畢業(yè)設(shè)計(jì)論文 外文文獻(xiàn)翻譯 中英文對(duì)照 鋁合金壓鑄工藝過(guò)程中金屬流動(dòng)行為的變形分區(qū)
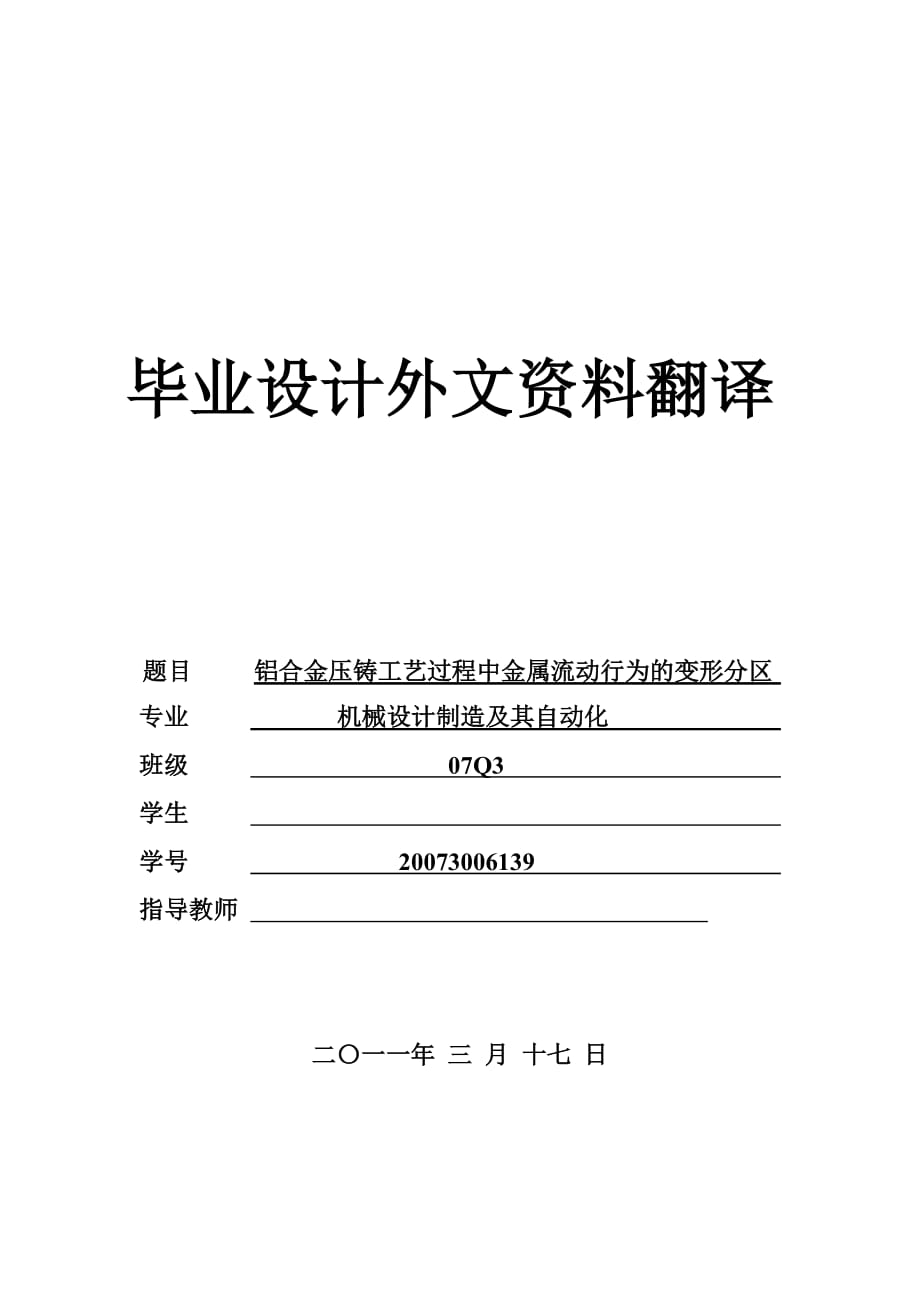


《畢業(yè)設(shè)計(jì)論文 外文文獻(xiàn)翻譯 中英文對(duì)照 鋁合金壓鑄工藝過(guò)程中金屬流動(dòng)行為的變形分區(qū)》由會(huì)員分享,可在線閱讀,更多相關(guān)《畢業(yè)設(shè)計(jì)論文 外文文獻(xiàn)翻譯 中英文對(duì)照 鋁合金壓鑄工藝過(guò)程中金屬流動(dòng)行為的變形分區(qū)(20頁(yè)珍藏版)》請(qǐng)?jiān)谘b配圖網(wǎng)上搜索。
1、 畢業(yè)設(shè)計(jì)外文資料翻譯 題目 鋁合金壓鑄工藝過(guò)程中金屬流動(dòng)行為的變形分區(qū) 專業(yè) 機(jī)械設(shè)計(jì)制造及其自動(dòng)化 班級(jí) 07Q3 學(xué)生 學(xué)號(hào) 20073006139 指導(dǎo)教師
2、 二〇一一年 三 月 十七 日 J. Cent. South Univ. Technol. (2009) 16: 0738?0742 DOI: 10.1007/s11771?009?0122?3 Deformation division of metal flow behavior during extrusion process of 7075 aluminum alloy LI Feng CHU Guan-nan LIU Xiao-jing (1. College of Materials Science
3、 and Engineering, Harbin University of Science and Technology, Harbin 150040, China; 2. College of Shipping, Harbin Institute of Technology at Weihai, Weihai 264209, China) Abstract: To reduce defects caused by non-homogeneous metal flow in conventional extrusion, a die with guiding angle w
4、as designed to improve the metal flow behavior. The characteristic quantities such as the second invariant of the deviator stress J2 and Lode’s coefficient were employed for the division of deformation area. The results show that when the metal is extruded with the guiding angle, no metal flow inte
5、rface forms at the container’s bottom, the dead zone completely disappears, the deformation types of the metal in the plastic deformation area change from three types to one type of tension, and the homogeneity of the deformation as well as metal flow are greatly improved. The non-homogeneous metal
6、flow at the final stage of extrusion is improved, reducing the shrinkage hole at the axis end. The radial stress of the furthest point from the axis is transformed from tensile stress to compressive stress and the axial stress, and decreased from 70.8 to 34.8 MPa. Therefore, the surface cracks cause
7、d by additional stress are greatly reduced. Key words: extrusion process; flow defect; deformation division 1 Introduction The improvement of the metal flow during extrusion processes is an important means to increase the formability and eliminate defects [1]. Many factors may influence the
8、 metal flow, among which the die structure is closely related to the metal flow.Analysis of die pocket design parameters shows that different pocket angles and pocket offsets will influence the metal flow greatly, and the latter tends to cause the bending of extrusion products [2?4]. CHUNG et al [5]
9、 discovered that the inhomogeneity of the strain distribution and generation of dead zone during double shear extrusion could be decreased by applying a smaller taper. ULYSSE [6] found that if the die bearing was not corrected or tuned appropriately, the product might be twisted and warped. Finite e
10、lement method can be used for the optimum design of the die [7],and the homogeneity of the metal flow can be controlled effectively; the metal can beextruded easily [8], and the extrusion force can be decreased greatly [9]. Many researches on the optimum design of the die have been done, but most o
