,為鏜直徑為180mm的軸承孔提供更加直接方便的裝夾步驟,夾具示意圖如下: 圖2夾具體裝夾 6、設計總結? 機械制造工藝學是機械類專業(yè)的一門主要課程,對于我們機械設計制造及其自動化專業(yè)顯得更為重要。機械制造工藝學為我們以后進行實際的機械設計制造提供知識基礎,而機械制造工藝學課程設計能夠對所學理論知識的掌握程度及運用能力進行檢驗。正所謂“學以致用”“實踐是檢驗真理的唯一標準”,所以在老師精心指導下進行此次課程設計尤為必要。 這次機械制造工藝學課程設計的過程是艱辛而又充
45、滿樂趣的,在這短短三個星期里,我們學到了許多知識,同時獲得了一定的寶貴的實踐經(jīng)驗。通過這次課程設計,我們對課本知識更加融會貫通,對機械制造工藝學有了更深的認識,也通過查閱大量的書籍和手冊,對有關機械制造工藝學的標準和參數(shù)有了一定的了解。同時,在此次課程設計中,全體組員分工合作,齊心協(xié)力,保證了設計任務的順利完成。大家不僅在一定程度上拓展了知識和提高了實踐能力,而且都從中深深體會到了合作的力量,團隊的力量,這對我們這群即將走出校門踏進社會年輕人來說,無疑是一筆無比寶貴的財富。 不過,有些問題是
46、我們在以后的學習工作中必須注意的。首先,設計過程絕非只是計算過程,即使其必不可少,我們要充分考慮零部件的工作條件及加工工藝性,所設計出得零部件既要滿足工作強度,又要方便加工,即我們要注重結構設計。第二,我們不能死套教材,在設計過程中,我們要結合實際,因地制宜,設計出既滿足要求又經(jīng)濟實用的產(chǎn)品。我們要學習課本知識,借鑒前輩的設計經(jīng)驗,但我們也絕不能過于迷信課本,拘泥于以往經(jīng)驗,墨守陳規(guī),固步自封。我們在設計過程中要敢于創(chuàng)新。 7、參考文獻 1安二中,黃瑞玲.箱體類零件夾具發(fā)展趨勢[J].機械工程學報,1997 2郭華勝.箱體機械加工工藝的改進[J].機
47、械車輛工藝,2004 3謝成.箱體類零件加工及其夾具定位誤差的分析[J].機械,2008 4馬曉春.我國現(xiàn)代機械制造技術的發(fā)展趨勢[J].森林工程.2002, 5趙志修.機械制造工藝學[M].北京:機械工業(yè)出版社,1985 6趙志勇,王麗杰.機械加工工藝規(guī)程的發(fā)展[J].科技資訊.2009,(6)25-29. 7王世敬,溫筠.現(xiàn)代機械制造技術及其發(fā)展趨勢[J].石油械.2002, 8曾愛新.談機械加工工藝的發(fā)展趨勢[J].職園培地,2002, 9秦嵩,周偉.淺談提高機械加工工藝的方法[J].科學時代.2011 10王穎.機械加工工藝規(guī)程及工藝文件[J].科技資訊,2008,(3
48、0):44. 11朱耀祥,浦林祥.現(xiàn)代夾具設計手冊[M].北京:機械工業(yè)出版社,2010: 12賈建華,范建蓓.柔性夾具在現(xiàn)代制造業(yè)中的應用與展望[J].機電程.2005,(12):53-55. 13朱耀祥.柔性夾具與計算機輔助夾具設計技術[J].制造技術與機床.2000,(8):12-15. 14隋聚艷.夾具的發(fā)展及其趨勢分析[J].現(xiàn)代商貿工業(yè).2009,(4):20-22. 15張亞明.機床夾具分類與構成[J].科技資訊.2008,46(5):2-5. 16蔡瑾,段國林,姚濤,等.計算機輔助夾具設計技術回顧與發(fā)展趨勢綜述[J].機械設計,2010,(2):1-4 17王先奎,艾興.機械加工工藝手冊(第1卷)[M].北京:機械工業(yè)出版社,2000:5-71. 18王力.機械制造工藝學[M].北京:中國人民大學出版社,2001.
- 溫馨提示:
1: 本站所有資源如無特殊說明,都需要本地電腦安裝OFFICE2007和PDF閱讀器。圖紙軟件為CAD,CAXA,PROE,UG,SolidWorks等.壓縮文件請下載最新的WinRAR軟件解壓。
2: 本站的文檔不包含任何第三方提供的附件圖紙等,如果需要附件,請聯(lián)系上傳者。文件的所有權益歸上傳用戶所有。
3.本站RAR壓縮包中若帶圖紙,網(wǎng)頁內容里面會有圖紙預覽,若沒有圖紙預覽就沒有圖紙。
4. 未經(jīng)權益所有人同意不得將文件中的內容挪作商業(yè)或盈利用途。
5. 裝配圖網(wǎng)僅提供信息存儲空間,僅對用戶上傳內容的表現(xiàn)方式做保護處理,對用戶上傳分享的文檔內容本身不做任何修改或編輯,并不能對任何下載內容負責。
6. 下載文件中如有侵權或不適當內容,請與我們聯(lián)系,我們立即糾正。
7. 本站不保證下載資源的準確性、安全性和完整性, 同時也不承擔用戶因使用這些下載資源對自己和他人造成任何形式的傷害或損失。