五軸數(shù)控銑削畢業(yè)論文
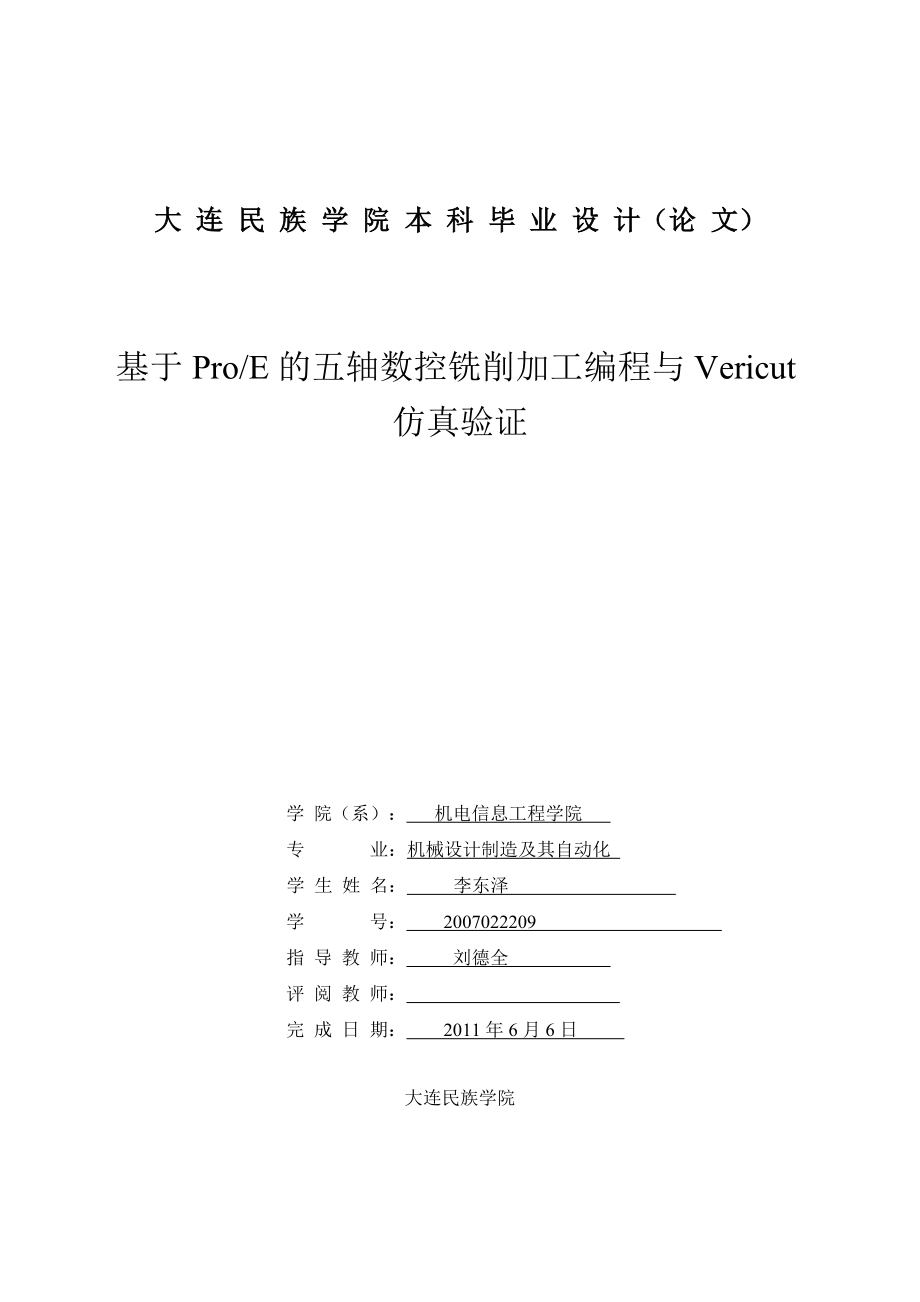


《五軸數(shù)控銑削畢業(yè)論文》由會員分享,可在線閱讀,更多相關《五軸數(shù)控銑削畢業(yè)論文(32頁珍藏版)》請在裝配圖網(wǎng)上搜索。
1、 大 連 民 族 學 院 本 科 畢 業(yè) 設 計(論 文) 基于Pro/E的五軸數(shù)控銑削加工編程與Vericut仿真驗證 學 院(系): 機電信息工程學院 專 業(yè):機械設計制造及其自動化 學 生 姓 名: 李東澤 學 號: 2007022209 指 導 教 師: 劉德全 評 閱 教 師: 完 成 日 期:
2、 2011年6月6日 大連民族學院 基于pro/e五軸數(shù)控銑削加工編程與Vericut仿真驗證 摘 要 五軸聯(lián)動數(shù)控加工技術以其特有的優(yōu)越性在復雜、高精度零件加工方面起著越來越重要的作用。五軸加工優(yōu)越性的充分發(fā)揮離不開高質(zhì)量的五軸加工編程和有針對性的后置處理程序。由于刀具與工件相對運動的復雜性,五軸加工編程的復雜程度遠遠超過三軸加工的編程。同時,五軸加工后置處理,由于開發(fā)難度大和技術保密等原因,也成為五軸加工設備充分發(fā)揮效率的制約因素。 針對上述兩個方面的問題,本文作了相應的研究。首先,五軸聯(lián)動加工中心進行了數(shù)控銑削后置處理開發(fā),通過基于Pro/e軟件
3、的輔助模塊進行了后置處理程序的開發(fā)。 本文的研究對于如何提高五軸加工編程質(zhì)量和解決后置處理問題,具有一定的實際意義。 關鍵詞:五軸加工編程;后置處理;坐標變換;仿真加工 - I - 基于pro/e五軸數(shù)控銑削加工編程與vericut仿真驗證 Abstract Five.axis NC machining technology with its special advantages becomes more and more important in the machining of complex and high precision Parts.Without the r
4、easonable programming of five.axis NC machining and the pertinent special post processing,the advantages can not be exerted completely.owing to the complexity of the motion between the tool and the workpiece,it is more difficult to get the programming of the five.axis NC machining than the three.axi
5、s.And the five.axis post processing is the main constraint in improving the effectivity of the machining tool just because of the difficult redevelopment,technique secrecy and so on. Based on resolving the two problems above,some relative research is done in this paper.There is one methods to reali
6、ze the post processing :It is the redevelopment of the general post.processing module based on the pro/e. The research of the paper have some important significance at resolving the problem of post.processing and improving the effectivity of NC machining programming Key words: five.axis NC machi
7、ning programming;post Processing;coordinate transformation;simulation for machining - 28 - 目 錄 摘 要....................................................................................................................................I Abstract...........................................