11、f them are designed for avoiding a certain extrusion defect. It is complicated tooptimize the die structure by employing the finite element method, and even difficult to apply it to practical production [10?12]. For the above shortcomings, an extrusion die with guiding angle was designed to improve
12、the metal flow during extrusion process. The guiding angle is different from the entry round corner of the conventional die [13]. Although a wider entry round corner can be employed to improve the product quality, it cannot basically improve the metal flow and avoid the defects; after the guiding an
13、gle is employed, the metal in the deforming area is extruded twice with a lower extrusion ratio, which greatly changes the metal flow at the die pocket and influences the extrusion defects. Therefore, in this work, numerical simulation of extruding with and without guiding angle was carried out to i
14、nvestigate the influence of guiding angle on metal flow, and comparison analysis between simulation and experiment results was also conducted. 2 Simulation conditions 2.1 Die structure The direct hot extrusion was taken as example. The die structures with and without guiding angle are shown in
15、 Fig.1. Guiding angle (θ) can change in a certain range, and θ=0? means without guiding angle. 2.2 Finite element model DEFORMTM?2D was used to simulate the extrusion process. Because of the symmetrical characteristics, axisymmetric model was selected in the simulation, as shown in Fig.2. The
16、 radial constrain is superimposed on the symmetry plane to make the normal deformation zero. Fig.1 Schematic drawings of die structure under conditions of without (a) and with (b) guiding angle (θ) Fig.2 Finite element model of extrusion process under conditions of without (a) and with (b)
17、 guiding angle Aluminum alloy 7075 billet was used in the experiments. The billet was 50 mm in diameter and 50 mm in height. The geometrical and material parameters were the same in both the simulation and experiment. In this work, the extrusion process was simulated by using rigid-plastic fi
18、nite element model. The punch, container and die were considered as rigid bodies. The speed of the punch was 2 mm/s; the time increment was 0.1 s; the friction coefficient was 0.3; the isothermal extrusion temperature was 435 ℃, and the extrusion ratio was 9.8. Numerical simulation was carried out a
19、t θ=5?, 10?, 15?, 20? and 30?, respectively. The results showed that extrusion load was the minimum at θ=15? [14]. Therefore, the die with θ=15? was selected. 3 Simulation of metal flow 3.1 Steady stage It can be seen from the deformation of the grids that, grids in this area mostly flo
20、w towards the die pocket in the form of parallelogram, which indicates that the deformation and flow of the metal are homogeneous. Therefore, it is easy for the metal to flow out the die pockets without the formation of dead zone. Fig.3 shows the velocity field with and without the guiding angle at