8、..........................................................................................II 1. 緒論......................................................................................................................................1 1.1 數(shù)控編程技術的發(fā)展歷程.................................................
9、.......................................1 1.2 數(shù)控編程技術的關鍵技術........................................................................................2 1.3 后置處理技術概述....................................................................................................2 1.3.1后置處理的主要任務. .....................
10、.............................. ............... .................3 1.3.2 后置處理技術發(fā)展..........................................................................................3 1.33 國內(nèi)后置處理技術研究現(xiàn)狀...........................................................................4 1.4 課題的研究內(nèi)容及意義.................
11、...........................................................................4 2. 五軸加工編程及后置處理算法..........................................................................................5 2.1 五軸數(shù)控加工工藝有關內(nèi)容...................................................................................5 2.1.1 刀具選擇.
12、......................................................................................................5 2.1.2 切削用量的選擇..........................................................................................6 2.1.3 五軸加工編程刀具軌跡生成....................................................................8
13、 2.1.4 刀位干涉處理.............................................................................................11 2.2 本章小結..................................................................................................................14 3五軸數(shù)控加工仿真幾何模型的建立...... .........................................
14、..................................15 3.1 三維實體表示方法概述..........................................................................................15 3.1.1 線框圖表示法...........................................................................................15 3.1.2 邊界表示法... ..........
15、.................................................................................16 4 凸管模型數(shù)控加工.............................................. ..............................................................17 4.1建立制造模型.......................................... ..................................
16、............................17 4.2 體積塊加工 .......................................... ..............................................................17 4.3 曲面銑削精加工 . ................................. ........................................................ .....21 4.4后置處理生成程序.............