21、 the bottom of the die. It can be seen from Fig.3(a) that without employing the guiding angle, there is an obvious metal flow interface at the bottom of the die. A part of metal flows towards the die pocket, the other flows inward, and the dead zone is formed. After employing the guiding angle, as s
22、hown in Fig.3(b), the metal near the container flows towards the die pockets homogeneously, and no velocity interface is formed in the plastic deformation zone. The metal flows towards the die pockets radially without large angle turning, which will not only decrease the flow line turbulence, dead z
23、one and overlap, but also improve the extrusion product quality. Fig.3 Velocity field at bottom of die under conditions ofwithout (a) and with (b) guiding angle Comparison of the axial stress on the die exit section with and without the guiding angle is shown in Fig.4. The stress st
24、ates of the axis and surface are compressive stress and tensile stress respectively when the metal is extruded without the guiding angle. With the increase of the distance from axis, the axial stress transforms from compressive stress to tensile stress. The compressive stress and tensile stress are
25、approximately equal, which will result in non-homogeneity of the microstructure and properties. The additional stress increases rapidly and leads to the surface cracks when the lubrication condition is not very good. After the guiding angle is employed, the axial tensile stress of the surface point
26、decreases from 70.8 (P1) to 34.8 (P2) MPa, and the axial stress distribution along theradial direction changes a little (Fig.4(a)). The radial stress distribution is shown in Fig.4(b), without employing guiding angle, the stress state of axial points is compressive stress and that of the surface p
27、oints is tensile stress that increases with the distance from axis. After the guiding angle is employed, the radial stress at the die exit becomes compressive stress, and the radial stress and compressive stress are almost equal. 3.2 Final stage When lower billet is extruded at the final stage of
28、 extrusion process, shrinkage cavity is a common defect. The comparison of the equivalent strain distribution at the feeding of the punch of 48 mm is shown in Fig.5. Fig.4 Distribution of axial stress (a) and radial stress (b) Fig.5 Equivalent strain distribution at final stage of extrusion
29、under conditions of without (a) and with (b) guiding angle The inhomogeneous deformation and flow are obvious during the extrusion without the guiding angle, as shown in Fig.5(a). Compared with the outside metal, the inner metal deforms and flows faster, which causes that the outside metal cannot f
30、ill in time and the shrinkage cavity forms at the last stage of extrusion. After the guiding angle is employed as shown in Fig.5(b), the mean strain difference between the metal near the axis and at the bottom of the die changes a little, and the metal flow in the deformation zone is homogeneous.
31、4 Deformation division The stress distribution in the deformed grids can be obtained by the post-process module of the numerical simulation software, which is convenient for further analysis. 4.1 Method of deformation division In extrusion, the metal in some regions of a billet cannot sa
32、tisfy the plastic deformation condition and the plastic deformation cannot occur due to the friction. For the convenience, the von-Mises yield criterion can be described by [15] where J2 is the second invariant of the deviator stress, and σS is the flow stress of the work piece, which is a
33、 constant value. Using invariant J2, the division of stress field without or with the guiding angle can be shown in Fig.6. The regions marked with shadow represent the areas where the plastic deformation occurs. Fig.6 Division of rigid and plastic regions under conditions of without (a) and with
34、 (b) guiding angle Fig.6(a) shows that without the guiding angle, the region of the workpiece in the upper part of the container and in the lower corner of the container does not deform plastically. In the extrusion with the guiding angle, as shown in Fig.6(b), the plastic region is larger, and
35、 there is no dead zone. So it can be assumed that the guiding angle increases the area of plastic deformation of the metal at the bottom corner of the container. 4.2 Types of deformation Lode’s parameter is used to represent the stress situation regularly since it can reflect the relative magni
36、tude of the second principal stress, and it is also relative with the type of strain state. ?1≤<0 represents tensile strain state, =0 represents plane strain state and 0≤<1 represents compressive strain state. That is, the type of strain state and the degree of complicacy can be determined by Lode’
37、s coefficient. Through the analysis of Lode’s coefficient, some measures can be taken to change the stress situation, and then change the plastic deformation condition to improve the forming property of the billet. Based on the rigid-plastic division, the strain of the material in the plastic are
38、a during extrusion process can be classified into different types using the visual display of Lode’s coefficient, as shown in Fig.7. Fig.7 Division of Lode’s coefficient under conditions of without (a) and with (b) guiding angle It can be seen from Fig.7(a) that without the guiding angle, L
39、ode’s coefficient in most of the region near the die is negative, i.e. the strain in the material is tensile. The region where Lode’s coefficient equals zero belongs to plane strain; while at the corner of the container, Lode’s coefficient is positive, i.e. the strain is compressive. In the extrusio