17、..................... ........................................................ .....24 結 論. ...............................................................................................................................25 參考文獻.....................................................................
18、............................................................26 致 謝. ...............................................................................................................................27 1. 緒論 五軸數(shù)控技術是數(shù)控技術中難度最大、應用范圍最廣的技術[1]。在復雜曲面的高效、精密、自動化加工方面,五軸聯(lián)動加工更是具有三軸加工所不能比擬的的優(yōu)勢。主要體現(xiàn)在以下幾個方面:1)
19、五軸加工可有效地避免刀具千涉,加工三軸機床難以加工的復雜零件;2)對于直紋面的加工,五軸加工可以采用側(cè)銑的方式一刀成型,加工質(zhì)量和加工效率高;3)五軸加工可以實現(xiàn)一次裝夾、多面多工序加工,容易保證產(chǎn)品精度;4)五軸加工中刀具相對于工件具有良好的切削狀態(tài);5)對于加工空間受到限制的通道加工和組合曲面過渡區(qū)域加工,五軸加工可以選用較大尺寸刀具避開干涉進行加工,刀具剛性好[3]。 因此,五軸加工技術一直是數(shù)控加工領域內(nèi)國內(nèi)外學者的研究熱點之一[15]。并且,也一直受到西方國家對我國的技術封鎖。因為許多先進武器裝備的制造,如飛機、導彈、坦克等的關鍵零件,都離不開高性能數(shù)控機床的加工。五軸編程技術是五
20、軸加工技術的關鍵問題之一。在此對數(shù)控編程技術的各方面內(nèi)容做一簡單概述。 1.1數(shù)控編程技術的發(fā)展歷程 20世紀50年代,美國麻省理工學院 (MIT)設計了一種專門用于零件數(shù)控加工程序編制的語言APT(Automatically Programmed Tools)。其后MIT組織美國各大飛機公司共同開發(fā)了APTII。到了60年代,在APTII的基礎上研制的APTIII已經(jīng)到了應用階段。以后又幾經(jīng)修改和充實,發(fā)展成為APT.IV,APT.AC和APT一IV/SS。APT能處理二維、三維銑削加工,但較難掌握。為此,在APT的基礎上,世界各國發(fā)展了帶有一定特色和專用性更強的APT衍生語言[3]。
21、 1972年,美國洛克西德加里福尼亞飛機公司首先研究成功采用圖像儀輔助設計、繪圖和編制數(shù)控加工程序的一體化系統(tǒng)以DAM系統(tǒng)。1975年,法國達索飛機公司引進CADAM系統(tǒng),為己有的二維加工系統(tǒng)CALIBRB增加二維設計和繪圖功能,1978年進一步擴充,開發(fā)了CATIA系統(tǒng)。隨著計算機處理速度的發(fā)展和圖形設備及,數(shù)控編程系統(tǒng)進入了CAD/CAM一體化時代[3]。 目前應用較為廣泛的數(shù)控編程系統(tǒng)有APT一IV/SS、CADAM、CATIA、EUKLID、UGNX、INTERGRAPH、Pro/Engineer、MasterCAM、Cimatron E、Edge CAM等。我國西北學、華中科技大學
22、等開發(fā)的圖形編程系統(tǒng)如NPU/GNCP和InteCAM也具有兩軸加工和雕塑曲面多軸加工等功能,達到了實用化程度。 1.2數(shù)控編程技術的關鍵技術 1.零件幾何建模 要完成復雜零件的數(shù)控加工編程,必須要用自動編程軟件來實現(xiàn)。其首節(jié)是建立被加工零件幾何模型[3]。復雜形狀零件幾何建模的主要技術內(nèi)容包線曲面創(chuàng)建及編輯技術、實體建模技術和特征建模技術等。 2.加工方案及工藝參數(shù)的合理選擇 加工方案的確定及工藝參數(shù)的選擇,直接決定著數(shù)控加工的效率和質(zhì)量中刀具、刀軸控制方式、走刀路線和進給速度的自動優(yōu)化選擇與自適應控制年來所研究的重點問題[3]。 3.刀具軌跡生成 刀具軌跡生成是復雜形狀零件數(shù)
23、控加工中最重要同時也是研究最為廣泛的內(nèi)容,能否生成有效的刀具軌跡直接決定了加工的可能性、質(zhì)量和效率。軌跡生成的首要目標是使所生成的刀具軌跡能滿足:無干涉、無碰撞、軌跡切削負荷光滑并滿足要求、代碼質(zhì)量高、代碼量小等條件[3]。 4.數(shù)控加工仿真 零件實際加工之前,對所編制的數(shù)控加工程序進行加工仿真驗證是十分的,特別是在多軸加工編程中,其作用更為突出。由于多軸加工中刀具相對件運動的復雜性,所生成的加工程序在加工過程中有可能會出現(xiàn)過切與欠切涉與碰撞等問題。數(shù)控加工仿真通過軟件模擬加工環(huán)境、刀具路徑與材料切程來檢驗并優(yōu)化加工程序[3],可以有效地避免上述問題,提高編程效率與質(zhì)量。 5.后置處理
24、 后置處理是數(shù)控編程技術的一個重要內(nèi)容,它將CAM系統(tǒng)生成的不包含具體機床和數(shù)控系統(tǒng)信息的刀位數(shù)據(jù)轉(zhuǎn)換成能夠控制特定機床運動的數(shù)控加工程序。有效的后置處理對于保證加工質(zhì)量、效率與機床可靠運行具有重要作用[3]。 1.3后置處理技術概述 數(shù)控機床的各種運動都是執(zhí)行特定的數(shù)控指令的結果,完成一個零件的數(shù)控加工一般需要執(zhí)行一連串的數(shù)控指令,即數(shù)控程序。在以M系統(tǒng)中,考慮到具體機床的結構和系統(tǒng)不同以及以M編程的獨立性,其自動生成的是相對于工件坐標系的刀位文件,這個過程稱為前置處理。前置處理產(chǎn)生的刀位文件不能用于驅(qū)動數(shù)控機床的運動。因此,這時需要設法把刀位文件轉(zhuǎn)換成特定數(shù)控機床能夠識別并且能夠執(zhí)行的
25、數(shù)控程序,這個過程稱為后置處理[2]。 1.3.1后置處理的主要任務 后置處理的主要任務包括以下幾個方面[3]: 1.機床運動變換 五軸數(shù)控編程生成的刀位文件中的刀位數(shù)據(jù),是刀具相對于工件坐標系的刀心位置和刀軸矢量數(shù)據(jù)。機床運動變換的作用就是根據(jù)具體的機床運動結構將刀位文件中的刀位數(shù)據(jù)轉(zhuǎn)換成為機床各運動軸的運動數(shù)據(jù)。 2.非線性運動誤差校驗 CAM系統(tǒng)進行刀位數(shù)據(jù)的計算時,是使用離散直線來逼近工件輪廓。加工過程中,只有當?shù)段稽c實際運動為直線時,才能與編程精度相符合。多坐標加工時,由于旋轉(zhuǎn)運動的非線性,由機床各運動軸線性合成的實際刀位運動會嚴重偏離編程直線。因此,應對該誤差進
26、行檢驗,若超過允許誤差時應作必要修正。 3.進給速度校驗 進給速度是指刀具接觸點或刀位點與工件表面的相對速度。在多軸加工中,由于回轉(zhuǎn)半徑的放大作用,其合成速度轉(zhuǎn)換到機床坐標時,會使平動軸的速度變換很大,超出機床伺服能力或機床、刀具的負荷能力。因此,應根據(jù)機床伺服能力(速度、加速度)及切削負荷能力進行校驗修正。 4.數(shù)控加工程序生成 數(shù)控加工程序生成是指根據(jù)數(shù)控系統(tǒng)規(guī)定的指令格式將機床運動數(shù)據(jù)轉(zhuǎn)機床程序代碼。后置處理在完成這個過程時,原則上是逐行解釋執(zhí)行,根據(jù)文件記錄行的類型,來確定是進行針對特定機床的坐標變換還是進行代碼轉(zhuǎn)直到刀位源文件結束。 1.3.2后置處理技術發(fā)展 自20世紀
27、50年代由美國麻省理工學院設計APT語言以來,后置處理就成為編程的重要組成部分。在APT中,對于不同的數(shù)控系統(tǒng),編寫不同的后置處理由于數(shù)控系統(tǒng)種類繁多,機床配置不盡相同,APT的專用后置處理程序達上千多。 1980年IBM公司為解決APT刀位源文件的處理推出了DAPP(Design Aid Post Processor)系統(tǒng),系統(tǒng)包括輸入模塊、輸出模塊、數(shù)據(jù)處理模塊等,可以利用它生成所需后置處理。該系統(tǒng)的推出使后置處理系統(tǒng)向通用化發(fā)展了一步[10]。 隨著CAD/CAM一體化技術的出現(xiàn)及迅速發(fā)展。各種CAD/CAM系統(tǒng)的CAM部分配置了通用后置處理(PostPr。cessing)模塊。例如
28、UG軟件系統(tǒng)采用的UG/Pro/Engineer系統(tǒng)采用的Pro/NC一POST、CATIA軟件系統(tǒng)采用的ImsPost,CimaE系統(tǒng)采用的GPPZ等。 1.3.3國內(nèi)后置處理技術研究現(xiàn)狀 近年來,國內(nèi)對后置處理理論與技術也進行了深入研究,取得了一定的成果。在通用后置處理技術方面,張利波,周濟[10]提出了一種基于配置文件的式數(shù)控編程通用后置處理模型;程筱勝,劉壯[10]對南京航空航天大學的超人CAD/CAM系統(tǒng)的通用后置處理系統(tǒng)進行了研究,開發(fā)了具有交互式圖形系統(tǒng)用面的通用后置處理程序;CAXA制造工程師是目前國內(nèi)應用最廣泛的國產(chǎn)CAD/CAM系統(tǒng),其后置處理功能模塊解決了常見數(shù)控
29、機床的后置處理[10]。 在后置處理的有關技術方面,劉雄偉[13]探索了典型配置多坐標數(shù)控機床后置處理的算法;陳濤,彭芳瑜,周云飛[13]提出了適用于任意結構形式的多坐標數(shù)控機床運動模型的建立與反求方法,在此基礎上建立了對機床幾何誤差進行補償?shù)暮笾米儞Q。韓向利,袁哲俊[11]對五坐標數(shù)控機床的后置處理算法原理和后置處理配置文件參數(shù)進行了探索和設計;劉日良、張承瑞[10]等研究解決了45B軸特殊雙轉(zhuǎn)臺五坐標數(shù)控機床后置處理算法。馮顯英、丁勇、耿小強[10]等也針對特殊雙轉(zhuǎn)臺結構的機床進行了后置處理算法研究。周艷紅、周濟[12]提出了通過后置處理實現(xiàn)數(shù)控機床幾何誤差軟件補償?shù)脑砗退惴ā? 在針
30、對國外CAD/CAM系統(tǒng)的應用研究方面,明興祖[9]介紹了后置處理系統(tǒng)的組成、數(shù)控自動編程系統(tǒng)瓶Mastercam后置處理程序的結構及其慣用文件的設定內(nèi)容,并探索了開發(fā)途徑,通過操作修改后的后置處理程序,使它能適合其它數(shù)控系統(tǒng)的NC程序生成;呂鳳民[14]研究了基于UG/open GRIP下的DMU60M特殊雙轉(zhuǎn)臺數(shù)控機床后置處理程序的開發(fā)。李吉平、劉華明在分析五軸數(shù)控加工中心基本結構的基礎上,給出了涉及多軸數(shù)控加工后置處理角度分配和坐標變換的數(shù)學模型,以此數(shù)學模型為核心,基于Pro/Engineer軟件開發(fā)了后置處理器。陳輝、王知行[10]基于UG/Post后置處理器,開發(fā)了并聯(lián)機床的后置處
31、理。 1.4課題的研究內(nèi)容及意義 加工編程和后置處理是數(shù)控加工技術的重要內(nèi)容,決定著數(shù)控加工質(zhì)量和效率的發(fā)揮。特別是在五軸加工領域,由于刀具與工件相對運動以及機床結構的復雜性,使得編程與后置的實現(xiàn)技術難度更大。針對上述兩個方面的問題,本文進行了相應的研究:針對DMG DMU760M型特殊雙轉(zhuǎn)臺五軸聯(lián)動加工中心進行了基于Edge CAM軟件環(huán)境下的后置處理開發(fā),并利用所開發(fā)的后置處理程序進行了數(shù)控機床加工仿真,驗證了五軸編程和后置處理的正確性。本文的研究對于如何提高五軸加工編程質(zhì)量和解決后置處理問題,具有一定的實際意義。 2. 五軸加工編程及后置處理算法 2.1五軸數(shù)控加工工藝有關內(nèi)