40、n with active friction, the strain in the plastic region is everywhere tensile, as shown in Fig.7(b). So, compared with the extrusion without the guiding angle, the metal flow in the container is more homogeneous. 5 Experimental Comparison of the metal flow line at the final stage of extru
41、sion is shown in Fig.8. Flow line in the container is inhomogeneous at the last stage of conventional extrusion. It bends more seriously at bottom die corner in the extrusion process, which indicates that the hard deforming area increases. Flow velocity near the container and axis is greatly differe
42、nt, and the metal at axis flows faster, which tends to cause the shrinkage cavity, as shown in Fig.8(a). 6 Conclusions (1) When the guiding angle is used, axial stress state of the metal near the axis changes from tensile stress to compressive stress, and the shrinkage cavity caused by the
43、 higher flow velocity of the axial metal is reduced. (2) The axial stress at the die exit is decreased by using the guiding angle, the inhomogeneity of flow velocity is reduced remarkably, and the twisting caused by the inhomogeneous metal flow is decreased. Therefore, the surface cracks caused by
44、 additional stress are avoided. (3) The results indicate that when the metal extruded with the guiding angle by deformation division, the dead zone of metal completely disappears, the deformation type of the metal in the plastic deformation area changes from three types to a type of tension, and t
45、he homogeneity of the deformation as well as metal flow are greatly improved, which is helpful for extruding and promoting the quality of extrudates. References [1] PONALAGUSAMY R, NARAYANASAMY R, SRINIVASAN P. Design and development of streamlined extrusion dies: A Bezier curve approach
46、[J]. Journal of Materials Processing Technology, 2005, 161(3): 375?380. [2] DAMODARAN D, SHIVPURI R. Prediction and control of part distortion during the hot extrusion of titanium alloys [J]. Journal of Materials Processing Technology, 2004, 150(1/2): 70?75. [3] DENG Xiao-min, SUN Hong-jian, LI
47、Sheng-zhi, FANG Mu-yun, CAO Jie. Friction and friction coefficient for aluminium alloyextrusion [J]. The Chinese Journal of Nonferrous Metals, 2003, 13(3): 599?605. (in Chinese) [4] HAMBLI R, BADIE L D. Damage and fracture simulation during the extrusion processes [J]. Computer Methods in Applied
48、Mechanics and Engineering, 2000, 186(1): 109?120. [5] CHUNG S W, KIM W J, HIGASHI K. The effect of die geometry on the double shear extrusion by parametric FVM simulation [J]. Scripta Materialia, 2004, 51(11): 1117?1122. [6] ULYSSE P. Extrusion die design for flow balance using FE and optimizati
49、on methods [J]. International Journal of Mechanical Sciences, 2002, 44(2): 319?341. [7] HOSSEIN R D, MOSTAFA K. Simulation of “L” section extrusion using upper bound method [J]. Journal of Materials and Design, 2004, 25(6): 535?540. [8] ZOU L, XIA J C, WANG X Y. Optimization of die profile for i