32、容 編制高質(zhì)量的五軸加工程序,加工工藝的合理確定具有極為重要的作用。五軸加工工藝的內(nèi)容包括機床選擇、刀具選擇、走刀路線規(guī)劃、主軸轉(zhuǎn)速、切削速度和進給速度等[3]。有關五軸數(shù)控機床的內(nèi)容,已在前面有所闡述,在此不再贅述。現(xiàn)對五軸加工工藝的其它內(nèi)容作簡單介紹。 2.1.1刀具選擇 數(shù)控銑削加工中常用的刀具主要有平底立銑刀、端銑刀、球頭刀、環(huán)形刀、鼓形刀和錐形刀等,根據(jù)具體的加工特征選擇合理的刀具,是非常重要的。對于各種刀具的使用特點簡介如下[3]: 1.平底立銑刀 平底立銑刀[圖2.1(a)所示]在多坐標加工中的應用有側(cè)銑和端銑兩種方式。側(cè)銑方式主要應用于直紋面的加工,可用其周邊切削刃一
33、次成形,加工效率和加工質(zhì)量高。端銑方式在保證刀具不與型面干涉的前提下,盡可能使平底立銑刀底部貼近被加工表面進行加工,從而改善切削條件,并有效抑止行間殘余高度。 2.端銑刀 端銑刀[圖2.l(b)所示]主要用于面積較大的平面銑削和較平坦的立體輪廓(如大型葉片、螺旋槳、模具等)的多坐標銑削,以減少走刀次數(shù),提高加工效率與表面質(zhì)量。 3.球頭刀 球頭刀[圖2.1(c)所示]加工的刀具中心軌跡是由零件輪廓沿其外法線方向偏置一個刀具半徑而成。球頭刀球頭切削刃上各點的切削情況不一,越接近球頭刀的底部其切削條件越差(切削速度低、容屑空間小等)。但是,球頭刀對于加工對象的適應能力很強,且編程與使用也較
34、方便,是多軸加工的常用刀具。 4.環(huán)形刀 環(huán)形刀[圖2.1(d)所示]主要用于凹槽、平底型腔等平面銑削和立體輪廓的加工,其工藝特點與平底立銑刀類似,切削性能好。 5.鼓形刀 鼓形刀[圖2.1(e)所示]多用來對飛機結構件等零件中與安裝面傾斜的表面進行三坐標加工。鼓形刀也應用于一般表面的多坐標側(cè)銑,而且它比圓柱面或圓錐面?zhèn)茹姷倪m應能力強。鼓形刀不適于加工內(nèi)緣表面。 6.錐形刀 錐形刀[圖2.1(f)所示]的應用目的與鼓形刀有些相似,在三坐標機床上,它可替代多坐標側(cè)銑加工零件上與安裝面傾斜的表面。對于底部狹窄的通道等情況的加工,采用錐形刀可在滿足結構空間限制的情況下增加刀具的剛度,從而
35、提高加工效率與精度。 圖2.1數(shù)控銑削常用刀具 2.1.2切削用量的選擇 1.切削深度 在機床動力足夠、工藝系統(tǒng)剛度允許的情況下,盡量提高,這是提高生產(chǎn)率的一個有效措施。切削深度的提高會降低刀具使用壽命,但是影響不大。 2.切削寬度 一般與刀具直徑d成正比,與切削深度成反比。經(jīng)濟型數(shù)控加工中,一般的取值范圍為。切削寬度對刀具壽命的影響同切削深度。 3.切削速度 提高也是提高生產(chǎn)率的一個措施,但與刀具耐用度的關系比較密切。隨著的增大,刀具耐用度急劇下降,故的選擇主要取決于刀具耐用度。另外,切削速度與加工材料也有很大關系,例如用立銑刀銑削模具鋼時,可采用120
36、m/min左右;而用同樣的立銑刀銑削鋁合金時,可選80m/min以上。 4.主軸轉(zhuǎn)速n(r/min) 主軸轉(zhuǎn)速一般根據(jù)切削速度來選定。計算公式為: (2.1) 式中:d一一刀具或工件直徑(mm) 數(shù)控機床的控制面板上一般備有主軸轉(zhuǎn)速修調(diào)(倍率)開關,可在加工過程中對主軸轉(zhuǎn)速進行整倍數(shù)調(diào)整。 5.進給速度 進給速度應根據(jù)零件的加工精度和表面粗糙度要求以及刀具和工件材料來選擇。的增加也可以提高生產(chǎn)效率。進給速度與每齒進給量有關。粗加工時,每齒進給量的選取主要決定于工件材料的力學性能、刀具材料和銑刀類型
37、。工件材料強度和硬度越高,選取的越小,反之則越大:硬質(zhì)合金銑刀的每齒進給量應大于高速鋼銑刀。而精加工時,每齒進給量的選取要考慮工件表面粗糙度的要求,表面粗糙度要求越高,越小進給速度每齒進給量與轉(zhuǎn)速n之間的關系是: =/Zn (2.2) 在加工過程中,也可通過機床控制面板上的修調(diào)開關進行人工調(diào)整,但是最大進給速度要受到設備剛度和進給系統(tǒng)性能等的限制。 進給速度的選擇,還需要注意零件加工的特殊情況。例如,當加工圓弧時,切削點的實際進給速度并不等于編程數(shù)值。加工外圓弧時,切削點的實際進
38、給速度小于編程值。而加工內(nèi)圓弧時切削點的實際進給速度大于編程值。若刀具半徑與圓弧路徑的半徑接近時,實際進給速度將變得很大,有可能損傷刀具和工件。 6.體積切除率 (2.3) 式中,一工作臺進給量,mm/min; n一機床主軸轉(zhuǎn)速,r/min; z一齒數(shù); 一每齒進給量,mm/r Dc一刀具直徑,mm 合理選擇切削用量的原則是,粗加工時,一般以提高生產(chǎn)率為主,但也應考慮經(jīng)濟性和加工成本;精加工時,首先應保證加工質(zhì)量,兼顧切削效率、經(jīng)濟性。具體數(shù)值應根據(jù)機床說明書、切削用量手冊,并結合經(jīng)驗
39、而定。 粗加工為體積加工,從高的生產(chǎn)率考慮,應在保證刀具耐用度的前提下,使材料的去除率最大,而材料的去除率又與吃刀量(切削深度、切削寬度)、進給速度切削速度等有關。切削用量各要素中,任一要素的增加都會使刀具的耐用度下降,但影響程度不同,影響最大的是切削速度,切削速度稍一提高,刀具壽命就會有明顯的降低,其次是進給速度,最小的是吃刀量。為使所選的切削用量使生產(chǎn)率高且對刀具耐用度下降影響最小,一般首先選擇盡可能大的吃刀量,其次是確定進給速度,最后根據(jù)刀具耐用度確定切削速度 精加工主要保證精度,進給速度受表面粗糙度限制,根據(jù)刀具耐用度確定切削速度。 2.1.3五軸加工編程刀具軌跡生成 1.刀具
40、軌跡生成方法 五軸數(shù)控加工刀具軌跡生成是數(shù)控編程的基礎和關鍵,主要方法如下: l)參數(shù)線法 曲面參數(shù)線加工方法[如圖2.2所示]是多坐標數(shù)控加工中生成刀具軌跡的主要方法,特點是切削行沿曲面的參數(shù)線分布,即切削行沿u線或v線分布,適用于網(wǎng)格比較規(guī)整的參數(shù)曲面的加工。該算法的優(yōu)點是計算方法簡單,速度快;不足之處是當加工曲面的參數(shù)線分布不均勻時,切削行刀具軌跡的分布也不均勻。 圖2.2 參數(shù)線加工刀具軌跡分布 2)截平面法 截平面法加工方法[如圖2.3所示〕是采用一組截平面去截取加工表面,截出一系列交線,刀具與加工表面的接觸點就沿