50、mproving die life in the hot extrusion process [J]. Journal of Materials Processing Technology, 2003, 142(3): 659?664. [9] FAZAL A, ARIF M. On the use of non-linear finite element analysis in deformation evaluation and development of design charts for extrusion processes [J]. Finite Elements in An
51、alysis and Design, 2003, 39(10): 1007?1020. [10] LI Q, SMITH C J, HARRIS C, JOLLY M R. Finite element investigations upon the influence of pocket die designs on metal flow in aluminium extrusion (Part I): Effect of pocket angle and volume on metal flow [J]. Journal of Materials ProcessingTechnolog
52、y, 2003, 135(2/3): 189?196. [11] LI Q, SMITH C J, HARRIS C, JOLLY M R. Finite element modelling investigations upon the influence of pocket die designs on metal flow in aluminium extrusion (Part II): Effect of pocket geometry configurations on metal flow [J].Journal of Materials Processing Technol
53、ogy, 2003, 135(2/3): 197?203. [12] LEE D J, KIM D J, KIM B M. New processes to prevent a flow defect in the combined forward-backward cold extrusion of a piston-pin [J]. Journal of MaterialsProcessing Technology, 2003, 139(1/3): 422?427. [13] LI F, YUAN S J, HE Z B. Effect of guiding angle on me
54、tal flow and defects in extrusion deformation [J]. Journal of Materials Science and Technology, 2007, 15(1): 15?18. (in Chinese) [14] ZOU Liang. Study on the function of impeding angle in extrusion die [J]. Journal of Plastic Engineering, 2006, 13(2): 67?69. (in Chinese) [15] HU W L, HE Z B, FAN
55、G Y. Uniform principle on stress, strain and yield locus for analyzing metal forming processes [J]. Journal of Materials Processing Technology, 2004, 151(1/3): 27?32. (Edited by CHEN Wei-ping) 鋁合金壓鑄工藝過(guò)程中金屬流動(dòng)行為的變形分區(qū) 哈爾濱工業(yè)大學(xué) 材料科學(xué)與工程學(xué)院 哈爾濱工業(yè)大
56、學(xué)威海分校 船舶工程學(xué)院 摘 要:為減少因傳統(tǒng)壓鑄過(guò)程中不均勻金屬流動(dòng)引起的缺陷,設(shè)計(jì)發(fā)明了一款帶有導(dǎo)角的沖模用于改善金屬流動(dòng)行為。諸如偏應(yīng)力的第二不變量J2和羅德系數(shù)等特征量均用于變形分區(qū)。結(jié)果顯示,當(dāng)使用導(dǎo)角對(duì)金屬進(jìn)行壓鑄時(shí),容器底部未形成任何金屬流動(dòng)界面,死區(qū)完全消失,塑性變形區(qū)域中的金屬變形類型由三種張力變?yōu)橐环N張力,且變形和金屬流動(dòng)的均勻性均得到極大改善。最后壓鑄階段的不均勻金屬流動(dòng)得到了改善,從而減少了軸端的縮孔。距離軸最遠(yuǎn)的點(diǎn)上的徑向應(yīng)力由張應(yīng)力轉(zhuǎn)變?yōu)榭箟簯?yīng)力和軸向應(yīng)力,壓強(qiáng)由70.8兆帕降至34.8兆帕。因此,由附加應(yīng)力引起的表面裂縫大大減小。 關(guān)鍵詞 壓鑄工藝 流
57、動(dòng)缺陷 變形分區(qū) n 1簡(jiǎn)介 在擠壓過(guò)程中改善金屬流動(dòng)是一個(gè)重要手段,可以提高成形性和消除缺陷[1]。許多因素可能會(huì)影響到金屬的流動(dòng),其中模具結(jié)構(gòu)與金屬流動(dòng)是密切相關(guān)的。模袋設(shè)計(jì)參數(shù)分析表明,不同的角度和模腔的偏移對(duì)金屬流動(dòng)影響較大,而后者往往造成產(chǎn)品的擠壓彎曲[2?4]。CHUNG等人[5]發(fā)現(xiàn)可以通過(guò)采用一個(gè)較小的錐形來(lái)降低應(yīng)變分布和雙剪切擠壓過(guò)程中死區(qū)產(chǎn)生的不均勻性。ULYSSE[6]發(fā)現(xiàn),如果不糾正或適當(dāng)調(diào)整模具軸承,該產(chǎn)品可能被扭曲和變形。有限元方法可用于模具[7]優(yōu)化設(shè)計(jì),以及有效控制金屬流動(dòng)的均勻性,金屬很容易被擠壓 [8],擠壓力也可以大大降低[9]。 許多對(duì)模具優(yōu)化