41、著這些交線運動,完成曲面的加工。截平面法使刀具與曲面的切觸點軌跡在同一平面上。該方法對于曲面網(wǎng)格分布不太均勻及由多個曲面形成的組合曲面的加工非常有效,可以使加工軌跡分布相對比較均勻,可使殘留高度分布比較均勻,加工效率也較高。 圖2.3 截平面法加工的刀具跡 a)繞z軸旋轉(zhuǎn)的截平面 b)平行于x軸的截平面 c)任意角度截平面 3)回轉(zhuǎn)截面法 回轉(zhuǎn)截面法加工方法[如圖2.4所示]是采用一組回轉(zhuǎn)圓柱面去截取加工表面,截出一系列交線,刀具與加工表面的接觸點就沿著這些交線運動完成曲面加工。一般情況下,回轉(zhuǎn)圓柱面的
42、軸心線平行于Z坐標值。 圖2.4回轉(zhuǎn)截面法加工的刀具軌跡 4)投影法 投影法加工方法[如圖2.5所示]是使刀具沿一組事先定義好的導動曲線(或軌跡)運動,同時跟蹤待加工表面的形狀。導動曲線在待加工表面上的投影一般為觸點軌跡,也可以是刀尖點軌跡。切觸點軌跡適合于曲面特征的加工,而對于有干涉面的場合,限制刀心點更為有效。由于待加工表面上每一點的法矢方向均不相同,因此限制切觸點軌跡不能保證刀尖點軌跡落在投影方向上,所以限制刀尖點容易控制刀具的準確位置,可以保證在一些臨界位置和其他曲面(如干涉面)不
43、發(fā)生干涉。 圖2.5投影法加工的刀具軌跡 2.刀軸控制方式[3] 多坐標數(shù)控加工不同于三坐標數(shù)控加工,在加工過程中其刀具軸線(刀軸矢量)是不斷變化的。并且,根據(jù)機床配置型式的不同,其刀具軸線的變化方式也不同。但是,在刀位文件的刀位數(shù)據(jù)計算過程中并不考慮具體機床的結構,而是相對于統(tǒng)一的工件坐標系進行計算。多坐標數(shù)控加工的刀位數(shù)據(jù)由工件坐標系中的刀位點位置數(shù)量和刀軸矢量組成。刀軸矢量控制方式可在局部坐標系內(nèi)進行描述。[如圖2.6所示],為基于前傾角a和傾斜角r的一般刀軸控制方式。
44、 圖2.6傾斜軸刀軸控制方式 圖中,(a,v,n)為曲面在切削點的局部坐標系。a為曲面上切削點處沿進方向的單位切失,n為曲面上切削點處單位法失,v=。前傾角a為刀軸矢量垂直于進給方向的平面所成角度,可在端銑加工凹面時防止干涉。傾斜角r為刀與曲面法矢的夾角,不屬某個截面,位于以法矢為軸線,r為頂角的圓錐上,但可由r角及指定沿走刀方向的左右側(cè)來確定刀軸的空間方向。 根據(jù)前傾角a和傾斜角r的不同,可得到兩種特殊情況下的刀軸控制方式: l)垂直于表面端銑(a=r=0) 垂直于表面端銑方式是使刀具軸線始終平行于各切削點處的表面法矢,由刀具底面緊貼加
45、工表面來對切削行間殘余高度作最大限度的抑止,以減少走刀次數(shù)和獲得高的生產(chǎn)效率。該方式一般用于大型平坦的無干涉凸曲面端銑加工[16]。 2)平行于表面?zhèn)茹?r=90) 平行于表面?zhèn)茹姺绞绞侵傅毒咻S線或母線始終處于各切削點的切平面內(nèi)。這種方式的重要應用是直紋面的加工,由圓柱或圓錐形刀具側(cè)刃與直紋面母線接觸,可以一刀加工成型,效率高而且表面質(zhì)量好[16]。 2.1.4刀位干涉處理 1.干涉的產(chǎn)生[3] 五坐標加工中刀具干涉可分為端銑干涉和側(cè)銑干涉。按照與零件發(fā)生干涉的刀具部位的不同,存在刀具頭部干涉和刀桿干涉兩種情況。 l)端銑加工時的刀具干涉 端銑加工時,刀具頭部干涉[如圖2.7所
46、示]是主要的干涉方式,在曲面的內(nèi)凹區(qū)域和組合曲面的過渡區(qū)域附近加工時都可能出現(xiàn)。在加工一些異型結構零件和加工通道類、復雜型腔類等具有約束面的零件時則容易出現(xiàn)刀桿干涉[如圖2-8所示]。 圖2.7 端銑刀具頭部干涉 圖2.8端銑刀桿干涉 2)側(cè)銑加工時的刀具干涉 側(cè)銑加工時刀桿干涉[如圖2.9所示]是主要形式。以直紋面加工為例,當被加工表面不可展時,刀桿干涉是不可避免的。因此,這種情況下側(cè)銑本
47、身就是一種近似方法,其問題的關鍵在于如何處理刀具干涉以滿足加工精度要求。 圖2.9側(cè)銑刀桿干涉 圖2.10側(cè)銑刀頭干涉 2.干涉的避免方法[3] l)端銑加工刀具干涉的避免 在五坐標端銑加工出現(xiàn)干涉時,調(diào)整刀位數(shù)據(jù)(即刀具位置與方向)以避免干涉的方法有:軸向移動法[如圖2.11(a)所示]和軸線擺動法[如圖2.11(b)所示]。
48、 圖2.11端銑干涉刀頭避免 a)軸向移動法 b)軸線擺動法 軸向移動法是使刀具沿著刀軸方向移動到一新的位置,以使刀具與加工表面(離散多面體)相切觸且不再存在干涉。該方法的主要優(yōu)點是算法較簡單,但是該方法未能發(fā)揮五坐標加工可調(diào)整刀軸方向的優(yōu)勢,在避免過切的同時又將導致一定程度的欠切,因此一般只在用軸線擺動法難以避免干涉的情況下使用。此外,對于球頭刀加工,其刀頭部位干涉則只可能用軸向移動法來避免。軸線擺動法則是保持刀具接觸點不變,而通過擺動刀具軸線到一新的方向,以使刀具與加工表面相切觸且
49、不再存在干涉。由于刀具切觸點不變,因此該方法在避免過切的同時不會產(chǎn)牛欠切。因此,它是五坐標加工中避免刀具干涉的較理想的方法,且在刀桿干涉時也只能用軸線擺動法進行處理,[如圖2.12所示]。 圖2.12軸線擺動法避免刀桿干涉 2)側(cè)銑加工刀具干涉的避免 五坐標側(cè)銑加工刀具干涉避免有三種方法:軸線平移、軸線擺動和軸向移動。其中軸線平移和軸線擺動用于處理刀桿干涉,而軸向移動用于處理刀頭干涉。 軸線平移方法[如圖2.13所示]是使刀具在垂直于刀軸的平面內(nèi)沿某一方向(如曲面法失方向)平移到一個新的位置,
50、以使刀具與加工表面相切接觸或使在整個刀具切削長度內(nèi)的加工誤差分布滿足給定精度要求。該方法計算簡單,但是有可能產(chǎn)生較大欠切。軸線擺動方法與端銑加工時類似,但其目的是要使得在整個刀具切削長度內(nèi)的加工誤差分布均勻且最大誤差滿足給定精度要求。由于算法復雜,目前只是針對特定的加工對象和加工方式進行一定程度的處理,例如在加工不可展直紋面時采取的雙點偏置法和多點偏置法。 圖2.13軸線平移法避免刀桿干涉 2.2本章小結 高質(zhì)量的五軸加工編程對于實現(xiàn)高質(zhì)、高效的五軸數(shù)控加工至關重要。本章首先介紹了五軸加工編程工藝的有關內(nèi)容,
51、包括刀具選擇、切削用量確定、刀路軌跡生成方法以及干涉的產(chǎn)生和避免方法。其次討論了對雙轉(zhuǎn)臺型、雙擺頭型以及特殊轉(zhuǎn)臺配置型式機床的后置處理算法。特別是特殊運動軸旋轉(zhuǎn)方式數(shù)控機床后置處理算法的討論,不僅有助于加深對機床運動學的理解,還可以為其它類型運動軸旋轉(zhuǎn)方式的數(shù)控機床的后置處理提供一定的解決思路。3 五軸數(shù)控加工仿真幾何模型的建立 所謂仿真,就是用模型代替實際系統(tǒng)進行的試驗和研究,它的最基本和最重要的 步驟就是建立數(shù)學模型。通過數(shù)學建模對現(xiàn)實世界中存在的復雜的實體及實體的關系 進行抽象和簡化,得到系統(tǒng)的基本特征和實體的基本屬性或特點,忽略其次要的屬性, 并通過這種
52、簡化建立一定的數(shù)學表示方法和數(shù)據(jù)結構來描述實體的基本屬性及實體 間的相互關系。本文所涉及的數(shù)控加工仿真就是通過計算機在屏幕上模擬出刀具對工 件的加工過程,因此建模的關鍵就是要為這個加工過程建立一套可以被計算機接受并 表示的數(shù)據(jù)結構。 3.1 三維實體表示方法概述 3.1.1 線框圖表示法 早期的計算機圖形生成技術中,三維物體大多是用線框模型來表示的。線框模型 是由定義一個物體邊界的直線和曲線組成,每一條直線和曲線都是單獨構造出來的, 并不存在面的信息。由于它具有表示方法比較簡單和運算速度快的優(yōu)點,在早期數(shù)控 加工仿真和驗證中得到了應用。但是,單一的線框模型存在
53、著幾個不可克服的缺陷; (1) 用線框模型表示出來的三維物體常常具有二義性;(2) 表示空間實體的線框模 型也易于構造無效形體;(3) 線框模型不能正確表示曲面信息。由于存在這些問題 所以線框模型應用并不廣泛。 3.1.2 邊界表示法 邊界表示法((Boundary Representation ,B-rep)也是一種出現(xiàn)比較早的幾何建 模方法,它的基本思想是把物體定義為封閉的邊界表面圍成的有限空間,這樣一個形 體可通過它的邊界即面的子集來表示。而每一個面又通過邊、邊通過點、點又通過 三個坐標值來定義。因此邊界表示法強調(diào)的是形體外表細節(jié)詳細,記錄了構成幾何形 體的
54、所有幾何、拓撲信息,其模型中的數(shù)據(jù)結構如圖2.1所示是一個網(wǎng)狀結構。 邊界表示法的優(yōu)點在于含有較多的關于面、邊、點及其相互關系的信息,這些信 息對于工程圖繪制及圖形顯示都是十分重要的,并且易于同二維繪圖軟件銜接和同曲 面建模軟件聯(lián)合應用,此外,這種方法便于通過人機交互方式對物體模型進行局部修改。但是有關物體生成的原始信息,即它是由哪些基本體定義的,是怎樣拼合而成的, 在邊界表示法中無法提供,同時描述所需信息量較大并有信息冗余。 在數(shù)控加工仿真中,直接利用邊界表示法來作為幾何造型方法的幾乎沒有,更多 使用的是一種可以認為是從邊界表示法演變而來,或者說它就是屬于邊
55、界表示法的一 種方法,一種被稱為三角片離散法的方法,[也有的學者將這種方法稱為Z-map結構。 這種方法僅僅針對于三軸的數(shù)控銑削仿真。在三軸數(shù)控銑床加工中加工工件有以下特 點:(1) 只有毛坯的上表面才是加工表面;(2) 平行于刀軸的一條直線與被加工的 毛坯的上表面有且僅有一個交點。三角片離散法將上表面離散為均勻點陣,再將這些 點陣連接成三角網(wǎng)格。在加工仿真過程中,通過不斷修改上表面點陣的高度,再對三 角網(wǎng)格進行真實感渲染,以此實現(xiàn)數(shù)控加工仿真時材料的去除過程。 使用三角片離散法進行數(shù)控加工仿真,對于三軸仿真來講,這是一種不錯的選擇, 它有簡單、高效和易于實現(xiàn)等優(yōu)點。但
56、是其缺點也是顯而易見的,它只適用于三軸銑 削對多于三軸的銑削仿真無能為力,而且在對仿真的精度要求較高或者仿真的模型 較大時,由于三角網(wǎng)格數(shù)目的增大,會影響動態(tài)顯示的速度減少離散點可以加快仿真速度,但是以犧牲仿真精度和圖像的顯示質(zhì)量為代價。 4.圓管凸模數(shù)控加工 4.1 建立制造模型。 圖4.1 圓管凸模
57、1.利用原件放置操控板,選擇約束類型為缺省,然后單擊原件放置對話框上的確定按鈕。 2.創(chuàng)建工件,具體步驟如下。 a.單擊右側(cè)制造單元工具欄自動工件,打開操縱版,選中創(chuàng)造矩形工件。 b.單擊右側(cè)選項按鈕,設計矩形的尺寸。 4.2體積塊加工 (1) 單擊上面NC銑削工具欄的體積塊粗加工,彈出NC序列菜單,依次選擇序列設置、刀具、參數(shù)、退刀曲面、窗口、完成、命令。 (2) 刀具設置,具體操作步驟如下。系統(tǒng)自動打開刀具設定對話框設定刀具參數(shù)如下圖。 圖4.2 刀具設定及設置 (3) 加工參數(shù)的設置。系統(tǒng)自動打開編輯序列參數(shù)對話框,設定銑削參數(shù)如下圖
58、所示。 圖4.3編輯序列參數(shù)、體積塊加工 (4)刀具路徑演示,具體步驟如下。在NC序列菜單中依次選擇菜單播放路徑、演示命令,如下圖。 圖4.4刀具演示路徑 (5)刀具路徑檢查。在NC序列中依次選定播放路徑、NC檢查命令,系統(tǒng)彈出下圖所示的VERICUT對話框,系統(tǒng)進入切削動態(tài)模擬狀態(tài),并顯示加工完成后的效果。 圖4.5vericut切削檢查
59、 4.3曲面銑削精加工 (1) 單擊上面NC銑削工具欄上的曲面加工按鈕彈出加工軸菜單選擇5軸,在彈出的NC序列菜單中依次選擇序列設置,刀具,參數(shù),曲面,定義切削,軸定義,完成。 (2) 刀具設置具體步驟如下圖 圖4.6精加工刀具設定 (3)加工參數(shù)的設定系統(tǒng)自動打開編輯序列參數(shù)曲面銑削對話框,設定銑削參數(shù)如下圖收示。 圖4.7曲面銑削序列參數(shù) (4) 刀具路徑檢查。在NC序列菜單中依
60、次選擇菜單播放路徑,NC檢查命令,系統(tǒng)彈出如圖對話框,單擊播放,系統(tǒng)進入切削動態(tài)模擬狀態(tài),并顯示加工完成后的效果。 圖4.8vercuit切削檢查 4.4后置處理生成加工程序 (1)選擇下拉菜單編輯,CL數(shù)據(jù),輸出命令,彈出選取特征菜單選擇操作--OP010,在彈出的軌跡菜單中選擇文件選項,彈出輸出類型菜單,選擇CL文件,交互,完成,系統(tǒng)彈出保存副本對話框使用默認的文件名OP010.ncl單擊確定完成CL文件創(chuàng)建。 (2)選擇選擇下拉菜單工具,CL數(shù)據(jù),后處理命令,系統(tǒng)彈出打開對話框,選擇上一步創(chuàng)建后處理文件OP010.n