58、設(shè)計(jì)的研究工作已經(jīng)完成,但其中大多數(shù)是為避免某些擠壓缺陷而設(shè)計(jì)的。通過(guò)采用有限元方法可以使復(fù)雜的模具結(jié)構(gòu)優(yōu)化,但很難將它應(yīng)用到實(shí)際生產(chǎn)[10-12]。對(duì)于上述缺點(diǎn),從擠壓模具的設(shè)計(jì)與導(dǎo)流角來(lái)看可以提高擠壓過(guò)程中金屬的流動(dòng)性。 導(dǎo)流角是指?jìng)鹘y(tǒng)的模具[13]項(xiàng)圓角不同。雖然引入過(guò)渡角可以提高產(chǎn)品質(zhì)量,難以根本改善金屬的流動(dòng)以及避免缺陷;經(jīng)過(guò)導(dǎo)流角之后,在擠壓變形區(qū)金屬具有兩次較低擠壓比,極大地改變了死在腔里的金屬流動(dòng),影響擠壓缺陷。因此,在這項(xiàng)工作中,數(shù)值模擬擠壓和無(wú)導(dǎo)流角會(huì)影響金屬流動(dòng)的角度,還必須比較分析模擬與實(shí)驗(yàn)的結(jié)果。 n 2 模擬條件 n 2.1模具結(jié)構(gòu) 直接熱擠
59、壓被視為典范。有無(wú)導(dǎo)流角模具結(jié)構(gòu)如圖1所示。導(dǎo)流角(θ)可以在一定范圍內(nèi)變化,θ=0?只沒(méi)有導(dǎo)流角的情況。 n 2.2有限元模式 DEFORMTM- 2D的是用來(lái)模擬擠壓過(guò)程。由于對(duì)稱的特點(diǎn),選擇了如圖2所示的在軸對(duì)稱模型仿真。在徑向約束的對(duì)稱平面上,使正常的變形零疊加。 圖1圖中模具結(jié)構(gòu)沒(méi)有導(dǎo)流角(a)和有導(dǎo)流角(b) 圖2在擠壓工藝條件下有限元模型沒(méi)有導(dǎo)流角(a)和有導(dǎo)流角(b) 在實(shí)驗(yàn)中應(yīng)用7075鋁合金坯。坯料直徑為50毫米,高度50毫米。模擬實(shí)驗(yàn)的幾何和材料參數(shù)均相同。在這項(xiàng)工作中,模擬進(jìn)行擠壓過(guò)程,采用剛塑性有限元模型。沖床,容器和模具被視為剛體。該沖壓速度為2毫
60、米/秒;的時(shí)間增量為0.1秒;摩擦系數(shù)為0.3;等溫?cái)D壓溫度為435℃,擠壓比為9.8。分別進(jìn)行的數(shù)值模擬為θ= 5?,10?,15?,20?,30?。結(jié)果表明,擠壓負(fù)荷是在θ=15?[14]最低。因此,選中θ=15的沖模。 n 3金屬流動(dòng)的模擬 n 3.1穩(wěn)定階段 從網(wǎng)格變形可以看出,在這個(gè)區(qū)域的電網(wǎng)在沖模腔內(nèi)為平行四邊形。這表明,變形和金屬流動(dòng)很均勻。因此,很容易生成沒(méi)有死區(qū)的沖模腔。 圖3顯示了在模具底部有和沒(méi)有導(dǎo)流角的流場(chǎng)可以看出,從圖3(a),如果沒(méi)有導(dǎo)流角,在模底有一個(gè)明顯的金屬流接口。沖模腔內(nèi)有部分金屬流動(dòng)向內(nèi)部其他方向流動(dòng)形成死區(qū)。有導(dǎo)流角的情況如圖3(b)所示,沖模腔
61、內(nèi)的金屬流向均勻,在塑性變形區(qū)形成沒(méi)有速度的接口。金屬的放射狀流動(dòng)沒(méi)有大角度轉(zhuǎn)向,這不但會(huì)降低湍流流線,死區(qū)和重疊,而且提高擠出模具腔的產(chǎn)品質(zhì)量。 圖3中在模具的底部的流場(chǎng)無(wú)導(dǎo)流角(a)有導(dǎo)流角(b) 關(guān)于出境斷面有無(wú)導(dǎo)流角的軸向應(yīng)力對(duì)比如圖4所示。軸和表面的壓應(yīng)力和拉應(yīng)力分別是金屬在有無(wú)導(dǎo)流角的情況下的擠壓產(chǎn)生的。隨著從軸的距離的增加,軸向應(yīng)力由壓應(yīng)力轉(zhuǎn)變?yōu)槔瓚?yīng)力。壓應(yīng)力和拉應(yīng)力大致相等,這將導(dǎo)致微觀結(jié)構(gòu)和性能的非均勻性。潤(rùn)滑條件不是很好時(shí)額外的壓力急劇增大,并導(dǎo)致表面裂縫。有導(dǎo)流角后,軸向拉應(yīng)力從70.8(?。┙抵?4.8(P2)MPa,沿徑向方向的軸向應(yīng)力分布的變化如(圖4(a)
62、)。無(wú)導(dǎo)流角的徑向應(yīng)力分布如圖4(b),從軸軸向應(yīng)力狀態(tài)為壓應(yīng)力,隨著距離的增加表面變成拉應(yīng)力。有導(dǎo)流角后,在模具出口徑向應(yīng)力變?yōu)閴簯?yīng)力,徑向應(yīng)力和壓應(yīng)力幾乎相等。 n 3.2 最后階段 在擠壓膨化過(guò)程的最后階段,縮孔是一種常見(jiàn)的缺陷。在48毫米打孔的等效應(yīng)變分布比較如圖5所示 圖4 軸向應(yīng)力分布(a)和徑向應(yīng)力(b) 圖5 在擠壓等效應(yīng)變分布的最后階段條件下的無(wú)導(dǎo)流角(a)和有導(dǎo)流角(b)。 非均勻變形和流動(dòng)過(guò)程中沒(méi)有明顯的擠壓,如在圖5(a)所示。在最后階段的擠壓縮孔中,與外面的金屬相比,內(nèi)部金屬變形和流動(dòng)加快。這將導(dǎo)致金屬外面沒(méi)有填補(bǔ)時(shí)間。有導(dǎo)流角后顯示如圖5
63、(b),靠近軸之間的金屬和在一個(gè)小模具更換底部平均應(yīng)變的差異,以及在變形區(qū)金屬流動(dòng)均勻。 n 4 形變分區(qū) 從電網(wǎng)中的變形應(yīng)力分布可以得到數(shù)值模擬軟件,該軟件可以方便的進(jìn)行進(jìn)一步分析后處理模塊。 n 4.1 形變方法的劃分 在一些地區(qū)的鋼坯不能滿足金屬塑性變形和塑性變形的條件,在擠壓時(shí)不能發(fā)生因摩擦。為方便起見(jiàn),馮- Mises屈服準(zhǔn)則可描述[15] 其中J2的是偏應(yīng)力第二不變量,強(qiáng)度σs是工件,這是一個(gè)恒定價(jià)值流的壓力。 J2的使用不變,應(yīng)力場(chǎng)有無(wú)導(dǎo)流角的角度劃分可以顯示在圖6。在標(biāo)有陰影的區(qū)域發(fā)生塑性變形。 圖6剛性和塑性區(qū)沒(méi)有導(dǎo)流角(a)和有導(dǎo)流角(b)。 圖6