61、cl。 (3)在彈出后置處理選項菜單中選擇詳細跟蹤,在彈出后置處理列表菜單中選擇UNCX01.P11,在系統(tǒng)彈出命令提示符窗口輸入程序號1000后,系統(tǒng)自動在后臺進行后置處理,后置處理完成后NC代碼存放在OP010.ncl。 (4)在當前目錄下們用記事本程序打開保存的OP010.ncl文件。則生成數(shù)控加工程序。 結 論 五軸加工領域,由于機床結構的多樣性和機床運動的復雜性,對于后置處理和加工編程的實現(xiàn),技術難度較大,特別是后置處理己成為機床效率發(fā)揮的制約因素。本課題針對五軸機床后置處理和五軸編程的實現(xiàn),主要進行了以下幾個方面的
62、工作: 1、分析討論了多種配置類型的五軸數(shù)控加工中心后置處理坐標變換算法,特別是45度斜B軸特殊雙轉(zhuǎn)臺五軸機床的坐標變換算法,不但有助于加深對機床運動學的理解,還可以為推導其它特殊配置形式五軸機床的后置處理算法提供一定的解決思路。 2、針對45度斜B軸特殊雙轉(zhuǎn)臺五軸機床,通過兩種手段進行了后置處理開發(fā)。一是基于Pro/E輔助模塊進行了后置處理開發(fā),一是基于五軸機床坐標變換算法采用。語言編寫了專用后置程序。 3、綜合運用課題所涉及的五軸加工編程工藝的有關內(nèi)容,特別是刀路軌跡生成以及干涉避免的方法。 本課題雖然在五軸加工后置處理和五軸編程方面進行了一定程度的研究,但是由于五軸加工的復雜性,
63、在后置處理和五軸編程方面還有很多需要解決的問題。比如,后置處理過程中非線性誤差補償?shù)葐栴};五軸加工編程中考慮到加工效率和刀具壽命等問題的工藝優(yōu)化等問題,都是需要進一步進行廣泛學習和深入研究的內(nèi)容。 參 考 文 獻 [1]全榮.五坐標聯(lián)動數(shù)控技術.長沙:湖南科學技術出版社,1995. [2]劉雄偉.數(shù)控加工理論與編程技術.北京:機械工業(yè)出版社,2003. [3]周濟,周艷紅.數(shù)控加工技術.北京:國防工業(yè)出版社,2002. [4]劉雄偉,張定華等.數(shù)控加工理論與編程技術.北京:機械工業(yè)出版社,1994. [5]王隆太.機械CAD/CAM技術.北京:機械工業(yè)出版社,2004
64、. [6]孔慶復.計算機輔助設計與制造.哈爾濱工業(yè)大學出版社,1997. [7]唐榮錫,汪嘉業(yè)等.計算機圖形學教程.北京:科學出版社,2001. [8]李明雪,劉小川等.EdgeCAM12.0基礎與實例教程.北京:化學工業(yè)出版社,2008. [9]李云龍,曹巖.數(shù)控機床加工仿真系統(tǒng)VERICUT.西安:西安交通大學出版社,2005. [10]呂鳳民.后置處理算法及基于UG/即Open GRIP下的程序開發(fā).大連理工大學碩士學位論文.2005. [11]丁勇,耿小強,陳剛一種特殊結構的五軸數(shù)控機床的后置處理算法與軟件實現(xiàn).CAD/C枷與制造業(yè)信息化,2005,l:77.78. [1
65、2]馮顯英,葛榮雨.五坐標數(shù)控機床后置處理算法的研究.工具技術,2006,40(4):44-46. [13]劉日良,張承瑞,宋現(xiàn)春,劉戰(zhàn)強,艾興.5軸數(shù)控機床坐標系統(tǒng)的一個特例及其后置處理,2005,40(4):44-46. [14]鄧奕,彭浩炯,謝駭.CAM后置處理技術研究現(xiàn)狀與發(fā)展趨勢.湖南工程學院學報,2003,40(4):44-46. [15]〕何永紅,齊樂華等.雙轉(zhuǎn)臺五軸數(shù)控機床后置處理算法研究.制造技術與機床,2006,40(4):44-46. [16]C.Lartigue,E.Duc,A.Affouard.Tool path deformation in 5.axis f
66、lank milling using envelop surface.Computer.Aided Design,2003,35:375.382. [17]Yen.Hung Chen,Yuan.Shen Lee,and Shu.Cherng Fang.Optimal cutter selection and machining Plane determination for Process Planning and NC machining of complex surface. Journal of Manufacturing systems,1998,17(5):371一388. [18]Tae.Soon Lim,Chea.Moon Lee,Seok.Won Kim etc.Evalution of cutter or ientations in 5.axis high speed milling of tubine blade.Journal of Materials Processing Teehnology,2002,130.131:401.406.
- 溫馨提示:
1: 本站所有資源如無特殊說明,都需要本地電腦安裝OFFICE2007和PDF閱讀器。圖紙軟件為CAD,CAXA,PROE,UG,SolidWorks等.壓縮文件請下載最新的WinRAR軟件解壓。
2: 本站的文檔不包含任何第三方提供的附件圖紙等,如果需要附件,請聯(lián)系上傳者。文件的所有權益歸上傳用戶所有。
3.本站RAR壓縮包中若帶圖紙,網(wǎng)頁內(nèi)容里面會有圖紙預覽,若沒有圖紙預覽就沒有圖紙。
4. 未經(jīng)權益所有人同意不得將文件中的內(nèi)容挪作商業(yè)或盈利用途。
5. 裝配圖網(wǎng)僅提供信息存儲空間,僅對用戶上傳內(nèi)容的表現(xiàn)方式做保護處理,對用戶上傳分享的文檔內(nèi)容本身不做任何修改或編輯,并不能對任何下載內(nèi)容負責。
6. 下載文件中如有侵權或不適當內(nèi)容,請與我們聯(lián)系,我們立即糾正。
7. 本站不保證下載資源的準確性、安全性和完整性, 同時也不承擔用戶因使用這些下載資源對自己和他人造成任何形式的傷害或損失。