64、(a)表明,沒(méi)有導(dǎo)流角,工件在容器的上部和容器的右下角的區(qū)域并未塑性變形。圖6(b)所示,有導(dǎo)流角擠壓時(shí)會(huì)有較大的塑性區(qū),但沒(méi)有死區(qū)。因此,可以認(rèn)為,導(dǎo)流角增加了金屬塑性變形的容器底部角落區(qū)域。 n 4.2 變形的類型 洛德的參數(shù)μ是用來(lái)表示定期壓力的情況,因?yàn)樗梢苑从车诙鲬?yīng)力的相對(duì)大小,而且也與應(yīng)變狀態(tài)類型相對(duì)-1≤μ<0表示拉伸應(yīng)變狀態(tài),μ=0表示平面應(yīng)變狀態(tài),0≤μ〈1指壓應(yīng)變狀態(tài)。也就是說(shuō),應(yīng)變狀態(tài)的類型和復(fù)雜程度可以由洛德的系數(shù)確定。通過(guò)洛德的系數(shù)分析,可以采取一些措施在改變壓力的情況下,然后更改的塑性變形條件,提高鋼坯的成形性能。 以剛塑性分工為基礎(chǔ),該地區(qū)在塑料擠出過(guò)程
65、中材料變形可利用洛德的系數(shù)視覺(jué)展示,如在圖7所示的不同類型。 圖7部洛德的系數(shù)條件下,沒(méi)有導(dǎo)流角(a)和有導(dǎo)流角(b) 從圖7(a)可以看出,如果沒(méi)有導(dǎo)流角,洛德在附近的模具地區(qū)最系數(shù)為負(fù),即在材料拉伸應(yīng)變。所在地區(qū)的洛德系數(shù)為零屬于平面應(yīng)變,而在集裝箱角落,洛德的系數(shù)為正,即應(yīng)變壓縮。主動(dòng)摩擦擠壓時(shí),塑性區(qū)中的拉伸應(yīng)變是無(wú)處不在的,如在圖7(b)所示。因此,相對(duì)于無(wú)導(dǎo)流角的擠壓,在容器中金屬的流動(dòng)更加均勻。 n 5 實(shí)驗(yàn) 在最后階段的金屬擠壓流線的比較圖8所示。流線在最后階段的常規(guī)擠壓不均勻。在擠壓過(guò)程中它的彎曲角多在底模,這表明硬盤嚴(yán)重變形面積增加。在金屬軸快流時(shí)軸附近的速度會(huì)
66、大大不同,往往導(dǎo)致縮孔,在圖8(a)所示。 圖8 金屬流線在上一節(jié)最后階段的擠壓條件下的無(wú)導(dǎo)流角(a)和有導(dǎo)流角(b) 從圖8所示的流線(b)可以看出,在擠壓與導(dǎo)角的最后階段,部分金屬流線均勻且?guī)缀跗叫杏谳S。在模具底部金屬流線稍微彎曲。相對(duì)于傳統(tǒng)的擠壓,在容器中金屬的流動(dòng)更加均勻??s孔減少,產(chǎn)品質(zhì)量明顯提高。 n 6 結(jié)論 (1)當(dāng)使用導(dǎo)流角時(shí),附近的軸拉應(yīng)力變化。對(duì)較高流動(dòng)速度的金屬軸其壓應(yīng)力,縮孔及軸向應(yīng)力狀態(tài)降低。 (2)在模具出口使用導(dǎo)流角降低了軸向應(yīng)力,流速不均勻性明顯降低,由金屬流動(dòng)不均勻造成的扭曲現(xiàn)象減少。因此,表面引起的附加應(yīng)力裂縫是可以避免的。 (3)結(jié)果表明,在金屬擠壓與導(dǎo)流角的變形區(qū),金屬死區(qū)完全消失,在塑性變形區(qū),改變了金屬三種類型類型的變形均勻性,很大的提高了金屬的流動(dòng)性,提高了質(zhì)量。 參考文獻(xiàn): [1] PONALAGUSAMY R, NARAYANASAMY R, SRINIVASAN P. Design and development of streamlined extrusion dies: A Bezier c
- 溫馨提示:
1: 本站所有資源如無(wú)特殊說(shuō)明,都需要本地電腦安裝OFFICE2007和PDF閱讀器。圖紙軟件為CAD,CAXA,PROE,UG,SolidWorks等.壓縮文件請(qǐng)下載最新的WinRAR軟件解壓。
2: 本站的文檔不包含任何第三方提供的附件圖紙等,如果需要附件,請(qǐng)聯(lián)系上傳者。文件的所有權(quán)益歸上傳用戶所有。
3.本站RAR壓縮包中若帶圖紙,網(wǎng)頁(yè)內(nèi)容里面會(huì)有圖紙預(yù)覽,若沒(méi)有圖紙預(yù)覽就沒(méi)有圖紙。
4. 未經(jīng)權(quán)益所有人同意不得將文件中的內(nèi)容挪作商業(yè)或盈利用途。
5. 裝配圖網(wǎng)僅提供信息存儲(chǔ)空間,僅對(duì)用戶上傳內(nèi)容的表現(xiàn)方式做保護(hù)處理,對(duì)用戶上傳分享的文檔內(nèi)容本身不做任何修改或編輯,并不能對(duì)任何下載內(nèi)容負(fù)責(zé)。
6. 下載文件中如有侵權(quán)或不適當(dāng)內(nèi)容,請(qǐng)與我們聯(lián)系,我們立即糾正。
7. 本站不保證下載資源的準(zhǔn)確性、安全性和完整性, 同時(shí)也不承擔(dān)用戶因使用這些下載資源對(duì)自己和他人造成任何形式的傷害或損失。
最新文檔
- 物業(yè)管理制度:常見(jiàn)突發(fā)緊急事件應(yīng)急處置程序和方法
- 某物業(yè)公司冬季除雪工作應(yīng)急預(yù)案范文
- 物業(yè)管理制度:小區(qū)日常巡查工作規(guī)程
- 物業(yè)管理制度:設(shè)備設(shè)施故障應(yīng)急預(yù)案
- 某物業(yè)公司小區(qū)地下停車場(chǎng)管理制度
- 某物業(yè)公司巡查、檢查工作內(nèi)容、方法和要求
- 物業(yè)管理制度:安全防范十大應(yīng)急處理預(yù)案
- 物業(yè)公司巡查、檢查工作內(nèi)容、方法和要求
- 某物業(yè)公司保潔部門領(lǐng)班總結(jié)
- 某公司安全生產(chǎn)舉報(bào)獎(jiǎng)勵(lì)制度
- 物業(yè)管理:火情火災(zāi)應(yīng)急預(yù)案
- 某物業(yè)安保崗位職責(zé)
- 物業(yè)管理制度:節(jié)前工作重點(diǎn)總結(jié)
- 物業(yè)管理:某小區(qū)消防演習(xí)方案
- 某物業(yè)公司客服部工作職責(zé)
相關(guān)資源
更多